
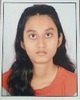
- Open Access
- Authors : Patel Kinjal Rajeshbhai, Prof. Hinal Surati
- Paper ID : IJERTV14IS030133
- Volume & Issue : Volume 14, Issue 03 (March 2025)
- Published (First Online): 27-03-2025
- ISSN (Online) : 2278-0181
- Publisher Name : IJERT
- License:
This work is licensed under a Creative Commons Attribution 4.0 International License
A Comparative Study of Controlling Method for Buck-Boost Converter using PID Controller and Artificial Neural Network
Patel Kinjal Rajeshbhai, Prof. Hinal Surati
Department of Electrical Engineering Uka Tarsadia University
Bardoli, Surat
Abstract This study compares PID and Artificial Neural Network (ANN) control methods for a buck-boost converter. PID offers simplicity and robustness, while ANN adapts to nonlinearities for improved performance. The Simulation is performed in MATLAB. Results highlight ANNs advantages in dynamic adaptability over traditional PID control.
KeywordsBuck-Boost Converter (BBC), PID Controller, Artificial Neural Network (ANN), Control Methods, Efficiency, Adaptive Control.
- INTRODUCTION
Power converters play a crucial role in power electronics, particularly in renewable energy applications. The buck- boost converter is widely used due to its ability to step up or down the voltage as required. Traditional control techniques like PID controllers offer robustness but struggle with nonlinear dynamics. In contrast, Artificial Neural Networks (ANN) provide adaptability and improved performance in varying conditions. This study compares these two control strategies to determine their effectiveness.
- Understanding Converter Problems
Buck-Boost converters often face the following issues:
- Control Requirements
- Fluctuation in input parameters can lead to significant variation in output.
- Renewable inputs can introduce high overshoot and settling time issues.
- Reduced Efficiency at extreme Duty Cycles
- Maintaining Stable operation at extreme duty cycles requires control methods.
- Control Requirements
- Objective.
The objective of this paper is:
-
- To analyze and compare the performance of PID and ANN controllers in regulating output voltage.
- To evaluate the transient response, efficiency, and stability of both control methods under varying input conditions.
- To highlight how ANN can improve performance compared to conventional PID control.
-
- Understanding Converter Problems
- ARCHITECTURE
-
-
-
- PID Controller
Fig 1: Buck-Boost Converter Circuit Diagram
A PID (Proportional-Integral-Derivative) controller used with a buck-boost converter is a widely utilized configuration in power electronics to maintain a stable output voltage. The main elements include a DC voltage source here it is a PV array, a switching element IGBT, an inductor, capacitors, a diode, and a load resistor. The switching element is controlled by a PWM (Pulse Width Modulation) signal generated by the PID controller.
Fig 2: Block Diagram of BBC with PID control
The working principle of the buck-boost converter is straightforward. It operates in two distinct modes: buck mode and boost mode. In buck mode, the converter steps down the voltage when the input voltage is higher than the desired output voltage. And, in boost mode, the converter steps up the voltage when the input voltage is lower than the desired output voltage. This dual capability makes it versatile for various applications.
The PID controller plays a crucial role in regulating the output voltage by continuously adjusting the duty cycle of the PWM signal. It does this by minimizing the error between the actual output voltage and the reference voltage. The PID controller achieves this by processing the error through its proportional, integral, and derivative components, which collectively generate the control signal.
The control loop in this setup involves several steps. First, the output voltage is continuously monitored and fed back to the PID controller. The controller then calculates the error by comparing the actual output voltage with the reference voltage. The PID processes this error to generate a control signal that adjusts the duty cycle of the PWM signal. This PWM signal, in turn, controls the switching element, ensuring the desired output voltage is maintained.
- ANN Controller
An Artificial Neural Network (ANN) controller in a buck- boost converter offers a better approach to voltage regulation in power electronics. This system integrates several key components, such as a DC voltage source here it is a PV array, a switching element IGBT, an inductor, capacitors, a diode, and a load resistor. The switching element is driven by a PWM (Pulse Width Modulation) signal that is generated by the ANN controller. The buck-boost converter operates in two modes: buck mode, and boost mode.
The ANN controller continuously adjusts the duty cycle of the PWM signal to maintain the target output voltage, learning from the system’s behavior and predicting necessary adjustments. This dynamic control is facilitated by a feedback loop where the output voltage is constantly monitored and fed back to the ANN controller. The controller calculates the error by comparing the actual output voltage with the reference voltage, processes this error through its neural network, and generates a control signal that modifies the PWM duty cycle, thereby controlling the switching element.
Fig 3: Block diagram of BBC with ANN control
- Back Propagation
Back Propagation is used for training ANN. The proposed algorithm has two hidden layers. The first layer consists of 10 neurons and the other has 5 neurons. Backpropagation consists of two main phases: Forward and Backward.
Fig 4: Block diagram of Neural Network
- Forward Pass
- The input data flows through each layer of the network sequentially.
- Each neuron uses an activation function (tansig, sigmoid) to decide whether the signal should proceed to the next layer.
- The network generates an output, which is compared to the actual target to calculate the loss.
- Backward Pass
- Starting from the output layer, the error signal is propagated back through the network to update weights and biases. This involves:
- The weights and biases are adjusted in the direction that minimizes the loss. This is done using an optimization algorithm.
- Iterative Training
This forward-backward cycle is repeated for multiple epochs (iterations over the dataset). Overtime:
- The network learns to reduce the error and improve its predictions.
- Weights converge to values that enable the model to recognize patterns in the data.
