
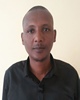
- Open Access
- Authors : Jaleta Sori , Edosa Ketema
- Paper ID : IJERTV11IS010144
- Volume & Issue : Volume 11, Issue 01 (January 2022)
- Published (First Online): 09-02-2022
- ISSN (Online) : 2278-0181
- Publisher Name : IJERT
- License:
This work is licensed under a Creative Commons Attribution 4.0 International License
A Composite Propeller Shaft Analysis Using Ansys Software
Jaleta Sori
Department of Mechanical Engineering, College of Engineering and Technology, Wollega University, Nekemte,
Ethiopia.
Edosa Ketema Department of Mechanical Engineering, College of Engineering and Technology,
Wollega University, Nekemte, Ethiopia.
Abstract:- In the automobile, one of the most significant components is the drive shaft, which transmits power from the engine to the rear wheels via the differential gear. Steel drive shafts are often utilized in the vehicle industry; however, composite drive shafts are increasingly being employed to replace steel drive shafts. The purpose of this article is to investigate a composite propeller shaft. The use of composite materials instead of traditional steel materials for drive shafts has increased the design benefits due to their high specific stiffness, strength, and possible life with a high critical speed. The design parameters are scrutinized with the goal of reducing the weight of the composite drive shaft. The concept demonstrates a considerable potential increase in propeller shaft performance. Pro/E is used to create the propeller shaft model. FEA analysis is successfully completed using ANSYS 11.0 Multiphysics. The FEA findings are utilized to calculate deflection, stresses, and natural frequencies under applied loads. A further comparison of steel and composite materials will be performed to examine the torsion, buckling, and bending natural frequency weight savings of the propeller shaft.
Keywords Composite Propeller Shaft, Weight, Design, Deflection, Stress, Natural frequencies.
-
INTRODUCTION
The term propeller shaft refers to the mechanism utilized to transmit motion from one place to another. Propellers are commonly linked with ships and planes because they are driven in the water or air by a propeller fan. The drive shaft of a car, on the other hand, is also known as the propeller shaft because, in addition to delivering rotational motion from the engine to the back end of the vehicle, these shafts also push the vehicle forward. The shaft is the fundamental link between the front and rear ends (engine and differential), and it is responsible for both conveying motion and pushing the front end. As a result, the phrases driving shaft and propeller shaft are interchangeable. A propeller shaft, in other terms, is a longitudinal drive shaft used in vehicles when the engine is located at the opposite end of the vehicle from the driving wheels. A propeller shaft is a grouping of one or more tube shafts joined together by universal, constant velocity, or flexible joints. The number of tubular parts and joints required is determined by the distance between the gearbox and the axle. As with rear-wheel drive, some four-wheel drive vehicles employ one propeller shaft to power the back wheels and a second propeller shaft to power the front wheels. In this situation, one of the most significant components is the second propeller shaft, which is responsible for the actual motions of the vehicle after motion is created in the engine. The design of such important components is often strict, as a fracture in this
element might result in a catastrophic failure of the vehicle while it is in motion. Torque generated by the engine and
Figure. 1. Schematic arrangement of an Automobile.
Figure. 2. Schematic arrangement of a Propeller Joint
gear box must be transmitted to the rear wheels in order for the vehicle to go forward and reverse. The drive shaft must deliver a constant, steady transfer of power to the axles. This torque is transferred via the drive shaft and differential. It is responsible for transmitting torque from the gearbox to the differential gear box. The drive shaft must also be capable of turning at the vehicle's needed high speed. The driveshaft must also be able to work by continually adjusting the angles between the transmission, differential, and axels.A driveshaft is a spinning shaft that distributes power from the engine to a rear wheel drive vehicle's differential gear. The driveshaft must work through continually changing angles between the transmission and axle. Steel of high grade is a frequent building material. Because the bending natural frequency of a shaft is inversely related to the square of beam length and proportionate to the square root of specific modulus, steel drive shafts are often constructed in two parts to raise the fundamental bending natural frequency. The two-piece steel
drive shaft is made up of three universal joints, a central supporting bearing, and a bracket, all of which add to the overall weight of the vehicle. Power transmission can be enhanced by lowering inertial mass and reducing weight. Because composite materials have better particular stiffness and specific strength, substituting composite structures for conventional metallic structures offers various advantages.
