
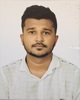
- Open Access
- Authors : Nirav Agrawal , Dr. Vinubhai Ratilal Patel
- Paper ID : IJERTV10IS090124
- Volume & Issue : Volume 10, Issue 09 (September 2021)
- Published (First Online): 22-09-2021
- ISSN (Online) : 2278-0181
- Publisher Name : IJERT
- License:
This work is licensed under a Creative Commons Attribution 4.0 International License
A Study on Load Distribution Mechanism of Pile-Raft Foundation Systems
Nirav Agrawal 1, Dr. Vinubhai Ratilal Patel 2
1Post Graduate Student, Civil Engineering Department, MS University, Vadodara,
2Associate Professor Applied mechanics and structural engineering department, M S University, Vadodara, Gujarat , India,
Abstract:- Design concepts and load sharing mechanism of piled raft foundations have been studied in this thesis. In the conventional piled foundations, the load transferred only by the piles and the piles are used for the reducing of both total and differential settlements and the contribution of the raft is generally disregarded. In the first part of the thesis, design approaches in the literature have been discussed. In the second part of the thesis, parametric analyses have been conducted for typical foundation in over consolidated Bhaili clay and finite element analyses have been done for Aura prime building. Three dimensional analyses have been made by the widely used commercial software of Plaxis 3D and SAFE-2016, which solve the models by using the Finite Element Method. The foundation settlement and the load sharing between raft and pile have been investigated to identify the contribution of raft to the total capacity of piled raft foundations. The results showed that the raft can carry up to the 41.52% of the total applied load for an optimum number of piles for acceptable settlement levels.
Keywords: Pile, raft, foundation, plaxis-3d, deep-foundation, soil-interaction, settlement, soil-pile interaction, safe-2016
INTRODUCTION
One of the most important aspects of a civil engineering project is the foundation system. Designing the foundation system carefully and properly, will surely lead to a safe, efficient and economic project overall. In other words, foundation system design is one of the most critical and important step when a civil engineering project is considered. Until quite recently, there were some separately used systems like shallow foundations such as rafts and deep foundations such as piles. However, lately the foundation engineers tend to combine these two separate systems. By combining these two systems, the foundation engineer will provide the necessary values for the design obtain the required safety and also come out with a more economical solution.
To carry the excessive loads that originate from the superstructures like elevated structures, spans, power plants or other common structures and to prevent excessive settlements, piled foundations have been created and broadly utilized in late decades. However, it is seen that the design of foundations considering just the pile or raft is not a feasible solution because of the load sharing mechanism of the pile-raft-soil. In this manner, the blend of two separate systems, to be specific "Piled Raft Foundations" has been created (Clancy and Randolph (1993)).
Piled Raft foundation system is verified to be economical foundation type comparing with the traditional piled foundations , where, just the piles are utilized for the diminishing both aggregate and differential settlements and the contribution of the raft is commonly ignored.
In this examination, conduct of the piled raft foundation systems under axial loads has been explored by comparing the traditional design approaches and investigating parametric analyses. In the literature, there are a lot of explores centering of these boundaries, like; the number of piles, length of piles, diameter of piles, pile spacing ratio, location of piles, stiffness of piles, distribution of load, level of load, raft thickness, raft dimensions and type of soil. In any case, through these boundaries, the number of piles, length of piles and level of load are emphasized in this examination. Effects of these parameters are discussed with the solutions of finite element models. To this end, parametric investigations are directed through the software Plaxis 3D and SAFE-2016 with the comparisons.
FINITE ELEMENT ANALYSIS OF PILED RAFT FOUNDATIONS
Geotechnical and Material Parameters for Input
Piled raft on two different softwares were analyzed in this study. A typical 23-storey building in Bill village soil, in software PLAXIS-3D. The second one is in software SAFE-2016 with same building and soil parameters.
A typical 23-storey building in BHAILI
Soil Properties: The SPT data was taken from a report for a construction site on Bhaili, where the soil is commonly overconsolidated clay. Raw SPT-N values for four different boreholes are shown in Figure1.
