
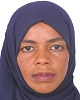
- Open Access
- Authors : Eng. Zubeida Tajelsir Abdallah Elsheikh And Dr. Majdi Elgaili Mukhtar Ahmed
- Paper ID : IJERTV13IS010087
- Volume & Issue : Volume 13, Issue 01 (January 2024)
- Published (First Online): 05-02-2024
- ISSN (Online) : 2278-0181
- Publisher Name : IJERT
- License:
This work is licensed under a Creative Commons Attribution 4.0 International License
Analysis and Design of Reinforced Concrete Building using Different Software Programs
Authors:
Eng. Zubeida Tajelsir Abdallah Elsheikh And Dr. Majdi Elgaili Mukhtar Ahmed
Department of civil engineering, alzaiem alazhari university kafori Block 7, khartoum north, sudan
-
ABSTRACT:
The research dealt with how to analyze a multi-story building consisting of a ground floor and 5 floors using manual analysis and programs. Etabs and Excel programs were used to compare with the manual design.
The manual method used for the analysis is the moments distribution with excel program.
A structural analysis of wind loads for a building consisting of 6 floors was carried out using manual and computer methods. The results were compared and it was found that the results are close.
The slabs, columns, beams, and foundations were analyzed manually, and the structural design of the structural elements was made and compared with the program design, and it was found that the results are close.
Key word:
Analysis, Design, moment distribution (Excel program) and portal frame.
Objective:
To analysis and design a multi-story RC building. Manual analysis is done with the aid of Excel software.
Analysis and design is done with the aid of Etabs & SAFE software. And compare the design with Robot software.
The design is done with the aid of revit software.
To gain design knowledge on various structural elements like beam, column, slab, and foundation .etc.
INTRODUCTION:
Now a days due to overpopulation and high cost of land, multi-storied building is more essential for metropolitan city. Multi-storied Residential building is the perfect solution for living of high populated area. A multi-storied building, which possess multiple floor above the ground level, which aim to increase the floor area of building in shortest built up area.
Structure analysis is a subject which involves designing, planning to build up a perfect building. Basically each project are different with their design criteria such as incoming load, soil properties, dynamic load, built up area etc. Here we provided the details to complete a residential apartment theoretically.
We firstly collected some required data to measure the soil specific such as moisture content, bearing capacity of soil, types of soil etc. We provided the perfect parameter in beam, slab, column and footing with the consideration of incoming load to avoid shear and bending collapse. In
Accordance with limit state method of collapse in BS 0.0035
We built G+5 building which deal with strength and stability of structure under maximum design load Flexure, compression, shear and torsion.
1. METHODOLOGY:
Design of concrete member
Planning and drawing
Analysis in ETABS
&SAFE and Robot
DATA COLLECTION
Detailing of residential building
WORK PROGRESS
BASIC DATA
-
Type of building Residential building.
-
Type of structure multi story rigid jointed framed iii. No. of story 6 (G+5)
-
-
Floor to floor height 3 m.
-
External walls 250 mm including plaster
-
Internal walls 150 mm including plaster.
-
Bearing capacity of soil 200 KN/m2
-
Height of plinth 0.5 m.
NOTE:-Others required data assume using NBC(national building code) for planning and (BS8110) & (ACI 318-14)for concrete design work.
