
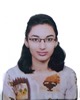
- Open Access
- Authors : S.Mounika, Ch. Ratnam
- Paper ID : IJERTV13IS100005
- Volume & Issue : Volume 13, Issue 10 (October 2024)
- Published (First Online): 16-10-2024
- ISSN (Online) : 2278-0181
- Publisher Name : IJERT
- License:
This work is licensed under a Creative Commons Attribution 4.0 International License
Design and Analysis of Knuckle Joint using AA7075 Material
S. Mounika
PG Student(Machine Design) Department of Mechanical Engineering
Andhra University, Visakhapatnam, Andhra Pradesh, India
Ch. Ratnam
Professor
Department of Mechanical Engineering
Andhra University, Visakhapatnam, Andhra Pradesh, India
ABSTRACT
A knuckle joint is a device used to secure two loaded rods together. When connecting two rods under tensile load, a knuckle joint is utilized. This connection allows the rods to be misaligned in both directions and, with proper guidance, can withstand compressive loads. These joints are employed in the construction of bridges for various kinds of connections, such as tension links and tie rods. One of the rods in this is forked, with eyes at both legs, and the other has an eye at the rod end. A collar and a split pin are used to fasten the pin once it has been placed through the rod end and fork end eyes. In many cases, screwed connections are crucial to the load transmission via machine assemblies. The paper reports on the study and design of a power transmission- related knuckle joint. This study used the Finite Element Method to model and analyse a knuckle joint. Software in three dimensions is used to model the knuckle joint. Modelling in this case was done on CATIA V5. Ansys Workbench 19.0, an analysis program, was used for the simulation portion of the endeavour. The selection of appropriate material, such as AA7075, is necessary to improve operating efficiency. The choice of the most appropriate material for producing the practical knuckle joint is aided by comparing the structural behaviour of the knuckle joints after applying this material to the standard default material that is already in use.
Keywords ANSYS, FEA, Knuckle joint, Static Structural Analysis
-
INTRODUCTION
A knuckle joint is used to join two rods that are subjected to the action of tensile loads. However, the rods can support compressive loads if the joint is directed. A knuckle joint can be easily disconnected for adjustment or repair. The knuckle joint is used to transmit axial tensile force. A knuckle joint is a mechanical joint that connects two rods or bars at an angle, allowing limited angular movement. It consists of a pin or rod inserted into a series of alternating holes in the two components, enabling rotation and axial movement. Knuckle joints are commonly used in applications where flexibility and articulation are required, such as in linkages and suspension systems. The knuckle joint operates on the principle of a pivot, where the rod end fits between the fork ends, and the knuckle pin passes through aligned holes in both parts. This configuration allows the connected parts to rotate around the pin, providing the necessary angular movement. The figure of a knuckle joint is shown in Fig.1. The knuckle joint assembly consists of following major components.
Fig.1 Knuckle joint
-
Single-Eye End
-
Double-Eye End or Fork End
-
Knuckle Pin
-
Collar
-
Taper Pin or Lock Pin or Split Pin
The picture above displays a knuckle joint in its assembled state. The knuckle pin's axis can be rotated by both the fork end and the eye end in their respective planes.
A knuckle joint may be failed on following three modes. They are:
-
Shear failure of pin (single shear).
-
Crushing of pin against rod.
-
Tensile failure of flat end rod.
The failure of knuckle joint has been studied by several investigators (1-2). Jones (1) has reported that shear failure due to torsional loading is the normal failure mechanism in many engineering components. Pantazopouloes et.al (2) have studied the failure of knuckle joint of a universal coupling system. It was mentioned that torsional overload of a knuckle joint is the major cause of failure. Suraj et.al (3) determines the allowable stress for 30C8 is 400 MPa, and the knuckle joint experiences 201 MPa, ensuring a safe design. A 25 mm pin can support a 50KN load, as confirmed by CATIA modeling and ANSYS analysis. Miss Yogini et al. (4) determined a 30 mm diameter knuckle joint pin made of 30C8 steel was designed to handle a 50KN load. ANSYS analysis with 70,337 nodes and 18,289 elements confirmed the pin's safety with a factor of safety of 5. Theoretical and FEA results closely matched, with maximum tensile stresses and deformation (0.052 mm) occurring in the eye region, highlighting potential crack or fatigue risks.
