
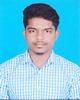
- Open Access
- Authors : Priyabrata Parida , Mausam Acharya , Ajay Purty , Chandan Soren, Sasank Shekhar Panda
- Paper ID : IJERTV10IS040317
- Volume & Issue : Volume 10, Issue 04 (April 2021)
- Published (First Online): 06-05-2021
- ISSN (Online) : 2278-0181
- Publisher Name : IJERT
- License:
This work is licensed under a Creative Commons Attribution 4.0 International License
Analysis of Connecting Rod Under Different Material Condition
Priyabrata Parida
Sasank Shekhar Panda
Assistant Professor Department of Mechanical Engineering
GIET University Rayagada, Odisha, India
Mausam Acharya
Department of Mechanical Engineering GIET University
Rayagada, Odisha, India
Department of Mechanical Engineering GIET University,
Rayagada, Odisha, India
Ajay Purty
Department of Mechanical Engineering GIET University
Rayagada, Odisha, India
Chandan Soren
Department of Mechanical Engineering GIET University
Rayagada, Odisha, India
Abstract: – Piston cylinder, crank, connecting rod, crank shaft and so on are the additives of IC engine in which connecting rod is the primary component. In IC engine maximum stressed component is connecting rod. A connecting rod act as a lever armby transmitting motion from piston to crankshaft. In this we studied the failure and strain analysis of the connecting rod beneath extraordinary loading situation by way of the usage of various materials like BeI220H, Al a360, Al 5083and Al(T6)7075, in order to get a better material and update the same old material, which is used to make connecting rod in every engine. With the intention to give an explanation for that in regular load and strain circumstance, an advanced stress and deformation evaluation is completed through ANSYS. For this reason, this study targets to carry out for the deformation, stress and strain analysis of the connecting rod of various materials. Based on which we can get a better material for the manufacturing of connecting rod. For a good way to get the solution the geometric model of connecting rod had been created in the software program (FUSION 360) and Dynamic analysis is carried out for determining of equivalent stress, maximum principle elastic strain and total deformation is calculated under loading conditions of compression at big end and small end of connecting rod.
KeywordsFusion 360, ANSYS, Connecting Rod
-
INTRODUCTION
Connecting rod is an important component of an automobile engine. All automobile that uses IC engine requires connecting rod. It connects the piston to the crankshaft, i.e., transfers the thrust from piston which is occurred due to gas pressure to the crankshaft [1 – 4].
The small end of the connecting rod interfaces with the piston with a piston pin. The big end of the connecting rod associates with the crankpin journal to give a rotate point on the crankshaft [5]. Combustion in IC Engine delivers very high burden which communicates to crankshaft by means of connecting rod hence connecting rod is exposed to numerous stress. The ductile and compressive burdens are created because of gas pressure, during compressive and power strokes the connecting rod is exposed to compressive burdens and during the last part of the fumes and the start of the suction strokes, to tensile burdens, subsequently sturdiness of this part has basic significance[2,6].In present day automotive internal combustion engines, the connecting rod are most normally made of steel for production motors, yet can be made of aluminum (for softness and the capacity to ingest high effect to the detriment of toughness) or titanium (for a blend of strength and lightness at the cost of affordability) for elite motors, or of cast iron for applications like engine bikes(scooters)[3,7,8].
Failure of a connecting rod, typically called "throwing a rod" is quite possibly the most widely recognized reasons for catastrophic engine failure in cars, frequently putting the broken rod through the side of the crankcase and thereby rendering the engine irreparable [3,7]. The connecting rod is under gigantic pressure from the reciprocating load addressed by the piston, really extending and compressing with each revolution, and the load increments to the third power with speeding up[3]. When a connecting rod is in operation then a combination of both bending and axial stress act on it, in which the axial stress is due to the gas pressure produced by the cylinder and the inertia forces occurs due to reciprocating operation and due to the centrifugal effect bending stresses occurs [9].Automobile has to be light in weight to devour less fuel, simultaneously they have to provide comfort and well-being to travellers, sadly which prompts weight of the vehicle, execution of new materials which are light and meet plan prerequisites can take care of this issue [4]. The most widely recognized sorts of manufacturing process are casting, forging and
powdered metallurgy. Connecting rod are generally utilized in various types of engines which are, for example, in line engine, V engine, opposed cylinder engines, radial engines and opposed-piston engines [10]. The capacity and objective of design are one of the most fundamental variables to decide the performance of connecting rod principle bearing [11]. Ansys was used for simulation purpose; it is all-round finite element analysis (FEA) software. FEM which is an analytical method i.e., used for dismantle a difficult system into small particle pieces called as elements [5].
