
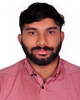
- Open Access
- Authors : Mr.Muhammed Aslam E. U, Mr. Riyas .P, Mr.Muhammed Afsal Pt, Mr.Nihal M Basheer, Mr.Afreed K
- Paper ID : IJERTV14IS030085
- Volume & Issue : Volume 14, Issue 03 (March 2025)
- Published (First Online): 22-03-2025
- ISSN (Online) : 2278-0181
- Publisher Name : IJERT
- License:
This work is licensed under a Creative Commons Attribution 4.0 International License
A Drone Technology Implementation Approach to Conventional Paddy Fields Application
Published by : http://www.ijert.org
International Journal of Engineering Research & Technology (IJERT)
ISSN: 2278-0181
Vol. 14 Issue 03, March-2025
Mr.MUHAMMED ASLAM E. U
Assistant Professor
Dept of Electrical and Electronics Engineering
MEA Engineering College Perinthalmanna, India
Mr. RIYAS .P
Assistant Professor
Dept of Electrical and Electronics Engineering
MEA Engineering College Perinthalmanna, India
Mr.MUHAMMED AFSAL PT
Dept of Electrical and Electronics Engineering
MEA Engineering College Perinthalmanna, India
Mr.NIHAL M BASHEER
Dept of Electrical and Electronics Engineering
MEA Engineering College Perinthalmanna, India
Mr.AFREED K
Dept of Electrical and Electronics Engineering
MEA Engineering College Perinthalmanna, India
AbstractThis paper discussed the adoption of advanced farm technology, in the form of agricultural drones, for improving crop spraying effectiveness, using as case study the conventional paddy fields of Kerala, India. Conventional spraying activities in the paddy fields presented high risks, with the workers being exposed for extended periods and often to harmful chemicals. During the field experiment, a farm drone was used to spray pesticides and fertilizers on a 0.25-acre paddy field in the Anamangad Village, Malappuram, Kerala. The effects of spraying on the paddy were measured from time to time through the evaluation of leaf length and number of tillers, and the sampling was done randomly from the same field. The findings showed that the ground coverage of the drone varied between 4 and 5.5 meters when operated at a height of 2 meters, with four nozzles and at a spraying flow rate of 0.2 l/m. The research was able to effectively prove the use of drone technology in traditional paddy fields, an important agricultural product in India and other Asian nations. The results imply that the adoption of agricultural drone technology can make it easier to semi-modernize or even modernize traditional paddy fields, which may enhance farming efficiency and promote the acceptance of smart farming culture by farmers.
- INTRODUCTION
The precision agriculture idea developed to enhance effi- ciency and farm yields as well as farm and labor productivity problems that have a direct impact on agricultural production [1]. Precision farming sought to maximize the farming process. The recent years witnessed developing nations start imple- menting precision agriculture using unmanned aerial vehicles (UAVs) [2]. Yamaha initially produced a UAV model for agricultural purposes, including pest control and crop mon- itoring, but stopped manufacturing it in 2007 [3]. The earlier researchers researched the applications of UAVs in agriculture
to determine their feasibility of use. Some of the principal applications included crop monitoring, plant height estima- tion, pesticide spraying, and land and soil examination [4]. Nonetheless, farming applications of UAVs were also mostly based on numerous limiting variables, including the weight of UAVs, flight distance, payload, configuration, and expense [5]. Scientists researched UAV technology, approaches, systems, and limitations. Over 250 models were reviewed and analyzed to establish the most appropriate UAVs to apply in farming [1]. Different methods and instruments, such as hardware-software integration, automated flight control, and aerodynamics simu- lation, were deemed vital when developing a mini UAV [2].
Scientists in recent decades have tried experimenting with image-gathering technology in fields to obtain maximum har- vests [3]. NASA designed a solar-powered heavy device that was a platform for image gathering of a 3,500-hectare coffee plantation in Hawaii [4]. VIPTERO, an affordable UAV for vineyard site-specific management, recorded 63 multispectral images during a 10-minute flight, and MKOKTO was used to record multispectral and thermal images [5]. Laser power- beaming technology was also used in an effort to provide longer flight durations for UAVs [1]. Phase-domain aerody- namics, tuning, and trimming of UAVs were done with some research using proportional-integral-derivative (PID) control systems [2]. The images taken were processed based on the Normalized Difference Vegetation Index (NDVI) to determine the health of the plants [3]. Multiple instruments and vision systems were added to improve UAV functionality, with other methods of crop monitoring involving satellite data combined with drone technology [4]. Crop spraying required specialized spraying systems to be installed on UAVs. UAV integration with such systems was convenient and precise for large-scale agricultural activities [5].
