
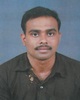
- Open Access
- Authors : Asegid Tadesse , Selva Ganesh
- Paper ID : IJERTV9IS090317
- Volume & Issue : Volume 09, Issue 09 (September 2020)
- Published (First Online): 05-11-2020
- ISSN (Online) : 2278-0181
- Publisher Name : IJERT
- License:
This work is licensed under a Creative Commons Attribution 4.0 International License
An Overview on Metal Matrix Composite Processing and Al7075 based Mechanical Properties
Asegid Tadesse1, Selva Ganesp
Lecturer, Institute of Technology, Department of Mechanical Engineering, Wollega University, Ethiopia.
Assistant Professor, Institute of Technology, Department of Mechanical Engineering, Wollega University, Ethiopia.
Abstract : – Demands have been increased towards the result of lighter and energy-efficient materials for current development of the world. Metal matrix composite is the best selected materials for research during this time due to the benefits of matrix and reinforcement combinations. For the combination matrix and reinforced materials, there is a series need of combination techniques. The techniques often classified in to two types liquid and solid state processes. The most typical techniques for the production of liquid state processing materials are stir-casting techniques. Comparatively, it is simple and cost effective and provides a fairly uniform distribution of particles. This paper shows a direction for the assembly of metal matrix composite in the development of highly effective and improved properties using simple and effective techniques of productions. There are a various ways of production of MMCs. Friction stir casting, compo-casting, squeeze casting spray casting etc. are a class of routs of metal matrix composite. The addition of reinforcement in Al7075 improves specific strength, tensile, hardness and other properties of aluminium alloy
.researchers shows, experiments with adding reinforcement material using diverse techniques of production which they are finding results for the event of material technology. This paper shows the rout of metal matrix composite production it evaluates the mechanical properties of Al7075.
Key words: MMC, Metallurgy, stir casting, Matrix, and Reinforcement
INTRODUCTION
A metal matrix composite contains a metal or an alloy because the continual matrix and reinforcement which can be a particle, short fiber or whickers or continues fiber for the
assembly of enhanced properties of materials (K.KChawla, 2012). The use of composite materials is only realized when there is a cheap cost versus performance relationship within the component production. Currently, having strong fibers, continuous or non-continuous surrounded by a weaker matrix material are needed in the development of materials. There are three kinds of metal matrix composite. Particle reinforced, short fiber or whickers reinforced, continuous fiber sheet reinforced metal matrix composite. The characteristics are determined by their microstructure and internal surface, which are affected by their production and thermal- mechanical properties. It covers the structure of the matrix and thus the reinforced phase. Local varying internal tension or because of the varied thermal expansion behavior of the two phases may be a further influencing factor. MMCs are found in many areas of the application. The progress within the event of sunshine metal matrix composite has been achieved in recent decades so as that they could be introduced into the foremost important application. Within the automotive industry, metal matrix composite are used commercially in fiber-reinforced piston and aluminium crankcase with strengthened cylinder surface also as particle strengthened brake disks. The advancement of metal matrix composite for light metal composite materials is: increased in yield strength and lastingness at temperature and above while maintaining the minimum ductility or rather toughness, increase in fatigue strength, especially at higher temperature compared there to of conventional alloys, increases in fatigue strength, especially at higher temperature, improvement of thermal elongation. The classification is on the consideration
of type and contribution of reinforcement component in particle layer, fiber and penetration of composite materials. Fiber composite materials are offen further classified in to continuous fiber composite materials and short fiber or rather whiskers composite materials (Kainer 2006).
Figure 1:Development curve of the market for modern materials(Kainer, 2006)
Figure 2:Schematic presentation of three shapes of metal matrix composite materials(Kainer, 2006)
Al7075 has good strength, higher toughness, and are chosen in the aerospace and automobile part (Muzakkir, 2014). Due to their strength, fracture toughness, wear-resistance and stiffness, the composites formed out of aluminum alloys are of wide interest. Further, these composites are superior in nature for elevated temperature applications when reinforced with ceramic particles (C. Saravanan, 2015).