- Forward Pass
- PID Controller
-
-
Published by : http://www.ijert.org
-
- SIMULATION
International Journal of Engineering Research & Technology (IJERT)
ISSN: 2278-0181
Sr. No. Components Ratings 1 Input Voltage 30 V 2 Power 250 W 3 PWM frequency 10 kHz 4 Inductnce 0.116 H 5 Capacitance 0.0039 F 6 Resistive Load 10 Ohm 7 Reference Voltage -12 V Vol. 14 Issue 03, March-2025
The simulation models a PV Array-based buck-boost converter designed to regulate an output voltage of -12V with a Pulse Width Modulation frequency of 10 kHz. The PV Array serves as the input source, the converter consists of an inductor, and two capacitors, which help smooth current and voltage fluctuations. A 5-ohm resistive load is incorporated into the circuit. The power output is 250W, with stable operation under given load conditions. The control strategy adjusts the duty cycle of the PWM signal to maintain the desired output voltage efficiently. The simulation evaluates the converters performance in terms of voltage regulation, efficiency, and transient response under varying solar conditions.
Fig 5: Buck-Boost Converter Simulation with PID control
The ANN controller dynamically adjusts the duty cycle for precise voltage regulation and enhances system stability, transient response, and efficiency under varying solar conditions.
Fig 6: Buck-Boost Converter Simulation with ANN control
Fig 7: Feed Forward Neural Network
The above diagram of a neural network consists of two hidden layers. The DC-DC converter in Simulink uses the ideal components without parasitic elements. The components and parameters used in the converter are listed below:
Table 1: Simulation Parameters
- Output Waveforms
Fig 8: (a) Output voltage, current, and power response with time, of ANN and PID controllers in (a), (b), and (c) respectively.
Published by :
http://www.ijert.org
- Observation
It is observed that the output voltage, current, and power responses of an ANN-controlled system are better than a PID- controlled system in terms of transient performance. In all the responses, the PID controller exhibits an overshoot and a longer settling time, whereas the ANN controller demonstrates a lower overshoot and faster stabilization. In the ANN controller, the steady-state reaches more quickly than the PID controller. Overall, the ANN-based control method provides superior transient performance by reducing overshoot, shortening the settling time, and improving stability. In contrast, the PID controller, while eventually reaching the same steady-state values, suffers from higher oscillations and slower convergence. These results suggest that ANN control is a more effective approach for ensuring a stable and rapid response in the buck-boost converter system. ANN controller achieves a faster settling time of 0.6 sec compared to PID with 1.5 sec. ANN has a smoother and faster
International Journal of Engineering Research & Technology (IJERT)
ISSN: 2278-0181
Vol. 14 Issue 03, March-2025
- Nik Fasdi Nik Ismail, Norazlan Hashim, Rahimi Baharom A comparative study of Proportional Integral Derivative Controller and Fuzzy Logic Controller on DC/DC Buck-Boost Converter (2011).
- Krishnapriya, Shashidhar Kasthala- A Comparative Analysis on Different Control Techniques for Buck Converter (2016).
- Filza Ahsan, Prof. Avinash Kumar Dewangan, Dr. Ritesh Diwan- Modeling and Control of a Buck DC-DC Converter Based on Artificial Neural Network (2024).
- Sepehr Saadatmand, Pourya Shamsi, and Mehdi Ferdowsi- The Voltage Regulation of a Buck Converter Using a Neural Network Predictive Controller (2020).
transient response. Here the overshoot is almost the same with minor differences but with the varying solar conditions, ANN has the adaptability to perform better.
- Output Waveforms
- CONCLUSION AND FUTURE SCOPE
Analyzed the performance of both control strategies, the PID controller, known for its simplicity and ease of implementation, demonstrated satisfactory performance in terms of stability and response time. However, it exhibited limitations in handling non-linearities and parameter variations in the system. On the other hand, the ANN-based controller showcased superior adaptability and robustness. It effectively managed the non-linear behavior of the Buck- Boost Converter and provided a faster response. The ANN controller’s ability to learn and adapt to changing system dynamics resulted in improved performance compared to the traditional PID controller. In conclusion, while the PID controller remains a viable option for controlling Buck-Boost Converters, the ANN-based controller offers significant advantages in terms of adaptability, robustness, and overall performance. Future scope can focus on exploring hybrid strategies that combine PID controllers with advanced methods like ANN, fuzzy logic, or model predictive control could enhance the strengths of each approach. Validating these strategies on actual hardware, improving energy efficiency, and creating fault-tolerant algorithms are also crucial areas for future research.
- REFERENCES
- Jazmin Ramirez-Hernandez, Oswaldo-Ulises Jaurez-Sandoval, Leobardo Hernandez-Gonzalez, Abigail Hernandez-Ramirez, Raul-Sebastian Olivares-Dominguez- Voltage Control Based on a Back Propagation Artificial Neural Network Algorithm (2020).
- Omar Kamrul Islam, Md. Sabbir Ahmedy, Khalilur Rahmanz, Tasnia Tahsin- A Comprehensive Comparison Between Boost and Buck-Boost Converters in Solar MPPT With ANN (2020).
- Saleh Elkelani Babaa Novel Switch Adaptive Control to Improve the Efficiency of Boost Converter in Photovoltaic
Systems (2017).
- S. Vijayalakshmi, E. Arthika, G. Shanmuga Priya Modeling and Simulation of Interleaved Buck-Boost Converter with PID Controller (2015).
- Moirangthem Dennis Singh, Shine V J, Varaprasad Janamala Application of Artificial Neural Networks in Optimizing MPPT Control for Standalone Solar PV System (2014).