The maximum torsion capacity of a hybrid aluminum/composite shaft is investigated in this research for various winding angles, layer counts, and stacking sequences. The hybrid shaft was analysed using the finite element method under static torsion. The numerical study for the hybrid shaft was carried out using ANSYS finite element software. The results reveal that modifying the winding angle, stacking sequences, and number of layers has a substantial effect on static torque capacity. At a winding angle of 45o, the highest static torsion capacity of an aluminum tube coiled outside by six layers of carbon fiber/epoxy composite was 295 Nm Mutasher (2009) [1]. Ummuhaani and Sadagopan (2011) [2] discuss the replacement of a standard steel drive shaft in a Maruti Omni 5 passenger vehicle with an EGlass/ Epoxy composite drive shaft. The design parameters were chosen with the goal of reducing the weight of the composite propeller shaft, and the shaft was analysed utilizing ANSYS
11. The displacement obtained when the maximum torque is applied is 0.54E-03 m. In the identical conditions, the greatest shear stress obtained is 8.54 MPa. Rao et al. (2012) [3] use ANSYS software to calculate harmonic analysis on a propeller made of a metal composite material, in order to examine its displacements and natural frequencies. CATIA V5R17 was used to create the propeller model. According to the findings of the harmonic analysis, the composite propeller is secure against the phenomena of resonance, and efforts are being made to lower the frequency of the composite propeller so that the benefit of weight reduction may be gained. Kim et al. (2013) [4] used aluminum, carbon fiber composite material, and glass fiber composite material to create a one-piece hybrid propeller shaft. The adhesive strength of the hybrid propeller shaft in relation to the roughness of the aluminum surface was investigated. The one-piece hybrid propeller shaft was manufactured to meet propeller shaft performance parameters such as statistic torsion torque strength and first bending natural frequency. The vibration characteristics of the hybrid shaft are 237Hz, which is much greater than the conventional vibration characteristics of the present two-piece steel construction propeller shaft, which are 150Hz.
Ravi (2014) [5] Solidworks is used to create the 3D model of the Propeller Shaft, which allows for design automation and product development. FEA is used to optimize the model. The high-strength carbon composite drive shafts were created to replace an automobile's steel drive shaft. According to the results, the weight reduction of the HS Carbon is 24 percent when compared to the same dimensions of steel shaft. With th aid of modeling tools, the structural design parameters were improved with the goal of reducing the weight of the composite drive shaft. The design optimization also revealed a considerable potential increase in propeller shaft performance. The CATIA/ANSYS software was used to model and analyze the drive shaft assembly. The propeller shaft is made of glass fiber reinforced polymer with silicon carbide. Finally, the
findings of the investigation were compared to those of a standard steel drive shaft Ramesh and Sangeethkumar (2015) [6]. This paper investigates the composite hollow shafts built of Carbon Reinforced Plastics (CFRP) and Glass Fiber Reinforced Plastics (GFRP) for automobile applications. Failure analysis was performed utilizing maximum stress criteria, and it was discovered that the failure torque is significantly more than the design torque level. The propeller shaft was studied utilizing FEM methods for an accurate design solution (ANSYS package). FEM "3D-shell99 element and solid46 layered element" was used to simulate the propeller shaft. All failure modes were investigated, as well as linear static analysis, vibration Eigen value analysis, buckling analysis, and harmonic analysis Rao (2016) [7]. High Strength Carbon composite drive shafts have been created in this effort to replace an automobile's steel drive shaft. Using FEA, an attempt was made to determine deflection, stresses under applied loads, and natural frequencies. When compared to a traditional steel drive shaft, the use of composite materials resulted in significant weight savings ranging from 70% to 63%. Finally, the author compared boron to HS Carbon/Epoxy, the cost of composite material is low and best Mohan and Vinoth (2016) [8]. The author Karthikeyan et al (2017) [9] investigated composite drive shafts rather than conventional steel drive shafts by