Processing of Metal Matrix Composites:
The primary function of the matrix in composite materials is to transfer the stress between the reinforcing fibers and protect the fibers from mechanical damage. A basic
requirement for a matrix materialis that its strain at break must be larger than the fibers it is holding. From the production of metal matrix composite,liquid and solid-state of production are the popularly known routs. The selection of the appropriate process has a great role in the quantity and distribution of the reinforcement components, the matrix alloy, and the application.The production of metal matrix composite can be reached by the addition of the reinforcement phase to the matrix.Through varying manufacturing method, the finishing and the form of the reinforcement components, it is possible to gain diverse characteristic profiles, although the same composition and amounts of the components. In the strengthen mechanisms of the materials, the reinforcing particles are injected into a solid or liquid matrix either by powder metallurgy technique or through a liquid metallurgy route by casting or any other methods. In general, metal matrix composites are fabricated by the addition of a reinforcement phase to the matrix, using one of the following routs like powder metallurgy processing, spray atomization and co-deposition, plasma spraying, stir casting, and squeeze-casting.
Liquid phase processing techniques
From the two mostly known productions process of metal matrix composites, liquid phase processing techniques is the one and researcher are selected for the study. The composite production practice is an important consideration for all composite and hybrid materials. Liquid state fabrication of MMC involves incorporation of dispersed phase in to a molten matrix metal followed by its solidification. In the formation of MMCs, the key success is the proper bonding between the matrix and the reinforcement in order to manage the load transfer between phases. Here, when the continuous phase (metal matrix) is in a liquid state, then the discontinuous phase (reinforcement) is incorporated into it. Then, the molten metal in the liquid state is cast into various molds of desired shapes by conventional casting. For a given set of constituents, the fundamental link between properties and cost is determined by the fabrication method. Not all combinations of reinforcement and matrix are compatible and many cannot be processed into commercially useful composites. The main processes under this category are as follows:
Stir casting
Stir casting is a liquid state method for the fabrication of composite materials in which a dispersed phase is mixed in to with a molten matrix metal by means of mechanical stirrer. It is the simplest and the most cost effective methods of liquid
state fabrication. The processwas came into existence in 1968 through S. Ray, when he stirred the molten aluminum alloy by incrporating alumina ceramic powder particles into the aluminum melt. And the discontinuous reinforcement phases are incorporated into matrix when the matrix is in molten form by a mechanical stirrer. Rotation speed, speedstirring, stirring temperature, reinforcement pre-heat temperature, stirring time, pouring temperature, mold temperature is variable parameters to be considered while preparing the metal matrix composite by stir casting (Gowri Shankar, 2013.). The distribution of the reinforcement in the final solid depends on the wetting condition of the reinforcement with the melt, relative density, rate of solidification, etc. microstructure and the bonding of the matrix and reinforcement is basically depends of the distribution of the reinforcement. So it is depends on the geometry of the stirrer, melt temperature, and the position of the stirrer in the melt. The following figure shows a schematic diagram of the stir casting process.
Figure 3: stir casting
An improvement in conventional stir casting is a double stir casting method or two-step casting process. Comparatively, from the types of liquid phase processing of metal matrix composites, stir casting is carefully chosen and better for researchers for the performance of the newly invented materials.
Infiltration:
Various methods can be applied for production of metal matrix composite using infiltration method. However, four majors methods are widely used, namely spontaneous infiltration, squeeze casting infiltration, gas pressure infiltration and centrifugal infiltration.
The second method for the fabrication of metal matrix composite in liquid phase processing techniques is infiltration. Here, the formations of the materials are using
dies. The reinforcement are arranged as perform and placed inside the die and liquid metal is poured over it. The pore of performing is either by atmospheric or by vacuum pressure. Unlike to the stir-casting process where the reinforcements are free to float or settle in the melt, the reinforcements do not have the freedom to move in the infiltration processes because of the die. The liquid metal enters between the fibers or particles during infiltration; it cools and then solidifies, producing a composite. The following figure shows the formation of the composite during the infiltration of a fiber preform by liquid metal.
