
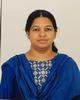
- Open Access
- Authors : Jyothirmayi Narne, Sandhya .V, B.V. S. Rao, Jyothi Jagadish Narisetti, Charan Sai Goli, Sumanth Thipparthi
- Paper ID : IJERTV13IS120117
- Volume & Issue : Volume 13, Issue 12 (December 2024)
- Published (First Online): 04-01-2025
- ISSN (Online) : 2278-0181
- Publisher Name : IJERT
- License:
This work is licensed under a Creative Commons Attribution 4.0 International License
Advances in Multi-Material Layered Composites using 3D Printing: A Comprehensive Review
Jyothirmayi Narne Department of Mechanical Engineering Chaitanya Bharathi Institute of Technology Hyderabad, India
Jyothi Jagadish Narisetti Department of Mechanical Engineering Chaitanya Bharathi Institute of Technology Hyderabad, India
Sandhya .V
Department of Mechanical Engineering Chaitanya Bharathi Institute of Technology Hyderabad, India
Charan Sai Goli
Department of Mechanical Engineering Chaitanya Bharathi Institute of Technology Hyderabad, India
B. V. S. Rao
Department of Mechanical Engineering Chaitanya Bharathi Institute of Technology Hyderabad, India
Sumanth Thipparthi Department of Mechanical Engineering Chaitanya Bharathi Institute of Technology Hyderabad, India
Abstract The Additive Manufacturing (AM) techniques have emerged as revolutionary technologies because of their ability to print complex geometries, rapid prototyping, and facilitate the manufacturing of functional parts. Dual extruder Fused Deposition Modeling (FDM) printing has gained attention for its adaptability in producing multi-material polymer composite structures, such as laminated and panel-based designs. This paper examines current research in dual extruder 3D printing for the fabrication of layered polymer composites. The study begins with a brief literature review, exploring potential applications of laminated polymer composites produced by using dual extruder FDM printing. It examines essential three- dimensional printing (3DP) conditions, optimal 3DP parameters, and assesses the resulting mechanical and functional properties of the printed composites. Furthermore, the assessment highlights deficiencies in existing studies such as the necessity for enhanced interfacial bonding, limited material compatibility and the establishment of standardized testing protocols for laminated composite structures. This study provides an overview of relevant developments and challenges in the field of multi-material 3D printing technology, offering significant insight for the researchers.
Keywords 3D Printing, Additive Manufacturing (AM), Dual extruder Fused Deposition Modeling, Laminated Polymer Composites, Multi-Material Integration, Standardized Testing Protocols
- INTRODUCTIONAdditive manufacturing (AM) which is also known as 3D printing (3DP) signifies a revolutionary advancement in manufacturing methods by facilitating the fabrication of complex geometries quickly and accurately. In contrast to subtractive manufacturing, additive manufacturing reduces material waste making it a basically sustainable method. As defined by ASTM International, additive manufacturing (AM) includes various processes such as vat photopolymerization (VPP), extrusion-based AMFused Deposition Modelling (FDM) or Fused Filament Fabrication (FFF), powder bed fusion (PBF), directed energy deposition (DED), material jetting (MJ), selective laser sintering (SLS), and binder jetting (BJ). These various techniques facilitate the production of customized components for specific purposes across industries including aerospace, automotive, healthcare, construction industry and consumer goods.
Fused Deposition Modeling (FDM) is a widely used additive manufacturing technique that mainly works by extruding thermoplastic filaments heated to a molten or semi- molten state through a nozzle. The material is deposited in layers according to the instructions obtained from a digital design file, such as a standard tessellation language (.stl) file. FDM was introduced in the 1980s and evolved significantly in the 1990s achieving commercial success. Subsequent decades saw technological advancements that widened its application from rapid prototyping to industrial-scale manufacturing of end-use products. This technology is especially advantageous because of its simplicity, cost- effectiveness, and compatibility with many materials, such as polymers, composites, and multi-material systems.
The capacity of FDM to process materials with low melting points such as polymers and polymer-based composites has facilitated its extensive use in various industries. Layered composite structures made by multi materials offer benefits such as reduced weight, improved mechanical and thermal properties and other unique advantages.
