
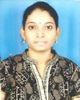
- Open Access
- Authors : Dr. N. Suganya , M Anusha , K Devi Shree , Tryphena
- Paper ID : IJERTV12IS030083
- Volume & Issue : Volume 12, Issue 03 (March 2023)
- Published (First Online): 29-03-2023
- ISSN (Online) : 2278-0181
- Publisher Name : IJERT
- License:
This work is licensed under a Creative Commons Attribution 4.0 International License
A Study on Rice Husk Ash Replaced Foam Concrete
Dr. N.Suganya1, M Anusha2, K Devi Shree2, Tryphena2
1Associate Professor,2Final year B.E Students Department of Civil Engineering,
Sri Sairam Engineering College, Chennai, Tamil Nadu, India
Abstract – Concrete is a composite material of binder, aggregates and water. It is naturally heavy in weight and has high compressive strength. However, conventional concretes application is limited mostly to mass constructions thereby restricting its widespread usage in special application areas. A best alternative is the use of Foam Concrete (FC) in areas of small loads. Foam concrete is comparatively lightweight thus reducing the dead weight of the structures and also lowering the cost of production, construction and transportation. Foam Concrete is commonly prepared using cement, sand, water and foaming agent. Because of its porous matrix, it also serves as a low cost, highly effective solution for thermal and acoustical needs of the building. In addition, its lightweight and self-compacting properties makes it even easier for use in special construction.
Our study focusses on understanding the properties of Rice husk ash replaced FC in 50% and 100% replacement to sand. A short study is conducted by casting cubical concrete specimens of size 7cm×7cm×7cm in order to analyze and compare the properties between conventional Plain cement mortar, conventional foam concrete, 50% and 100% replacement of sand with rice husk ash. The foaming agent used to prepare foam concrete is SLES Sodium Lauryl Ether Sulphate (a common surfactant in soaps).Rice husk ash utilized as replacement for sand would be an ecofriendly option. Properties mainly Compressive Strength(at 7 days and 28 days), water absorption and dry density were studied to assess the effectiveness in replacing sand with rice husk ash and its suitability in making foam concrete. The results of these tests were found to be satisfactory and the use of foam concrete replaced with rice husk ash is recommended.
Keywords: Foam Concrete, Sand, Rice husk ash, Foaming agent
1 INTRODUCTION
For centuries, the use of concrete has been predominant in the construction sector. Conventional concrete is made by incorporating certain mix proportion involving varying ratios of cement, aggregates (fine and coarse) and water to achieve the expected target strength. The diversified physical properties of the above raw materials namely its shape, surface area, surface roughness
& porosity, strength, abrasive nature etc., and the various chemical reactions taking place at the molecular level between these raw materials namely degree of bonding, oxidation and reduction reaction of cement with water, heat of hydration, degree of reactiveness etc., is what makes concrete, the most sought composite material or heterogeneous mixture in the construction industry.
Despite its immense applications and high strength, conventional concrete is regarded as a highly polluting material because of the reason that the raw materials for concrete making isnt environmentally sustainable and the amount of debris or demolition waste created after the useful service life of concrete structure poses a huge threat to environment. Particularly, the manufacturing of coarse aggregate for concrete making involves destruction of natural rock formations and an elaborate energy intensive processes to obtain the aggregate of desired size and shape to fill up and complete the concrete matrix. Recent studies and researches indicate that construction sector is one of the huge contributors of overall CO2 emissions and calls for innovating sustainable construction materials and incorporating sustainable construction practices is being put forth by all nations in order to be in accordance and comply with the United Nations Sustainable Development Goals (UNSDG).
Although conventional concrete is highly versatile and most sought after material for construction owing to its highly desirable overall properties, its usage is limited to mass constructions in order to serve common load bearing and load transfer criterion. Conventional concrete becomes uneconomical for usage in areas where the load bearing & load transfer necessity is less in a structure. To overcome the aforementioned shortcomings of conventional concrete and to reduce considerable material consumption, foam concrete is recommended for utilization in specific areas where usage of conventional concrete is proven to be obsolete and uneconomical.
