
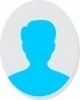
- Open Access
- Authors : Sushma Kumari, Harinder Pal, Sagarika Pal, Sushma Kumari
- Paper ID : IJERTV12IS060195
- Volume & Issue : Volume 12, Issue 06 (June 2023)
- Published (First Online): 08-07-2023
- ISSN (Online) : 2278-0181
- Publisher Name : IJERT
- License:
This work is licensed under a Creative Commons Attribution 4.0 International License
A Study on Handloom Made Bamboo/ Cotton Fabric-Part-1: Impact of Blend Ration and Weave on Physical Properties
Sushma Kumari, Harinder Pal & Sagarika Pal
Dept. of Fashion Technology, Bhagat Phool Singh Mahila Vishwavidyalaya, Sonepat, Haryana
*Corresponding Author: Sushma Kumari,
M.Tech Scholar, Department of Fashion Technology,
Bhagat Phool Singh Mahila Vishwavidyalaya, Khanpur Kalan, Sonepat, Haryana- 131305
Abstract : The purpose of the study is to investigate physical properties of bamboo/cotton fabric developed on handloom to examine the impact of constructional parameters which includes weave and blend ration. The bamboo yarn was chosen as an alternative to promote sustainability when compared with synthetic as well as cotton. Six woven samples were prepared on handloom with different blend ratio of yarn and weave structure. 100% cotton of 2/20s yarn was used in warp direction for all fabric samples and 100% cotton, 50/50 (bamboo/cotton), and 100% bamboo yarn was used as weft yarn. Three samples each for plain and twill were made on handloom. Analysis of all samples demonstrates that the weave structure and yarn blend ratio influences on fabric characteristics. Results indicate that the use of bamboo fiber influences the physical properties in adding values to fabric characteristics apart from its environmental sustainability. Greater fiber length, lesser fiber density with more moisture regain gives an edge to bamboo-cotton blend when compared with only cotton fabric. Lower Drape coefficient of bamboo-cotton blend offers more flexibility to fabric ability is influenced. The study also advocates the use of bamboo fiber in handloom industry, which could be seen as promising scope for consumers and entrepreneurs who are in environmental conscious.
Keywords: Bamboo, Cotton, Woven Fabric, Handloom, Sustainability
-
INTRODUCTION
The textile industry is the most polluting sector in the world and has a hazardous impact on the environment in several ways starting from the extraction of raw materials to the final disposal of clothing [1, 2]. Most of the synthetic fibers are made from petroleum-based chemicals, which are non-renewable resources that contribute to greenhouse gas emissions and climate change. The production of synthetic fibers also requires a lot of energy, much of which comes from non-renewable sources such as coal or natural gas. Synthetic fibers are not biodegradable and can take hundreds of years to break down in landfills, contributing to the growing problem of textile waste. To reduce the negative environmental impact of synthetic fiber production, sustainable alternatives such as recycled polyester or bio-based fibers made from renewable resources like corn or bamboo are being developed. Additionally, reducing overall consumption and increasing the use of natural fibers can also help mitigate the negative environmental impact of synthetic fiber production. While cotton is a natural fiber, its production can still have negative impact on the environment, particularly when conventional farming practices are used [3]. Conventional cotton farming often involves huge amount of water consumption. This can put a strain on local water resources, particularly in regions that are already experiencing water scarcity. Their productions also consume large amounts of pesticides and fertilizers to protect it from pests and maximize yields. These chemicals can have negative impacts on the environment, including soil degradation, water pollution, and can be harmful to non-target organisms such as bees and other pollinators. Even the textile processing units involves a lot of water usage, and the wastewater generated can contain harmful chemicals such as dyes, heavy metals, and other pollutants that can end up in water ways. The chemicals used in textile production can be harmful to both the environment and human health, as many are known to be carcinogenic or have other negative health effects [4, 5].