Average of the SPT-N values has been taken to derive a single corrected SPT value, N60, which is shown in Figure2. It is assumed that the stiffness of the soil is linearly increasing; therefore the profile of the corrected N values is deeper than the
profile of raw SPT-N values. For the input parameters of the Plaxis 3D, it is needed to convert the SPT-N values to soil stiffness parameter E. The correlation of Stroud (1975) has been used for the N60 – E relationship.
E = N60 0.8
Where E is in MPa
10
10
20
20
30
30
40
40
50
50
BH-2
BH-1 BH-3
BH-4
BH-2
BH-1 BH-3
BH-4
DEPTH(m)
DEPTH(m)
Corresponding E values vs. depth has been shown in the Figure3. E increases averagely 1.600 MPa per one meter depth, starting from the 10.24 MPa at ground level.
SPT-N
0
-2 0
-4
-6
-8
-10
-12
-14
-16
-18
SPT-N
0
-2 0
-4
-6
-8
-10
-12
-14
-16
-18
Figure 1 SPT-N values vs Depth(m)
N60
17 |
20 |
28 |
33 |
38 |
42 |
|
BH-2 BH-1 BH-3 BH-4 |
||||||
17 |
20 |
28 |
33 |
38 |
42 |
|
BH-2 BH-1 BH-3 BH-4 |
||||||
0
-2
-4
DEPTH(m)
DEPTH(m)
-6
-8
-10
-12
-14
-16
-18
Figure 2 Corrected SPT-N values
0
-2
-4
Depth(m)
Depth(m)
-6
-8
-10
-12
-14
-16
-18
102 |
40 112 |
00 137 |
60 153 |
60 169 |
60 182 |
40 |
102 |
40 112 |
00 137 |
60 153 |
60 169 |
60 182 |
40 |
E'(Kpa)
Depth(m)
Figure 3 E (kPa) vs. Depth (m)
Table 1 – Soil Properties for BHAILI CLAY
Parameter |
Symbol |
Overconsolidated Clay |
Unit |
Material Model |
– |
Mohr-Coulomb |
– |
Unsaturated weight |
unsat |
18 |
kN/m3 |
Saturated weight |
sat |
18 |
kN/m3 |
Stiffness |
E |
10,240 |
kN/m2 |
Stiffness Increment |
Eincrement |
1600 |
kN/m2/m |
Cohesion |
cref |
12 |
kN/m2 |
Friction angle |
25 |
– |
|
Poisson ratio |
' |
0.25 |
– |
Lateral pressure coefficient (K0x=K0z) |
K0 |
0.8 |
– |
Interface stiffness ratio |
Rinter |
1.0 |
– |
Drainage Type |
– |
Drained |
– |
Structural Properties: The building is assumed as reinforced concrete building with 23- storey and 28x22m floor area. Piled raft foundation located at 5m below ground level. Raft thickness and the length of the piles are variable. Raft and pile properties used in the Plaxis 3D model are shown in Table 2 and Table 3. Piles are designed as embedded piles. Massive circular pile was selected among the predefined pile types for embedded piles. Skin resistance and the base resistance of embedded piles must be calculated and specified for the material input phase. The correlation of Stroud (1975), shown in Figure 28, has been used for the conversion of SPT-N values to shear strength of soil by taking the coefficient f1 as 4.6. In addition the unit skin friction multiplier is taken as 0.35 of Cu. With the multiplication of these coefficients by related area and circumference values of piles,
maximum skin resistance at the top (Ttop ) and the bottom (Tbottom) of the pile and the base resistance were calculated for the
max max
piles with a diameter of 1m. Material and section properties, used in SAFE-2016 Analyses of raft and pile are shown in Table 4 and Table 5 for Building in BHAILI CLAY.
