
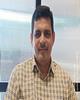
- Open Access
- Authors : Anirudhan R, Ajay S K, Abhimanyu J S, Adarsh Sankar, Vinay B, Dr.Jyothi Sankar Pr, Sajith Vs
- Paper ID : IJERTV13IS120128
- Volume & Issue : Volume 13, Issue 12 (December 2024)
- Published (First Online): 06-01-2025
- ISSN (Online) : 2278-0181
- Publisher Name : IJERT
- License:
This work is licensed under a Creative Commons Attribution 4.0 International License
A Novel IOT Based Fruit Drier System Utilizing The Waste Heat Recovered from Domestic Refrigerators
Anirudhan R Department of Mechanical Engineering
NSS College of Engineering Palakkad, India
Ajay S K
Department of Mechanical Engineering
NSS College of Engineering Palakkad, India
Abhimanyu J S
Department of Mechanical Engineering NSS College of Engineering
Palakkad, India
Adarsh Sankar Department of Mechanical Engineering
NSS College of Engineering Palakkad, India
Vinay B
Assistant Professor (Adhoc)
Department of Mechanical Engineering
NSS College of Engineering Palakkad, India
Dr.Jyothi Sankar Pr
Associate Professor Department of Mechanical Engineering
NSS College of Engineering Palakkad, India
Sajith VS
Associate Professor Department of Mathematics NSS College of
Engineering Palakkad, India
Abstract Refrigeration is the process of removing heat from an enclosed space or from a substance for the purpose of lowering the temperature. Currently, it is claimed that the refrigeration sector consumes about 17% percentage of the total electricity used worldwide, where there are currently more than 1.5 billion domestic refrigerators in use. During the working of a refrigerator, it releases some amount of heat to the surrounding which is considered as waste heat. The aim of this proposed project work is to develop a fruit drier that utilizes refrigeration waste heat for food processing applications. The project is designed to improve the current refrigerators by recovering the waste heat, storing it in the allocated chamber and continuously monitoring the conditions inside the chamber via IoT, using a number of sensors. The developed system will be capable of saving a huge amount of energy which will be used to store or dry food items. Also, this smart product will be helped to store the food items and dry the fruits, which are highly demanding for an extremely populated state like Kerala.
-
INTRODUCTION
Refrigeration is the process of removing heat from a space, substance, or system, with the goal of lowering its temperature. It is typically used to preserve perishable foods, make certain industrial processes more efficient, and provide air conditioning for buildings. There are several different types of refrigeration systems, including mechanical refrigeration systems, thermoelectric refrigeration systems, and absorption refrigeration systems. Mechanical refrigeration systems use a refrigerant, such as freon, to transfer heat from the space or substance being cooled to another location, where it is then released to the environment. Thermoelectric refrigeration systems use the Peltier effect to transfer heat from one side of a device to the other, while absorption refrigeration systems use a heat source to drive a refrigeration cycle that removes heat from a space or substance. The coefficient of performance (COP) of a refrigerator is a measure of its efficiency. It is defined as the
ratio of the heat removed from the space or substance being cooled to the amount of work required to operate the refrigeration system. A higher COP indicates a more efficient refrigerator. The COP of a refrigerator can be calculated using the following formula: COP = Q / W where
Q is the heat removed from the space or substance being cooled and W is the work required to operate the refrigeration system. The COP of a typical refrigeration system is typically between 1 and 3, with higher values indicating more efficient operation. Factors that can affect the COP of a refrigerator include the type of refrigeration system being used, the size and design of the system, and the ambient temperature and humidity. Waste heat recovery in refrigeration systems involves capturing the heat that is produced as a byproduct of the refrigeration process and using it for some useful purpose, rather than allowing it to go to waste. There are a number of ways this can be done, depending on the specific refrigeration system and the needs of the application. Some common approaches include using the waste heat to preheat ventilation air, heat water for use in a building or industrial process, or to generate electricity using a thermoelectric generator. In some cases, the waste heat can also be used to support the operation of the refrigeration system itself, by providing additional heat to the system's evaporator or condenser. Currently, it is claimed that the refrigeration sector (including air conditioning) consumes about 17% of the total electricity used worldwide, where there are currently more than
1.5 billion domestic refrigerators in use .Since a large amount of energy is being used for refrigeration worldwide, a slight improvement in efficiency could have a great impact on the environment and energy saving. Since all of the refrigeration systems release a considerable amount of heat into the atmosphere, this project focuses on implementing refrigeration heat recovery for drying and food storage applications along with the application of IoT-based temperature control. IoT stands for the Internet of Things. It refers to the network of physical objects or "things"
Published by : http://www.ijert.org
International Journal of Engineering Research & Technology (IJERT)
ISSN: 2278-0181
Volume 13, Issue 12, December 2024
embedded with sensors, software, and connectivity capabilities that enable them to collect and exchange data over the Internet. IoT is a concept that encompasses the interconnection of various physical objects or devices through the internet. These objects, often referred to as "smart" or "connected" devices, are embedded with sensors, actuators, and network connectivity, allowing them to collect, exchange, and act upon data