To address environmental issues, there are a number of sustainable practices that the textile industry can adopt, such as using organic and recycled materials, reducing water usage and pollution, minimizing waste, and using renewable energy sources [6]. Additionally, consumers can play a role in promoting sustainability by choosing eco-friendly clothing options and supporting companies that prioritize sustainability. Sustainable fiber plays a role in meeting the needs and demands of the textile market while enhancing product quality in terms of comfortability [7]. The most significant feature of sustainable fibers is their renewability, biodegradability and their other properties [8]. Aloe-Vera, banana, sisal, hemp, jute, bamboo, milk fiber, corn, soya, groundnut shell, areca nut, lyocell, and eucalyptus are some of the sources to produce sustainable fibers. This study employs the use of bamboo fiber in different blend ration with cotton. This paper covers the investigation of bamboo yarn used in fabric
production on handloom as a mean to achieve sustainability to some extent in textile industry. Bamboo is a highly sustainable material that can be used in clothing in a number of ways. Bamboo is a fast-growing plant that requires very little water and no pesticides or fertilizers to grow. Bamboo also has a lower carbon footprint due to its ability to absorb large amounts of carbon dioxide from the atmosphere during its growth. Bamboo clothing is also biodegradable, which means that it can be broken down naturally in the environment without leaving behind harmful pollutants or micro plastics. Bamboo clothing is naturally antibacterial and moisture-wicking, which can help to reduce odor and keep the wearer cool and comfortable [6]. Overall, bamboo clothing has the potential to be a more sustainable option than many other materials used in clothing production. By choosing bamboo clothing, consumers can help to reduce the environmental impact of their clothing choices and support more sustainable practices in the textile industry. Bamboo yarn along with cotton yarn was used to produce fabric on handloom to promote environmental sustainability. The handloom industry offers several sustainable solutions in the textile sector. Handloom weaving is a low-impact, labor-intensive process that requires minimal use of electricity, water, and other resources. It has much lower carbon footprint than those produced by industrial processes. By supporting the handloom industry, consumers can help to preserve these traditions and support local artisans and communities.
-
LITERATURE REVIEW
Prakash Chidambaram and Ramakrishnan Govindan studied the influence of blend ratio on thermal properties of bamboo/ cotton blended woven fabrics [9] and found that bamboo fabric has substantially more air and water permeable, more absorbent, have lower thermal resistance and yield higher wicking than the equivalent fabrics produced with cotton fabrics. Ajay Rathod et al.[10], studied physical characteristics of bamboo & bamboo-cotton blended yarn fabrics, and exhibits that higher breaking strength and higher elongation in 100% bamboo than blended yarn fabrics. Shivaraj R. Kulkarni et al. [4] reported that the main motive of blending is to minimization of cost and to increase the utility of Bamboo with Cotton. K Avinash [11] examined ultraviolet radiation protection of human through protection covering and found that bamboo fabric has shown higher ultraviolet protection factor than cotton fabric. Vinitha paulose et al. [12], analyzed anti-bacterial efficacy in bamboo and bamboo /Cotton Handloom Fabrics finished with selected herbal extracts and cocluded that the herbal extracts of the three medicinal plants selected in equal proportion can be used to develop herbal anti-bacterial finished eco-fabrics for a healthier life and the use of natural finishing agents for textile fabrics which ensures a safe and sustainable end product. Singh Manju & Pal Harinder [5], compared handloom denim using bamboo and cotton yarn for their handle, mechanical and comfort properties and the result concluded that fabric made from bamboo fiber has a better elongation %, tearing strength, better flexibility, but lesser crease recovery as compared to fabric made from cotton.
Smita Bhuyanand and Nabaneeta Gogoi have reported following fiber properties of bamboo and cotton along with their fiber specification. Results in Table: -1 indicates higher fiber length but with slight coarser fineness when compared with cotton fiber. Density of bamboo fiber is much lesser than cotton fiber which makes it lighter in weight. Bamboo fiber has remarkable moisture regain as compared to cotton fiber. Bamboo fiber has more tensile strength than cotton in dry condition but loses in wet condition. [9, 13, 14, 15]
Table: 1- Fiber properties
Fiber properties
Fiber length (mm)
Fiber fineness (dtex)
Density (g/cm3 )
Moisture regain (%)
Dry tenacity (cN/dtex)
Wet tenacity (cN/dtex)
Tensile strength (MPa)
Bamboo
38-76
1.3-5.6
0.8-1.32
13.03
2.33
1.37
140-1150
Cotton
25-45
1.2-2.8
1.5-1.54
8.5
1.9-3.1
2.2-3.1
264-654
-
EXPERIMENTAL WORK
3.1 Material and Method
In this study, six woven fabric samples with different specifications using bamboo and cotton yarn were prepared on a handloom. Single warp beam using 100 % cotton yarn of 2/20s was prepared and in weft direction samples were prepared using three different yarns; 100 % cotton, 50:50 bamboo-cotton and 100 % bamboo. Three samples with plain weave and three samples with twill weave were produced with different blend ratio. Different properties as per standards have been evaluated to investigate the physical properties of fabrics. The detail of fabric specification as produced on handloom is given below:
Table 2: Constructional parameters of samples
Sample ID
Yarn blend ratio
Structure
Warp yarns
Weft yarns
Count of yarns
EPI
PPI
S1
100%C
Plain
100% C
100% C
2/20s
46
32
S2
50:50 (C:B)
Plain
100% C
50/50 (B/C)
2/20s
46
35
S3
100% B
Plain
100% C
100%B
2/20s
46
36
S4
100%C
Twill
100% C
100% C
2/20s
46
46
S5
50:50 (C:B)
Twill
100% C
50/50 (B/C)
2/20s
46
48
S6
100% B
Twill
100% C
100%B
2/20s
46
49
-
RESULTS& DISCUSSION
Attempt was made to produce samples with constructional parameters in control but due to manual control on handloom and weaving the material by the researcher herself lead to the variation in picks per inch, which may have influenced various physical properties as shown in Table 3.