Ramesh et.al (5) investigated on a knuckle joint made of FE410W material (yield strength 467 MPa) was modeled in SOLID EDGE and analyzed in ANSYS. The analysis showed that a 25 mm diameter knuckle joint can support a load of 229.238KN. Asmaa et.al (6) studied on modified AA7075 alloys were studied during casting and laser melting. AA7075- TiB had the best properties, with finer grains and improved corrosion resistance. AA7075-ScZr also showed better corrosion resistance, while AA7075-standard and AA7075- FeNi had issues with liquation and poor element distribution. Future work will optimize welding and additive manufacturing. K. Emre et.al (7) studied on heat treatment of AA2024 and AA7075 in T3 and T6 was assessed. AA7075-T6 had better strength but lower toughness, while AA2024-T3 showed higher impact energy. AA7075-T6's hardness and strength make it ideal for high-performance applications.
-
-
THEORETICAL CALCULATIONS
-
Material Selection
Engineers must choose materials that possess the requisite properties for optimal performance, including sufficient tensile strength, yield strength, and hardness to withstand applied loads without deforming or failing. Attributes such as ductility and toughness are also critical, as they enable the material to absorb impact loads and prevent brittle failure, especially in dynamic applications. Furthermore, corrosion resistance is a key factor, particularly in environments exposed to moisture or chemicals, as this property ensures the joint's longevity and reduces degradation risks over time. By carefully considering these material properties, engineers can significantly enhance the reliability and durability of the knuckle joint. There is tensile force applied to the rods. Thus, the criterion for choosing the rod's material is yield strength. Both bending and shear pressures might affect the pin.
Table.1 Material Mechanical Properties
Materials
AA7075-T6
AA7075-Ti+B
Density (kg/
2810
2810
Youngs Modulus (GPa)
71.7
71.7
Yield strength (MPa)
503
169
Ultimate Tensile Strength (MPa)
572
269
Poissons Ratio
0.33
0.33
-
Selection of factor of safety
In stress analysis of knuckle joint, the effect of stress concentration is neglected. To account for this effect, a higher factor of safety of 4 is assumed in present design.
-
Calculations
P
Yield strength of material AA7075-Ti + B (Syt)=169 N/mm2
Tensile stress ) =
Shear stress =
Step i : Dimension of each rod
=
=
=
= 95.08
D = 97mm
Step ii : Dimensions of enlarged diameter of each rod by empirical relationship.
D1 = 1.1 x D
= 1.1 x 97
= 106.7
D1 108
Step iii : Dimension of a & b by empirical relationship.
a = 0.75 D b = 1.25 D
= 0.75×97 = 1.25×97
= 72.75 = 121.25
74 123
Table .2 chemical composion of wt% of materials
Alloy
Al
Zn
Mg
Cu
Cr
Mn
Ti
B
Fe
Ni
Zr
Sc
Other Elements
AA7075-T6
Bal
5.57
2.38
1.49
0.20
0.03
0.03
–
0.11
–
0.04
–
<0.1
AA7075-TiB
Bal.
6.8
2.2
1.4
0.3
0.3
1
0.2
–
–
–
–
<0.1
Step iv : Dimension of Pin a) By shear consideration
=
= 95.04
d 97mm
-
By bending consideration
=
= 126
b 128mm
The minimum value of diameter of Pin (d) = 128
Step V : Dimension of o & i by empirical relationship
do = 2 d di = 1.5d
= 2 x 128 = 1.5 X 128
o = 256 i= 192
Step vi : Checking the tensile crushing and shear stress in eyes
-
t = /b(dodb)
= 300000 /123(256128)
19.05 < 42.25 N/ mm2
-
= P /b(db)
= 300000 /123(128)
= 300000/ 15744
19.05 < 42.25 N/ mm2
-
= P/ b(dodb)
-
= 300000/ 123(256128)
= 300000/ 15744
19.05 < 21.25 N/ mm2
Step vii: Checking the tensile crushing and shear stress
-
t = P /2a(dodb)
= 300000/ 2 (74)(256128)
= 300000/ 18944
15.8365 < 42.25 N/ mm2
-
= /2(b)
= 300000 /2(74)(128)
300000 /18944
= 15.836
-
= / 2(ob)
= 300000/ 2(74)(256128)
= 300000/ 18944
= 15.836 < 21.12 / 2
Hence The design is safe
Table.3 Dimensions of knuckle joint
Parameters
Symbols
Values (mm)
Axial load
P
300 KN
Diameter of each rod
D
97
Enlarged diameter of each rod
D1
108
Diameter of knuckle pin
d
128
Thickness of each eye of fork
a
74
Thickness of eye end of rod- B
b
123
Outer diameter of eye of fork
do
256
Diameter of pin head
di
192
-
-
CAD MODELLING
Making a CAD model is the initial stage in finite element analysis. A 128 mm-diameter knuckle joint that is subjected to tensile force has been examined. The design using the dimensions of the knuckle joint used in this investigation are displayed in Fig. 1. Dimensions displayed in Table.3 are used in CATIA V5 R20 to generate the CAD model of the knuckle joint. The assembled CATIA model of the knuckle joint is displayed in Fig. 2.
