
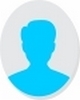
- Open Access
- Authors : Rahul Shukla, Prof. Dr. V. B. Ugale
- Paper ID : IJERTV14IS030145
- Volume & Issue : Volume 14, Issue 03 (March 2025)
- Published (First Online): 01-04-2025
- ISSN (Online) : 2278-0181
- Publisher Name : IJERT
- License:
This work is licensed under a Creative Commons Attribution 4.0 International License
An Overview in use of Airless/ Non Pneumatic Tyres (NPTs) in Military Vehicles
Rahul Shukla
College of Military Engineering
Prof. Dr. V. B. Ugale
College of Military Engineering
Pune Pune
Abstract
This paper investigates the implementation of airless or non-pneumatic tyres (NPTs) for Indian military vehicles, focusing on their design, functionality, and potential benefits. NPTs utilize a flexible honeycomb or spoke-like structure in place of air-filled chambers, making them resistant to punctures and blowouts. This study highlights the necessity of adopting NPTs for military applications due to their enhanced durability, reduced maintenance needs, and improved reliability in rough terrains. The advantages of NPTs, including puncture resistance, longevity, and safety, are thoroughly analysed, along with their limitations, such as increased weight and ride comfort concerns. The research also explores the practical deployment of NPTs in military vehicles, including light tactical vehicles, armoured personnel carriers, and logistics vehicles. Additionally, the study evaluates the current challenges faced by NPT technology, such as higher manufacturing costs and the need for further refinement to enhance ride comfort. The findings indicate that while NPTs offer significant benefits, future research should focus on optimizing their performance and cost-effectiveness for widespread military adoption.
This paper explores the application of airless or Non-Pneumatic Tyres (NPTs) for Indian military vehicles. It covers the fundamental concepts, advantages, limitations, and practical applications of NPTs, emphasizing their potential in enhancing performance and reducing vulnerabilities in military operations. The study also analyses the challenges and future prospects of adopting this innovative technology.
Keywords
Airless tyres, Non-Pneumatic Tyres, Military Vehicles, Durability, Puncture Resistance
-
INTRODUCTION
The Indian Military Forces operate in some of the most challenging environments in the world, from the scorching deserts of Rajasthan to the freezing altitudes of the Himalayas. Military vehicles play a critical role in ensuring the mobility, logistics, and operational effectiveness of the armed forces in these diverse terrains. However, the performance of military vehicles is heavily dependent on the durability and reliability of their tyres, which serve as the primary point of contact between the vehicle and the ground. In military operations, where mobility and time are often decisive factors, tyre failures can have catastrophic consequences.
Pneumatic tyres, which are currently the standard for almost all military vehicles, are air-filled and designed to provide comfort, traction, and flexibility over various terrains. However, they are also prone to punctures, blowouts, and rapid wear, particularly in rough and unforgiving environments. A puncture in a co mbat zone or remote operation can immobilize a vehicle, leaving it vulnerable to enemy attacks, delaying crucial missions, and disrupting supply chains. These challenges underscore the need for a more durable, reliable, and maintenance -free alternative to conventional pneumatic tyres.
In recent years, airless or non-pneumatic tyres (NPTs) have emerged as a promising alternative to traditional tyres. Unlike pneumatic tyres, which rely on pressurized air to support the vehicle's weight and provide shock absorption, NPTs use innovative materials and structures that do not require air. This design eliminates the risk of punctures and blowouts, offering increased durability and reducing the need for maintenance. For military applications,
especially in hostile and remote environments, these features make NPTs a highly attractive solution.
While NPTs have been primarily developed and tested by global automotive and military industries, their adoption by the Indian military remains limited. However, given Indias unique geographical and operational challenges, there is significant potential for NPTs to revolutionize military vehicle performance in India. From high-altitude border regions, where sharp rocks and uneven terrain pose constant threats to vehicle tyres, to desert operations in Rajasthan, where extreme temperatures accelerate tyre wear, the Indian military could benefit greatly from the durability and low-maintenance nature of NPTs.
The strategic and operational advantages of adopting NPTs in Indian military vehicles extend beyond puncture resistance. NPTs also offer improved mobility in rugged terrains, reduced vehicle downtime, and long-term cost savings due to their longer operational lifespan. Moreover, the integration of NPTs aligns with Indias broader efforts to modernize its military forces and adopt cutting-edge technologies that enhance operational readiness
Figure-1: TWEEL NPT by Michellin
-
OBJECTIVE
This objective of the report is to bring out the following aspects of NPTs:-
-
The Need for Airless Tyres in Indian Military Operations. Analyzes the operational challenges faced by Indian military vehicles and the limitations of conventional pneumatic tyres.
-
Working Mechanism of Airless/Non-Pneumatic Tyres. Provides a detailed breakdown of the design, materials, and functionality of NPTs.
-
Advantages of Airless Tyres in Military Vehicles. Discusses the key benefits of NPTs, including durability, reduced maintenance, and improved mobility in harsh terrains.
-
Challenges in Adopting Non-Pneumatic Tyres for Indian Military Vehicles. Explores the technical, logistical, and cost-related challenges that need to be addressed for successful implementation.
-
Global Military Use of Non-Pneumatic Tyres. Examines how NPTs have been used by foreign militaries and what India can learn from these experiences.
-
Prospects of Non-Pneumatic Tyres in the Indian Military. Looks at the future potential of NPTs for Indian military vehicles and the steps needed for successful adoption.
-
Conclusion. Summarizes the key findings and recommendations for integrating NPTs into Indian military vehicles.
