
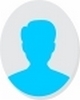
- Open Access
- Authors : Anoop Raj
- Paper ID : IJERTV11IS100117
- Volume & Issue : Volume 11, Issue 10 (October 2022)
- Published (First Online): 03-11-2022
- ISSN (Online) : 2278-0181
- Publisher Name : IJERT
- License:
This work is licensed under a Creative Commons Attribution 4.0 International License
Analysis and Evaluation of Centrifugal Blower Performance using Finite Element Analysis by Ansys Software
Anoop Raj
Department of Mechanical Engineering Maria college of Engineering and Technology,
Attoor, Tamilnadu, India
Abstract:- Blower mechanisms are frequently utilized on- board submarines. Submarines have blowers installed in nearly all of their systems, including those that control the temperature and the ventilation. The ventilation systems consist of supply fans as well as exhaust fans. The blower that is installed in ventilation systems is responsible for ventilating living quarters as well as other areas. Blades made of modern materials for use in marine applications typically include aluminum and steel. These blades produce a significant amount of noise. Those who are working in close proximity to the blower are bothered by the noise because of this, composite materials are going to be used instead of metals as an alternative for better vibration management. This study will look into the possibility of using composites rather than metals in place of those components. The capacity of a structure to reduce the transmission of vibrations that are caused by mechanical disturbances is represented by the property of damping in that structure. The damping factor of a material is a measurement of the material's damping. Composite materials have a better chance of reducing vibration when compared to metals of the same type. This is because, in comparison to metals, the damping properties of composites are significantly higher.
Keywords:- Blowers, steel, aluminum, marine
-
INTRODUCTION
Blower mechanisms are frequently utilized on-board submarines. Submarines have blowers installed in nearly all of their systems, including those that control the temperature and the ventilation [1]. The ventilation systems of central systems consist of supply fans as well as exhaust fans. The blower that is installed in ventilation systems is responsible for ventilating living quarters as well as other areas. They remove potentially harmful impurities from the atmosphere as well as cool and purify it. Storage batteries are another source of these impurities. Single, compartment group, and local duct systems are all components that can be found in air conditioning systems. Both in areas where they sleep and in those where they do not sleep, crew members are provided with conditions that are comfortable in terms of temperature and humidity. These systems are also able to clean the air in sanitary areas, as well as in rooms and galleries. Additionally, the air in the compartments is mixed thanks to these systems[2].The primary components of a composite material that is reinforced with fibres are the fibres themselves. These fibres are responsible for bearing the majority of the load that is applied to a composite structure. It is very important
to choose the appropriate orientation, amount, and type of fibres for a laminate because these factors influence the following characteristics of the laminate[3].
In a composite material that is strengthened by fibre, the role of the matrix can be given as follows:
-
The matrix provides protection for the fiber surface from any mechanical aberration that may occur.
-
The Matrix acts as a barrier that protects against unfavorable environmental conditions.
-
The matrix acts as a conduit for the transmission of stress between the fibers.
-
The constituents of the matrix are typically used for the first level of classification in composites. Organic Matrix Composites, also known as OMCs, are one of the three primary types of composites, along with Metal Matrix Composites, also known as MMCs, and Ceramic Matrix Composites (CMCs). Organic matrix composites are commonly known as carbon-carbon composites [4]. In general, it is assumed that organic matrix composites include composites of two classes, namely PMCs (Polymer Matrix Composites) and CMCs (Carbon Matrix Composites) (carbon matrix composites). The second level of classification is referred to as the reinforcement form. Examples are laminar composites and fiber reinforced composites (FRPs). FRPs, also known as Fiber Reinforced Composites, can be further subdivided into two categories: those that consist of discontinuous fibers and those that consist of continuous fibers[5].