Ankit Gupta et al. [12] described the designing and analysis of two-wheeler connectingrod. In this study material of connecting rod is replaced by beryllium alloy and magnesium alloy analysis was carried out by considering three materials AL360, beryllium alloy, magnesium alloy. In this study PRO-E software is used to design the connecting rod and analysis is done in ANSYS 10.0 Software. The parameters like maximum von-mises stress, maximum von-mises strain and maximum displacement are found minimum in beryllium alloy connecting rod as compare to other materials and stress induced in beryllium alloy is less. Author suggested that beryllium alloy can be used for production of connecting rod for long durability. Prateekjoshi et al. [13] compared connecting rod of Carbon Fiber material with Aluminium Alloy and Stainless-Steel connecting rod based on the load, strain and stress analysis of the connecting rod. For designing PRO-E and for analysis of connecting rodAnsys software is used. Author concluded that Carbon Fiber is the best material that can be utilized for the manufacturing of Connecting Rod, for being lighter and equivalent strength with that of Stainless Steel and Aluminium Alloy.D.Jeeva et al.[14] analysed the fracture on the connecting rod using finite element analysis. Ansys software is used to analyse the stress and thermal in the connecting rod. For designing of connecting rod CATIA V5 software is used. Author found the result that maximum displacement and maximum von mises strain in beryllium alloy connecting rod is lesser. And also concluded that the aluminium alloy of connecting rod having more weight and displacement then magnesium and beryllium alloy connecting rod. So, aluminium alloy connecting rod shows more shaky behaviour.
MarthanapalliHari Priya et al. [15] performed on connecting rod of forged steel for reducing in weight and production cost. Actual cross section of connecting rod is changed from I to H, it is found that weight of connecting rod is reduced 10g.Material of connecting rod is replaced with Al360, foundthat the connecting rod weight is reduced 4 times less than the carbon steel connecting rod.VikashSingh et al. [16] compared connecting rod using different materials based on ANSYS parameter von mises strain, stress and Displacement. Analysis of connecting rod is done in Ansys workbencp6.2 software and 3D model of connecting rod is prepared in solid works 2016 software. It is found that Maximum von mise strain, stress and maximum displacement re lesser in beryllium alloy connecting rod as compare to carbon steel, aluminium andmagnesium alloy of connecting rod. Author suggested that Beryllium alloy can be used for production of connecting rod for longer life.K U Arun Kumar et al. [17] used NX NASTRAN and ANSYS software for analysis of connecting rod made up of typical and composite material in their research work, they concluded that equivalent von-misses stress is nearly same for all the material, whereas AISI4140 is discovered to be exposed to least von-misses stress among various materials.AkshayNighot et al. [18]Used CATIA for designing and ANSYS 16.2 for simulation purpose for their research work to optimize the design by computing weight and stiffness for various material and found that connecting rod made up of forged steel has more weight as compared to one made up of Aluminium, magnesium and beryllium alloy also, stress, strain and displacement in beryllium was found to be least.