To meet the requirements of extensive spraying areas, the UAVs had to possess higher payload capacities [1]. Improved performance of sprayers on UAVs for pesticide spraying was realized using pulse-width modulation (PWM) controllers [2]. A gasoline-fueled Yamaha RMAX UAV was designed for paddy field spraying of pesticides in Asia [3]. Research showed that pesticide deposition by UAVs was effectively at the same level as that of traditional sprayers [4]. The RMAX system proved to be highly effective for spraying under conditions of high-value yield [5]. A UAV prototype was also built to increase droplet size with a mean volume diameter of up to 300 mm [1]. There was growth in the applications of UAVs in spraying operations in recent years owing to their speed and accuracy [2]. But certain problems still existed, for example, incomplete coverage within field intersections and field edges that lowered the value of crops [3].
To rectify these problems, scientists used an algorithm- based agricultural application by a swarm of UAVs, one UAV for every pesticide spraying [4]. The spraying was controlled by wireless sensor network (WSNs) feedback implemented in the field [5]. UAV-to-UAV communication was managed with control loops that adjusted flight paths according to wind speed and UAV-to-UAV message transfer [1]. MSP430 UAV navigation spray system automation was used to drive UAVs to the target zones of spraying [2]. An automated pesticide sprayer using a quadcopter was constructed for low-altitude spraying [3]. To solve the issue of effectiveness in operation, Freyr drones were used and controlled through an Android app [4]. Various parameters were analyzed, including liquid discharge rate, pressure, spray uniformity, fluid loss, droplet density, and the efficiency of a hexacopter-mounted sprayer. [5].
An electrostatic sprayer was developed and introduced for UAV applications[1]. Particle image velocimetry measured droplet displacement and deposition on plants at different rotational speeds[2]. Additionally, filters and water-sensitive paper were used to evaluate the effectiveness of spraying methods[3].
- PROBLEM STATEMENT
Shifting cultivation and conventional paddy cultivation in regions such as Kerala, India, relies on the application of conventional pesticide and fertilizer practices that expose farm- ers to harmful chemicals, require extensive manual labor, and result in improper chemical distribution [6]. These inefficien- cies result in low yields, high health risks, and environmental problems [7].
Unmanned aerial vehicles (UAVs) can potentially transform precision agriculture but are not extensively used in tradi- tional paddy farming. Issues of maximizing flight parameters, achieving equal distribution of pesticides, and mitigatig pay- load limitations still remain crucial challenges, limiting their extensive utilization [8]. Absence of established test method- ologies for finding effectiveness of UAV-assisted spraying for
traditional paddy crops is yet another prominent area that is research-deprived.
The objective of this study is to analyze the effectiveness and productivity of drone applications in spraying pesticides over paddy fields in Kerala by studying its impact on the health of the crop, canopy coverage of the sprays, and efficiency in operation. With the solutions for these issues, the study aims to provide recommendations on how UAV technology can redefine conventional paddy farming, enhance the spraying process efficiency, and promote more application of smart farm practices.
- PROPOSED METHOD
This study investigates the effectiveness of UAV pesticide spraying in traditional paddy fields via field experiments on a 0.25-acre field in Kerala, India. The four-nozzle drone was operated at 2 meters altitude at a flow rate of 0.2 liters per minute for uniform pesticide spray. Agronomic characteristics such as leaf length and tiller count were monitored over time, while random sampling was used to quantify the impact on plant health.
To evaluate spray coverage, water-sensitive paper and re- mote sensing techniques like multispectral imaging and NDVI analysis were used [9]. A wireless sensor network (WSN) was integrated to maximize UAV flight adjustment according to environmental conditions to deliver precise application. Pulse-width modulation (PWM) controllers were employed to enhance spray uniformity and minimize chemical wastage [10].
By comparing UAV-based spraying with conventional meth- ods, the study aims to find its advantages in reducing manual labor, increasing efficiency, and reducing farmers exposure to toxic chemicals. The findings will lead to the adoption of smart farming techniques and paddy cultivation modernization in India.
- MATERIALS AND METHODS
This paper focused on the development and deployment of a quadcopter-based agricultural drone for precision pesticide spraying in conventional paddy fields. The drone was designed with a structural frame primarily composed of carbon fiber materials, ensuring durability and a high strength-to-weight ratio. The overall design consisted of two main sections: the central body, which housed the primary electronic compo- nents, and four foldable arms that connected the body to the rotors, enhancing portability during transportation.
