
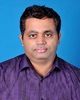
- Open Access
- Authors : Dhanesh S(Asst Prof), Vydoorya J, Navin A Menon, Kiran M
- Paper ID : IJERTV13IS090061
- Volume & Issue : Volume 13, Issue 09 (September 2024)
- Published (First Online): 01-10-2024
- ISSN (Online) : 2278-0181
- Publisher Name : IJERT
- License:
This work is licensed under a Creative Commons Attribution 4.0 International License
Thermal Model for Friction Stir Welding of AA5052 Tailor Welded Blanks
Dhanesh S(Asst Prof)
Department of Mechanical Engineering Ahalia School of Engineering and Technology Palakkad, Kerala
Navin A Menon
Department of Mechanical Engineering Ahalia School of Engineering and Technology Palakkad, Kerala
Vydoorya J
Department of Mechanical Engineering Ahalia School of Engineering and Technology Palakkad, Kerala
Kiran M
Department of Mechanical Engineering Ahalia School of Engineering and Technology Palakkad, Kerala
Abstract
In this paper, a three-dimensional finite element based transient model is used to predict the thermal history during friction stir welding (FSW) of AA5052 Tailor welded Blanks (TWB). The model uses temperature dependent material properties and it is validated using results from published literature. The model is used to investigate the effect of process parameters namely tool rotation speed (TRS), welding speed (WS), shoulder diameter (SD) and Thickness Ratio (TR) on the temperature distribution and peak temperature during FSW of AA5052 TWB. The parameters are varied at two levels and all the parameter combinations are numerically simulated. The numerical results obtained from the model are used to develop a regression model. The regression model is employed to explore the effect of parameters on the peak temperature during FSW of AA5052 TWB. The results indicate that the peak temperature attained is directly related to tool rotational speed and shoulder diameter. It is found that increase in the WS causes a drop in the peak temperature for a given TRS and SD. Keywords: AA5052, Tailor Welded Blanks, Regression Model, Process Parameters
-
INTRODUCTION
Tailor Welded Blank (TWB) is basically a blank with two or more sheets of different thickness, materials or coatings which are welded into a single plate before forming [1-2]. TWBs are finding wide range of applications in automotive, aerospace and manufacture of household items due to their superior property [1]. TWB generally made of light-weight materials like aluminum, magnesium, titanium offers high strength-to-weight ratio along with excellent stiffness and corrosion resistance, dimensional stability etc. TWBs made of dissimilar thickness find application in areas which require different strength at different sections and proper weight distribution. Dissimilar TWBs find application in transportation and propulsion industries [5]. The major challenges faced in the joining TWBs are the difference in the chemical, mechanical and thermal properties of the components involved.
Various methods are used in the manufacturing of
TWBs. The formability of the welded blanks is mainly influenced by the welding method adopted [5]. The choice of welding method for manufacture of TWB depends on its applications. Laser welding is a method which can be used for the manufacture of TWB however laser welding presents challenge due to keyhole
penetration which results in rapid solidification of the weld metal. Laser welding also results in defects like cracking, porosity, loss of alloying elements and grain boundary melting. Aluminium which is most commonly used light weight material cannot be welded using laser welding due to specific characteristics of aluminium like its reflectivity [5]. Friction Stir Welding (FSW) which is a solid-state welding process invented at The Welding Institute (TWI) in 1991 produces a solid-state bonding between the base metals using the frictional heat generated between the tool and the base metals. FSW offers advantages of better tensile, bend and fatigue properties [6]. Arun et al. [7] explores the effect of FSW parameters tool rotation speed, shoulder diameter, tool traverse speed and thickness ratio on the maximum temperature, contact status and energy input during FSW of TWB. A hybrid model integrating the linear function and radial basis function was used. Computational fluid dynamics based numerical model can be handy in determining thermal history and material flow during FSW of dissimilar aluminium alloys[8].
The quality of weld produced by FSW depends on the process parameters considered. Major process parameters which are considered are tool rotation speed, tool traverse speed, shoulder diameter, thickness ratio [10]. Optimization of these process parameters is required for getting a good quality weld and better joint strength [14].
Prediction of the thermal history and material flow is essential for understanding the process and its optimization. A three- dimensional finite element model is developed to explore the effect of parameters on peak temperature during FSW of AA5052 TWB in this work. The four process parameters considered are tool rotation speed (TRS), welding speed (WS), thickness ratio (TR) and shoulder diameter (SD). This model is used to simulate FSW of TWB for different combinations of process parameters. Prediction of the thermal history and material flow is essential for understanding the process and its optimization. A three- dimensional finite element model is developed to explore the effect of parameters on peak temperature during FSW of AA5052 TWB in this work. The four process parameters considered are tool rotation speed (TRS), welding speed (WS), thickness ratio (TR) and shoulder diameter (SD). This model is used to simulate FSW of TWB for different combinations of process parameters.
