
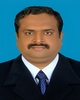
- Open Access
- Authors : Parthasarathy K , Dr. S Vijayaraj
- Paper ID : IJERTV9IS110214
- Volume & Issue : Volume 09, Issue 11 (November 2020)
- Published (First Online): 02-12-2020
- ISSN (Online) : 2278-0181
- Publisher Name : IJERT
- License:
This work is licensed under a Creative Commons Attribution 4.0 International License
An Overview of Battery Charging Methods, Charge Controllers, and Design of MPPT Controller based on Adruino Nano for Solar Renewable Storage Energy System
Parthasarathy K
Research Scholar, Department of EEE,
Vels Institute of Science, Technology &
Advanced Studies (VISTAS), Chennai, India.
Dr. S Vijayaraj
Assistant Professor, Department of EEE,
Vels Institute of Science, Technology &
Advanced Studies (VISTAS), Chennai, India.
Abstract–In this paper, a simple method battery charge controller is proposed and designed to protect the battery from over-charging and deep cycle discharges. The charge controller can adapt the MPPT technique for the photovoltaic(PV) power generation system, and the algorithm used is the Incremental Conductance (IC) algorithm. The process is controlled by the Arduino Nano board, which can find out the battery state and determine when the battery must complete the charging process. The state of the battery is perfectly controlled most of the time. The use of an Arduino Nano based on a microcontroller has been found correct to have adequate flexibility and simplify the hardware required (only a few external components used) by providing an intelligent tool to undertake programmed algorithm. The proposed charge controller system can control the solar-powered system. In the future, this type of solar-powered system will reduce the consumption of paid grid electric power, which will minimize cost, and power optimization would be good.
Keywords—Over-charging, algorithm, photovoltaic, Arduino Nano, optimization.
I. INTRODUCTION
Renewable energy sources are natural resources such as sunlight, wind, rain, tides, and geothermal heat. These resources are renewable and replenished naturally. Therefore, these sources can be utilized inexhaustible for all practical purposes, unlike dwindling conventional fossil fuels. The global energy crunch has provided a renewed impetus to the growth and development of Clean and Renewable Energy sources. Organizations are adopting CDMs all across the globe. Fossil fuels are rapidly decreasing globally. Another major factor working against fossil fuels is the pollution associated with their combustion. In contrast, renewable energy sources are much cleaner and produce energy.
Studies reveal that a solar panel converts 30-40% of energy incident on it to electrical energy. A Maximum Power Point Tracking algorithm is suitable for effective utilization of the solar panels. Various techniques for MPPT, such as Perturb and Observe (hill-climbing method, proposed in this paper), Incremental conductance, Fractional Short Circuit Current, Fractional Open Circuit Voltage, Fuzzy Control, Neural Network Control, etc. Out of these, Perturb and Observe (P&O), and Incremental conductance is used commonly because of their simple implementation, lesser time to track the MPPT, and several other economic reasons. Under abruptly changing weather conditions (irradiance level) as MPPT changes continuously, P&O takes it as a change in MPPT due to perturbation rather than irradiance and sometimes calculates the wrong MPPT. This problem gets avoided in the Incremental Conductance method as the algorithm takes two samples of voltage and current to figure MPPT. However, instead of higher efficiency, the algorithm’s complexity is very high compared to the previous one, and hence the cost of implementation increases. So we have to mitigate with a trade-off between complexity and efficiency. It has been observed that the efficiency of the system also depends upon the converter. Typically it is maximum for a buck topology, then for buck-boost topology, and minimum for a boost topology. It is straightforward to implement and has high efficiency both under stationary and time-varying atmospheric conditions.
Initially, photovoltaic solar panels have been designed and used mainly for space technology applications, and the production costs of such panels were also very high. As time passes, the photovoltaic cells were produced cheaper and cheaper, and their efficiency was also raised. This is also a reason why they are being used much more frequently, and it is not rare to see them on the rooftops anymore. Photovoltaic solar systems can be divided into two basic categories – grid-connected and off-grid solar systems. The grid-connected systems feed the electricity produced by solar panels to the grid using an inverter. When the electricity is needed during the night or periods with little sunlight, the energy is taken back from the grid. In off-grid systems, normally the excess electricity is usually stored in batteries during the day time, and the batteries are used to power the consumer appliances at times when photovoltaic panels do not have enough energy. Solar charge controllers play a vital role in isolated solar systems. Their goal is to ensure that the batteries are working in optimal conditions, mainly to prevent overcharging (by disconnecting solar panels when batteries are full) and too deep discharge (by disconnecting the load when necessary). The aim of this paper is to propose and suggest a solar charge controller that could control more lead-acid batteries at the same time.