LucjanWiteket al. [19] Used CATIA for creating geometric model and analysis was done by using ANSYS for the purpose to study failure and stress analysis of turbocharged diesel engine and concluded that crack origin is not covered by corrosion product or material defect, maximum principal stress occurred at the bolt hole of connecting rod, fatigue failure occurred due to high tightened torque of bolts.VinayakChambre et al.[20] Used NX 6.0 and ANSYS 14.5 software to examine and study the connecting rod structure utilizing FEA technique in their investigation work and tracked down that underlying weight was 129.9 grams which was decreased to 127.96 grams because of alteration in design.PuneetAgarwal et al.[21] Used SOLIDWORKS ver. 2013 to develop 3D model of connecting rod for the purpose to find the influence of various material constituent on the structural behaviour of connecting rod in his research work and found that von-misses stress and strain is less in Aluminium allot 7075 as compared to forged steel, titanium alloy which occurred due to the increase in silicon percentage in the Aluminium alloy.Kuldeep B et al.[22] replaced the connecting rod material Al360 with hybrid Alfa Sic composite and describe the designing and analysis of connecting rod.Ansys parameter von misesstrain, von-mises stress, and displacement are obtained for material Al360 and hybrid Alfa Sic composite and compared. It is obtained that weight of hybrid Alfa Sic composite connecting rod 43.48% less than the Al360 connecting rod.
B. Anusha et al. [23] analysed the static analysis conducted on connecting rod. Designing of connecting rod is done in PRO-E software. FEA in done to determine the von mises stress,von mises strain and total deformation in the Ansys software. Author concluded that the stress induced in the structural steel is less than the cast iron for the present investigation.HD Nittukar et al.[24]describe the designing and analysis of connecting rod using different material. Designing of connecting rod is done by the help of NX10 software and drafting of connecting rod is done by calculation. FEA is done by the help of Ansys software to determine the von misesstress,vonmises strain and total deformation of connecting rod.From the ANSYS result it is observed that the parameters of analysis are lesser in beryllium alloy connecting rod.H D. Nitturkar et al.[25] Used NX10 and ANSYS software for the purpose of to analyse the stress using FEA approach on each material selected for study and concluded that minimum stress was at the crank end cap and at the piston end. And from the static analysis the maximum stress is found in small end.Ramesh B T et al.[26] Used ANSYS software to analysis and reducing the weight of connecting rod using different material and found that aluminium7075 is best material for connecting rod regarding stress handling,also manufacturing and cost.
-
Saikiran et al. [27] Used SOLIDWORKS software to design connecting rod and analysis was done using ANSYS for the purpose of measuring the transient temperature of connecting rod at different points and found that maximum deformation occurred one at the small end bearing at the inner fibre surface & other at centre of big end and deformation also occurred because of buckling under critical loading and shear failure of big and small end bearing. Mohamed AbdusalamHussin et al. [28] Utilized SOLIDWORKS and ANSYS 15.0 for the purpose behind plan and investigation of connecting rod and tracked down that minimum stress is at crank end cap also at piston end under each stacking condition and henceforth we can decrease material from these bits to lessen the expense of material. Naman Gupta et al. [29] Used CREO 2.0 for designing and hyper work for simulation of connecting rod for the purpose to optimize weight and make the component lighter within permissible limit and found that up to 74% weight of connecting rod is reduced for AISI4340 to the vertical cut connecting rod of Al7068.On the off chance that passable permissible limit is considered up to 15% the horizontal cut community segment connecting rod of Al7068 can be restored instead of solid connecting rod of Al7068.Sebastian Antony et al. [30] Used CATIA V5 for geometric modelling and ANSYS for analysis for the purpose to perform FEA analysis and obtain stress analysis on application of load upon connecting rod and found that comparing with aluminium, steel is a better choice as because higher intensity of stress is found in case of connecting rod prepared from aluminium as compared to steel.
Dr. B S N Murthy et al. [31] Utilized ANSYS 18.1 programming to performed improvement of connecting rod for pressure creation under stacking and recommend weight decrease openings, they inferred that as far as mechanical properties and machine- capacity titanium is higher and furthermore less malleable. According to limited component investigation it is likewise realized that, there is an enormous edge of material expulsion from large end zone, small end zone and district interfacing with the small end of the connecting rod. As per the results got from the analytical calculations, there may be a degree of lessening in its I-area thickness.Amit Kumar et al. [32] Used CATIA and ANSYS 14.0 software for the purpose of Dynamic Analysis of Bajaj Pulsar 150cc Connecting rod and found that, as compared to 20CrMo and 30CrMO, 42CrMo steel alloy requires less material and less dimension to sustain pressure and comparing weight, 42CrMo is 11.67% lighter as compared to other material whereas 30CrMo alloy is only 6.42% less compared to 20CrMo connecting rod.
