
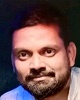
- Open Access
- Authors : Mr.Chavan U.J, Prof.Shitole J.S, Prof.Kathale S.S.
- Paper ID : IJERTV13IS030212
- Volume & Issue : Volume 13, Issue 03 (March 2024)
- Published (First Online): 19-04-2024
- ISSN (Online) : 2278-0181
- Publisher Name : IJERT
- License:
This work is licensed under a Creative Commons Attribution 4.0 International License
Analysis and Optimization of Contact Stresses in Spur Gear using Finite Element Analysis
Mr.Chavan U.J ,Prof.Shitole J.S, Prof.Kathale S.S.
(Department of Mechanical Engineering, DGOI,FOE, Swami-Chincholi)
ABSTRACT:
Spur gear is cylindrical shaped gear in which the teeth are parallel to the axis. It is easy to manufacture and it is mostly used in transmitting power from one shaft to another shaft up to certain distance & also used to vary the speed & Torque. The cost of replacement of spur gear is very high and also the system down time is one of the effect in which these gears are part of system. Failure of gear causes breakdown of system which runs with help of gear. When gear is subjected to load, high stresses developed at the root of the teeth, Due to these high stresses, possibility of fatigue failure at the root of teeth of spur gear increases. There is higher chance of fatigue failure at these locations. So to avoid fatigue failure of the gear, the stresses should be minimized at maximum stress concentrated area. Design of spur gear can be improved by improving the quality of material, improving surface hardness by heat treatment, surface finishing methods. Apart from this stress also occurs during its actual working.
Hence it is important to minimize the stresses. These stresses can be minimized by introducing stress relief features at stress zone. Many simulation packages are available for checking the different values of stresses. Simulation is doesnt give exact results but gives a brief idea where stresses are induced. Hence experimental stress analysis method can also be adopted for studying stresses.
Keywords: Spur gear,Stress,Simulation, Ansys
-
INTRODUCTION
Spur gear is a cylindrical shaped gear in which the teeth are parallel to the axis. It is easy to manufacture and it is mostly used in transmitting power from one shaft to another shaft up to certain distance & it is also used to vary the speed & Torque. e.g. Watches, gearbox etc.
The cost of replacement of spur gear is very high and also the system down time is one of the effect in which these gears are part of system. Failure of gear causes breakdown of system which runs with help of gear. e.g. automobile vehicle.
When gear is subjected to load, high stresses developed at the root of the teeth, Due to these high Stresses, possibility of fatigue failure at
Hence it is important to minimize the stresses. These stresses can be minimized by introducing stress relief features at stress zone. Many simulation packages are available for checking the different values of stresses. Simulation is doesnt give exact results but gives a brief idea where stresses are induced. Hence experimental stress analysis method can also be adopted for studying stresses:
Gears have a wide variety of applications. Their applications vary from watches to very large mechanical units like the lifting devices and automotives. Gears generally fail when the working stress exceeds the maximum permissible stress. Number of studies has been done by various authors to analyze the gear for stresses. Gears have been analyzed for different points of contact on the tooth profile and the corresponding points of contact on the pinion. In this study
Then the variation stress in root fillet region is found, which is then used for the study of variation of various parameters of stress reducing features. The effect and use of stress relief feature in geometry of gear is studied as reported by researchers. A study of the optimum size and location of the stress relief features for pinion and gear is proposed which help in reducing the fatigue failure in gears.
Gears are the most common means of transmitting power in the modern mechanical engineering world. They vary from a tiny size used in watches to the large gears used in watches to the large gears used in lifting mechanisms and speed reducers. They form vital elements of main and ancillary mechanisms in many machines such as automobiles, tractors; metal cutting machine tools etc. toothed gears are used to change the speed and power ratio as well as direction between input and output.
Spur gear is a cylindrical shaped gear in which the teeth are parallel to the axis. It has the largest applications and, also, it is the easiest to manufacture. Spur gears are the most common type used. Tooth contact is primarily rolling, with sliding occurring during engagement and disengagement. Some noise is normal, but it may become objectionable at high speeds.
-
LITRATUREREVIEW
Andrews J.D, [1] investigated the finite element analysis of bending stresses in involute gears. This paper describes the use of the finite element method for predicting the fillet stress distribution experienced by loaded spur gears. The location of the finite element model boundary and the element mesh density are investigated. Fillet stresses predicted by the finite element model are compared with the results of photo elastic experiments. Both external and internal spur gear tooth forms are considered.
Costopoulos Th. [2] studied the reduction of gear fillet stresses by using one-sided involute teeth. For increasing the load carrying capacity of geared power transmissions several tooth designs alternative to the standard involute have been proposed. The use of non-involute teeth has a number of disadvantages and for this reason asymmetric involute-type teeth have been studied as a promising alternative. In this paper the idea of one-sided involute asymmetric spur gear teeth is introduced to increase load carrying capacity and combine the good meshing properties of the driving involute and the increased strength of non involute curves. These novel teeth are intended for constant direction of rotation although they can be used in a limited way for reverse rotation. Both flanks are fully generated by a hob, the design of which is also investigated. The increase in load carrying capacity can reach up to 28% compared to the standard 200 involute teeth.
