
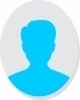
- Open Access
- Authors : Rajesh Chaudhari, Soham Pethkar, Payal Kohade
- Paper ID : IJERTV14IS010024
- Volume & Issue : Volume 14, Issue 1 (January 2025)
- Published (First Online): 16-01-2025
- ISSN (Online) : 2278-0181
- Publisher Name : IJERT
- License:
This work is licensed under a Creative Commons Attribution 4.0 International License
Additive Manufacturing of AISI 316L Stainless Steel Block by Weld Overlay Technique
Rajesh Chaudhari, Soham Pethkar, Payal Kohade
Vishwakarma Institute of Technology, Pune, India
Abstract.
Stainless steel 316L (SS 316L) is known for its exceptional corrosion resistance, robust mechanical properties. Additive Manufacturing is basically a process of building a 3D object layer by layer. Stainless Steel 316 L has versatile applications across various industries, including the areas such as aerospace, medical, and marine engineering. The main objective of this study is to assess and compare the mechanical properties i.e. Hardness, microstructural traits, and overall efficiency of SS 316L parts produced using arc welding technique. Through a thorough examination, results of characteristic microstructure using inverted optical microscope and study of hardness using Wickers hardness testing machine are carried out with different magnifications. This research adds to the expanding field of understanding in materials science and engineering and enhancing manufacturing methods.
Keywords Additive manufacturing, Arc welding, Hardness test, Inverted Optical Microscope, Microstructure, Stainless steel 316L.
INTRODUCTION
Additive manufacturing (AM) is leading in industrial innovation, showcasing the creative abilities of humans by revolutionizing the manufacturing process from traditional subtractive techniques to a method that builds materials step by step. Additive manufacturing is process of building parts in small layer by layer method [1][2][3]. Stainless steel 316L is a low carbon version of the 316-steel alloy, which is part of the austenitic family of stainless steel having melting point 1375 °C 1400 °C. It is known for its corrosion resistance. By having a lower carbon content, it helps to minimize carbide precipitation during welding, which maintains its corrosion resistance in welded structures [4][5]. Stainless steel 316L stands out for its exceptional resistance to corrosion and strong mechanical capabilities, bridging the gap between AM's possibilities and real-world utility. This material is an essential component in industries that require top-tier performance and dependability [6][7][8]. This paper presents the study to investigate the effects of this method on the micro structure and mechanical properties of the material. Additionally, the research outlines additional goals that involve optimizing arc welding settings to improve both the quality and productivity of the production process, aiming to expand the possibilities for leveraging SS 316L in the field of AM [9].
The arc welding technique, a hopeful method in Additive Manufacturing, faces challenges like thermal distortion and residual stresses that may compromise the structural integrity and performance of the final prototype [10][11][12]. The main goal of this research study is to thoroughly analyze and understand the characteristics of Stainless steel 316L material when shaped using arc welding. The wire arc additive manufacturing process can be used to create or improve components with superior mechanical qualities and resistance to corrosion in high- temperature settings, such as applications in nuclear reactors, aerospace, medical, automotive, and marine applications [13][14][15].
.
LITERATURE REVIEW
-
Bintao Wu et al. reviewed the mechanical properties and micro-structural analysis using wire arc additive manufacturing (WAAM) for various metals along with their alloys such as steel, aluminum, titanium etc. It discusses process planning and fabrication, sensing, controlling and also suggests future research directions. WAAM research integrates materials science, thermo-mechanical engineering, and process planning. Automation is the next step, requiring research in process control, optimization, and automated planning [16][17].
-
Vahid Amiri et al. used the method of WAAM for Stainless steel 316L and Nickel based- Inconel 625 to examine the analysis of microstructure and mechanical properties. Initially eight layers were built with 316L Stainless steel, followed by eight layers of Inconel 625. They used the Nital etching solution for 316L stainless steel and mixture of HCl, HNO3 and glycerin for Inconel 625. The results were finally performed using the optical microscope, the field emission scanning electron microscope and along it, X-ray energy diffraction spectroscopy detector was used for the microstructural study [18].