-
LITERATURE REVIEW
Juan M. Belman-Flores et al. [1] describe the thermal load on a domestic refrigerator as the amount of heat that must be removed from the refrigerator in order to maintain the desired temperature. This heat is typically produced by the food and other materials stored in the refrigerator, as well as by the ambient temperature and humidity. Evaluating the thermal and energy performance of a domestic refrigerator under different thermal loads can help to identify ways to improve the efficiency of the refrigerator, and to optimize its operation to reduce energy consumption and greenhouse gas emissions. There are a number of methods that can be used to evaluate the thermal and energy performance of a domestic refrigerator, such as measuring the power consumption of the refrigerator, monitoring the temperature inside and outside the refrigerator, and analyzing the performance of the refrigeration system. By examining the influence of the thermal load on these factors, it is possible to identify the most effective ways to improve the efficiency of the refrigerator and reduce its energy consumption The thermal load on the refrigerator varies depending upon the number of materials inside the refrigerator. By analyzing the variation of efficiency of refrigerators based on load it is possible to form a relationship between the amount of heat rejected by the refrigerator and the load condition of the refrigerator.
Richard Law et al. [2] describe low-grade heat recovery the process of capturing and using the waste heat produced by industrial processes that operate at relatively low temperatures, such as the food processing industry. Around
11.4TWh of recoverable heat is being wasted every year of which a quarter is produed by the food and drinks processing sector. This waste heat is often rejected to the environment and goes to waste, but it can be used for a variety of purposes, such as preheating ventilation air, heating water, or generating electricity. Also by doing so the dependency on conventional energy sources can be reduced. Implementing low-grade heat recovery can lead to significant energy savings and reduce greenhouse gas emissions. It can also help to reduce the reliance on fossil fuels and contribute to the development of more sustainable industrial systems.
Georgios Maouris et al. [3] explain that CO2 refrigeration systems are refrigeration systems that use carbon dioxide (CO2) as the refrigerant. They are becoming increasingly popular due to their high energy efficiency and low environmental impact. One way that CO2 refrigeration systems can be made even more efficient is by implementing heat recovery and thermal storage systems. These systems capture the waste heat produced by the refrigeration process and use it to providespace heating for the supermarket, rather than allowing it to go to waste. This can lead to significant energy savings and reduced greenhouse gas emissions. Modelling the performanceof such systems can help to optimize their design and operation, and ensure that they are as efficient and effective as possible. Implementing heat recovery systems helps to save energy along with a significant
reductionin greenhouse gases. The waste heat recovered from
CO2 refrigeration systems in places like supermarkets can be directly used for space heating thereby allowing us to reduce the use of electric heaters in cold countries.
V.Naveenprabhu et al. [4] describe a smart hot chamber in a refrigeration system as a device or system that is designed to capture and use the waste heat produced by the refrigeration process for some useful purpose. This can be done using a variety of technologies, such as heat exchangers, thermoelectric generators, or other heat recovery systems. By using the waste heat in this way, the overall efficiency of the refrigeration system can be increased, and energy consumption is reduced by around 40%. A smart energy system refers to a system that is able to optimize the use of energy resources and minimize waste. By capturing and using waste heat in a smart hot chamber, a refrigeration system can become a more integral part of a larger smart energy system, contributing to its overall efficiency and sustainability. Capturing the waste heat from a refrigerator and using it for heating purposes lead to a 40% reduction in energy consumption. A hybrid system like this is capable of handling both heating and cooling without any negative effect on the COP of the refrigerator. The development of such a hybrid
system is also cost-efficient
Alessio Polzot et al. [5] detail that modelling commercial refrigeration systems in conjunction with water storage systems can be an effective way to improve the energy efficiency and performance of heat recovery systems. By modelling the performance of such systems, it is possible to optimize their design and operation and ensure that they are as efficient and effective as possible. In a commercial refrigeration system coupled with a water storage system, waste heat produced by the refrigeration process is captured and used to heat water. The heated water is then stored in the water storage system and can be used for a variety of purposes, such as space heating, hot water provision, or process heating. This can lead to significant energy savings and reduced greenhouse gas emissions, as the waste heat is being used rather than being released to the environment. Modelling the performance of such systems can help to identify the most effective ways to recover and use the waste heat, and to optimize the design and operation of the system to maximize its efficiency. Also a cold sink in the form of water storage helps improve the performance of the entire system.
