
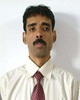
- Open Access
- Authors : Manoj Kundu , Arnab Mandal
- Paper ID : IJERTV11IS100065
- Volume & Issue : Volume 11, Issue 10 (October 2022)
- Published (First Online): 02-11-2022
- ISSN (Online) : 2278-0181
- Publisher Name : IJERT
- License:
This work is licensed under a Creative Commons Attribution 4.0 International License
Additive Manufacturing Process (3D Printing): A Critical Review of Techniques, Applications & Future Scope
Manoj Kundu1,
Assistant professor, Department of Mechanical Engineering,
DR. B.C Roy Engineering College, Durgapur, West Bengal, India,
Arnab Mandal2,
B.Tech Student, Department of Mechanical Engineering,
DR. B.C Roy Engineering College, Durgapur, West Bengal, India,
Abstract:- This research paper on 3D printing aims to create awareness in people to use 3d printing in everyday life by providing the current trend of how 3D printing techniques are used particularly in different fields of application .3D printing has become a big deal in the last few years which can help reinforce some concepts of coding and help everyone learn the process which is fairly simple; design, slice, print. More recently, 3D printing technology has become available to more people at a lower cost to create objects on demand locally. 3D printers are great for household use and students as, a 3D printer is a one-time investment with lifelong uses. This paper provides a high-level overview of 3D printing techniques, applications & future scope. The advantages and disadvantages of each technique are evaluated along with summarised typical geometries and designs used by each technique. The potentials of 3D printing technology and the future outlooks of 3D printed items are also presented here.
Keywords- Additive Manufacturing, 3D printing, 3D printers
INTRODUCTION
3D printing uses computer-aided design (CAD) to create three-dimensional objects using additive processes in which an object is created by laying down successive layers of material until the object is created. Each of these layers can be seen as a thinly sliced cross-section of the object. 3D printing is the opposite of subtractive manufacturing which is cutting out / hollowing out a piece of metal or plastic with for instance a milling machine. The process is extremely accurate, faster and much more efficient than other manufacturing processes especially for very complicated objects. Production time is cut and material waste is minimal compared to traditional manufacturing methods. While it is currently too slow to be used in mass production, 3D printing technology is still evolving and has the potential to massively disrupt both the manufacturing logistics and inventory management industries. Companies have used 3D printers in their design process to create prototypes since the late seventies. Using 3D printers for these purposes is called rapid prototyping.
A few examples of fields in which 3d printing is used-
-
Automotive – Automotive enthusiasts all over the world are using 3D printed parts to restore old cars. One such example is when Australian engineers printed parts to bring a Delage Type-C back to life. In doing so, they had to print parts that were out of production for decades.
-
3D printing for automotive brackets
-
Porsches 3D-printed custom seats
In the Rolls Royce example, the team was able to incorporate some really cool features into parts, including the 3D-printed brand name and a QR code, along with numbers to identify the specific, unique, part.
Ford 3D prints parts for high-performance Mustang Shelby GT500
-
3D-printed lug nuts that save car wheels from thieves
-
3D printing for motorsports
-
Aviation – GE Aviation has 3D printed 30,000 Cobalt-chrome fuel nozzles for its LEAP aircraft engines. GEs fuel nozzles also made their way into the Boeing 787 Dreamliner, but its not the only 3D printed part in the 787. The 33-centimeter-long structural fittings that hold the aft kitchen galley to the airframe are 3D printed by a company called Norsk Titanium. Norsk chose to specialize in titanium because it has a very high strength-to-weight ratio and is rather expensive, meaning the reduction in waste enabled by 3D printing has a more significant financial impact than compared to cheaper metals where the costs of material waste are easier to absorb. Rather than sintering metal powder with a laser like most metal 3D printers, the Norsk Merke 4 uses a plasma arc to melt a metal wire in a process called Rapid Plasma Deposition (a form of Directed Energy Deposition) that can deposit up to 10kg of titanium per hour. A 2kg titanium part would generally require a 30kg block of titanium to machine it from, generating 28kg of waste, but 3D printing the same part requires only 6kg of titanium wire.
-
Jewellery
-
Construction -Is it possible to print a building? yes, it is. 3D printed houses are already commercially available. Some companies print parts prefab and others do it on-site.
-
Footwear- Adidas 4D range has a fully 3D printed midsole and is being printed in large volumes. Eyewear- The market of 3D printed eyewear is forecasted to reach$3.4 billion by 2028. The Luxexcel VisionEngine 3D printer uses a UV-curable acrylate monomer to print two pairs of lenses per hour that require no polishing or post-processing of any kind. The focal areas can also be completely customized so
that a certain area of the lens can provide better clarity at a distance while a different area of the lens provides better vision up close.
-
Healthcare- Over the last decade, more than 100,000 hip replacements have been 3D printed by GE Additive. The Delta-TT Cup designed by Dr. Guido Grappiolo and Lima Corporate is made of Trabecular Titanium, which is characterized by a regular, three- dimensional, hexagonal cell structure that imitates trabecular bone morphology. Another 3D printed healthcare component that does a good job of being undetectable is the hearing aid. Nearly every hearing aid in the last 17 years has been 3D printed thanks to a collaboration between Materialise and Phonak. Phonak developed Rapid Shell Modelling (RSM) in 2001.
-
Dental- The moulds are 3D printed with both resin and powder-based 3D printing processes, but also via material jetting. Crowns and dentures are already directly 3D printed, along with surgical guides.
-
Bio-printing- As of the early two-thousands 3D printing technology has been studied by biotech firms and academia for possible use in tissue engineering applications where organs and body parts are built using inkjet techniques. Layers of living cells are deposited onto a gel medium and slowly built up to form three dimensional structures.
-
Food- Restaurants like Food Ink and Melisse use 3d printing as a unique selling point to attract customers from across the world.
-
Education- Educators and students have long been using 3D printers in the classroom. 3D printing A few other applications of 3d printing include-
-
Movies-
-
-
Props can take hours of hard work to create and apply. With 3D printing, many of those props can be created and re-created faster, easier, and without starting from scratch.
-
3D printing techniques have been featured in movies such as IronMan, The Hobbit, Jurassic Park, Avatar, The Muppets, Terminator Salvation, RealSteel, Paranorman, The Avengers and Paranorman.
-
3D Bioprinting Can Create Pseudo Organs Although the size of a penny, this "lung" shows the feasibility of 3D printing living cells
enables students to materialize their ideas in a fast and affordable way. Printed prototypes are also common in the arts, animation and fashion studies as well.
-
3D Printing Can Make an Unsmashable Guitar
-
3D Printers Can Produce Iridescent Surfaces
-
3D printing is launching intospace.
-
-
NASA researches are currently working on figuring out how to bring 3D printing technology to space.