Nital etching solution 2 ml Nitric acid (HNO3) + 98ml Alcohol (CH3OH)
-
Amagoia Paskual et al. studied the analysis of mechanical properties of two alloys, AISI 316L Stainless steel and Ti6Al4V using three welding processes namely Plasma arc welding, Fronius cold metal transfer and Air Liquide Top Tungsten inert gas. The results showed the evaluation of mechanical properties using tensile test specimens in two orientations: along the bead generation direction and the bead vertical overlapping direction with the help of three welding processes as mentioned [19].
-
Brittany A. Branch et al. acquired the method of laser powder bed fusion (LBPF) wherein a thin layer of metal powder was spread on the building platform and melted using focused laser.[20] This method was performed to fabricate the 316L stainless steel lattices with ProX DMP 200 3D systems. Post fabrication, the defects and the internal structure of the octet geometry were characterized using an X3000 CT machine and Varex 2520DX X-ray detector. Lastly CT scan images were converted into binary format in order to identify clearly using the MATLAB simulation [21]. F. Khodabakhshi et al. also utilized the same technique, the LBPF technique with the focus on the hot deformation characteristics [22].
-
Tiago A. Rodrigues et al. examined the phase transformation after wire arc additive manufacturing and gas metal arc welding in 316L Stainless steel using synchrotron X-ray diffraction technique. They heated the steel at different temperatures such as at 400°C, 950°C, 1050°C, and 1200°C in order to see how the -ferrite, a part of the steel dissolves over time. Finally, they measured the hardness and electrical conductivity and showed the affection of each phase with the properties of 316L Stainless steel [23].
-
Simon Sankaré et al. used Laser additive manufacturing of AISI 316L Stainless steel. Basically, two structures were built of different dimensions i.e. (height-100mm, length-25mm) and (height-25mm, length-100 mm) in order to differentiate among the two. Micro-structural results were carried out using optical confocal, an Olympus model and scanning electron microscope. Tensile and mechanical tests were performed on the sample having height 100mm, with the help of MTS 810 machine. X-ray diffraction technique was employed to study the phase transformations in the material for the sample having height 25mm [24].
METHODOLOGY MATERIAL SELECTION
FIGURE 1. Chemical composition of 316L Stainless steel.
COMPONENTS
(a) |
(b) |
FIGURE 2. Components used for the fabrication of the prototype (a) Arc Welding Machine (b) Electrodes of 316L Stainless Steel.
(a) |
(b) |
FIGURE 3. Instruments used for Testing (a) Inverted Optical Microscope to study Micro structure b) Vickers hardness testing machine t study Hardness Test.
FLOWCHART
FIGURE 4. Flowchart of the Additive Manufacturing of Stainless Steel 316L.
THEORY
This project aims to investigate the micro-structural study and the mechanical properties of 316L Stainless steel, an alloy having low carbon content and superior strength characteristics. Additive manufacturing of Stainless steel 316L was conducted on the base metal plate having the dimensions 100 mm x 10 mm x 50 mm using the technique of arc welding, utilizing the current range and operating voltage as shown in the Table 1. The time required to build consecutive layer is depicted in Figure. 5. Post welding, the removal of slag process carried out with the help of chipping hammer and wire brush for each consecutive layer.
Furthermore, the prototype underwent machining using angle grinder and the final prototype is shown in Fig. 6(a). A small piece of the prototype was trimmed to facilitate smooth characterization and result analysis. After that the prototype was polished on dual disc polishing machine using sand paper. Subsequently, lapping process was executed with diamond paste for mirror finishing and surface was henceforth cleaned. The metal surface contained some patterns denoted as micro structure. To examine the micro-structural outlines, etching solution was used due to gradient nature of the material. Different acids are used depending on the material.
The polished surface was then henceforth etched using 37% hydrochloric acid (HCl) for a cumulative 15 minutes. Due to the corrosion resistant nature of 316L stainless steel, an alternative was required. The samples polished surface was finally etched using 30% nitro hydrochloric acid, which is a mixture of concentrated Hydrochloric (HCl) acid and concentrated Nitric acid (HNO3). The etching was done by swabbing the acid on the surface continuously for 15 seconds at a time. 10 such swabbing cycles were performed in order for smooth characterization. Afterwards the sample was also placed in 5ml of nitro hydrochloric acid for a cumulative 15 minutes, 3 minutes at a time. The action of the acid on the surface revealed the micro structure of the 316L stainless steel sample.