Hebbal M.S, [3] explains the reduction in root fillet stress in spur gear using internal stress relieving features. Gear teeth failure due to fatigue is a common phenomenon observed. Even a slight reduction in the root tensile stress results in great increase in the fatigue life of a gear. If gear fails in tensile fatigue, the results are catastrophic and occur with little or no warnings. Therefore for all the reasons mentioned above, this work is of more practical importance. For many years, gear design has been improved by using improved material, hardening surfaces with heat treatment and carburization, and shot penning to improve surface finish etc. Few more efforts have been made to improve the durability and strength by altering the pressure angle, using the asymmetric teeth, altering the geometry of root fillet curve and soon. Most of the above methods do not guarantee the interchangeability of the existing gear systems. This work presents the possibilities of using the stress redistribution techniques by introducing the stress relieving features in the stressed zone to the advantage of reduction of root fillet stress in spur gear. It also ensures interchangeability of the existing gears systems. In this work, combination of
circular and elliptical stress relieving features are used and better results are obtained than using circular stress relieving features alone which were used by earlier researchers. A finite element model with a segment of three teeth is considered for analysis and stress relieving features of various sizes are ntroduced on gear teeth at various locations. Analysis revealed that, combination of elliptical and circular stress relieving features at specific, locations are beneficial than single circular, single elliptical, two circular or two elliptical stress reliving features.
Senthil Kumar V. [4] focused the optimization of asymmetric spur gear drives to improve the bending load capacity. In a given size of symmetric involute gear designed through conventional approach, as the load carrying capacity is restricted at the higher pressure angle due to tipping formation, the use of the asymmetric toothed gear to improve the fillet capacity in bending is examined in this study. Non-standard asymmetric rack cutters with required pressure angles and module are developed to generate the required pinion and gear of a drive with asymmetric involute surfaces and trochoidal fillet profiles. The respective profiles thus generated are optimized for balanced fillet stresses that are equal and possibly the lowest also. For this study of optimization, several non- standard asymmetric rack cutters are designed to accommodate different combinations in the values of pressure angle, top land thickness ratio, profile shift, speed ratio and the asymmetric factors. However for any drive with a given center distance and a speed ratio, only two non-standard asymmetric rack cutters, one for the pinion and other for the gear are used to generate a required numbers of pinion and gear with different cutter shift values for the purpose of optimization. The influence of these parameters on the maximum fillet stress has been analyzed to suggest the optimum values of these parameters that improve the fillet capacity in bending. The optimization of the asymmetric spur gear drive is carried out using an iterative procedure on the calculated maximum fillet stresses through FEM for different rack cutter shifts and finally the optimum values of rack cutter shifts are suggested for the given center distance and the speed ratio of an asymmetric gear drive. Comparisons have also been made successfully with the results of the AGMA and the ISO codes for symmetric gears to justify the results of the finite element method pertaining to this study.
Ulrich T.W.[5] explains the auxiliary holes for stress reduction. Stress concentration reduction in a plate is accomplished by introducing optimum size holes and regularly placed. This paper presents a method based on boundary elements and mathematical programming to determine these auxiliary holes. The mathematical programming method consists of a modified
Newton's method and subsequent parallel tangents method (PARTAN). A solution is presented for an elliptical hole in a tension strip.
-
ANALYSIS
A finite element model with segment of five teeth is considered for analysis. Apoint load of 300N is applied at the teeth are meshed with two dimensional nodes. The boundary conditions used, program is developed in ansys to automate the process of geometry creation, meshing, applying boundary conditions and displaying the results. Gear teq software is used for geometry of gear teeth, the location and size of the stress relieving features A spur gear with module 20 mm, number of teeth 20, pressure angle 20degrees is considered for analysis. The FEA results of root fillet stress without holes are compared with the stress calculated using the gear root fillet stress with holes. The maximum principal stress is obtained without any stress relieving features. Used for stress reliving feature.
Configurations of stress reliving feature used, for the various analyses are as follows:
Circular stress reliving feature of different sizes and at same location (Varying dia.2 holes).
-
Circular stress reliving feature of same size at different locations (1 hole).
-
Circular stress reliving feature of same size at different locations (fixing the dia. of 2 hole).
