
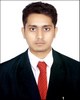
- Open Access
- [post-views]
- Authors : Tushar Shivaji Dhamane , Prashant A. Narwade
- Paper ID : IJERTV10IS100120
- Volume & Issue : Volume 10, Issue 10 (October 2021)
- Published (First Online): 25-10-2021
- ISSN (Online) : 2278-0181
- Publisher Name : IJERT
- License:
This work is licensed under a Creative Commons Attribution 4.0 International License
A Review on Particle Damper Based System for Suppression of Vibration with Modeling and Testing Processes
Tushar Shivaji Dhamane, Prof. Prashant A. Narwade,
M.E Design, Department of Mechanical Engineering Dr. Vithalrao Vikhe Patil Collage of Engineering Savitribai Phule Pune University
Abstract:- Vibrations suppression with help of particle damper for system to prevent it from damage and saving its life is utmost important at high speed vibration. Concepts involved in studying are relationship between the vibration responses and the input force amplitude for varied particle damper parameters like Particle Size (PS), Particle Density (PD). The review covers about particle damper, their numerical methods and basic experimental test processes to measure magnitude of vibrations with FFT analyzer and impact hammer test.
Keywords Particle damper, Particle Size, FFT analyzer and impact hammer.
-
INTRODUCTION
Particle dampers are devices that work by a combination of impact and friction damping. They dissipate the energy of a system by transferring it to a bed of particles. This bed is geometrically constrained to remain inside a container fixed to the vibrating system. As such, the motion-caused interaction occurring inside the container damps the absorbed energy. The main dissipative mechanisms involved are: collisions between the container walls and the particles and between the particles themselves; sliding friction between the same; and, rolling friction between the same. For collisions between the particles and the cavity walls to occur, both should be out-of-phase with each other. This type of damping mechanism allows for relatively empty containers, can work at low frequencies. Its optimization often focuses on the travel time of the particles within the cavity. This damping mechanism is often linked to the work of Masri and Ibrahim[12]. Another important mechanism that is active inside particle dampers relates to the state of matter of the granular medium. For example, gas-like states occur at higher frequencies and solid and liquid-like states occur at lower frequencies and excitation amplitudes. The optimization of that damping mechanism focuses on the state of the vibrated granules in the cavity. Particle damping is also referred to as acceleration damping, multiple impact damping, multi-particle damping, and granular damping, granular-fill damping, and shot damping. Their invention stems from impact dampers, which work similarly but with a single particle. Both damper concepts are shown in Fig. 1, where uvib is the transmitted vibrating motion.
-
BASIC TRADITIONAL PARTICLE DAMPERS
Based on the number of units and particles per unit, the traditional particle dampers can be grouped into four major types: the impact damper, the multi-unit impact damper, the particle damper and the multi-unit particle damper as shown in Fig. 2.1. The development and evolution of these four fundamental types of particle dampers have broken the traditional single design concept, laying a solid foundation for the development of the subsequent multiform particle dampers.
The multi-unit impact damper is the descendant of impact dampers. In 1969, Masri [12] obtained the exact solution for the steady-state motion of a multiple-unit impact damper attached to a sinusoidally excited primary system, verified by numerical simulation and experiments. He found that, compared to the impact damper of equivalent total mass, as to reducing vibration, especially reducing the noise generated during the dampers impact process, properly designed multi-unit impact dampers are
more effective. The increasing interest in the particle damper dates from 1985, when Araki [5] replaced the shock unit of the traditional impact damper containing a single particle with a bed of granular materials. He studied the effectiveness of this kind of impact damper for reducing the vibration of a single-degree-of-freedom (SDOF) system under simple harmonic excitation, and the effect of mass ratio and clearance on the performance of the damper was determined. The non-obstructive particle damper (NOPD), which is one of the most common types of particle dampers, was proposed by Panossian [13] in 1991 through the experiment of an aluminum beam. Such technology consists of making small diameter cavities at appropriate locations inside the vibrating structure, which is capable of yielding the maximum damping effect for any desired mode. The multi-unit particle damper was first put forward by Saeki [14] in 2005. He found that the damping performance of the particle damper depends on the size of the cavity. If the optimum size of the cavity is too large, from the standpoint of practical design, it will lead to excessive clearance and decrease the number of effective collisions between the particles and the wall, which has negative effects on the damping performance. Hence, Saeki divided the cavity into multiple small cavities with an appropriate number and the influence of the number and the size of the cavities on damping performance was studied.