Table 1. Arc Welding Machine specifications.
Specifications |
Values |
Operating Voltage |
220 V |
Current Range |
100 – 110 A |
Table 2. Specifications of 316L Stainless Steel electrodes
Specifications |
Values |
Current Range |
80 110 A |
Temperature Range Dimensions |
-120 °C +400 °C 3.15 × 350 mm |
FIGURE 5. Time (in seconds) versus Number of layers build during fabrication.
(a) |
(b) |
FIGURE 6. Dimensions of the fabricated prototype (a) After Machining and polishing (b) As formed by Additive manufacturing.
MATHEMATICS
Number of layers required for welding(N) = 16 Time taken to lay the welds(T) = 3047 seconds.
Feed rate =
(1)
Feed rate (in seconds) = 5.251 × 10-3 layers/seconds. Feed rate (in minutes) = 0.3150 layers/minute.
Feed rate (in hours) = 1.890 × 10-1 layers/hour.
RESULTS AND DISCUSSIONS
Analysis of Micro structure
Following Additive manufacturing, Micro structure analysis was conducted. The results were captured using Inverted microscope at various magnifications as illustrated in Figure 7 and Figure 8. This analysis revealed that 316L Stainless steel exhibits low porosity.
(a) |
(b) |
FIGURE. 7(a, b) Micro structure captured at 400x zoom.
(a) |
(b) |
FIGURE. 8(a, b) Micro structure captured at 200x zoom.
STUDY OF HARDNESS TEST
The sample underwent hardness testing for three times using a Vickers hardness testing machine, and the results were carried out which is summarized in the Table 3. Based on the below data as shown in Table 3, Average value of hardness testing has been found out to be 205.8 HV. Table 3. Observations revealed after performing hardness testing. Observations Hardness values 1 202.6 HV 2 207.3 HV 3 207.5 HV The characterization of the samples done by Moritz Braun et. al on the welded joints from Laser Powder bed fusion (LPBF) parent material and hot rolled material, the findings showed that for LPBF specimens, the hardness range varied from 220 HV to 250 HV, whereas in the hot rolled specimens, the hardness was approximately 190 HV, across both the weld metal and base metal [25]. For Shot peened reference (REF) and Additive manufacturing (AM) produced using selective laser melting (SLM), the measured micro hardness was found to be 183 HV and 230 HV, respectively. The process of shot peening significantly increased hardness in both REF and AM samples, with the REF showing a 160% increase and the AM exhibiting 108% increase. This difference is attributed due to the transformation of austenite to martensite in REF samples and shallower grain refinement depth in AM samples [26][27]. In comparison with the results given by other authors as shown in Table 4, the characterization of the samples fabricated using arc welding technique for Additive manufacturing of 316L Stainless steel in this project revealed that the hardness values ranging between 200 HV and 208 HV, shown in Table 3. Table 4. Comparison of the hardness values produced using different techniques. |
||
Techniques |
Hardness value |
References |
Laser powder bed fusion (LPBF) |
220-250 HV |
25 |
Hot rolled specimen |
190 HV |
25 |
Selective Laser melting (SLM) Arc Welding |
180-230 HV 205.8 HV |
26, 27 Our study |
FUTURE SCOPE
-
The future research could focus on ensuring more better quality and capability of fabricated product.
-
Expanding the applications of additive manufacturing to higher level and other industries as well to evaluate its versatility, its cost effectiveness and rapid prototyping.
-
Future work could also be exploring other new alloy compositions for development of additive manufacturing leading to amplify properties such as corrosion resistance improvement, growth in strength.
-
More Research could be done by optimizing the welding parameters such as layer thickness, beam or laser power and scan speed to enhance mechanical properties of material components and precision.
-
Applications in medical field like surgical tools by investigating bio-compatibility and sustainability of 316L stainless steel through additive manufacturing.
-
Assessing the impact of 316 L stainless steel additive manufacturing on environment and focusing on the thermal stability, waste generation, consumption of energy and practicing more sustainable manufacturing methods.