Fig.2 Knucle joint Model using CATIA
-
STATIC STRUCTURAL ANALYSIS USING ANSYS
For modelling and simulation tasks in complex fields such advanced engineering manufacturing, transportation, housing, and architectural design, finite element analysis is an essential tool. We consider a knuckle joint with a diameter of 128 mm. An ANSYS 15.0 model is imported once the assembled CATIA model has been converted into STP format. With 135,700 nodes and 103,870 elements, the ANSYS meshed model of the original knuckle joint is displayed in Fig 3.
Fig.3 Meshing
-
RESULTS AND DISCUSSIONS
Table.4 shows the results of shear stress and tensile stress for fork, eye and pin by theoretical calculations with their maximum permissible limits when the load is considered as 300KN and the material used is AA7075-Ti+B.
Table .4 Stress calculations by Analytical method
Element
Type of stress
Analytical calculations
stress results (N/mm2)
Maximum Permissible limits (N/mm2)
Eye
Shear stress
19.05
21.25
Tensile stress
19.05
42.25
Fork
Shear
stress
15.836
21.25
Tensile stress
15.83
42.25
Pin
Shear stress
21.25
21.25
Tensile stress
21.25
21.25
-
Static Structural Analysis of Pin
Figure 4 shows the shear stress of Pin, which is 21.25 MPa analytically. This value is confirmed by the FEA result, which is 6.0773 MPa, which is less than maximum stress limit. The pin's normal stress
in Figure 5 is 15.027 MPa, or less than the allowed stress determined by FEA, despite being 21.25 MPa according to
theoretical calculations. Thus, a pin under stress is safe. Figure 6 shows that the highest
shear stress for a pin calculated by ANSYS is 17.779 MPa, which is less than 21.25 MPa maximum allowable limit. Therefore, pin is secure.
Fig.4 Shear stress for pin using AA7075-Ti+B
Fig.5 Normal stress for pin using AA7075-Ti+B
Fig.6 Maximum shear stress for pin using AA7075-Ti+B
-
Static Structural Analysis for Eye
Fig.7 Normal stress for eye using AA7075-Ti+B
Fig.8 Shear stress for eye using AA7075-Ti+B
Fig.9 Maximum shear stress for eye using AA7075-Ti+B
In fig.7, the normal stress for eye is 31.966 MPa which is less similar to theoretical normal stress 19.05 MPa, but is below maximum permissible limit. i.e. 42.25 MPa. Hence eye is safe for tensile stress. Fig.8 explains the shear stress for eye by FEA is 8.7138 MPa which is less than theoretical calculations
i.e. 21.25 MPa. Hence eye is safe for shear stress. Fig.9 shows the maximum shear stress for eye with 300 KN force, i.e.38.307 MPa.
-
Static Structural Analysis of Fork
Fig.10 Normal stress for fork using AA7075-Ti+B
Fig.11 Shear stress for fork using AA7075-Ti+B
Fig.12 Maximum shear stress for fork using AA7075-Ti+B
As seen in fig.10 the normal stress for fork by FEA is 40.832 MPa which is less similar to theoretical stress i.e. 15.832 MPa but it is less than maximum permissible limit i.e. 42.25 MPa . Hence fork is safe for tensile stresses. Fig 11 explains, the shear stress for fork by FEA is 17.564 MPa, which is less than to theoretical stress value i.e. 15.832 MPa, and also less than maximum permissible limits i.e. 42.25 MPa. Hence fork is
safe for shear stress. Maximum shear stress for fork with 42.841 MPa,as seen in fig.2
IJERTV13IS100005
(This work is licened under a Creative Commons Attribution 4.0 International License.)
Table.5 Validation of results
Elem ent
Type of stress
Hand calculations stress results
(N/mm2)
FEA
Results (N/mm2)
Maximum Permissible limits
(N/mm2)
Eye
Shear stress
19.05
8.7138
21.25
Tensile stress
19.05
31.966
42.25
Fork
Shear stress
15.836
17.564
21.25
Tensile stress
15.83
40.832
42.25
Pin
Shear stress
21.25
6.0773
21.25
Tensile stress
21.25
15.027
21.25
Max. shear stress
21.25
17.779
21.25
Table.5 shows the comparison of shear and tensile/normal stress values for eye, fork and pin by theoretical and FEA method.