Table 2-1 Table 2-5
Table 2-2
Table 2-3
Table 2-4
Table 2-6
Name |
Design Type |
Element Type |
Material |
Total Thickness mm |
SLAB 18 |
Slab |
Shell-Thin |
Fcu25 |
180 |
Slab 20C, |
Slab |
Shell-Thin |
Fcu25 |
200 |
Table 2-7
B.S CODE:
3. OUT PUT ANALYSIS:
Figure 3-1 Robot modeling
Figure 3-2: Deform shape
COLUMN RESULT
Fcu=30N/mm2
Table 3-1: Loads & moment
MEMBER |
ETABS |
ROBOT |
|||||
F |
My |
Mz |
F |
My |
Mz |
||
C1 |
Short col&Gr |
2176 |
-6.4 |
0.13 |
2104 |
.79 |
7.16 |
1st & 2nd |
1623 |
2.6 |
0.45 |
1564 |
-1.2 |
6.16 |
|
3rd & 4th &5th |
805 |
1.45 |
-0.24 |
774 |
-4.56 |
3.3 |
|
C2 |
Short col&Gr |
1283 |
0.8 |
-3.6 |
1000 |
9.1 |
-3.9 |
1st & 2nd |
913 |
-2.2 |
36.3 |
836 |
23 |
-0.43 |
|
3rd & 4th &5th |
683 |
17 |
-30 |
496 |
20.3 |
0.25 |
|
C3 |
Short col&Gr |
714 |
-4.3 |
-3.2 |
451 |
-2.7 |
1.4 |
1st & 2nd |
509 |
10.8 |
18.3 |
364 |
9.4 |
9.98 |
|
3rd & 4th &5th |
252 |
8.1 |
16.3 |
213 |
-8.6 |
-7.5 |
Table 3-2: COLUMN DESIGN
6T16mm As=1206mm^2
6 120/
MEMBER |
ETABS |
ROBOT |
MANUAL |
|
C1 |
Short col&Gr (30*60)cm |
6T16mm As=1206mm^2 6 120/ |
6T16mm As=1206mm^2 6 150/ |
|
1st & 2nd (30*55)cm |
6T16mm As=1206mm^2 6 120 |
6T16mm As=1206mm^2 6 120 |
4T16mm As=804mm^2 6 150/ |
|
3rd & 4th &5th (45*25)cm |
4T16mm As=804mm^2 6 120 |
4T16mm As=804mm^2 6 120 |
4T16mm As=804mm^2 6 150/ |
|
C2 |
Short col&Gr (30*50)cm |
6T16mm As=1206mm^2 6 120/ |
6T16mm As=1206mm^2 6 120/ |
6T16mm As=1206mm^2 6 150/ |
1st & 2nd (30*45)cm |
4T16mm As=804mm^2 6 120 |
4T16mm As=804mm^2 6 120 |
4T16mm As=804mm^2 6 150/ |
|
3rd & 4th &5th (40*25)cm |
4T16mm As=804mm^2 6 120 |
4T16mm As=804mm^2 6 120 |
4T16mm As=804mm^2 6 150/ |
|
C3 |
Short col&Gr 1st & 2nd (40*25)cm |
4T16mm As=804mm^2 6 100 |
4T16mm As=804mm^2 6 100 |
4T16mm As=804mm^2 6 150/ |
3rd & 4th (40*20)cm |
4T16mm As=804mm^2 6 100 |
4T16mm As=804mm^2 6 100 |
4T16mm As=804mm^2 6 150/ |
Table 3-3: Beam Design
D.L=13.4KN/m fcu=25N/mm2
section |
ETABS |
ROBOT |
MANUAL |
||||||
B(20*40) cm |
Load |
My |
Fz |
Load |
My |
Fz |
Load |
My |
Fz |
13.4 KN/m |
50 KN.m |
73KN |
13.4 KN/ m |
31.9 KN.m |
+37 -37 KN |
13.4 KN/m |
|||
B(20*50) cm |
Load |
My |
Fz |
Load |
My |
Fz |
Load |
My |
Fz |
13.4 KN/m |
+18.4 -28.3 KN.m |
-45.1 |
13.4 KN/ m |
-27.4 +16.5 KN.m |
+51 -45.3 KN |
13.4 KN/m |
12.3 KN.M |