Foam concrete is a combination of cement, sand, water and foaming agent. It is a porous and self levelling material having high workability. . It was used as an insulation material in 1920s and many research were carried out after that to make it a potential and suitable construction material. Until 1990s, it is regarded as a weak and non- durable material. This is due to uneven distribution of air bubbles in foam concrete due to manual mixing for creation of foam. Now, foam generator is used to produce foam which creates stable and even bubbles within the matrix of foam concrete. The density of foam concrete is very low and ranges from 300 to 1600kg/m3.Size of Air bubbles varies from 0.1 to 1mm. The degree of uniformity of distribution of air bubbles in foam concrete helps in ascertaining its density and strength characteristics. Air bubbles created by foaming agent gets entrapped in the foam concrete matrix which results in lightweight and high porosity of the concrete. Though, foam concrete doesnt possess the high
strength like conventional concrete it makes up for it by possessing special thermal and acoustic insulation properties. Due to absence of coarse aggregates and increased workability, it can be used in relatively small areas where conventional concrete cannot be laid.
Generally, the performance and properties of foam concrete depends on the foaming agent used, cement used, uniformity and effectiveness in mixing etc., Using rice husk ash as replacement is a greener, ecofriendly and economical option. Due to presence of high silica content, it gives suitable strength upon hydration with cement. When compared to sand, it possess high fineness which contributes to better stability of bubbles thereby improving the overall property of foam concrete.
All the preliminary tests were carried out in cement, sand and rice husk ash. The grade of cement used for casting is OPC 43 grade. For all types of concrete mixes namely conventional plain cement mortar, conventional foam concrete, foam concrete with 50% and 100% replacement of sand with rice husk ash, 3 cubes were casted each for assessing the compressive strength, Water absorption and dry density for all the specimens. Throughout the study, the ratio of foaming agent with water is adopted 1:30 and the ratio of cement with sand is adopted 1:1. The water cement ratio is determined by trial and error as there is no guidelines or codebooks for the selection of water cement ratio. Later on by various trials, it is determined that water cement ratio of 0.4- 0.52 can be adopted for making foam concrete.
2 REVIEW OF LITERATURES 2.1Enhancing The Strength Of Pre-made Foams For FoamConcrete Applications by Ailar Hajimohammadi, Tuan Ngo And Priyan Mendis: They emphasized the need to improve the stability of fresh foams in order to improve the cellular structure of foam concrete. They proposed the use of xanthan gum to be used as a foam stabilizer and to aggregate the liquid film around each bubble. They concluded that the use of xanthan gum improved the pore size distribution of foam concrete and substantially all the properties are iproved.
-
Influence of recycled concrete aggregate on the foam stability of aerated geopolymer concrete by Kirubajiny Pasupathy, Sayanthan Ramakrishnan, Jay Sanjayan
:Recycled concrete aggregates were used as partial or full replacement to fine aggregates in aerated geopolymer concrete. They found out that the use of recycled concrete aggregate improved the foam stability and reduced the settlement of concrete mixes. It was found out that by increasing the recycled concrete aggregate content, the setting time of the aerated geopolymer concrete mix was decreased. It was concluded that by using recycled concrete aggregate, the hardened properties of geopolymer concrete was improved.
-
Foam concrete: a state-of-the-art and state-of-the- practice review by Yanbin Fu, Xiuling Wang, Lixin Wang, Yunpeng Li: They insisted that in order to produce better quality of foamed concrete, a study on its characteristics is necessary instead of simply evaluating the properties. They urged the need to do more research on drying shrinkage, long term durability, foam stability and micro structure characterization of foamed concrete.
-
Fibre reinforced foamed concretes: a review by Mugahed Amran, Roman Fediuk, Nikolai Vatin, Yeong Huei Lee, Gunasekaran Murali, Togay Ozbakkaloglu, Sergey Klyuev & Hisham Alabduljabber :They analyzed the properties of foamed concrete by adding fibers such as nylon and aramid. They found that the addition of these fibers does not change the thermal and sound insulation properties of foamed concrete. It was concluded that addition of fibers to foam concrete improved its overall properties and the dosage of foam agent plays a key role in determining the final properties of hardened foam concrete.
-
Experimental study on Light weight foamed concrete by Aswathy M: It was concluded that foam concrete upon aging gives better thermal insulation. The dead load of the concrete is reduced and the author recommends foam concrete to be environmentally better than normal concrete due to simplicity, less labor requirements and versatility.