From the above literature review authors found that the analysis on the following materials, e.g., BeI220H, Al A360, Al 5083and Al (T6)7075 is limited. Hence, we have chosen these materials for our investigation which can resist a high pressure on the connecting rod.
-
-
MATERIALS AND METHODS:
From the above literature review we have taken four different materials for our experimental investigation for making the connecting rod. These are BeI220H, Al A360, Al 5083and Al(T6)7075. In table 1- 4 shows the composition of these four materials:
TABLE 1: COMPOSITION OF BEI220H
Material
Beryllium Assay
Beryllium oxide
Aluminium
Carbon
Iron
Magnesium
Silicon
Other Metallic Impurities
Percentage (in %)
98
2.2
0.10
0.15
0.15
0.08
0.08
0.04
TABLE 2: COMPOSITION OF AL A360
Material
Aluminium
Copper
Iron
Magnesium
Manganese
Nickel
Silicon
Tin
Zinc
Other
Percentage (in %)
90.6
0.6
1.3
0.60
0.35
0.50
10
0.15
0.50
0.25
TABLE 3: COMPOSITION OF ALUMINIUM-7075
Material
Aluminium
Zinc
Chromium
Titanium
Manganese
Silicon
Iron
Copper
Magnesium
Percentage (in %)
88.85
5.5
0.15
0.2
0.3
0.4
0.5
1.6
2.5
TABLE 4: COMPOSITION OF AL 5083
Material
Silicon
Iron
Copper
Manganese
Magnesium
Zinc
Tin
Chromium
Aluminium
Percentage (in %)
0.40
0.40
0.10
0.40-1.0
4.0-4.9
0.25
0.15
0.05-0.25
Balanced
Characterisation of Materials:
Table 5-7 gives different properties of selected materials such as density, ultimate strength, and yield strength, modulus of elasticity, melting point, thermal conductivity and Specific heat capacity.
TABLE 5: COMPARISON OF DENSITY OF SELECTED MATERIALS
Material
BeI220H
Al A360
AL(T6)7075
AL 5083
Density(g/cc)
1.844g/cc
2.68g/cc
2.67g/cc
2.66 g/cc
TABLE 6: MECHANICAL PROPERTIES
Sl no
Material
Ultimate tensile strength (in MPa)
Yield tensile strength (in MPa)
Elongation at break
(in %)
Poissons ratio
Shear modulus (in GPa)
Modulus of elasticity (in GPa)
1.
Be I220H
448
345
1.00
0.070-0.18
135
303
2.
Al A360
300
170`
3
0.33
26.5
71.0
3.
AL(T6)7075
572
503
11
0.33
26.9
71.7
4.
Al 5083
317
228
16
0.33
26.4
70.3
Table 7: Thermal properties
Sl no
Material
Melting point (in 0C)
Thermal conductivity (in W/m-k)
Specific heat capacity (in J/g0C)
1.
Be I220H
1273-1283
216
1.925
2.
Al A360
557-596
113
0.963
3.
AL(T6)7075
477-635
130
0.96
4.