-
-
OVERVIEW OF TERRAIN CHALLENGES FACED BY MILITARY VEHCLES
Mobility is one of the most critical components of military operations, as it directly affects the speed, efficiency, and success of any mission. In a military context, mobility refers to the ability to move troops, equipment, and supplies quickly and effectively across diverse terrains and under various operational conditions. The Indian military, given its geographical diversity, operates in some of the most challenging environments in the world. These include arid deserts, dense forests, coastal regions, mountainous terrain, and icy altitudes. Effective mobility in these regions is essential for maintaining operational readiness, conducting strategic maneuvers, delivering supplies, and providing support to troops in combat zones.
Different types of military mobility, including tactical mobility (battlefield movements), strategic mobility (long-distance movement of troops and equipment), and logistical mobility (supply and support chain), all depend on the capability of vehicles to traverse varied and difficult terrains. As such, tyres, one of the most important components of military vehicles, play a critical role in ensuring that vehicles remin mobile, reliable, and ready for action. Any tyre failure can severely compromise a mission by delaying troop movements or supply of deliveries, making the importance of durable, resilient tyres paramount. Below is an in-depth exploration of the various terrain challenges faced by the Military vehicles:
–
-
Challenges of Desert Terrain. Loose sand provides poor traction, making it difficult for vehicles to maintain stability. Moreover, the high temperatures often cause tyres to wear more quickly, leading to increased risks of blowouts or tyre damage. Dust and sand particles can also infiltrate vehicle components, accelerating wear and tear.
-
Challenges of Jungle Terrain. In jungle environments, vehicles must navigate through narrow, muddy trails that are often flanked by dense vegetation. Pneumatic tyres are highly prone to punctures from sharp branches, roots, and debris. The frequent exposure to mud and water can also accelerate tyre wear and increase the likelihood of vehicles getting stuck in boggy areas. Resupplying tyres in these remote areas can be logistically challenging and time-consuming.
-
Challenges of Mountain Terrain. The rocky, uneven surfaces, steep inclines, and narrow mountain roads increase the risk of tyre damage from sharp stones and debris. Additionally, the extreme cold can make pneumatic tyres more susceptible to brittleness and failure. Tyre maintenance in such remote and high-altitude locations is logistically difficult, and any vehicle breakdown can delay critical operations, making units vulnerable.
-
Challenges of Cold-Weather Terrain. The extreme cold affects the rubber compounds in conventional tyres, making them more brittle and prone to cracking. Ice and snow present additional challenges, as vehicles require tyres with enhanced grip to avoid skidding. Punctures from sharp ice or hidden rocks are common, and maintaining vehicles in these conditions is difficult due to the logistical challenges of transporting supplies to such remote locations.
-
Challenges of Coastal and Amphibious Terrain. The combination of saltwater, sand, and marshy ground can quickly degrade pneumatic tyres. Saltwater exposure accelerates corrosion and wears down rubber components, while sandy and marshy ground can cause vehicles to get stuck. The frequent transitions between wet and dry conditions also make it challenging to maintain tyre integrity and punctures or blowouts in these areas can leave vehicles immobilized and vulnerable.
-
Challenges of Urban Terrain. In urban settings, tyres are often subjected to rough surfaces, broken roads, and debris from buildings or explosions. There is also the risk of tyres being damaged by sharp objects or gunfire during counter- terrorism operations. Pneumatic tyres, in such environments, are highly vulnerable to punctures, which can immobilize vehicles and expose them to enemy fire.
Figure-2: Damage to the Pneumatic Tyres of Vehs
-
-
OVERVIEW OF PNEUMATIC TYRES
-
Components of Pneumatic Tyres. A pneumatic tyre comprises several key components, each made from specific materials chosen for their unique properties:
-
Tread
-
Material. Synthetic rubber compounds (such as butadiene rubber, styrene-butadiene rubber), natural rubber and sometimes silica.
-
Function. The tread is the outermost layer of the tyre that comes into direct contact with the road or terrain. It is designed to provide traction, resist wear, and handle a variety of surfaces like mud, gravel, sand, or snow. The rubber compound in the tread is engineered to be flexible yet resistant to cuts, tears, and abrasions. For military applications, treads are often designed with deeper grooves and aggressive patterns to improve grip and handling in off-road conditions.
-
-
Sidewall
-
Material. Natural and synthetic rubber with additives for strength.
-
Function. The sidewall connects the tread to the bead of the tyre and is designed to provide lateral stability and protect the inner components of the tyre from damage. In military tyres, the sidewall must be particularly strong to resist impacts from sharp rocks, debris, and other hazards in rough terrains. It also helps absorb shocks from uneven surfaces, ensuring smoother vehicle handling.
-
-
Carcass ( Body Ply)
-
Material. Layers of textile cords made of nylon polyester coated with rubber.
-
Function. The carcass is the skeleton of the tyre, providing structural integrity and strength. It consists of multiple layers (plies) of cords embedded in the rubber to give the tyre its shape and flexibility. In military tyres, the carcass is designed to withstand heavy loads and impacts, as military vehicles often carry substantial weight over long distances.
-
-
Bead
-
Material. High-tensile steel wire coated with rubber.
-
Function. The bead is the edge of the tyre that ensures an airtight fit between the tyre and the wheel rim. It prevents the tyre from slipping off the rim during heavy braking or acceleration, especially in high-stress military applications. The steel wire in the bead.Provides the necessary strength to keep the tyre securely attached to the rim, even under extreme pressure or while carrying heavy loads.
-
-
Belt (Breaker Belt)
-
Material. Steel or synthetic cords (often made from aramid fibres like Kevlar).
