
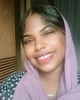
- Open Access
- Authors : Dr.Eng. Ali Hussein Mohammed M. Bass, Eng. Maram Abubaker Alsiddig Abass
- Paper ID : IJERTV13IS110140
- Volume & Issue : Volume 13, Issue 11 (November 2024)
- Published (First Online): 06-12-2024
- ISSN (Online) : 2278-0181
- Publisher Name : IJERT
- License:
This work is licensed under a Creative Commons Attribution 4.0 International License
The Effects of Waste Materials on Cement Mortar Properties [Case Study: Fly Ash and Cement Dust]
Dr.Eng. Ali Hussein Mohammed M. Bass
Civil Engineering Department University of Bahri, College of Engineering,
Khartoum, Sudan
Eng. Maram Abubaker Alsiddig Abass
Civil Engineering Department University of Bahri, College of Engineering,
Khartoum, Sudan
Abstract This work investigates the effectiveness of using fly ash and cement dust as partial cement substitutes in mortar production. The study aims to address the dual challenge of high waste generation and construction material costs. Samples of fly ash and cement dust were incorporated into mortar mixtures at different percentages (10%,20%,30%,40% and 50%), and their effect on compressive strength was evaluated through chemical and mechanical tests. The results indicate that 30% cement dust replacementachieved optimum compressive strength, significantly outperforming the reference mix by 20.43%. This optimized mix also demonstrated significant cost savings, with the potential to reduce overall production costs by more than 30%. While fly ash mixtures faced challenges such as solubility and high loss on ignition, the results underscore the promising potential of cement dustas a viable alternative to conventional cement. By incorporating cement dust, the study succeeded in enhancing the properties of cement mortar while mitigating environmental pollution and reducing the industrys dependence on raw materials. Overall, the study suggests that incorporating waste materials such as fly ash and cement dust tooptimum levels without decreasing the chemical composition of either can enhance cement mortar properties while reducing production costs and environmental pollution.
Keywords Cement mortar, Waste materials, Flyash, Cement dust, Properties, Cost effectiveness, Environmental impact, Resource conservation.
-
INTRODUCTION
Concrete and cement mortar are fundamental building materials that plays a vital role in infrastructure development. At present no construction activity is possible without using concrete. The main reason behind this is because of its high strength, durability and workability. The construction industry is reliance on cement as a primary component of concrete, presents significant environment and economic challenges.
The energy intensive production of cement contributes substantially to greenhouse gas emissions, while the depletion of natural resources exacerbates the need for sustainable alternatives. Concrete manufacture is responsible for 8.0% of global carbon emissions [1]. Global demand for cement is expected to increase 48% from 4.2bn to 6.2bn tons by 2050. Incorporating waste materials into concrete offers a promising avenue to mitigate these issues. Previous research has explored the potential of various waste materials such as (Fly ash, Cement dust and Silica fume) as partial replacements for cement [1]. This study seeks to produce low-cost concrete with enhanced performance, reducing the consumption of raw materials and reducing the hazards of waste materials. The work focuses on the possibility of using fly ash and cement dust in concrete and studying their effect on its properties. Yasir M. Alharthi et al. investigated the potential benefits of replacing part of the cement with CKD in two construction applications,
i.e., plain concrete and cement blocks.
An experimental program was carried out to study how replacing various percentages of Ordinary Portland Cement (OPC) with CKD affected the compressive strengths, the tensile strengths, and the air contents of concrete and cement blocks. Although the results showed that the compressive and tensile strengths decreased as the amount of CKD increased, regarding there was no significant difference between 0% and 5% CKD, which was only approximately 3%. In the concrete mix, the percentage of air content from 0% to 5% CKD replacements made no difference; however, when CKD was increased to 10%, 15%, and 20%, it increased by 24%, 33%, and 43%, respectively. The percentage of water absorption due to partial replacement by CKD in cement blocks can be increased up to 25% within the allowed limits [2].
A. Venkateswara Rao and K. Srinivasa Rao, they founded that the experimental results on stress strain behavior revealed that the replacing cement with fly ash between 30% and 50%, compared withthose of control Concrete, the concrete with 30% fly ash has more peak stress value, ductility decreased, and stiffness was decreased. It is concluded that replacement of cement with 30% fly ash in regular works can be recommended and where strength is of minor importance cement can be replaced with either 40% fly ash or 50% fly ash based on the strength Requirements [3]. M. A. Daous utilized cement kiln dust
and fly ash as waste materials blended with ordinary Portland cement at various ratios. These blends were tested for their water requirements for normal consistency, initial setting times, and compression and tensile strengths, and were compared to those of Portland cement. Test results show that Mortars of satisfactory mechanical strength can still be produced using Blends containing 90% Portland cement but not more than 4% fly ash as Blended waste material and blends containing as low as 70% Portland cement can still exhibit Adequate strength if only CKD is used as theblending waste material [4].