Al 5083
591-638
117
0.9
-
CALCULATION
-
Pressure calculation for connecting rod
Calculations made by considering a 150cc Engine of Bajaj pulsar, Followed by its specifications. Specifications
Engine type = Air cooled 4-stroke Bore =58 mm
Stroke = 56.4 mm Displacement = 149.01cc
Maximum Power = 15.1ps @ 9000 rpm Maximum Torque = 12.45 Nm @ 6500 rpm Compression Ratio = 9.5 ± 0.5:1
Density of Petrol (C8H18) = 737.22 kg/3
= 737.22× 109/ 3
Auto ignition temperature = 280 0C=536 0F =553.15 0k Mass = Density x volume
= 737.22× 109 × 149.01× 103
= 0.1098531522 kg
= 0.11423 kg/mole From gas equation,
PV= × ×
Where, P = Gas Pressure, MPa V = Volume
m = Mass, kg
T = Temperature, °K
= Specific gas constant
= R/M
= 8.3144/0.114228
= 72.788 Nm/kg K
P = ( × × )/V
P = (0.18356 x 72.788*103 x 553.15)/(149.01*103 )
= 29.67 ~30 MPa
Calculation of analysis is done for maximum Pressure of 30 MPA and 15 MPA.
-
Calculation for total force Total Force acting F = Where,
= force acting on the piston
= force of inertia
= (/ 4) × 2 ×Gas pressure Where, D = Bore Diameter
= ( /4) × (58)2 ×15
= 39631.19133 N
F= × 2 × ( + (2)/n) Where, M = Mass of the reciprocating part
=Angular speed of crank Figure 1: Forces on Connecting Rod
= (2N)/60
= (29000) /60
= 942.47 rad/sec
= length of connecting rod (l) / crank radius(r)
= (2 × )/(2)
=112.8/28.2
= 4
Refer fig for , The maximum gas load occurs shortly after the dead centre position at = 3.3° cos (3.3) = 0.9983 1 On substituting these
F= × 2 × ( + (2)/n)
= 0.10985 × (942.47)2× 0.0282× (1 + 1 /4)
=0.10985 ×888249.70× 0.0282 ×1.25
=3439.49 N F=FP-FI
=39631.19133-3439.49
=36191.70133 N
-
-
ANALYSIS USING ANSYS
-
Modeling of Connecting rod
Connecting rod of Bajaj pulsar 150 Four-stroke single cylinder engine is selected for the current examination. As per the dimensions the model of connecting rod is created by utilizing FUSION 360. The modelled version of connecting rod is shown in figure 2.
Figure 2: Model of Connecting Rod
-
Mesh
Meshing is an important part of the engineering simulation process where complex geometries are divided into small and simple elements. It influences the convergence, accuracy and speed of the simulation. It helps in Finite Element Analysis of a continuous body.
For this case, Automatic mesh gives less numb nodes and elements. With the assistance of Hex-Dominant mesh, it gives a greater number of nodes yet a smaller number of elements; because of this the complexities to tackle the problem will rise. Tetrahedron mesh method gives proper mesh result as shown in figures 3 & 4.
Choosing Tetrahedron method with picking improved sizing of mesh, we got maximum number of nodes = 27137 and elements
=18006.
Figure 3: Detail of Mesh Figure 4: Meshing of Connecting Rod
-
Loading condition
Figure 5: Small End Loaded Figure 6: Big End Loaded
In figure 5 we have given a fixed support to the big end or crankshaft side end of the connecting rod and put a force of 36191.7 N similar to 36192 Non the Small end or Piston side end of the connecting rod in the direction to the big end which is a compressive type of load. In Figure 6 shows the similar loading condition at big end.
-
Analysis of BeI220H Connecting Rod
Small End Loaded
Figure 7: Small End Connecting Rod of BeI220H
From the figure7, [A] the maximum total deformation occurs at the small end of the Connecting rod is 0.14537 mm, [B] the maximum principal elastic strain occurs at the small end of the connecting rod is 0.00028049, [C] the maximum equivalent stress occurs at the small end of the connecting rod is 989.6 MPa [D] the safety factor of the small end of the connecting rod is 0.34.
Big End Loaded
Figure 8: Big End Connecting Rod of BeI220H
From the figure8, [A] the maximum total deformation occurs at the big end of the connecting rod is 0.44395 mm, [B] the maximum principal elasic strain occurs at the big end of the connecting rod is 0.0028258, [C] the maximum equivalent stress occurs at the big end of the connecting rod is 1332.7 MPa, [D] the safety factor of the big end of the connecting rod is 0.25.