TYPES OF 3D PRINTING TECHNOLOGIES AND PROCESSES
The most common 3D printing processes are:
-
Stereolithography (SLA), which is a vat photopolymerization technology
-
Fused deposition modelling (FDM), which is a material extrusion technology
-
Selective laser sintering (SLS), which is a powder bed fusion technology
ISO/ The American Society for Testing and Materials (ASTM), standard 52900 was created in 2015 to standardize the exploding terminology around 3D printing and to classify each of its methods. A total of seven 3D printing process categories was established:
1. Vat polymerization
-
Stereolithography (SLA)
-
SLA was invented in 1986 by Charles Hull.
-
It is the first modern 3D printing measure that dominate at delivering elevated levels of detail, smooth surface completions, and tight resistances. Its generally utilized in the clinical business and basic applications incorporate anatomical models and microfluidics.
-
Stereolithography employs a vat of liquid curable photopolymer resin and an ultraviolet laser to build the objects layers one at a time. For each layer, the laser beam traces a cross-section of the part pattern on the surface of the liquid resin. Exposure to the ultraviolet
laser light cures and solidifies the pattern traced on the resin and fuses it to the layer below.
-
After the pattern has been traced, the SLAs elevator platform descends by a distance equal to the thickness of a single layer, typically 0.05 mm to 0.15 mm (0.002 to 0.006). Then, a resin- filled blade sweeps across the cross section of the part, re-coating it with fresh material. On this new liquid surface, the subsequent layer pattern is traced, joining the previous layer.
-
Depending on the object & print orientation, SLA often requires the use of support structures.
-
In particular, an SLA printer utilizes mirrors, called galvanometers. One is situated on the X- pivot, the other on the Y-hub. These point to the purpose of a laser pillar across the tank of gum, specifically
relieving and setting across-part of the item in the forming zone, developing it layer by layer.
-
SLA is a quick prototyping measure where exactness and accuracy are taken seriously. It can create objects from 3D CAD information in only a couple of hours. This is a 3D printing measure its fine subtleties and precision by changing over fluid photopolymers (a unique kind of plastic) into strong 3D items, each layer in turn. The plastic is initially warmed to transform it into a semi-fluid structure, an afterward, it solidifies on contact. The printer develops every one of these layers utilizing a bright laser, coordinated by X and Y filtering mirrors.
-
A recoater sharp edge also gets across the surface right before the next step to guarantee each thin layer of gum spreads equitably across the article. The print cycle proceeds thusly, building 3D items from the base up. When finished, the 3D part will typically have a synthetic shower to eliminate an overabundance. Its additionally basic practice to post-fix the article in a bright broiler. This makes the product more grounded and steadier.
-
-
APPLICATION: SLA printing has gotten support from many assortments of ventures. A portion of these incorporate auto, clinical, aviation, diversion, and furthermore to make different customer items.
-
ADVANTAGES: Smooth surface finish; print complex pattern; best for miniatures; short print time; easy ergonomics; variety of material choice; easily portable; compact design
-
DISADVANTAGES: Easy to handle but still some parts require attention; high cost; the laser and transparent display are fragile; could not print large prints; somewhat weak in strength; need curing after print; not environment friendly; required perfect assembly of the printer.
-
PRINTERS: Vipers, ProJets, and iPros 3D printers fabricated by 3D Systems.
-
-
Digital Light Processing (DLP)
-
It makes use of light and photosensitive polymers.
-
The primary difference between the two technologies is that DLP uses a digital light projector screen whereas SLA uses a UV laser.
-
DLP is relatively quick compared to other 3D printing technologies. DLP 3D printers can image an entire layer of the build all at once, resulting in faster build speeds.
-
Light is projected onto the resin by light- emitting diode (LED) screens or an ultraviolet (UV) light source, such as a lamp. It is directed onto the build surface by a Digital Micromirror Device (DMD), which is an array of micro-mirrors that control where the light is projected and generate the light pattern on the build surface.
-
Since the projector is a digital screen, the image of each layer is made up of square pixels, so each layer is formed from small rectangular blocks called voxels.
-
While frequently used for rapid prototyping, the higher throughput of DLP printing makes it suitable for low-volume production runs of plastic parts. Their strengths are they have fine feature details and smooth surface finish while they are limited by being brittle, therefore unsuited for use as mechanical parts.
-
APPLICATION: Common applications for SLA and DLP are injection mould-type polymer prototypes, jewellery, dental applications, and hearing aids. Regular applications for SLA and DLP are infusion shape type polymer models, adornments,
dental applications, and amplifiers. They have fine element subtleties and smooth surface completion.
-
ADVANTAGES: High print speed, excellent accuracy of laying, different application areas, the low cost of printers.
-
LIMITATION: They are restricted by being weak, in this way unsatisfactory for use as mechanical parts.
-
-
Continuous Liquid Interface Production (CLIP)
One of the fastest processes using Vat Photopolymerisation is called CLIP, short for Continuous Liquid Interface Production, developed by Carbon.
Digital Light Synthesis-
-
The heart of the CLIP process is Digital Light Synthesis technology. In this technology, light from a custom high-performance LED light engine projects a sequence of UV images exposing a cross section of the 3D printed part causing the UV curable resin to partially cure in a precisely controlled way.
-
Oxygen passes through the oxygen permeable window creating a thin liquid interface of uncured resin between the window and the printed part known as the dead zone which is as thin as ten of microns. Inside the dead zone, oxygen prohibits light from curing the resin situated closest to the window therefore allowing the continuous flow of liquid beneath the printed part. Just above the dead zone the UV projected light upwards causes a cascade like curing of the part.
-
Simply printing with Carbons hardware alone does not allow for end use properties with real world applications. Once the light has shaped the part, a second programmable curing process achieves the desired mechanical properties by baking the 3d printed part in a thermal bath or oven. Programmed thermal curing sets the mechanical properties by triggering a secondary chemical reaction causing the material to strengthen achieving the desired final properties.
-
Components printed with Carbons technology are on par with injection moulded parts. Digital Light
Synthesis produces consistent and predictable mechanical properties, creating parts that are truly isotropic.
-
APPLICATIONS: Medical equipment/ tools/ impressions; Footwear midsoles & athletic equipment; Automotive parts; Prototyping; An alternative process to injection moling; End-use functional parts & direct digital manufacturing
-
ADVANTAGES: Have the accuracy and the surface quality of DLP/SLA prints but are completed
100 times faster, enhanced surface finish, parts are watertight, fully isotropic (have strength in any orientation), and have increased strength over SLA/DLP prints, variety of material choice
-
LIMITATIONS: very expensive; still under active patent, so alternatives will not be available; high cost
-
MATERIAL EXTRUSION
-
Fused Deposition Modelling (FDM)
-
-
-
It is a common desktop 3D printing technology for plastic parts.