Table 3: Physical properties of all samples
Sample ID.
Yarn blend ratio
Structure
GSM
Thickness
Crimp%
Drape coefficient
Fabric shrinkage
%
(gm/m2)
(in mm)
warp
Weft
S1
100%C
Plain
200
0.53
16.8
8
0.59
8.82
S2
50:50 (C:B)
Plain
210
0.48
15
12
0.56
10.72
S3
100% B
Plain
216
0.47
13.8
12.2
0.54
10.82
S4
100%C
Twill
237
0.58
11.4
8.4
0.5
8.8
S5
50:50 (C:B)
Twill
248
0.57
6.6
16
0.46
8.82
S6
100% B
Twill
256
0.56
6.2
16.8
0.44
10.76
-
Thread density
Thread density
50
Yarns Per Inch
40
30
20
10
0
S1 S2 S3 S4 S5 S6
Figure 1:- Thread Density of fabric
All samples were produced on handloom keeping all parameter same other than blend ration of yarn in weft direction and weave structure. Since warp beam was used during weaving for all samples, hence same thread density in warp direction is observed as shown in Table 2 & Fig.1. IS 1963 (2004) standard used to measure the warp and weft thread density per unit length using pick glass. Result reveals that there is insignificant difference in thread density among plain weave samples and among twill weave samples. However there is significant difference between plain weave and twill weave samples with same set of yarn used in both directions. This is due to change in weave as well as manual control while weaving on handloom.
-
Thickness
Thickness
0.6
Thickness in mm
0.5
0.4
0.3
0.2
S1 S2 S3 S4 S5 S6
Figure 2:- Thickness of fabric samples
Thickness of fabric samples was measured as per ASTM D1777 standard using thickness tester. Result are shown in Table 3 & Fig. 2 which indicate significant difference between plain and twill weave samples, the reason of which may be attributed due to weave structure as well as crimp percentage. Among plain weave samples, S1 shows maximum thickness, which may be due to higher crimp percentage in warp direction. While in twill weave samples, there is no significant difference among all samples.
-
Fabric Weight in GSM (gm/m2)
GSM (gm/m2)
250
200
150
100
50
0
S1 S2 S3 S4 S5 S6
Figure 3:- Fabric Weight
Fabric weight in terms of GSM is tested as per ISO 3801 standard using GSM round cutter, the results of which is shown in Table 3& Fig.3. Results indicate minor differences in gm/m2 among plain weave and among twill weave samples. However there is significant difference in GSM between plain weave and twill weave samples, the difference of which may be attributed to weave structure and change in PPI due to manual control on handloom which happened during weaving by the researcher herelf.
-
Drape Coefficient
Drape Coefficient
0.8
0.6
0.4
0.2
0
S1 S2 S3 S4 S5 S6
Figure 4:- Drape Coefficient
The drape ability of all the samples was measured using drape meter as per standard ISO 9073-9:2008. The drape coefficient has been shown in Table 3& Fig. 4 which indicates that plain weave samples exhibit higher drape coefficient in comparison to twill weave samples due to more flexibility of twill weave or less stiffer as compared to plain weave fabric, the results shows similar trends as reported by Nitin S Dhoot, L G Patil& P M Katkar [16]. Another major observation regarding drape coefficient indicates that it decreases with increase in bamboo content in weft yarn imparting more flexibility than cotton yarn.