-
Analysis of Al 5083 Connecting Rod
Small End Loaded
Figure9: Small End Connecting Rod of Al 5083
From the figure9, [A] the maximum total deformation occurs at the small end of the connecting rod is 0.62003 mm, [B] the maximum principal elastic strain occurs at the small end of the connecting rod is 0.0074996, [C] the maximum equivalent stress occurs at the small end of the connecting rod is 925.04MPa, [D] the safety factor of the small end of the connecting rod is 0.24.
Big End Loaded
Figure 10: Big End Connecting Rod of Al 5083
From the figure10, [A] the maximum total deformation occurs at the big end of the connecting rod is 1.8954 mm, [B] the maximum principal elastic strain occurs at the big end of the connecting rod is 0.012408, [C] the maximum equivalent stress occurs at the big end of the connecting rod is 1277.5MPa, [D] the safety factor of the big end of the connecting rod is 0.17.
-
Analysis of Al A360 Connecting Rod
Small End Loaded
Figure 11: Small End Connecting Rod of Al A360
From the figure11, [A] the maximum total deformation occurs at the small end of the connecting rod is 0.61328 mm, [B] the maximum principal elastic strain occurs at the small end of the connecting rod is 0.0081321, [C] the maximum equivalent stress occurs at the small end of the connecting rod is 921.72 MPa, [D] the safety factor of the small end of the connecting rod is 0.18.
Big End Loaded
Figure 12: Big End Connecting Rod of Al A360
From the figure12, [A] the maximum total deformation occurs at the big end of the connecting rod is 1.9091 mm, [B] the maximum principal elastic strain occurs at the big end of the connecting rod is 0.0130096, [C] the maximum equivalent stress occurs at the big end of the connecting rod is 1355 MPa, [D] the safety factor of the big end of the connecting rod is 0.12
-
Analysis of Al(T6)7075 Connecting Rod
Small End Loaded
Figure 13: Small End Connecting Rod of Al(T6)7075
From the figure13, [A] the maximum total deformation occurs at the small end of the connecting rod is 0.60729 mm, [B] the maximum principal elastic strain occurs at the small end of the connecting rod is 0.0080527, [C] the maximum equivalent stress occurs at the small end of the connecting rod is 921.72 MPa, [D] the safety factor of the small end of the connecting rod is 0.54
Big End Loaded
Figure 14: Big End Connecting Rod of Al(T6)7075
From the figure14, [A] the maximum total deformation occurs at the big end of the connecting rod is 1.849 mm, [B] the maximum principal elastic strain occurs at the big end of the connecting rod is 0.012027, [C] the maximum equivalent stress occurs at the big end of the connecting rod is 1336.6 MPa, [D] the safety factor of the big end of the connecting rod is 0.37
-
-
RESULT
Comparison of weight:
Figure 15: Weight comparison graph
From figure 15 we can see the weight comparison of materials taken for this experiment, as result, we can figure out the BeI220H material is very light in weight as compared to other materials.
Materials Mech. Values
BeI220H
Al A360
Al 5083
Al(T6)7075
Small end loaded
Total Deformation (in mm)
0.14537
0.61328
0.62003
0.60729
Maximum principal Elastic Strain
0.00028049
0.0081321
0.0074996
0.0080527
Equivalent Stress (in MPa)
989.6
921.72
925.04
921.72
Safety Factor
0.34
0.18
0.24
0.54
Big end loaded
Total Deformation (in mm)
0.44395
1.9091
1.8954
1.849
Maximum principal Elastic Strain
0.0028258
0.0130096
0.012408
0.012027
Equivalent Stress (in MPa)
1332.7
1355
1277.5
1336.6
Safety Factor
0.25
0.12
0.17
0.37
-
CONCLUSION
This is a general study on the connecting rod made up of different materials along with the design of connecting rod. The main objective of this paper is to optimize weight and get material for making the connecting rod that has a better lifespan and withstands extreme loading conditions.
