
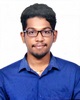
- Open Access
- Authors : Vignesh Asokan , Yogesh Vaidhyanathan , Venkat Prasanna
- Paper ID : IJERTV9IS100029
- Volume & Issue : Volume 09, Issue 10 (October 2020)
- Published (First Online): 12-10-2020
- ISSN (Online) : 2278-0181
- Publisher Name : IJERT
- License:
This work is licensed under a Creative Commons Attribution 4.0 International License
A Macroscopic Review on Contribution of Methanol in an Internal Combustion Engines
Vignesh Asokan1*, Yogesh Vaidhyanathan2, Venkat Prasanna3
1Department of Mechanical Engineering, SRM Institute of science and technology, Chennai 600 089, India,
2Department of Mechanical Engineering, College of Engineering Guindy, Chennai 600 025, India,
3Department of Mechanical Engineering, SRM Institute of science and technology, Chennai 600 089, India,
Corresponding Author: Vignesh Ashokan, Department of Mechanical Engineering, SRM Institute of Science and Technology, Ramapuram Campus, Chennai 600 089, India.
Abstract:- The use of, and research on methanol in a combustion engine has been increased greatly due to its better outcomes in terms of performance, combustion, and emission behavior. To get extensive knowledge about the combustion behavior and emission benefits of a methanol-fueled internal combustion engine, a literature survey on recent academic research has been made and presented in this paper. Maximum 90% of methanol was effectively used in a compression ignition engine at high load conditions under dual fuel combustion technology. The methanol-fueled dual fuel combustion mode breaks a trade-off between the oxides of nitrogen (NOx) and the soot emissions which was the major problem existing in conventional diesel combustion (CDC). The methanol-fueled dual fuel combustion resulted in completely premixed combustion. The methanol blended with high cetane fuels improved the combustion rate due to the presence of oxygen content.
Keywords: Methanol, Dual fuel, blended fuels, oxygen, NOx, Soot.
-
INTRODUCTION
The high cost of fossil fuels and their dependency on other countries is the main reasons for searching for alternative fuels from renewable sources [1]. Methanol is the best alternative fuel for use in internal combustion engines. Methanol is synthesized from natural gas, coal, coke oven gas, CO2, H2, and biomass [2]. Ministry of road transport and highways have framed norms and guidelines for the use of methanol to reduce the dependency of fossil fuels from other countries [3]. Methanol is a low reactivity fuel having a higher-octane number. The chemical formula for methanol is CH3OH which reveals that the methanol is a simpler molecular fuel contains larger hydrogen density [4]. In spark-ignition engines methanol can be used directly or in a blended form with other low reactive fuels. The high-octane rating of the methanol is the main barrier for use of a higher percentage of methanol in a compression ignition engine. The high-octane number of methanol fuel restricts the auto- ignition tendency when subjected to use in a compression ignition engine. The methanol ignition quality and cetane number can be improved by blending with high cetane fuels like diesel and biodiesel [5].
Three are three possible ways to admit methanol inside the compression ignition engine combustion chamber. There are
(i) Methanol can be blended with a high cetane fuel to inject directly inside the combustion chamber (ii) Methanol can be injected at the engines intake port by using a separate injector (iii) Methanol can be injected directly inside the combustion chamber by using a separate injector. The systematic illustration for the above three possible methanol injection positions in a diesel engine is shown in Figure 1-3. Methanol was used in conventional combustion mode and also in different low temperature combustion (LTC) techniques such as homogeneous charge compression ignition (HCCI), premixed charge compression ignition (PCCI) and reactivity-controlled compression ignition (RCCI). In HCCI combustion, the air-fuel mixture has been made completely homogeneous by using a well-advanced injection strategy or by means of external mixture formation. In PCCI combustion, partially premixed charge is allowed to become a homogeneous mixture in order to control the combustion and to extend the operating range.