Stress relief features of different sizes and at same location (2Holes)
Application of Stress relief features of different sizes and at same location (with 2 Holes) is shown in Fig. 1 Diameter of hole varies from 1mm to 9 mm and at the same time locations of holes is kept same. For first hole value for X- axis
=9.39 mm and for Y axis= 13.86 mm. For second hole value for X axis=13.47mm and for Y axis=
9.87 mm. Stress value is minimum for diameter 8 mm
6.353 N/mm2
Fig.1.Equivalent stress maximum for diameter 8 mm
Table 1 Stress relief features of different sizes and at same location (2Holes)
Stress relief features of same size at different locations (1- hole)
Application of Stress relief features of same sizes and at different location (with 1 Holes) is shown in Fig.2 Diameter of hole is same 8 mm and at the same time locations of holes are varies. For first hole value for X axis Varies in between for x axis 9.39 mm to 15.39 mm and for Y axis in between 13.11 to 14.65
mm. varying location for getting minimum value of stress at that location.
Fig.2Equivalent stress maximum for location X=9.39 mm and Y= 13.86 mm
IJERTV13IS030212
(This work is licensed under a Creative Commons Attribution 4.0 International License.)
Table2 Stress relief features of same size at different locations (1- hole)
Stress relief features of same size at different locations (two holes)
Application of Stress relief features of same sizes and at different location (with 2 Holes) is shown in Fig.3 Diameter of hole is same 8 mm andat the same time locations of holes are varies. For first hole value for Xaxis9.39mmand for Y axis in between 13.9 mm. and at the same time varying locations for another hole for X axis
=13.23mm to 13.79 mm,ForY axis=9.46 mm to 12.54mm.
Fig. 3. Equivalent stress maximum for diameter 8 mm with 2 holes
Table3Stress relief features of same size at different locations (two holes)
-
-
RESULT AND DISCUSSION
Equivalent Stress (Mpa)
It is seen that the maximum principal stress at root fillet is 7.5 N/mm2 without any stress relieving features Maximum principal stress v/s orientation of major axis of the circular stress reliving features at more beneficial locations and combination of size, are plotted in Fig. 4.
Principal stresses in the gear segment with circulars stress reliving features are as shown in Fig.
3. Different cases are considered for analysis choosing different values of parameters viz. size of hole, locations of holes and hole and varying number of holes.
Analysis shows that the case with two circular holes having parameters for 1st hole ,x=
9.39 mm, y= 13.86 mm, and 2nd hole, x= 13.47mm, y= 9.87
mm. shows the greater benefit in comparison with other cases. As the location of stress relieving feature approaches the high stress effective zone up to a certain value, there results are found to be beneficial. Later on the benefit reduces, it indicating that the benefit becomes more sensitive as the location of the stress relieving features approaches the zone of stress concentration to a certain value only.
12.00
10.00
8.00
6.00
4.00
Equivalent Stress Maximum (N/mm2)
2.00
0.00
Diameter Of Holes (mm)
Equivalent Stress Maximum
It is important to note that introduction of more than one stress relieving feature has added advantages In one of the most beneficial location principal stresses in the gear segment with a combination of two circular stress reliving features are as shown in Fig. 3. A maximum of 15% reduction in maximum principal stress is obtained. Fig. 3 shows the stress pattern in gear with the combination of two circular stress relieving feature obtained in the above analysis at the most beneficial location. Fig. 4 shows a diameter of hole vs equivalent Stress
1
3
5
7
9
7.5
8.1
8.25
Fig4 Dimeter of hole Vs Equivalent Stress Maximum
450
400
350
300
250
EquivalentStres s
100
50
246810121416
POSITIONOFHOLES(X,Y)
Fig5 Position of hole Vs Equivalent Stress Max
6. CONCLUSION
Single stress reliving features did not improve gear stress. stress reduction by means of introducing of stress reliving feature is possible. Stress redistribution is highly sensitive to the change in size, Location and Number so select size, Location and Number very carefully. Using two holes as a stress reliving features gives more stress reduction. Small variation in size, location and number gives large difference in equivalent stress. Introduction of stress reliving feature at specific
location of specific size and number gives maximum reliving of stress otherwise strength of gear reduces.
REFERENCES
-
Andrews J.D. (1991) A Finite Element Analysis of Bending Stresses induced in external and internal involute spur gears, The Journal of Strain Analysis for Engineering Design, page no.153- 163.
-
Costopoulos Th. Spitas V. (2009) Reduction of gear fillet stresses by using one-sided involute asymmetric teeth,page no.1524 1534.
-
Hebbal M.S.,Math V.B.,Sheeparamatti
B. G. (2009) A Study on Reducing the Root Fillet Stress in Spur Gear Using Internal Stress Relieving Feature of Different Shapes, International Journal of Recent Trends in Engineering, Vol. 1, No. 5, May 2009, page no.163
165.
-
Senthil Kumar V., Muni D.V., Muthuveerappan G. (2008) Optimization of asymmetric spur gear drives to improve the bending load capacity, Mechanism and Machine Theory, page no. 829 858.
-
Ulrich T.W., Moslehy F.A. (1995) A boundary element method for stress reduction by optimal auxiliary holes, Engg. Analysis with Boundary elements, page no. 219 223.
IJERTV13IS030212
(This work is licensed under a Creative Commons Attribution 4.0 International License.)