-
Function. The belt is positioned between the tread and the carcass, providing additional strength to the tyre. It helps to reinforce the tyre against punctures and cuts while also improving handling by maintaining the tyre's shape under pressure. Steel belts are commonly used in military tyres to provide extra durability and resistance to penetration from sharp objects such as rocks or debris on the battlefield.
-
-
Inner Liner
-
Material. Butyl rubber or halo butyl rubber (air-impermeable synthetic rubber).
-
Function. The inner liner acts as a modern substitute for an inner tube, creating an airtight seal that holds the compressed air inside the tyre. For military applications, the inner liner is crucial because it ensures that the tyre maintains its air pressure even when subjected to harsh conditions or damage. Butyl rubber is used for its excellent air retention properties and resistance to temperature changes.
-
-
-
Materials used in Pneumatic Tyres. Military tyres need to balance durability, flexibility, and resistance to extreme conditions. The choice of materials in each component of the tyre reflects the need to optimize these characteristics for operational performance. Below is an overview of the primary materials used in the construction of pneumatic tyres for Indian military vehicles.
-
Natural Rubber
-
Use. Found in the tread and sidewall.
-
Properties. Provides excellent flexibility and durability. Natural rubber is valued for its ability to maintain its elasticity in various temperature conditions and to absorb impacts from rough terrain, making it a key material for military tyres.
-
-
Synthetic Rubber (Butadiene Rubber, Styrene-Butadiene Rubber)
-
Use. Used in the tread, sidewall, and carcass coatings.
Properties. Synthetic rubber is engineered to offer superior wear resistance and temperature stability. Butadiene rubber (BR) and styrene-butadiene rubber (SBR) are often used in military tyres because they perform well under heavy loads and in extreme weather conditions.
-
-
Steel
-
Use. Reinforces the bead and breaker belt.
-
Properties. Steel provides strength and puncture resistance, especially in off-road conditions. High-tensile steel wire is used in the bead to ensure the tyre stays secured to the rim, even during high-stress military maneuvers. Steel belts in the tyre structure improve rigidity and reduce the risk of punctures.
-
-
Textile Cord (Nylon, Polyester, Rayon)
-
Use. Embedded in the carcass.
-
Properties. These textile materials provide flexibility and strength, allowing the tyre to withstand heavy loads without losing its shape. Nylon is often used for its high tensile strength, while polyester and rayon provide improved durability and resilience against wear and tear.
-
-
Aramid Fibres (Kevlar)
-
Use. In reinforced breaker belts for high-performance military tyres.
-
Properties. Kevlar is an extremely strong, heat-resistant synthetic fibre known for its use in bulletproof vests. In tyres, it adds additional puncture resistance and structural integrity. This is particularly important for military vehicles operating in areas where tyre damage from sharp objects or debris is common.
-
-
Butyl Rubber (or Halobutyl Rubber)
-
Use. In the inner liner.
-
Properties. Butyl rubber is known for its excellent air retention, making it a perfect choice for the inner liner, which holds the compressed air within the tyre. It also has good resistance to heat and ageing, helping tyres retain their air pressure over time.
Figure-3: Design of Pneumatic Tyres
-
-
-
-
DESIGN OF NPTs
The NPTs do not rely on air pressure for support, which makes it puncture-proof and highly resilient to damage from rough terrains. It is an integrated unit of the tyre and wheel, unlike traditional tyres where the wheel and tyre are separate components. Instead of relying on compressed air for load-bearing and shock absorption, NPTs use a solid or semi-solid structure made from advanced materials such as elastomers, polyurethane, or composite materials. The construction of non-pneumatic tyres is fundamentally different from that of pneumatic tyres, as it focuses on the use of structural elements to provide the necessary flexibility, load distribution, and durability.
At the core of a non-pneumatic tyre is a solid hub, which serves as the mounting point for the wheel. The hub is typically made from high-strength metals like steel or aluminium, or lightweight composite materials, depending on the application. From the hub, a series of spokes or webs radiate outward, replacing the role of the air chamber in pneumatic tyres. These spokes are made from elastomeric materials, such as polyurethane, which can flex and deform under load, mimicking the behaviour of air-filled tyres. The spokes are designed to provide both vertical and lateral flexibility, allowing the tyre to absorb shocks and maintain stability even on rough terrains. Some designs, like the TWEEL, use a radial spoke pattern that allows the tyre to flex when encountering obstacles, distributing the load evenly across the contact patch.
The outer rim of a NPT serves as the structural framework that holds the entire assembly together. It is often made from composite materials or high-strength metals, providing the necessary rigidity to keep the tyre intact under heavy loads. The rim is designed to withstand impacts and stress, ensuring that the tyre maintains its shape and performance in extreme conditions. The tread of a non-pneumatic tyre is similar to that of a pneumatic tyre, with rubber compounds and tread patterns optimized for the intended application. However, since NPTs do not rely on air pressure, the tread can be designed to focus more on wear resistance and grip, without the need to accommodate for pressure changes or the risk of punctures.
One of the most significant advantages of non-pneumatic tyres is their puncture resistance. Since they do not rely on
air pressure, they are immune to punctures, blowouts, and leaks, making them ideal for applications where reliability is critical, such as military vehicles operating in hostile environments. The use of elastomeric materials in the spokes and tread ensures that the tyre can withstand extreme wear, cuts, and abrasions, providing a longer lifespan compared to pneumatic tyres.
In terms of load distribution, non-pneumatic tyres rely on the structural integrity of their components to bear the vehicle's weight. The spokes or webs flex under load, distributing the weight evenly across the tyre's contact patch. This design allows the tyre to maintain a consistent performance, even under heavy loads or in rough terrains, without the risk of deflation or performance degradation. The use of advanced materials in the construction of non-pneumatic tyres also contributes to their durability, as they are resistant to environmental factors such as temperature fluctuations, UV exposure, and chemical degradation.