-
Physical and functional characteristics of foam concrete: a review by Amritha Raj, Dhanya Sathyan, K.M. Mini: A study on characteristics of foamed concrete is done.It was found that Chemically expanded and air cured foams in the making of foam concrete results in uniform connected pore which improves the durability of foam concrete. It was concluded that the use of fly ash and silica fume improved the physical and mechanical properties of foam concrete.
-
Role of non reactive powder in strength enhancement of
foamed concrete By A.Bagheri, S. A. Samea: The sand used in the making of foamed concrete is replaced by an inert stone powder. Due to the addition of inert stone powder, the porosity and workability of the foam concrete is reduced and thereby super plasticizers are required to compensate for the loss of workability of the foamed concrete.
-
Properties And Applications Of Foamed Concrete: A Review by Y.H.Mugahed Amran, Nima Farzadnia, A.A.Abang Ali
They studied the characteristic of foamed concrete instead of normally evaluating its properties. They found out that foam stabilization plays an important role in producing foamed concrete with high consistency and stability. They concluded that by partially replacing cement with fly ash and by using light weight aggregates, the rate of heat of hydration is reduced and the overall properties of foamed concrete was improved.
3 STUDY OF MATERIALS
Preliminary study of materials used in this study are done and the values obtained for each material is tabulated below
-
Cement
Testing of cement is done as per IS 8112-1989. Standard OPC 43 grade is used. The cement should be free from lumps. The particles should sink if thrown in a bucket of water. The various test results conducted on the cement and its values are tabulated,
Table 3.1: Cement Properties
S.No
Characteristics
Values
1.
Specific Gravity
3.15
2.
Setting time – initial(minutes)
30
3.
Setting time final(minutes)
600
4.
Fineness (%)
0.62
5.
Normal Consistency
34%
-
Fine aggregate
As per IS 383-1970, the sand used in the experiments
confirmed to grading zone 2. The sand is sieved in 4.75mm IS sieve to remove any large particles. sand grains should be angular and should not contain clay, silt and organic matter.Its properties are listed below,
Table 3.2 Sand Properties
S.No |
Characteristics |
Values |
1. |
Moisture content |
Nil |
2. |
Specific gravity |
3.09 |
3. |
Maximum size |
4.75mm |
4. |
Fineness modulus |
3.079 |
5. |
Shape |
Sharp, coarse and angular grains |
3.2 Rice husk ash
It is obtained by burning rice husk in a controlled manner without causing pollution to environment. It has high silica content and high pozzolanic characteristics that makes it a good replacement material in concrete. Its properties measured are given in table
Table 3.3(A): Properties of Rice husk ash
S.no |
Properties |
Values |
1. |
Colour |
Grayish black |
2. |
Specific gravity |
2.17 |
Composition |
% wt |
SiO2 |
90.18 |
CO2 |
0.1 |
K2O |
4.5 |
P2O5 |
2.45 |
CaO |
1.01 |
MgO |
0.69 |
Fe2O3 |
0.47 |
Al2O3 |
0.46 |
MnO |
0.14 |
Its general chemical constitution is listed in table, Table 3.3(B): Chemical Constitution of Rice husk ash
4 MIX DESIGN
At present, there is no standard guidelines for mix proportioning foam concrete. All the mix proportions for foam concrete, and foam concrete replaced with Rice Husk Ash (RHA) at 50% and 100% for sand are determined by trial and error. Six cubes were casted each for conventional Plain cement mortar, Conventional foam concrete, 50% and 100% replacement of sand by rice husk ash and for each type three cubes were tested for compressive strength at 7 days of curing and remaining three cubes were tested for compressive strength at 28 days of curing. The dimension of the cubical mould is 0.07m×0.07m×0.07m.For all cube specimens, 1:30 foaming agent to water dilution is maintained. Cement to sand ratio is maintained 1:1.