32.3 KN |
Table 3-4: Beam design at X direction: At mid span
section |
ETABS |
ROBOT |
MANUAL |
|||
mom |
design |
mom |
design |
mom |
design |
|
B2(20*40)cm |
0 |
Assembly rein 2T16 As=402mm2 R6@160mm c/c |
31.9 |
2T16 As=402mm2 R6@160mm c/c |
2T16 As=402mm2 R6@160mm c/c |
|
B1(20*50)cm |
+18.4 |
2T16 As=402mm2 R6@160mm c/c |
+18.6 |
2T16 As=402mm2 R6@160mm c/c |
12.3 |
2T16 As=402mm2 R6@160mm c/c |
At interior support
section |
ETABS |
ROBOT |
MANUAL |
|||
mom |
design |
mom |
design |
mom |
design |
|
B2(20*40)cm |
-56.6 |
2T16 As=402mm2 R6@160mm c/c |
3.3 |
2T16 As=402mm2 R6@160mm c/c |
2T16 As=402mm2 R6@160mm c/c |
|
B1(20*50)cm |
-26 |
2T16 As=402mm2 R6@160mm c/c |
-24.9 |
2T16 As=402mm2 R6@160mm c/c |
-10.6 |
2T16 As=402mm2 R6@160mm c/c |
Maximum shear (concrete and stirrups):
section |
ETABS |
ROBOT |
MANUAL |
|||
shear |
design |
shear |
design |
shear |
design |
|
B2(20*40)cm |
+72 |
R6@160mm c/c |
-34.9 |
R6@160mm c/c |
||
B1(20*50)cm |
+43.3 |
R6@160mm c/c |
-44 |
R6@160mm c/c |
34.8 |
Table 3-5: Beam design at Y direction: At mid span positive:
section |
ETABS |
ROBOT |
||
mom |
design |
mom |
design |
|
B1(20*50)cm |
+35 |
2 16 As=402mm2 |
+45 |
2 16 As=402mm2 |
At interior support negative
section |
ETABS |
ROBOT |
||
mom |
design |
mom |
design |
|
B1(20*50)cm |
-42 |
2 16 As=402mm2 |
-35 |
2 16 As=402mm2 |
At support:
section |
ETABS |
ROBOT |
||
mom |
design |
mom |
design |
|
B1(20*50)cm |
-42.4 |
2 16 As=402mm2 |
-31.8 |
2 16 As=402mm2 |
Maximum shear (concrete and stirrups):
section |
ETABS |
ROBOT |
||
mom |
design |
mom |
design |
|
B1(20*50)cm |
+74.8 |
6@160mm c/c |
-68 |
6@160mm c/c |
SLAB DESIGN:
Table 3-6: Positive moment bottom:
member |
ETABS & SAFE |
ROBOT |
MANUAL |
|||
Moment |
design |
Moment |
design |
Moment |
design |
|
Roof slab(Y) |
7 |
T10@300mmc /c |
7 |
T10mm@300 mmc/c |
13.6 |
3T12mm@300mmc /c |
Floor slab(X) |
28 |
T12mm@200 mmc/c |
33 |
T12mm@200 mmc/c |
72.4 |
4T12mm@200mmc /c |
Floor slab(Y) |
33 |
T12mm@200 mmc/c |
28.2 |
T12mm@200 mmc/c |
86.4 |
3T12mm@300mmc /c |
Table 3-7: Negative moment top
td>Moment
member |
SAFE |
ROBOT |
MANUAL |
|||
design |
Moment |
design |
Moment |
design |
||
Roof slab(Y) |
16 |
T10@300mmc/c |
12.7 |
Middle strip T10@300mmc/c Col strip T10@200mmc/c |
13.6 |