By checking and contrasting the results of the materials in finalizing the outcomes are shown below:
Considering the parameters:
-
ANSYS Total Deformation & Maximum Principal Elastic Strain are both lowest in the materials BeI220H as compare to other materials.
-
ANSYS Equivalent Stress is higher in the case of small end loaded and second-lowest in the big end loaded.
-
In the case of Safety Factor BeI220H is the second-highest in the material that is taken in the experiment.
-
For BeI220H material the weight very lighter than other materials.
so, from the above points, we can conclude that the BeI220H material is more suitable than the other materials for manufacturing connecting rods.
REFERENCES
-
Magesh Kumar and Prof. Ankush K Biradar, Design, Analysis and optimization of connecting rod International Journal of Innovative Research in Science, Engineering and Technology, volume. 6, Issue-11, May 2017.
-
NilamPranjalPatil-Dhande, PundlikPatil and R. Y. Patil Analysis of Connecting Rod for Weight Reduction in Case of a CI Engine International Journal of Engineering Development and Research volume 6, Issue 1, 2018
-
Leela Krishna Vegi, and VenuGopalVegi Design and Analysis of Connecting Rod Using Forged steel International Journal of Scientific & Engineering Research, Volume 4, Issue 6, June-2013
-
NilamPranjalPatil and Prof. PundlikNivruttiPatil Design analysis of connecting rod for weight reduction in case of a ci engine International Conference Proceeding ICGTETM Dec 2017
-
P.Viswabharathy, G. Vishnukumar, R. Yuvapraksh and M.Anbalagan Modelling and Analysis of Connecting Rod in Two Wheeler by Using ANSYS International Journal of Emerging Technologies in Engineering Research (IJETER) Volume 5, Issue 3, March (2017)
-
Suraj Pal and Sunil Kumar Design Evaluation and Optimization of Connecting Rod Parameters Using FEM International Journal of Engineering and Management Research, Vol.-2, Issue-6, December 2012
-
Ramesh B T, VinayakaKoppad and HemanthaRaju T Analysis and Optimization of Connecting Rod with Different Materials World Journal of Research and Review (WJRR), Volume-4, Issue-1, January 2017
-
Karthikeyan P, Sathishkumar S, Dinesh B, Praveen k, and Surendar J Material optimization and structural analysis of internal combustion engine connectng rod and crank shaftInternational journal of innovative research in technology, Volume 4, Issue 11, April 2018
-
Yogesh. B. Dupare, Raju.B.Tirpude and Akshay.Y.Bharadbhunje Fatigue analysis in connecting rod using ANSYS ,International Journal of Modern Trends in Engineering and Research (IJMTER) Volume 02, Issue 02, [February – 2015]
-
Akbar H Khan&Dr. Dhananjay R Dolas Design, Modelling and Static StructuralAnalysis of Connecting rod, Imperial Journal of Interdisciplinary Research (IJIR)Vol-3, Issue-1, 2017
-
Jun Sun, Biao Li, Shaoyu Zhu, Enming Miao, Hu Wang, Xiaoyong Zhao and Qin Teng Lubrication Performance of ConnectingRod and Main Bearing in Different Engine Operating Conditions (2019)
-
Ankit Gupta1, Mohd. Nawajish, Design and Analysis ofTwo-Wheeler Connecting Rod Using Different Materials, International Journal of Advance Research in Science and Engineering IJARSE, Vol. No.3, Special Issue 01, September 2014
-
Prateek Joshi and Mohammad UmairZaki FEM Analysis of Connecting Rod of different materials using ANSYS, International Journal of Engineering and Techniques – Volume 1 Issue 3, May – June 2015
-
D.Jeeva and Ashok Kumar.R Design And Analysis Of Connecting Rod Using Different Materials, International Journal of Science and Engineering Research (IJ0SER), Volume 7 Issue 4 April -2019