Lakshya Soni et al. [6] define domestic refrigerators as the common household appliance that is used to store and preserve perishable foods. Like all refrigeration systems, they produce waste heat as a byproduct of the refrigeration process. This waste heat can be captured and used for some useful purpose, rather than being allowed to go to waste. Some possible ways to recover waste heat from domestic refrigerators include using it to preheat ventilation air, heat water, or generate electricity using a thermoelectric generator. Capturing and using the waste heat produced by domestic refrigerators can lead to energy savings and reduced greenhouse gas emissions. It can also help to reduce the reliance on fossil fuels and contribute to the development of more sustainable domestic energy systems. There are many ways in which the waste heat can be captured and utilized. The utilization of waste heat helps improve energy efficiency and reduce the dependency on fossil fuels. There is a significant improvement in the performance of the refrigerator with proper implementation of waste heat recovery.
Robert A Clark et al. [7] conducts an experimental investigation into the feasibility of recovering waste heat from a residential refrigerator. The study involved conducting experiments on a residential refrigerator to quantify the amount of waste heat generated during its operation. A heat recovery system was implemented to capture and utilize this waste heat for space heating purposes. Through careful measurements and analysis, the effectiveness of the heat recovery system and its impact on the refrigerator's energy efficiency are determined. The heat recovery system demonstrated in the study was able to effectively capture a portion of the waste heat and repurpose it for space heating, thereby potentially reducing energy consumption and improving overall energy efficiency. The implementation of a heat recovery system proved successful in capturing and utilizing a portion of the waste heat, offering the possibility of reducing energy consumption and enhancing energy efficiency in households. By repurposing the waste heat for space heating, the study highlights a practical approach to simultaneously improving comfort and conserving energy resource
Ramadan Bassiouny [8] investigates the impact of the space surrounding the condenser of a household refrigerator on its performance and energy efficiency. Through experimental evaluations by systematically varying the spacing between the refrigerator's condenser and surrounding surfaces, simulating different installation conditions, measurements of key parameters, such as condenser temperature, compressor power consumption and overall system performance are taken to analyze the effect of varying the condenser's space. Thus, it is found that the spacing and arrangement of the condenser's surroundings significantly affect the refrigerator's performance. It is also found that inadequate spacing or poor ventilation around the condenser can hinder heat dissipation, leading to higher condenser temperatures and increased compressor power consumption. On the other hand, optimal spacing and adequate airflow around the condenser contribute to improved heat transfer and more efficient refrigerator operation. The experimental results demonstrate that the spacing and arrangement of the condenser's surroundings play a critical role in the dissipation of heat generated by the refrigerator. Inadequate spacing or poor ventilation can hinder heat transfer, leading to higher condenser temperatures and increased compressor power consumption. Also, optimal spacing and sufficient airflow around the condenser contribute to enhanced heat dissipation and improved energy efficiency.
Y.A Patil et al. [9] studied the methods for enhancing the performance of household refrigerators by utilizing heat recovery techniques. The study aims to investigate the potential benefits of recovering and utilizing waste heat from the condenser of a refrigerator. Through experimental analysis, different heat recovery approaches and their impact on the refrigerator's performance are evaluated. The effectiveness of various heat exchangers and systems for capturing and utilizing the waste heat from the condenser is examined. Implementation of heat recovery techniques in household refrigerators has the potential to improve overall performance and energy efficiency also by recovering and utilizing the waste heat from the condenser, it is possible to reduce energy consumption, enhance cooling efficiency, and minimize environmental impact. The experimental analysis
conducted in the study highlights the effectiveness of different heat recovery approaches and systems for capturing and utilizing the waste heat from the condenser. By implementing these techniques, it is feasible to reduce energy consumption and improve cooling efficiency, thereby offering potential environmental and economic advantages..
Reny Varghese et al [10] explores the feasibility and benefits of recovering waste heat from the refrigerator's condenser for other useful purposes. Through experimental investigations and analysis, the effectiveness of the heat recovery system in capturing and utilizing the waste heat generated by the refrigerator's condenser is examined also the impact of the system on energy efficiency, cooling performance and overall operation of the refrigerator are evaluated. The study shows that implementing a heat recovery system in a domestic refrigerator has the potential to improve energy eefficiency and offer additional benefits. The experimental investigations conducted demonstrate the effectiveness of the heat recovery system in capturing and utilizing the waste heat generated by the refrigerator's condenser. By implementing this system, it is possible to improve energy efficiency, reduce energy consumption, and potentially utilize the captured heat for other applications.