Also, the methanol was largely utilized in dual fuel combustion technology. The dual fuel combustion is reactivity-based control combustion and hence also referred to as reactivity-controlled compression ignition (RCCI) combustion. In dual fuel combustion, both low cetane fuels (e.g. Methanol) and high cetane fuels (e.g. Diesel and biodiesel) are admitted inside the combustion chamber by using two separate injectors [6] which are illustrated in Figure 2 and Figure 3.
To understand about the current trend and combustion benefits obtained from the methanol fueled internal combustion engines, a study on previous recent academic literatures were done and has been presented in this paper.
Figure 1 Direct injection of Methanol blended fuels
Figure 2 Pure methanol injection at the intake port
Figure 3 Direct injection of pure methanol
-
LITERATURE SURVEY AND DISCUSSIONS Methanol has been used in internal combustion engines on both compression and spark-ignition engines. To improve the heat engine performance and to reduce both exhaust emissions and fossil fuel utilization, an effective use of better alternative fuel like methanol in an internal combustion engine are necessary. Also, to know about the current features and existing benefits of using methanol in an internal combustion engine, a study on previous literature is needed. With this motivation, a study has been made on previous literature on engine performance, emissions from methanol and has been presented in this section.
A. Methanol in conventional combustion and RCCI (Reactivity controlled compression ignition) combustion modes.
Ganesh Duraisamy et al (2020) used methanol (M) as a low reactive fuel in dual fuel combustion. The diesel (D) and polyoxymethylene dimethyl ether (PODE) was used as a high reactivity fuel. The M/D and M/PODE combustion were performed on the automotive light duty diesel engine and the obtained results were compared with the conventional diesel combustion (CDC). The experiments were conducted for 3.4 bar brake mean effective pressure (BMEP) at 1500 rpm with 25% exhaust gas recirculation (EGR) conditions. The M/D and M/PODE dual fuel combustion were capable to break a trade-off relation between oxides of nitrogen (NOx) and soot with a 3.5% increase in brake thermal efficiency (BTE) compared to CDC. The increased BTE was due to reduced compression work caused by prolonged ignition delay. The M/D and M/PODE exhibited prolonged ignition delay and decreased peak in-cylinder pressure due to high latent heat of vaporization of methanol. Slightly higher hydrocarbon (HC) and carbon monoxide (CO) emissions were observed from M/D and M/PODE combustion mode compared to CDC operation. The increased HC and CO emissions were due to a reduction in global in-cylinder temperature caused by the addition of methanol. The M/PODE delivered lower HC, CO, and soot emissions compared to M/D due to the increased global reactivity gradient caused by the addition of PODE [7].
Hao Chen et al (2019) prepared diesel: n-pentanol: methanol blended fuel with a blending ratio of 70:20:10 fueled in a turbocharged common rail diesel engine and the experimental investigation was carried out. The oxygen content in the blended fuel and the prolonged ignition delay made the combustion to occur at a faster rate. The peak combustion temperature and the peak heat release rate (HRR) increased due to high premixed combustion during low and medium loads. At the above mid load, the diffusion combustion dominated the premixed combustion region which further increased in-cylinder temperature. With an increase in methanol percentage, the soot decreased due to lower rich fuel-air mixture regions compared to the CDC operation. It was further reported that the advanced injection angle increased the NOx formation and the retarded injection angle reduced the NOx formation of blended fuel compared to the CDC operation [8].
