
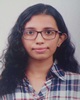
- Open Access
- Authors : Ankeeta Nevrekar , Sakshi Dighe , Siddhant Pawar , Malhardutt Hublikar
- Paper ID : IJERTV10IS100003
- Volume & Issue : Volume 10, Issue 10 (October 2021)
- Published (First Online): 14-10-2021
- ISSN (Online) : 2278-0181
- Publisher Name : IJERT
- License:
This work is licensed under a Creative Commons Attribution 4.0 International License
A Study of Magnetic Piston Repulsion Engine
Ankeeta Nevrekar Malhardutt Hublikar
Mechanical Engineering Mechanical Engineering
University of Mumbai University of Mumbai
Mumbai, India Mumbai, India
Siddhant Pawar Sakshi Dighe
Mechanical Engineering Mechanical Engineering
University of Mumbai University of Mumbai
Mumbai, India Mumbai, India
AbstractThe need and advancements of electric vehicles is well known, the problem with the electric vehicles now available in the market is that they are expensive, thus are difficult for middle-class masses to afford, which form the most percentage of the countrys population. Thus, to avoid this restriction, the best solution is to create a technology that can convert the already used petrol cars into an electric car. The Magnetic Repulsion Piston Engine (MRPE) is a newly found green technology that focuses on running the engine using magnets. It describes an engine that works on the principle of repulsion of two different types of magnets, i.e., a permanent magnet and an electromagnet. The aim of this research is to manufacture an engine that can use the attraction and repulsion between the magnets to create a to-and-fro movement of the piston that would result in the production of power and rotation of the crankshaft with just minor changes in the design of an IC engine. As mentioned previously, repulsion between a permanent magnet and an electromagnet creates the basis of the concept. The cam-valve mechanism of the engine is replaced by an electromagnet and a permanent magnet is attached on top of the piston, this arrangement with proper timing of the flow of current in the electromagnet in order to magnetize and demagnetize, reacts with the permanent magnet and rotates the crankshaft. In our research study, we have calculated the data for working in a single cylinder engine
KeywordsMagnets; Electromagnets; Electric Vehicles; Engine; MRPE; Ceramic magnets
-
INTRODUCTION
We got over with the first decade of the twenty-first century and the chances of having any fossil fuels left by the next three decades are extremely slim. With global warming stepping over its peak, we, as humans, have a burdensome responsibility of at least attempting to save the environment for better generations to come. In order to do so, researchers and scientists have tried to use alternate fuels such as wind energy, solar energy, biogas energy, etc., to generate power and sustain its need for humankind. However, since the energy consumed by us in this generation is exceedingly well above the two-hundred percent mark as compared to the 1900s, it is almost impossible for these alternate fuel options to come to our rescue and satisfy the requirements. Some of these fuels like biogas, even though it is an option to curb the energy needs, still contributes to the increasing pollution. Also, these alternatives need a hefty initial investment which might or might not give the desirable output. Hence, although effective, the use of alternate fuels might not be efficient.
With technology seeing the brightest sun, electric vehicles have made their way into mankinds almost-decimated hope of having a clean environment. India has seen increasing demand for sales in electric vehicles but only restricted to the high-class population. The people lying in the middle-class belt have hardly been the buyers. This may be because the citizens are not as educated or aware of the existing technologies and how they can exploit them or also because India, on the bottom line, is not a rich country. Fifty percent of the Indian population is middle-class which cannot really afford buying an expensive electric vehicle. Also, most of them already have vehicles which they wish to hold on to owing to the fact that they still work smoothly and would not want to discard them. On taking the above points into consideration our main objective of the paper was to figure out a way to make an electric vehicle by doing some modifications in the engine so that we can achieve an electric vehicle which was initially dependent on petrol. This technology involves using a technique called Magnetic Repulsion Piston Engine.
-
LITERATURE REVIEW
The main design and manufacturing methodology was taken from US patent 4317058 [1] wherein Inventor, Sherman S. Blalock, Inola, Okla has given briefs about the Electromagnetic reciprocating engine. The important takeaway from this patent were the engine designed being a V-type engine and has the use of the relays and switches for the timing gears.
Paper[3] describes the methodology for making of MAGNETIC REPULSION PISTON ENGINE for single
cylinder engines. However, from their experiment, it is found out that the energy of the permanent magnet is greater than the electromagnet which causes the permanent magnet to be attracted to the iron core despite the absence of current. Another notable problem was the choice of permanent magnet they had used i.e., NdFeB, which, due to its low mechanical strength could not sustain the stresses developed due to the oscillations.
Paper [4] shares their discussion about their experimental investigation of the magnetised piston powered engine. It mentions the need of the technology, the principle of the invention and its working too, however, the notable
discussion in the paper is the temperature and strengths of permanent magnets at those temperatures along with the simulation analysis showing the strength of the magnetic field at different lengths from the magnet.
