
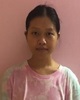
- Open Access
- Authors : Lalhminghlui , Ranjitha M , Dr. B. M Rajaprakash , K. Malsawmkima, Rosangkima
- Paper ID : IJERTV10IS060231
- Volume & Issue : Volume 10, Issue 06 (June 2021)
- Published (First Online): 24-06-2021
- ISSN (Online) : 2278-0181
- Publisher Name : IJERT
- License:
This work is licensed under a Creative Commons Attribution 4.0 International License
A Study on the Mechanical Behaviour of Bamboo Fibres and Chicken Feathers Reinforced Polymer Hybrid Composites
Lalhminghlui, Ranjitha M, K. Malsawmkima, Rosangkima, Dr. B. M Rajaprakash
Department of Mechanical Engineering, University Visvesvaraya College of Engineering, Bengaluru, India
Abstract In the recent research natural fibers have been getting considerable attention due to their superior qualities such as low density, biodegradeability, great specific stiffness, more impact absorption capacity and their relative low cost. The aim of this paper is to study the mechanical properties of bamboo fibers and chicken feathers reinforced polymer matrix hybrid composite at different weight fractions. Bamboo fibers and chicken feathers reinforced epoxy resin matrix hybrid composites have been fabricated by using hand layup method. The mechanical properties tests such as tensile strength test and flexural strength test were carried out in the FIE Electronic Universal testing machine (UTM). The results showed that the tensile strength is maximum for 40:0 (Bamboo:Chicken feather) and the flexural strength is maximum for 40:10 (Bamboo:Chicken feather)
Keywords Bamboo, Chicken feather, weight fraction, epoxy, hybrid composite
-
INTRODUCTION
Polymer composites, in this day and age, find their applicability in a multitude of engineering equipment as well as everyday items such as racing car bodies, aircraft, sports goods, biomedical implants, etc. Composite materials can be defined as materials that consist of two or more chemically and physically different phases separated by a distinct interface. Composite materials contain a strong load-carrying material which is known as reinforcement embedded in a weaker material which is known as the matrix. Reinforcement provides strength, rigidity, and stability in supporting the structural load. A very notable property of composite materials is that individual chemical and physical properties of the constituents are retained but when they are adhered to or combined, they produce qualities that individual constituents would be incapable of producing alone. Polymer composites have many advantages such as great specific stiffness, great impact absorption capacity, and relatively low cost. It makes sense that modern industries and research scholars all over the world have been paying keen attention to composite materials. Composite materials have many advantages over conventional materials such as wood, steel, etc. They have properties that cannot be found in nature. This is so because composite materials have properties that are a combination of two or more constituents of the composite material. Fibers that are used in reinforcements can be classified into two types: Natural and synthetic fibers. Recently, there is a growing interest in fiber-
reinforced polymer composites, where the fibers are the reinforcements of mainly thermosetting polymers. This growing interest is fuelled because there is strong evidence that supports that fiber reinforced polymer composites are environment friendly [1] the mechanical properties of the composite material depend on its physical compositions such as the structure of fibers, moisture content, cellulose content, cross section [2]. Bamboo fibers have many advantages including a high aspect ratio and strong mechanical performance. Bamboo fiber is intended to replace glass fiber for a cleaner and more sustainable future for industries. The size of single bamboo fibers is 10-30µm in diameter and 1- 4mm in length [3]. Chicken feathers contain 91% keratin, 1% lipids, and 8% water. Chicken father fiber (CFF) possesses good resilient property because of the presence of more void spaces in its cross-section[4] The unique feathers for a number of potential applications. Many types of research have been done to determine the mechanical properties of bamboo fibers and Chicken Feather Fibers (CFF) separately, but a composite material of bamboo fibers and Chicken Feather Fibers (CFF) examined in this work is a new class of composite material, in which no known previous publication has been made.