Conventional techniques for producing polymer composites including resin transfer molding, filament winding, and pultrusion depend mainly on optimization of process parameters and molds to attain dimensional precision. Although these traditional methods are efficient, they possess constraints regarding cost, scalability, and design flexibility. But additive manufacturing, especially dual extruder FDM printing facilitates the creation of composite structures without the need for molds, providing design flexibility and decreased production time. Furthermore, recent improvements in 3D printing and emerging 4D printing techniques have created novel opportunities for the fabrication of multi-functional composites with complex 3D structures and improved mechanical properties.
Laminated composite structures (LCS) have gained significant attention among composite structures due to their exceptional mechanical qualities, including high stiffness, strength-to-weight ratio, and flexural strength. LCS consist of various layers of materials that can be tailored to fulfill unique application needs.
Fig. 1. Dual Extruder 3D Printer (FDM)
The capability of dual extruder FDM to fabricate multi- material LCS with customized features has provided it a compelling choice for diverse applications. In the aerospace, automotive and packaging industries, these composites are employed to reduce weight while preserving structural integrity. In the defense sector, their superior impact resistance makes them suitable for protective gear. Moreover, their applicability facilitates sports equipment and medical devices where customization and performance are paramount.
In Spite of its various benefits, dual extruder FDM possesses some constraints that require resolution to fully harness its capabilities. A primary difficulty is the anisotropic mechanical characteristics caused by inadequate interlayer bonding, which may undermine the structural integrity of printed components. This technology falls short in surface polish and resolution compared to other additive manufacturing techniques, frequently necessitating post- processing to achieve high-quality standards. The selection of materials appropriate for dual extrusion FDM printing is restricted by parameters such as melting point and temperature characteristics.
Recent studies concentrate on addressing these constraints via novel material compositions, process enhancement, and hybrid production techniques. Advancements in nozzle design and process control are resolving challenges associated with layer adhesion and surface finish.
The advancement of multi-material LCSs via dual extruder FDM signifies a progressing area with significant prospects for future research. This review facilitates a thorough examination of documented investigations on dual extruder FDM-fabricated LCS, emphasizing material selection, structural design, and performance tailored to specific applications. This study identifies current research deficiencies and suggests solutions for additional exploration to improve the efficacy of dual extruder FDM in fabricating advanced composite structures. By resolving these deficiencies, researchers can identify new prospects for utilizing dual extruder FDM in high-performance applications across sevral industries.
In conclusion, additive manufacturing, particularly dual extruder FDM, has transformed composite fabrication by
facilitating the production of multi-material structures with improved mechanical characteristics and design versatility. This review intends to be a significant resource for researchers offering insights into the latest advancements in FDM-based multi-material composite fabrication.
- LITERATURE REVIEWThe current research mainly examines the influence of various 3D printing (3DP) process parameters on the mechanical properties of printed composites. The analyzed key process variables include Layer Height (LH), Infill Pattern (IP), Thickness Ratio (TR), Number of Layers (NL), Infill Density (ID), Flow Rate, Orientation angle, print speed, nozzle diameter, extrusion temperature, bed temperature, print chamber temperature, retraction speed, print time, wall thickness, layer width, Number of shells. The estimated mechanical properties include impact strength, interfacial adhesion, ultimate tensile strength (UTS), tensile yield strength, tensile strain (), interfacial fracture toughness, critical energy release rate (CERR), strength-to-weight (S/W) ratio, tensile toughness, flexural strength (FS), and flexural yield strength (FYS).
Ahmed et al. [16] investigated the influence of LH, TR, ID, and Orientation angle on the impact strength of laminated composite structures (LCS) composed of carbon fiber Reinforced PLA (CF-PLA) / Acrylonitrile Butadiene Styrene (ABS). Their studies demonstrated an improvement in impact strength relative to monolithic materials highlighting the potential of these LCS in aerospace and automotive applications.
Similarly, Ahmed et al. [17] enhanced ultimate tensile strength (UTS), Youngs modulus (E), and strain () through the manipulation of laser power, processing speed (PS), interlayer distance, and cooling rate. Their findings demonstrated enhanced mechanical characteristics in LCS relative to monolithic sheets, facilitating the development of high-performance, lightweight composite materials.
Ahmad et al. [18] employed the Response Surface Methodology (RSM) to investigate interfacial adhesion in CF-PLA/ABS LCS. The study illustrated enhancements in interfacial adhesion by optimizing 3DP parameters, specifically print speed, infill density, LH and TR, with optimal circumstances identified as a print speed of 50.54 mm/s, infill density of 79.82%, LH of 0.15 mm, and TR of
0.49. Furthermore, they evaluated interfacial fracture toughness (IFFT) employing techniques such as Double Cantilever Beam (DCB) tests for mode I and Mixed-Mode Bending (MMB) testing for combination modes. Their findings indicated that augmenting NT and PS improved thermal fusion, resulting in elevated IFFT values.
