
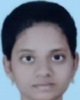
- Open Access
- Authors : Katta Deepika, Bhukya Vamsi Prasad, Kanaparthi Yuvateja, P Narendhra Babu, N A G K Manikanta Kopuri
- Paper ID : IJERTV13IS030055
- Volume & Issue : Volume 13, Issue 03 (March 2024)
- Published (First Online): 21-03-2024
- ISSN (Online) : 2278-0181
- Publisher Name : IJERT
- License:
This work is licensed under a Creative Commons Attribution 4.0 International License
A Study on Concrete with Quarry-Dust as Partial Replacement to Fine Aggregate
Katta Deepika, Bhukya Vamsi Prasad, Kanaparthi Yuvateja, P Narendhra Babu, N A G K Manikanta Kopuri
UGStudentsFinalYear, Associate professor & HOD, Associate professor Department of Civil Engineering, NRI Institute of Technology, Agriripalli, India
Abstract – This experimental study is conducted to analyze the behaviour characteristics of concrete where Quarry-Dust is partially replaced with fine aggregate. M30 grade concrete has been chosen as the reference concrete specimen. This will not only allow the sustainable use of aggregates available to us but also provide an effective and mass management of quarry dust. This quarry dust is replaced as 20%, 40%, 60% to the fine aggregate. In this study compressive strength and split tensile of concrete was evaluated to investigate the optimal use of quarry dust as fine aggregate in concrete.
KeyWords: Cement, River Sand, Quarry-Dust (QD), Coarse Aggregate
-
INTRODUCTION
Concrete is a widely used construction material due to its strength and durability. However, the production of concrete requires a significant amount of natural resources, such as fine & coarse aggregates like gravel and sand. A very large amounts of quarry dust extracted while crushing and sizzling the stones and mountains, cumulate in the world every year out of which 275 million in the India and around 180 million in European Union. One of the most popular methods to get rid of this quarry dust is to fill in open areas, and even though it is fine or coarse state it is difficult to dispose due to large consumption area. However, this quarry dust higher amounts can be utilized Constructions as filling, plastering motor etc. One of such applications that could use waste fine powdered quarry dust effectively in concrete. Concrete can be making more available in the local market than sand which also affordable and available at nearby quarry sites.
Partial replacement of quarry dust aggregates in concrete has the additional advantage of saving in natural aggregates used in the production of concrete which are becoming increasingly scarce. Quarry-Dust is more workable compare to normal concrete. Global warming and environment destruction have come forward as a major issue in the recent years. Started alarming in engineers mind, especially in civil engineers mind. Looking forward for finding out the solution of these issues and also the use of more and more environment friendly materials in every Industry particularly construction industry is a paramount importance. Civil engineers start thinking about concrete, which is more dominant product to be used by civil engineers to make it environment friendly.
-
LITERATURE REVIEW
Various researches for the partial replacement of fine aggregate with quarry dust, which are related to my work, areas under:
Ilangovan et al. (2008) Studied and reported that the strength of Quarry Rock Dust concrete is comparatively 10% to 12% more than that of similar mix of Conventional Concrete. The permeability of Quarry Rock Dust concrete isless compared to that of conventional concrete. The water absorption of Quarry Rock Dust concrete is slightly higher than Conventional Concrete. IIangovan gives attention to physical and chemical properties of quarry dust with respect to requirements of codal provision which are satisfied. The 100% replacement of sand with quarry dust gives better results in terms of compressive strength studies.
Sivakumar et al. (2010) The 28 days compressive strength of 100% replacement of sand with quarry dust of mortar cube (CM1:1) is higher than the controlled cement mortar cube. The 56 days maximum Compressive strength, split tensile strength and modulus of elasticity of concrete for 100% replacement of sand with quarry dust of 400 kg/m3 at F/C=0.6, was higher than the reference concrete.
Bhikshma et al. (2010) The stone dust as replacement for natural sand enhances the strength of concrete mix. The rough profile of stone dust provides good interlocking and bond between ultra-fine particles of cement paste. The concrete is less permeable and durable than conventional concrete with river sand. The compressive strength increased significantly up to about 20% for concrete with crusher dust compared to conventional concrete.