R Murugan et al (2019) had attempted to convert the low reactive fuel (Methanol) into a medium reactive fuel to
improve the cetane and ignition quality of methanol. Methanol (M), PODE, Iso-butanol (I) were used to prepare the medium reactive fuel and referred to as MPI fuel. Diesel was injected directly inside the cylinder at a high injection pressure (300 bar). The maximum 60% premixed fuel ratio of M and MPI fuels were injected at the intake port at low injection pressure (4bar). The M/D and MPI/D dual fuel combustion were performed and compared with CDC readings. The experiments were performed on a three- cylinder automotive engine at low load conditions with 20% EGR. The results showed that the M/D and the MPI/D dual fuel combustion reduced NOx and soot emissions simultaneously by about 80% with increased HC and CO emissions compared to CDC. The NOx was reduced due to the reduced in-cylinder temperature caused by the high enthalpy of vaporization of methanol. The soot was reduced due to the reduced fuel-rich regimes inside the combustion chamber. The HC and CO were increased because of lower in-cylinder temperature and the stagnation of fuel in the crevice volumes. It was observed that CDC exhibits both premixed and diffusion combustion whereas, the M/D and MPI/D dual fuel combustion delivers only premixed combustion. The methanol substitution increased the ignition delay due to high latent heat of vaporization of methanol. The increased ignition delay of the combustion process reduced the total compression pressure and combustion duration. This shorter combustion duration reduced the heat transfer losses during the expansion process which increased the indicated thermal efficiency. The peak in-cylinder pressure increased due to more premixed fuel substitution. About 66% and 74% reduction in HC and CO were observed for MPI/D combustion due to the enhanced ignition quality compared to the M/D combustion. The higher coefficient of variation (COV) was predicted during the experiment due to the higher premixed fuel portion compared to the CDC [9].
Han Lu et al (2019) carried out the experiments on a turbocharged four-cylinder dual fuel diesel engine fueled with methanol and diesel. The formation of nitrogen dioxide (NO2) emission and the combustion characteristics were experimentally analyzed by varying the methanol percentage, EGR rate, and the exhaust backpressure. The NO2 formation of dual fuel methanol/diesel combustion was reduced when a 10% to 40% EGR rate was used. Also, the use of EGR improved the combustion efficiency of methanol/diesel combustion. The NO2 emission increased steadily and then decreased gradually with an increase in methanol substitution ratio. It was also observed that the NOx emission increased with an increase in exhaust backpressure. The use of more methanol substitution in dual fuel combustion produced more premixed combustion and less diffusion combustion [10].
Bin Wang et al (2019) focused an experimental analysis on a turbocharged diesel engine using methanol and diesel as a fuel to address the auto-ignition characteristics and the combustion characteristics of methanol/diesel combustion. The results of which revealed that the advanced diesel injection strategy with sufficient EGR reduced the NOx and the soot emissions. The diesel was the main ignition source for methanol-air premixture. Initially, the diesel-air mixture
started to burn, then the produced heat was used to burn the surrounding methanol-air mixture inside the combustion chamber. The more increase in intake air temperature resulted in methanol autoignition. The methanol autoignition was prevented by maintaining the in-cylinder temperature below 900k before diesel injection. The existence of methanol autoignition in dual fuel combustion causes several drawbacks such as increased knocking tendency, piston damage, and a significant increase in HRR [11].
Ganesh Duraisamy et al (2019) performed the methanol/diesel dual fuel combustion on a three-cylinder turbocharged diesel engine by varying the EGR and the methanol premixed fuel percentage. The diesel was injected directly at 480 bar injection pressure and the methanol was used as a premixed fuel injected along with intake air at 3 bar pressure. The engine was operated at 3.4 bar and 5.1 bar BMEP conditions at 1500 rpm. The methanol percentage was varied from 57 % to 90% during the experiment. The results demonstrated that the increase in methanol percentage reduced the compression pressure and rate of pressure rise due to high latent heat of vaporization of methanol. Also, the M/D dual fuel combustion resulted in higher in-cylinder pressure and heat release compared to CDC. The increased methanol premixed ratio reduced the nitric oxide (NO) emissions by about 90% compared to CDC due to lower in-cylinder temperature caused by the high latent heat of vaporization of methanol. The start of ignition was retarded and the combustion duration was shortened due to the more premixed methanol fuel admission. The soot emission was reduced by about 94% for M/D combustion due to the elimination of fuel-rich regions compared to the CDC operation. The HC and CO emissions were increased with an increase in methanol and EGR substitution due to low in-cylinder temperature and fuel accumulation in the crevice volumes. The effect of variation in EGR on combustion and emissions were also analyzed by varied the EGR rate from 25% to 40%. The results of which revealed that the 25% of the cooled EGR with premixed methanol mass percentage of 76% and 85% yielded lower cyclic variation, improved stable engine operation, 3.5% increased BTE and lower exhaust emissions when compared to both CDC operation and dual fuel hot EGR operation [12].