Khan et al. [19] produced CF-PLA/ABS LCS via fused filament fabrication (FFF) to assess fracture toughness under various loading conditions. The study indicated considerable improvements in the critical energy release rate (CERR) for mode II IFFT as PS and NT levels were elevated. This was assessed to improve layer bonding and thermal adhesion.
Yadav et al. [20] used Fused Deposition Modeling (FDM) to fabricate Acrylonitrile Butadiene Styrene (ABS), polyethylene terephthalate glycol (PETG), multi-material LCS. Their investigations revealed that the ultimate tensile strength (UTS) reached its maximum at an ID of 50%. Further, a Genetic Algorithm-Artificial Neural Network
(GA-ANN) model optimized Ultimate Tensile Strength (UTS) to 46 MPa by modifying the normalization temperature (NT) to 240°C and decreasing the interdigitated (ID) percentage to 45%. This discovery emphasized the susceptibility of UTS to NT in contrast to ID.
Chen et al. [21] focused on enhancing PS, LT, and ID for PETG/ABS bi-material composites produced using extrusion-based additive manufacturing. The ideal parameter combinations of 30 mm/s PS, 0.1 mm LT, and 75% ID produced the maximum ultimate tensile strength (UTS) and elastic modulus (E), demonstrating the capacity for performance improvement through parameter optimization. Yin et al. [22] investigated the production of Acrylonitrile Butadiene Styrene (ABS)/thermoplastic polyurethane (TPU) LCS using a dual-extruder FDM method. Through the manipulation of NT, BT, and PS, they determined that the interfacial bonding strength improved with elevated levels of these parameters. The research emphasized possible uses in interactions between stiff and compliant materials.
Baca and Ahmad [23] conducted a comparison of single- mixing nozzle systems (SMNS) and multi-nozzle systems (MNS) for the fabrication of multi-material polymer composites. Although SMNS provided simplicity and reduced calibration errors, MNS facilitated accurate material transitions and multi-hued extrusion. However, MNS faced challenges such as oozing and material transition defects, indicating a need for further research on advanced nozzle designs to enhance material deposition accuracy and mechanical properties.
Tamburrino et al. [24] investigated the tensile adhesion strength of different bi-material combinations (copolyester (CPE)-PLA, CPE-TPU, and PLA-TPU) in 3D-printed LCS.
They found that interfacial adhesion was highest in the CPE- TPU combination, while PLA-TPU composites achieved maximum adhesion through mechanical interlocking patterns. The study highlighted that higher IDs resulted in stronger bonding, though the type of infill pattern had a limited effect.
Research consistently highlights the influence of 3DP process parameters on the mechanical performance of laminated composites. Studies have shown that optimizing parameters such as LT, PS, ID, and NT can significantly enhance properties like UTS, IS, and IFFT. While advancements in multi-material and multi-nozzle systems have broadened the scope of FDM, challenges remain, such as weak layer bonding, calibration issues, and limited material compatibility.
Future work should focus on developing advanced extrusion systems, novel material formulations, and hybrid fabrication techniques. These efforts will be critical in addressing current limitations and unlocking new applications for multi- material laminated composites in high- performance industries such as aerospace, automotive, and biomedical engineering.
- METHODLOGYThe methodology adopted in this review consists several systematic phases designed to the exploration of dual- extruder fused deposition modeling (FDM) for multi-material layered composites. A detailed survey of relevant academic and industrial sources conducted to understand the limitations and advancements of existing FDM systems. This involved
identifying critical process parameters, material compatibility issues, and mechanical performance metrics relevant to dual-extruder applications.
Fig. 2. Printing of Laminated Composite Structures using dual extruder FDM
Focusing on the role of nozzle configurations, composite designs, and material properties in improving mechanical performance. Observational data to be done from experimental setups and industry applications to validate findings. The synthesized results to be analyzed to identify key challenges such as material calibration, interlayer bonding, and surface finish quality. This approach provided a comprehensive understanding of dual-extruder FDM applications and areas for further innovation.