Table 2 Raft Properties for BHAILI CLAY
Parameter |
Symbol |
Raft |
Unit |
Material Model |
– |
Linear-Isotropic |
– |
Unit weight |
25 |
kN/m3 |
|
Stiffness |
Eref |
2.7386E+07 |
kN/m2 |
Poisson ratio |
0.2 |
– |
|
Thickness |
t |
1.6 |
m |
Width – Breadth |
W x B |
30 x 24 |
m |
Table 3 Embedded Pile Properties for BHAILI CLAY
Parameter |
Symbol |
Embedded Pile |
Unit |
|
Material Model |
– |
Linear Elastic |
– |
|
Unit weight |
30 |
kN/m3 |
||
Stiffness |
Eref |
2.7386E+07 |
kN/m2 |
|
Diameter |
d |
0.75 |
m |
|
Length |
L |
15 |
25 |
m |
Ttop max |
– |
16.57 |
16.57 |
kN/m |
Tbottom max |
– |
55.79 |
81.94 |
kN/m |
Base resistance |
Fmax |
281.46 |
410 |
kN |
No. of piles |
– |
110 & 210 |
– |
Table 4 Material and section properties of Raft in BHAILI CLAY for SAFE-2016 Analyses
Parameter |
Symbol |
Raft |
Unit |
Property |
– |
Shell Thick |
– |
Unit weight |
25 |
kN/m3 |
|
Modulus of Elasticity |
E |
2.7386E+07 |
kN/m2 |
Poisson ratio |
0.2 |
– |
|
Thickness |
t |
1.6 |
m |
Width – Breadth |
WxB |
30 x 24 |
m |
Table 5 Material and section properties of Pile in BHAILI CLAY for SAFE-2016 Analyses
Parameter |
Symbol |
Pile |
Unit |
Property |
– |
Frame – Pile |
– |
Unit weight |
25 |
kN/m3 |
|
Modulus of Elasticity |
E |
2.7386E+07 |
kN/m2 |
Poisson ratio |
0.2 |
– |
|
Diameter |
d |
0.75 |
m |
Length |
L |
15 & 25 |
m |
No. of piles |
– |
110 & 210 |
– |
Building-1: A typical 23-storey building in BHAILI
The building is a reinforced concrete building with 23-storey and 28x22m floor area. Piled raft foundation located at 5m below ground level (assuming two basements). Lengths of the piles are variable. Due to loading and the shape/geometry of the structure and also the soil beneath the foundation only a quarter of the foundation has been taken into account and the center of the model foundation has been placed in alignment with the z-axis the as shown in Figure 5. For the parametric analyses of the Building-1, sub-cases have been used, which are listed in the Table 6.
Table 6 Sub-cases of Building-1
Sub-Case |
Number of piles |
Pile length (m) |
Distributed load (kPa) |
Model-1 |
110 |
15 |
390 |
Model-2 |
110 |
25 |
390 |
Model-3 |
210 |
15 |
390 |
Model-4 |
210 |
25 |
390 |
Figure 5 Deformed shape of Finite Element method of the piled raft foundation of Model-4
Raft and pile properties, including the geometrical properties, were previously tabulated in Table 5 and in Table 6. The raft thickness is taken as 1.6m. Ultimate capacity of 15m and 25m length piles are 3347kN and 7374kN respectively.
The maximum total (dead and live) load has been taken as 16.9kN/m2/floor. Therefore, the maximum total design load of the structure becomes 202034KN for the selected case with 23- storey building. Total 390 kN/m2 load applied to the foundation in the direction of gravity as distributed load.