incorporating composite materials such as Kevlar/Epoxy and Glass/Epoxy as a composite material in order to increase specific strength, specific modulus, improved fatigue, corrosion resistances, and reduction in energy requirements due to weight reduction as compared to steel shaft. For ease of understanding, modeling is done with CATIA software and analysis is done with ANSYS 10.0 software. When compared to a typical steel drive shaft, the composite drive shaft saves weight by 81.67 percent for Kevlar/Epoxy and 72.66 percent for Glass/Epoxy. The authors Yeswanth and Andrews (2017) [10] primary goal is to reduce the weight of the drive shaft by replacing the current steel drive shaft with a composite material shaft made of High Modulus carbon/Epoxy or E glass polyester materials. CATIAV5R20 is used to generate a shaft model, and ANSYS
16 is utilized to forecast the outcomes. To compare the outcomes of steel and composite drive shafts, parametric optimization is performed by adjusting design variables such as inner diameter, outer diameter, and torque of the drive shaft, and the effects of change in design variables are compared. Using hydrodynamics and structural analysis, Chen et al (2017) [11] present a composite propeller blade to increase efficiency and to lower acoustic emission. For analysis, Finite Element (FE) software is employed, and ANSYS Fluent is used to model the hydrodynamics surrounding the propeller. The findings emphasize that increased MCP performance and discovered the morphing composite propeller arrangement has improved efficiency by 1.1% while boosting structural durability. Reddy and Nagaraju (2017) [12] investigated the design, material selection, optimum stacking sequence, and performance of composite drive shafts in order to compare the performance of composite drive shafts to steel drive shafts. The optimally designed drive shaft finite element model is created with the commercial finite element program ANSYS. Static, free vibration and tensile buckling analyses were performed, which are essential
for rotating parts such as drive shafts. Finally, it is found that across all evaluations, a weight reduction of 97% over steel drive shaft is attainable. The shaft was developed and analyzed using ANSYS ACP by the authors Naveen and Reddy (2018) [13]. The analysis was performed on four distinct materials, including traditional structural steel and three different composite materials. E glass/Epoxy, High Strength Carbon Epoxy (230GPA), and High Modulus Carbon Epoxy are all examples of carbon epoxies (395GPA). Based on the results, it is concluded that High strength carbon with reduced weight has a deformation of 7.37 mm, an elastic strain of 0.0058667 mm, and a von misses stress of 92.279 MPa at a frequency of (51.15, 306.22, 535.9, 801.27), which is superior to other composite materials and conventional structural steel. The general goal of this research is to examine a Metal-Composite shaft for marine propulsion systems that performs better under various stress circumstances than a typical metal/alloy shaft. When compared to conventional metal shafts, a combination of metal and composite material in a shafting system results in lower loads and fewer torsional vibrations, as well as reduced deformation over a longer duration. Furthermore, the use of composites in the shaft improves thermal stability. Under identical loading circumstances, comparisons were made between the conventional metal shaft and the metal-composite shaft utilizing ANSYS Workbench for simulation and results, and solid works for modeling Shah (2018) [14]. The lowering of the weight of the propeller shaft is a very desirable aim. As a result, we create composite drive shafts utilizing computer- aided graphic design softwares CATIA and HYPERMESH to design and evaluate composite shafts. The design parameters were improved to reduce the weight of the composite propeller shaft Sankar (2018) [15]. Mohanraj (2019) [16] analyzed a split type propeller shaft will be modelled first in Creo software, and then imported into ANSYS software for FE analysis. The propeller shaft design will next be revised and analyzed under the same material and boundary circumstances. This improved shaft will now be analyzed using composite materials under the same boundary conditions. In order to discover the ideal bonding angles, the layer wrapping angle between the layers will also be adjusted. In order to reduce the time required to pick the composite material and layer wrapping methods, a genetic algorithm will be used in this study. The findings