The design is limited to lead-acid batteries, as they are currently the most preferable used type in isolated photovoltaic applications due to their high efficiency and excellent price per capacity compared with other battery types.
The energy infrastructure of India is relatively deficient, insufficient and inappropriately managed. The per capita
energy consumption of our country is 841 kWh. Access to affordable and reliable electricity is critical to a country’s growth and prosperity. Per capita, electricity consumption rose from merely 15.6 kWh in 1950 to 592 kWh in 2003-04. However, it is a matter of concern that the per capita consumption of electricity is among the world’s lowest.
Moreover, the low quality of power supply and frequent power cuts and shortages impose a heavy burden on India’s fast-growing trade and industry. Considering all these facts, we are motivated to do this project. It will be beneficial in every way for people who want to use renewable energy at affordable prices.
II. RENEWABLE ENERGY SOURCES
A. Wind power
Wind turbines generate electricity when airflows. Current day turbines range from around 600 kW to 5 MW of rated power. Since the power output is a function of the cube of the wind speed, it increases rapidly with an increase in available wind velocity. Recent advancements have led to aerofoil wind turbines, which are more efficient due to a better aerodynamic structure.
B. Solar power
The tapping of solar energy owes its origins to the British astronomer John Herschel who famously used a solar thermal collector box to cook food during an expedition to Africa. Solar energy can be used in two major ways. Firstly, the captured heat energy can be referred to solar thermal energy, with space heating applications. Another alternative is converting incident solar radiation into electrical energy, which is the most usable energy form. This method is achieved with the help of solar photovoltaic cells or by concentrating solar power plants.
C. Hydropower
Hydropower installations up to 10MW are considered as small hydropower and counted as renewable energy sources. These involve converting the potential energy of water stored in dams into usable electrical power through water turbines. run-of-the-river hydroelectricity aims to utilize the kinetic energy of water without the need to build reservoirs or dams.
D. Biomass
Plants capture the energy of the sun through the process of photosynthesis. On combustion, these plants release the trapped energy. This way, biomass works as a natural battery to store the sun’s energy and yield it on the requirement. 1.2.5 Geothermal Geothermal energy is the thermal energy which is stored within the layers of the Earth. The gradient thus developed gives rise to continuous conduction of heat from the core to the Earth’s surface. This gradient can be utilized to heat water to produce superheated steam and run steam turbines to generate electricity. The main disadvantage of geothermal energy is that it is usually limited to regions near tectonic plate boundaries, though recent advancements have led to this technology’s propagation.
III. BATTERY TYPES
A. Nickel Cadmium (Ni-Cd)
Nickel Cadmium (Ni-Cd) batteries were the standard technology for years, but today they are out of date, and new laptops don’t use them anymore. They are heavy and very prone to the “memory effect.” When recharging a Ni-Cd battery is not fully discharged, it “remembers” the old charge and continues there the next time when it is used. The memory effect is caused by the crystallization of the battery’s substances and can permanently reduce your battery’s lifetime and makes it useless. To avoid it, you should completely discharge the shower and then fully recharge it again at least once every few weeks. As this battery contains cadmium, a toxic material, it should always be recycled or disposed of properly.
B. Nickel Metal Hydride (Ni-MH)
Nickel Metal Hydride (Ni-MH) batteries are the cadmium-free replacement for Ni-Cd. They are less affected by the memory effect than Ni-Cd and thus require less maintenance and conditioning. However, they have problems at very high or low room temperatures, and even though they use less hazardous materials (i.e., they do not contain heavy metals), cannot be fully recycled. Another main difference between Ni-Cd and Ni-MH is that Ni-MH battery offers higher energy density than Ni-Cad. In other words, the capacity of a Ni-MH is approximate twice the capacity of its Ni-Cd counterpart. What this means for you is increased run-time from the battery with no additional bulk or weight.