- FUTURE SCOPEWhile numerous studies have explored multi-material composite structures fabricated using FDM, there are significant opportunities for further research and development. Current research has primarily focused on a limited selection of thermoplastic materials. Future efforts should focus on leveraging this diversity to fabricate and analyze novel layered composite structures with enhanced properties.
In spite of advancements in the fabrication of LCS and similar structures using FDM, the development of systems capable of highthroughput manufacturing has received limited attention. Research also should focus on optimizing multi-nozzle configurations and addressing challenges such as material calibration, nozzle clogging, and material transitions to enhance efficiency and output.
Many existing studies are feasibility-focused, exploring the basic fabrication and testing of LCS. Future research should be beyond feasibility and investigate the development of functional composites and complex geometries suitable for specific applications. Comparative studies between LCS and similar structures produced through conventional manufacturing methods could provide valuable insights into cost, labor, time efficiency, and performance advantages.
Simulation tools, such as finite element analysis (FEA), offer untapped potential for advancing LCS research. FEA can help predict defects, such as delamination or thermal expansion mismatches, caused by differing polymer properties (e.g., thermal expansion coefficients or melting points). Moreover, FEA could provide theoretical estimates of LCS properties, which can then be compared with experimental results.
- CONCLUSION
This review examined the current progress in the production of multi-material laminated composite structures by extrusion-based additive manufacturing. Although numerous studies have emphasized the improved mechanical and functional characteristics of 3D-printed components, significant limitations remain.
To address these shortcomings, future research should focus on the fabrication and testing of multi-material structures with an emphasis on material diversity, comprehensive testing methodologies, application-specific designs, and high-throughput manufacturing systems. Furthermore, the incorporation of finite element analysis (FEA) can substantially improve comprehension by simulating interfacial interactions and forecasting features prior to experimental confirmation.
REFERENCES
- Mishra V, Negi S, Kar S. FDM-based additive manufacturing of recycled thermoplastics and associated composites. J Mater Cycles Waste Manage 2023; 25. https://doi.org/10.1007/s10163-022-01588-2.
- Khalid MY, Arif ZU, Al RA. Investigation of tensile and flexural behavior of green composites along with their impact response at different energies. Int J Precision Eng Manuf – Green Technology 2022;9. https://doi.org/10.1007/s40684-021-00385-w.
- Khan I, Abas M, Ahmad S, Al Rashid A, Koç M. Fabrication of a low- cost fused filament fabrication-based 3D printer and investigation of the effects of process parameters on mechanical properties of 3D- printed samples. J Eng Res 2024.https://doi.org/10.1016/J.JER.2024.06.018.
- Almesmari A, Baghous N, Ejeh CJ, Barsoum I, Abu Al-Rub RK. Review of additively manufactured polymeric metamaterials: design, fabrication, testing and modeling. Polymers 2023;15. https://doi.org/10.3390/polym15193858.
- Arif ZU, Khalid MY, Noroozi R, Sadeghianmaryan A, Jalalvand M, Hossain M. Recent advances in 3D-printed polylactide and polycaprolactone-based biomaterials for tissue engineering applications. Int J Biol Macromol 2022;218. https://doi.org/10.1016/j.ijbiomac.2022.07.140.
- Al Rashid A, Koç M. Fused filament fabrication process: A review of numerical simulation techniques. Polymers (Basel) 2021;13:118. https://doi.org/10.3390/polym13203534.
- Tariq A, Arif ZU, Khalid MY, Hossain M, Rasool PI, Umer R. Recent advances in the additive manufacturing of stimuli-responsive soft polymers. Adv Eng Mater 2023;25. https://doi.org/10.1002/adem.202301074.
- Wang X, Jiang M, Zhou Z, Gou J, Hui D. 3D printing of polymer matrix composites: A review and prospective. Compos B Eng 2017;110. https://doi.org/10.1016/j.compositesb.2016.11.034.
- Yankin A, Alipov Y, Temirgali A, Serik G, Danenova S, Talamona D, et al. Optimization of printing parameters to enhance tensile properties of abs and nylon produced by fused filament fabrication. Polymers 2023;15. https://doi.org/10.3390/polym15143043.
- Abas M, Khan I, Jan Z. An Integrated Approach of Particle Swarm Optimization and Grey Relational Analysis in Multi-Response Optimization of Fused Deposition Modeling. In: Thanigaivelan R, editor. Metaheuristics Algorithm and Optimization of Engineering and Complex Systems. 2024th ed., IGI Global; 2024, p. 2342. DOI: 10.4018/979-8-3693-3314-3.ch002.