will be compiled and compared in order to choose the best sample. Prakash and Arun (2019) [17] reviewed conventional steel shafts are manufactured in two sections to lower the bending natural frequency, however composite material drive shafts are produced in a single piece to reduce overall weight. Suresh et al (2021) [18] done a research work, the aforesaid characteristics of composite materials are used to fabricate the mechanical drive shaft using a composite combination of Eglass fiber CSM (0 percent, 10%, 20%, 30%, 40%, 50%) and IPN resins, and the shaft is experimentally tested using a torsional testing machine. A comparable shaft is modeled in CATIA V5, and numerical analysis is done in ANSYS to cross-check the experimental data. Finally, the optimal range for mixing E-glass fiber with IPN resins is identified. The drive shaft discussed here is used to transmit the required torque from the differential to the wheels. All the components
of the drive shaft were designed analytically, modeled in SolidWorks and analyzed using ANSYS software to ensure its safety. The main objective is to fabricate more reliable and eco- friendly drive shaft by minimizing the cost and increasing the overall performance Gowtham et al (2021) [19]. The researcher Choi et al ((2021) [20] used structural analysis and optimization to reduce the weight of a propeller shaft for a passenger automobile. Finite element analysis and testing were used to investigate the natural frequency and durability of the growing propeller shaft. The optimization process was then carried out by focusing on the weight reduction of the tubes manufactured of the provided steel material. The meta model-based optimization approach kriging interpolation was used in this procedure, and the weight was lowered by 5.3% on the propeller shaft and 14.1% on the tube. For structural analysis, ANSYS Workbench was utilized, an in-house tool was used to generate the kriging model, and MATLAB was used for optimization.
-
DESIGN OF STEEL PROPELLER SHAFT
Nowadays Steel (SM45C) is now utilized to manufacture vehicle drive shafts. Table 1 shows the steel (SM45C) material parameters. Three design characteristics must be met by the steel drive shaft: torque transmission capability, buckling torque capability, and bending natural frequency.
Table 1. Mechanical properties of steel (SM45C).
Sl.No
Mechanical Properties
Notations Used
Steel
1
Youngs modulus (GPa)
E
207.0
2
Shear modulus (GPa)
G
80.0
3
Poissons ratio
0.3
4
Density (Kg/m3)
7600
5
Yield strength (MPa)
Sy
370
6
Shear strength (MPa)
Ss
370
Table 2. Design Parameter of Steel propeller Shaft
Sl.No
Parameter of Shaft
Symbol
Value
Unit
1
Outer Diameter
do
90
mm
2
Inner Diameter
di
83.36
mm
3
Length of the Shaft
L
1250
mm
4
Thickness of shaft
T
3.32
mm
-
PROCEDURE FOR SHAFT MATERIAL SELECTION AND PROPOSED ANALYSIS
Because of their high specific strength and specific modulus, the composite materials such as "graphite, carbon, Kevlar, and Glass" with compatible resins are commonly employed. Composite materials appear to be an excellent choice for extended power driver shaft applications. The automobile industry is utilizing composite material technologies for the fabrication of structural components in order to reduce weight while maintaining vehicle quality and durability. It is well recognized that energy conservation is one of the most essential goals in vehicle design, and weight reduction is one of the most efficient ways to achieve this goal. The current work comprises an examination of the drive shaft using several composite materials and indicates that the
use of composite materials for the drive shaft will cause less stress, hence reducing the vehicle's weight. PRO-E 5.0 is used to build the propeller shaft model and (ANSYS) FEA program is utilized to evaluate the cad model with appropriate circumstances. Boron/Epoxy, Kevlar/Epoxy, and Carbon/Epoxy are the three composite materials chosen because of their high strength-to-weight ratio, high stiffness- to-weight ratio, high impact resistance, better fatigue resistance, improved corrosion resistance, and good thermal conductivity.
-
DESIGN OF PROPELLER SHAFT
study, finite element analysis was performed using the ANSYS program. The nodal solutions are used to determine the starting unknowns in this analysis. Figure 3 shows the model of propeller shaft and Figure 4 shows the image of a propeller shaft.
Mass of the steel drive shaft:
Where,
in kg (1)
=density of the drive shaft kg/m3: For steel =7600 kg/m3 A = Area of the drive shaft,
L = length of the drive shaft.