Figure 4:Infiltration process
Gas Pressure Infiltration:
Gas pressure infiltration is a forced infiltration method of liquid phase fabrication of metal matrix composites using a pressurized gas for applying pressure on the molten metal and forcing it penetrate in to a performed dispersed phase. It is a forced infiltration method of liquid phase fabrication of metal matrix composites, different to atmospheric or vacuum pressure using a pressurized gas in applying pressure on the molten metal and forcing it to penetrate and for the preformed dispersed particle. In this method the mold and perform are kept at a temperature close to the melting point of the metal; this gives the metal-free to flow and fill the mold without choking. The following figure shows the gas pressure infiltration of the fabrication of metal matrix composites.
Figure 5: Gas Pressure Infiltration Process
It is used for manufacturing large composite parts. The methods allow using non-coating fibers due to short contact time the fibers with the hot metals.
Squeeze Casting Infiltration:
It is a forced infiltration of liquid phase fabrication of metal matrix composite using movable mold part for applying pressure on the molten metal and forcing it to penetrate into a performed dispersed phase placed in to the lower fixed mold part as gas pressure infiltration however instead of using gas pressure using a movable mold part (ram) for applying pressure on the molten metal and forcing it to penetrate into a performed dispersed phase, placed into the lower fixed mold part. It is similar to the squeeze casting techniques used for metal alloys casting. The following figure shows the squeeze casting infiltration process.
Figure 6: Squeeze casting infiltration process Pressure Die Infiltration:
This technique is forced infiltration method of liquid phase fabrication of metal matrix compositesusing a die casting technology. In this method a preformed dispersed phase (particles, fibers) is placed into a die (mold) which is then filled with a molten metal entering into the die through a sprue and penetrating into the perform under the pressure of a movable piston (plunger). The following figure shows the Pressure die infiltration process.
Figure 7:Pressure dies infiltration process
Diffusion Bonding
It is a technique which employs the solid state diffusion of atoms as a main process for the development of a joint.It is a practice by which two nominally flat interface can be joined at an elevated temperature using an applied pressure for a time ranging. The method is used for fabrication of simple shape parts like plates or tubes. The principal advantage of this technique is the ability to route a wide variety of metal matrices and control of fiber orientation and volume fraction.
Figure 8: Diffusion bonding process
Solid-phase fabrication methods
It is a process where metal matrix composite are formed as a result of bonding matrix metal and dispersed phase due to mutual diffusion occurring between them in solid state at elevated temperature and under pressure. The following points are under the solid phase fabrication methods.
Powder Metallurgy
Powder metallurgy covers a wide range in materialsthat are made from metal powders. It reduce the need to use metal removal processes, thereby severely reducing yields losses in manufacturer and often resulting in lower cost. This process is consists of, powder manufacture, powder mixing or blending, compacting, and sintering. The process is in the conversion of the matrix metal and dispersed phase into a fine powder, then it comes toblending (it is the powder of matrix metal is mixed with a powder of dispersed phase) then
shaping and finally it comes to sintering are the basic procedure of the method.
Friction stirs processing:
These methods arean effective and capable technique that can be used to improve microstructure and to make metal matrix composites. This process is settled based on the principle of friction stir welding that locally handle the microstructure by imparting a high level energy in the solid state resulting in improved mechanical properties. In friction stirs processing, the composites are manufactured when the matrix is in solid- state condition.
In-situ of Metal Matrix Composites:
In this method the reinforcing phase is prepared in the matrix as a result of precipitation from the melt during its cooling and solidification. One of the reacting elements is usually a constituent of the molten matrix alloy. The other reacting elements may be either externally-added fine powders or gaseous phases. The final reaction product is the reinforcement homogeneously dispersed in the matrix alloy. This kind of internally-produced reinforcement has many desirable attributes. However, the method requires that the reaction system be carefully screened.