-
WASTE MATERIALS (CEMENT DUST & FLY ASH):
The incorporation of cement dust and fly ash into concrete mixes as partial replacement for cement offers significant performance and sustainability benefits. It is possible to develop durable, strong and environmentally friendly concrete by carefully evaluating their properties and optimizing their use. The use of these waste materials represents a major advance towards a more sustainable and resource-efficient construction industry.
-
Cement dust:
-
Origin: Produced during the grinding of cement clinker, it is a by-product of the cement manufacturing process.
-
Properties: Fine-grained powdered material with cementitious properties.
-
Benefits: Improves workability and cohesion of concrete mixes, reduces carbon footprint due to its use as a waste material, and enhances durability, cracking and weathering resistance.
-
Challenges: Possibility of segregation during mixing, which can affect the homogeneity of concrete and careful consideration of the water-cement ratio to maintain adequate workability and strength.
-
-
Fly ash:
-
Origin: A by-product of coal-fired power plants, collected from flue gas.
-
Properties: Fine-grained glassy material with pozzolanic properties, meaning it reacts with lime to form cementitious compounds.
-
Benefits: Improves the strength and durability of concrete, including resistance to sulphate attack, significantly reduces greenhouse gas emissions and conserves natural resources, and improves the workability and cohesion of concrete mixes.
-
Challenges: Variation in properties depending on source and production process, careful study of water-cement ratio and curing conditions to optimize its performance.
The fly ash and cement dust standard component as illustrated in Tables (I) & (II) contain some compounds that have an important effect on improving theproperties of concrete:
-
Silicon Dioxide (SiO2): Its increase the pozzolanic activity and leads to increased development of concrete strength anddurability.
-
Aluminum Oxide (Al2O3): Its increase the pozzolanic reaction of cement dust which may increase its ability to contribute tostrength development.
-
Loss on ignition (LOI): Reduce permeability and enhance workability of concrete.
-
Calcium oxide (CaO): Has potential pozzolanic properties and reflecting its primary role in cement hydration.
TABLE I The standard component of Fly ash.
COMPONENT
STANDARD RANGE (%)
Silicon Dioxide (SiO2)
30 50
Aluminum Oxide (Al2O3)
15 30
Iron Oxide (Fe2O3)
5 15
Calcium Oxide (CaO)
5 15
Magnesium Oxide (MgO)
1 5
Sulfate (SO3)
1 5
Loss on Ignition (LOI)
10 20
TABLE II The standard component of Cement dust.
COMPONENT
STANDARD RANGE (%)
Silicon Dioxide (SiO2)
20 25
Iron Oxide (Fe2O3)
1 5
Calcium Oxide (CaO)
45 55
Magnesium Oxide (MgO)
1 3
Sulfate (SO3)
2 5
Aluminum Oxide (Al2O3)
5 10
Loss on Ignition (LOI)
10 15
-
-
-
RESEACH METHODOLOGY
The study aims to investigate the use of waste materials in concrete manufacturing, focusing on factors such as availability and cost. And a systemic review was conducted to understand the current practices, limitations and future potential of using waste products in concrete. The study focused on two waste materials, fly ash and cement dust. These materials were selected based on their
potential to contribute to the development of sustainable concrete and the availability of research studies on their effect. Through conducted Specific laboratory tests on concrete samples containing these waste materials their properties and sustainability were evaluated. This study seeks to provide insights into the use of waste products in concrete manufacturing, and help stakeholders understand the benefits, challenges and potential applications of sustainable concrete.
-
Concrete Mix Design Using British Method( DOE Method ):
The DOE method is the method used in this study because it's popular way to design concrete mixes. It's easy to use, reliable, and helps make strong, durable concrete. Although there are other methods, but the British Method is often considered one of the best. This method was first published in 1975 and then revised in 1988, and it's applicable to concrete for most purposes, including roads. The following are the steps of DOE method:
Step 1: Find Target Mean Strength.
Step 2: Calculation of Water/Cement Ratio.Step 3: Calculation of free Water Content. Step 4: Calculation of Cement Content.