Figure 3. Model of propeller shaft
Where,
Do= outer diameter in (mm) DI= inner diameter in (mm).
in mm2 (2)
= /4(902-83.362)
= /4(8100-6948.8896)
= /4(1151.1104) A=903.621mm2
in mm2 (3)
Mass of shaft material = M=7.6E-9×903.621×1250 (4) m =8.58Kg
Torque transmission capacity of the Steel drive shaft
(5)
Where,
T=Torque of the shaft Nm Ss= Shear strength (MPa) Do= outer diameter in (mm) DI= inner diameter in (mm)
=760×e -6×0.19625× [(904-83.364) ×90]
T =55.93×103 Nm
Angular velocity of shaft:
Where,
N=Speed of the shaft in rpm.
=2××6500/60
=680.57rad/sec.
(6)
Figure 4. Image of a propeller shaft
-
MODELLING OF COMPOSITE SHAFT Torsion is applied to a layer of a structural shell model. At
each node, the element has six degrees of freedom: translations in the nodal x, y, and z directions, as well as rotations about the nodal x, y, and z axes. The shaft is fixed in axial, radial, and tangential directions at one end and subjected to torsion at the other. Shear stresses are computed after a static study of the shaft. The following are the analytical findings for Boron/Epoxy, Kevlar/Epoxy, and Carbon/Epoxy composite shafts. Figure 5 shows the meshing image of steel shaft.
-
STATIC ANALYSIS
A static analysis is used to estimate the displacements, stresses, strains, and forces induced by loads that do not create substantial inertia and damping effects in structures or components. A static analysis, on the other hand, can incorporate constant inertia loads such as gravity, spinning, and time variable loads. Loading and response conditions are
-
-
MODELLING OF SHAFT: FINITE ELEMENT ANALYSIS
Finite element analysis (FEA) is a computer-based numerical approach for evaluating engineering structures' torsion, buckling analysis and natural bending analysis. In this
assumed in static analysis, which means that the loads and structural reactions are considered to fluctuate slowly with respect to time. The following types of loading can be used in static analysis: External forces, moments, and pressures Gravity and spinning are examples of steady-state inertial
forces. Non-zero displacements were imposed. If the stress levels derived in this study exceed the permitted limits, the structure will fail in the future. Figure 6 shows the torsion analysis of steel shaft. Figure 7 shows the maximum principal
Figure 5. Meshing image of steel shaft
Figure 6. Torsion analysis of steel shaft
Figure 7. Maximum principal stress of steel
Figure 8. Maximum principal strain of steel shaft
Figure 9. Equivalent stress of steel shaft
Figure 10. Total buckling deformations of steel shaft.
stress of steel. Figure 8 shows the maximum principal strain of steel. Figure 9 shows the equivalent stress of steel shaft. Figure 10 shows the total buckling deformations of steel shaft.
-
CONCLUSION
In this study, a comparison of steel and composite drives shafts. Its design technique is investigated, and certain critical parameters are found using finite element analysis. The current effort intended to reduce the fuel consumption of vehicles in particular, or any machine that uses a drive shaft in general. The developed shafts fulfil the design standards for shaft design. Steel Shafts and Composite Shafts are developed to suit the design criteria. The theoretical shaft design values are virtually identical to the analytical shaft design values obtained using an analysis tool ANSYS. This was accomplished by using composite materials to reduce the weight of the driving shaft. The mechanical behaviours and qualities of existing propeller shafts are investigated. Carbon/Epoxy, Boron/Epoxy, and Kevlar/Epoxy fiber matrix materials are chosen, and their characteristics are investigated. ANSYS is used to evaluate mechanical behaviours such as torsion, buckling analysis, and natural bending analysis for existing propeller shafts (SM45C).
- REFERENCES
-
-
S.A. Mutasher, Prediction of the torsional strength of the hybrid aluminum/composite drive shaft, Materials & design, vol. 30, no. 2 pp. 215-220, 2009.
-
A.M.Ummuhaani and P. Sadagopan. Design, Fabrication and stress analysis of a composite propeller shaft, No. 2011-28-0013. SAE Technical Paper, 2011.
-
Rao, Y. Seetharama, and B. Sridhar Reddy. Harmonic analysis of composite propeller for marine applications, Int. J. of Research in Engg. and Tech , vol.1, no. 03, 257-60, 2012.