-
DESIGN AND DEVELOPMENT
Thermally insulated chamber:The refrigerator condenser coil is directly exposed to the atmosphere for easier rejection of heat. Since the coil is exposed, the heat is directly lost to the atmosphere without much utilization. Hence a chamber is designed and developed that helps contain the heat rejected by the refrigerator for some time. The thermal chamber is made to follow a removable design that can also be fixed or removed from the refrigerator using minimum human effort. This feature is particularly useful in household applications due to the reason that the chamber can be removed and stored when not in use. The human effort required to fix the thermal chamber is reduced by having a simple push-type design that does not require any type of screws or harnesses to hold onto the refrigerator. The only use of screws in the chamber is to have the condenser properly encapsulated from the bottom side of the chamber. Since the chamber is to be fixed on the back side of a refrigerator covering the entire condenser coil the weight is a factor to be considered as a heavier chamber on the backside of the refrigerator might negatively impact its stability. Hence the material chosen was plywood. The reason for selecting plywood as the material is because plywood is cheap, lightweight and it has low thermal conductivity compared to other substitute materials like aluminium.. The chamber has a door opening from the front side and a magnet is used to ensure that the door stays closed while operating. There are two divisions are provided inside the chamber, as shown in Fig .The divisions are made of steel grills with plywood frames. This is where the fruits to be dried are placed. The grill also allows free passage of air through it. To reduce the heat that may escape out of the chamber during operation, a layer of insulation is given on the inside of the chamber. Polystyrene foam is used as insulating material with a layer of aluminium foil given over it. Polystyrene has a thermal conductivity of 0.150W/mK. Polystyrene foam also has a lot of small air pockets that enhance its already significant thermal conductivity. Polystyrene foams are lightweight and are also very cheap. Aluminium foil layers are given to ensure efficient trapping of heat and also to avoid direct contact of food products with polystyrene.
IOT-based temperature control system:In order to control the temperature inside the thermal chamber, a temperature control system is introduced. The system is programmed to reduce the temperature inside the chamber when it goes above a threshold temperature. The temperature control system reduces the temperature of the chamber using a DC fan which is fitted on the bottom right corner of the chamber. The circuit is programmed to run the fan at a variable speed instead of the fixed on/off condition. The variable speed fan helps maintain the required temperature inside the chamber. The entire temperature control system is IOT enabled which means the entire circuit can be remotely observed and controlled. The program allows the user to monitor the temperature of the chamber on their smartphones or personal computers. The IoT is enabled through Blynk.io. Blynk application also provides the interface required by the user to control the threshold temperature and monitor the current temperature and fan speed.
Insualted chamber fixed on refrigerator with circuit and fan IV. RESULT AND DISCUSSION
The testing of the fruit drier by utilizing refrigeration waste heat recovery is tested practically by attempting to dry fruits in it. The system is tested by placing the selected fruit in the chamber and letting it dry for a particular amount of time. The fruits selected for drying purposes are ordinary red grapes and bananas. The fruits are weighed to around 50g each, then placed in the chamber and the refrigerator is turned on. Three tests were conducted with three different samples for a time period of 30 min, 60 min and 90 min and a graph is plotted. After the particular time, the fruits are taken out of the chamber and are weighed again and the readings are noted. The change in their initial and final weight would suggest a loss of moisture from the fruit. Different fruits dry to a different extent in the same
period and hence each sample is weighed after the test time. The temperature rise in the chamber with respect to time is also measured at an interval of 60 seconds and a graph is plotted
Banana slices before and after 30 minute test
Grapes before and after 30 minute test
Banana slices before and after 90 minute test
Grapes before and after 90 minute test
IJERTV13IS120128
(This work is licensed under a Creative Commons Attribution 4.0 International License.)
After testing the three different sets of samples of both fruits, for different time- periods, the following observations were made.