-
MODELLING
Modeling was carried out using COMSOL PHYSICS 5.0. AA5052 plate of dimensions 158 mm 50mm was considered [4]. The modeled plates are shown in figure 1. The tool considered is made up of high speed tool steel material. The plate is assumed to undergo heat transfer by convection and radiation and a moving coordinate system is used.
Figure 1 Geometry Used
-
BOUNDARY CONDITION
Since the heat conductivity of the work piece is much higher than the tool material, it is assumed that a significant amount of heat will be transported from the tool to the work piece. Top, front and back surfaces are subjected to both convective and radiative heat transfer. Bottom, left and right surfaces are subjected to only convective heat transfer. Temperature in the surroundings is assumed to be ambient temperature [3].
-
HEAT TRANSFER CONDITIONS
Both convective and radiative heat transfer conditions are considered in the model. Heat transfer coefficient of top and bottom surface is assumed to be different and is given by h_upside and h_downside. The total heat generation is obtained by the total sum of heat generated on the shoulder and pin as given in equation (1) [9]
= + (1)
Convective and radiative heat equations is given by equation
(2) [9]
= (4 4) + _( )
(2)
Convective heat transfer alone is given by equation (3) [9]
= _( ) (3)
2.0 FACTORIAL DESIGN
A two-level factorial design was used to study the effect of parameters on the peak temperature during FSW of AA5052 TWB. The process parameters that were varied during the simulation are tool rotation speed, welding speed, shoulder diameter and thickness ratio. The effect of the parameters upon the peak temperature was analysed using a 2k factorial design [4]. The peak temperatures obtained from the model are given in Table 1.
Table 1 : Process parameter vs Peak Temperature
SLN O
PROCESSS PARAMETER
PEAK TEMPERA TURE
(k)
TRS (RPM
)
WS (MM
/S)
SD (M
M)
TR
1
750
0.33
15
0.8
431
2
750
0.33
15
0.9
418
3
750
0.33
20
0.8
440
4
750
0.33
20
0.9
430
5
750
1
15
0.8
413
6
750
1
15
0.9
397
7
750
1
20
0.8
434
8
750
1
20
0.9
420
9
1000
0.33
15
0.8
465
10
1000
0.33
15
0.9
447
11
1000
0.33
20
0.8
465
12
1000
0.33
20
0.9
461
13
1000
1
15
0.8
439
14
1000
1
15
0.9
426
15
1000
1
20
0.8
445
16
1000
1
20
0.9
434
3.0 REGRESSION MODELLING OF PEAK TEMPERATURE
In order to explore the effect of parameters on the peak temperature, a regression model is developed. Regression is a mathematical expression that relates the dependent variables or responses and independent variables of an experiment. Regression can be used to understand the effect of independent variables on the response. It also helps in evaluation and selection of variables to be used for building predictive models. In this paper a regression model considering the effect of four variables TR,SD,WS and TRS and their interactions was developed.
4.0 RESULT AND DISCUSSION
The effect of TRS, WS, SD and TR on peak temperature was studied using the model results. Contour plots of peak temperature obtained for various process parameters are given in Figure 2.
The figure shows the temperature plot for a given set of process parameters. It can be observed that TRS and SD have a major influence on peak temperature and the peak temperature increases as TRS and SD increase. however the peak temperature is found to decrease with WS. For a given shoulder diameter, it is observed that the peak temperature attained is found to decrease with increase in TR. Figure 2 shows peak temperature obtained for the process parameters considered.
adj
The ANOVA for the model is presented in Table 2. The terms with p-values less than 0.05 (Table 2) are considered insignificant and are not included in the model. The R2 and R 2 for the model are 0.9887 and 0.9736 respectively. The final regression model for the peak temperature is T=493.2957-349.4179(TMR)- 1.2664(SD)+21.6418(WS)+0.2082(TRS)-0.0074(SD*TRS)-
0.0582(WS*TRS)
The effect of individual parameters on the peak temperatures are explored using the line plots shown in Figure 3. The peak temperature is found to decrease with increase in thickness ratio from Figure 3(a). Asymmetry in the thickness has an impact on the maximum temperature developed.
Table 2 : ANOVA
source
Sum sq
D.F
Mean Sq
F
p- value
TMR
612.56
1
612.56
50.78
0.0008
SD
540.56
1
540.56
44.81
0.0011
WS
1387.56
1
1387.56
115.03
0.0001
TRS
2475.06
1
2475.06
205.19
0
TMRXSD
27.56
1
27.56
2.28
0.191
TMRXWS
5.06
1
5.06
0.42
0.5457
TMRXTRS
3.06
1
3.06
0.25
0.6358
SDXWS
33.06
1
33.06
2.74
0.1587
SDXTRS
85.56
1
85.56
7.09
0.0447
WSXTRS
95.06
1
95.06
7.88
0.0377
Error
60.31
5
12.06
Total
5325.44
15
The same trend is obtained for both the levels of parameters. With increase in SD the peak temperature is found to increase. The heat generation increases with increase in SD and hence peak temperature increases. The peak temperature for a given shoulder diameter is found to decrease with increase in TR,WS and TRS. Increase in WS decreases the peak temperature, because the heat input to the plate decreases as the WS increases. As TRS is increased the heat generation increases which results in an increase in peak temperature. The increase in peak temperature is more when the other parameters are set at their higher level.