Fig 1. Methodology
A composite material is a system that is created by the synthetic assembly of two or more materials. It is characterized by distinct interfaces between the individual components of the system. The component of the material that provides both the strength and the modulus is a fiber
that is embedded in a resin. They produce combined properties, the achievement of which is not possible by any of the components acting alone[6]. These combined properties cannot be achieved. Composite materials have a modulus that is relatively high in terms of their strength. A laminate is a form of reinforced composite that is very common and used in structural applications. The term "laminate" describes this form. In order to obtain it, numerous thin layers of fibers and matrix are stacked. The consolidation of those components gives it the thickness that was desired. When making the composite laminate, the sequence of stacking the fibers on each layer and the orientation of the fibers can each be checked to ensure that the desired properties, such as mechanical and physical, are achieved [7]. Materials of this type can be found with damping coefficients of high values. The capacity of a structure to reduce the transmission of vibrations that are caused by mechanical disturbances is represented by the property of damping in that structure. The damping factor of a material is a measurement of the material's damping.
Fig 2. (a) 3D model of the centrifugal blower (b) Hexa mesh in ANSYS
-
-
METHODS AND MATERIAL
-
Static analysis
The displacements, stresses, strains, and forces in structures or components caused by loads that do not induce significant inertia and damping effects are determined by a static structural analysis.When designing a structure, performing a static analysis is a crucial step in the process. The response of the structure to the external forces that have been applied can be determined by using static analysis[8]. In addition, the static analysis is carried out whenever the structure is subjected to external displacements such as differential support settlements. These kinds of movements can cause the structure to move in unanticipated ways.
-
Modal analysis
The most fundamental type of dynamic analysis is called modal analysis, and it can provide information about the natural frequencies at which a structure will resonate. These naturally occurring frequencies are of the utmost significance in a number of different engineering subfields. It is common practice to tune the suspensions of passenger cars and race cars so that they resonate at different natural frequencies [9]. The process of determining the inherent dynamic characteristics of a system in the form of natural frequencies, damping factors, and mode shapes and then using these to formulate a mathematical model for the system's dynamic behavior is referred to as modal analysis. Modal analysis can also be thought of as a subset of frequency analysis.
-
Harmonic analysis
Harmonic analysis is a subfield of mathematics that focuses on the study and generalization of the concepts of Fourier series and Fourier transforms, as well as the representation of functions or signals as the superposition of fundamental waves (i.e., an extended form of Fourier analysis)[10].
-
Composite materials
The term "composite material" refers to a solid material that is produced when two or more distinct substances, each of which possesses its own properties, are combined to create a new substance whose properties are superior to those of the original components when applied to a particular purpose. This new substance is referred to as "composite"[11].
-
-
RESULT AND DISCUSSION
-
Static analysis
Through finite element analysis (FEA), the results of a static analysis, modal analysis, and Fourier analysis are presented here. Composites and Aluminum blowers are selected for further investigation [12]. Figure 3 depicts the deformation that occurred within the aluminum blower. It demonstrates the deformation of the aluminum blower. The utmost deflection that could be achieved was 0.00035 millimeters. The utmost equivalent stress that could be achieved was 8.87 N/mm2. Figure 3 illustrate displacements and stresses in x-, y-, and z- directions. The stresses and deformations that are caused by aluminum blowers are outlined in Table 1. The maximum amount of deflection that can be caused by induction in a metallic blower is 0.00035 millimeters. It falls within the suitable range of values. Therefore, the planning that prioritizes rigidity also prioritizes safety. The maximum amount of stress that was induced is 8.87 MPa. The strain level may not exceed 160 MPa. It's significantly lower than that. Therefore, taking into consideration the strength, it's a design that is safe. Table 1. Aluminum blowers static analysis results
Aluminum Blower
Results
Static structural total deformation
0.00035 millimeter
Static structural equivalent stress MPa
8.87 Newton/millimeter2
Static structural Maximum principal stress MPa
5.57 Newton/millimeter2
Static structural directional deformation (X-axis) mm
0.00034
Static structural directional deformation (Y-axis) mm
0.00035
Static structural directional deformation (Z-axis) mm
4.7E-5
An experiment is carried out to calculate stresses in order to test the bonding stress among the various layers, as well as the inter-laminar shear of the composite blower, and to analyze the results statically. A total deformation of 0.0038 millimeters was discovered in the composite blower, which can be seen in figure 3. As shown in figure 3, the maximum normal stress that could be applied in the x direction was 4.534 Newton/mm2. The stresses and deformations caused by induction are outlined in Table 2
for the composite blower. The deflection that was obtained for the composite blower over all of its layers was approximately 0.0038 millimeter. It has a larger diameter than the aluminium blower, which measures 0.00035 millimeters. Calculations of inter-laminar shear stresses were carried out for the composite blower, and it was discovered that the layer experienced the greatest amount of inter-laminar shear stress.