It can store 100 watt-hours per kg. They are more thermally stable than lithium-ion batteries. The self-discharge is higher than the other batteries.
At
Anode
Ni(OH)2(s) + HO-(aq) Ni(O)(OH) + H2O + e-
E0= 0.49 V
At Cathode
M(s) + H2O + e- MH(s) + HO-(aq)
E0= 0.83 V
Table 1. Ni-MH electrode equations
C. Lithium-Ion (Li-ion)
Lithium-Ion (Li-ion) is the new standard for portable power. Li-ion batteries produce the same energy as Ni-MH but weigh approximately 20%-35% less. They do not suffer significantly from the memory effect, unlike their Ni-MH and Ni-Cd counterparts. Their substances are non-hazardous to the 0. Because lithium ignites very easily, they require special handling. Unfortunately, few consumer recycling programs are already existing for Li-ion batteries at this point.
D. Lead Acid Battery
These batteries are most commonly used in automobiles and used to store solar energy because they can provide high current, and their cost is relatively low. They hold only about 25 watt-hours per kg. Each cell consists of lead electrodes in a sulfuric acid solution. Electrodes are made out of the lead and coated with lead oxide. Connecting 6 of these cells in series gives a 12 V battery.
Deep cycle batteries have thicker electrodes than the standard starter batteries. Gel batteries and sealed lead-acid batteries are preferred commonly to store solar electric energy for off-grid applications. About 93% of lead-acid battery is recycled to make new Lead-Acid batteries.
The self-discharge characteristic of the lead-acid battery is relatively high. At a normal room temperature of 20°C, the self-discharge rate is around 3% per month. Theoretically, a lead-acid battery can be stored for up to 12 months without a recharge. However, at higher temperatures, the self-discharge is more increased. At 30°C, the self-discharge increases, and recharge will be needed every six months so that it will not let the battery drop below 60% for some time causes sulphation.
IV. CHARGING METHODS
A. Constant Voltage Charging
This method is the standard method, which is used for charging the lead-acid battery because it reduces the total charging time and increases the capacity by up to 20%. But this method reduces efficiency by 10% approximately. In this method, the charging voltage is kept constant throughout the charging process. The charging current is high in the beginning when the battery is in the discharge condition. The current value is gradually dropping off as the battery picks up charge resulting in an increase back emf.
Figure 1. Constant voltage method
The advantages of charging at constant voltage are that it allows cells with different capacities and ensures different degrees of discharge to be charged. The large charging current at the beginning of the charge is of relatively short duration and will not harm the cell. At the end of the charge, the charging current drops to almost zero because the voltage of the battery becomes nearly equal to the voltage of the supply circuit.
B. Constant Current Charging
In this method of charging, the batteries are connected in series so as to form small groups, and each group charges from the DC supply mains through-loading rheostats. The charging in each group depends on the charging circuit voltage, which should not be less than 2.7 V per cell.
The charging current is kept constant throughout the charging period by reducing the circuit’s resistance as the battery voltage goes up. In order to avoid excessive gassing or overheating, the charging may be carried out in two steps, an initial charging of approximately higher current and a finishing rate of low current.
Figure 2. Constant current method
In this method, the charge current is approximately one-eighth of its ampere ratings. The excess voltage of the supply circuit is absorbed in the series resistance. The groups of the battery to be charged should be so connected that the series resistance consumes as little energy as possible.
The current carrying capacity of series resistance should be greater than or equal to the required charging current; otherwise, the opposition will overheat and burn out.
The group of batteries which is to be selected should have the same capacity. If the battery has a different ability, then it will have to be set according to the least power.
C. Mixed constant current / constant voltage charging method
It is known from the above that the constant voltage and constant current charging methods have their own advantages and disadvantages. In order to improve the shortcomings of the two methods, a constant current / constant voltage charging method is proposed. This charging method can significantly reduce the charging time, and it also has the function of self-regulating current with a constant voltage charging method and does not cause the battery to overcharge.