Table 4(A): Mix proportion of Conventional Plain Cement mortar(PCM)
Water cement ratio |
Cement (g) |
Sand(g) |
Water(ml) |
0.4 |
250 |
250 |
100 |
Table 4(B)Mix Proportion for conventional; foam concrete(FC)
Water cement ratio |
Cement(g) |
Sand(g) |
Water(ml) |
Foaming agent(ml) |
0.4 |
250 |
250 |
100 |
4 |
Table 4(C) Mix proporton of 50% replacement by RHA (50%RHA)
Water cement ratio |
Cement(g) |
Sand(g) |
Rice husk ash(g) |
Water(ml) |
Foaming agent(ml) |
0.45 |
250 |
125 |
47 |
135 |
4.5 |
50% volume of sand is replaced with rice husk ash (volume batching) and foam concrete is prepared
Water cement ratio |
Cement(g) |
Rice husk ash(g) |
Water(ml) |
Foaming agent(ml) |
0.52 |
250 |
86 |
175 |
6 |
Table 4(D) Mix proportion of 100% replacement by RHA (100% RHA)
100% volume of sand is replaced with rice husk ash by volume batching and foam concrete is prepared
5 CASTING OF CONCRETE CUBES
The batching of raw materials is done as per arrived mix proportions as in mix design. Weigh batching is done for conventional plain cement concrete and foam concrete. Volume batching is done for replacement of rice husk ash for sand. For preparation of cube specimens, initially mixing is done between foaming agent and water in a container that produces stable foam. Then, the proportioned quantity of raw materials (cement, sand and rice husk ash) are dry mixed and poured in the bucket. For mixing, a drill machine with 2800rpm speed attached with
mixing equipment is used to produce stable foam in the container. Concrete mixes are poured in cubical moulds of 0.07m×0.07m×0.07m.The mould is designed and constructed so as to remain sufficiently rigid during placing concrete. No compaction is required in foam concrete mixes as they have high workability (self-compacting).The mould should be free from any dust and rubbish particles. The interior of the moulds is oiled and then concrete is poured completely to fill the mould. After 24 hours, demoulding is done and the specimens are cured in water.
Fig 1: Casting of cube specimens
Fig 2: specimens cured in water
6 OBSERVATIONS MADE FROM CONDUCTING TESTS
-
Dry Density Test
The cube specimens after curing for 28 days are dried and its dry density is calculated
Table 6.1 Test Results of Dry Density Test
Type
Sample 1
(kg/m3)
Sample 2 (kg/m3)
Sample 3 (kg/m3)
Mean (kg/m3)
Conventional Plain cement mortar
1839.6
1816.42
1794.5
1816.3
Conventional foam concrete
995.19
990.18
979.63
988.34
50% replacement by RHA
879.4
840.44
895.32
871.72
100%
replacement by RHA
1020.3
1000.51
1057.46
1026.09
A graph is plotted for comparison of dry densities of different specimens,
2000
Density in kg/m3
1816.8
Type
1500
988.33
1026.09
1000
871.72
500
Dry density
0
Average density (kg/m3)
Fig 3: Test results of dry density test
-
Water absorption Test
This test is done as per IS 2185 (part 4). The specimens immersed in water for 24 hours are taken, wiped off the surface and weighed immediately. The immersed/wet density is noted from which water absorption is calculated as given in table,
Tests
Dry Density (kg/m3) (Y)
Wet Density (kg/m3) (X)
Water absorption
= ×100 (%)
1
1839.6
1883.83
2.4
2
1816.4
1869.2
2.9
3
1794.5
1834.6
2.23
Average =2.51%
Table 6.2(A): Water Absorption Test results for conventional Plain cement mortar
Table 6.2(B): Water Absorption Test results for conventional foam concrete
Tests
Dry Density (kg/m3) (Y)
Wet Density (kg/m3) (X)
Water absorption
= ×100 (%)
1
995.19
1270.8
27.7
2
990.18
1246.73
25.9
3
979.63
1235.4
26.1
Average = 26.5%
Tests
Dry Density (kg/m3) (Y)
Wet Density (kg/m3) (X)
Water absorption
= ×100 (%)
1
879.4
1188.75
35.17
2
840.44
1152.5
37.13
3
895.32
1190.6
32.98
Average = 35.09%
Table 6.2(C): Water Absorption Test results for 50% replacement by RHA
26
24
22
20
18
16
14
12
10
8
6
4
2
0
compressive strength(7 days) in N/mm2
23.9
Table 6.2(D): Water Absorption Test results for 100% replacement by RHA
Tests
Dry Density (kg/m3) (Y)
Wet Density (kg/m3) (X)
Water absorption
= ×100 (%)
1
1020.3
1236.15
21.1
2
1000.51
1195.8
19.52
3
1057.46
1252
18.4
Average =19.7%
Compressive strength in N/mm2
A graph is plotted for water absorption test as per results obtained,
Water Absorption in percentage(%)
37.13
6.52
4.76
3
PCM
40 35.17
Water absorption in %
35 32.98
30 25.9 26.1
25
20
15
10
2.4
5
0
27.7
2.9 2.23
21.1
19.52
18.4
FC 50% RHA 100% RHA
Type
PCM FC 50% RHA 100% RHA
Type
Trial 1 Trial 2 Trial 3
7th day compressive strength
Fig 5: Compressive strength test results (7 days)
