
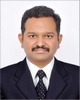
- Open Access
- Authors : Rakesh Namdeti , Prema P.M
- Paper ID : IJERTV11IS120107
- Volume & Issue : Volume 11, Issue 12 (December 2022)
- Published (First Online): 28-12-2022
- ISSN (Online) : 2278-0181
- Publisher Name : IJERT
- License:
This work is licensed under a Creative Commons Attribution 4.0 International License
A Review on Application of Nanomaterials for Corrosion Control and Protection
Rakesh Namdeti*, Prema P.M
Chemical Engineering,
University of Technology and Applied Science-Salalah, Salalah, Sultanate of Oman.
Abstract:- In many sectors, corrosion is an expensive and sometimes deadly problem. The potential use of various nanostructured materials in corrosion protection, prevention, and control is becoming more popular. Nanomaterials are significant because of their distinct qualities, which could lead to new and intriguing uses. This review discusses the current state of nanotechnology application in the field of preventing metal corrosion.
Keywords: Corrosion, Nanocoating, Nanomaterials, Self-healing, Smart Coatings.
-
INTRODUCTION:
Scientists are working to create coatings and structures with improved corrosion and wear resistance. Nanostructures encourage selective oxidation, resulting in the formation of a protective oxide scale with enhanced substrate adherence. Nanocrystalline nc-coatings have been effectively created by thermally activated techniques such as high-speed thermal spraying using oxyfuel1-3.
A polymer nanocomposite coating can effectively combine the advantages of inorganic materials with those of organic polymers, such as elasticity and water resistance4,5. By using nanostructured particles instead of hazardous solvents, improvements in environmental impact can be made. The risky phosphatechromate pretreatment method has been replaced by nanoscale silica6,7.
Nanocomposite coatings based on hydroxyapatite nanoparticles can provide superior corrosion resistance provided by titanium implants. The practicality of protective nc-coatings will rely on how well these materials resist corrosion in general over long periods of service8-9.
-
TYPE OF NANOCOATINGS
-
Nc-alloys' Corrosion Behavior
The size of the grains has a significant impact on their properties, including hardness, wear resistance, and electrical resistivity.The corrosion resistance of nc- Fe32-Ni36-Cr14-P12-B6 is higher than that of its amorphous cousin. FeA18's ability to construct passive films is substantially facilitated in the slightly acidic to weakly basic pH range. The passive layer's protective qualities in the nanostructured alloy are dependent on oxygen content11-15.
NC-state holds significant potential for the creation of protective (fracture, wear and corrosion resistant) nc-coatings. It appears to sustain the better corrosion performance generally seen with traditional pc-Ni and Ni-based alloys. Nc-zinc has a larger activation energy with dissolution than electro-galvanized steel16-17.
NC alloys retain a more perfect passive layer, but the pc-passive material's film stability declines in hostile ion-containing solutions. In nc-alloys, atoms will alloy at a faster rate of diffusion. Such a covering is more durable and less prone to corrosion and stress cracking18-19.
-
Coats Made of Ceramic
Liquid paint contains ceramic nanoparticles that are free to move around as it is applied to vehicles. Depositing nanocoating's made of colloids, such as graphite, is a recent breakthrough in tribology. Co-depositing Al2O3 and TiO2 particles in highly conductive metal electrolytes leads to improved corrosion resistance20-22.
-
Polymer-based paints
Conducting polymers can be mixed with organic or inorganic particles to vary their conductivity, morphology and other properties of physical, based on goal, such as prevention of corrosion. Polyaniline, polythiophene, and polypyrene are a few particular nano conductive polymers that improve corrosion resistance23-26.
"Smart coatings" that release corrosion inhibitors, when necessary, in reaction to stress, a hole, or an electrical or mechanical control signal are made possible by nanostructured materials engineering. Organic corrosion inhibitors are joined to nanoparticles with huge surface areas that may be released on demand27-28.