Step 5: Weight of Total Aggregate. Step 6: Trial Mixes and make.
Step 7: Adjust for concrete properties (density, shrinkage, strength, and durability) and for aggregate weight and water content.
-
-
EXPERIMENTAL WORKS
In this research the experimental work decidedto have three types of mixes:
-
Reference mortar mix.
-
Fly ash mortar mix.
-
Cement dust mortar mix.
-
Cement 500g.
-
Sand 1,375 g.
-
Water 310 g/cm3.
-
Fly ash & Cement motor mixes
These type of mortar mixes contains fly ash and cement replaced with different percentages.
-
-
First mix contains: 30% fly ash and 70%pure cement.
-
Second mix contains: 20% fly ash and80% pure cement.
-
Third mix contains: 10% fly ash and 90%pure cement.
-
Cement dust and Cement mortar mix:
These mixes contain cement mixed with cementdust with different percentages:
-
-
First mix contains: 30% cement dust and70% cement.
-
Second mix contains: 40% cement dustand 60% cement.
-
Third mix contains: 50% cement dust and50% cement.
-
Materials used:
The materials used in the tests are:
-
Portland cement (Class 42.5 N/mm2).
-
Cement dust, [see Fig (1)].
-
Fly ash, [see Fig (2)].
-
Coarse sand (Size about 0.05 mm and1,375 g).
-
Water (310 ml).
-
Reference Mortar Mix:
This mix is standard mix which contains no replacement or waste materials (pure cement mix) and the constituents of this mortar mix are:
Fig. (1): Cement dust.
-
-
-
The used Equipment:
Fig. (2): Fly ash.
The equipment used are:
-
Sieve analysis, [see Fig (3-a)].
-
Mixing plate, [see Fig (3-b)].
-
Mixing tools (Mixing trowel), [see Fig (3-c)].
-
Water beaker, [see Fig (3-d)].
-
Tamping rod (steel), [see Fig (3-e)].
-
Cube molds, [see Fig (3-f)].
-
Digital balance, [see Fig (3-g)].
-
Compressive strength machine (A & B), [see Fig (3-h)].
(a) Sieve analysis (b) Mixing plate. (c) Mixing trowel. tools for coarse fine.
(d) Water beaker. (e) Tamping rod. (f) Cube moulds.
(g) : Digital balance.
(A)
(B)
(h) : Compressive strength crush machine (A) & (B).
Fig. (3): The Used Equipment in Laboratory.
-
-
Test preparation:
-
Material Preparation: After carefully measuring the required
materials, they were mixed well in impermeable plate to ensure uniform consistency.
-
Mold Preparation: The mold was cleaned and lubricated to facilitate easy removal ofhardened concrete cubes.
-
Stacking and Compaction: The mortar was poured into the mold in two layers, each ofwhich was firmly compacted with a iron rode 35 times to eliminate air voids.
-
Finishing: The surface of the mold was smoothed using a trowel to ensure a clean and even finish.
-
Curing of cubes: After mixing the materials, the samples were stored in a moist air for 24 hours. Then they were removed from the molds, numbered, weighed and submerged in clean water until testing. These samples were cured for 7 and 28 days to evaluate their strength.
-
-
Comperessive Strength Test:
Compressive strength test is for assessing the mechanical performance of materials, understanding their response to pressure, andcomparing their relative strengths to determine optimal mixture.
-
Test procedure:
-
The samples were removedfrom the water after a specified curing period and excess water was wiped from their surfaces.
-
The samples were then weighed to determine their mass.
-
The compressive testing machines bearing surface was cleaned to ensure accurate results.
-
The sample was carefully placed in thecenter of the machine so that the load would be applied gradually and evenly until the samples failure.
-
The maximum load was recorded, and anyunusual features of the failure were noted.
-
Chemical Analysis for The Used Waste Marterials:
-
Chemical composition analysis facilitates comparison of measured chemical composition datafrom fly ash and cement
dust samples with established standards. A sample of fly ash was taken from the Gari Thermal Power Plant [Sudan Khartoum North] and a sample of cement dust was collected from Elnazir Contracting Company and tested at the Chemical Laboratory of Industrial Research and Consulting [Sudan Khartoum North]. The analysis enables identification of significant deviations in chemical composition and their possible implications for concrete properties.
-
-
RESULTS AND DISCUSSION
-
Chemical test results of Fly ash:
The results are shown in Table (III).