-
Kim, Hyun Sik, Dong Pyo Hong, and Hee Yong Kang, Design of the Hybrid-Propeller Shaft Using Composite Materials, In Applied Mechanics and Materials, Trans Tech Publications Ltd, vol. 284, pp. 687-691, 2013.
-
Ravi, Arun, Design, comparison and analysis of a composite drive shaft for an automobile, International Review of Applied Engineering Research, vol. 4, no. 1, 21-28, 2014.
-
N. Ramesh Babu and E. Sangeeth Kumar, Improving the Mechanical Properties of the Propeller Shaft by Using Composite Materials, In Applied Mechanics and Materials, Trans Tech Publications Ltd, vol. 813, pp. 1090-1097, 2015.
-
Rao, B. James Prasad, D. V. Srikanth, T. Suresh Kumar and L. Sreenivasa Rao, Design and analysis of automotive composite propeller shaft using fea, Materials Today: Proceedings, vol. 3, no. 10, 3673-3679, 2016.
-
S. Mohan and M. Vinoth, Design and analysis of composite drive shaft for automotive application, Middle-East Journal of Scientific Research Recent Innovations in Engineering Technology, Management & Applications, 2016.
-
P. Karthikeyan, R. Gobinath, L. Ajith Kumar and D. Xavier Jenish, Design and analysis of drive shaft using kevlar/epoxy and glass/epoxy as a composite material, In IOP Conference Series: Materials Science and Engineering, IOP Publishing, vol. 197, no. 1, p. 012048. 2017.
-
I.V.S.Yeswanth, and A. Abraham Eben Andrews, Parametric Optimization of Composite Drive Shaft Using ANSYS Workbench 14.0, Internaltional Journal of Mechanical Engineering and Technology,vol. 8, no. 5, pp.10-23, 2018.
-
Chen, Fanlong, Liwu Liu, Xin Lan, Qinyu Li, Jinsong Leng, and Yanju Liu, The study on the morphing composite propeller for marine vehicle. Part I: Design and numerical analysis, Composite structures, vol. 168 , pp. 746-757, 2017.
-
Reddy, P. Satheesh Kumar, and Ch Nagaraju, Weight optimization and finite element analysis of composite automotive drive shaft for maximum stiffness, Materials Today: Proceedings, vol. 4, no. 2, pp. 2390-2396, 2017.
-
P.N.E. Naveen and R. Bhaskara Reddy, An Analysis of Composite Drive Shaft using ANSYS ACP. International Journal of Mechanical and Production Engineering Research and Development, vol.8, Is. 5, pp. 117-124, 2018.
-
Shah, Kaushal Mayankkumar, Analysis and Comparison between A Conventional Metal and A Metal-Composite Marine Propeller Shaft, PhD diss, 2018.
-
V. Sankar, Analysis of Automotive Composite Propeller Shaft using Computer Aided Graphic Design, Taga Journal, vol. 14, pp. 1804- 1809, 2018,
-
K.S.Mohanraj, Design and analysis of composite drive shaft, Journal of Material Science & Manufacturing Technology, vol. 4, Is.1, pp. 11- 31, 2019.
-
Prakash, Ravi and Arun Patel, Review and Analysis of Various Composite Propeller Shaft, International Journal Online of Science, vol.. 5, Is. 4, 2019.
-
G. Suresh, T. Srinivasan, S. Stephen Bernard, S. Vivek, R. M. Akash,
G. Baradhan and B. Anand, Analyzing the mechanical behavior of IPN composite drive shaft with E-glass fiber reinforcement, Materials Today: Proceedings, vol. 45, pp. 1107-1111, 2021.
-
S. Gowtham, V. Raaghul, B. N. Sreeharan, RA Praveen Kumar and S. Mohamed Kasim, Drive Shaft Design and Analysis For Mini Baja, In IOP Conference Series: Materials Science and Engineering, IOP Publishing, vol. 1123, no. 1, p. 012015, 2021.
-
Choi, Ji-Won, Seung-Ho Han and Kwon-Hee Lee, Structural analysis and optimization of an automotive propeller shaft, Advances in Mechanical Engineering, vol. 13, no. 10, 16878140211053173, 2021.