-
DESIGN COMPONENTS
A NPT consists of several critical design components that work together to replicate the performance of pneumatic tyres while eliminating the need for air pressure. These components are optimized to provide the necessary load- bearing capacity, shock absorption, and handling characteristics required in various military applications.
The main design elements of NPTs include: –
-
Hub (Wheel Mounting Interface)
-
Spokes (Shear Beam)
-
Tread
-
Rim
-
Elastomeric Web or Support Structure
-
Hub (Wheel Mounting Interface)
-
Material. The hub is typically made of durable metals such as steel or aluminium alloy, capable of handling high stress and heavy loads.
-
Function. The hub serves as the mounting interface between the tyre and the vehicles axle, replacing the traditional wheel in a pneumatic system. The hub is bolted directly onto the vehicles wheel assembly, and its structural integrity is critical for ensuring the overall performance and safety of the tyre.
-
Design Consideration. The hub must provide a secure connection and be able to withstand heavy loads, as military vehicles often carry considerable weight. In addition, it is designed to be highly resistant to corrosion, especially for use in harsh environments like deserts or coastal regions.
-
-
Spokes (Shear Beam)
-
Material. The spokes are generally made of polyurethane or other elastomeric materials. These materials are chosen for their flexibility, durability, and ability to deform under load while maintaining structural integrity.
-
Function. The spokes are one of the most innovative aspects of the TWEEL type tyre. They replace the role of air in traditional tyres, acting as flexible yet resilient structures that absorb impacts and provide shock absorption. The spokes can flex and deform to conform to rough terrain, ensuring that the tyre remains stable even when subjected to uneven surfaces or heavy loads.
-
Design Consideration. The radial spoke design is key to distributing the load evenly across the tyre while allowing it to flex and absorb shocks. The number, thickness, and orientation of the spokes can be adjusted based on the application and terrain. In military applications, the spokes are designed to be robust enough to handle impacts from rocks, debris, or other obstacles encountered during off-road operations.
-
-
Tread
-
Material. The tread is made from synthetic rubber compounds similar to those used in pneumatic tyres. These compounds are formulated to provide wear resistance, traction, and durability in various terrains.
-
Function. The tread is the outermost part of the TWEEL and comes into direct contact with the ground. It provides traction, enhances grip, and ensures stable handling of the vehicle on different surfaces, including
mud, gravel, sand, and snow. The tread pattern is designed to maximize contact with the ground while also expelling debris or water to prevent slipping.
-
Design Consideration. Depending on the vehicles mission, the tread pattern may be designed for specialized military operations. For example, off-road or all-terrain treads have deeper grooves for better traction on soft or uneven terrain. The tread compound is engineered to resist wear and tear over time, especially in high- temperature or abrasive environments like deserts and rocky regions.
-
-
Rim (Outer Structural Ring)
-
Material. The rim is often constructed from high-strength steel or composite materials that offer both durability and reduced weight.
-
Function. The rim serves as the structural framework that holds the entire TWEEL assembly together. It supports the spokes and ensures that the tyre maintains its shape under load. The rim is essential for ensuring the wheels structural integrity, particularly when subjected to heavy loads or high speeds in military operations.
-
Design Consideration. In military applications, the rim is designed to withstand impacts and stress without deforming. It must be corrosion-resistant and capable of withstanding the environmental stresses of military operations, such as exposure to extreme temperatures, mud, and moisture.
-
-
Elastomeric Web or Support Structure
-
Material. This component is made from elastic polyurethane materials, known for their ability to stretch, flex, and return to their original shape.
-
Function. The elastomeric web connects the outer tread to the inner hub and works in tandem with the spokes to distribute load and absorb shocks. It provides lateral stiffness to maintain handling and vehicle control while allowing vertical flexibility for shock absorption. The web can stretch and contract to accommodate obstacles such as rocks or potholes, making it ideal for off-road military vehicles.
-
Design Consideration. The geometry of the elastomeric web plays a crucial role in how the Tyre performs under load. The shape, thickness, and configuration of the web determine how well the tyre can handle impacts and absorb shocks. The material must be resilient enough to resist cuts, punctures, and damage from sharp objects while maintaining flexibility.
Figure-4: Design of NPT
Figure-5: Design of TWEEL NPT
-
-
-
ANALYSIS OF NPTS ON VARIOUS PARAMETERS
-
Load-Bearing Mechanism. In traditional pneumatic tyres, compressed air within the tyre's chamber acts as the
primary load-bearing element. However, in non-pneumatic tyres, the load is supported by a network of rigid and flexible structural components. Typically, this involves a central hub, radial spokes, or webs, and an outer rim.
-
Hub. The hub is the central component of an NPT, mounted directly to the vehicle's axle. It provides the necessary strength to support the spokes or structural elements that extend outward to the tread surface.
-
Spokes or Webs. One of the critical features of NPTs is the use of flexible spokes or web-like structures that radiate from the hub toward the outer rim. These spokes are often made from advanced materials such as elastomers or composite polymers. The design of the spokes varies between manufacturers but is generally intended to provide vertical flexibility for shock absorption and lateral stiffness for improved handling. The flexible nature of these spokes allows them to deform under load, distributing the vehicle's weight evenly across the tread surface. Once the load is removed, the spokes return to their original shape, providing both support and flexibility.
