
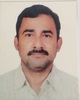
- Open Access
- Authors : Munawar Nawab Karimi , Salem Alabd , Amit Lawania , Homi Hussain, Kushal Chaturvedi, Mirza Ghufran Beg, Shahawaz Jalees
- Paper ID : IJERTV10IS050132
- Volume & Issue : Volume 10, Issue 05 (May 2021)
- Published (First Online): 21-05-2021
- ISSN (Online) : 2278-0181
- Publisher Name : IJERT
- License:
This work is licensed under a Creative Commons Attribution 4.0 International License
Analysis of Air-Water Cooled Condenser in Vapour Compression System
Munawar Nawab Karimi, Salem Alabd, Amit Lawania, Homi Hussain, Kushal Chaturvedi, Mirza Ghufran Beg, Shahawaz Jalees
Mechanical Engineering Department, JamiaMilliaIslamia, New Delhi, Delhi, India
AbstractThe development and performance enhancement of heat exchanger is major concern of emerging nascent technology. Performance enhancement contributes to minimize the operating cost and energy consumption. In this paper theoretical analysis of air-water cooled condenser is presented and a 3D (three dimensional) model of air-water cooled condenser has been made in ANSYS. The tubes in the model are half dipped in water and the other half exposedtoair. Copper tubes were used as they are the most thermally conductive common metal and aluminium fins were used because they are lightweight and flexible. The validation of theoretical values is carried out by the Computational Fluid Dynamics (CFD) software ANSYS.The use of such condensers might prove to be more beneficial for residential purposes.
Keywords:- Heat transfer, CFD,Viscous Laminar models, Simulation, ANSYS
-
INTRODUCTION
With the rapid growth of industrialisation and clearing of land, the average temperature of the environment has been increased within the last two decades. The reason for this gradual/exponential increase in temperature is the greenhouse effect and global warming. As the earths surface temperature rises and to achieve thermal comfort the use of air conditioning has also been increased which in turn has increased power consumption. The researchers of this domain have continuously tried to enhance the performance of air conditioners so that they become more efficient and consume less power.PrachaYeunyongkul, Passawat Watcharadumrongsak, Sampan Rittidech [1] tried to increase the efficiency of ACC by cooling ACC coils with the use of a hybrid condenser. K. Sumeru, C Sunardi, M.F.Sukri [2] in their work used condensate water to provide subcooling to the compressor discharge for split air conditioning system and reported about the augmentation in COP. Hua Chen, W.L.Lee, F.W.H.Yik [3] experimentally show about 17.4% increment in COP of split air conditioning system while using water cooled condenser relative to the air cooled condenser. A. Sirichaoroenpanich, S.Wiriyasart, R.Prurapark, P.Naphon
[4] boosted the thermal performance of an air conditioning system using a cooling water loop with the concentric helical coiled tube heat exchanger between the compressor unit and condenser unit for cooling the refrigerant whereas S.S.Hu, B.J.Huang [5] employed residential water-cooled air conditioners with a cellulose pad as filling material for cooling tower and observed that the COP of this kind of air conditioner is higher than the conventional air conditioner. W.L.Lee, Hua Chen, F.W.H.Yik [6] developed anempirical model for predicting the operational performance and consumption of energy for the use of water-cooled air conditioners. Jingyuan Xu, Jianying Hu, Limin Zhang, Ercang Luo [7] simulated novel shell tube and conventional shell tube heat exchanger to achieve better heat transfer power. E. Hajidavalloo [8] reported about the decrement in the power consumption by installing cooling pads on both sides of the air conditioner.Xiaojing Zhu et al [9] in their work found that the wet-bulb temperature has a huge effect on the heat transfer performance than the relative humidity for an evaporative condenser.Huanwei Liu, Qiushu Zhou, Yuling Liu, Peifeng Wang, Defa Wang [10] in their study of evaporative condenser reported about the increment in COP with the air velocity and spray rate whereas the decrement in COP with the increaseininlet air dry bulb temperature and frequency of compressor. M.R.Islam, K.A.Jahangeer, K.J.Chua [11]experimentally reported about the 28% hike in the COP of an evaporatively cooled air conditioning unit than the traditional air conditioning unit. M.Fiorentino, G.Starace [12] worked upon increasing heat transfer of evaporative condensers by applying a hybrid method on a countercurrent evaporative condenser. Zhiwei Huang, Yunho Hwang, Reinhard Radermacher [13] have proposed a new design to apply biomimicry to heat exchangers which increases heat transfer coefficients per unit area as well as reduce water consumption and pumping power. Manpreet Singh, Babool Rai, Vikul Vasudev [14] installed evaporative pads in vapour absorption and vapour compression refrigeration system and compared the COP of air-cooled and water-cooled condensers and concluded that WCC is much more efficient. M. Hosoz, A.Kilicarslan