Vapor State Processing
Physical vapor Deposition processes are relatively slow, but the fastest is evaporation involving thermal vaporization to the target species in a vacuum. Composite fabrication is usually completed by assembling the coated fiber into a bundle and consolidating in a hot-pressing operation.Coating processes are primary processes that coat the matrix onto individual reinforcement elements of the ingredient material
i.e. vapor deposition, or electrolytic coating creating composite elements, that require subsequent consolidation. It is may be a primary process wherein the matrix deposited from the vapor phase onto individual reinforcement elements of the ingredient. A very uniform distribution of fibers produced in this way, with fiber contents of up to about 80%. The fiber volume fraction accurately controlled through the thickness of the deposited coatings and therefore the fiber distribution is usually very homogeneous.
While Electrolytic coating is a primary process wherein the matrix deposited from solution using electrochemical means onto individual reinforcement elements of the ingredient material.
Porosity in metal matrix composites
The volume fraction of porosity and its size and distribution in a cast metal matrix composite play an important role in controlling the material's mechanical properties (j.Hashine, 1999). This kind of a composite defect can be detrimental also to the corrosion resistance of the casting. Porosity cannot be fully avoided during the casting process, but it can be reduced through different mechanisms. Porosity arises from the gas entrapment during mixing, hydrogen evolution, and shrinkage during solidification. According to (P.K. Ghosh S. R., 1988), the process parameters of holding times, stirring speed, and the size and position of the impeller will influence the development of porosity. From the study of parker, has been recommended that a turbine stirrer should be placed so as to have 35% liquid below and 65% liquid above (Parker. 1964). And according to Lloyd (D.J. Lloyd, 1989) and (M. Samuel, 1989), structural defects such as porosity, particle cluster, oxide inclusions, and interfacial reaction are found to arise from unsatisfactory casting technology. From many observations, the amount of gas porosity in casting depends more on the volume fraction of inclusions than on the amount of dissolved hydrogen (K.J. Brondyke, 1964). It observed that the porosity in cast composites increases almost linearly with particle content. For the reduction of porosity, the parameters of the matrix and the reinforcement are highly recommended. In composite materialsthe porosity isfrom air bubbles entering the slurry either independently or as an air envelope to the reinforcement particles (P.K. Ghosh S. R., 1984). In the experimental work of (K. Miwa, 1990), it was found that the evolution process of H2O gas relying on temperature is mostly finished at temperatures between 200 and600oC.
Figure9:the different stages of particle pushing and pore formation in silicon carbide reinforced composites during solidification (L. Lajoye, 1987).
Most of the H2O gas absorbed on the surface of the particles can be liberated by treatment with isothermal heating at 6000C. The affinity of aluminum for oxygen leads to a reduction of the surrounding water vapor and the formation of hydrogen, which is readily dissolved in liquid aluminum.
The nucleation and growth of pores during the solidification of A356/SiC particle reinforced composites (L.Lajoye,1987).The occurrence of porosity can be attributed variously to the amount of hydrogen gas present in the melt, the oxide on the surface of the melt that can be drawn into it at any stage of stirring and therefore the gas being drawn into the melt by certain stirring methods. Degassing liquid aluminum alloy is a usual step in the casting procedure. When reinforcement materials are incorporated into a melt in air, the molten compound must be treated to get rid of the dissolved gas.
Degassing is carried out in a vacuum chamber. At the top of the degassing step, the formation of bubbles is enhanced by an injection of nitrogen gas. The application of vacuum to the molten mixture of metal and particles during the mixing step can reduce the atmospheric gases available for introduction into the melt, and also draw dissolved, entrapped, and collected gases out of the melt during mixing. Solidification shrinkage arises as a result of incorrect mold temperature and incorrect gating systems. It observed that increasing the mold temperature will improve the soundness of the casting, as shown by a decrease in the porosity level (A.M. Samuel, 1995).
Mechanical properties
Composite materials are determined by either isotropic or anisotropic, by the structure of composites. Isotropic material is a material in which the properties do not depend on the direction of measuring. An anisotropic material is a material in which the properties of which along a particular axis or parallel to a particular plane are different from the properties measured along with other directions. From the following figure, we can see the ROM (Rule of Mixtures) is a method of approach to approximate estimation (Schwartz.M, 1984) of composite material properties, based on an assumption that a composite property is the volume-weighted average of the phases (matrix and reinforcement) properties.