As shown in the figure below, the constant current mode is used at the beginning of charging. Since the battery accepts higher current when the battery is low, most of the energy released can be quickly replenished. When this mode continues until the battery voltage reaches. When the voltage is set, the charger will switch to the constant voltage mode to continue charging. At this time, it is called the equalization mode. After the battery is fully charged, the charger will automatically switch to the floating mode to keep the battery fully charged.
Figure 3. Mixed constant current / constant voltage charging method
D. Pulse charging method
The pulse charging method charges the battery with a periodic pulse current. As shown in the figure, this method can make the electrolyte more uniform in the battery during this period because there is a time to stop charging. The energy of charging can be fully converted into electrical energy by chemical energy, so the charging efficiency is higher than the above method.
Figure 4. Pulse charging method
E. Float charging method
Float charging is the most commonly used method for backup and emergency power applications, where the battery’s discharge is not frequent. During the process of float charging, the charger, battery, and load have to be connected in parallel. The charger operates off the standard power supply, which provides current to the load during operation. In the event of a typical power supply failure, the battery provides backup power until the regular power supply is back. Since most of the equipment requires alternating current, a rectifier circuit is usually added between the battery and the load. Operating the charger at a low voltage, generally, less than about 2.4 V per cell, keeps the charging current low and minimizes the damaging effects during high-current overcharging.
For valve-regulated acid batteries, when float charging is in process, the rate of internal heat generation exceeds the rate at which the heat can be expelled, and this phenomenon is called “thermal runaway.” The best way of preventing thermal runaway is through the use of a temperature-compensated battery charger. A temperature-compensated charger adjusts the float voltage based upon battery temperature. Temperature-compensated chargers will increase the reliability and prolong the life of the battery/charger system. They are especially useful for batteries located in areas where temperatures may be significantly above ambient conditions.
Figure 5. Float charging method
V. CHARGE CONTROLLER METHODS
A. Simple On/Off charge controller
It has shunt transistors to control the voltage in one or two steps. This controller shorts the solar panel when a specificvoltage has arrived. Their genuine primary fuel for keeping such a notorious reputation is their unwavering quality, and they have so many segments, there is very little to break.Figure 6. Simple On/OFF Charge Controller
Figure 6. Simple On/OFF Charge Controller
B. PWM charge controller
PWM controllers are similar to series regulators, they use a transistor instead of a relay to open the array. By switching the transistor at a high frequency with various modulated widths, a constant voltage can be maintained. The PWM regulator self-adjusts itself by varying the widths (lengths) and speed of the pulses sent to the battery. Unlike the on/off charge controllers, which instantaneously cut off the power transfer to minimize battery overcharging, PWM regulators act as a rapid on/off controller constantly.
When the width is at 100%, the transistor is at full ON, allowing the solar array to bulk charge the battery. When the width is at 0%, the transistor is OFF open, circuiting the array preventing any current from flowing to the battery when the battery is fully charged.
Like the series regulator, the transistor can be placed in either the positive or negative line, allowing the regulator to be used in positive and negative ground systems. The difference between the series regulator and the PWM regulator is the PWM of the transistor. When the modulation
width is at 100% or 0%, the regulator is essentially a series regulator. It is that modulation width variation that allows the PWM regulator to create a constant voltage to the battery as opposed to the on/off of the series regulator.
Figure 7. PWM Controller Schematic
Some PWM regulators have provisions for converting it into a series (on/off) regulator. This could be needed for sensitive loads, which have an issue with the noise created by the frequency of the PWM. Because PWM charge controllers require transistors, they are always solid-state; this means heat dissipation can become a problem, especially in larger solar arrays. Figure 7. PWM controller current to battery for a given duty cycle.
C. MPPT charge controller
Background
The average power given to the batteries equals the average charging current times the battery voltage which is fairly constant. Thus in order to maximize the power output of the solar panel using MPPT, it is enough to maximize the average charging current of the battery. Solar panels are non-linear sources of power. Figure below shows the output current and voltage (I-V curve) for a particular intensity of light falling on the solar panel.
The power output at a point Pm is the product Po=Vm*Im.MPPT is about finding the point at which the power output is maximum. This normally occurs on the knee of the curve. Fig shows how the I-V curves vary with the intensity of light falling on the panel and also on the temperature of the cell. It is also called a hill climbing technique. To the left of the peak in the P-V curve, the operating voltage is increased and to the right side, the voltage is decreased. This results in the operating point to oscillate about the peak power point.