Nagabhushana et al. (2011) The strength of mortar containing 40% Crushed Rock Powder is much higher than normal mortar containing only sand as fine aggregate. It is concluded that the compressive strength, split tensile strength and flexural strengths of concrete are not affected with the replacement of sand by CRP as fine aggregate up to 40%.
Lohani et al. (2012) The slump value increases with increase in percentage replacement of sand with quarry dust. The increase in dust content up to 30% increases compressive strength of concrete, if the dust content is more than 30% the compressive strength decreases gradually. But the compressive strength of quarry dust concrete continues to increase with age for all the percentage of quarry dust contents.
Joseph O Ukpata et al. (2012) The workability of concrete using lateritic sand and quarry dust as fine aggregates was found to have the same trend with normal concrete. The density of hardened concrete using lateritic sand and quarry dust was found to range from 2293-2447 kg/m.
Rajput et al (2018) The nominal mixes were prepared for grades M-20 and M-30 of cement concrete as per Indian Standards codes using natural sand (NS) and replacement of NS sand to crushed stone dust (CSD) in different proportions. The results of the study show that, the strength properties of cement concrete using crushed rock sand is higher and homogeneous to the conventional concrete.
Hmaid Mir The suitability of quarry dust as a sand replacement material shows that the mechanical properties are improved and also elastic modulus. The compressive strength achieved optimum by replacing fine aggregate with quarry dust in ratio of 60:40 .
Felekoglu et al Observed that the incorporation of quarry waste at the same cement content generally reduced the super plasticizer requirement and improved the 28 days compressive strength of SCC. Normal strength SCC mixtures that contain approximately 300310Kg of cement per cubic meter can be successfully prepared by employing high amount of quarry waste.
Sukumar et al Found that the relations have been established for the increase in compressive strength at premature ages of curing (12h to 28 days) for different grades of SCC mixes and are compared with the IS Code formula for straight concrete as per IS: SP 23-1982.
Ho et al Explained that the granite fines can be used in the SCC production. However, it is important to spot out that, as a waste material, the properties of stone fines are likely to vary with time. Then, after that, the fineness of granite fines could solve durability problems, such as silica-alkali reactions. These two issues would require to be addressed if the material is to be used with assurance.
Dehwah Utilization of quarry dust in concrete is recommended particularly in regions where sand is not easily available
Muhit et al Determined that passing from 200mm sieve is used as cement replacement whereas retaining from 100mm sieve is used as sand replacement. Cement was replaced with stone dust in percentage of 3, 5, and 7 percent. Similarly, sand was replaced with stone dust in percentage of 15 to 50 with an increase of 5 percent. Test result gives that compressive strength of mould with 35% of sand and 3% of cement replacing dustincreases to 21.33% and 22.76% in that order compared to the normal mortar mould at 7 and 28 days for tensile strength which increased to 13.47%.
Soutsos et al The physical characteristics of recycled destruction aggregates may unfavorably affect the properties of the blocks. However, levels of replacement of quarried stone aggregates with destruction recycled aggregates determined that it will not have significant harmful effect on the compressive strength.
Chitlange and Pajgade It is observed that there is consistent increase in the strength of plain concrete when natural sand is fully replaced by quarry dust.
-
EXPERIMENTAL STUDY
-
CEMENT Cement when mixed with minerals fragments and water, binds the particles into a whole compact. Cement is the most important and costliest ingredient of concrete. Portland Pozzolana cement of 53 grade.
Table-1: Tests Results of Cement
S.NO
PROPERTIES
RESULT
1
Normal Consistency
30 %
2
Initial Setting Time &
Final Setting Time
45 min & 330 min
3
Fineness
5%
4
Specific Gravity
3.15
-
FINE AGGREGATE
Fine aggregate is defined as material that will pass a 4.75mm sieve. For increased workability and for economy as reflected by use of less cement, the fine aggregate should have a rounded shape (As per IS 383-2016).
-
SAND
Fine aggregate is defined as material that will pass a 4.75mm sieve. For increased workability and for economy as reflected by use of less cement, the fine aggregate should have a rounded shape. The purpose of the fine aggregate is to fill the voids in the coarse aggregate and to act as a workability agent.
Figure 1: Sand
-
QUARRY DUST
Quarry-Dust is the material which is obtained while crushing the stone. Quarry dust is small sand-sized particles and washed to be used in Constructions.