-
Static structural analysis of knuckle joint
Fig.13 Total Deformation of Knuckle joint using AA7075- Ti+B material
Fig.14 Equivalent Stress of knuckle joint using AA7075-Ti+B material
Fig.15 Total Deformation of Knuckle joint using AA7075-T6 material
Fig.16 Equivalent Stress of knuckle joint using AA7075-T6 material
Table.6 Results comparison chat
Materials
Total Deformation(mm)
Maximum stresses (MPa)
AA7075- Ti+B
0.44794
82.616
AA7075-T6
0.78423
206.72
Table.6 describes the total deformation and maximum stresses obtained when applying tensile load is 300KN using AA7075 but with different chemical composition weight percentages and the results obtained are compared in the above table and found out that when comparing the maximum stress among these two materials, AA7075-Ti+B shows better results because the stresses developing when using this material obtains less stresses when compared with AA7075-T6.
-
-
CONCLUSION
The knuckle joint being developed in this study is designed to withstand an applied force of 300KN. The diameter of the pin is approximately 128 mm, and the material selected for the knuckle joint is AA7075-T6 and AA7075-Ti+B. A 3D CAD model of the knuckle joint was created based on the calculated dimensions. For the stress analysis, a mesh was generated, comprising 1,35,700 nodes and 1,03,870 elements. The simulation was performed using ANSYS software, producing results including stress contours, tensile stress distribution, displacement contours, and total deformation contours for both the eye pin and the fork.
The ANSYS analysis indicates that a pin with a diameter of 30 mm can safely withstand a load of 300KN when a factor of safety of 4 is applied. The theoretical stress values for shear, tensile, and maximum allowable stresses closely align with the FEA stress results. Since both the theoretical and FEA results are nearly identical and remain below the maximum allowable stress for all components, it can be concluded that the design is safe for all three components. This agreement between the theoretical and FEA results confirms the accuracy of the FEA software. Additionally, it can be concluded that the region of the eye where the 300KN force was applied experiences the highest tensile stresses, as depicted in figure 10.
The analysis shows that the material with a lower yield strength experiences considerably lower stresses compared to the material with higher yield strength under similar loading conditions. This suggests that, although both materials are capable of effective performance, the material with lower yield strength operates in a safer stress range, which may contribute to better ductility and a reduced likelihood of failure. These results imply that the material with higher yield strength is more appropriate for applications requiring greater load-bearing capacity and structural stability. However, when choosing materials for specific uses, it is crucial to also factor in aspects like fatigue performance, toughness, and resistance to corrosion.
REFERENCES
-
Jones DRH, Engineering Materials 3 materials failure analysis,
Oxford (UK) Pergamon Press (1993).
-
Pantazopoulos G.,. Sampani, A. Tsagaridis E, Torsional failure of a knuckle joint of a universal steel coupling system during operation A case study , Engineering Failure Analysis, Volume 14, Issue1, January(2007)73-84.
-
Suraj Yadav, Design and analysis of knuckle joint by using FEA, International journal of current engineering and scientific research (IJCESR), Volume-4, issue-6, 2017
-
Miss. Yogini .V. Deore, International Journal Of Advanced Research in Engineering & Management (IJAREM) ISSN: 2456-2033 || PP. 10-22, Vol. 03, Issue 04, 2017.
-
Ramesh B T, Design and Analysis of Knuckle Joint by using Solid EDGE and ANSYS, International Journal of Engineering Research & Technology (IJERT) ISSN: 2278-0181 ICEI – 2022 Conference Proceedings
-
Asmaa M.Khalil, Evaluation of the Microstructure and Mechanical Properties of a New Modified Cast and Laser-Melted AA7075 Alloy, Materials 2019, 12, 3430.
-
K.Emre Öksüz, Investgaton Of Mechancal Propertes and Mcrostructure of AA2024 and AA7075, Applied Mechanics and Materials Vol 390 (2013) pp 547-551.
-
Sangamesh, Structural static analysis of knuckle joint, International Journal of Engineering Research and General Science Volume 4, Issue 2, March-April, 2016 ISSN 2091-2730
-
Ms. Nilesha Patil, Static structural analysis of knuckle joint, International Journal of advanced technology in Engineering and Science Volume 4, Issue.12, December 2016.
-
Ritvik Bhardwaj, Design and analysis of knuckle joint for different materials, research gate, August 2020.