-
Outer Rim and Tread. The outer rim, which contains the tread, is the component that contacts the road or terrain. This part of the NPT is designed to provide the necessary grip, traction, and wear resistance. The tread pattern and rubber composition in NPTs are similar to those found in pneumatic tyres, ensuring reliable performance across different terrains. However, the tread in NPTs is not designed to accommodate air pressure changes, allowing for more rigid construction focused on durability and consistent performance.
-
The entire structure works as a cohesive unit, with the spokes flexing to absorb loads and distribute the weight evenly across the contact patch. This eliminates the need for air pressure while ensuring that the tyre can bear heavy loads without deforming or losing structural integrity.
-
-
Shock Absorption. Shock absorption is one of the most critical functions of a tyre, particularly for vehicles
operating in rough terrains, such as military vehicles. In pneumatic tyres, the air chamber compresses to absorb shocks when the vehicle encounters bumps, potholes, or uneven surfaces. NPTs, in contrast, rely on the flexibility of their structural elements to provide shock absorption.
-
Flexible Spokes. The most common shock absorption mechanism in NPTs is the deformation of the spokes. These spokes are designed to flex under impact, effectively mimicking the cushioning effect of compressed air in pneumatic tyres. The material properties of the spokes, such as elasticity and tensile strength, allow them to absorb vertical forces and return to their original shape once the load is removed. Unlike pneumatic tyres, where air pressure can vary, the shock absorption in NPTs remains consistent across different terrains because the material properties of the spokes do not change with external factors like temperature or pressure.
-
Tread Deformation. In addition to the spokes, the tread itself plays a role in absorbing shocks. The rubber compound used in the tread is designed to be flexible enough to conform to small surface irregularities while providing sufficient stiffness for traction and durability. This dual functionality ensures that the tyre can absorb minor impacts at the contact surface, complementing the shock absorption provided by the spokes.
-
NPTs are particularly effective at shock absorption in rough terrain or off-road conditions, where the tyre may encounter sharp rocks, debris, or uneven ground. The flexible spokes can adapt to these conditions without the risk of punctures, ensuring reliable performance and reduced maintenance.
-
-
Handling and Stability. Handling and stability are essential parameters in tyre design, as they directly affect vehicle control, steering response, and safety. In pneumatic tyres, air pressre plays a crucial role in maintaining the tyre's shape, which in turn affects how the tyre interacts with the road. Non-pneumatic tyres, on the other hand, maintain their shape through the rigid structure of the hub and outer rim.
-
Lateral Stiffness. The spoke design in NPTs provides lateral stiffness, ensuring that the tyre does not deform excessively during cornering or under lateral forces. This stiffness is critical for maintaining stability during high-speed manoeuvres, such as sharp turns or sudden direction changes. The material properties of the spokes, along with the design of the hub and rim, ensure that the tyre remains stable even under heavy lateral loads. This contrasts with pneumatic tyres, where improper air pressure can cause sidewall deformation, leading to reduced stability and handling performance.
-
Consistent Performance Across Terrains. One of the key advantages of NPTs is their consistent performance across different terrains and conditions. While pneumatic tyres can experience changes in handling due to variations in air pressure, temperature, or punctures, NPTs maintain their structural integrity regardless of external factors. This consistency makes them ideal for military applications, where vehicles may need to operate in extreme environments, such as deserts, rocky terrains, or snow-covered roads. The combination of flexible spokes for shock absorption and rigid sidewalls for lateral stability ensures that the tyre performs reliably in any condition.
-
-
Durability and Puncture Resistance. Durability is a major advantage of non-pneumatic tyres, especially in applications where tyres are exposed to harsh conditions, sharp objects, or high levels of wear and tear. One of the most significant weaknesses of pneumatic tyres is their vulnerability to punctures and blowouts. NPTs, by design, are puncture-proof, making them ideal for military vehicles, off-road applications, and environments with high risks of tyre damage.
-
Material Strength. NPTs are constructed from durable materials, such as elastomers, polyurethane, or advanced composites, which are resistant to cuts, abrasions, and impacts. These materials can withstand harsh conditions without degrading, ensuring a longer lifespan compared to traditional pneumatic tyres. Additionally, because NPTs do not rely on an air-filled chamber, there is no risk of deflation or blowout, which is a common issue in pneumatic tyres when they encounter sharp objects or extreme stress.
-
Resistance to Environmental Factors. Non-pneumatic tyres are also more resistant to environmental factors, such as temperature fluctuations, UV radiation, and chemical exposure. The materials used in NPTs are less susceptible to degradation from these factors, ensuring consistent performance and longer service life. This makes NPTs particularly well-suited for military vehicles, which may operate in extreme environments where temperature changes and exposure to harsh chemicals are common.
-
-
Wear and Maintenance. One of the significant benefits of non-pneumatic tyres is their low maintenance. Because they do not rely on air pressure, there is no need for regular inflation checks or pressure adjustments. This eliminates the risk of under-inflation or over-inflation, both of which can lead to uneven wear and reduced tyre life in pneumatic tyres.
-
Even Wear. The structural design of NPTs ensures even wear across the tread surface. The consistent load distribution provided by the flexible spokes or web structure means that the tyre wears evenly, reducing the need for frequent tyre replacements. In contrast, pneumatic tyres can suffer from uneven wear if the air pressure is not maintained correctly, leading to reduced performance and the need for more frequent maintenance.
-
Puncture-Free Operation. One of the primary maintenance concerns with pneumatic tyres is the risk of punctures.
When a pneumatic tyre is punctured, it often requires immediate repair or replacement to prevent further damage or a blowout. In contrast, NPTs are puncture-proof, eliminating the need for frequent repairs due to road hazards such as nails, sharp rocks, or other debris. This not only reduces maintenance costs but also increases the overall reliability of the vehicle.