Figure 8. MPPT charging method
1. Trickle charge – 1o stage (from T0 to T1)
This first stage is active when the battery voltage is below the value VCHGENB. This voltage value, specified for the manufacturers, shows that the battery arrives at its critical discharge capacity. In this condition the battery should receive a small charge current defined by ITC that has a typical value of C/100 where C is the normal battery capacity with a 10 hours charging process. This small current ITC is applied until the battery voltage reaches the value of VCHGENB. This stage also avoids that some accident could happens in the case of the one battery element is in curt circuit, therefore if this really happens the battery voltage will not grow and then the battery charging process does not pass to the next stage.
2. Bulk charge – 2o stage (from T1 to T2)
After the battery voltage reaches the value VCHGENB it should be applied to the battery a constant current IBULK. The IBULK is the maximum charge current that battery supports without a big water losing, and its value is specified by the manufacturers. This current is applied until the battery voltage reaches the maximum value of over charge voltage, defined by VOC, and also specified by the manufacturers. In this stage the prototype implemented board will run the P&O MPPT algorithm but the IBULK is never exceeded. The maximum power of the PV panel should be correctly chosen.
3. Over charge – 3o stage (from T2 to T3)
During this stage the control algorithm should regulate the battery voltage VOC until the complete charge has been reached. When the charging current fall down to a pre-established value IOTC and the voltage stays in the value VOC, the charge process should go to the next, and final, stage. The value of IOCT is around 10% of the IBULK.
4. Float charge – 4o stage (from T3 until the end)
In this stage the control algorithm will apply to the battery a constant voltage VFLOAT which is specified by the battery manufacturers. This voltage is applied to the battery with the objective of avoiding its auto-discharge. During the discharging process the battery voltage will fall down and when it reaches 0.9 VFLOAT the control algorithm will execute again the 2o stage providing the IBULK current. The control algorithm only returns to the 2o stage if the PV panel is capable of delivering energy. If it is not the case the battery will continue the discharge process. If the voltage goes below the value VCHGENB the control algorithm should restart the charging process in 1o stage as soon as the PV panel is capable of delivering energy. In this work some simplifications have been introduced in the implementation of the four different charging stages of a lead-acid battery.
Figure 9. Stages of Charging
VI. SYSTEM DESCRIPTION
The Solar Panel is a device, which converts light energy into electricity. The MPPT charge controller is the circuit combining sensors, buck converter, and switches, which is used to maintain the battery at the highest possible state of charge,and when it is fully charged, it detaches the battery and
Figure 10. System Block Diagram
enables the drain of solar power to a connected load.
The battery is a storage device that stores the charge from the solar panel for future use. We are using a Lead-Acid type of battery.
Figure 11. Block Diagram
A. HARDWARE SPECIFICATIONS
1. Arduino NANO
The Arduino Nano is a small, complete, and breadboard-friendly board based on the ATmega328 (Arduino Nano 3.x). It has more or less the same functionality as the Arduino Duemilanove but in a different package. It lacks only a DC power jack and works with a Mini-B USB cable instead of a standard one. Nano has six analog input pins and 14 digital I/O pins, of which five are dedicated PWM pins.
Figure 12. Arduino NANO board
2. Current Sensor ACS712
ACS712 is a Hall current sensor. Current from the 250-watt solar panel is fed to the IP+ terminal of the current sensor ACS712, and an output signal from it is fed to the A1 pin of Arduino nano through an LC current filter.
Figure 13. Current Sensor ACS712
3. IRFZ44N MOSFET (switching device)
The IRFZ44N is an N-channel MOSFET with a high drain current of 49A and a low Rds value of 17.5 mΩ. It also has a low threshold voltage of 4V at which the MOSFET will start conducting. Hence it is commonly used with microcontrollers and MOSFET drivers to drive with 5V.