TABLE III Chemical test results of Fly ash.
COMPONENT
FLY ASH (%)
Silicon Dioxide (SiO2)
4.99
Aluminum Oxide (Al2O3)
16.30
Iron Oxide (Fe2O3)
23.69
Calcium Oxide (CaO)
10.41
Magnesium Oxide (MgO)
1.53
Sulfate (SO3)
6.30
Loss on Ignition (LOI)
36.78
DISCUSSION
-
Silicon Dioxide (SiO2): The significantly lower SiO2 content compared to the standard range may lead to reduced pozzolanic activity and potentially decreased strength development in concrete.
-
Iron Oxide (Fe2O3): The elevated Fe2O3 content could contribute to color variations and potential staining in the concrete, particularly if used in exposed areas.
-
Loss on Ignition (LOI): The significantly higher LOI suggests the presence of a substantial amount of unburned carbon or other organic matter, which may negatively impact the setting time, strength, and durability of the concrete.
-
-
Chemical Test results of Cement dust: The results are shown in Table (IV).
TABLE IV Chemical test results of Cement dust.
COMPONENT
FLY ASH (%)
Silicon Dioxide (SiO2)
11.00
Iron Oxide (Fe2O3)
2.25
Calcium Oxide (CaO)
46.50
Magnesium Oxide (MgO)
1.40
Sulfate (SO3)
4.70
Sodium Oxide (Na2O)
2.85
Potassium Oxide (K2O)
2.10
Aluminum Oxide (Al2O3)
3.60
Chloride (Cl-)
4.20
Loss on Ignition (LOI)
14.00
DISCUSSION
-
Silicon Dioxide (SiO2): The lower SiO2 content compared to the standard range could result in reduced strength development and durability of the concrete.
-
Aluminum Oxide (Al2O3): The lower Al2O3 content may limit the pozzolanic reactivity of the cement dust, potentially affecting its ability to contribute to strength development.
-
-
Compressive Strength Test:
To validate each models predictive capability, experimental compressive strength testing results were measured for mortar cubes at times ranging from 7 to 28 days. The average value of the results was taken for all mixes which included reference mix are shown in Table (V), fly ash mixes and cement dust mixes are shown in Tables (VI) and(VII).
TABLE V Standard Reference mix.
No.
Reference mix
Cube weight (g)
Density (g/cm3)
W/C (%)
Compressive Strength 7days (kN)
Compressive Strength 28 days (kN)
1
100% Cement
260
2.175
0.7
19.29
22.81
TABLE VI Fly ash Mix Results.
No.
Mix design
Cube weight (g)
Density (g/cm3)
W/C %
Compressive Strength 7days (kN)
Compressive Strength 28 days (kN)
1
10% FA
90% C
261
2.07
1
0.27
0.28
2
20% FA
80% C
259
2.08
1
0.23
0.226
3
30% FA
70% C
0
0
0
0
0
TABLE VII Cement dust Mix Results.
No.
Mix design
Cube Weight (g)
Density (g/cm3)
W/C %
Compressive Strength 7days (kN)
Compressive Strength 28 days (kN)
1
10% CD
90% C
260
2.08
0.69
15.11
21.42
2
20% CD
80% C
259
2.072
0.775
14.14
20.04
3
30% CD
70% C
261
2.186
0.88
18.19
27.47
4
40% CD
60 % C
260
2.163
0.96
16.75
24.176
5
50% CD
50 % C
262
2.165
1
18.11
23.52
-
FLy Ash Mixes Results Discussion:
The results of compression tests from Table (4) are shown in Fig (4), 3 samples of fly ash were tested with parentages gradually (10%, 20% and 30%), There is no heat emission observed during the mixing process, which is mainly due to unburnt carbonic particles (loss of ignition) as it reduces the hydration reaction process that leads to decrease the ultimate compressive strength of the flyash.
.
27.47
24.176
23.52
22.81
21.42
20.04
19.29
18.11
18.19
16.75
15.11
14.14
10% 30% 40% 50% STANDARD CEMENT CEMENT CEMENT CEMENT CEMENT MIX
DUST DUST DUST DUST DUST
Strength in 7days (KN/m2) Strength in 28days (KN/m2)
22.81
19.29
0 0 0.23 0.226 0.27 0.28
30% FLY ASH 20% FLY ASH 10% FLY ASH STANDARD MIX
Strength in 7days (KN/m2) Strength in 28days (KN/m2)
Fig. (4): Compressive Strength for Fly ash Mix
From the test results, 30% sample of fly ash mix was melted during the curing process. While the 10% & 20% gave weak result after 28 days, that mainly dueto high parentage of loss of ignition (L.O.I).