Table 1: The mechanical properties of various natural/synthetic fiber reinforced composites
S.No
Reinforcement Material
Matrix Material
Tensile Strength (MPa)
Flexural Strength (MPa)
Ref
1
Banana, coir
Epoxy
16.43
20.52
[5] 2
Banana Eglass
Polyester
18.1
193.75
[6] 3
Basalt,carbon
Polyamide
86.18
158.57
[7] 4
Coir,human hair
Epoxy
18.5
56
[8] 5
Silk, Flax
Epoxy
41
121
[9] 6
Sisal, Coir
Epoxy
17.92
170.76
[10] -
EXPERIMENTATION
In this research work, bamboo fibers and chicken feather fibers are used for fabricating the composite material. After treating the fibers chemically, they are hammered to obtain thin fibers. The epoxy resin and hardener were purchased from Shankar Dyes and Chemicals, New Delhi, India. The composite was prepared by using the hand layup method given in Fig 6, which is a closed molding method
done manually. The composites were divided into five different concentrations. Bamboo stems were cut into thin sticks and were immersed in 1% NaOH solution for 10 hours at 70°C. The chicken feathers were also treated with 1% NaOH solution and 2% Ethanol to remove unwanted smells and to increase the bonding between the fibers and the resin. The fabrication route for bamboo and chicken feathers is given in table 1. After the chemical treatment is finished, the already softened bamboo sticks were manually hammered to obtain thin and long fibers. The pre-treated bamboo and chicken feathers along with treated bamboo and chicken feathers are shown in figure 1. The bamboo fibers and chicken feather fibers were divided into five different concentrations in which the behavior of chicken feather fibers with respect to a constant concentration of bamboo fibers were observed. The molds for the hand layup method were made with cardboard material. The resin was poured into the molds, the composite laminate has a dimension of 300mmx300mmx4mm. This particular dimension was chosen to conduct the specimen testing according to ASTM 3039 and certain allowances are kept to obtain accurate results. The composite laminate has four layers in which the bamboo fibers and chicken feathers are arranged on top of each other. For the composites which undergo the flexural strength test, the dimension chosen was 180mmx20mmx10mm; this dimension was chosen specifically to conduct the testing to ASTM D790.
Fig 1: Process flowchart of hybrid composites
Fig 2: Untreated Bamboo Sticks Fig 3: Chemically Bamboo Sticks
Fig 4: Untreated Chicken Feather Fig 5: Chemically treated Chicken feather
Fig 6: Hand Layup method [11]
Tensile strength test:
Ultimate Tensile Strength (UTS) is the maximum stress that a material can withstand while being stretched or pulled before fracture. In the present work, the tensile test for the specimens using a Universal Testing Machine was conducte according to ASTM D3039. The specimens of size 250mmX25mmX4mm were tested with a gauge length of 50mm in tensile mode at a crosshead speed of 1mm/min and their average values were reported. The set up of the tensile test is given in Fig 7.
Ultimate Tensile Strength was determined using the equation: Ultimate Tensile Strength= Maximum load in N/Cross sectional area in mm2
Flexural Strength test:
The use of flexural tests to determine the mechanical properties of polymeric composites is largely employed because of its relative simplicity of the method of testing, instrumentation, and testing equipment required. The flexural strength of the specimens was determined by using three point bending test as per ASTM D790. The specimen having dimensions 180mmX20mmX10mm were tested with a span length of 250mm and their average values were reported. The set up of the flexural strength test is given in Fig 8.
The Flexural Strengths of the composites were determined by using the formula:
FS= 3PL/2BD2
Where, FS- Flexural Strength [N/mm2]
P- Peak Load [N], L- Support Length
B- Breadth of the specimen, D- Depth of the specimen
Fig 7: Ultimate Tensile strength [12]
Fig 8: Flexural Strength test set up [13]
-
OBSERVATIONS FROM THE TESTS CONDUCTED
Tensile Strength Test:
The bamboo fibers and chicken feather fibers reinforced hybrid composites were prepared with different weight fractions and tested in the universal testing machine. The tensile strength of different weight fractions of hybrid composites for the tensile test is presented in table 2. From the table, it can be seen that the maximum tensile strength occurs at 40% Bamboo fibers and 0% CFF (72.555 MPa) compared to other hybrid composites. The weight fraction of bamboo was kept constant to determine the performance of the CFF in the overall tensile strength of the composite. At 40% bamboo fibers and 10% CFF the tensile strength was found to be 41.049 MPa. At 40% bamboo fibers and 20% CFF, the tensile strength was found to be 35.191 MPa. At 40% bamboo fibers and 30% CFF the tensile strength was found to be 44.041 MPa. At 40% bamboo fibers and 40% CFF, the tensile strength was found to be 32.452 MPa. The average tensile strength of the composites was found to be
-
MPa. The variation of total weight fraction with tensile strength is given in Fig 9.