CONCLUSION
This project aims to perform additive manufacturing of stainless steel 316L via arc welding technique. Here is the exploration of the obtained results:
-
Method of Additive manufacturing was adapted to fabricate the multi layered material of 316L Stainless Steel using Arc welding technique and henceforth successfully carried out.
-
Machining and polishing of the prototype using various methods achieved high preision and overall integrity of the structure.
-
The detailed analyzation of Micro structure and hardness of the sample were made using the Inverted optical microscope and the Vickers hardness testing machine, respectively.
-
Microstructural observations showed the precipitates inside the grains as well as at the grain boundaries at 200x zoom and 400x zoom.
-
The hardness testing observations showed the average hardness as 205.8 HV.
-
The results show high potential of using 316 L stainless steel in additive manufacturing and rapid utilization in the large industries like automotive, aerospace and the medical fields.
REFERENCES
-
Herzog, Dirk, V. Seyda, E. Wycisk, and C. Emmelmann. "Additive manufacturing of metals." in Acta Materialia 117 (Elsevier, Tehran, 2016), 371-392.
-
Abdulhameed, Osama, A. Al-Ahmari, W. Ameen, and S. H. Mian. "Additive manufacturing: Challenges, trends, and applications." Advances in Mechanical Engineering 11(2) (2019), p. 1687814018822880.
-
H. Bikas, P. Stavropoulos and G. Chryssolouris, Additive manufacturing methods and modelling approaches: a critical review in The International Journal of Advanced Manufacturing Technology, 83 (Springer, Greece, 2016), pp.389-405.
-
E Gorji, N., Recyclability of stainless steel (316 L) powder within the additive manufacturing process, Instituto de IngenierÃa y TecnologÃa (2019).
-
C. Morsiya, A review on parameters affecting properties of biomaterial SS 316L in Australian Journal of Mechanical Engineering, 20(3), pp.803-813 (2022).
-
J. P. Pragana, I. M. Braganca, L. Reis, C. M. Silva, and P. A. Martins, "Formability of wire-arc deposited AISI 316L sheets for hybrid additive manufacturing applications." Proceedings of the Institution of Mechanical Engineers, Part L: Journal of Materials: Design and Applications 235, no. 12 (2021), pp.2839-2850.
-
DAndrea, Danilo. "Additive manufacturing of AISI 316L stainless steel: a review." Metals 13, no. 8 (Italy, 2023), p. 1370.
-
T. A. Rodrigues, F. W. C. Farias, K. Zhang, A. Shamsolhodaei, J. Shen, N. Zhou, N. Schell, J. Capek, E. Polatidis, T. G. Santos and J. P. Oliveira, Wire and arc additive manufacturing of 316L stainless steel/Inconel 625 functionally graded material: development and characterization, Journal of materials research and technology, 21, (Elsevier Science, 2022), pp.237-251.
-
T. Pasang, A. Kirchner, U. Jehring, M. Aziziderouei, Y. Tao, C. P. Jiang, J. C. Wang, and I. S. Aisyah. "Microstructure and mechanical properties of welded additively manufactured stainless steels SS316L." Metals and Materials International 25 (Springer, 2019), pp. 1278- 1286.
-
V. T. Le and H. Paris, On the use of gas-metal-arc-welding additive manufacturing for repurposing of low-carbon steel components:
microstructures and mechanical properties, Welding in the World, 65(1), (Springer Nature, 2021) pp.157-166.
-
A. Karpagaraj, S. Baskaran, T. Arunnellaiappan, and N. Rajesh Kumar. "A review on the suitability of wire arc additive manufacturing (WAAM) for stainless steel 316." In AIP Conference Proceedings, vol. 2247, no. 1. AIP Publishing, 2020.
-
Dupont, N. John, and R. A. Marder. "Thermal efficiency of arc welding processes." Welding Journal-Including Welding Research Supplement 74, no. 12 (1995), p. 406s.
-
Mishra, K. Neeraj, J. Nakrani, V. Ajay, and A. Shrivastava. "Microstructural Evolution and Anisotropy in Stainless Steel 316L from Wire Arc Additive Manufacturing." in TMS Annual Meeting & Exhibition, pp. 290-298. (Springer Nature, Switzerland, 2024).