-
-
Efficiency and Fuel Economy. The rolling resistance of a tyre plays a significant role in determining a vehicle's fuel efficiency. Pneumatic tyres, when properly inflated, offer low rolling resistance, which improves fuel economy. However, if the tyre is under-inflated, rolling resistance increases, leading to higher fuel consumption. Non-pneumatic tyres are designed to offer low rolling resistance through the use of lightweight materials and optimized spoke designs. While early NPTs had higher rolling resistance compared to pneumatic tyres, advancements in material science and structural design have reduced this gap. Today, modern NPTs are competitive with pneumatic tyres in terms of fuel efficiency, particularly in applications where the tyre must operate in extreme conditions or over long distances.
-
-
ADVANTAGES OF NPTS OVER TRADITIONAL TYRES
Here is a detailed comparison table listing the advantages of Non-Pneumatic Tyres (NPTs) over traditional Pneumatic Tyres across key performance parameters:
Parameter
Non-Pneumatic Tyres (NPTs)
Pneumatic Tyres
Puncture Resistance
Completely puncture-proof due to the absence of air; highly reliable in harsh environments and off-road
conditions.
Susceptible to punctures, blowouts, and air leaks, requiring repairs or replacements.
Maintenance
Low maintenance; no need for air pressure checks or repairs due to punctures.
Requires regular pressure checks and maintenance to avoid under-inflation, punctures, and blowouts.
Durability
Highly durable; resistant to environmental damage, cuts, and abrasions. Longer lifespan due to tough structural materials.
Prone to wear and damage from cuts, abrasions, and punctures. Frequent replacement or repairs are necessary in harsh conditions.
Shock Absorption
Shock absorption through flexible spokes or web structures, providing consistent performance across varying loads and terrain.
Air pressure provides shock absorption, but performance can degrade if the pressure is not maintained correctly.
Load-Bearing Capacity
Supports loads through structural elements like spokes, offering consistent load-bearing capacity even under harsh conditions.
Depends on air pressure for load-bearing; improper pressure can reduce performance or cause tyre failure.
Terrain Adaptability
Performs well on rough and uneven terrains without risk
of punctures or damage; suitable for off-road, military, and industrial use.
Performs well in different terrains but is vulnerable to
punctures, blowouts, and pressure loss, especially on rough surfaces.
Handling and Stability
Consistent handling and stability due to rigid structural design; no sidewall deformation.
Handling and stability can be affected by air pressure,
leading to sidewall deformation and reduced performance if not maintained.
Wear and Tear
Even wear due to consistent load distribution; resistant to uneven tread wear.
Susceptible to uneven wear due to improper inflation, overloading, or road conditions.
Rolling Resistance
Lower rolling resistance through optimized design,
Low rolling resistance if properly inflated, but increases
Parameter
Non-Pneumatic Tyres (NPTs)
Pneumatic Tyres
leading to better fuel efficiency in modern NPTs.
significantly if the tyre is under-inflated.
Weight
Slightly heavier due to solid construction and materials
used in spokes, hub, and rim.
Generally lighter, though run-flat tyres and reinforced
pneumatic tyres may weigh more.
Operational Reliability
Provides operational reliability in extreme conditions; no risk of deflation or blowouts, making it ideal for military vehicles.
Risk of deflation and performance degradation in extreme conditions or high-risk environments (e.g., military, off-road).
Cost Efficiency
Higher initial cost but lower long-term operational costs due to reduced maintenance and longer lifespan.
Lower initial cost but higher maintenance and replacement costs due to frequent repairs and wear.
Customization
Customizable tread patterns and materials for specific applications, such as military or off-road.
Tread customization is possible but limited by the need to maintain air pressure for optimal performance.
Performance in Extreme Conditions
Performs reliably in extreme temperatures, pressure, and chemical exposure. Resistant to UV damage and degradation.
Performance can degrade in extreme temperatures; UV exposure and chemicals may cause material degradation.
Safety
No sudden deflation or blowout risk, improving safety in critical operations.
Blowouts and sudden deflation are risks, potentially leading to loss of control and accidents.
Environmental Impact
Longer-lasting materials reduce the environmental impact by lowering the frequency of replacements.
More frequent replacements lead to greater environmental impact due to material waste.
-
LIMITATIONS OF NPTs
Here is a table highlighting some of the limitations of Non-Pneumatic Tyres (NPTs) compared to traditional Pneumatic Tyres:-
Parameter
Non-Pneumatic Tyres (NPTs)
Pneumatic Tyres
Weight
Generally heavier due to the solid construction and
materials used in the spokes and hub.
Typically lighter, especially when not using run-flat or
reinforced designs.
Ride Comfort
May provide a slightly stiffer ride due to the lack of air cushioning, particularly on smooth or paved roads.
Superior ride comfort due to the natural cushioning effect of compressed air.
Initial Cost
Higher initial purchase cost due to advanced materials and manufacturing processes.
Lower initial cost, making them more accessible for general use.
High-Speed Performance
May not perform as well at very high speeds due to limitations in structural flexibility and heat dissipation.
Designed for high-speed performance with the ability to dissipate heat effectively.
Rolling Noise
Can generate more noise, especially on smooth surfaces,
due to the solid construction and lack of air cushion.
Quieter performance in most conditions, as air helps
absorb vibrations and noise.
Parameter
Non-Pneumatic Tyres (NPTs)
Pneumatic Tyres
Limited Availability
Currently less widely available, with fewer manufacturers producing NPTs compared to traditional tyres.
Widely available in a range of sizes, styles, and price points from many manufacturers.
Mass Market Adoption
Primarily used in niche applications (e.g., military, off- road, industrial) and not yet mainstream for personal or commercial vehicles.
