
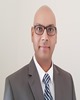
- Open Access
- Authors : Amar Pali
- Paper ID : IJERTV13IS120098
- Volume & Issue : Volume 13, Issue 12 (December 2024)
- Published (First Online): 08-01-2025
- ISSN (Online) : 2278-0181
- Publisher Name : IJERT
- License:
This work is licensed under a Creative Commons Attribution 4.0 International License
Advanced Forecasting and Streamlined MRP for Grocery Success
Abstract
Amar Pali (B.E Nagpur University) SAP Solution Architect Applexus Technologies
Houston, TX United States December 12, 2024
Within the grocery sector, a perpetual hurdle lies in ensuring products meet demand while efficiently managing inventory levels. The ability to accurately predict customer preferences and optimize inventory management can make or break a grocery store's profitability. Traditional forecasting methods, once reliable, now fall short in decoding the intricate consumption patterns specific to the retail grocery sector. The landscape has evolved, revealing a complex interplay of factors like seasonality, promotional events, and ever-shifting consumer preferences demanding a more tailored approach. Todays grocery landscape calls for proactive strategies that not only respond to customer preferences but anticipate them before they surface. It necessitates an inventory management system that doesn't merely adapt to fluctuations but molds them. Think of it as a constantly shifting puzzle where finding the perfect fit is a constant quest. Fundamentally, grocery success hinges on two factors: the accuracy of demand forecasting and the efficacy of Material Requirements Planning (MRP) strategies.
Keywords: MRP, forecasting, retail industry, grocery, seasonal, moving average.
INTRODUCTION
Forecast Model for the Grocery Industry
The grocery industry operates within a dynamic environment influenced by fluctuating consumer demands, seasonal trends, and supply chain variables. Accurate forecasting is vital to ensure efficient inventory management, reduce waste, and meet customer expectations. This document outlines a tailored forecasting model designed specifically for the grocery sector, emphasizing adaptability and precision.
Historical Data Range
A critical factor in developing an effective forecasting model is selecting the appropriate historical data duration. Our analysis suggests that a focus on a range of one week to a month offers the most accurate predictions. This timeframe captures the daily consumption patterns of various grocery products, forming a robust foundation for forecasting. Additionally, incorporating insights from seasonal consumption shiftswhich often occur semi-annually or annuallyenables the model to align with broader market trends and maintain forecast reliability.
To smooth fluctuations and enhance prediction accuracy, we employ a weighted moving average model. This approach accounts for consumption highs and lows, balancing short-term variations with longer-term trends. The resulting forecasts are more reliable, reducing the risk of stock shortages or overstocking.
Customization Capabilities
The forecasting model offers extensive customization options, allowing users to adapt parameters to specific needs. By harmonizing seasonal dynamics and product-specific characteristics, users can achieve highly targeted forecasts. For example:
Adjusting Demand Parameters: When demand for a product like salt increases by 3%, the model can scale the forecast proportionally, such as raising it by 10% to anticipate potential spikes in sales.
Perishable Products: For items like milk that have a limited shelf life, a 5% increase in forecasted demand provides a more suitable adjustment to prevent overstocking or wastage.
These customizations enable daily or weekly refinements, ensuring that forecasts remain responsive to real-time demand fluctuations.
Addressing Supply Chain Challenges
Another significant feature of the model is its ability to address supply chain disruptions. For instance, if inventory shortages hinder the movement of products from distribution centers to stores, consumption data might reflect zero sales. However, this does not accurately represent the underlying demand for those products.
Unlike traditional forecasting systems that rely solely on consumption history, our model integrates supply chain considerations. By factoring in supply shortages alongside consumption data, the model provides a comprehensive view of demand and supply dynamics. This holistic approach ensures that forecasts remain accurate, even in the face of inventory challenges.
Model Parameters
To streamline forecasting processes, the following parameters are implemented:
Forecast Model: Weighted Moving Average (WMA) incorporating two high and two low periods, along with percentage adjustments for outliers.
OUTS: Shortages are explicitly considered in the forecasting model.
Period Indicator: Weekly indicators are used to align with industry practices. History/Consumption Periods: The model analyzes data from the past 13 weeks to establish trends.
Forecast/Future Periods: Predictions are generated for the next 10 weeks to support inventory planning. Forecast Frequency: Updates are made weekly, allowing the model to adapt to changing conditions promptly.