-
An FDM printer functions by extruding a plastic filament layer-by-layer onto the build platform. Its a cost-effective and quick method for producing physical models.
-
There are some instances when FDM can be used for functional testing but the technology is limited due to parts having relatively rough surface finishes and lacking strength.
-
FDM works using a plastic filament which is unwound from a spool and is supplied to an extrusion nozzle which can turn the flow on and off.
-
The nozzle is heated to melt the material and can be moved in both horizontal and vertical directions by a numerically controlled mechanism.
-
The object is produced by extruding melted material to form layers as the material hardens immediately after extrusion from the nozzle. When the
layer is finished, the printer sets out another layer, until the item is complete.
-
FDM was invented by Scott Crump in the late 80s. After patenting this technology, he started the company Stratasys in 1988. The term Fused Deposition Modelling and its abbreviation to FDM are trademarked by Stratasys Inc.
-
APPLICATIONS: Basic applications for FDM incorporate electrical lodgings, structure and fit testing, jigs and fixtures, and investment casting patterns.
-
ADVANTAGE: The best part about FDM is that it offers the best surface completion in addition to full tone alongside the reality there are different materials accessible for its utilization.
-
DISADVANTAGE: It is limited by being brittle, therefore unsuitable for mechanical parts. It also has a higher cost than SLA/DLP.
Types of FDM 3D printers include
-
Cartesian: uses the Cartesian axis X-Y-Z, with three axes perpendicular to each other. Its main benefit lies in its ease of use, and being the type of printer with the simplest mechanics, they are the easiest to calibrate and for correcting errors that may arise during use.
-
Delta: Delta robots have a static circular printing bed. Their 3 articulated arms in different heights move up and down to get the job done. Their printing quality, higher speed, precision and no backlash reaction as their straps dont stop tightening stand out.
-
Polyjet
-
-
PolyJet is another plastic 3D printing process, but theres a twist. It can fabricate parts with multiple properties such as colours and materials.
-
Designers can leverage the technology for prototyping elastomeric or over moulded parts.
-
APPLICATIONS: High-resolution, high- accuracy prototypes can be created with Polyjet or Multijet Modeling.
-
ADVANTAGES: Very high accuracy and resolution; Very smooth surface; fine layer lines can be easily removed; Can combine different materials
-
DISADVANTAGES: Support material creates alterations in surface quality (no support: glossy, smooth; with support: dull, rougher); Relatively high cost compared to other 3D printing technologies; In Polyjet, sharp edges are often slightly rounded
-
Powder bed fusion (PBF)
-
Selective Laser Sintering (SLS)
-
-
SLS uses a high-power laser to fuse small particles of powder into a mass that has the desired three- dimensional shape. The laser selectively fuses powder by first scanning the cross- sections (or layers) on the surface of a powder bed. After each cross- section is scanned, the powder bed is lowered by one- layer thickness. Then a new layer of material is applied on top and the process is repeated until the object is completed.
-
SLS softens together nylon-based powders into strong plastic. Since SLS parts are produced using genuine thermoplastic material, they are tough, reasonable for utilitarian testing, and can uphold living pivots and snap-fits. In contrast with SL, parts are more grounded, yet have harsher surface completions.
-
SLS doesnt need help structures so the entire form stage can be used to settle various parts into a solitary formmaking it appropriate for part amounts higher than other 3D printing measures.
-
Numerous SLS parts are utilized to model plans that will one day be infusion-shaped.
-
It utilizes a 3D printing measure called Power Bed Fusion. A container of thermoplastic powder (Nylon 6, Nylon 11, Nylon 12) is warmed simply beneath its liquefying point. At that point, a recoating
or wiper sharp edge stores a meagre layer of the powder generally 0.1 mm thick onto the forming stage.
-
A laser bar starts examining the surface, where it specifically sinters the powder, which means it hardens a cross-part of the article.
-
When the whole cross-segment is filtered, the stage drops somewhere near one thickness of layer stature and the entire cycle is rehashed until the item is completely made. Powder that isnt sintered remaining parts set up supporting the item that has been sintered, dispensing with the requirement to support structures.
-
Not many of the applications for SLS are the assembling of practical parts, complex ducting requiring empty plans, and low-run creation. Its qualities are in the production of utilitarian parts, which leaves behind great mechanical properties, and with complex calculations.
-
APPLICATIONS: Rapid Manufacturing in Aerospace Hardware, Medical and Healthcare, Electronics; Packaging, Connectors, Homeland Security, Military Hardware; Rapid Prototypes in Functional Proof of Concept Prototypes, Design Evaluation Models (Form, Fit & Function), Product
Performance & Testing, Engineering Design Verification, Wind-Tunnel Test Models; Tooling and Patterns in Rapid Tooling (concept development & bridge tools), Injection Mold Inserts, Tooling and Manufacturing Estimating Visual Aid, Investment Casting Patterns, Jigs and Fixtures, Foundry Patterns – Sand Casting
-
ADVANTAGE: Batch printing is easy; no need for supports; extremely detailed prints; best for experimental use; very fast 3d printing; high dimensional accuracy; the cost of printing is comparatively low.
-
DISADVANTAGE: SLS is restricted by requiring longer lead times and its greater expense;
-
variety in the raw material is limited; material recycling is not possible; brittle in nature; potential health hazards; post-processing procedures are difficult.
-
Multi Jet Fusion (MJF)
-
-
Multi Jet Fusion technology was developed by Hewlett Packard and works with a sweeping arm which deposits a layer of powder and then another arm equipped with inkjets which selectively applies a binder agent over the material. The inkjets also deposit a detailing agent around the binder to ensure precise dimensionality and smooth surfaces. Finally, the layer is exposed to a burst of thermal energy that causes the agents to react.
-
Multi Jet Fusion assembles utilitarian parts from nylon powder.
-
As opposed to utilizing a laser to sinter the powder, MJF utilizes an inkjet cluster to apply melding specialists to the bed of nylon powder. At that point, a warming component disregards the bed to
combine each layer. This outcome in more predictable mechanical properties contrasted with SLS just as improved surface completion.
-
MJ differs from other types of 3D printing technologies that deposit, sinter, or cure build material with point-wise deposition. Instead, the print head jets hundreds of droplets of photopolymer and cures/solidifies them using UV light.
-
Once a layer is deposited and cured, the build platform lowers by one-layer thickness, and the process is repeated until the 3D object is built.
-
Another difference from 3D printing technologies is instead of using a single point to follow a path that outlines the cross-sectional layer, MJ machines deposit build material in a fast, line-wise manner.
-
Articles made with MJ need help during printing and are printed all the while during the form cycle with a dissolvable material that is taken out in post-handling. MJ is one of the solitary sorts of 3D printing innovation that can make objects produced using numerous materials and with full tone.