Figure 2: Quarry dust
TABLE: 2 Tests results of Fine Aggregate:
S.NO
PROPERTIES
SAND
QUARRY DUST
1
Specific Gravity
2.52
2.71
2
Fineness Modulus
2.55
2.41
3
Bulking
32 %
28 %
4
ZONE
II
-
-
Coarse Aggregate Coarse Aggregates can be defined as irregular broken stone or naturally-occurrin grounded gravel used for making concrete. Coarse aggregate curtained on the sieve of mesh size 4.75mm. It acts as volume increasing component and is responsible for strength, hardness and durability of concrete (As per IS 383-2016)
Figure 3: Coarse aggregate
TABLE: 3 Tests Results of Coarse Aggregate
S.NO
PROPERTIES
RESULTS
1
Specific Gravity
2.71
2
Fineness Modulus
7.2
3
Aggregate Impact Value
21.36 %
4
Aggregate Crushing Value
21.06 %
70
70
-
-
RESULTS AND DISCUSSIONS:
-
COMPRESSIVE STRENGTH VALUES
60
60
55.45
51.66
55.45
51.66
56
52.22
56
52.22
56.95
53.88
56.95
53.88
58
54.04
58
54.04
50
50
48.66
48.66
43.55
43.55
43.77
43.77
44.89
44.89
40
40
7 Days
14 Days
28 Days
7 Days
14 Days
28 Days
COMPRESSIVE STRENGTH N/mm2
COMPRESSIVE STRENGTH N/mm2
The strength in compression has a definite relationship with all other properties of concrete In India cubical moulds of size 150mm X 150mm X 150mm had casted and tested for 7days, 14 days and 28days. The test results are tabulated below.
30
20
30
20
10
10
Figure 4: Cube Under Compressive Testing Machine
0
0
0% 20% 40% 60%
% REPLACEMENT OF QUARRY DUST
0% 20% 40% 60%
% REPLACEMENT OF QUARRY DUST
S. NO
% REPLACEMENT OF
QUARRY-DUST
COMPRESSIVE STRENGTH (N/mm2)
7
DAYS
14
DAYS
28
DAYS
1
0
43.55
51.66
55.45
2
20
43.77
52.22
56.00
3
40
44.89
53.88
56.95
4
60
48.66
54.04
58.00
S. NO
% REPLACEMENT OF
QUARRY-DUST
COMPRESSIVE STRENGTH (N/mm2)
7
DAYS
14
DAYS
28
DAYS
1
0
43.55
51.66
55.45
2
20
43.77
52.22
56.00
3
40
44.89
53.88
56.95
4
60
48.66
54.04
58.00
TABLE-4 Compressive Strength of Cubes At 7, 14 And 28 Days of Curing
Figure 5: Compressive strength VS % Replacement of quarry dust
-
SPLIT TENSILE STRENGTH:
The split tensile strength obtained by testing the specimen for M30 grade of concrete to all the mixes designed for various replacement given below.
Figure 6: Cylinder under Split Tensile Testing Machine
4.17
4.17
4.26
4.26
4.44
4.44
3.68
3.34
3.68
3.34
SPLIT TENSILE
STRENGTH N/mm2
SPLIT TENSILE
STRENGTH N/mm2
Table-5 Split Tensile Strength of Cylinders at 7, 14 & 28 Days of Curing
S. NO
% REPLACEMENT OF QUARRY – DUST
SPLIT TENSILE STRENGTH (N/mm2)
7 DAYS
14 DAYS
28 DAYS
1
0
2.55
2.64
4.17
2
10
3.11
3.25
4.26
3
20
3.22
3.34
4.44
4
30
3.34
3.68
4.67
5
4.5
4
3.5
3
2.5
2
1.5
1
0.5
0
4.67
5
4.5
4
3.5
3
2.5
2
1.5
1
0.5
0
4.67
0% 20% 40% 60%
% REPLACEMENT OF QUARRY-DUST
0% 20% 40% 60%
% REPLACEMENT OF QUARRY-DUST
3.113.25
3.113.25
3.223.34
3.223.34
2.552.64
2.552.64
7 Days
14 Days
28 Days
7 Days
14Days
28 Days
Figure 7: Split tensile strength VS % Replacement of quarry dust
-
-
CONCLUSIONS:
Based on the above experimental testing following conclusion were drawn
-
Compressive and split tensile strength values are increased up to 60 % replacement of quarry dust to fine aggregate.