Hiregoudar et al (2018) performed an engine experiment on a twin-cylinder diesel engine fueled with methanol blended with rapeseed oil, mango seed oil, and apricot oil. The modified piston geometry was used for the experiment. The BTE and the brake specific energy consumption was observed to be higher for all type of biodiesel blended fuels used along with modified piston compared to CDC with a conventional piston. The emissions such as HC, CO, NOx, smoke, and aldehydes were found to be lower due to better air-fuel mixing and better combustion efficiency promoted by modified piston compared to CDC [13].
Zhiqin Jia et al (2018) demonstrated M/D dual fuel combustion on a single cylinder heavy-duty diesel engine. The experiments were conducted for three different locations of methanol fuel injection such as port injection, early direct at intake stroke (DI-E), late direct at compression stroke (DI-L). The diesel fuel was injected
directly inside the combustion chamber at high injection pressure. The results showed that for all the three types of methanol injection locations the M/D dual fuel combustion reduced NO and soot emission when 30% EGR was used compared to CDC. The DI-E and DI-L delivered a more significant reduction in HC and CO emissions because of less accumulation of fuel at crevice volumes compared to the port injection of methanol. The port injected methanol and DI-L combustion showed relatively lower CO2 emissions compared to DI-E [14].
Chenyang Fan et al (2018) carried out an engine test on a stationary diesel engine fueled with methanol/diesel blend under steady-state operating conditions to evaluate the carbonyl compound emissions. The result revealed that the diesel/methanol blended fuel emitted more carbonyl compound emissions such as formaldehyde and acetaldehyde compared to the CDC operation. It was observed that the propionaldehyde emissions were reduced from methanol/diesel blended fuel combustion. Also, the authors suggested the employment of a diesel oxidation catalyst (DOC) to reduce carbonyl compound emissions from a non-road diesel engine fueled with methanol/diesel blended fuels [15].
Meisam et al (2018) conducted experiments using an oxygenated fuel blend of methanol, diesel, and waste cooking oil biodiesel (MDB) under various loading conditions at a constant speed of 1500 rpm. The obtained results from the MDB combustion were compared with the CDC operation. The experimental results concluded that the MDB prolonged the ignition delay and shortens the combustion duration due to higher latent heat of vaporization which tends to lower the in-cylinder temperature. HRR increased due to large premixed combustion caused by longer ignition delay. Also, the fuel atomization was improved due to the lower viscosity of MDB. Specific fuel consumption (SFC) increased because of lower calorific value and the engine might take more fuel to deliver the same power output. The CO emission was found to be high at low load conditions due to lower in- cylinder temperature caused by the addition of methanol. Lower carbon dioxide (CO2) emission was observed from MDB combustion due to the lower carbon to hydrogen ratio of MDB. With an increase in load, a 25% reduction in CO and HC emissions were recorded due to complete combustion caused by the availability of oxygen content in MDB fuel. The shorter combustion duration worsens the residence time and in-cylinder temperature for the production of NO emission and hereby reduced NO emission was observed from MDB combustion compared to CDC. About 70% reduction in particulate matter (PM) emission was observed due to better soot oxidation caused by higher oxygen content and lower carbon to hydrogen ratio. BTE increased by about 3.5% due to improved combustion caused by better atomization. The exhaust gas temperature (EGT) decreased due to improved cooling environment inside the combustion chamber caused by the higher latent heat of vaporization of MDB fuel. The geometric mean diameter of the fuel particles reduced due to better mixing rate caused by the longer ignition delay [16].
Horng-Wen Wu et al (2018) integrated a methanol steam recovery (MSR) unit with a diesel engine. The MSR was heated with the help of waste heat produced from the engine. From the experimental result, it was found that the diesel engine equipped with methanol steam recovery could reduce the smoke, PM, and NOx emissions. On the other hand, the efficiency of heat recovered from the engine exhaust was increased with an increase in methanol aqueous solution and reaction temperature [17].