-
Brubaker, Nicholas, A. Hussam, S. Dhakal, N. V. Rooyen, M. L. Jaster, I. Charit, B. Jaques, and M. R. Maughan. "Investigating microstructure and properties of 316L stainless steel produced by wire-fed laser metal deposition." Journal of Materials Engineering and Performance (2022), pp. 1-12.
-
A. R. Kannan, S. M. Kumar, R. Pramod, N. S. Shanmugam, M. Vishnukumar, and S. Naveenkumar. "Microstructural characterization and mechanical integrity of stainless steel 316L clad layers deposited via wire arc additive manufacturing for nuclear applications." Materialwissenschaft und Werkstofftechnik 52, no. 6 (2021), pp. 617-623.
-
B. Wu, Z. Pan, D. Ding, D. Cuiuri, H. Li, J. Xu, and J. Norrish, A review of the wire arc additive manufacturing of metals: properties,
defects and quality improvement in Journal of manufacturing processes, 35, pp. 127-139.
-
J. P. Oliveira, T. G. Santos, and R. M. Miranda. "Revisiting fundamental welding concepts to improve additive manufacturing: From theory to practice." Progress in Materials Science 107 (Elsevier, 2020), p. 100590.
-
Amiri, Vahid, and Homam Naffakh-Moosavy. "Wire arc additive manufacturing of functionally graded carbon steel-stainless steel 316L- Inconel 625: Microstructural characterization and mechanical behavior." Journal of Advanced Joining Processes 9 (Elsevier, 2024): 100194.
-
A. Paskual, P. Ãlvarez, and A. Suárez. "Study on arc welding processes for high deposition rate additive manufacturing." Procedia Cirp 68 (Elsevier, Spain, 2018), pp. 358-362.
-
R. Groarke, R. K. Vijayaraghavan, D. Powell, A. Rennie, and D. Brabazon. "Powder characterizationmethods, standards, and state of the art." Fundamentals of Laser Powder Bed Fusion of Metals (2021), pp. 491-527.
-
-
Branch, B. A., Specht, P. E., Jensen, S., & Jared, B., Detailed meso-scale simulations of the transient deformation in additively manufactured 316 L stainless steel lattices characterized by phase contrast imaging in International Journal of Impact Engineering, 161 (U.S, 2022), p. 104112.
-
F. Khodabakhshi, N. Hasani, M. R. Kalaie, A. Hadadzadeh, M. A. Wells, and M. Mohammadi. "Dynamic recrystallization under hot deformation of additively manufactured 316 L stainless steel." Materials Characterization 202 (2023), p. 113055.
-
T. A. Rodrigues, J. D. Escobar, J. Shen, V. R. Duarte, G. G. Ribamar, J. A. Avila, E. Maawad, N. Schell, T. G. Santos, and J. P. Oliveira. "Effect of heat treatments on 316 stainless steel parts fabricated by wire and arc additive manufacturing: Microstructure and synchrotron X-ray diffraction analysis." Additive Manufacturing 48 (2021), p. 102428.
-
de Lima, Milton Sergio Fernandes, and Simon Sankaré. "Microstructure and mechanical behavior of laser additive manufactured AISI 316 stainless steel stringers." Materials & Design 55 (2014): 526-532.
-
M. Braun, J. Schubnell, A. Sarmast, H. Subramanian, L. Reissig, F. Altenhöner, S. Sheikhi, F. Renken and S. Ehlers, Mechanical behavior of additively and conventionally manufactured 316L stainless steel plates joined by gas metal arc welding in Journal of materials research and technology, 24 (Elsevier, Hamburg, 2023), pp.1692-1705.
-
T. Gundgire, T. Jokiaho, S. Santa-aho, T. Rautio, A. Järvenpää, and M. Vippola. "Comparative study of additively manufactured and reference 316 L stainless steel samplesEffect of severe shot peening on microstructure and residual streses." Materials Characterization 191 (2022), p.112162.
-
N. Iqbal, E. Jimenez-Melero, U. Ankalkhope, and J. Lawrence. "Microstructure and mechanical properties of 316L stainless steel fabricated using selective laser melting." MRS Advances 4, no. 44-45 (Cambridge University Press, 2019), pp. 2431-2439.