[15] have performed a comparison of all three condensers including evaporative, air-cooled and water-cooled and concluded that water-cooled condenser has a better coefficient of performance than the evaporative condenser and evaporative condenser have a better coefficient of performance than the air-cooled condenser. G.P. Maheshwari, A.A Mulla Ali [16] have investigated both air-cooled and water-cooled based on peak power and energy consumption. K. Harby, Doaa.R.Gebaly, Nader.S.Koura, Mohamed.S.Hassan [17] reported that the evaporative condensers are much more effectivethan traditional condenser for hot region. Zongwei Han et al [18] tried to reduce the power consumption by maximizing the utilization of natural cold energy using an evaporative condenser with water cooling condensation. Chnag Yong Park, Pega Hrnjak [19], numerically and experimentally investigated the performance of microchannel condenser and conclude that microchannelcondenser are much more efficient than round tube condenser.P Dalai, P.Nanda, C.Mund, D.Mishra, Abhijeet Gupta [20] using the concept of humidification- dehumidification focused on the utilization of condensed water for drinking and other purposes. H.N.Patel, Y.R.Patel, D.Patel, J.Patel, S.K.Kulkarni [21] optimized performance coefficient of air-cooled condenser by spraying water on the fins of the condensing unit at regular intervals. H.Yang et al [22] reduced the energy consumption around 2.37%-13.53% with the combination of a spray evaporative cooling system and an air cooled chiller for a refrigeration unit. J.Wei, J.Liu, X.Xu, J.Ruan, and G.Li [23] using vertical tube evaporative condenser instead of conventional finned tube type air cooled condenser increased the coefficient of performance by 30%. Mulla Irfan Ahmad, Jameel Basha S.M, Viswanatha Chari V, Srinivas Kumar G [24] have used a combination of R290 and R600a as a refrigerant which in turn is less toxic as well as ozone friendly and provides as an alternative. T Hussain, AK Singh, A.Mittal, A Verma, Z Alam [25] has increased the coefficient of performance by employing evaporative cooler using cellulose and steel
Pitch of tubes in plane perpendicular to flow (P1) = 50.0 mm
Boundary Conditions
Mass flow rate of air (.) = 0.1687 kg/s Density of air () = 1.2170 kg/m3
() = 15.9*106 m2/s
Prandtl number(Pr) = 0.705
Thermal conductivity of air (Kair)= 26.9*103 W/mK Specific heatcapacity of air (Cpa) = 1007 J/kg.K Refrigerant inlet temperature ( ) = 335 K
Air free stream temperature () = 313 K
Governing Equations
Surface area of the fins (Af) is given by,
1 2 2
wire pads.
From the literature reviewed above, it has been observed
=
[(+) 2
(
) + ] (1)
that a lot of work has been performed to increase the COP of an air conditioning unit by proposing the different design of water cooled, air-cooled and evaporative condensers or by instaling cooling pads and by the usage of microchannel condenser. In contrast to the above, the present literature proposed a novel concept of water cum air cooled condenser for the split air conditioning system.
-
THEORETICAL ANALYSIS:
Surface area of tubes between fins(Aw) is given by,
= [ ] (2)
(+)
Total surface area of air side condenser (Aa),
Aa= Af+Aw (3)
Min cross sectional flow area () is given by,
-
Air Side
= na
[12 ] (4)
+
Assumptions
The assumptions which are to be considered in thepresent analysis are as follows:
-
Hydrodynamically and thermally fully developed flow
Total tube surface area (without fins) At is given by,
At = N*Lt* *Dr (5)
Reynolds Number(Re) is gven by,
.
-
Tube wall remains at constant temperature
-
Steady State with no heat generation
Vmax
=
(6)
-
High fins with In-line array
R = ×
e
e
(7)
Geometrical Parameters
External diameter of condenser tube at fin root (Dr) = 22.7 mm
External diameter of fin(Dt) = 32.7 mm Height of fin (L) = 5.0 mm
Thickness of fin (w) = 0.5 mm
where,
is the kinematic viscosity of air .
is maximum velocity
The Nusselt number ( Nu) is given by
0.375
N = 0.3(P )0.333 ( )0.625 ( ) (8)
u r
Fins spacing(s) = 5.0 mm
Total length of air side condenser tube(Lt) = 1.5 m
Average heat transfer coefficient () for air is calculated using the formula below,
Number of air side tubes in a row (na) = 3 Total number of air side tubes (Na) = 3
= Nu
(9)
The efficiency ( ) of the radial fin can be determined by modifying the efficiency of the longitudinal fin otherwise it can be calculated by graph.