Flexural Strength test:
The bamboo fibers and chicken feather fibers reinforced hybrid composites were prepared with different weight fractions and tested in the universal testing machine. The flexural strength of different weight fractions of hybrid
composites for the bending test is presented in table 3. From the table, it can be seen that the maximum flexural strength occurs at 40% Bamboo fibers and 10% CFF (227.25 MPa) compared to other hybrid composites. At 40% bamboo fibers and 0% CFF the flexural strength was found to be 49.5 MPa. At 40% bamboo fibers and 20% CFF, the flexural strength was found to be 102.375 MPa. At 40% bamboo fibers and 30% CFF, the flexural strength was found to be 97.8 MPa. At 40% bamboo fibers and 40% CFF, the flexural strength was found to be 60.1 MPa. The average flexural strength of the composites was found to be 107.405 MPa. The variation of total weight fraction with flexural strength is given in Fig 10.
Table 2: Tensile test values
TRIAL
BAMBOO FIBER (%
wt)
CFF (%wt)
UTS (MPa)
AVERAGE UTS (MPa)
1
40
0
72.555
2
40
10
41.049
3
40
20
35.191
45.65
4
40
30
44.041
5
40
40
32.452
Table 3: Flexural strength test values
TRIAL
BAMBOO FIBER
(%wt)
CFF (%wt)
UTS (MPa)
AVERAGE UTS (MPa)
1
40
0
49.5
2
40
10
227.25
3
40
20
102.375
107.45
4
40
30
97.8
5
40
40
60.1
Fig 9: The variation of total weight fraction with tensile strength
Fig 10: The variation of total weight fraction with flexural strength
-
-
CONCLUSIONS
The bamboo and chicken feather fibers reinforced hybrid composites are prepared at different weight fractions and subjected to tensile and flexural strength tests. From the experimental study, the following conclusions can be inferred:
At 40% bamboo fiber loading and 0% chicken feather fiber loading, the tensile strength is maximum. Therefore, we can conclude that bamboo fiber is the main contributor to the overall tensile strength of the composite.
Bamboo fiber at 40% and chicken feather fiber at 30% give better tensile strength than other concentrations, therefore we can conclude that the optimum concentration of chicken feather fiber for maximum tensile strength is 30% fiber loading.
At 40% bamboo fiber loading and at 10% Chicken feather fiber loading, we have the maximum flexural strength. The flexural strength is minimum at 40% bamboo fiber loading and at 40&% chicken feather fiber loading.
The hybrid composite developed shows superior tensile properties when compares with other composites such as, coir-human hair, silk-flax, sisal-coir composites etc and it has superior flexural properties when compared to other composites such as coir-human hair, jute-flyash, sisal- pineapple etc.
ACKNOWLEDGEMENT
First and foremost, praises and glory to God, the Almighty for his blessings throughout our research.
We take this opportunity to express our sincere gratitude to our guide, Dr. BM Rajaprakash, Professor, Department of Mechanical Engineering, University Visvesvaraya College of Engineering, Bangalore University, Bengaluru, for his meticulous guidance, supervision and continuous support throughout the research work.
We would like to thank all the staff of Raghavendra Spectro Metallurgical Laboratory, Bengaluru, for granting us permission to conduct our experimental work in their Research Laboratory.
We wish to express sincere appreciation to our beloved parents who have been our constant source of inspiration throughout our research work.