-
All compressive strength results are more than the target mean compressive strength of concrete.
REFERENCES
-
Ilangovan R, Mahendrana N and Nagamanib K Strength anddurability properties concrete containing quarry rock dust as fine aggregate, ARPN Journal of Engineering and Applied Sciences, ISSN (2008).
-
Joseph O Ukpata, Maurice E Ephraim and Godwin A Akeke,Compressive strength of concrete using lateritic sand and quarry dust as fine aggregate, ARPN Journal of Engineering and Applied Sciences, (2012).
-
Lohani T K, Padhi M, Dash K P and Jena S Optimum utilization of Quarrydust as partial replacement of sand in concrete, international Journal of Applied Science and Research, Vol. 1, No. 2.117 Int. J. Struct. & Civil Engg. Res. 2014 Kumar S et al., 2014(2012),
-
Nagabhushana and SharadabaiH ,Use of crushed rock powder as replacement of fine aggregate in mortar and concrete , Indian Journal of Science and Techno., (2011).
-
Radhikesh P Nanda., Amiya K Das and Moharana N C,Stone crusher dust as a fine aggregate in Concrete for paving blocks, International Journal of Civil and Structural Engineering, (2010).
-
Shiva Kumar and Praksah Characteristic studies on the mechanicalproperties of quarry dust addition inconventional concrete, Journal of CivilEngineering and ConstructionTechnology, (2011).
-
Md.Safiuddin, S.N.Raman and M.F.M. Zain, Utilization of Quarry waste fine Aggregate inconcrete mixures, 2007 Journal of Applied sciences research 3(3)
-
The text book of Concrete Technology byM. S. Shetty
-
M. N. Soutsos, K. Tang, and S. G. Millard, Concrete building blocks made with recycleddemolition aggregate, Construction and Building Materials, vol. 25, no. 2, pp. 726 735,2011
-
M. R. Chitlange and P. S. Pajgade, Strength appraisal of artificial sand as fine aggregate in SFRC, ARPN Journal of Engineering and Applied Sciences, vol. 5, no. 10, pp. 34 38,2010.
-
M. Devi and K. Kannan, Analysis of strength and corrosion resistance behavior of inhibitors in concrete containing quarry dust as fine aggregate,Journal of Engineering and Applied Sciences, vol. 6, no. 11, pp. 124 135, 2011.
-
R. P. Nanda, A. K. Das, and N. Moharana, Stone crusher dust as a fine aggregate inconcrete for paving blocks, International Journal of Civil and Structural Engineering, vol.1, no. 3, p. 613, 2010.
-
B.P.Hudson, Manufactured sand for concrete, The Indian ConcreteJournal, May 1997 , pp237-240
-
Indian standard recommended method of concrete mix design(IS 10262 – 2009).
-
Baalbaki, W., Benmokrane, B., Chaallal, O and Aitcin,P.C (1991). Influence of coarse aggregate on Elasticproperties of Highperformance concrete, ACI MaterialsJournal, 88(5):499- 503.
-
Ho, D.W.S., Sheinn, A.M.M., Ng, C.C and Tam C.T (2002).The use of quarry dust for SCC applications, Cement andConcrete Research 32 (2002) 505511.
-
Draft (2005). Sydney Construction Materials Strategy Newnes Plateau – Draft Issues Paper
-
Reddy, M.V and Reddy, C.N.V.S (2007). An ExperimentalStudy on use of Rock Flour and Insulator Ceramic Scrap inConcrete, IE
-
Journal CV, 88: 47-50
-
-
A.K.Sahu, Sunil kumar and A.K.Sachan, Crushed stone waste as fine aggregate for concrete, The Indian Concrete Journal, January 2003 pp845-847.
-
J. Karthik, T.Rama, IIIN. Mani Bharathi (July-September, 2014)
An Experimental Study on Usage of Quarry Rock D
-
ust as PartialReplacement for Sand in Concrete.
Volume 1, Issue 1 (July-Sept,2014).