Heat transfer effectiveness of heat exchanger is:
=
(15)
= tanh
(10)
Where, = actual heat transfer rate between refrigerant and cooling water
Where,
= ( 1) (1 + 0.35 ln ) (11)
= Thermodynamically limited maximum possible heat transfer rate.
2 1
Hence the effective average heat transfer coefficient () is
= ( ) ( ) (16)
given by,
=
(17)
= +]
(12)
[NTU is number of transfer unit for the heat exchanger which phase change occurs
Log mean temperature difference experienced by air ()
is given by,
NTU = ln(1 ) (18)
1
.
Over all heat transfer coefficient () is given by,
= ( ) [
.
.
] (13)
( )
( )
= (19)
Rate of heat rejected to air side ( ) is calculated by,
= (14)
Log mean temperature difference experienced by water ( ) is given by,
-
-
WATER SIDE :
=
(20)
Assumptions
The assumptions which are to be considered in thepresent analysis are as follows:
-
Counter flow between hot fluid and cold fluid.
-
Turbulance is present in side the shell.
-
Ignore sensible heat removal by the condenser.
-
Geometrical Parameters
Length of water box = 588 mm
The formula below is used to obtain water outlet temperature ()
= × × ( ) (21)
Here = represents the heat given out by condenser for the three tubes dipped in water.
Total heat rejected= + (22)
1
Total length of water side condenser tube(Lw) = 1.5 m
= 3
21
(23)
Total number of water side tubes (Nw
Boundary Conditions
) = 3
12 are found out using p-h chart and 3 is calculated using total heat rejected
-
-
CFD ANALYSIS:
Mass flow rate of refrirerant ( ) = 0.047 kg/s Mass flow rate of water( ) = 0.1 kg/s
Saturation temperature of the refrigerant() = 335 K Inlet temperature of the water () = 285 K
Specific heatcapacity of water (Cpw) = 4184 J/kg.K Specific heatcapacity of refrigerant (Cpr) =1560 J/kg.K
Latent heat of condensation of refrigerant() = 161 KJ/kg.K
Condensation pressure= 25 bar
Total Surface area of water side tube (A) = 0.106917 m2
Governing Equations
-
Modelling
Fig 1. Prototype of AWCC Condenser
In this section 3D (three dimensional) model of a condenser which is both air cooled and water cooled has been made in ANSYS by Computational Fluid Dynamic Modelling (CFD modelling) . The condenser modelled for present study is show in Fig.1. The model consists of air cooled part and a water cooled part. The refrigerant used in condenser pipes in the study is R-22. To accommodate water for the water cooled part a box has been designed as shown and condenser tubes dipped in the box in order to be water cooled. Inlet and outlet is provided in the box for the entry and exit of the water. Fins made of aluminium have been provided on the
air cooled part to disperse the heat more quickly.
Table I. Condenser specification dimensions
Total length of condenser tubes
3 m
Length of water box
588 mm
Internal diameter of fins
22.7 mm
External diameter of fins
32.7 mm
Fins spacing
5 mm
Thickness of fins
0.5mm
Diameter of condenser tubes
22.7 mm
-
Numerical Scheme
Ansys fluent software is used to find out the solution of governing equations. Viscous-Laminar model is used for simulation. Coupled method is selected for solution. To obtain the convergence in the solution 1e-06 is the absolute criteria for residuals.
Table II. Properties of R-22
Density(kg/m3)
Specific Heat(J/Kg-K)
Thermal Conductivity(W/m- k)
Viscosity (Kg/m-s)
1069
1560
0.0658
0.001
Table III. Boundary Conditions at prototype
S.No
Location
Boundary Conditions
Thermal Conditions
1
Refrigerant inlet
mass-flow-inlet
Temperature
2
Water inlet
mass-flow-inlet
Temperature
3
Refrigerant outlet
Mass-flow-outlet
–
4
Water outlet
Mass-flow-outlet
–
5
Adiabatic wall
wall
Heat flux
6
Air side tube
wall
Convection
7
fins
wall
Convection
8
Refrigerant side tube
Interface
Temperature
9
Air side tube
Interface
Convection
10
Water side tube
Interface
Convection
11
fins
Interface
Convection
Table IV. Residual Table
Residual
Absolute Criteria
Continuity
1e-06
x-velocity
1e-06
y-velocity
1e-06
z-velocity
1e-06
Energy
1e-06
-
Grid Test
Fig.2 Mesh with Element size: 5
Fig.2 Mesh with Element size: 5
Grid independence study is performed to eliminate/reduce the influence of the number of grids/grid size on the computational results.If the results tend towards identical, the grid is considered as grid independent
Table V. Comparison for Grid Independence
S.No
Element Size
Nodes
Elements
Water Outlet Temp (K)
Mesh Behaviour
1
4
191281
496170
299.74
Fine
2
5
178279
407367
299.99
Fine
3
6
164320
371827
302.34
Fine
4
7
162471
363090
310.23
Fine
5
15
162024
360856
315.47
Medium
6
25
161981
360571
319.76
Coarse
It has been observed from the table above that there is a sudden change in water outlet temp after 5 mm element size. Variation of water outlet temp is 0.42% and change in pressure at water outlet is approching to zerotherefore mesh with Element size 5 mm (Fig.2) which is fine in nature and has 178279 nodes and 407367 elements is selected for analysis.