SAFE-2016 Analyses
Simplified Method (Using the outputs of Manual Calculation):
SAFE-2016 software has been used for back analyses of the model. As mentioned before, the main supports are joint springs and area springs in SAFE-2016. The stiffness of soil is modeled by the joint and area springs. A sample of a 3D view of the Sap2000 model is shown in Figure 30. Raft settlements are taken as average by the suggested formula of Davis & Taylor (1962) as following;
Savg =
1
(2Scentre + Scorner)
3
To find the spring constant of raft and pile separately, a soil capacity is calculated by using soil parameters of site in BHAILI SOIL. Skin Resistance at bottom of pile is calculated by theoretical equation for 15m length and 25m length piles are 55.796KN/m and 81.94KN/m respectively. Similarly, End Bearing Résistance for 15m length and 25m length are calculated as 281.46KN and 410KN respectively. By considering the different allowable displacement of pile as 5mm, 10mm, 20mm, 50mm different spring constant are calculated shown in Table7
Figure 6: Plan View of SAFE-2016 model for Model-1
TABLE 7 FOR PILE SPRING CONSTANT |
||||
Allowable displacement (mm) |
5(mm) |
10(mm) |
20(mm) |
50(mm) |
15m length pile |
171546KN/m |
85773 KN/m |
42886KN/m |
17154KN/m |
25m length pile |
413560KN/m |
206780KN/m |
103390kN/m |
41356KN/m |
Disregarding the outputs of Plaxis
Separate analyses have been conducted to observe the behavior of piled raft by disregarding the outputs of Plaxis. In these analyses, allowable loading capacities of piles have been divided to the variable allowable settlements (at the top of the pile) to the usage of spring stiffness of piles. Initially, maximum allowable settlement is taken as 0.01m. This results in to a spring constant of 85773 KN/m and 206780KN/m for 15m and 25m length piles, respectively. Also, to analyze the effect of raft contribution, raft springs have been used as; 0, 1000, 2000, 5000, 10000 kN/m/m2. This process has been repeated for the allowable settlements; 0.05m, 0.02m, 0.01m and 0.005m. All results are listed in Appendix V. Critical pile loads are listed in Table 8 and the locations of piles are shown in a quarter of the piled raft in Figure 7.
Figure 7 Piles taken as reference shown in a quarter of the piled raft.
Table 8 Comparison of pile loads (Model-1-15m pile length)
Springs |
Pile Loads (kN) |
|||||
Pile (kN/m) |
Raft (kN/m/m2) |
A |
B |
C |
||
SAFE 2016 |
k for 0.005m |
171546 |
10,000 |
1458.165 |
2181.863 |
1782.005 |
k for 0.010m |
85773 |
10,000 |
1230.728 |
1585.339 |
1413.817 |
|
k for 0.020m |
42886 |
10,000 |
971.77 |
1091.729 |
1045.988 |
|
k for 0.050m |
17154 |
10,000 |
664.295 |
645.723 |
662.954 |
Pile load distributions
Case 1: A typical 23-storey building in BHAILI
Axial load distributions are plotted in Figure 8. All the piles are 15 m length. It is observed that the center piles have lower axial loads on both 110 piles and 210 piles situations. This is because of the pile group effects. However, for 210-pile case, it is observed that the axial load of the center pile is almost half of the outer piles. Center pile can approach to the load level of outer piles after the depth of 10m and moves parallel after this point. This may be the effect of small ratio of pile spacing and pile diameter, which causes the block movement of soil just beneath the center of raft. Therefore, considering the movement of the soil beneath the center of raft, shown in Figure 9 and Figure 10, the behavior of the center and corner piles is in reasonable.
Axial Load (KN)
0
0 200 400 600 800 1000
-5
-10
-15
-20
-25
110-piles-Center
110-piles-Mid- Edge
110-piles-Corner
Figure 8 Comparison of axial load distributions along piles for different number of piles (Model-1 (110piles, 15m, 390kPa) vs. Model-3(210piles, 15m, 390kPa))
0
0
0
500
1000
1500
2000
0
500
1000
1500
2000
-5
-10
-15
15m-Center Pile
-20 15m-Mid-edge pile
15m-Corner pile
-25 25m-Center pile
-30 25m-Mid edge pile
25m-Corner pile
-35
-5
-10
-15
15m-Center Pile
-20 15m-Mid-edge pile
15m-Corner pile
-25 25m-Center pile
-30 25m-Mid edge pile
25m-Corner pile
-35
Figure 9 Comparison of axial load distributions along piles for different length of piles (Model-1 (110piles, 15m, 390kPa) vs. Model-2 (110piles, 25m, 390kPa))
0
0
0
200
400
600
800
1000
1200
0
200
400
600
800
1000
1200
-5
-10
-15
-20
-25
-30
-35
15m- Center piles
15m-Mid-edge piles 15m-Corner piles 25m-Center piles 25m-Mid edge piles
25m-Corner piles
-5
-10
-15
-20
-25
-30
-35
15m- Center piles
15m-Mid-edge piles 15m-Corner piles 25m-Center piles 25m-Mid edge piles
25m-Corner piles
Figure 10 Comparison of axial load distributions along piles for different length of piles (Model-3 (210piles, 15m, 390kPa) vs. Model-4 (210piles, 25m, 390kPa))
Load Sharing of Raft
After all of the analyses have been carried out, the loads on each pile are added and subtracted from the total applied load to find the total load carried by the raft. The values are tabulated in Table 9. As stated in the previous subject, the usage of longer piles increases the shared load of piles. Other points can be listed as; total load carried by the raft increases in higher load levels and it also increases in higher number of piles for longer piles. However, the load on raft is decreased by the higher number of piles for shorter piles.