-
Nanophase coating that self-assembles
SiO2 nanoparticles are electrophoretically coated on AISI 304 stainless steel substrates to create coatings up to 5 mm thick with good corrosion resistance. According to studies, including nanoparticles into the sol can thicken the coating without raising the sintering temperature29.
Zirconia nanoparticles are ideal candidates for coatings as they have reduced porosity and a lower propensity to crack. Corrosion inhibitors are combined with inorganic nanoparticles to create nano reservoirs for self-healing pre-treatments. Doping with cerium nitrate increases the corrosion resistance of this hybrid nanostructured sol-gel coating30-32.
Molecular modeling techniques have been applied to coating processes to better understand complex chemical interactions. SNAP coatings provide barrier-type corrosion protection, but they lack the ability to release corrosion inhibitors upon coating degradation. Multifunctional coatings may be feasible if coating components can be designed from the molecular level up30-34.
-
Biocidal coatings and self-cleaning paints
Surfaces that are biocidal but also simple to clean and even self-cleaning are designed and produced with great care35. Nano particles with an Al2O3 surface treatment help to increase their scratch resistance and hydrophobicity33. In a latest study, Cai37 used an anatase TiO2 layer, an inert coating of sol-gel and a corona treatment.
An EU-funded research project is investigating how to prevent organisms from developing on surfaces in marine environments. Nanostructured surfaces may offer a novel and ecologically friendly solution to the biofouling problem. By employing nano structure to severely restrict organism adherence, the goal of the research is to control fouling34.
-
Application of Nanostructured composite and alloy coatings at high-temperatures
Extreme resistance to corrosion at high temperatures is shared by coatings made of metal-oxide composites, oxide-dispersive alloys, and nanocrystalline alloys. At high temperatures, fine-grained coatings exhibit a rapid creep rate, which can relieve the internal tensions of the scales and lessen their propensity to spallate.
Alloys with 2 wt percent Al could completely form an a-Al2O3 scale at 1000°C in air when the Ni-20Cr-Al coating grain size was 60 nm. The amount of aluminum needed to fully produce a protective oxide scale can be significantly decreased by nc-alloy coatings35.
Titanium alloys and Ti-Al intermetallic may be used in the automotive and aerospace industries due to their outstanding properties of mechanical at high temperatures and resistance to corrosion. They can be employed as high temperature structural materials with the help of nano- or sub-micro alloy coatings made via electro-spark deposition.
-
-
CONCLUSION
From the above various methods of nanocoatings, it is concluded that the alloy and composite coatings are more suitable and economical at the high temperatures. Self-cleaning and self-assembled coatings are suitable in the various types of industries like chemical, refinery and marine vehicles. All polymeric coatings designed to prevent corrosion are normally durable. They can now be used on thick films as a result heat, chemicals, moisture, or salt should never cause them to decay. A ceramic coating will shield the paint against damage caused by water stains, grit from the road, bird droppings, and other contaminants. Nanocrystalline alloys created through adequate annealing treatments of specific aorphous ribbons systems that can be used as soft magnetic materials.
-
REFERENCES
1016.
[14] Barbucci, A., Farne, G., Mattaezzi, P., Riccieri, R. and Cereisola, G., Corrosion behavior of nanocrystalline Cu90Ni10 alloy in neu- tral solution containing chlorides. Corros. Sci., 41, 1999, 463475. [15] Alves, H., Ferreira, M. G. S. and Koster, U., Corrosion behavior of nanocrystalline (Ni70Mo30)90B10 alloys in 0.8 M KOH solution. Corros. Sci., 45, 2003, 18331845. [16] Rofagha, R., Langer, R., El-Sherik, A. M., Erb, U., Palumbo, G. and Aust, A. K., The corrosion behavior of nanocrystalline nickel. Scr. Metall. Mater., 25, 1991, 28672872. [17] Youssef, Kh. M. S., Koch, C. C. and Fedkiw, P. S., Improved cor- rosion behavior of nanocrystalline zinc produced by pulse-current electrodeposition.Corros. Sci., 46, 2004, 5164.