-
APPLICATIONS: Vehicles electronic system housings, guides, grommets, clips, connectors & covers; vessels for fuel, oil housings and washer fluid; environmental control system components like fan housings, plenums, ducting, valves, diverters and vents
-
ADVANTAGES: High production speed; strength of large mother company; high process/post process automation
-
DISADVANTAGES: Lack of clear information on ceramics am specifications; high performance polymer currently prioritized; no ceramic materials available commercially yet
-
Direct Metal Laser Sintering (DMLS)
-
-
DMLS is basically the same as SLS, but uses metal powder instead. All unused powder remains as it is and becomes a support structure for the object. Unused powder can be re-used for the next print.
-
Due to of increased laser power, DMLS has evolved into a laser melting process.
-
Here, a heat source is utilized to fuse metal particles one layer at a time.
-
Typical materials used are metal powder, aluminium, stainless steel, and titanium. DMLS is used for producing parts from metal alloys. Instead of melting it, DMLS heats the metal powder with a laser to the point where it fuses together on a molecular level. Its often
used to reduce metal, multi-part assemblies into a single component or lightweight parts with internal channels or hollowed out features.
-
DMLS is viable for both prototyping and production since parts are as dense as those produced with traditional metal manufacturing methods like machining or casting.
-
Creating metal components with complex geometries also makes it suitable for medical
applications where a part design must mimic an organic structure.
-
APPLICATIONS: Widely used by the automotive and aerospace industries for high performance parts. Other applications include medical prosthetics, tooling, functional prototypes and many more.
-
ADVANTAGES: Great for producing unique shapes and designs with stable mechanical and material properties. There is relatively wide material availability and the machines are repeatable once a part is printed successfully.
-
DISADVANTAGES: While effective, DMLS machines are notoriously difficult to purchase and operate. They require skilled operators, supporting machines (like EDM machines), and powder managements. Because the process his so high-energy, machines often require a process of trial and error before producing accurate and functional parts.
b. Electron Beam Melting (EBM)
-
It uses an electron beam that's controlled by electromagnetic coils to melt the metal powder.
-
The printing bed is heated up and in vacuum conditions during the build. The temperature that the material is heated to is determined by the material in use.
-
A focused beam of electrons scans over a thin layer of powder, causing localized melting and solidifying over a particular cross-sectional area. The areas are then built up to create a solid object. Because of its higher energy density, EBM has a much better build speed than DMLS or SLM. Minimum feature size, powder particle size, layer thickness, and surface finish are generally larger with EBM. Also, because of the nature of the process, EBM parts must be made in a vacuum and can only be used with electrically conductive materials.
-
APPLICATIONS:
-
EBM process is used to remove small broken taps from holes.
-
It is also used for making fine gas orifices in space nuclear reactors.
-
Used for making turbine blades for supersonic aero engines.
-
It is also used to manufacture field emission cathodes, integrated circuits, and computer memories.
-
Used for making drawing dies and flow orifices.
-
Used for frilling synthetic jewels in the watch industry.
-
Used for micro-machining of thin materials. drilling, perforating, slotting and scribing are some of the micro-machining operations that can be done using ultrasonic machining.
-
Used for welding small pieces of highly reactive and refractory metals.
-
Common applications for these last three 3D printing technologies are functional metal parts for the aerospace, automotive, medical and dental industries.
-
-
ADVANTAGES:
-
This process provides very high drilling rates when small holes with large ratios are to be drilled.
-
It can be used to machine almost any material irrespective of their mechanical properties.
-
The heat-affected zone is very less in this process due to shorter pulses.
-
As in this process, no mechanical cutting force applies therefore holding and fixing cost is very less.
-
This process can be used to create holes of any shape with high accuracy by combining it with the CNC table.
-
This process can be automated easily.
-
Strengths are the fabrication of the strongest functional metal parts and the ability to produce complex geometries.
-
-
DISADVANTAGE S:
-
The primary limitations are the high capital cost of the equipment.
-
It requires regular maintenance of the equipment using a vacuum system.
-
Recast layer formation takes place in this process.
-
Many non-productive pumps are used for attaining the desired vacuum.
-
If not properly handled the bottom of through hole would become cone-shaped.
-
The power consumption of this process is very high.
-
The material removal rate of this process is very low.
-
Skilled operators are required to operate this machine.
-
Material jetting
-
-
In this process, material is applied in droplets through a small diameter nozzle, similar to the way a common inkjet paper printer works, but it is applied layer-by-layer to a build platform and then hardened by UV light.
-
It uses photopolymer resin (Standard, Castable, Transparent, High Temperature) and works in a way similar to the common inkjet printer. The difference is, instead of printing a single layer of ink, multiple layers are built upon one another, creating a solid object.
-
MJ differs from other types of 3D printing technologies that deposit, sinter, or cure build material with point-wise deposition. Instead, the print head jets hundreds of droplets of photopolymer and
cures/solidifies them using UV light. Once a layer is deposited and cured, the build platform lowers by one- layer thickness and the process is repeated until the 3D object is built.
-
Another difference from 3D printing technologies is instead of using a single point to follow a path which outlines the cross-ectional layer, MJ machines deposit build material in a fast, line-wise manner.
-
The advantage to this is MJ printers can fabricate multiple objects in a single line without affecting build speed. As long as the models are arranged correctly with optimal spacing, MJ can produce parts faster than other types of 3D printer.
-
Objects made with MJ require support during printing and are printed simultaneously during the build process with a dissolvable material that is removed in post-processing. MJ is one of the only kinds of 3D printing technology that can create objects made from multiple materials and with full colour.
-
APPLICATIONS: PolyJet, Nano Particle Jetting (NPJ), DOD Drop on demand
-
ADVANTAGES:
-
Highly accurate parts with resolution down to 14 microns
-
Due to high accurate layer resolution, it can produce smooth parts with surfaces comparable to injection moulding and very high dimensional accuracy
-
Low wastage due to accurate jetting and material on-demand dropping technology unlike processes like powder bed fusion where sintering takes place inside the power chamber
-
Multi-material and multi-colour capability within the same print volume
-
Material Jetting has homogeneous mechanical and thermal properties
-
-
DISADVANTAGES:
-
Material jetted parts are mainly suitable for non-functional prototypes, as they have poor mechanical properties NPJ and DOD produces better parts than PolyJet in terms of mechanical properties
-
Mechanical properties of photosensitive material used in PolyJet, degrade over time quickly
-
Compared to some other AM technologies, MJ machines are still expensive making it not feasible for some applications
-
Produces relatively brittle parts making it difficult to use in a production load-bearing part
-
Although its easier to remove, most of the parts often require support material
-
High accuracy can be achieved but materials are limited and only polymers and waxes can be used with PolyJet
a. DROP ON DEMAND (DOD)
-
-
It uses a pair of inkjets. One deposits the wax- like build material, the second deposits the dissolvable support material. Like other typical kinds of 3D printing technology, a DOD printer follows a predetermined path for jetting material in a point-wise deposition, creating the cross-sectional area of an object layer by layer.