Table-9 Model cases for Building-1 with variable number of piles, pile length
Models |
Number of piles |
Pile Length(m) |
Dist. Load(kPa) |
Total Load(KN) |
Pile Load(KN) |
Raft Load(KN) |
Load on Piles(%) |
Load on raft(%) |
1 |
110 |
15 |
390 |
280800 |
86285 |
194514 |
30.73% |
69.27% |
2 |
110 |
25 |
390 |
280800 |
172359 |
108440 |
61.38% |
38.62% |
3 |
210 |
15 |
390 |
280800 |
164040 |
116759 |
58.42% |
41.58% |
4 |
210 |
25 |
390 |
280800 |
23036 |
50563 |
81.99% |
18.01% |
Table-10 Comparison of load and settlement with different spring constant
Spring constant |
Load (KN) |
||||
Max Allow. Sett |
Pile (KN/m) |
Raft (KN/m/m2) |
Pile (KN) |
Raft (KN) |
Pile load/Total load |
5mm |
171546 |
0 |
231324 |
0 |
100% |
171546 |
5000 |
195776 |
35548 |
84.6% |
|
171546 |
10000 |
171005 |
60318 |
73.92% |
|
10mm |
85773 |
0 |
231324 |
0 |
100% |
85773 |
5000 |
171982 |
59341 |
74.34% |
|
85773 |
10000 |
139650 |
91673 |
60.36% |
|
20mm |
42886 |
0 |
231324 |
0 |
100% |
42886 |
5000 |
140426 |
90898 |
60.70% |
|
42886 |
10000 |
105837 |
231324 |
45.75% |
|
50mm |
17154 |
0 |
231324 |
0 |
100% |
17154 |
5000 |
96046 |
135277 |
41.52% |
|
17154 |
10000 |
68968 |
162356 |
29.81% |
Table-18- Maximum and minimum Settlement of Rafts
PLAXIS |
SAFE-2016 (Considering raft spring 2000KN/m2) |
|||
Max. Sett. (mm) |
Min. Sett. (mm) |
Max. Sett. (mm) |
Min. Sett. (mm) |
|
Model-1-(110 piles- 15m) |
-134 |
-105 |
-80 |
-65 |
Model-2-(110 piles- 25m) |
-73 |
-60 |
-51 |
-34 |
Model-3-(210 piles- 15m) |
-98 |
-80 |
-54 |
-42 |
Model-4-(210 piles- 25m) |
-72 |
-58 |
-31 |
-20 |
0
0
Raft spring-0KN/m2 Raft spring-1000KN/m2 Raft spring-2000KN/m2 Raft spring-5000KN/m2
Raft spring-10000KN/m2
PLAXIS-3D
Raft spring-0KN/m2 Raft spring-1000KN/m2 Raft spring-2000KN/m2 Raft spring-5000KN/m2
Raft spring-10000KN/m2
PLAXIS-3D
0
0
20
20
40
40
60
60
80
80
100 120
100 120
-50
-50
-100
-100
-150
-150
PILE NUMBER
PILE NUMBER
SETTLEMENT(mm)
SETTLEMENT(mm)
Figure 11 Settlements at the head of piles (i.e. Outer piles)
(Model 1-110 piles-15m)
SUMMARY AND CONCLUSION
Piled raft systems are verified to be an economical foundation type comparing the conventional piled foundations, where, only the piles are used for the reducing of both total and differential settlements and the contribution of the raft is generally disregarded. In this study, the foundation settlement and the load sharing between raft and pile have been investigated to identify the contribution of raft to the total capacity of piled raft foundations.