Bin Wang et al (2018) did experiments on a four-cylinder turbocharged dual fuel diesel engine using methanol and diesel. The diesel was injected directly inside the cylinder and the methanol was injected at the engines intake port. The experimental result proved that a maximum 80% of the methanol substitution was possible in a dual fuel diesel engine at full load condition and the remaining 20% of the diesel fuel was used as an ignition source. Also, it was found that the diesel injection timing had to be delayed for some angle to effectively increase the methanol substitution percentage during the engine operation. The NOx and the soot emissions were reduced simultaneously with an increase in methanol substitution ratio due to a reduction in both in-cylinder temperature and fuel-rich regions. The maximum 20% EGR was used to attain the combustion phasing and to suppress the NOx formation. The soot was found to be observed around 0.004 g/kWh which is even very low than the requirement of BS-VI emission norms. The HC and CO emissions were increased with increase in methanol substitution ratio due to the reduced global in- cylinder temperature created by the higher latent heat of vaporization of methanol. The brake specific fuel consumption was reduced with an increase in methanol percentage due to longer ignition delay, lower calorific value, and lesser density of methanol fuel compared to pure diesel [18].
Changming Gong (2018) carried an experimental investigation on a four-cylinder direct injection spark ignition engine fueled with methanol. The emissions such as formaldehyde and partially burned emissions were predicted by varying the fuel injection timing, spark timing, and the air-fuel ratio. The results of which showed that the formaldehyde emission was reduced and the partially burned emissions increased with an increase in the air-fuel ratio. On the other hand, increased formaldehyde emission and the decreased partially burned emissions were observed while retarding the spark timing [19].
Taoyang Wu et al (2018) performed the dual fuel combustion using methanol and diesel on a six-cylinder turbocharged diesel engine to explore the effects of injection timing on engine performance and emission. The test was carried out at 10 bar BMEP with a constant speed of 1340 rpm. The promising results proved that the methanol/diesel dual fuel combustion reduced the NOx and soot simultaneously when the late injection strategy was adopted. The mean gas temperature (MGT) increased during early injection due to the combustion of more premixed fuel and MGT reduced for late injection due to the availability of less premixed fuel. Also, the diesel late injection increased the exhaust gas temperature. Furthermore, the late injection strategy formed a weak combustion rate inside the
combustion chamber which increased the global equivalence ratio [20].
Jiangtao Hu et al (2018) injected the methanol and diesel directly into the constant volume combustion chamber by two separate injectors. The combustion characteristics of directly injected methanol and diesel fuel were experimentally observed. The injection timing and the mass of fuel injection of methanol and diesel were controlled by two different electronic control units (ECUs). The methanol was injected well before the injection of diesel fuel to form a premixed methanol-air mixture. It was noticed that the methanol/diesel combustion exhibits smoke-free combustion. The ignition delay reduced with increased mass of pilot injection. The advanced diesel pilot injection and the increased pilot mass reduced the flame lift-off length of diesel/methanol flame. Also, it was observed that the HRR reduced with an increase in diesel pilot mass during methanol/diesel dual fuel combustion [21].
Jinling Tian et al (2018) carried out experiments on a four- cylinder water-cooled diesel engine fueled with diesel, biodiesel, and methanol/diesel blend. The gas chromatography-mass spectrometry was used to analyze the volatile organic compound emissions of three different fuels and the obtained results were compared. From the experiment, it was found that the methanol/diesel combustion contributed more benzene and toluene emissions when compared to pure diesel and biodiesel combustion. Methanol/Diesel combustion exhibited less volatile compound emissions than pure diesel. As the load increases the tendency of volatile compound emission from methanol/diesel combustion gradually decreased [22].