- Al Rashid A, Koç M. Additive manufacturing for sustainability and circular economy: needs, challenges, and opportunities for 3D printing of recycled polymeric waste. Mater Today Sustain 2023;24. https://doi.org/10.1016/j.mtsust.2023.100529.
- Dananjaya SAV, Chevali VS, Dear JP, Potluri P, Abeykoon C. 3D printing of biodegradable polymers and their composites Current state-of-the-art, properties, applications, and machine learning for potential future applications. Prog Mater Sci Dec. 2024;146:101336. https://doi.org/10.1016/J.PMATSCI.2024.101336.
- Bakhtiari H, Aamir M, Tolouei-Rad M. Effect of 3D printing parameters on the fatigue properties of parts manufactured by fused filament fabrication: a review. Appl Sci (Switzerland) 2023;13. https://doi.org/10.3390/app13020904.
- Abas M, Habib T, Noor S, Zimon D, Wo´zniak J. Application of multi- criteria decision-making methods in the selection of additive manufacturing materials for solid ankle foot orthoses. J Eng Des 2023;34. https://doi.org/10.1080/09544828.2023.2247859.
- Hussain G, Khan I. Characteristics of friction stir processed UHMW polyethylene-based composite. IOP Conf Series: Mater Sci Eng 2018;301. https://doi.org/10.1088/1757-899X/301/1/012109.
- Ahmed H, Hussain G, Gohar S, Ali A, Alkahtani M. Impact toughness of hybrid carbon fiber-PLA/ABS laminar composite produced through fused filament fabrication. Polymers 2021:13. https://doi.org/10.3390/polym13183057.
- Ahmed SW, Hussain G, Al-Ghamdi KA, Altaf K. Mechanical properties of an additive manufactured CF-PLA/ABS hybrid composite sheet. J Thermoplast Compos Mater 2021:34. https://doi.org/10.1177/0892705719869407.
- Ahmed SW, Hussain G, Altaf K, Ali S, Alkahtani M, Abidi MH, et al. On the effects of process parameters and optimization of interlaminate bond strength in 3D printed ABS/CF-PLA composite. Polymers 2020:12. https://doi.org/10.3390/POLYM12092155.
- Khan AS, Ali A, Hussain G, Ilyas M. An experimental study on interfacial fracture toughness of 3-D printed ABS/CF-PLA composite under mode I, II, and mixed-mode loading. J Thermoplast Compos Mater 2021:34. https://doi.org/10.1177/0892705719874860.
- Yadav D, Chhabra D, Kumar Garg R, Ahlawat A, Phogat A. Optimization of FDM 3D printing process parameters for multi- material using artificial neural network. Mater Today: Proc 2020;21. https://doi.org/10.1016/j.matpr.2019.11.225.
- Chen Z, Gong K, Huang C, Hu S, Xu H, Fuenmayor E, et al. Parameter optimization for PETG/ABS bilayer tensile specimens in material extrusion 3D printing through orthogonal method. Int J Adv Manuf Technol 2023;127. https://doi.org/10.1007/s00170-023-11515-w.
- Yin J, Lu C, Fu J, Huang Y, Zheng Y. Interfacial bonding during multi- material fused deposition modeling (FDM) process due to inter- molecular diffusion. Mater Des 2018;150. https://doi.org/10.1016/j.matdes.2018.04.029.
- Baca D, Ahmad R. The impact on the mechanical properties of multi- material polymers abricated with a single mixing nozzle and multi- nozzle systems via fused deposition modeling. Int J Adv Manuf Technol 2020:106. https://doi.org/10.1007/s00170-020-04937-3.
- Tamburrino F, Graziosi S, Bordegoni M. The influence of slicing parameters on the multi-material adhesion mechanisms of FDM printed parts: an exploratory study. Virtual Phys Prototyping 2019;14. https://doi.org/10.1080/17452759.2019.1607758.
- Wang Y, Zhou Y, Lin L, Corker J, Fan M. Overview of 3D additive manufacturing (AM) and corresponding AM composites. Compos Part A: Appl Sci Manuf 2020;139.
https://doi.org/10.1016/j.compositesa.2020.106114.
IJERTV13IS120117
(This work is licensed under a Creative Commons Attribution 4.0 International License.)