-
Result
The temperature of the refrigerant at the inlet and outlet is 62°C and 43°C which clearly validates our assumption, the outlet temperature of refrigerant turns out to be slightly less than assumed because of sub cooling and the temperature of the water at the inlet and outlet is found to be 12°C and 31°C which also validate the temperature obtained through calculation (equation 21). Temperature around the fins turns out to be 42°C.
Fig 3. Contour of static temperature
Fig.5 Contour of Static Temperature of Fins
Fig.5 Contour of Static Temperature of Fins
Fig.4 Contour of Static Temperature of Fins
Fins have been taken on air cooled condenser side and the air flowing over the fins is around 313 K. The material chosen for fins is aluminium and the convective heat transfer rate over the fins is 44.84 W/ m2 K .Temperature of the fins using CFD analysis comes around 42 °C.
Fig.5 Contour of Velocity Magnitude
Fig.6 Contour of Static temperature of condenser tubes
-
-
CONCLUSION
This paper gives you a 3D model of air water cooled condenser designed in ANSYS by CFD modelling.thecomparision of parameter obtained using
theoretical calculations is validated using CFD analysis.The COP obtained for AWCC is 6.22 which is much higher than traditional air conditioner.Therefore,itis concluded that the coefficient of performance of residential air conditioner can be enhanced by using air water cooled condenser in place of air-cooled or water-cooled condenser.
REFERENCES
-
P. Yeunyongkul, P. Watcharadumrongsak, and S. Rittidech, Research Article, vol. 10, no. 4, pp. 2327, 2016, doi: 10.14456/sustj.2016.14.
-
K. Sumeru, C. Sunardi, and M. F. Sukri, Effect of compressor discharge cooling using condensate on performance of residential air conditioning system Effect of Compressor Discharge Cooling Using Condensate on Performance of Residential Air Conditioning System, vol. 020002, no. August, 2018, doi: 10.1063/1.5049962.
-
H. Chen, W. L. Lee, and F. W. H. Yik, Applying water cooled air conditioners in residential buildings in Hong Kong, vol. 49, pp. 14161423, 2008, doi: 10.1016/j.enconman.2007.12.024.
-
A. Siricharoenpanich, S. Wiriyasart, R. Prurapark, and P. Naphon, Case Studies in Thermal Engineering Effect of cooling water loop on the thermal performance of air conditioning system, Case Stud. Therm. Eng., vol. 15, no. August, p. 100518, 2019, doi: 10.1016/j.csite.2019.100518.
-
S. S. Hu and B. J. Huang, Study of a high efficiency residential split water-cooled air conditioner, vol. 25, pp. 15991613, 2005, doi: 10.1016/j.applthermaleng.2004.11.011.
-
W. L. Lee, H. Chen, and F. W. H. Yik, Modeling the performance characteristics of water-cooled, vol. 40, pp. 14561465, 2008, doi: 10.1016/j.enbuild.2008.02.009.
-
J. Xu, J. Hu, L. Zhang, and E. Luo, A novel shell-tube water-cooled heat exchanger for high-capacity pulse-tube coolers, Appl. Therm. Eng., vol. 106, pp. 399404, 2016, doi: 10.1016/j.applthermaleng.2016.06.020.
-
E. Hajidavalloo, Application of evaporative cooling on the condenser of window-air-conditioner, vol. 27, pp. 19371943, 2007, doi: 10.1016/j.applthermaleng.2006.12.014.
-
X. Zhu, S. Chen, S. Shen, S. Ni, X. Shi, and Q. Qiu, Experimental study on the heat and mass transfer characteristics of air-water two- phase fl ow in an evaporative condenser with a horizontal elliptical tube bundle, Appl. Therm. Eng., vol. 168, no. September 2019, p. 114825, 2020, doi: 10.1016/j.applthermaleng.2019.114825.