As cement replacement arentages increases in the mix, the compressive strength of the mortar decreased due to the following reasons:
-
The low present of chemical components in the sample in comparison to the standards ratio of these components in each fly ash sample, 6 out of 9 chemical components were just presented in the tested sample.
-
The source of sample has great effect on the compressive strength development, since the sample was taken from (Electroplating/Gari Thermal power plant)and this sample of fly ash has some percentage of oils in its components and this oil acted as additive which prevented the cohesion between the fly ash and cement.
-
Low percentage of Silica dioxide compared to the standard composition and high percentage of Iron oxide as one of the reasons of getting low compressivestrength.
-
-
Cement Dust Mixes Results Discussion:
The compressive strength test results from Table (5) are shown in Fig (5), 5 samples of cement dust were tested with percentages gradually (10%, 20%, 30%, 40% and
50%).
Fig. (5): Compressive Strength for Cement dust Mix.
For 10% sample the compressive strength at 28 days was near to compressive result of the standard reference mix (S.R.M), since the cement amount is close to the cement that founded in the S.R.M. while the 20% compressive strength result reduced by12.14% from the S.R.M.
And 30% sample gave the best compressive strength result that increased by 20.43% of the S.R.M, which is the optimum mix percentage as shown in Fig. (5).
For 40% and 50% samples their compressive strength results started to reduce due to the high- water cement ratio W/C, that leads to increase workability of the mortar which resulted in reduction of the compressive strength.
One more reason of the reduction of the compressivefor the 40% 50% samples because of low percentage of CaO% in the samples tested in comparison to the standard test chemical component of the cement dust.
-
Optimum mix:
The results indicate that 30% cement dust replacement achieved optimum compressive strength as shown in Fig (6), significantly outperforming the reference mix by 20.43%, with the potential to reduce overall production costs by more than 30%.
-
-
CONCLUSTION AND RECOMMENDATIONS
-
Waste materials potential: The study proves the potential of utilizing waste materials (Cement dust and Fly ash) as partial replacement for cement in concrete.
-
Cement dust successful: A 30% replacement level yielded optimal compressive strength, surpassing
the standard reference mix.
-
Fly ash challenges: While fly ash demonstrated potential, its effectiveness was influenced by factors such as loss on ignition (LOI) and a nonlinear relationship between replacement percentage andconcrete strength.
-
Recommendations for fly ash: Future research should focus on understanding nonlinear relationship between fly ash percentage and concrete strength, developing models to predict long term strength gain and prioritizing fly ashsamples with lower LOI.
-
Enhancing fly ash performance: To improve the performance of fly ash with high LOI, incorporating lime and silica could be explored.
-
Broader fly ash investigation: A comprehensive understanding of fly ashs suitability for concrete can be achieved by examining different types and sources of fly ash.
-
Waste reducing and management: Addressing the root cause of waste generation is crucial. Technological advancements, increased awareness and the implementation of sustainable practicesare essential for minimizing waste production.
-
Diversifying fly ash applications: Exploring the potential of fly ash in other applications such as (ceramic pastes, geopolymer cement and roads construction) can maximize its value and environmental benefits.
-
Optimizing fly ash production: Reducing LOI in fly ash production through increased burning rates is essential for enhancing its performance in concrete works.
-
Industry-wide impact: By implementing these recommendations, the construction industry can significantly reduce its environmental impact, conserve resources and achieve cost- effective concreteproduction through the innovative use of waste materials.
-
REFERENCES
-
Mission Possible Partnership, Making net-zero concrete and cement possible, (2023).
-
Yasir M. Alharthi, Ahmed S. Elamary, Waleed Abo-El-Wafa, Performance of plain concrete and cement blocks with cement partially replaced by cement kiln dust, (2021).
-
A. Venkateswara Rao and K. Srinivasa Rao, Effect of fly ash on strength of concrete, (2020).
-
M. A. Daous, Utilization of cement kiln dust and fly ash in cement blends in Saudi Arabia, (2004).
Compressive Strength Result at 28 days
27.47
24.21
23.52
21.42
22.81
20.04
10%
20%
30%
40%
50%
STANDARD MIX
REPLACEMENT MIX%
Fig. (6): Optimum mix % for the cement dust.