CONCLUSION
This forecasting model is tailored to the unique requirements of the grocery industry, combining robust analytical techniques with high levels of customization. By incorporating both demand and supply-side considerations, it offers a reliable and adaptable solution for managing inventory and meeting consumer needs. The integration of weekly updates and customizable parameters ensures that the model remains responsive to market dynamics, supporting efficient operations and minimizing waste.
MRP Model for the Grocery Industry
Material Requirements Planning (MRP) plays a pivotal role in inventory management, offering strategic guidance to efficiently align supply with demand. Functioning within the broader framework of supply chain management, MRP is instrumental in organizing the flow of materials and ensuring timely product delivery while maintaining cost-effectiveness. Unlike simple inventory management, MRP addresses the complex and ever-changing demands of grocery products, driven by diverse consumer preferences, varying product categories, and dynamic consumption patterns. External factors such as festivals and seasonal shifts further complicate the equation, making it insufficient to rely solely on recent consumption trends.
In the grocery industry, MRP goes beyond merely managing inventory; it involves crafting an initial plan that sets the stage for optimization, followed by continuous fine-tuning to adapt to demand fluctuations. However, the approach to MRP is not one-size- fits-all. It varies significantly depending on the size and scale of the grocery business. For instance, a local retail store in a neighborhood operates under entirely different dynamics compared to a retail giant like Walmart. Each organization requires tailored inventory management strategies, making MRP a nuanced and evolving discipline.
A Comprehensive MRP Model
Our meticulously crafted Material Requirements Planning (MRP) model considers a multitude of factors essential for success. This automated model delves deeply into the intricacies of:
Reorder Points: Determining the optimal inventory levels to trigger replenishment orders.
Safety Stock: Calculating buffer stock to mitigate risks associated with demand variability or supply chain disruptions. MRP Frequency: Establishing regular intervals for updating plans and forecasts.
Integration with Inventory Systems: Seamless integration ensures real-time adjustments based on current demand and supply data.
Such comprehensive planning ensures businesses can optimize inventory levels, efficiently meet customer demands, and minimze costly disruptions. By addressing these variables, the MRP model reduces the risks associated with stockouts or overstocking and supports businesses in maintaining a balanced inventory.
Key Benefits of MRP
At its core, MRP provides businesses with a significant advantage: clarity. It enables organizations to gain precise insights into their inventory requirements, ensuring they meet customer demand with accuracy. Without such clarity, businesses risk accumulating excessive inventory, leading to increased costs and inefficient allocation of financial resources. Conversely, inadequate inventory levels can result in stockouts, eroding customer trust and satisfaction.
Material Requirements Planning (MRP) serves as a strategic asset for navigating the complexities of supply and demand in the volatile grocery industry. It empowers businesses to adapt to fluctuations, streamline operations, and achieve cost efficiency, ultimately fostering resilience in an unpredictable market.
MRP Parameters
The following parameters define the functionality and customization of the MRP model:
Chart Title
500
450
400
350
300
250
200
150
100
50
0
On Hand Stock (OHS)
Available Stock (OHS+OOS)
PO Receipt
New PO
MRP Type: ZV Forecast-Based Planning (VV) ensures forecasts are leveraged to predict future demand accurately. MRP Procedure: Reorder Point Planning facilitates automatic replenishment once inventory reaches predefined levels. Automatic Reorder Point Calculation: Dynamically adjusts reorder points based on consumption patterns and lead times.
Day 0 |
Day 5 |
Day 7 |
Day 10 |
Day 14 |
Day 17 |
Day 21 |
|
On Hand Stock (OHS) |
400 |
300 |
260 |
340 |
260 |
340 |
260 |
Available Stock (OHS+OOS) |
400 |
440 |
400 |
480 |
400 |
480 |
400 |
PO Receipt |
140 |
140 |
|||||
New PO |
140 |
0 |
140 |
0 |
140 |
140 |
Figure 1: Reorder Point Calculation
Automatic Safety Stock Calculation: Calculates optimal safety stock levels to account for demand and supply uncertainties.
CONCLUSION
In the grocery industry, where volatility is the norm, an effective MRP model provides a vital foundation for success. By integrating advanced planning methodologies and customizable parameters, businesses can align supply with demand, minimize risks, and maintain a competitive edge. The adoption of such a model ensures improved inventory management, reduced costs, and enhanced customer satisfactionkey drivers for long-term growth in a demanding marketplace.