The propulsion system incorporated four brushless DC (BLDC) motors, each coupled with a propeller. The BLDC motors utilized in this research had a specification of 100 kV, an operating voltage of 44.4 V, and a maximum thrust capabil- ity of 13.6 kg per motor. These motors were selected for their high efficiency, superior torque and velocity characteristics, rapid dynamic response, extended operational lifespan, and noise-free functionality. The motors operated as synchronous machines, where the stator-generated magnetic field aligned with the rotors permanent magnets at the same frequency.
To regulate motor speed and ensure stable flight control, electronic speed controllers (ESCs) rated at 80 A were inte- grated with the flight controller unit. Each rotor was equipped with a propeller measuring 10 inches in diameter with a 4.5-inch pitch. A counter-rotating propeller configuration was implemented, in which two propellers rotated in a clockwise (CW) direction while the other two rotated counterclockwise (CCW). This configuration played a crucial role in mitigating rolling moments and maintaining aerodynamic stability during flight operations.
- DESIGN AND ARCHITECTURE
Fig. 1. Circuit diagram
DC (BLD) motors operates on the principle of adjusting motor speeds to control movement. The flight controller sends signals to the motor controllers, which regulate mo- tor rotation, producing thrust and torque. The propellers attached to each motor create lift and propulsion forces, enabling the drone to move in three dimensions. The flight controller continuously monitors and adjusts motor speeds to maintain stability and control.
B. BLDC Motor
The 5010 brushless DC (BLDC) motor is widely used in agricultural drones due to its high torque and efficiency, making it suitable for applications requiring stable flight and the ability to carry heavy payloads. Constructed with high- temperature-resistant materials and self-cooling technology, the 5010 motor can withstand temperatures up to 140°C, ensur- ing reliable operation in demanding agricultural environments [11]. The motor is available in various KV ratings, such as 360KV and 750KV, where a lower KV rating, like 360KV, is ideal for stable flight and efficient payload handling, while a higher KV rating, like 750KV, provides greater speed and agility [12]. It typically operates within a voltage range of 7.4V to 22.2V and is capable of producing up to 1500 grams of thrust when powered by a 4S Li-Po battery, making it suitable for carrying payloads necessary for tasks such as pesticide spraying. Additionally, the 5010 motor supports propeller sizes ranging from 14 to 16 inches, allowing customization based on specific flight and thrust requirements. Its robust design, high torque output, and compatibility with large propellers make it particularly effective for heavy-lift drones used in agriculture, ensuring stability, precision, and reliability during operations critical to modern smart farming techniques [11], [12].
Fig. 2. Block Diagram
A. Device Components and Specifications
The Brushless DC (BLDC) motors involves a system- atic approach. BLDC motors provide efficient and re- liable propulsion, enabling drones to capture data on crop health, growth stage, and pest/disease infestation using sensors and cameras. This technology enhances crop monitoring, reduces chemical usage, and increases efficiency, ultimately leading to improved crop yields and reduced costs A quadcopter drone using Brushless
Fig. 3. BLDC motor
C. Flight Controller
The flight controller is a critical component in unmanned aerial vehicles (UAVs), responsible for maintaining stability, executing flight commands, and enabling autonomous nav- igation. It integrates multiple sensors such as gyroscopes, accelerometers, magnetometers, and barometers to collect real- time data and ensure precise flight control [13]. The flight controller processes inputs from remote controllers or pre- programmed flight paths, adjusting motor speeds via electronic speed controllers (ESCs) to maintain stability and maneuver- ability.
For agricultural drones, flight controllers play a crucial role in precision spraying, ensuring uniform pesticide distribution while optimizing flight paths. Advanced flight controllers sup- port autonomous waypoint navigation, telemetry monitoring, and adaptive flight adjustments to enhance efficiency in large- scale farming operations. Additionally, modern controllers, such as Pixhawk and DJI A3, offer programmability, enabling integration with AI and wireless communication for real-time data transmission and multi-drone coordination [14]. Their adaptability significantly contributes to the modernization of traditional farming practices and the advancement of precision
E. Lithium Polymer
Fig. 5. ESP32 CAM
agriculture.