Middle strip T16@500mmc/c Col strip T16@500mmc/c |
Floor slab(X) |
80 |
Middle strip T16@300mmc/c Col strip |
72.7 |
Middle strip T16@300mmc/c |
106.7 |
Col strip 5T16mm@200mmc/c |
Middle strip 2T16@500mmc/c |
||||||
Col strip T16@100mmc/c |
||||||
T16@100mmc/c |
||||||
Floor slab(Y) |
116 |
Middle strip T16@300mmc/c |
77.2 |
Middle strip T16@300mmc/c |
98.7 |
Col strip 5T16mm@200mmc/c |
Col strip T16@100mmc/c |
Col strip T16@100mmc/c |
Middle strip 2T16@500mmc/c |
Figure 3-3 Check of punching shear: Robot
ETABS:
Figure 3-4: chech of punching shear
-
I added on ETABS modeling three beams to the slab to check the punching shear
Stair Design:
L.L=3KN/m2 D.L=3.7KN/m2
Table 3-8: Design of stair
ETABS& SAFE |
ROBOT |
MANUAL |
||||||
Mx |
bottom |
Top At support |
Mx |
bottom |
Top |
Mx |
X direction |
Y direc |
-21 |
4T10@25 0mmc/c |
4T12@250 mmc/c |
-15.2 |
4T10@250 mmc/c |
4T10@ 250mm c/c |
-10.4 |
4T10@250 mmc/c |
4T10@250 mmc/c |
Foundation design:
Design of footings: Fy=460N/mm2 T16mm Q=h =20*1.4=28KN/m2 K=120*(200-28)=20640KN/m2 K=20.60MPa
Thickness=680mm
p=200KN/m2 fc=25N/mm2 K=120*q
Figure 3-5: Ultimate load in footings
Figure 3-6 check of punching shear
Figure 3-7 Check of soil pressure:
Robot:
Fy=460N/mm2 T16mm p=200KN/m2 fc=25N/mm2 K=120*q Q=h =20*1.4=28KN/m2
K=120*(200-28)=20640KN/m2 K=20.60MPa
Thickness=600mm
Figure 3-8: Ultimate load in footings
FOUNDATION DESIGN:
Table 3-9: Positive moment top:
member |
ETABS & SAFE |
ROBOT |
||
Moment |
design |
Moment |
design |
|
Floor slab(X) |
353 |
T16mm@200mmc/c |
250 |
T16mm@170mm c/c |
Floor slab(Y) |
420 |
T16mm@300mmc/c |
19.7 |
T16mm@240mm c/c |
Table 3-10: Negative moment bottom:
member |
SAFE |
ROBOT |
||
Moment |
design |
Moment |
design |
|
Floor slab(X) |
-165 |
Middle strip T16@200mmc/c Col strip T16@90mmc/c |
-602.6 |
Middle strip T16@120mmc/c Col strip T16@90mmc/c |
Floor slab(Y) |
-114.8 |
Middle strip T16@200mmc/c Col strip T16@90mmc/c |
-576 |
Middle strip T16@120mmc/c Col strip T16@90mmc/c |
Figure 3-9 check of punching shear
Figure 3-10 Check of soil pressure:
ACI CODE:
Figure 3-11: Deform shape in Robot
Figure 3-12 Deform shape in ETABS
Table 3-11: Column design:
member |
ETABS |
ROBOT |
|
C1 |
Short col&Gr (30*60)cm |
6T16mm As=1206mm^2 6 120/ |
6T16mm As=1206mm^2 6 120/ |
1st & 2nd (30*55)cm |