Figure 14. IRFZ44N Pinou
4. IR2104 MOSFET Driver
A Microcontroller cannot turn on a MOSFET as it cannot supply enough current to charge the MOSFET because the gate of the MOSFET is capacitive in nature. That is why a MOSFET driver is required. The driver itself will supply the current that the MOSFET will need. As we are using a buck converter, the PWM signal will be applied with respect to the
Figure 15. IR2104 Connection diagram
respect to the MOSFET source. That is why the MOSFET driver will also provide ground isolation capability so that the source of the MOSFET and ground are not shorted. WE have used two optocouplers to form the driver. The advantage of this driver is that it is cheap compared to the available pull-up driver in the market. Moreover, it compensates for dead time, and the two MOSFETs will never be turned on together. This decreases the cost of the circuit further.
5. Pulse width modulation technique
The PWM technique is used to sway the digital output signal by switching it on and off very rapidly, just by differing the width of the on/off duration is going to affect outputs.
VOUT = TON/ (TON+TOFF)*VIN
PWM is authorized to provide a wide span of digital output at a distinct power floor, which is indistinguishable to analog outputs. This technique is used to control the MOSFET driver and, in turn, is used to switch on the three MOSFETs in the circuit. It is also used in the buck converter circuit.
6. Buck Converter
A buck converter (step-down converter) is a DC-to-DC power converter that steps down voltage (while stepping up current) from its input (supply) to its output (load). In our case, the load is the battery and the input is the Solar panel voltage.
Figure 16. Buck Converter schematic
7. IC7605 Voltage Regulator
IC7605 is a low-drop 5V regulator well suited to supplying stabilized voltage to microprocessors in harsh industrial environment.
Pin
Pin
Function
Description
1
V1
Input voltage
(<30V)
In this pin of the IC positive unregulated voltage is given in regulation.
2
V2
Ground
(0V)
The output of the regulated 5V volt is taken out at this pin of the IC regulator.
3
GROUND
Regulated output;
5V
(4.875 V-5.125 V)
In this pin where the ground is given. This pin is neutral for equally the input and output
Table 2. Pins of LM7805
B. CHARGING ALGORITHM
1. MPPT Algorithm
2. LED indicator
Our charge controller comes with an LED indicator to indicate the charging state of the battery. As mentioned earlier, we used a 12V Lead-Acid battery, and the LED will indicate a different charging state by illuminating different colors. The LED indication for different level is given below state of charge 12V battery.
100%
14.5
green
90%
14
green
80%
13.5
yellow
70%
13
yellow
60%
12.75
yellow
50%
12.50
yellow
40%
12.25
yellow
30%
12
Red
20%
11.8
Red
10%
11.4
Red
0%
11
Red
Table 3. Battery State Of Charge indication using LEDs
The green light indicates that it is fully charged, the yellow light indicates that it medium charged, and the red light indicates it is low charged and needs to be charged.
VII CIRCUIT DIAGRAM
9. IMPLEMENTATION AND OBSERVATIONS
9.1 Circuit design
Figure 16.a Circuit diagrm
Implementation and Observation
Circuit Design
Figure 16.b Circuit diagram
1. Implementation and Observation
Circuit Design
Figure 17.. Proteus circuit diagram
Figure 18. Hardware Prototype
Figure 19. Output on the LCD of the solar charge controller
2. Sample set of reading
Panel voltage
Panel current
Panel power
13.14 v
0.16 A
2.1 W
Battery voltage
State
Percent charged
12.60
ON
90%
Type of signal provided
State of load
PWM
OFF
Table 4. Set of readings
VIII. CONCLUSION
The realization of this solar charge controller using Arduino was done at low cost but effective for small DC loads, and we can use this controller to implement other algorithms or to make comparisons. This paper explains a battery charging system for the laboratory using a direct connection between the Solar panel and the battery system. With the help of this charge controller, we used solar power effectively and prolonged battery lifetime. In this paper, we have presented the experimental results using the LCD display (panel power, current, voltage, and state of charge of the battery, state of load, percentage of PWM, etc.).
REFERENCES
[1] W. Makni, N. Ben hadj, H.Samet, R.Neji, Design simulation and realization of solar battery charge controller using Arduino Uno, a17th international conference on Sciences and Techniques of Automatic control & computer engineering – STA’2016, Sousse, Tunisia, December 19 – 21, 2016.