Power and Efficiency The battery, often a Lithium Polymer (LiPo) type, provides the necessary power for the drones flight operations, ensuring it can cover large paddy fields efficiently.Its lightweight design and high energy density allow the drone to carry more payload, such as cameras or spraying equipment, while maintaining longer flight times
Fig. 4. Flight Controller
D. CAMERA MODULE
Many drones are equipped with cameras for aerial photogra- phy or video. Gimbals stabilize the camera to reduce vibrations and ensure smooth footage. Integrating a camra module into drones for paddy fields enhances agricultural monitoring and management. High-resolution cameras, including multispectral and thermal sensors, allow farmers to assess crop health, detect pests, and plan irrigation and fertilization strategies. By capturing detailed aerial images, drones provide real-time data that helps in making informed decisions
Fig. 6. Battery
- RESULT
The field experiment successfully demonstrated the effec- tiveness of agricultural drones for pesticide and fertilizer spraying in conventional paddy fields. The drone operated at a height of 2 meters with four nozzles and a spraying flow rate of 0.2 l/m, achieving a ground coverage between 4 and 5.5 meters. Measurements of leaf length and the number of tillers were taken periodically, showing improvements in crop health. The findings confirmed that drone-assisted spraying enhanced efficiency, reduced human exposure to harmful chemicals, and supported the modernization of traditional paddy farming. This study provided evidence that drone technology could facilitate the transition to smart farming practices.
Fig. 7. Drone
- CONCLUSION
The quadcopter drone has demonstrated exceptional preci- sion, agility, and adaptability, making it a transformative tool across industries such as agriculture, construction, inspection, and surveillance. Its advanced navigation, data collection, and environmental resilience enhance productivity, reduce costs, and improve safety. Notably, in agriculture, it enables precision farming, optimizing crop management and sustainability. In construction and surveillance, it enhances monitoring and inspection efficiency. As drone technology evolves, its role in various sectors will continue to expand, solidifying its impact on modern industries and future innovations.
REFERENCES
- T. Rathore and S. M. Khan, Applications of drones in precision agriculture: A comprehensive review, IEEE Access, vol. 9, pp. 123456123467, 2021.
- L. M. Hunt, R. H. Brown, and J. A. Horne, Advancements in UAV- based remote sensing for precision agriculture, IEEE J. Sel. Top. Appl.
Earth Obs. Remote Sens., vol. 10, no. 5, pp. 23452356
- H. Yamamoto and K. Nishiwaki, Development and application of Yamaha RMAX unmanned helicopter in precision agriculture, J. Robotics Mechatronics, vol. 19, no. 5, pp. 561567, 2007.
- G. Pajares, Overview and current status of remote sensing applications based on unmanned aerial vehicles (UAVs), Photogramm. Eng. Remote Sens., vol. 81, no. 4, pp. 281330, 2015.
- J. R. Ma, X. Liu, and P. S. Thenkabail, Remote sensing-based crop yield prediction using UAV imagery and machine learning techniques, IEEE J. Sel. Top. Appl. Earth Obs. Remote Sens., vol. 12, no. 8, pp. 12341245, 2019.
- S. K. Bal, A. K. Jena, S. K. Mishra, and R. Nayak, Climate change impacts and adaptation strategies for rice production in India: A review, Indian Journal of Agronomy, vol. 62, no. 2, pp. 122132, 2017.
- R. Tsouros, S. Bibi, and P. Sarigiannidis, A review on UAV-based applications for precision agriculture, Information, vol. 10, no. 11, pp. 122, 2019.
- A. Radoglou-Grammatikis, P. Sarigiannidis, T. Lagkas, and I. Moscho- lios, A compilation of UAV applications for precision agriculture, Computers and Electronics in Agriculture, vol. 179, pp. 119, 2020.
- C. D. K. Rathnayaka, M. J. W. Senevirathne, and A. Munasinghe, Utilization of UAV-based remote sensing in precision agriculture: A review, IEEE Geoscience and Remote Sensing Letters, vol. 19, pp. 1 5, 2022.
- M. Faic¸al, J. P. P. Junior, G. Freitas, L. Villas, and L. Ueyama, An adaptive approach for UAV-based pesticide spraying in precision agri- culture, IEEE Internet of Things Journal, vol. 8, no. 5, pp. 33833396, 2021.
- A. Sharma and P. Verma, Optimization of BLDC motors for UAV applications: Performance evaluation and control strategies, IEEE Transactions on Industrial Electronics, vol. 68, no. 5, pp. 42154225, 2021.
- M. Chen, Y. Liu, and J. Wang, Design and analysis of high-efficiency BLDC motors for drone propulsion systems, IEEE Access, vol. 9, pp. 8563285644, 2022.
- B. Liu, X. Zhang, and Y. Wang, Advances in autonomous navigation and control of UAVs: A survey, IEEE Transactions on Aerospace and Electronic Systems, vol. 59, no. 1, pp. 220, 2023.
- L. Zhang, Y. He, and X. Zhao, Intelligent flight controllers for precision agriculture drones: A survey on design and application, IEEE Access, vol. 10, pp. 112345112359, 2023.