-
-
CONCLUSION
Fabric produced on handloom using various blends of bamboo/cotton in weft yarn with plain and twill are compared in terms of constructional parameters and physical properties. Results indicate that the use of bamboo fiber influences the physical properties in adding values to fabric characteristics apart from its environmental sustainability. Greater fiber length, lesser fiber density with more moisture regain gives an edge to bamboo-cotton blend when compared with only cotton fabric. Lower Drape coefficient of bamboo-cotton blend offers more flexibility to fabric ability is influenced. Results of comfort and mechanical properties will be published in due course of time which is under investigation phase. However it could be concluded that bamboo yarn on handloom could play a vital role in producing comfortable and sustainable clothing.
REFERENCE
-
Y. Kim, S. Suh, The Core Value of Sustainable Fashion: A Case Study on Market Gredit, Sustainability, vol. 14, pp.1-21, 2022
-
Prendergast, J. and Venkatraman, P.D., A study on the development of sustainable organic clothing for womens wear using natural fibres with specific focus on product serviceability. In: 14th Annual Conference of the International Fashion Foundation Institute, (IFFTI), 17 March 2012 – 21 March 2012, Pearl Academy of Fashion, Jaipur, India.
-
M. Waite, Sustainable Textiles: the Role of Bamboo and a Comparison of Bamboo Textile Properties, Journal of Textile and Apparel, Technology and Management, vol. 6, Issue 2, 2009
-
S. R. Kulkarni , S. Banu Emerging Fiber Of The Century- Bamboo, International Journal of Advanced Research in Engineering and Technology (IJARET), vol. 5, Issue 11, pp. 19-25 ,November 2014
-
M. Singh, H. Pal, K. Nath Chatterjee, A Comparative Study of Handloom Denim using Bamboo and Cotton Yarn, International Journal of Engineering Research & Technology (IJERT), vol. 10 Issue 12, pp 162-166, December 2021
-
F. Sekerden, Effect of Fabric Weave and Weft Types on the Characteristics of Bamboo/Cotton Woven Fabrics, FIBRES & TEXTILES in Eastern Europe, Vol. 19, No. 6 (89) pp. 47-52, 2011
-
O. Roselyn Devi , New Sustainable Fibres and their application in Textiles: A Review, International Journal for Modern Trends in Science and Technology, vol. 6(9S), pp 136-141, 2020
-
M. Adnan Ali. M. Imran Sarwar, Sustainable and environmentally friendly fibres in textile fashion: A study of organic cotton and bamboo fibers, Master Thesis, Applied Textile Management, University of Baros, Boras, Sweden, (2010)
-
P. Chidambaram and R. Govindan Influence of Blend Ratio on Thermal Properties of Bamboo/ Cotton Blended Woven Fabrics, Silpakorn U Science & Tech J Vol.6(2), pp 49-55, 2012
-
A. Rathod, A. Kolhatkar, Study on Physical Characteristics of Bamboo & Bamboo-Cotton Blended Yarn Fabrics, International Journal of Research in Advent Technology, Vol.2, No.7, pp-105-110, July 2014
-
A. Kolhatkar, A. Rathod, Ultraviolet Radiation Protection of Human through Protection Coverings: Bamboo, International Journal of Engineering Research in Electrical and Electronic Engineering (IJEREEE), Vol. 4, Issue 2, February 2018
-
V.Paulose and I. Jayalakshmi, Analysis of Anti-Bacterial Efficacy in Bamboo and Bamboo /Cotton Handloom Fabrics Finished with Selected Herbal Extracts, International Journal of Applied Social Science, Vol. 5 (10), pp- 1626-1633, October 2018
-
S. Bhuyan and N. Gogoi, Natural Fibers: Innovative Sustainable and Eco-Friendly, International Journal of Current Microbiology and Applied Sciences , Vol. 9 (7), pp 1004-1011, 2020
-
Z. Zupin. and K. Dimitrovski, A Text Book of Woven Fabric Engineering, Slovenia; Intech Open publishing, pp. 25-46, November 2010
-
Textilsphere.com [Internet].India: Association of Textile Sphere; c2019 [updated 2020 September 14; cited 2023 June 25] https://www.textilesphere.com/2020/09/bamboo-fiber.html
-
N. S. Dhoot , L. G. Patil, & P. M. Katkar, Effect of fabric weaves on compressional behaviour of woven fabric, Indian Journal of Fibre & Textile Research Vol. 39, pp. 79-82, March 2014