Electrical Machines and Systems, Beijing, 2011, pp. 1-6, DOI: 10.1109/ICEMS.2011.6073783.
[10] A. M. Rahimi, “A lithium-ion battery charger for charging up to eight cells,” 2005 IEEE Vehicle Power and Propulsion Conference, Chicago, IL, 2005, pp. 6 pp.-, DOI: 10.1109/VPPC.2005.1554545. [11] J. Ripley, M. T. Ansari, and J. Dehn, “Battery chargers and batteries for DC and AC back-up power systems,” Record of Conference Papers. IEEE incorporated Industry Applications Society. Forty-Eighth Annual Conference. 2001 Petroleum and Chemical Industry Technical Conference (Cat. No.01CH37265), Toronto, Ontario, Canada, 2001, pp. 139-144, DOI: 10.1109/PCICON.2001.960534. [12] H. A. Serhan and E. M. Ahmed, “Effect of the different charging techniques on battery life-time: Review,” 2018 International Conference on Innovative Trends in Computer Engineering (ITCE), Aswan, 2018, pp. 421-426, DOI: 10.1109/ITCE.2018.8316661. [13] S. G. Tesfahunegn, O. Ulleberg, T. M. Undeland, and P. J. S. Vie, “A simplified battery charge controller for safety and increased utilization in standalone PV applications,” 2011 [14] International Conference on Clean Electrical Power (ICCEP), Ischia, 2011, pp. 137-144, DOI: 10.1109/ICCEP.2011.6036367. [15] A. Musa, L. H. Pratomo and F. Y. Setiono, “Design and implementation of solar power as battery charger using incremental conductance current control method based on dsPIC30F4012,” 2014 The 1st International Conference on Information Technology, Computer, and Electrical Engineering, Semarang, 2014, pp. 324-327, DOI: 10.1109/ICITACEE.2014.7065765. [16] F. Boico, B. Lehman and K. Shujaee, “Solar Battery Chargers for NiMH Batteries,” in IEEE Transactions on Power Electronics, vol. 22, no. 5, pp. 1600-1609, Sept. 2007, DOI: 10.1109/TPEL.2007.904164. [17] H. A. Serhan and E. M. Ahmed, “Effect of the different charging techniques on battery life-time: Review,” 2018 International Conference on Innovative Trends in Computer Engineering (ITCE), Aswan, 2018, pp. 421-426, DOI: 10.1109/ITCE.2018.8316661. [18] P. K. Atri, P. S. Modi, and N. S. Gujar, “Comparison of Different MPPT Control Strategies for Solar Charge Controller,” 2020 International Conference on Power Electronics & IoT Applications in Renewable Energy and its Control (PARC), Mathura, Uttar Pradesh, India, 2020, pp. 65-69, DOI: 10.1109/PARC49193.2020.236559. [19] S. S. Valunjkar, S. D. Joshi and N. R. Kulkarni, “Hardware and simulation study of MPPT charge controller for non-conventional energy sources,” 2015 International Conference on Industrial Instrumentation and Control (ICIC), Pune, 2015, pp. 529-534, DOI: 10.1109/IIC.2015.7150799. [20] W. Makni, N. Ben hadj, H.Samet, R.Neji, Design simulation and realization of solar battery charge controller using Arduino, a 17th international conference on Sciences and Techniques of Automatic control & computer engineering- STA’2016, Sousse, Tunisia, December 19-21, 2016. [21] N K. M’Sirdi, B. Nehme, M. Abarkan, A. Rabhi, The Best MPPT Algorithms by VSAS approach for Renewable Energy Sources (RES), conference paper EFEA 2014, PARIS. [22] N. Barua, A. Dutta, S. Chakma, Implementation of Cost- effective MPPT Solar PV System Based on the Comparison between Incremental Conductance and P&O Algorithm, WIECON-ECE 2016, India. [23] A. Chandwani, A. Kothari, Design, Simulation and Implementation of Maximum Power Point Tracking (MPPT) for solar-based Renewable Systems, ICEPES Dec 14-16, 2016. [24] T. Kaur, J. Gambhir, S. Kumar, Arduino Based Solar Powered Battery Charging System for Rural SHS, Power ElectronicsIICPE), 7th (IICPE), 7th 2016 India