-
Shaik.John Bhasha, Modeling and Analysis of Knuckle Joint, International Journal & Magazine of Engineering, Technology, Management and Research, ISSN No: 2348-4845, Volume No: 2 (2015), Issue No: 11 (November).
-
Somase Anil R, Material Optimization for Knuckle Joint by Using FEA, International Research Journal of Engineering and Technology (IRJET), Volume: 06 Issue: 10 | Oct 2019.
-
Nishant Vibhav Saxena Int. Journal of Engineering Research and Applications ISSN : 2248-9622, Vol. 5, Issue 3, ( Part -4) March 2015, pp.67-72.
-
D.sai teja, design and analysis of knuckle joint, International Journal for recent developments in Science and technology, Volume 03, Issue 12, Dec 2019, ISSN 2581 4575.
-
Prof. Kashinath H. Munde, Material optimization of knuckle joint using FEA, International Journal of Creative Research Thoughts (IJCRT), Volume 6, Issue 2 April 2018 | ISSN: 2320-2882.
-
Anupam Raj Jha, Design and Finite Element Analysis of Knuckle Joint Using CATIA and ANSYS Workbench, International Journal of Research in Mechanical Engineering Volume 4, Issue 3, May – June, 2016, pp. 01-05.
-
Aisha Muhammad, Structural Analysis of a Knuckle Joint using different materials, research gate, 1st International Civil Engineering Coference (ICEC 2018).
-
Shaik Vaseem Akram, Design and Analysis of Knuckle joint With Different Materials, Journal of Emerging Technologies and Innovative Research (JETIR), June 2019, Volume 6, Issue 6.
-
Siddharaj Barge, Design and Analysis of Knuckle Joint Utilized in Structures by using Polylactic Acid Material with Different Infill Percentage, International Journal of Innovative Research in Science, Engineering and Technology, Vol. 8, Issue 3, March 2019.
-
Aisha Muhammad, Transient Analysis and Optimization of A Knuckle Joint, Vol. 4, No. 2, May 2019, Pp. 179-186.
-
Shankar Majhi, Modeling and analysis of knuckle joint used in tractor, International Research Journal of Engineering and Technology (IRJET), Volume: 04 Issue: 07 | July -2017.
-
Duong Dinh Hao, Tran Hung Tra, Effects of friction stir welding parameters on the mechanical properties of AA7075-T6, Archives of Materials Science and Engineering 77/2 (2016) 58-64.
-
Elder Soares, Microstructure and Mechanical Properties of AA7075 Aluminum Alloy Fabricated by Spark Plasma Sintering (SPS), Materials 2021, 14, 430.
-
S. V. Sajadifar et al.: Effect of Tool Temperature on Mechanical Properties and Microstructure of Thermo-Mechanically Processed AA6082 and AA7075 Aluminum Alloys. HTM J. Heat Treatm. Mat. 75 (2020) 3, pp. 177-191.
-
E. Scharif, Effect of thermo-mechanical processing on quench-induced precipitates morphology and mechanical properties in high strength AA7075 aluminum alloy, materialsCharacterization174(2021)111026. 3
-
Edip Cetkin, Microstructure and mechanical properties of AA7075/AA5182 jointed by FSW, Journal of Materials Processing Tech. 268 (2019) 107116.
-
Tamilselvan Amuthan, Experimental study of mechanical properties of AA6061 and AA7075 alloy joints using friction stir welding, Materials Today: Proceedings xxx (xxxx) xxx 2021.
-
S. Babajanzade Roshan, Optimization of friction stir welding process of AA7075 aluminum alloy to achieve desirable mechanical properties using ANFIS models and simulated annealing algorithm, Int J Adv Manuf Technol 13 June 2013.
-
Suleyman Kilic, Effects of Aging Temperature, Time, and Pre-Strain on Mechanical Properties of AA7075, Materials Research. 2019; 22(5): e20190006.
-
Y. Phaneendra, Thermo-Mechanical Treated High Strength AA-7xxx Aluminium Alloy by Cold and Cryo-Rolling Study their Mechanical Properties Corrosion and Microstructure Correlation, Materials Science Forum ISSN: 1662-9752, Vol. 969, pp 62-67.
-
J Suresh Kumar, Forming of AA2xxx and AA7xxx Sheet Alloys & their Studies on Microstructural and Mechanical Properties of Cold & Cryo Rolled Aluminum Alloys, Materials Science Forum ISSN: 1662-9752, Vol. 969, pp 546-551.
-
Gokhan OZER, Properties of AA7075 aluminum alloy in aging and retrogression and raging process, Trans. Nonferrous Met. Soc. China 27(2017) 23572362.