Composite Blower
Results
Static structural total deformation
0.0038 millimeter
Static structural equivalent stress MPa
16.87
Newton/millimeter2
Static structural Maximum principal stress MPa
15.53
Newton/millimeter2
Static structural directional deformation (X-axis) mm
0.00378
Static structural directional deformation (Y-axis) mm
0.000371
Static structural directional deformation (Z-axis) mm
0.0008
Table 2. Results of Static analysis of composite blower
Fig 4. Modal analysis of aluminum and composite blower
Modes No.
Aluminum blowers Natural frequencies
Composite blowers Natural frequencies
%Variation
1
0 Hz
0 Hz
0
2
0 Hz
0 Hz
0
3
9.54 Hz
5.67 Hz
41.07
4
16.07 Hz
11.59 Hz
27.88
5
17.50 Hz
12.87 Hz
26.46
6
27.32 Hz
20.2 Hz
25.93
Table 3. Natural frequencies of aluminium and composites
Fig 3. Static structural analysis of aluminium and composite blower
The Eigen value is analyzed for both the composite and the aluminium blower. This analysis does not represent the response to any loading, but rather it produces natural frequencies and Eigen vectors that form in the blower's corresponding mode shapes when there is no dissipation of energy due to dampness. This investigates the free vibration of an undamped blower in the absence of external loads and damping. As can be seen in Tables 1 and 2, we were able to obtain the first six natural frequencies for the aluminium composite blower.
-
Modal analysis
Figure 4 depicts the modal analysis of a blower made of aluminium and a composite material. The Eigen value is analyzed for both the composite and the aluminium blower. This analysis does not represent the response to any loading, but rather it produces natural frequencies and Eigen vectors that form in the blower's corresponding mode shapes when there is no dissipation of energy due to dampness. This investigates the free vibration of an undamped blower in the absence of external loads and damping. As can be seen in Table 3, we were able to obtain the first six natural frequencies for the aluminium composite blower s.
-
Harmonic analysis
In table 4, we can see the maximum and minimum displacements of component X, Y, and Z that were obtained in the harmonic analysis for the Composite blower due to the pressures. Harmonic response testing is performed on blowers made of composite and aluminium materials respectively. According to the observations, the performance of the blower made of aluminium was inferior, while the performance of the blower made of composite was superior. Peaks of natural frequency can be seen in blowers made of composite material as well as blowers made of aluminium. There is a decrease in the amount of displacement that occurs in blowers made of composite material when compared to blowers made of aluminium. Since vibration is controlled by damping, a blower made of composite will have less acceleration, which will result in less vibration caused by the blower itself.
Harmonic response analysis indicates benefits of blower made of composite as under:
-
The blower made of composite has a significantly lower mass when compared to the blower made of aluminium.
-
A blower made of composite material experiences a lower level of vibration in the high-frequency range when compared to a blower made of aluminum.