In the first part of this study, a detailed literature review for the design of piled raft foundations has been presented. Advantages and disadvantages of different approaches have been discussed to model the piled raft foundation systems. Also the factors affecting the behavior of piled raft foundations have been discussed. Discussed factors are; the number of piles, length of piles, diameter of piles, pile spacing ratio, location of piles, stiffness of piles, distribution of load, level of load, raft thickness, raft dimensions and type of soil.
In the second part, a case has been created for Bhaili Clay and parametric analyses have been conducted with the help of Plaxis 3D software. Variables for the parametric analyses are pile number, pile length. In addition, a case study, SAFE-2016 Analyses validate the method of the calculation. Results show that the calculation method is in line with the actual piled raft behavior.
CONCLUSIONS
A method presented to find the settlements in Safe-2016 by using the outputs of the Plaxis. Using the embedded pile feature of Plaxis, raft and pile load sharing is calculated and the corresponding load-settlement curves are plotted. Taking the constant of the slope of this curve as the total spring of elements, corresponding average spring constants are assigned to the piles and raft in Safe-2016.
The proposed method of analysis becomes more realistic with the additional soil springs connected to the raft. This may be helpful for structural/foundation engineers to calculate the deformations more accurate and the structural properties of raft more effective.
Average percentage of raft load share is 41.52% for the allowable settlement of 65mm for the Plaxis Analysis. For the SAFE- 2016 Analysis, at the final design load, raft can carry up to 29.81% of applied load. The main reasons for the difference in these two cases are the Raft Spring, the foundation characteristic (number of piles and length of piles) and the soil stiffness.
HYP8: The principle of consuming income and not capital is not applied in construction project management.
REFERENCES
-
Behavior of large piled-raft foundation on clay soil by Shivanand Mali, Baleshwar Singh IIT Guwahati
-
Physical modeling of behaviors of cast-in-place concrete piled raft compared to free-standing pile group in sand by Mehdi Sharafkhah, Issa Shooshpasha (Babol Noshiravani University of Technology, Iran)
-
Modelling the behaviour of piled raft applying Plaxis 3D Foundation Version 2 by (Yasser El-Mossallamy, Associate Prof., Ain Shams University, Cairo, Egypt c/o ARCADIS GmbH, Berliner Allee 6, D – 4295 Darmstadt, Germany).
-
2D and 3D Numerical Simulation of Load-Settlement Behaviour of Axially Loaded Pile Foundations by Gowthaman S(Uni. Of Jaffna), Nasvi MCM (Uni. Of Peradeniya) Sri Lanka.
-
3D-Analysis of Soil-Foundation-Structure Interaction in Layered Soil by Mohd Ahmed1*, Mahmoud H. Mohamed2, Javed Mallick3, Mohd Abul Hasan4 (Civil Engineering Department, Faculty of Engineering, King Khalid University, Abha, Saudi Arabia)
-
An Analytical Approach for Piled-Raft Foundation Design Based on Equivalent Pier and Raft Analyses by Using 2D Finite Element Method by Fatih Celik (Saudi Society for Geosciences 2019)
-
Analysis of Piled Raft Foundations by Jayarajan P, Kouzer KM. Analysis of Piled Raft Foundations. Indian Journal of Science
-
DESIGN METHODS FOR PILE GROUPS AND PILED RAFTS METHODES by M.F. Randolph (the University of Australia)
-
EQUIVALENT PIER THEORY FOR PILED RAFT DESIGN by Balakumar Venkatraman(Simplex Infrastructure limited), Erwin Oh (Griffith University), Arumugam Balasubramaniam (Griffith University)
-
Soilstructure interaction in a combined pileraft foundation a case study by Ashutosh Kumar, Milind Patil, Deepankar Choudhury (IIT- BOMBAY)