Sl no. |
Fruit |
Time (minute) |
Initial weight (grams) |
Final weight (grams) |
Change in weight (grams) |
1. |
Banana |
30 |
53.26 |
45.58 |
7.68 |
60 |
52.20 |
42.63 |
9.57 |
||
90 |
51.19 |
36.02 |
15.17 |
||
2. |
Grapes |
30 |
51.00 |
50.72 |
0.28 |
60 |
52.51 |
51.52 |
0.99 |
||
90 |
51.24 |
49.89 |
1.35 |
Table 1
Percentage Weight Loss ;
Sl no. |
Fruit |
Time (minute) |
Percentage weight loss (%) |
1. |
Banana |
30 |
14.41 |
60 |
18.35 |
||
90 |
29.63 |
||
2. |
Grapes |
30 |
0.54 |
60 |
1.88 |
||
90 |
2.63 |
Table 2
From the observations Table 1. and Table 2, it is evident that the banana is much more effectively dried. The weight loss percentage of grapes is found to be too low when compared to banana. The banana lost 29.63% of its initial weight whereas grapes just lost 2.63% of its initial weight in the 90- minute session.
The relation between the chamber temperature and time is also noted from an initial temperature of 35 to give insight into how quickly the chamber is getting heated up.
Time vs Weight Loss
Time vs Temperature
The chamber kept increasing in temperature until it reached around 52, beyond which the rate of increase in temperature slowed down drastically. Therefore, this temperature might be the maximum possible temperature that can be reached by the refrigerator without greatly affecting its performance.
-
CONCLUSION
One comprehensive way to handle the urgent problem of dual energy usage in heating and cooling processes is to integrate waste heat recovery technologies. Conventional systems frequently act independently, requiring different energy sources for every task. This can result in inefficiencies and wasteful energy use. But by putting waste heat recovery systems in place, extra thermal energy generated during one process may be collected and used to power another, increasing energy efficiency and decreasing waste.Fruit and other agricultural produce can be dried using waste heat recovery systems, which is one prominent use for them. Fruits such as bananas and grapes have different drying rates, which emphasizes the need of maximizing output and minimizing energy use throughout the drying process.. Given the right conditions, bananas have the potential to dry quickly and effectively due to their faster rate of moisture loss. Conversely, because of their slower rate of moisture loss, grapes would need to be dried for longer periods of time or with alternative methods in order to get results that are equivalenent.Thermal energy that would otherwise disperse into the atmosphere can be redirected
more easily with the use of waste heat recovery systems. This recovered heat can be used for a number of useful purposes, such as space heating, water heating, and more, rather than being thrown away. Households and businesses may both greatly reduce their dependency on traditional energy sources by utilizing this otherwise untapped resource, which will lower overall energy consumption and greenhouse gas emissions. Waste heat recovery systems have a lot to offer in industrial settings in addition to the benefits that are enjoyed at home, especially when it comes to food preparation and preservation. Fruit dryer manufacturers can increase the effectiveness and dependability of their operations even in bad weather situations where traditional drying processes could be unfeasible or inefficient by incorporating waste heat recovery technology into their refrigeration systems. This strengthens the food preservation methods' resilience and advances the industry's general sustainability and environmental stewardship.Incorporating waste heat recovery systems is an essential step in maximizing energy efficiency, encouraging environmental sustainability, and strengthening the robustness of diverse industrial processes, such as food preservation.
-
REFERENCES
-
Belman-Flores, Juan M. "Thermal and energy evaluation of a domestic refrigerator under the influence of the thermal load." Energies 12.3 (2019)
-
Law, Richard, Adam Harvey, and David Reay. "Opportunities for low- grade heat recovery in the UK food processing industry." Applied thermal engineering 53.2 (2013)
-
Maouris, Georgios "CO2 refrigeration system heat recovery and thermal storage modelling for space heating provision in supermarkets: An integrated approach." Applied Energy 264 (2020)
-
Naveenprabhu, V."Smart Hot Chamber in Refrigeration System Based on Waste Heat Recovery." Indian Journal of Science and Technology 12 (2019)
-
Polzot, Alessio "Modelling commercial refrigeration systems coupled with water storage to improve energy efficiency and perform heat recovery." International Journal of Refrigeration 69 (2016)
-
Soni, Lakshya, Pawan Kumar, and Rahul Goyal. "A Review on Waste Heat Recovery From Domestic Refrigerator." Imperial Journal Of Interdisciplinary Research (2016)
-
Clark, Robert A., Richard N. Smith, and Michael K. Jensen. "An experimental study of waste heat recovery from a residential
refrigerator." IECEC 96. 31st Intersociety Energy Conversion Engineering Conference IEEE (1996).
-
Bassiouny, Ramadan. "Evaluating the effect of the space surrounding the condenser of a household refrigerator." International Journal of Refrigeration 32.7 (2009)
-
Patil, Y. A., and H. M. Dange. "Improving the performance of household refrigerator by recovering heat from the condenser." International Journal of Science and Research (IJSR), India Online ISSN (2013)
-
Varghese, Reny. "Heat Recovery System in Domestic Refrigerator." IEEE Sensors Journal (2014)