H. Yerrennagoudaru et al (2018) performed experiments on a multi-cylinder diesel engine fueled with methanol blended with coconut oil, mahua oil, and palm oil using a modified piston. The experiments showed better performance and emissions for methanol blended fuels used along with a modified piston compared to a diesel with the conventional piston. The air-fuel turbulence and mixing were improved with modified piston which reduced the HC and CO emissions for methanol blended fuels. The smoke emission was reduced due to better oxidation of air-fuel promoted by the oxygen content of biodiesel. The improvement in brake thermal efficiency was observed for all types of methanol blended fuels used with modified piston geometry [23].
S. Bhanu Teja et al (2018) attempted an experimental investigation on a single cylinder stationary diesel engine using linseed oil with methanol addition. It was noticed from the result that the fuel consumption increased for biodiesel compared to diesel due to lower calorific value. The engine consumed more fuel to maintain the same power output for a particular loa condition. The BTE decreased due to the higher fuel consumption needed for biodiesel operation. Also, the addition of a low percentage of methanol (<20%) reduced the CO emission. The use of higher methanol percentage increased the CO and HC emissions due to incomplete combustion and lower in-cylinder thermodynamic conditions [24].
-
Methanol in HCCI (Homogeneous charge compression ignition) combustion and PCCI (Premixed charge compression ignition) combustion modes.
Rakesh Kumar Maurya (2014) did an Experimental investigation to understand the performance, combustion and emission characteristics of ethanol and methanol fueled HCCI engine. Used methanol as a port injection to perform HCCI combustion. Methanol HCCI combustion reduced the NOx and soot emissions to near zero level with improved thermal efficiency. The intake air temperature was used to attain the auto ignition of methanol fuel. Reduced combustion duration was predicted during the HCCI operation due to burning of more homogeneous mixture. Also, HC and CO emissions increased in HCCI operation due to lower in-cylinder temperature [25].
Toshiyuki Seko (2001) performed experiments on a single cylinder engine to improve the combustion efficiency and to extend the operating load range of an existing methanol premixed charge compression ignition combustion. The promising results showed drastic reduction in HC and CO emissions along with improved thermal efficiency due to use of flash boiling fuel injection technique. The flash boiling fuel injector reduced the fuel penetration and increased the fuel dispersion inside the cylinder which aids in better mixture formation for complete burning of air fuel in a shorter crank angle duration. Also, the results proved that the heating of fuel during the PCCI combustion reduces NOx at high load operation compared to the results obtained from PCCI without fuel heating [26].
Mingfa Yao. (2005) worked with methanol blended dimethyl ether fuel and studied the effect of cooled EGR on HCCI combustion. The methanol blended DME fuel was injected at a port of the engine cylinder to create a homogeneous mixture. The methanol blended DME HCCI combustion reduced the NOx level to near zero and increased HC and CO emissions compared to conventional diesel combustion. The increased EGR rate increases HC, CO emissions and reduced the peak cylinder pressure with retarded start of combustion. The methanol blended DME HCCI combustion extended the operating range of HCCI combustion compared to normal diesel HCCI combustion [27].
Troels Dyhr Pedersen. (2010) experimented on a four- cylinder automotive diesel engine with port injection of methanol and direct injection of dimethyl ether to perform optimum HCCI combustion. The results proved that the sufficient EGR rate and methanol percentage yielded better controllable HCCI combustion without knocking [28] and Rakesh Kumar Maurya (2011) did an experimentation on port injection methanol HCCI combustion and proved that the factors such as methanol percentage, stat of injection timing of fuel, intake air temperature has an more impact of exhaust particulate emissions [29].
-
-
CONCLUSIONS
The following main conclusions were made based on the literature survey,
-
The methanol-fueled dual fuel combustion contributed to clean and smoke-free combustion.
-
The methanol-fueled dual fuel combustion breaks the trade-off relation between the NOx and the soot with increased brake thermal efficiency up to 5%.
-
Maximum 90% of high-octane methanol fuel can be effectively used in a compression ignition engine without compromising the engine performance.
-
The higher latent heat of vaporization of the methanol fuel creates a significant cooling effect inside the combustion chamber.
-
The cooling effect created by the methanol lowered both the in-cylinder temperature and fuel rich regions.