-
Since layup sequence and stiffness of the blower is high, therefore, the natural frequency of composite blower is reduced
Displacements of Composite Blower |
Minimum |
Maximum |
X-Component |
-0.0038 |
0.0037 |
Y-Component |
-0.0037 |
0.0037 |
Z-Component |
-0.00069 |
0.00082 |
Table 4. Maximum and Minimum Displacements of composite blower
Fig 5. Harmonic analysis of aluminium and composite blower
CONCLUSIONS
Present work draws conclusion as given below:
The stresses of the composite blower that were obtained in the static analysis were within the allowable stress limits, coming in at 16.876 N/mm2. As a consequence of the fact that the layup sequence and stiffness of the blower are both high, the natural frequency of the composite blower is decreased. The blower made out of composite material is lighter in weight compared to the blower made out of aluminium. According to the findings of the harmonic analysis, it is abundantly clear that blowers made of composite have a greater damping effect. As a consequence, it is responsible for the regulation of the vibration levels.
REFERENCES
[1] Matuzovi M (2022) Analysis of conjugate heat transfer in a roots blower and validation with infrared thermography . 16:. https://doi.org/10.1016/j.ijft.2022.100234 [2] Patel YM, Jain S V., Lakhera VJ (2020) Thermo-hydraulic performance analysis of a solar air heater roughened with reverse NACA profile ribs. Appl Therm Eng 170:114940. https://doi.org/10.1016/j.applthermaleng.2020.114940 [3] Poursaeidi E, Babaei A, Behrouzshad F, Mohammadi Arhani MR (2013) Failure analysis of an axial compressor first row rotating blades. Eng Fail Anal 28:2533. https://doi.org/10.1016/j.engfailanal.2012.08.021 [4] Kumar S, Verma SK (2022) Heat transfer and fluid flow analysis of sinusoidal protrusion rib in solar air heater. Int J Therm Sci 172:107323. https://doi.org/10.1016/j.ijthermalsci.2021.107323 [5] Goel V, Kumar R, Bhattacharyya S, et al (2021) A comprehensive parametric investigation of hemispherical cavities on thermal performance and flow-dynamics in the triangular-duct solar-assisted air-heater. Renew Energy 173:896912. https://doi.org/10.1016/j.renene.2021.04.006 [6] Bianco V, Szubel M, Matras B, et al (2021) CFD analysis and design optimization of an air manifold for a biomass boiler. Renew Energy 163:20182028. https://doi.org/10.1016/j.renene.2020.10.107 [7] Wani M, Swain A, Ukil A, et al (2022) Optimizing the overall performance of forced extraction systems: A multi-objective framework. Build Environ 221:109214. https://doi.org/10.1016/j.buildenv.2022.109214 [8] Wang J, Zhang Y, Zhang W, et al (2022) Design and evaluation of a lab-scale tungsten receiver for ultra-high-temperature solar energy harvesting . Appl Energy 327:120135. https://doi.org/10.1016/j.apenergy.2022.120135 [9] El-Emam MA, Zhou L, Shi W, Han C (2021) Performance evaluation of standard cyclone separators by using CFDDEM simulation with realistic bio-particulate matter. Powder Technol 385:357374. https://doi.org/10.1016/j.powtec.2021.03.006 [10] Venkatesh S, Suresh Kumar R, Sivapirakasam SP, et al (2020) Multi-objective optimization, experimental and CFD approach for performance analysis in square cyclone separator. Powder Technol 371:115129.https://doi.org/10.1016/j.powtec.2020.05.080
[11] Venkatesh S, Sakthivel M, Saranav H, et al (2020) Performance investigation of the combined series and parallel arrangement cyclone separator using experimental and CFD approach. Powder Technol 361:10701080. https://doi.org/10.1016/j.powtec.2019.10.087 [12] Zhao X, Li H, Yang S, et al (2021) Blade vibration measurement and numerical analysis of a mistuned industrial impeller in a single-stage centrifugal compressor. J Sound Vib 501:116068. https://doi.org/10.1016/j.jsv.2021.116068