Universally adopted for personal, commercial, and industrial vehicles, with extensive infrastructure for repairs and replacement.
Tread Life
While the material is durable, once the tread wears down, the entire tyre may need to be replaced, as retreading is not commonly available.
Pneumatic tyres can often be retreaded, extending their useful life at a lower cost.
Heat Dissipation
Solid materials may retain more heat, leading to potential performance issues under extreme heat conditions.
Pneumatic tyres dissipate heat better through air circulation, reducing the risk of overheating.
Off-Road Flexibility
While excellent for off-road use, they cannot be adjusted (e.g., by lowering air pressure) for different terrains like sand or snow.
Pneumatic tyres can have air pressure adjusted to adapt to various terrains for better performance.
Vibration
Transmission
Can transmit more road vibrations to the vehicle due to the
lack of air, which naturally dampens vibrations.
Air-filled chambers naturally dampen vibrations,
providing a smoother and quieter ride.
Repairability
Limited repair options once damaged or worn; the entire tyre may need to be replaced.
Often repairable through patches, plugs, or retreading, extending the tyre's life.
Customizability for Comfort
Limited ability to customize for different comfort levels, as there is no air pressure to adjust for softer or firmer rides.
Air pressure can be adjusted for specific ride comfort, making pneumatic tyres more adaptable to different driving conditions.
Testing and Regulation
Still undergoing extensive testing for mass-market safety standards, especially for high-speed, on-road use.
Already meets well-established safety and performance standards for a wide range of vehicles and speeds.
Adaptation to Existing Vehicles
Some vehicles may require design changes or modifications to accommodate NPTs, especially for suspension tuning.
Universally compatible with most vehicle designs without modification.
This table outlines several limitations of non-pneumatic tyres, indicating that while they offer substantial advantages in durability and reliability, they have some trade-offs, especially in terms of comfort, cost, and high-speed performance. These factors must be considered when evaluating their suitability for widespread use.
-
GLOBAL USE OF NPTs
The global use of NPTs as of today can be broadly categorized into military and civilian applications, each leveraging the unique advantages that NPTs offer over traditional pneumatic tyres.
-
Military Use of NPTs in US Army
-
Testing and Development. The U.S. military has been testing NPTs for use in light tactical vehicles such as Humvees and joint light tactical vehicles (JLTVs). The military sees great potential in NPTs for reducing vehicle downtime and enhancing mission reliability, especially in combat zones where tyres are exposed to sharp objects, debris, and harsh terrain.
-
Partnerships. Companies like Michelin and Goodyear have been collaborating with the U.S. military to develop advanced NPTs tailored for military vehicles. For instance, Michelins Tweel NPT has undergone testing in various military applications due to its durability and ability to handle extreme conditions.
-
Landmine and IED Resistance. NPTs provide a significant advantage in combat scenarios, as they are resistant to punctures from landmines, improvised explosive devices (IEDs), and other hazardous materials. This improves survivability in hostile environments where traditional pneumatic tyres would be prone to failure.
-
Armoured personnel carriers (APCs). The goal is to reduce downtime in operations and ensure that vehicles can continue operating even in situations where tyres would typically be damaged.
-
-
Construction and Industrial Equipment
-
Skid Steers and Loaders. The construction industry has been one of the largest civilian sectors to adopt NPTs, particularly in skid steers, backhoes, and loaders. These machines often operate in environments filled with debris, sharp objects, and uneven terrain, where pneumatic tyres are prone to punctures. NPTs like the Michelin Tweel have been widely adopted in these sectors due to their durability, puncture resistance, and ability to handle heavy loads without risk of blowouts.
-
Forklifts. In industrial settings, such as warehouses and factories, forklifts are increasingly using NPTs. The consistent load-bearing capacity of NPTs, combined with their low maintenance, makes them ideal for operations where downtime due to tyre failure is costly.
-
-
Agriculture Tractors and Agricultural Equipment. Farmers and agricultural operations have started adopting NPTs for use in tractors, combine harvesters, and all-terrain vehicles (ATVs). Agricultural fields can be littered with sharp objects like stones or metal debris, making pneumatic tyres susceptible to frequent punctures. NPTs provide a reliable alternative, allowing continuous operation without the risk of tyre failure in the middle of critical work.
-
Autonomous Vehicles
-
Unmanned Ground Vehicles (UGVs). Autonomous systems and UGVs, especially those used in agriculture, mining, and security, are incorporating NPTs due to their need for long operational periods without human intervention. NPTs provide these vehicles with the reliability needed to function in remote or hazardous environments without frequent maintenance.
-
Robotics: Some robotic systems used in warehouses and distribution centers also employ NPTs. These robots require highly reliable tyres that can perform in various conditions without maintenance, making NPTs an ideal choice for autonomous logistic operations.
-
-
Off-Road Vehicles and Recreational Use
-
ATVs and Utility Terrain Vehicles (UTVs). The recreational and commercial off-road vehicle market is another area where NPTs are gaining traction. All-terrain vehicles (ATVs) and utility terrain vehicles (UTVs) used in outdoor activities such as farming, forestry, and recreation benefit from NPTs' durability and resistance to punctures. Manufacturers like Polaris have experimented with NPTs for off-road use, promoting their reliability in rugged terrain.
-
Emergency Response Vehicles. In areas prone to natural disasters, emergency response vehicles are using NPTs to ensure that they can continue operating during rescue missions, regardless of the terrain or obstacles in their way.