Table 6.3(B): Compression Strength test results at 28 days
Type
Sample 1 (N/mm2)
Sample2 (N/mm2)
Sample 3 (N/mm2)
Mean (N/mm2)
Conventional Plain cement mortar
39.81
38.76
39.5
39.36
Conventional foam concrete
7.4
7.65
7.58
7.54
50%
replacement by RHA
7.93
7.56
7.52
7.67
100%
replacement by RHA
10.21
10.65
10.4
10.42
Fig 4: Test results for water absorption test
-
Compressive Strength Test
The compressive strength test is done for all types of cube specimens and the results are tabulated below,
Table 6.3(A): Compressive Strength test results at 7 days
Type |
Sample 2 (N/mm2) |
Sample 3 (N/mm2) |
Mean (N/mm2) |
|
Conventional Plain cement mortar |
23.24 |
24.5 |
24.21 |
23.9 |
Conventional foam concrete |
2.76 |
3.11 |
3.13 |
3 |
50% replacement by RHA |
4.33 |
4.89 |
5.07 |
4.76 |
100% replacement by RHA |
6.53 |
6.35 |
6.67 |
6.52 |
A graph is plotted below for comparison of compressive Strength of cubes ,
A graph is plotted below for comparison of different cube specimens,
28th day compressive strength in N/mm2
45
39.36
40
35
30
25
20
10.42
PCM
FC
50% RHA
Type
100% RHA
28th day compressive strength
15
7.67
7.54
10
5
0
Compressive strength in N/mm2
Fig 6: Compressive strength test results (28 days)
Fig 7: Cubes dried and density is determined
Fig 8: Compressive strength test of cube specimens
7 RESULTS AND DISCUSSIONS
-
Dry Density Test
The test results show that the dry density is lowest in the foam concrete mix containing 50% replacement by RHA. However, it is noticed that the dry density becomes slightly higher for the foam concrete containing 100% replacement of RHA. It is due to well grading of particles of cement and RHA in foam concrete thereby leading to slight increase in dry density. It is noted that all the cube specimens showed half the dry density when compared to conventional plain cement mortar cubes indicating that foam concrete is lightweight due to entrapment of air bubbles in the concrete. The foam concrete containing 50% RHA has shown the lowest density indicating that it would be a suitable proportion for making lightweight foam concrete. However, reduction in dry density cause reduction in compressive strength and concrete becomes weak in resisting even small loads. Thus, it can be concluded that 100% replacement shows optimum dry density which is satisfactory for foam concrete and it can be recommended.
-
Water Absorption Test
Water Absorption test is done as a measure of degree of porosity and durability of concrete. More water absorption means there is more porosity in concrete and as more water is absorbed, it leads to less durability. The test results shows that water absorption of all foam concrete types is 10 to 15 times higher than conventional plain cement mortar. Conventional plain cement mortar has minimum or no pores in the system and hence water absorption is minimum. On the contrary, foam concrete has air bubbles entrapped in the system thereby leading to increased porosity and water absorption. The durability will be obviously less than conventional plain cement mortar. Foam concrete cannot be used in areas where more water is present. However, on comparing the different foam concrete cube specimens, 50% replacement of RHA showed highest water absorption inferring that it has low density, more pores and is less durable. Hence, it is not a suitable replacement proportion. On 100% replacement by RHA, the water absorption is reduced notably than conventional foam concrete and 50% replacement by RHA indicating that this will give sufficient performance and durability among other lightweight foam concrete types.
-
Compressive Strength Test at 7 days
Conventional Plain cement mortar will have the highest compressive strength in 7 days owing to its high density, better packing and no voids in the system. All the cube specimens has reached 70% of the target strength in 7 days indicating that rate of hydration reactions taking place is high. Foam concrete is lightweight and due to its porous nature and low density it will not give appreciable compressive strength. On comparing conventional foam concrete and 50% replacement by RHA, there is no improvement in compressive strength even upon
replacement. On 100% replacement by RHA, compressive strength has improved as compared to other foam concrete specimens. Foam concrete has restricted usage in only specific areas of construction.100% replacement showed sufficient strength even at 7 days hence it can be recommended for use in foam concrete applications.