[18] Mishra, R. and Balasubramaniam, R., Effect of nanocrystalline grain size on the electrochemical and corrosion behavior of nickel. Corros. Sci., 46, 2004, 30193029. [19] Jensen, H. and Sorensen, G., Ion bombardment of nano-particle coatings. Surf. Coat. Technol., 84, 1996, 500505. [20] Droniou, P., Fristad, W. E. and Liang, Li. J., Nanoceramic based conversion coating in the paintshop. Coating, 38, 2005, 237239. [21] Shen, G. X., Chen, Y. C., Lin, L., Lin, C. J. and Scantlebury, D., Study on a hydrophobic nano-TiO2 coating and its properties for corrosion protection of metals. Electrochim. Acta, 50, 2005, 5083 5089. [22] Euler, F., Jakob, C., Romanus, H., Spiess, L., Wielage, B., Lampke,T. and Steinha, S., Interface behavior in nickel composite coatings with nanoparticles of oxide ceramic. Electrochim. Acta, 48, 2003, 30633070. [23] Rout, T. K., Jha, G., Singh, A. K., Bandyopadhyay, N. and Mohanty, O. N., Development of conducting polyaniline coating: a novel approach to superior corrosion resistance. Surf. Coat. Technol., 167, 2003, 1624. [24] Wessling, B. and Posdorfer, J., Nanostructures of the dispersed organic metal polyaniline responsible for macroscopic effects in corrosion protection.Synth. Met., 102, 1999, 14001401.
[25] Garcia, B., Lamzoudi, A., Pillier, F., Le, H. N. T. and Deslouis, C., Oxide/polypyrrole composite films for corrosion protection of iron. J. Electrochem.Soc., 149, 2002, 5260.
[26] Yeh, J. M. and Chin, C. P., Structure and properties of poly(o- methoxyaniline)-clay nano-composite materials. J. Appl. Polym. Sci., 88, 2003, 1072 1078. [27] Kendig, M., Hon, M. and Warren, L., Smart corrosion inhibiting coating. Prog. Org. Coat., 47, 2003, 183189. [28] www.tda.com/Library/docs/Cook_MDA_Corrosion.pdf [29] Castro, Y., Ferrari, B., Moreno, R. and Duran, A., Coatings produ- ced by electrophoretic deposition from nano-particulate silica sol gel suspensions.Surf. Coat. Technol., 182, 2004, 199203.
[30] Zheludkevich, M. L., Miranda Salvado, I. M. and Ferreira, M. G. S., Solgel coatings for corrosion protection of metals. J. Mater. Chem., 15, 2005, 50995111. [31] Zheludkevich, M. L., Serra, R., Montemor, M. F., Miranda Sal- vado, I. M. and Ferreira, M. G. S., Corrosion protective properties of nanostructured solgel hybrid coatings to AA2024-T3. Surf. Coat. Technol., 200, 2006, 30843094. [32] Zheludkevich, M. L., Serra, R., Montemor, M. F., Yasakau, K. A., Miranda Salvado, I. M. and Ferreira, M. G. S., Nanostructured solgel coatings doped with cerium nitrate as pre-treatments for AA2024-T3 corrosion protection performance. Electrochim. Acta, 51, 2005, 208217. [33] Voevodin, N. N., Kurdziel, J. W. and Mantz, R., Corrosion protec- tion for aerospace aluminum alloys by Modified Self-assembled NAnophase Particle (MSNAP) solgel. Surf. Coat. Technol., 201, 2006, 10801084. [34] Balbyshev, V. N., Anderson, K. L., Sinsawat, A., Farmer, B. L. and Donley, M. S., Modeling of nano-sized macromolecules in silane-based self- assembled nano-phase particle coatings. Prog. Org. Coat., 47, 2003, 337341. [35] Li, R. and Chen, L., A paint containing nano titanium oxide and nano silver, and its preparation method. Chinese Patent, CN 10027622, 2005.