-
The methanol-fueled dual fuel combustion reduced the compression work and increased the expansion work of the engine.
-
The methanol-fueled dual fuel combustion resulted in completely premixed combustion.
-
The methanol blended with high cetane fuel improved the fuel atomization and combustion rate.
-
The methanol blended with high cetane fuel increased the ignition delay and improved the homogeneity of air-fuel mixture inside the combustion chamber.
-
-
FUTURE SCOPE Possible further research direction on,
-
Improving the production and availability of methanol.
-
The compact fuel supply system for methanol- fueled dual fuel combustion.
-
The compact electronic control unit to improve the control of methanol fueled dual fuel combustion.
-
Development of in-cylinder combustion treatment by optimizing various engine parameters to reduce the HC and CO emissions of dual fuel combustion without compromising existing combustion and emission benefits.
REFERENCES
-
Gautam Kalghatgi, Howard Levinsky, Med Colketd, Future transportation fuels, Progress in Energy and Combustion Science 69 (2018) 103-105.
-
Yisong Chen, Jinqiu Ma, Bin Han, Peng Zhang, Haining Hua, Hao Chen, Xin Su, Emissions of automobiles fueled with alternative fuels based on engine technology: A review, Journal of Traffic and Transportation Engineering 5(4) (2018) 318-334.
-
https://morth.nic.in/Motor-Vehicle-Legislation.
-
Mark Allard, Issues Associated with Widespread Utilization of Methanol, SAE Technical Paper. 2000-01-0005
-
Yahya Çelebi, Huseyin Aydin, An overview on the light alcohol fuels in diesel engines, Fuel 236 (2019) 890-911.
-
Jing Li, Wenming Yang, Dezhi Zhou, Review on the management of RCCI engines, Renewable and Sustainable Energy Reviews 69 (2017) 65-79.
-
Ganesh Duraisamy, Murugan Rangasamy, Nagarajan Govindan, A comparative study on methanol/diesel and methanol/PODE dual fuel RCCI combustion in an automotive diesel engine, Renewable Energy 145 (2020) 542-556.
-
Hao Chen, Xin Su, Jingjing He, Bin Xie, Investigation on combustion and emission characteristics of a common rail diesel engine fueled with diesel/n-pentanol/methanol blends, Energy 167 (2019) 297-311.
-
R Murugan, D Ganesh and G Nagarajan, An integrated effort of medium reactivity fuel, in-cylinder, and after-treatment strategies to demonstrate potential reduction in challenging emissions of reactivity-controlled compression ignition combustion, Journal of Automobile Engineering, 2019, DOI:10.1177/0954407019875299.
-
Han Lu, Anren Yao, Chunde Yao, Chao Chen, Bin Wang, An investigation on the characteristics of and influence factors for NO2 formation in diesel/methanol dual fuel engine, Fuel 235 (2019) 617-626.
-
Bin Wang, Anren Yao, Chunde Yao, Chao Chen, Han Lu, Jun Feng, Experimental investigation on methanol auto-ignition in a compression ignition engine under DMDF mode, Fuel 237 (2019) 133-141.
-
Ganesh Duraisamy, Murugan Ramasamy, and Govindan Nagarajan, Effect of EGR and premixed mass percentage on cycle to cycle variation of methanol/diesel dual fuel RCCI combustion, SAE Technical Paper 2019-26-0090, 2019, DOI:10.4271/2019-26- 0090.
-
Hiregoudar Yerrennagoudaru, Manjunatha K, Kishore Kumar K S, Performance and emission characteristic of a multi-cylinder DI diesel engine running on diesel and biofuels blended with methanol, Materials Today: Proceedings 5 (2018) 3325-3333.
-
Zhiqin Jia, Ingemar Denbratt, Experimental investigation into the combustion characteristics of a methanol-Diesel heavy duty engine operated in RCCI mode, Fuel 226 (2018) 745-753.