6T16mm As=1206mm^2 6 120 |
6T16mm As=1206mm^2 6 120 |
|
3rd & 4th &5th (45*25)cm |
4T16mm As=804mm^2 6 120 |
4T16mm As=804mm^2 6 120 |
|
C2 |
Short col&Gr (30*50)cm |
6T16mm As=1206mm^2 6 120/ |
6T16mm As=1206mm^2 6 120/ |
1st & 2nd (30*45)cm |
4T16mm As=804mm^2 6 120 |
4T16mm As=804mm^2 6 120 |
|
3rd & 4th &5th (40*25)cm |
4T16mm As=804mm^2 6 120 |
4T16mm As=804mm^2 6 120 |
|
C3 |
Short col&Gr 1st & 2nd (40*25)cm |
4T16mm As=804mm^2 6 100 |
4T16mm As=804mm^2 6 100 |
3rd & 4th (40*20)cm |
4T16mm As=804mm^2 6 100 |
4T16mm As=804mm^2 6 100 |
Table 3-12: Beam design at X direction:
At mid span positive
section |
ETABS |
ROBOT |
||
mom |
design |
mom |
design |
|
B(20*40)cm |
+19.3 |
2 16 As=402mm2 |
27 |
2 16 As=402mm2 |
B(20*50)cm |
+14 |
2 16 As=402mm2 |
+11 |
2 16 As=402mm2 |
:
At interior support negative
section |
ETABS |
ROBOT |
||
mom |
design |
mom |
design |
|
B2(20*40)cm |
-7.8 |
2 16 As=402mm2 |
3 |
2 16 As=402mm2 |
B1(20*50)cm |
-22 |
2 16 As=402mm2 |
-14 |
2 16 As=402mm2 |
Maximum shear (concrete and stirrups):
section |
ETABS |
ROBOT |
||
shear |
Dist of stirrups |
shear |
Dist of stirrups |
|
B2(20*40)cm |
-32 |
6@160mm c/c |
-29 |
6@160mm c/c |
B1(20*50)cm |
-33 |
6@160mm c/c |
-38.8 |
6@160mm c/c |
At support:
section |
ETABS |
ROBOT |
||
mom |
design |
mom |
design |
|
B1(20*50)cm |
-23 |
2 16 As=402mm2 |
-12 |
2 16 As=402mm2 |
Table 3-13: Beam design at Y direction: At mid span positive:
section |
ETABS |
ROBOT |
||
mom |
design |
mom |
design |
|
B1(20*50)cm |
+29 |
2 16 As=402mm2 |
+39 |
2 16 As=402mm2 |
At interior support negative
section |
ETABS |
ROBOT |
||
mom |
design |
mom |
design |
|
B1(20*50)cm |
-27 |
2 16 As=402mm2 |
-30 |
2 16 As=402mm2 |
At support:
section |
ETABS |
ROBOT |
||
mom |
design |
mom |
design |
|
B1(20*50)cm |
-38.3 |
2 16 As=402mm2 |
-27 |
2 16 As=402mm2 |
Maximum shear (concrete and stirrups):
section |
ETABS |
ROBOT |
||
mom |
design |
mom |
design |
|
B1(20*50)cm |
-52 |
6@160mm c/c |
-58.7 |
6@160mm c/c |
SLAB DESIGN:
Fy=420N/mm2 fc=20N/mm2 h=250mm
Table 3-14: Positive moment
Bottom:
member |
ETABS & SAFE |
ROBOT |
||
Moment |
design |
Moment |
design |
|
Roof slab(Y) |
7 |
6@200mmc/c |
6 |
56 |
Floor slab(X) |
26 |
10mm@150m mc/c |
22 |
610 |
Floor slab(Y) |
29.8 |
10mm@150m mc/c |
20 |