-
DOD printers also use something called a fly- cutter which skims the build area after each layer is created, ensuring a perfectly flat surface before starting the next layer.
-
Common applications for MJ and DOD are full-colour product prototypes, prototypes similar to injection moulding, low-run injection moulds, and medical models.
-
Strengths are its surface finish, ability to use multiple materials and full colour. Limitations include brittleness making it unsuitable for mechanical parts and a higher cost than SLA/DLP.
-
APPLICATIONS: Areas of application for these processes include high-resolution marking such as direct marking of plastic profiles and steel pipes or of building material products and metal components.
-
ADVANTAGES: Low cost; Large character printing; High printing quality; High quality printing
on sensitive and uneven surfaces; Compatibility with special inks
-
DISADVANTAGES: They include a limited ink variety, as thermally sensitive materials cannot be processed and a lower durability of the print heads.
-
Binder jetting
-
-
With binder jetting two materials are used: (1) powder base material
(2) a liquid binder. In the build chamber, powder is spread in equal layers and binder is applied through jet nozzles that glue the powder particles in the required shape.
-
After the print is finished, the remaining powder is cleaned off which often can be re-used printing the next object.
-
This technology was first developed at the Massachusetts Institute of Technology in 1993.
-
APPLICATIONS: Casting patterns: Cores and molds: Aerospace parts: Prototypes: Full color decorative objects: Jewellery.
-
ADVANTAGES:
-
Parts can be made in a range of different colours
-
Uses a range of materials: metal, polymers and ceramics
-
The process is generally faster than others
-
The two-material method allows for many different binder-powder combinations and various mechanical properties.
-
-
DISADVANTAGES:
-
Not always suitable for structural parts, due to the use of binder material
-
Additional post-processing can add significant time to the overall process.
-
SAND BINDER JETTING
-
-
The process is similar to SLS as it requires an initial layer of powder, in this case, sand or silica, on the build platform. It differs from SLS, in that instead of using a laser to sinter powder, a print head moves over the surface depositing droplets of binder which bind the powder together, producing each layer of the object.
-
Once a layer is printed, the build platform is lowered and a new layer of powder is spread over the just printed layer. The process is repeated until the object is completed.
-
For full-colour models, objects are made using a plaster-based or acrylic powder along with a liquid binding agent. The printhead first jets the binding agent while the second printhead jets the colour, allowing for full-colour model printing.
-
After the parts are fully cured, they are taken out of the loose unbonded powder and cleaned.
-
An infiltrant (a fast-curing resin for strengthening 3D printed models) is often introduced to enhance mechanical properties. Coatings can also be added to enhance colours.
-
It is a low-cost technology for producing parts and sand cast moulds and cores. After printing, the cores and moulds are removed from the build area and cleaned, removing any loose sand. They are then ready for immediate casting. After casting, the mould is broken apart and the final metal component is removed.
-
METAL BINDER JETTING
-
-
It uses Binder Jetting for the fabrication of metal objects. The metal powder is bound using a polymer binding agent. It allows the production of objects with complex geometries that are far beyond the capabilities of conventional manufacturing techniques.
-
Functional metal objects do require a secondary process like infiltration or sintering, without which the part would have poor mechanical properties.
-
With infiltration, the metal powder is bound by a binding agent. Once cured, the object is placed in a furnace, where the binder is burned out. This leaves the object at about 60% density, with voids left throughout by the burned-out binder.
-
Bronze is then added by capillary action to infiltrate the voids, which results in an object of about 90% density and much greater strength. It should be noted objects made by Metal Binder Jetting typically have lower mechanical properties than those made with Powder Bed Fusion.
-
APPLICATIONS: Common applications for Sand and Metal Binder Jetting are sand casting, functional metal parts, and full-colour models.
-
ADVANTAGES:
-
Economical process for a very wide range of part quantities
-
No printing supports
-
Good surface condition
-
Dimensional precision and quality
-
Many eligible materials
-
Homogenity of the microstructure
-
-
DISADVANTAGES:
-
Many materials still to be developed
-
A limitation is mechanical properties are not as good as with metal powder bed fusion.
-
Direct energy depositon
-
-
This process is mostly used in the metal industry and in rapid manufacturing applications. The 3D printing apparatus is usually attached to a multi-
axis robotic arm and consists of a nozzle that deposits metal powder or wire on a surface and an energy source (laser, electron beam or plasma arc) that melts it, forming a solid object.
-
APPLICATIONS: DED is already utilised in key industries like aerospace, defence, oil & gas, as well as the marine industry, for example, aircraft frames and structures, refractory metal components, ballistic material tooling repair and reconditioning and marine propulsion, etc.
-
ADVANTAGES: High build rates; dense and strong parts; near net shape; can be used for repairing; multi-material range; larger parts; easy material change; reduced material waste
-
DISADVANTAGES: High capital cost; low build resolution; no support structures
-
Sheet lamination
-
-
Sheet lamination involves material in sheets which is bound together with external force. Sheets can be metal, paper or a form of polymer.
-
Metal sheets are welded together by ultrasonic welding in layers and then CNC milled into a proper shape.
-
Paper sheets can be used also, but they are glued by adhesive glue and cut in shape by precise blades.
-
APPLICATION: Paper-based techniques such as LOM and SDL are used for full-colour prints while metal-based sheet lamination is used in hybrid manufacturing. SLCOM can be used to make production quality composite fibre parts while the CAM-LEM process can be used to make ceramic parts.
-
ADVANTAGES:
-
Faster print time, but post-processing will be required
-
Ability to integrate as hybrid manufacturing systems
-
Ease of material handling
-
Ceramic (CAM-LEM) and composite fibre (SLCOM) parts can be manufactured
-
OEM components, such as sensors, wires, etc., can be embedded into the part during the layering stage. Highly depends on the sheet lamination technique and material used
-
Relatively low cost as it uses standard material
-
No support structures are necessary
-
Larger working area than most of the current AM technology equipment
-
Full-colour prints LOM/SDL can print in the whole colour spectrum
-
In some sheet lamination techniques, the material state does not change during or after the process
-
Multi-material layers possible (UAM)
-
In some cases, cut material can be easily recycled This could also be a disadvantage if the part is smaller compared to the sheet or the bed size
-
-
DISADVANTAGES:
-
Layer height cannot be changed without changing the sheet thickness hence part resolution is linked to sheet thickness along the vertical build axis
-
Finishes can vary depending on paper or plastic material but may require post-processing to achieve the desired effect
-
Limited material options available
-
It can be time-consuming and difficult to remove the excess material after the laminating phase and it generates a lot of waste compared to other AM methods
-
Hollow parts (internal voids and cavities) are difficult to produce in some types of sheet lamination processes, such as bond then form
-
Bonding strength will depend on the laminating technique used and, in some cases, adhesive bonds are not good enough for long term use of the product strength and integrity
-
Material waste can also be high if the part being made is smaller than the build area or the sheet size
A few more types of 3d printing process include:
-
Computed axial lithography
-
-
-
Computed axial lithography is a method for 3D printing based on reversing the principle of computed tomography (CT) to create prints in photo- curable resin.