Paper [5] describes the procedures and experimental observations made from making a MAGNETIC PISTON ENGINE, also referred to as MAPS, but for the multi cylinder engine. Even though they are able to make a successful prototype, it is suggested to change the design of engine cylinder by using non-magnetic metallic material laminations enhancing the thickness of the cylinder to ensure the magnetism stays contained in the cylinder body itself and does not hamper the other parts of the engine
Paper [6] describes the design and working principle of Electromagnetic Engine. It is observed that they have implemented a hollow piston casing made of non-magnetic stainless steel. Titanium or similar materials of high resistivity and low electrical conductivity also having high thermal resistance. They also suggest using a thin layer of non-magnetic material of sufficient thickness. A notable observation was because of the less current flow, a weaker field was generated causing lesser force of attraction and repulsion limiting the torque capacity.
Paper [7] talks about the complexities and shortcomings of the previous inventions in this subject. According to them, in order to have a better and an efficient electromagnetic engine, one must consider the residual magnetism for electromagnets, the change in the magnetic fields over a range of temperatures, and the decrease in magnetism power of the permanent magnets at higher temperatures. They also give a cautionary note for the use of the neodymium magnets because of their very high strengths.
-
PROPOSED SYSTEM
For the purpose of segmentation of the systems, the components are divided into three major sub-assemblies as:
-
Mechanical system
-
Electrical system
-
Magnets
-
Mechanical system:
The mechanical subsystem includes following parts:
-
Piston It is manufactured from non-magnetic materials like aluminium as per vehicle dimensions. A permanent magnet is fitted on as new dimensions have a reduced thickness to compensatefor the thickness of the permanent magnet to be attached on top of it. This reduces the strength of the piston compared to the original however by increasing the thickness of the piston shell, it compensates for the reduced strength.
Fig 1: Modified piston assembly
-
Connecting rod – The function of connecting rod is to connect the piston with the crankshaft. As the cylinder is expected to contain all the magnetic field in itself, the material of the connecting rod will not be affected much by the magnets. Hence, no major changes are done to the connecting rod.
-
Crankshaft – The reciprocating motion of the piston is converted into useful rotary motion and this is transmitted to the output shaft. It is a link between connecting rod and output shaft.
-
Cylinder – Along with containing the piston assembly, cylinder also houses the lubrication and cooling systems. Traditionally, cylinders are a part of cylinder block along with the cylinder head. However, since this system does not comprise of any valves, the cylinder head is replaced with electromagnet assembly as shown in the diagram.
-
-
Electrical system:
The electrical subsystem has the following sub systems:
-
Frequency Controller – It is made using NE555 timer. It is named so because it has a 5K ohm resistor in it. The general applications of NE555 are to make timers, delays, oscillators, and to generate pulses. They usually have a temperature range of 0-70 degrees, hence it is vital to ensure that the timer circuit does not get over heated and so implementing a temperature sensor is advisory. The frequency of the signals received by the electromagnet determines the frequency rpm of the engine. This is controlled by using a potentiometer whose resistance can be adjusted according to the output from the accelerator pedal sensors as shown in the block diagram.
-
PWM Circuit – PWM stands for Pulse Width Modulation. A PWM circuit gives square waves with on or off signals, duration of on time here is called the pulse width, which is modulated by varying the resistance of the potentiometer, again according to the output from the accelerator pedal sensor. The on time of the pulse is the time for which the signal will pass through the electromagnet, hence determining the strength of the field generated and also controlling the rpm of the engine.
-
Switch from Battery This circuit controls the amount of current to be passed through the electromagnet without burning the other circuit components. In order to produce required rpm, a current value is required, as follows (add table). Hence, according to the input from the accelerator pedal it regulates the value of current flowing through the circuit
-
Safety Circuit – In order to prevent the components from burning a safety circuit is used that will break the contact between the battery and the electromagnet to prevent overheating of the component if there are any instances
Fig 2: Block diagram representing the electrical sub system
-
-
Magnets:
-
Permanent magnets
Magnetism is one of the four fundamental forces in nature. Its occurrence Is due to the alignment of electrons according to their spins when two electrons have opposite rotational spins, they cancel each other. However, in nature, elements do not always have electrons with opposite spins, where in these electrons having same spins, align in a direction causing to attract atoms having opposite spin electrons or repelling atoms having same spins electrons. This phenomenon gives rise to magnetism. Sometimes these electrons do not get neutralised which results in the formation of permanent magnets.
Several types of permanent magnets have been found in nature but the strongest ones of them are the neodymium magnets.
Paper [3] describes the drawbacks of using neodymium magnets as they noticed that the permanent magnet had higher force of attraction which led to the piston being attracted to the electromagnet even when it was not charged along with being brittle and causing other parts of the engine to be attracted to the piston. In the previous iterations of calculations, it is found out the force of attraction produced by the permanent magnet was greater which would lead to the same problem. In order to tackle this drawback, it was suggested to use a permanent magnet with lesser magnetic
pull force but having greater ultimate tensile strength and also higher temperature range.
An alternative to Nd magnets was the ceramic magnets or ferrite magnets which are also the types of permanent magnets, only having lesser strengths compared to rest of the permanent magnets.