610 |
Table 3-15: Negative moment top
member |
SAFE |
ROBOT |
||
Moment |
design |
Moment |
design |
|
Roof slab(Y) |
20.4 |
Middle strip 6@250mmc/c Col strip 6@100mmc/c |
27 |
Middle strip 6@200mmc/c Col strip 6@100mmc/c |
Floor slab(X) |
75 |
Middle strip 16@400mmc/c Col strip 16@100mmc/c |
111 |
Middle strip 316 Col strip 6 16 |
Floor slab(Y) |
103 |
Middle strip 16@400mmc/c Col strip 16@100mmc/c |
86 |
Middle strip 316 Col strip 6 16 |
ROBOT
-
For economy slab I must minimize the thickness of slab to 22cm
Figure 3-1: Check of punching shear:
ETABS:
Figure 3-14: Check of punching shear:
Stair Design:
L.L=4.79KN/m2 D.L=3.7KN/m2 Fy=420N/mm2 h=0.18m
Table 3-16: stair design
ETABS |
ROBOT |
|||||||
Mx |
bottom |
Top |
Mx |
bottom |
Top |
Mx |
bottom |
Top |
-18 |
4 10 |
4 10 at support |
-16 |
4 10 |
4 10 at support |
-10.4 |
4 10 |
4 10 at support |
Design of footings:
Fy=280N/mm2 Ø=16mm p=200KN/m2 fc=25N/mm2 K=120*q
Q=h =20*1.4=28KN/m2 K=120*(200-28)=20640KN/m2 K=20.60MPa
Figure 3-15: Ultimate load in footings in robot
Figure 3-16: Ultimate load in footing in ETABS
Table 3-17: design of footings with ROBOT program
ROBOT |
|||||||
Type |
L |
B |
H |
bottom |
top |
||
X direction |
Y direction |
X direction |
Y direction |
||||
F1 |
1.5 |
1.5 |
0.5 |
7Ø16@250mm |
7Ø16@250mm |
||
F2 |
5.5 |
2.7 |
0.6 |
20Ø16@100mm |
34Ø16@150m m |
||
F3 |
2.2 |
2.2 |
0.5 |
10Ø16@200mm |
10Ø16@200m m |
||
F4 |
3.7 |
1.9 |
0.5 |
20Ø16@100mm |
24Ø16@150m m |
||
F5 |
3.1 |
3.1 |
0.5 |
33Ø16@90mm |
25Ø16@120m m |
||
F6 |
2.7 |
6 |
0.7 |
20Ø16@130mm |
39Ø16@150m m |
17Ø16@300 mm |
14Ø16@200mm |
F7 |
5.7 |
2.9 |
0.7 |
38Ø16@150mm |
22Ø16@130m m |
` |
|
F8 |
2.7 |
1.6 |
0.5 |
13Ø16@200mm |
10Ø16@160m m |
||
F9 |
5.5 |
2.8 |
0.6 |
26Ø16@100mm |
34Ø16@160m m |
||
F10 |
7.8 |
2.9 |
0.5 |
Ø16@100mm |
Ø16@100mm |
Ø16@220mm |
Ø16@220mm |
F11 |
7.4 |
2.7 |
0.5 |
Ø16@100mm |
Ø16@100mm |
Ø16@220mm |
Ø16@220mm |
F12 |
8 |
2.8 |
0.5 |
Ø16@100mm |
Ø16@100mm |
Ø16@220mm/p> |
Ø16@220mm |
Figure 3-17: Check of punching shear for F10
Figure 3-18: Check of punching shear for F11
Figure 3-19: Check of punching shear for F12
CHEACK WITH SAFE PROGRAM:
Figure 3-20: Check of soil pressure:
-
F(A-8) , F(C-8)& F(E-8) I have increase their dimensions because the soil pressure was not exceeded.