2.0 ROLE OF EMA (EXPERIMENTAL MODAL ANALYSIS) AND FEA (FINITE ELEMENT ANALYSIS) FOR
PARTICLE DAMPER BASED APPLICATION
-
Experimental setups for EMA on the packaged PCB [2]with free and fixed boundary conditions have been shown in Fig. 2. To avoid interference, hammering was performed on the reversed side of the packaged surface, Fig. 4, in which the locations where the accelerometer was affixed are labelled.
-
Fig. 5 shows full three-dimensional FE models built for the packaged PCB with free and fixed boundary conditions. The model for the packaged PCB contained 12,335 linear hexahedral solid elements along with 24 mass elements to take into account the accelerometer mass. For the fixed boundary condition, 192 additional linear spring-damper elements were employed to account for the tightness of screws at the four corners; the torque applied to tighten the screws was 8 kgf-m. The damping effect of the screws was neglected in this study while only the spring effect was considered. The spring constant was assumed to be constant and was to be determined in the subsequent optimization procedure after the material properties of the packaged PCB were determined from the optimization based on EMA and FEA results for the free boundary condition.
-
Final Conclusion includes An equivalent FE model for a standard 132 _ 77 _ 1 mm JEDEC drop test PCB mounted with 13 _ 13 mm packages in a 3 _ 5 full array has been established based on EMA results corresponding to free and fixed boundary conditions. Natural frequencies and mode shapes obtained by EMA and FEA are generally in very good agreement. We also provide modal damping ratios obtained experimentally, which would benefit the transient analysis of the packaged PCB that follows the concept of modal superposition. As a concluding remark, we have demonstrated in this work that overall material properties and screwing tightness of a packaged PCB can be determined by incorporating EMA and FEA along with an optimization Process. This technique is conducive to the FE modelling of complex PCB structures for the design for mechanical reliability.
-
PARTICLE DAMPING NUMERICAL METHODS
-
-
Yokomichi [4] are able to model a system with multiple particles using an equivalent single DOF system. They also consider that a complete bed of particles can be represented by an equivalent single mass body without friction that collides plastically.
-
From Dassault, Elmqvistet al. [5] also presents another multibody-based aproach focusing on correct physical representation of the particle collisions. They rely on a DEM. The DEM formulation was first presented by Cundall and Strack [6] and consists of modeling each particle individually using a contact model that causes viscoelastic forces to be exchanged between the particles. Ehrgott [10] use an axisymmetric finite element method (FEM) to study the impact of particle dampers on a turbine high pressure seal of a space shuttle. They ensure the natural frequency of the damped seal remains unchanged by the addition of the particle damper by using a material for the pellets which has a low modulus of elasticity. They also incorporate their test fixture into the FEM analysis. Their approach models the pellets using their strain energy and they conclude that the method shows limitations due to the underestimation, for certain modes, of the damping they obtained experimentally. Multi-DoF (MDoF) models use springand damper analogy to simulate particle-particle and particle-wall collisions.
-
THE DISCRETE ELEMENT METHOD FOR PARTICLE DAMPERS
The previous section drew attention to the predominance of DEM when simulating particle dampers. Actually, the most popular method to simulate agglomerations of dry macroscopic particles is DEM. Furthermore, the need to simulate the particle bed by individually modeling each particle is reinforced by the following peculiarities [7]:
-
The aspects of the excitation forces will influence whether the particle bed behaves as a fluid, as a solid, or as a gas
-
Granular material does not mix homogeneously as fluids and particles usually aggregate according to their sizes.