Figure 10:Rules of Mixtures
Pradeep R et.al studied on mechanical properties of Al- Red Mud and Silicon Carbide Metal Matrix Composite of Aluminium alloy (Al7075) with the incorporation of varying weight percentage composition such as SiC8%+Al7075, SiC6%+Red mud2%+ Al7075, SiC4%+Red mud 4%+Al7075, SiC2%+Red mud 6%+Al7075, Red mud 8%+Al7075ed mud and Silicon carbide particles by stir casting technique. The experimental result reveals that the combination of a matrix material with reinforcement such as SiC and Red mud particles enhances mechanical properties (tensile strength, compressive strength, hardness, and yield strength) of alloys. (Pradeep, 2014)
Keshavamurthy R et.al studied Al7075-TiB2, processed by stir casting technique using Al-10%Ti and Al-3%Br master alloys. Matrix alloy and composite were subjected to microstructure analysis, microhardness test, grain size studies, and tensile test. Microhardness, yield strength, and ultimate tensile strength of Al7075-TiB2 composite were considerably higher when compared with unreinforced alloy figures 2, 3, and 4 are shown the composite materials of Al7075. (Keshavamurthy, 2013). Kumar et al. (2010) study about hardness and Abrasive wear behavior with different particle sizes using a mathematical model with the analysis of variance AA7075Al l5- 25% SiC using Powder metallurgy methods. The study clearly shows the hardness of the composites increased with the SiC addition and micrographs showed uniform distribution of the SiC particles. And the abrasive wear behavior clearly indicated the increase in wear resistance as SiC acted as a load-supporting element. Composites with larger reinforcement size and high-volume fraction displayed improved abrasive wear resistance as compared to other combinations (S. Kumar, 43 (2010)). Baskaran et al. (2014) showed the combination of Al-7075 alloy with 4 and 8% of TiC particulate reinforcement. The study was using reactive in-situ casting methods. The study was about showing the microstructural studies and Wear
behavior of the composite. And the SEM analysis showed that TiC particles were uniformly distributed along the grain boundaries. From the result, the incorporation of 4% TiC improved the maximum wear resistance of the composite as compared to 8%TiC composite (S. Baskaran, 60 (2014).). R.Kartigeyan et.al has successfully developed Al 7075 alloy and Short Basalt Fibre composite through liquid metallurgy technique. The increase in short basalt fiber maximizes the ultimate tensile strength, yield strength, and Hardness. The composite containing 6% wt of short basalt fiber signifies a higher hardness value of 97.1 Mpa when compare to base matrix hardness 92Mpa. The Al-7075/short basalt fiber reinforced 6 vol % maximizes the ultimate tensile strength by 65.51%. The distribution of reinforcements in the metal matrix is genuinely uniform. From the above research paper, concluded that, under tension loading without affecting the tensile ductility, values of tensile strength increase. From the observation, experimental values of short basalt fiber give the best result for the study (R. Karthigeyan, 2012).
Figure 11: Optical microphotographs of a) Al7075 alloy and b) Al7075 8.5wt% TiB2 composite (C. Saravanan, 2015)
The figure shows the incorporation of TiO2 into Al7075 of the composite. The first figure shows, the pure form of Al7075, and the second figure shows the incorporated TiO2 into Al7075. From figure visibly observed that, the uniform distribution of TiB2 particles in the matrix alloy. From the microstructure observation, the grain size of the composite has lower than unreinforced alloy.
Figure 12:Hardness of Al7075 alloy and Al7075-TiB2 composite (C. Saravanan, 2015)
Here, the figure observed that there is a great difference between the base alloy and the incorporated one. From the base alloy, the increase of the hardness is by 20%. This shows how much hard mechanical properties are increases. This increase in the hardness of the properties of the materials is up to the limited points.