Figure 3-21: Check of punching shear
Table 3-18: design of footings with SAFE program
SAFE |
|||||||
Type |
L |
B |
H |
bottom |
top |
||
X direction |
Y direction |
X direction |
Y direction |
||||
F1 |
1.5 |
1.5 |
0.5 |
Ø16@250mm |
Ø16@250mm |
||
F2 |
5.5 |
2.7 |
0.6 |
Ø16@120mm |
34Ø16@150mm |
||
F3 |
2.2 |
2.2 |
0.5 |
Ø16@150mm |
Ø16@150mm |
||
F4 |
3.7 |
1.9 |
0.5 |
Ø16@100mm |
Ø16@150mm |
||
F5 |
3.1 |
3.1 |
0.5 |
Ø16@90mm |
Ø16@80mm |
||
F6 |
2.7 |
6 |
0.7 |
Ø16@130mm |
Ø16@150mm |
||
F7 |
5.7 |
2.9 |
0.7 |
Ø16@150mm |
Ø16@130mm |
` |
|
F8 |
2.7 |
1.6 |
0.5 |
Ø16@200mm |
Ø16@150mm |
||
F9 |
5.5 |
2.8 |
0.6 |
Ø16@100mm |
Ø16@100mm |
||
F10 |
7.8 |
2.9 |
0.5 |
Ø16@120mm |
Ø16@100mm |
Ø16@250mm |
Ø16@250mm |
F11 |
7.4 |
2.7 |
0.5 |
Ø16@100mm |
Ø16@100mm |
Ø16@250mm |
Ø16@250mm |
F12 |
8 |
2.8 |
0.5 |
Ø16@100mm |
Ø16@100mm |
Ø16@250mm |
Ø16@250mm |
0.60
0.55
0.45
0.45
Details:
c2
c2
c2
c2
c2
c3
c2
c1
A
B
c1
c1
c1
c1
c1
c1
c1
c2
C
c1
c1
c1
c1
c1
c1
c1
c2
D
c1
c1
c1
c1
c1
c1
c1
c2
E
c2
c2
c2
c2
c2
c2
c2
c3
F
G
1
2
3
4
5
6
7
8
0.30
0.30
0.25
0.25
C1
at top 13? 6mm@
at top 13? 6mm@
at top 13? 6mm@ at top 13? 6mm@ main Rein 4? 16 170mm main Rein 4? 16 170mm
main Rein 6? 16 170mm main Rein 4? 16 170mm bottom Stirrup 6? 6 bottom Stirrup 6? 6
bottom Stirrup 6? 6 bottom Stirrup 6? 6 @90mm @90mm @ 90mm @ 90mm
C2 0.30 0.30 0.20
at top 13? 6mm@ at top 13? 8mm@
at top 13? 6mm@
at top 13? 6mm@
170mm main Rein 4? 16 170mm main Rein 4? 16 170mm
main Rein 4? 16 170mm
main Rein 6? 16 bottom Stirrup 6? 6
bottom Stirrup 6? 6 bottom Stirrup 6? 6 bottom Stirrup 6? 6
@90mm
@ 90mm @90mm @90mm
0.25 0.20 0.20
C2
at top 13? 6mm@ at top 13? 6mm@ at top 13? 6mm@ main Rein 4? 16 170mm main Rein 4? 16 170mm main Rein 4? 16 170mm
bottom Stirrup 6? 6 bottom Stirrup 6? 6 bottom Stirrup 6? 6
@ 90mm @90mm @90mm
0.50
0.40
0.45
0.40
0.40
0.40
0.40
Figure 3-22 columns
4
4
section B 1
?
2? 16
8@250
section 4-4
2? 16
1 3 2
1 3 2
1 3 2
1
3
2
1
3
2
1 3
2
1
3
2
1 3 2 T16
1 3 2
1 3 2
1
3
2
1
3
2
1 3
2
1
3
2
0.20
2? 16
4? 16 4? 16
? 8@ ? 8@ ? 8@
150 mm 150 mm 150 mm
2? 16 4? 16 2? 16
sect 1-1 sect 2-2 sect 3-3
0.50
Figure 3-23: Beams
Top
bottom
? 16@100mm c/c
2.43 1.30
4.00 3.00 3.05 2.40 2.85 3.45 3.75
A B
C
D
E
16T @ 300mm (T )E.W. T 12@ 200mm (B )E.W.
F
G
16T @ 500mm (T )E.W. T 12@ 200mm (B )E.W.