-
Public and Passenger Vehicles (Emerging)
-
-
Prototyping in Passenger Cars. While the widespread adoption of NPTs in passenger cars is still limited, companies like Michelin and Bridgestone have developed NPT prototypes for cars. Michelin has been actively working on the Uptis prototype, which is designed to be used in everyday passenger vehicles. Uptis is currently undergoing testing, with plans for potential market introduction within the next few years.
-
Sustainable Mobility. NPTs are being explored in the context of sustainable urban mobility, particularly in electric vehicles (EVs). As electric vehicles continue to grow in popularity, the reduced maintenance requirements of NPTs align well with the low-operating-cost model of EVs.
-
-
PROSPECTS OF NON-PNEUMATIC TYRES IN THE INDIAN MILITARY
The adoption of Non-Pneumatic Tyres (NPTs) holds significant potential for the Indian military, given the diverse and challenging terrains where military operations take place. The unique advantages of NPTs, including puncture resistance, durability, and low maintenance, make them ideal for deployment in environments ranging from the rugged Himalayan terrain to the Thar Desert and dense forests of the northeastern states. The ability to withstand harsh conditions without risk of punctures, deflation, or blowouts offers strategic advantages for improving the reliability and operational readiness of military vehicles. In particular, NPTs could be highly beneficial for the following Indian military applications:
-
Armoured Vehicles. The Indian militarys Armoured Personnel Carriers (APCs), Light Utility Vehicles could benefit from NPTs' durability, allowing continuous operations even in hostile environments where tyre damage could compromise mission success.
-
Border Patrol and Off-Road Vehicles. Border patrol vehicles operating in extreme terrains such as Ladakh, Siachen Glacier, and Arunachal Pradesh could benefit from the robustness of NPTs, eliminating downtime due to tyre failures in remote areas where repairs are difficult.
-
Unmanned Ground Vehicles (UGVs). The increasing use of UGVs in reconnaissance and combat support missions could be enhanced with NPTs, ensuring these systems can operate in rugged environments without requiring frequent maintenance.
-
Logistics and Support Vehicles. Supply and logistics vehicles transporting goods and troops over long distances could benefit from the reduced maintenance needs and increased reliability of NPTs.
-
-
STEPS FOR SUCCESSFUL ADOPTION
To ensure the successful integration of NPTs into the Indian military, several steps must be taken:
-
Comprehensive Testing and Trials. The Indian military should conduct extensive field trials of NPTs across various terrains, including high-altitude regions, deserts, forests, and urban environments. This would help assess their performance under Indian conditions, particularly in terms of load-bearing, shock absorption, and durability over long distances.
-
Development of India-Specific NPT Designs. Collaborating with global tyre manufacturers like Michelin, Goodyear, and Bridgestone, or fostering indigenous development through the DRDO, India could develop NPTs specifically tailored to the unique needs of the Indian military. These tyres would need to be customized for varying loads, off- road conditions, and weather.
-
Logistics and Supply Chain Integration. A reliable supply chain for NPTs needs to be established to ensure easy availability across all military sectors. This would include manufacturing partnerships and possibly local production to reduce dependence on imports and shorten response times for replacements.
-
Cost-Benefit Analysis. Although NPTs have a higher initial cost than traditional pneumatic tyres, the Indian military must conduct a thorough cost-benefit analysis considerig the long-term savings in maintenance, reduced downtime, and longer operational lifespan. This analysis would be crucial to justify the investment in transitioning to NPTs.
-
Training and Maintenance Infrastructure. Adoption of NPTs would require military personnel to be trained in handling, installing, and maintaining these tyres. Infrastructure for maintenance and support needs to be established across military bases, especially in remote areas where vehicles equipped with NPTs will operate.
-
Strategic Partnerships. The Indian military should explore strategic partnerships with tyre manufacturers and technology providers to foster continuous research and development. These partnerships could ensure that the latest advancements in NPT technology are made available for military use.
-
Policy and Procurement Support. Adoption of NPTs would require government support, including favourable policies and procurement processes. The Indian government could encourage the use of NPTs by including them in defence procurement plans and promoting research initiatives focused on developing next-generation military tyres.
-
-
CONCLUSION
The adoption of Non-Pneumatic Tyres in the Indian military presents a promising solution to the challenges of operating in diverse and extreme terrains. NPTs offer significant benefits in terms of durability, reliability, and reduced maintenance, all of which are crucial for mission-critical military operations. Although challenges remain, such as high initial costs, performance at high speeds, and limited availability, the potential for long-term cost savings and enhanced operational efficiency makes NPTs an ideal candidate for future military use.
-
The way ahead for NPTs in the Indian military involves a combination of extensive testing, India-specific design
development, indigenous manufacturing, and strategic partnerships with international manufacturers. With the right approach, NPTs can be successfully integrated into the Indian militarys vehicle fleet, significantly improving the operational capabilities and readiness of military forces, especially in remote and hostile environments. By addressing current challenges and continuing to invest in research and development, the Indian military can be at the forefront of adopting this innovative tyre technology, ensuring the safety, reliability, and mobility of its vehicles in the years to come.
REFERENCES
-
A Comprehensive Review of NPTs by Yaogi Deng,Yangzhou University, China, dt 11 Feb 23
-
3D Ultra Connected Airless Tyre Model by Sanka Choudhary, Bubaneshwar University, Orissa, dt 11 oct 21 .
-
Design, Optimization and Static Analysis of NPTs by Mrs Divya, Delhi Tech University, Delhi dt, 05 May 23.
-
Design and Fabrication of Airless and Tubeless Tyres by Mr Gaurav Kumar, Vidya College of Engg dt, 01 June 22.
-
Design and Fabrication of NPTs by Muhammad Ali, University of Taxila, dt 01 Jan 2022
-