-
Chenyang Fan, Chonglin Song, Gang Lv, Guangyao Wang, Hua Zhou, Xiaojun Jing, Evaluation of carbonyl compound emissions from a non-road machinery diesel engine fueled with a methanol/diesel blend, Applied Thermal Engineeing 129 (2018) 1382-1391.
-
Meisam Ahmadi Ghadikolaei, Chun Shun Cheung, Ka-Fu Yung, Study of combustion, performance and emissions of diesel engine fueled with diesel/biodiesel/alcohol blends having the same oxygen concentration, Energy 157 (2018) 258-269.
-
Horng-Wen Wu, Tzu-Ting Hsu, Chen-Ming Fan, Po-Hsien He, Reduction of smoke, PM2.5, and NOx of a diesel engine integrated with methanol steam reformer recovering waste heat and cooled EGR, Energy Conversion and Management 172 (2018) 567-578.
-
Bin Wang, Chunde Yao, Chao Chen, Jun Feng, Han Lu, Luyu Feng, To extend the operating range of high MSP with ultra-low emissions for DMDF unit pump engine, Fuel 218 (2018) 295-305.
-
Changming Gong, Wei Huang, Jiajun Liu, Fuxing Wei, Jiawei Yu, Xiankai Si, Fenghua Liu, Yufeng Li, Detection and analysis of formaldehyde and unburned methanol emissions from a direct- injection spark-ignition methanol engine, Fuel 221 (2018) 188- 195.
-
Taoyang Wu, Anren Yao, Chunde Yao, Wang Pan, Hongyuan Wei, Chao Chen, Jian Gao, Effect of diesel late-injection on combustion and emissions characteristics of diesel/methanol dual fuel engine, Fuel 233 (2018) 317-327.
-
Jiangtao Hu, Chunde Yao, Peilin Geng, Jun Feng, Mingkuan Liu, Zhuangzhuang Li, Hui Wang, Effects of pilot injection strategy of diesel fuel on combustion characteristics in a premixed methanol- air mixture atmosphere in a CVCC, Fuel 234 (2018) 11321143.
-
Jinling Tian, Jianwei Tan, Naitao Hu, Tingjie Liu, Yulong Wang, Hao Zhong, Jin Cheng, Xuemin Zhang, Characteristics analysis for total volatile organic compounds emissions of methanol-diesel fuel, Journal of the Energy Institute 91 (2018) 527-533.
-
Hiregoudar Yerrennagoudaru, Manjunatha K, Ahmad Raza, Kantharaj B R, Abdul Mujahed, Irshad K, Analysis and comparison of performance and emissions of compression ignition engine fueled with diesel and different bio-fuels blended with Methanol, Materials Today: Proceedings 5 (2018) 5175-5185.
-
S. Bhanu Teja, Experimental investigation on the performance, emission and combustion characteristics of DI diesel engine with linseed methyl ester along with methanol carburization, Materials Today: Proceedings 5 (2018) 6470-6480.
-
Rakesh Kumar Maurya, Avinash Kumar Agarwal, Experimental investigations of performance, combustion and emission characteristics of ethanol and methanol fueled HCCI engine, Fuel Processing Technology 126 (2014) 30-48.
-
Toshiyuki Seko, Eiji Kuroda, Combustion Improvement of a Premixed Charge Compression Ignition Methanol Engine using Flash Boiling Fuel Injection, SAE Technical Paper. 2001-01- 3611.
-
Mingfa Yao, Zheng Chen, Zunqing Zheng, Bo Zhang and Yuan Xing, Effect of EGR on HCCI Combustion fueled with Dimethyl Ether (DME) and Methanol Dual Fuels, SAE Technical paper. 2005-01-3730
-
Troels Dyhr Pedersen, Jesper Schramm, Controlling the Heat Release in HCCI Combustion of DME with Methanol and EGR, SAE Technical Paper. 2010-01-1489.
-
Rakesh Kumar Maurya, Avinash Kumar Agarwal, Effect of Start of Injection on the Particulate Emission from Methanol Fuelled HCCI Engine, SAE Technical Paper. 2011-01-2408.