It was developed by a collaboration between the University of California, Berkeley with Lawrence Livermore National Laboratory.
-
Unlike other methods of 3D printing it does not build models through depositing layers of material like fused deposition modelling and stereolithography, instead it creates objects using a series of 2D images projected onto a cylinder of resin. It is notable for its ability to build objects much more quickly than other methods using resins and the ability to embed objects within the prints.
-
APPLICATIONS: This technique can be used to expand the range of printable geometries in additive manufacturing and relax constraints on factors such as overhangs in topology optimization.
-
ADVANTAGES: The advantage of this system design is that the optics can be rotated at a
much higher speed than the volume. This arises from the constraint of fluid motion in the resin volume at higher rotation speeds. The only constraints on the speed with which the optics can be rotated are motor rotation speed limits and the minimum frame rate of the optical system.
-
Liquid additive manufacturing
-
-
Liquid additive manufacturing (LAM) is an additive manufacturing technique which deposits a liquid or highly viscous material (e.g. Liquid Silicone
Rubber) onto a build surface to create an object, which is then vulcanised using heat to harden it.
-
The process was originally created by Adrian Bowyer and was then built upon by German RepRap.
-
APPLICATIONS: The range of applications extends from the automotive industry to medical technology. Seals are particularly interesting
application, as they are used in many different industries.
-
ADVANTAGES: Heat forces the silicone rubber to change on a molecular level. The end result is a stronger and more resilient object. Liquid additive manufacturing also supports the construction of objects in small sizes and complex shapes.
-
Directed Energy Deposition (DED)
-
Powder-fed directed-energy deposition
-
-
-
In powder-fed directed-energy deposition, a high-power laser is used to melt metal powder supplied to the focus of the laser beam. The laser beam typically travels through the centre of the deposition head and is focused to a small spot by one or more lenses. The build occurs on an X-Y table which is driven by a tool path created from a digital model to fabricate an object layer by layer. The deposition head is moved up vertically as each layer is completed.
-
Metal powder is delivered and distributed around the circumference of the head or can be split by
an internal manifold and delivered through nozzles arranged in various configurations around the deposition head. A hermetically sealed chamber filled with inert gas or a local inert shroud gas is often used to shield the melt pool from atmospheric oxygen for better control of material properties. The powder fed directed energy process is similar to Selective Laser Sintering, but the metal powder is applied only where material is being added to the part at that moment.
-
The process supports a wide range of materials including titanium, stainless steel, aluminium, and other
specialty materials as well as composites and functionally graded material. The process can not only fully build new metal parts but can also add material to existing parts for example for coatings, repair, and hybrid manufacturing applications.
-
LENS (Laser Engineered Net Shaping), which was developed by Sandia National Labs, is one example of the Powder Fed – Directed Energy Deposition process for 3D printing or restoring metal parts.
-
In selective powder deposition, build and support powders are selectively deposited into a crucible, such that the build powder takes the shape of the desired object and support powder fills the rest of the volume in the crcible.
-
Then an infill material is applied, such that it comes in contact with the build powder.
-
Then the crucible is fired up in a kiln at the temperature above the melting point of the infill, but below the melting points of the powders.
-
When the infill melts, it soaks the build powder.
-
But it doesn't soak the support powder, because the support powder is chosen to be such that it is not wettable by the infill. If at the firing temperature, the atoms of the infill material and the build powder are mutually diffusible, such as in case of copper powder and bronze infill, to prevent shape distortion, the firing temperature must be below the solidus temperature of the resulting mixture(alloy)
Industry use
PRINTERS
-
Metal wire processes
-
-
Laser-based wire-feed systems, such as Laser Metal Deposition-wire (LMD-w), feed wire through a nozzle that is melted by a laser using inert gas shielding in either an open environment (gas surrounding the laser), or in a sealed chamber.
-
Electron beam freeform fabrication uses an electron beam heat source inside a vacuum chamber.
-
It is also possible to use conventional gas metal arc welding attached to a 3D stage to 3-D print metals such as steel and aluminium.
-
Low-cost open source RepRap-style 3-D printers have been outfitted with Arduino-based sensors and demonstrated reasonable metallurgical properties from conventional welding wire as feedstock.
-
Selective Power Distribution (SPD)
-
-
As of October 2012, additive manufacturing systems were on the market that ranged from $2,000 to
$500,000 in price and were employed in industries including aerospace, architecture, automotive, defence, and medical replacements, among many others. As of 2018, 3-D printers have dropped in cost to as little
$100 and low-cost higher quality desktop printers are approximately $2500. These types of devices are used widely in industry for prototyping, jig making, fixturing, fixing small custom components, and even additive manufacturing of actual products.
-
In addition, higher end 3-D printers have now become relatively common for production and additive manufacturing.
-
For example, General Electric uses the high- end model to build parts for turbines. Many of these systems are used for rapid prototyping, before mass production methods are employed. Volkswagen uses 3D printers on their assembly lines to print tooling, jigs and fixtures. They estimate that 3D printers save 250,000 EURO per year in costs. One report estimates that almost 75% of desktop 3D printers made are used in industry and not by consumers.
-
Military and defence are also incorporating the use of 3D printers. The Royal Netherlands Air Force is using desktop 3D printers at their Woensdrecht Air Force Base to make fixtures and alignment tools. In the United States, the Hill Air Force base is using 3D printed parts in repair of fighter jets.
-
Higher education has proven to be a major buyer of desktop and professional 3D printers. Significant desktop 3D printer purchases by both K-12 and universities helped sustain a desktop 3D printer market that had problems in 2015-2016.
-
As higher education is the home to research, 3D printing is being used to fabricate equipment to further research and hold down costs.
-
For example, chemists can 3D print flow reactor systems that would otherwise be too costly to purchase. The UCL School of Pharmacy in the UK created a modular flow reactor system for chemical synthesis that can easily be 3D printed in laboratories around the world at low cost.
-
Libraries around the world have also become locations to house smaller 3D printers for educational and community access.
Consumer use
-
Several projects and companies are making efforts to develop affordable 3D printers for home desktop use. Much of this work has been driven by and targeted at DIY/Maker/enthusiast/early adopter communities, with additional ties to the academic and hacker communities.