1
2
3
4 5
6
7
8
1.30 2.45
? 16@300mm c/c
? 16@500mm c/c
A
B
C
? 16@200mm
D
E
F
G
1
2
3
4
5
6
7
8
? 16@200mm
Figure 3-24: Slab details
? 16@100mm
? 16@100mm
? 16@ 100mm
? 16@100mm
? 16@300mm
? 16@100mm
? 16@300mm
? 16@100mm
? 16@ 300mm
L1/4
L2/4
L1/4
L2/4
L1/4 L2/4
? 16@300mm
5.L1 L2/4
L1/4 L2/4
L1/4 L2/4
L1/4 L2/4
L1/4
? 12@200mm
? 12@200mm
? 12@200mm
4.00
3.00
3.05
2.40
2.85
3.45
3.75
section 1-1
? 16@ 300
? 16@ 500
? 16@300
? 16@500
? 16@300
? 16@300
? 16@300
? 16@500
? 16@300
? 12@ 200
? 12@ 200
section 2-2
Figure 3-25: section of slab
T 12@ 250mm
T 10@ 250mm
T 10@ 200mm
stair seaction
Figure 3-26: stairs
8T @ 230mm
8T @ 120mm
16T @ 250mm
16T @ 250mm
D
depend on site
H
50?
single footing
b
? 16@250mm
D
d
B
? 16@250mm
PLAN FOR SINGLE FOOTING
Figure 3-27: Isolate footing:
@ 100 mm
? 16@ 250
100mm
T @ 100 mm
? 16@ 120
SECTION F 10
? 16@ 100mm
? 16@ 100mm
L
B
Figure 3-28: Continues footing:
? 16@ 250 L ? 16@ 160
SECTION F 9
? 16@250
? 16@250
H
PLAN F 9
Figure 3-29: Combined footing:
L
h
Figure 3-30: raft foundation
4. CONCLUSIONS:
-
After analyzing the G+5 story building structure, concluded that structure is safe in loading like dead load, live load and wind load.
-
Member dimensions (Beam, Column and Slab) are assigns by calculating the load type and its quantity applied on it. AutoCAD plan gives detailed information of the structure members length, height, size and numbers etc.
-
ETABS & ROBOT has the capability to calculate the reinforcement needed for any concrete section. SAFE program used to check the foundation design. The program contains a number of parameters which are designed as per.
-
The next paper the analysis will be done using deformed shape by using software programs.
-
The ETABS program extracts high values, while the robot extracts low values. In my personal opinion, the robot produces more accurate values. The program uses the Finite method and works on analyzing all the elements, even the foundations, while ETABS designs most of the elements, and the design of the foundation and slab is verified using the SAFE program.
-
The difference in torque values is somewhat large, especially in beams, but as for the design, the design is almost uniform.
5. REFERENCES:
-
British standard BS8110: Part 1:1997 Code of practice for design and construction. British
Standard Institution: London.
-
D Polette and J MLanders, 1997Consrtuction Systems, London, Goodheart-Wilcox Co.
-
T.J.MancGinley and B.S.Choo, 1990 Reinforced Concrete Design Theory and Examples,2nd
edition, London, SPON Publishers.
-
Eugene JO and Andrew SD, 1999 Reinforced and Prestressed Concrete Design the Complete
-
Process, 2Tld edition, London Longman Publishers.
5,Moseley WH and Bungy JH, 1999 Reinforced Concrete Design, 5th edition, London, Macmillan Publishers.
-
Building Code Requirements for structural Concrete (ACI318-08) and Commentary (ACI 318-14), American Concrete Institute, P.O. Box 9094, Farmington Hills, Michigan.
-
Arthur H. Nilson, David Darwin, Charls W. Dolan, Design of concrete structures, 13th
edition.
-
Arthur H. Nilson, George Winter, Design of concrete structures, 10th edition.
-
D. Fanella, I. Alsamsam, The Design of Concrete Floor Systems, PCA Professional
Development Series, 2005.
-
McGregor, J.G. Reinforced Concrete Mechanics and Design, Prentice Hal, New Jersey, 1997.