1.1 Ceramic magnets
Also called as ferrite magnets, are the most widely used permanent magnets and find their applications in motors and speakers. They are very cost effective and suitable for higher rpms. Another important characteristic of ceramic magnets is that they are electrically insulated and can work in damp conditions, hence having high corrosion resistance. They are available in 27 grades. However, C10 ceramic magnets are used for this application. The specifications are as mentioned in the table no.1
On comparing neodymium and ceramic magnets it is found out that the ceramic magnets are more durable but have lesser magnetic field strengths.
material
BMX (MGOe)
Maximum Operating Temp
@ Pc = 2 (2)
neodymium (NdFeB)
48 ~ 53
80 °C
SmCo
29 ~ 34
300 °C
Alnico
5.5
540 °C
Ferrite (Ceramic)
1.1
250 °C
flexible
0.6
115.5 °C
Table no 1. Properties of Permanent Magnets
-
Electromagnet –
Electromagnetism is responsible for the force of attraction and repulsion between the electrons and atoms. An electromagnet is a current carrying conductor that produces magnetism when charged. However, by controlling the amount and direction of current it is possible to change the direction and strength of the magnetic field. Here, there are several types of electromagnets, like solenoid, torrid which find applications in conveyor belts and speakers. A solenoid is made of a soft iron core. It is wrapped with 1000 coils of copper wire of gauge 12.
The soft iron core is selected for its high susceptibility and very less retentivity. The permeability of this iron core is 1.2 mH/m. The number of turns of the copper wire are chosen considering the amount of force produced by the electromagnet. The gauge of the copper wire is selected considering the current capacity of the wire. This electromagnet assembly is placed in the position of the cylinder head as shown in fig-3 below.
Fig 3: Piston cylinder assembly with electromagnet
-
WORKING
On starting the vehicle, a current is supplied to the battery to the starter switch and it is turned on as the user accelerates the position of the accelerator pedal is taken as an input for the frequency controller and the PWM circuit. This combined circuit gives a signal whose frequency is comparable to the engine output rpm
-
CALCULATIONS Case 1: Force calculations for Nd52 magnet. Input Voltage=6V
Input Current= 1 Amp Input Power=6 W
Maximum Force exerted by electromagnet on piston, F1=N2×I2×K×A/2×G2
N=Number of turns=1000 K=Permeability =4o
A=Cross-Sectional area of electromagnet
G=Least distance between electromagnet and permanent magnet =0.005m
We get,
F1= 55.447N
F2= Force exerted by permanent magnet =B2×A /2o B=Flux density (T)=0.075 T at a distance G A=Cross-sectional area of permanent magnet Putting these values, F2=52.809 N
Total force, F=F1+ F2 = 108.265 N
Case 2 Force calculations for Ceramic C10 magnet. Input Voltage=6V
Input Current= 1 Amp Input Power=6 W
Maximum Force exerted by electromagnet on piston, F1=N2×I2×K×A/2×G2
N=Number of turns=1000 K=Permeability =4o
A=Cross-Sectional area of electromagnet
G=Least distance between electromagnet and permanent magnet =0.005m
We get,
F1= 55.447 N
F2= Force exerted by permanent magnet =B2×A /2o B=Flux density (T)=0.075 T at a distance G A=Cross-sectional area of permanent magnet Putting these values, F2=4.996 N
Total force, F=F1+ F2 = 60.447N
This force is transmitted through the shaft to the wheels
It is observed that force F1 and F2 is almost similar in case 1 while F1 is very much greater than F2 in case 2.
-
CONCLUSIONS
One of the problems faced in the previous iterations were the difference between the energies of the permanent magnet and electromagnet which made the iron core to be attracted to the piston head even if it was switched off, however by replacing Nd magnet with Ceramic magnet eliminates this issue as the ceramic magnets have weaker field strengths compared to Nd magnets.
In order to shield the magnetism of the permanent magnet and to ensure smooth working of the engine the piston is replaced by a hollow piston casing as shown in the diagram which is made of nonmagnetic material, which shields off the magnetic field from the other parts of the engine.
It is observed that the NE555 timer circuit cannot take high currents and hence it can get burned. The implementation of safety circuit with the help of temperature and current sensors is done so it always keeps in check and regulate the current flow.
-
REFERENCES
-
Piyush Hota, Mahima Rathore, Danish Shaikh Magnetic repulsion piston engine IJSR 2013
-
Ramanan. M, Balasubramanian. M, and Ilaiyaraja. S,Experimental Investigation on MagnetizedK. Elissa,
-
Abil Joseph Eapen, AbyEshowVarughese, Arun T.P, and Athul T.N, Electromagnetic Engine, IJRET, 2014
-
J. Rithula, J. Jeyashruthi and Y Anandhi, Electric Vehicle with Zero- fuel ElectromagneticAutomobileEngine,IJERT,
-
Shirsendu Das, An Electromagnetic Mechanism Which Works Like an Engine, IJETT, 2013.