-
RepRap Project is one of the longest running projects in the desktop category. The RepRap project aims to produce a free and open source hardware (FOSH) 3D printer, whose full specifications are released under the GNU General Public License,
which is capable of replicating itself by printing many of its own (plastic) parts to create more machines. RepRaps have already been shown to be able to print circuit boards and metal parts. The most popular 3D printer in the world is the Prusa i3, a RepRap printer.
(Prusa i3)
-
Because of the FOSH aims of RepRap, many related projects have used their design for inspiration, creating an ecosystem of related or derivative 3D printers, most of which are also open-source designs.
-
The availability of these open-source designs means that variants of 3D printers are easy to invent.
-
The quality and complexity of printer designs, however, as well as the quality of kit or finished products, varies greatly from project to project. This rapid development of open source 3D printers is gaining interest in many spheres as it enables hyper- customization and the use
-
of public domain designs to fabricate open source appropriate technology. This technology can also assist initiatives in sustainable development since technologies are easily and economically made from resources available to local communities.
-
The cost of 3D printers has decreased dramatically since about 2010, with machines that used to cost $20,000 now costing less than $1,000. For instance, as of 2013, several companies and individuals are selling parts to build various RepRap designs, with prices starting at about 400 / US$500.
-
The open source Fab@Home project has developed printers for general use with anything that can be squirted through a nozzle, from chocolate to silicone sealant and chemical reactants.
(Fab@Home)
-
Printers following the project's designs have been available from suppliers in kits or in pre- assembled form since 2012 at prices in the US$2000 range. Several new 3D printers are aimed at thesmall, inexpensivemarketincludingthemUVe3Dand Lumifold. Rapide 3D hasdesigned a professional grade crowdsourced 3D-printer costing $1499 which has no fumes nor constant rattle during use.
-
The 3Doodler, "3D printing pen", raised $2.3 million on Kickstarter with the pens selling at
-
$99, though the 3D Doodler has been criticized for being more of a crafting pen than a 3D printer.
-
As the costs of 3D printers have come down, they are becoming more appealing financially to use for self-manufacturing of personal products. In addition, 3D printing products at home may reduce the environmental impacts of manufacturing by reducing material use and distribution impacts.
-
In addition, several RecycleBots such as the commercialized Filastruder have been designed and fabricated to convert waste plastic, such as shampoo containers and milk jugs, into inexpensive RepRap filament.
(RecycleBots-Reprap)
-
There is some evidence that using this approach of distributed recycling is better for the environment.
-
The development and hyper-customization of the RepRap-based 3D printers has produced a new category of printers suitable for small business and consumer use.
-
Manufacturers such as Solidoodle, Robo3D, RepRap Pro and have introduced models and kits priced at less than $1,000, thousands less than they were in September 2012. Depending on the application, the print resolution and speed of manufacturing lies somewhere between a personal printer and an industrial printer.
-
A list of printers with pricing and other information is maintained. Most recently, delta robots, lie the TripodMaker, have been utilized for 3D printing to increase fabrication speed further. For delta 3D printers, due to its geometry and differentiation movements, the accuracy of the print depends on the position of the printer head.
-
Some companies are also offering software for 3D printing, as a support for hardware manufactured by other companies.
Large 3D printers
-
Large 3D printers have been developed for industrial, education, and demonstrative uses. A large delta-style 3D printer was built in 2014 by SeeMeCNC.
-
The printer is capable of making an object with diameter of up to 4 feet (1.2 m) and up to 10 feet (3.0 m) in height.
-
It also uses plastic pellets as the raw material instead of the typical plastic filaments used in other 3D printers.
-
Another type of large printer is Big Area Additive Manufacturing (BAAM).
-
The goal is to develop printers that can produce a large object in high speed.
-
A BAAM machine of Cincinnati Incorporated can produce an object at the speeds 200-500 times faster than typical 3D printers available in 2014.
-
Another BAAM machine is being developed by Lockheed Martin with an aim to print long objects of up to 100 feet (30 m) to be used in aerospace industries.
Microscale and nanoscale 3D printing
-
Microelectronic device fabrication methods can be employed to perform the 3D printing of nanoscale- size objects. Such printed objects are typically grown on a solid substrate, e.g. silicon wafer, to which they adhere after printing as they are too small and fragile to be manipulated post- construction.
-
In one technique, 3D nanostructures can be printed by physically moving a dynamic stencil mask during the material deposition process, somewhat analogous to the extrusion method of traditional 3D printers. Programmable- height nanostructures with resolutions as small as
10 nm have been produced in this fashion, by metallic physical vapor deposition Mechanical piezo- actuator controlled stencil mask having nanopore in a silicon nitride membrane.
-
Another method enhances the photopolymerization process on a much smaller scale, using finely-focused lasers controlled by adjustable mirrors. This method has produced objects with feature resolutions of 100 nm.
-
Micron wide, millimetre long copper wires have also been printed using lasers.
CONCLUSION
Along with modelling and three-dimensional scanning, 3D printing is a tool for creativity, but what sets it apart most is its ability to produce an almost infinite variety of shapes. Like every tool, it must be mastered in order to be used to its full potential. However, we must also be aware of its limitations. The ideal production solution is not always prototyping. Casting, machining, and blowing are three examples of centuries-old industrial processes that will continue to be used for a very long time. The complete control of production is the actual revolution that these digital manufacturing and design tools give. Inevitably, local, small-scale manufacturing will employ 3D printers as they become more economical, largely eliminating supply chains for many different product kinds. Even consumer units for home use will be possible, enabling customers to easily download and print the product designs they need.
The conventional manufacturing sector will face significant difficulties in adapting to these developments. However, the opportunities for science and engineering are unquestionably enormous, and the creative options for product design and the creation of printing materials are virtually limitless.
FUTURE REFERENCE
The use of 3D printing has the potential to completely change society. Customized and made-to-order consumer goods will be available, and 3D printing will allow producers to create entirely new designs for everyday objects. But when will we have houses that can be 3D printed, made-to-measure replacement bones, and embedded electronics? Here are some of the most accurate forecasts into an interactive timeline that explores what the future of 3D printing might entail:
-
10years: Production will take a turn towards the local with personalized medicines and integrated electronics
Rare Parts Replacement and Automotive Prototyping will be common along with lowered production costs. Manufacturers will be able to completely rethink the design of products, thanks to the printing of devices with embedded electrical circuits. A Chinese company by the name of Winsun offers 3D houses that are produced for less than $5000 and are made entirely of recyclable materials. They use "ink" created from recycled debris, cement, steel, fibreglass, and binder. They have already constructed housing in China, just expanded to Saudi Arabia, and over the next five years, they intend to extend to twenty more nations. Building contractors can save money on labour, building supplies, and transportation by using 3D printing. Another application will be to create a customised prescription with a certain dose. Advanced 3D printers that can combine metal and plastic will be as widespread in homes as microwaves, and they will also be installed in warships and aeroplane hangars. Additionally, by its very nature, 3D printing produces less waste than conventional manufacturing hence 3D printing could save the environment.