Most published DEM simulations model between 100 and 1 million particles [8]. DEM also is often combined with computational fluid dynamics or finite element methods [9]. Such combinations allow modelling the interaction between particles and fluids or deformable elements. The deformable elements can also be the particles themselves. These coupled methods are often classified as extended discrete element methods (XDEM), but this document relies on the term DEM for both coupled and uncoupled methods. Consequently, some aspects that must be taken into consideration to perform DEM simulations are discussed. This section thus covers the detection of contacts in 4.1; normal contact force models in 4.2; tangential and friction force models in 4.3; the coefficients of friction and restitution in 4.4; numerical aspects in 4.5; and, the choice of software toolboxes in 4.6. Focus is mostly given to cases where particle dampers are involved.
-
EXPERIMENTAL TESTING FOR NATURAL FREQUENCY
-
EXPERIMENTAL MODAL TESTING
-
Modal testing is a systematic method for identification of the modal parameters of a structure.
-
Generally these include natural frequencies, modal damping, and UMM mode shapes.
-
In experimental modal testing the structure is excited with a measured force at one or more points and the response are determined at one or more points.
-
From these sets of data, the modal parameters are determined, often by the use of multidimensional curve-fitting routines on a digital computer.
-
Modal testing may use sinusoidal, random, pseudorandom or impulsive excitation.
-
The first step in experimental modal testing is generally to obtain a set of frequency response functions.
-
-
FFT ANALYZER
-
The FRF describes the motion-per-force input, output relationship between two points on a structure as a function of frequency.
-
Since both force and motion are vector quantities, they have directions associated with them.
-
An FRF is actually defined between a single-input DOF (point and direction) and a single-output DOF.
-
In practice, the force and response are usually measured as functions of time, and transformed into the frequency domain using a fast Fourier transform (FFT) analyzer.
-
FFT transforms a signal from time domain representation into its frequency domain representation
-
-
IMPACT HAMMER TEST
-
With the ability to compute FRF measurements in an FFT analyzer, impact testing was developed during the late 1970s, and has become the most popular modal testing method used today. Impact testing is a fast, convenient, and low cost way of finding the modes of machines and structures.
-
-
Impact testing is depicted in Figure 9. The following equipment is required to perform an impact test,
-
An impact hammer with a load cell attached to its head to measure the input force.
-
An accelerometer to measure the response acceleration at a fixed point & direction.
-
A 2 or 4 channel FFT analyzer to compute FRFs.
-
Post-processing modal software for identifying modal parameters and displaying the mode shapes in animation.
A roving hammer test is the most common type of impact test. In this test, the accelerometer is fixed at a single DOF, and the structure is impacted at as many DOFs as desired to define the mode shapes of the structure. Using a 2-channel FFT analyzer, FRFs are computed one at a time, between each impact DOF and the fixed response DOF.
-
Roving Tri-axial Accelerometer Test
The only drawback to a roving hammer test is that all of the points on most structures cannot be impacted in all three directions, so 3D motion cannot be measured at all points.
When 3D motion at each test point is desired in the resulting mode shapes, a roving tri-axial accelerometer is used and the structure is impacted at a fixed DOF with the hammer. Since the tri-axial accelerometer must be simultaneously sampled together with the force data, a 4-channel FFT analyzer is required instead of a 2-channel analyzer.
5.0 RESULT COMPARISON OF PARTCLE DAMPER BASED AND WITHOUT PARTICLE DAMPER
In research made by P Veeramuthuvel1,2, K Shankar2 and K K Sairajan1 they concluded difference of Particle damper and without particle damper based system.
The novel application of particle damping as an external damper capsule has been used for the vibration suppression of a PCB structure in spacecraft applications. The effect of vibration responses with respect to applied forces for the various particle damper systems parameters (PD, PS and PR), various modes and at different measurement locations of PCB are studied from the extensive experiments conducted.