A final word of thanks is reserved for all our friends for their constant encouragement all throughout our research work.
REFERENCES
-
Pankaj Tripathi, Kuldeep Yadav, hjBiodegradation of natural fiber and glass fiber polymer composite. A review IJIRAE, Issue 04,Volume 4, April 2017.
-
S. Satish, K. Kumaresan, L. Prabhu, N. Vigneshkumar, Experimental investigation on Volume Fraction of Mechanical and Physical Properties of Flax and Bamboo Fibers Reinforced Hybrid Epoxy Composites Polymer and Polymer composites,Volume 25, Issue 3, 2017.
-
Yu, Y., Wang, H., Lu, F. et al. Bamboo fibers for composite applications: a mechanical and morphological investigation. J Mater
Sci 49, 25592566 (2014) https://doi.org/10.1007/s10853-013-7951-
z
-
Paraveej Shirahatti, A thesis on Mechanical properties of Risk Husk and Aramid fibers reinforced in vinyl ester Polymer Composite, UVCE 2017
-
T. Hariprasad, G.Dharmalingam and P.Praveen Raj Study of mechanical properties of banana-coir hybrid composite using experimental and FEM tchniques Journal of Mechanical Engineering and Sciences (JMES), ISSN (Print): 2289-4659; e-
ISSN: 2028-2508 CODEN: JMESC
-
M. R. Sanjay, G.R. Arpitha, L. Laxmana Naik, K. Gopalakrishna, B. Yogesha Studies on Mechanical Properties of Banana/E-Glass Fabrics Reinforced Polyester Hybrid Composites, J. Mater. Eviron.
Sci. 7 (9) (2016) 3179-3192, ISSN: 2028-2508 CODEN: JMESC
-
Doughlas J. Gardner, Yousoo Han, Mechanical properties of hybrid basalit-carbon fiber filled recycled polypropylene and polyamide-6 composites, University of Maine, Advanced Structures and Composites Center Alper Kiziltas, Debbie Mielewski, Ford Motor Company
-
Raghavalu Thirumalai, Durai Prabhakaran, Lgstrup Andersen, Tom, Markussen, Christen Ma;te, Madsen, Bo, Lilholt, Hans, Tensile and compression properties of hybrid composites- A comparative study Published in: Proceedings of the 19th International Conference on Composite Materials (ICCM19), 2013
-
P. Ramesh, J. Ayyamperum, P. Boopathi, V.M. Gokulakannan, Analysis of Mechanical Properties of Silk/Flax Hybrid Epoxy Composite Material, International Journal of Innovative Research in Science, Engineering and Technology, Vol 4, Special Issue 6,
May 2015
-
Madhukiran.J, Dr. T. Venkteswara Rao, Dr S. Madhusudan, Dr. R. Umamaheswara Rao, Evaluation of the Mechanical Properties on Sisal-Coir Hybrid Natural Fiber Composites, International Journal Of Engineering Research And Development, Volume 13, Issue 9 (September 2017), PP. 43-49.
-
Udupi, Sathish & Rodrigues, Lewlyn. (2016). Detecting Safety Zone Drill Process Parameters for Uncoated HSS Twist Drill in Machining GFRP Composites by Integrating Wear Rate and Wear Transition Mapping. Indian Journal of Materials Science. 2016. 1-8. 10.1155/2016/9380583.
-
Santos, Igor & Nieves, Javier & Bringas, Pablo & Penya, Yoseba. (2010). Machine-Learning-Based Defect Prediction in High-
Precision Foundry Production
-
Flexural strength of alumina ceramics: Weibull analysis – Scientific Figure on ResearchGate. Available from: https://www.researchgate.net/figure/Three-point-bending-test- 8_fig1_264713313 [accessed 15 Jun, 2021]
-
Md hasan Ikbal, Ayub Nabi Khan, S.M Kamrul Hasan, Mukwaya Vincent, Study on effect of fiber weight fraction on physical and mechanical behaviour of jute-epoxy composite laminates Textilefocus.com, July 2017