-
15years: Medical microfactories and scaffolds for tissue engineering
The medical world will be turned upside-down, from surgery to prosthetics to medications, 3D printing has the power to revolutionize the world of medicine. Scientists will be able to create scaffolds that are tailored to fit particular areas of a broken bone, offering a framework to support the body's natural healing process. The field of "bioprinting," or 3D printing with "ink" made of human cells and tissue, is
rapidly progressing. By 2025, several tech and medical experts anticipate that 3D-printed internal organs would be used in surgery.
Hospitals would be able to manufacture on-site, personalised medical items like dental aligners, medical guides or surgical instruments, and replacement organs thanks to medical microfactories.
-
Within 20years: Digital fabrication on a large scale
A crossbeam that holds a printing head over a construction site might be supported by two crane-like arms. Then, employing jets of concrete, the gadget could print a building layer by layer. According to researchers, the technique could construct a two-story house in less than a day.
3D printers might be used to make parts on the moon and in space, even printing astronaut housing.
-
Decades into future: 3D Printing will Spark a Creative Renaissance- "Internet of Things"
Devices with tiny batteries and sensors integrated in might be made possible by 3D printing. Engineers will be able to build an internet of things where common objects can detect their surroundings and interact with one another once this can be done affordably.
-
Far future: Digital fabrication on a nanoscale
Another advantage of the MJF cycle is the quickened fabricate time, which prompts lower creation costs and MJ printers can fabricate multiple objects in a single line without affecting build speed.
By utilising carbon atoms to create a lightweight material that is harder than diamond, 3D printers may one day be able to build materials atom by atom. High- power fuel cells, single-molecule sensors, molecular- scale computer circuits, and selectively permeable membranes might all be created using the technology.
REFERENCES
[1] A Review paper on 3D-Printing Aspects and Various Processes Used in the 3D-Printing by Vinod G. Gokhare, Dr. D. N. Raut and Dr. D. K. Shinde [2] An Overview on 3D Printing Technology: Technological, Materials, and Applications by N. Shahrubudin, T.C. Lee and R.Ramlana
[3] A review of 3D printing processes and materials for soft robotics Yee Ling Yap, Swee Leong Sing and Wai Yee Yeong [4] Dongkeon Lee, Takashi Miyoshi, Yasuhiro Takaya and Taeho Ha, 3D Micro fabricaton of [5] Photosensitive Resin Reinforced with Ceramic Nanoparticles Using LCD Microstreolithography, Journal of Laser Micro/Nano engineering Vol.1, No.2, 2006. [6] Ruben Perez Mananes, Jose Rojo-Manaute, Pablo Gil, 3D Surgical printing and pre-contoured plates for acetabular fractures, Journal of ELSEVIER 2016. [7] Alexandru Pirjan, Dana-Mihaela Petrosanu, The Impact of 3D Printing Technology on the society and economy, Journal of Information Systems and Operations Management, Volume 7, Dec 2013. [8] Gabriel Gaala, Melissa Mendesa, Tiago P. de Almeida, Simplified fabrication of integrated microfluidic devices using fuseddeposition modeling 3D printing Science Direct. [9] Pshtiwan Shakor, Jay Sanjayan, Ali Nazari, Shami Nejadi, Modified 3D printed powder to cement- based material andmechanical properties of cement scaffold used in 3D printing, Science Direct.
[10] Siddharth Bhandari, B Regina, 3D Printing and Its Applications, International Journal of Computer Science and Information Technology Research ISSN 2348-120X [11] ISO/PRF 17296-1,"Additive manufacturing — General principles — Part 1: Terminology", 2015. [12] P. Holzmann, J. Robert, A. Aqeel Breitenecker, Soomro, & J. S. Erich, User entrepreneur business models in 3D printing, Journal of Manufacturing Technology Management, Vol. 28, No. 1, pp. 75-94, 2017. [13] Thomas, 3D printed jellyfish robots created to monitor fragile coral reefs, 3D Printer and 3D Printing News, 2018. [Online]. Available: http://www.3ders.org/articles/20181003-3d-printed- jellyfish-robots- created-to-monitor-fragile-coral-reefs.html. [ Accessed 2019]. [14] Tess, Indian jewelry brand Isharya unveils Infinite Petals 3D printer jewelry collection, 3D Printer and 3D Printing News, 2017. [Online]. Available: http://www.3ders.org/articles/20170412-indian- jewelry-brand- isharya-unveils-infinite-petals-3d-printed-kewelry-collection.html. [Accessed 2019]. [15] Thomas, GE Transportation to produce up to 250 3D printed locomotive parts by 2025, 3D Printer and 3D Printing News, 2018-
[Online]. Available: http://www.3ders.org/articles/20180928-ge- transportation-to-produce-up-to-250-3d-printed-locomotive-parts- by-2025.html
[16] Thomas, Paul G. Allen's Stratolaunch space venture uses 3D printing to develop PGA rocket engine., 3D Printer and 3D Printing News. 2018 b, [Online]. Available: http://www.3ders.org/articles/20181001- paul-g-allens- stratolaunch-space-venture-uses-3d-printing-to-developpga-rocket- engine.html. [Accessed 2019].
[17] David, MX3D to install world's first 3D printed steel bridge over Amsterdam canal, 3D Printer and 3D Printing News, 2018. [Online]. Available: https://www.3ders.org/articles/20180403- mx3d-to-install- worlds-first-3d-printed-steel-bridge-over- amsterdam-canal.html. [Accessed 2019].
[18] A. M. T. Syed, P. K. Elias, B. Amit, B. Susmita, O. Lisa, & C. Charitidis, Additive manufacturing: scientific and technological challenges, market uptake and opportunities, Materials today, Vol. 1, pp. 1- 16, 2017.
[19] L. Ze-Xian, T.C. Yen, M. R. Ray, D. Mattia, I.S. Metcalfe, & D.
-
Patterson, Perspective on 3D printing of separation membranes and comparison to related unconventional fabrication techniques, Journal of Membrane Science, Vol 523, No.1, pp. 596-613, 2016.
-
& K. J. Bowman, Effect of build orientation on the mechanical reliability of 3D printed ABS, Rapid Prototyping Journal, Vol. 23, No.2, pp. 320-328, 2017.
[21] W. Yuanbin, Blache, & X. Xun, Selection of additive manufacturing processes, Rapid Prototyping Journal, Vol. 23, No. 2, pp. 434-447, 2017.