Figure 2 shows particle damper capsule configuration including fasteners and with particles for printed circuit board whereas Figure 6 shows test setup pf PCB for random vibration. Figure below shows one respective test of PCB with and without particle damper showing difference in acceleration.
Out of many trends observed from the experiments, a significant few are (i) the vibration response is significantly lower at higher particle densities and at higher input force magnitude which agree with the reported literatures. As an example, in one of the test configuration, the reduction of vibration response of PCB with a particle damper of mass ratio 7.51% (containing WC particle, PR of 60 %, PS of Ø 1.0mm and at Mode-1) is 5.2 times that of the PCB without particle damper. It can be noted that the responses would significantly go down if the input amplitude force is increased, (ii) the PR of 60% is effective for this type of PCB structure for the three particle materials and modes studied, and (iii) the vibration response is lower for PS of Ø 0.8mm with higher applied forces and particle size of Ø 1.0mm with lower applied forces for tungsten carbide particles in all the three modes.
It is observed that the PS in the range of Ø 0.8mm and Ø 1.0mm is the optimum for the considered case, (iv) the vibration responses are significantly lower even at other measurement locations which are far away from the partice damper location in the PCB. This gives a key input in the practical implementation of particle damper technique in the PCB structure and electronics package design. The obtained design guidelines were used for the implementation of particle damper for a PCB to successfully suppress the vibration under the random vibration environment encountered during the launch of a spacecraft.
6.0 CONCLUSION
From scrutinizing research and work of these authors particle dampers can suppress vibrations coming to applications. Experimental modal analysis and FEA signifies major scope for Particle Dampers. Also different approaches like numerical simulation and DEM simulation increases depth of research for Particle Dampers with different particle sizes, particle density and damping parameters.
7.0 REFERENCES
-
A review of particle damping modeling and testing" By Louis Gagnon , Marco Morandini.
-
Finite element model verification for packaged printed circuit board by experimental modal analysis By Ying-Chih Lee , Bor-Tsuen Wang, Yi-Shao Lai , Chang-Lin Yeh , Rong-Sheng Chen
-
Particle Damping Technology Based Structural Control by Zheng Lu ,Sami F. Masri , Xilin Lu.
-
I. Yokomichi, Y. Araki, Y. Jinnouchi, J. Inoue, Impact damper with granular materials for multibody system, J. Press. Vessel Technol.
-
H. Elmqvist, A. Goteman, V. Roxling, T. Ghandriz, Generic modelica framework for MultiBody contacts and discrete element method, in: Proceedings of the 11th International Modelica Conference, Versailles, France, September 21-23, 2015, Linkping University Electronic Press, 2015.
-
P.A. Cundall, O.D.L. Strack, A discrete numerical model for granular assemblies, Geotechnique.
-
E.M. Campello, A computational model for the simulation of dry granular materials, Int. J. Non-LinearMech.
-
C. OSullivan, Developing robust DEMmodels to simulate element tests, in: Presentation for the Doctoral School of the GEO-RAMP Project, from PDF-Rendered Presentation, 2016.
-
C. Coetzee, Review: calibration of the discrete element method, Powder Technol…
-
R. Ehrgott, H. Panossian, G. Davis, Modeling Techniques for Evaluating the Effectiveness of Particle Damping in Turbomachinery, Tech. Rep. MSFC- 2224,NASA, 2009
-
Experimental investigation of particle damper-based vibration suppression in printed circuit board for spacecraft applications by P Veeramuthuve, K Shankar and K K Sairajan.
-
S.F. Masri, A.M. Ibrahim, Response of the impact damper to stationary random excitation, J. Acoust. Soc.
-
Panossian, H.V. 1992. Structural damping enhancement via non-obstructive particle damping technique. Journal of Vibration and Acoustics.
-
Saeki, M. 2005. Analytical study of multi-particle damping. Journal of Sound and Vibration
-