-
MarthanapalliHariPriya and K. Manohar Reddy Materialized Optimization of Connecting Rod for Four Stroke Single Cylinder Engine, International Journal of Computational Engineering Research, Volume, 03, Issue 10, October 2013
-
Vikas Singh, Sumit Kr. Verma, Harish Chandra Ray, Vishal Kr. Bharti, and AbhineshBhaskar Design and Analysis of Connecting Rod for Different Material Using Ansys Workbench 16.2, International Journal for Research in Applied Science &EngineeringTechnology (IJRASET), Volume 5, Issue V, May 2017
-
K u arunkumar, b. Rama krishna, a. Maboob basha and k. Trinathkumar, modelling and simulation of connecting rod by conventional and composite (mmc) materials, International Journal of Technical Innovation in Modern Engineering & Science (IJTIMES) Volume 5, Issue 07, July-2019
-
Prof.AkshayNighot, Nikhil Kulkarni, YogeshaniKhedekar, SahebraoChakre and Sandeep Kumar Singh, Performance Analysis of Connecting Rod for different Materials Using FEM, International Journal of Advance Reasearch in Science and Engineering, volume 07, Issue 04, April 2018
-
LucjanWitek, PaweZelek, Stress and failure analysis of the connecting rod of diesel engine 02 January 2019
-
VinayakChumbre, VinayakKallannavar, AnilkumarShirahatti, RatanPatil, and Shirish M. Kerur Design and Comparative Analysis of Connecting Rod using Finite Element Analysis, Volume 6 Issue IV, April 2018
-
PuneetAgarwal, Ankit Gupta and Vishal Saxena Modelling and Analysis of Two-Wheeler Connecting Rod using Finite Element Method, Vol. 6, No. 1, January 2016
-
Kuldeep B1, Arun L.R2, Mohammed Faheem, analysis and optimization of connecting rod using alfa sic composites, International Journal of Innovative Research in Science, Engineering and TechnologyVol. 2, Issue 6, June 2013
-
B. Anusha and C. VijayaBhaskar Reddy Modelling and Analysis of Two-Wheeler Connecting Rod by Using Ansys, IOSR Journal of Mechanical and Civil Engineering (IOSR-JMCE), Volume 6, Issue 5 (May. – Jun. 2013)
-
S. Venkatesh, I. Bruno Clement, C. Arun Kumar, D. Boopathi Raja and S. Anand Design and Analysis of Connecting Rod withModified Materials and FEA Analysis, International Journal of Engineering Research & Technology (IJERT), Volume. 3, Issue 2, February 2014
-
Mr. H D. Nitturkar, Mr. S M. Kalshetti and Mr. A R. Nadaf Design and Analysis of Connecting Rod using Different Materials, International Research Journal of Engineering and Technology (IRJET), Volume: 07 Issue: 03, Mar 2020
-
Ramesh B T, VinayakaKoppad and HemanthaRaju T Analysis and Optimization of Connecting Rod with Different Materials, World Journal of Research and Review (WJRR), Volume-4, Issue-1, January 2017
-
p. Saikiran& p. Arunagiri a structural analysis of a connecting rod using fea, Vol. 9, Issue 2, Apr 2019
-
Mohamed AbdusalamHussin, Er. Prabhat Kumar Sinha and Dr.Arvind Saran Darbari design and analysis of connecting rod using Aluminium alloy 7068 t6, t6511, Volume 5, Issue 10, October 2014
-
Naman Gupta, ManasPurohit and KartikChoubey, Modern Optimized Design Analysis of Connecting Rod of an Engine, Volume: 05 Issue: 02, Feb- 2018
-
Sebastian Antony, Arjun A., Shinos T. K and Anoop P Design and Analysis of a Connecting Rod Vol. 5 Issue 10, October-2016
-
Dr. B S N Murthy, K. Adarsh Kumar, Mohammed Abdul Shafeeq and S. SaiSundara Praveen Design and Analysis of Connecting Rod for Weight and Stress Reduction, Volume 7, Issue 03,2019
-
R.S. KHURMI, J.K. GUPTA "A text book of Machine Design"