Figure 13:Tensile Strength of Al7075 alloy and Al7075-TiB2composite (C. Saravanan, 2015)
Here from the figure simply we observed the increase of the tensile property of the new materials. The materials are highly increased tensile property. This shows the incorporation of the TiO2 into Al7075 gives high tensile properties.
CONCLUSION
From the relative amount of the reinforcement material, obtain a composite with a broad range of mechanical properties.
If the process parameters are properly controlled, it could lead to better properties in composite material.
Route for fabrication methods used for AMMCs can be broad of two types solid-state processing and liquid state processing.
Stir casting is the greatest public liquid state process used for the production of MMCs. It is humble in action and cost- effective and provides a fairly uniform distribution of particles.
Powder metallurgy is the typically used solid-state process for manufacture. It provides uniform distribution of particles but dearer than stir casting.
It has been observed that there is a rise of 30% in hardness and there is a rise in tensile strength that is near twice the base aluminum alloy.
[20] S. Baskaran, V. A. (60 (2014) .). Investigation on Dry Sliding Wear Behaviour of in-situ casted AA7075-TiC Metal Matrix Composites by using Taguchi Technique. Mater. & Dsg., , 186-192. [21] S. Kumar. (43 (2010)). "Effect of Reinforcement Size, and Volume Fraction on the Abrasive Wear of AA7075 Al/SiCp P/M composites-A Statistical Analysis",. Tribol. Inter., , 414-422. [22] Schwartz.M, S. M.-H. (1984). composite materials. New York.REFERENCE
[1] A.M. Samuel, F. S. (1995). key engineering materials, 104-107. [2] C. Saravanan, K. S. (2015). Effect of Particulate Reinforced Aluminium Metal Matrix Composite. 8. [3] D.J. Lloyd. (1989). science and technology . [4] Daniel Gay, S. V. (2003). COMPOSITE materials design and application. New York Washington, D.C.: Boca Raton London. [5] Gowri Shankar, M. J. ( 2013.). Individual and Combined Effect of Reinforcements on Stir Cast Aluminium Metal Matrix Composites. A Review, . Interna-tional Journal of Current Engineering and Technology. [6] j.Hashine, L. (1999). Metal matrix composites: production by the stir casting method. journal of materials processing technology, 7. [7] K. Miwa, T. O. (1990). Preparation of Fine SiC Particle Reinforced Al.alloy composite by compocasting process. tama city. tokyo , 351- 362. [8] K.J. Brondyke, P. H. (1964). Trans. TMS-AIME , 1452. [9] K.K. Chawla. (2012). Composite Materials: Science and Engineering,. In K.K. Chawla, Composite Materials: Science and Engineering, (p. 52). New York : Springer Science+Business Media. [10] Kainer, K. U. (2006). Basics of Metal Matrix Composites. [11] Keshavamurthy, R. S. (2013). Microstructure and Mechanical Properties of Al7075TiB2 insitu composite. Journal of Material Sciences,, 6-10. [12] L. Lajoye, M. S. (1987). in: Proc. Conf. on Solidification Processing,. 473-476. [13] M. Samuel, H. L. (1989). M. Samuel, H. Liu, F.H. Samuel,. science and technology. [14] P.K. Ghosh, S. R. (1984). Trans. Jpn. Inst. Met. . 440. [15] P.K. Ghosh, S. R. (1988). indian journal technology , 7. [16] Parker., N. (1964). chemical engineering, 7. [17] Pradeep, R. P. (2014). Evaluation of mechanical properties of aluminium alloy 7075 reinforced with silicon carbide and red mud composite,. International Journal of Engineering Research and General Science, 1081-88. [18] R. Karthigeyan, G. R. (2012). Mechanical Properties and Microstructure Studies of Aluminium (7075) Alloy Matrix Composite Reinforced with Short Basalt Fibre . European Journal of Scientific Research. [19] Ravichandran, M. a. (2014). Synthesis of Al-TiO2 Composites through Liquid Powder Metallurgy Route,. International Journal of Mechanical En- gineering.