-
H. Liu, Q. Zhou, Y. Liu, P. Wang, and D. Wang, Experimental study on cooling performance of air conditioning system with dual independent evaporative condenser, Int. J. Refrig., 2015, doi: 10.1016/j.ijrefrig.2015.03.012.
-
M. R. Islam, K. A. Jahangeer, and K. J. Chua, Experimental and numerical study of an evaporatively-cooled condenser of air- conditioning systems, Energy, 2015, doi: 10.1016/j.energy.2015.05.005.
-
M. Fiorentino and G. Starace, The design of countercurrent evaporative condensers with the hybrid method, Appl. Therm. Eng., vol. 130, pp. 889898, 2018, doi: 10.1016/j.applthermaleng.2017.11.076.
-
Z. Huang, Y. Hwang, and R. Radermacher, Review of nature- inspired heat exchanger Étude de la technologie des échangeurs de chaleur inspirée de la nature, Int. J. Refrig., vol. 78, pp. 117, 2017, doi: 10.1016/j.ijrefrig.2017.03.006.
-
M. Singh, B. Rai, and V. Vasudev, A Study on Performance Comparison of Air Cooled and Water Cooled Condenser in Vapour Absorption and Compression Refrigeration Systems, vol. 3, no. 4, pp. 462468, 2016.
-
M. Hosoz and A. Kilicarslan, Performance evaluations of refrigeration systems with air-cooled , water-cooled and evaporative condensers, vol. 696, no. September 2003, pp. 683696, 2004, doi: 10.1002/er.990.
-
G. P. Maheshwari and A. A. M. Ali, Comparative Study Between Air-Cooled and Water-Cooled Condensers of the Air- Conditioning Systems, 2004.
-
K. Harby, D. R. Gebaly, N. S. Koura, and M. S. Hassan, Performance improvement of vapor compression cooling systems sing evaporative condenser: An overview, Renew. Sustain. Energy Rev., vol. 58, pp. 347360, 2016, doi: 10.1016/j.rser.2015.12.313.
-
Z. Han et al., Simulation study on performance of data center air- conditioning system with novel evaporative condenser, Energy, vol. 210, p. 118521, 2020, doi: 10.1016/j.energy.2020.118521.
-
C. Y. Park and P. Hrnjak, Experimental and numerical study on microchannel and round-tube condensers in a R410A residential air- conditioning system ´ rimentale et nume ´ rique sur les microcanaux et les Etude expe ` tubes ronds dans un syste ` me de condenseurs a ´ sidentiel au 41, vol. 31, pp. 822831, 2008, doi: 10.1016/j.ijrefrig.2007.10.007.
-
P. Dalai, P. Nanda, C. Mund, D. Mishra, and A. Gupta, An Experimental Study on Water Harvesting from a Modified Window Air-Conditioner, Energy Procedia, vol. 109, no. November 2016, pp. 253260, 2017, doi: 10.1016/j.egypro.2017.03.058.
-
H. N. Patel, Y. R. Patel, D. Patel, J. Patel, and S. K. Kulkarni, Performance Analysis of Evaporative Cooled Condenser of Split Air Conditioner, vol. 1, no. 1, pp. 2024, 2020.
-
H. Yang, L. Rong, X. Liu, L. Liu, M. Fan, and N. Pei, Experimental research on spray evaporative cooling system applied to air-cooled chiller condenser, Energy Reports, vol. 6, pp. 906913, 2020, doi: 10.1016/j.egyr.2020.04.001.
-
J. Wei, J. Liu, X. Xu, J. Ruan, and G. Li, Experimental and computational investigation of the thermal performance of a vertical tube evaporative condenser, Appl. Therm. Eng., vol. 160, no. June, p. 114100, 2019, doi: 10.1016/j.applthermaleng.2019.114100.
-
Ahmad.M.I, Jameel Basha S.M, Viswanatha Chari V, Srinivas Kumar G, "Investigation of Performance of Vapor Compression Refrigeration System with Forced Air-Cooling Condenser with R600a and Hydrocarbon Mixture (R290 + R600a) as Refrigerant ", Advances in Industrial Automation and Smart Manufacturing, pp 1035-1041, 2021
[25] T Hussain, AK Singh, A.Mittal, A Verma, Z Alam,Performance evaluation of vapor compression refrigeration system by varying air flow rates in air-cooled and evaporatively cooled condensers , International Journal of Energy for a Clean Environment, 2020