-
Compressive Strength Test at 28 days
Conventional plain cement mortar will obviously show a high compressive strength than other foam concrete types because of high density and better packing. Conventional foam concrete and foam concrete replaced 50% by RHA showed minimum compressive strength. There is no improvement in compressive strength even upon 50% replacement by RHA. On 100% replacement, the strength has improved by few times than other foam concrete types. This is because rice husk ash has high silica content and presence of silica in system improves the compressive strength characteristics of concrete. Also, Compressive strength of concrete increases with increase in fineness of cement particles. Here, cement and RHA being fine would have led to notable increase in the compressive strength as portrayed in the graph. Thus it can be concluded that 100% replacement of RHA for sand has improved the compressive strength notably and its usage in special applications would be highly suggested.
8 CONCLUSION
-
Rice husk ash as replacement improved the overall performance of foam concrete significantly in all aspects. Increase in percentage of rice husk ash replacement improved its properties.
-
Sodium Lauryl Ether Sulphate (SLES) produced stable foam under mechanical mixing. There is uniform distribution of air bubbles and the foam concrete produced is lightweight, porous and highly workable.
-
The dry density of foam concrete reduced on addition of 50% rice husk ash for sand. However, on 100% replacement the density is slightly increased as there is more fines in the system and RHA made the foam concrete slightly denser.
-
Water absorption test results clearly indicate that foam concrete absorbs 10 to 15 times more water than conventional plain cement mortar. This is no wonder as foam concrete being porous absorbs more water. Water absorption is a direct measure of durability of concrete.50% replacement by RHA has the highest water absorption percentage indicating it is highly porous but at the same time less durable and unsatisfactory for use.
-
100% replacement by RHA showed satisfactory results in dry density and water absorption test. It absorbs nearly 40 percent less water than 50% replaced RHA foam concrete and dry density is only 3 percent higher than conventional foam concrete.
-
Compressive Strength test results showed a notable change in strength for 100% replaced RHA foam concrete when compared with conventional and 50%
replaced RHA foam concrete. There is increased compressive strength at both 7 and 28 days. RHA being a pozzolanic material with high silica content has improved the strength characteristics significantly. However, RHA replaced by 50% has not improved the performance and its behavior is similar to conventional foam concrete in all aspects. The 100% replaced RHA foam concrete has nearly 40% more compressive strength than conventional and 50% replaced RHA foam concrete.
-
Further studies can be done by varying the foaming agent and cement used which can show highly improved performance. From the studies conducted, 100% replaced RHA foam concrete showed the best performance and is recommended to be used as a potential replacement in foam concrete.
REFERENCES
[1] Specifications for Ordinary Portland 43 grade cement (IS 8112- 1989) [2] Coarse and fine aggregate for concrete-Specification (IS 383- 2016) [3] Methods of physical tests for hydraulic cement (IS 4031) [4] IS 2720 Methods for test of soils [5] IS 2185 -2008(Part 4)- Preformed foam cellular concrete blocks [6] IS 516 -1959 Method of test for strength of concrete [7] https://www.sciencedirect.com/topics/engineering/foamed- concrete [8] https://clctek.com/info/foam-concrete-types/ [9] https://foamconcreteworld.com/making-foam-concrete/ [10] Concrete Technology by Shetty, 2019 Edition [11] https://aip.scitation.org/doi/pdf/10.1063/1.4965763#:~:text=The% 20ratio%20between%20foaming%20agent,into%2030%20liters% 20of%20water. [12] https://www.ijraset.com/research-paper/optimization-of-different- mix-proportions-of-foam-concrete [13] https://www.researchgate.net/figure/Mix-proportions-for-cement- sand-foam-concrete-mixes_tbl1_257407012 [14] https://egy.sika.com/content/dam/dms/eg01/b/FOAMED%20CO NCRETE.pdf [15] https://www.totalconcrete.co.uk/news/what-is-foamed-concrete/ [16] https://dailycivil.com/foam-concrete-lightweight-concrete/ [17] https://civilrack.com/concrete/ingredients-of-foam-concrete/ [18] https://www.azobuild.com/article.aspx?ArticleID=8527