The interaction effect of parameters is presented as contour plots in Figure 4. The interaction between TRS and SD as well as TRS and Ws are found to have a significant effect on peak temperature. From Figure 4(a), it is noted that for a given TRS, increase in SD or for a given SD increase in TRS increases peak temperature. From Figure 4(b) it is observed that for a given TRS increase in WS results in a decrease in peak temperature and for a given WS increase in TRS increases peak temperature.
5.0 CONCLUSION
Numerical simulation of FSW of AA5052TWB was performed. Finite element method is used for the simulation and factorial design is used to explore the effect of process parameter on peak temperature. The following conclusions are made:
-
The parameters considered TR, SD, WS and TRS have significant effect on the peak temperature during FSW of AA5052 TWB.
-
The parameters SD and TRS increase peak temperature while TR and WS decrease peak temperature as they are increased.
-
Peak temperature decreases with increase in TR when the SD is kept constant. It is observed that for a constant TRS and SD, the peak temperature is found to decrease with decrease in the WS and TR.
-
The interaction effect of TRS & SD and TRS & WS influences the peak temperature. Peak temperature is observed to increase with SD for a given TRS. It is observed that for a given TRS, the peak temperature is found to decrease with increase in WS.
-
Two level factorial design can be used to explore the effect of process parameterson FSW of AA5052 TWB.
-
6.0 REFERENCES
-
Davies, Richard W., H. E. Oliver, Mark T. Smith, and Glenn J. Grant. "Characterizing Al tailor-welded blanks for automotive applications." JOM 51, no. 11 (1999): 46-50.
-
Tufaro, Leonardo N., Ivan Manzoni, and Hernan G. Svoboda. "Effect of heat input on AA5052 friction stir welds characteristics." Procedia Materials Science 8 (2015): 914-923.
-
Zhang, X. X., B. L. Xiao, and Z. Y. Ma. "A transient thermal model for friction Stir Weld. Part I: the model." Metallurgical and Materials Transactions A 42, no. 10 (2011): 3218-3228.
-
Aravind, A. Yukesh, R. Vaira Vignesh, R. Padmanaban, and M. Govindaraju. "Study on the Mechanical and Corrosion behaviour of AA5052 Tailor Welded Blanks Fabricated using Friction Stir Welding." (2019).
-
Kinsey, B., and Xin Wu, eds. Tailor welded blanks for advanced manufacturing. Elsevier, 2011.
-
Mishra, Rajiv S., and Z. Y. Ma. "Friction stir welding and processing." Materials science and engineering: R: reports 50, no. 1-2 (2005): 1-78.
-
Arun Siddharth M., Padmanaban R., Vaira Vignesh R. (2020) Simulation of Friction Stir Welding of Aluminium Alloy AA5052 Tailor Welded Blanks. In: Abraham A., Cherukuri A., Melin P., Gandhi N. (eds) Intelligent Systems Design and Applications. ISDA 2018 2018. Advances in Intelligent Systems and Computing, vol 940. Springer, Cham. https://doi.org/10.1007/978-3-030-16657-1_11
-
Padmanaban, R.V.R.K., Kishore, V.R. and Balusamy, V., 2014. Numerical simulation of temperature distribution and material flow during friction
stir welding of dissimilar aluminium alloys. Procedia Engineering, 97, pp.854-863.
-
Comsol Available from: https://www.comsol.co.in/model/friction-stir- welding-of-an-aluminumplate-461
-
Shi, Ming F., Ken M. Pickett, and Kumar K. Bhatt. Formability issues in the application of tailor welded blank sheets. No. 930278. SAE Technical Paper, 1993.
-
Yong-Jai, K. W. O. N., S. H. I. M. Seong-Beom, and P. A. R. K. Dong- Hwan. "Friction stir welding of 5052 aluminium alloy plates." Transactions of Nonferrous Metals Society of China 19 (2009): s23-s27.
-
Parente, Marco, R. Safdarian, Abel D. Santos, Altino Loureiro, Pedro Vilaca, and RM Natal Jorge. "A study on the formability of aluminium tailor welded blanks produced by friction stir welding." The International Journal of Advanced Manufacturing Technology 83, no. 9- 12 (2016): 2129-2141.
-
Rojek, J., Hyrcza-Michalska, M., Bokota, A. and Piekarska, W., 2012. Determination of mechanical properties of the weld zone in tailor- welded blanks. Archives of Civil and Mechanical Engineering, 12, pp.156-162.
-
Padmanaban, R., Balusamy, V. and Vaira Vignesh, R., 2020. Effect of friction stir welding process parameters on the tensile strength of dissimilar aluminium alloy AA2024T3 and AA7075T6 joints. Material wissenschaft und Werkstofftechnik, 51(1), pp.17-27