
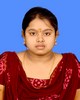
- Open Access
- Authors : K. Meenatchi , P. N. Raghunath , K. Suguna
- Paper ID : IJERTV11IS050048
- Volume & Issue : Volume 11, Issue 05 (May 2022)
- Published (First Online): 10-05-2022
- ISSN (Online) : 2278-0181
- Publisher Name : IJERT
- License:
This work is licensed under a Creative Commons Attribution 4.0 International License
ANN based Performance Evaluation of Fiber Reinforced Concrete Beams Incorporating Nano Fillers and Micro Fillers
-
Meenatchi, P. N. Raghunath, K. Suguna
Department of Civil and Structural Engineering, Annamalai University, India
Abstract:- An attempt has been made in this study to evaluate the performance of fiber reinforced concrete beams incorporating nano fillers and micro fillers using the neural computational tool ANN. The test data necessary for this exercise were collected from published literature. MATLAB software has been used for this purpose. Back propagation network with Levenberg Marquardt Algorithm, Bayesian Regularization Algorithm and Scaled Conjugate Gradient Algorithm was chosen for the proposed study .The length, breadth, depth, Ast, Asv, fck and fy were considered as input parameters and first crack load, deflection at first crack load, yield load, deflection at yield load, ultimate load and deflection at ultimate load were considered as target parameters. In the present study comparison has been made between the test results from published literature and results predicted from ANN using different algorithms. Statistical indicators such as RMSE, R² and MAPE were found to estimate the accuracy of results predicted through ANN modeling. The results predicted through ANN modeling exhibit better convergence with the experimental results collected through published literature.
Key Words: ANN, Deflection, Fiber Reinforced Concrete, MATLAB.
-
INTRODUCTION
Fiber reinforcement is introduced into concrete with a view to enhance the ductility of concrete and also to impart increased resistance to fatigue and impact. The intent of adding nano-fillers and micro-fillers in concrete is to improve the performance of concrete under a wide variety of environmental conditions. Fiber reinforced concrete (FRC) is concrete containing fibrous material which increases its structural integrity. It contains short discrete fibers that are uniformly distributed and randomly oriented. Fibers include steel fibers, glass fibers, synthetic fibers and natural fibers. Fiber-reinforced normal concrete are mostly used for on-ground floors and pavements, but can be considered for a wide range of applications (beams, pliers, foundations etc). some of the important factors of fiber reinforced concrete are (1).increases the tensile strength of the concrete, improved structural strength(2).increases the durability of the concrete (3). closely spaced and uniformly dispersed fibers to concrete would act as crack arrester (4). Improved freeze-thaw resistance.
-
LITERATURE REVIEW
Manar A.Ahmed et al (2017) investigated the structural performance of reinforced concrete beams with nano-metakaolin in shear. Seven beam specimens of size 2000mmx100mmx200mm were cast and tested at 28 days. Nanometakaolin was incorporated at 10%. The fracture mechanism was studied by focusing on crack and deflection behavior for beams under static loading. Different values of shear reinforcement ratio, shear span to depth ratio and characteristic strength were considered. The experimental result showed that the ultimate load, cracking load and toughness of the beam with 10% NMK as portion of cement increased by 7.4%, 31.5% and 17.6% respectively. The addition of nano- metakaolin significantly improved the performance of concrete mixes.
Stephen Jebamalai Raj.J (2013) investigated the static and fatigue response of high strength fiber reinforced concrete beam with FRP laminates. An analytical model was proposed for predicting the performance parameters of HSFRC beams. Modeling and analysis were done using the MSC/NASTRAN – PATRAN software. The analysis results showed that the deflection of HSFRC beams was lesser than the experimental results. The presence of steel fibers reduced the deflection more in FEA analysis.
In Hwan Yang et al (2010) investigated the structural performance of ultra high performance concrete beams subjected to bending. UHPC does not include coarse aggregate and had steel fibers with volumetric ratio of 2%. Amount of rebar and placing method of UHPC were considered. The experimental results showed the ability of UHPC to redistribute stresses and undergo multiple cracks before fiber pullout. Placing UHPC at end of beams provides better structural performance than placing UHPC at mid-span. In addition UHPC beams exhibit a better post – cracking behavior.
Doo Yeol Yoo et al (2015) studied the structural performance of ultra high performance concrete beams with different steel fibers. UHPC containing no coarse aggregate with two different reinforcement ratios. Two different fibers (smooth and twisted) and three different length (Lf = 13,19.5 and 30mm) were used. Control specimen made up of UHPC matrix without fiber were also fabricated and tested. The experimental results showed that addition of steel fibers slightly increased the compressive
strength, elastic modulus and significantly improved the flexural performance. The beams without fibers failed by crushing of concrete at compressive zone whereas beams with steel fibers failed by rupture of steel rebars.
S.Syed Ibrahim et al (2016) investigated the structural performance of glass fiber reinforced polymer laminated steel fiber reinforced concrete beams. Strengthening of RC beams was done by introducing short steel fibers and externally bonded GFRP laminates on tension face of the beam. Two groups of beams were cast and tested. Group A had RC beams with and without externally bonded GFRP laminates and in group B had SFRC beams with and without externally bonded GFRP laminates. The experimental results showed that the maximum increase in ultimate load was upto 130%, 27.8% and 91.9% and reduction in deflection to the tune of 27.40% when compared to SFRC beams.
Chao Xu et al (2019) studied the behavior of composite steel – concrete beams containing different amounts of steel fibers and conventional reinforcement. The steel cages in steel reinforcement concrete beams were replaced by steel fibers. Several steel fiber volume were designed and used to improve the mechanical properties of concrete. The combination of proper amount of steel fiber and steel had better bearing capacity and deformability of composite members. Shear span to depth ratio, web reinforcement, with or without longitudinal reinforcement were considered. The experimental results showed that addition of steel fibers improved the mechanical response, flexural and shear strength and ductility. The stitching effect of steel fibers between cracks lead to stable bearing capacity of specimens. Steel fibers as alternative for shear reinforcement and longitudinal reinforcement greatly enhanced the bearing capacity. Increasing the content of steel fibers delayed the bond failure.
Venkatesan.K.R et al (2015) investigated the flexural behavior of high strength steel fiber reinforced concrete beams. Beam specimens of size 3000mmx 150mmx250mm were constructed and tested. The authors attempted different steel fiber volume fractions of 0.5%, 1.0% and 1.5%. The stress transfer mechanism of failure caused significant improvement in ductility, toughness, impact resistance, tensile and flexural strength, shrinkage, fatigue life, abrasion resistance, and durability and cavitation resistance. The optimum fiber volume fraction was 1% and the beams failed in flexure mode only. SFRC beams with 1% fiber volume fraction has increased ultimate load by 30.3% and increase in ductility was 41.34%.
Ravichandran.R.S (2012) investigated the flexural behavior of composite high strength concrete fiber reinforced polymer beams. The beam specimens f size 3000x150x250mm were tested. Reinforcement ratio, GFRP laminate material and their thickness were considered. The beams were strengthened with chopped strand mat glass fiber reinforced polymer and uni- directional cloth glass fiber reinforced polymer of 3mm and 5mm thickness. The experimental results showed an increase in ultimate load by about 23.51%, 88.22%, and increase in deflection at ultimate stage by about 15.85% to 211.59% for GFRP strengthened beams. GFRP strengthened beams failed in flexure modes only.
Mohamed K.Ismail et al (2017) investigated an experimental study on flexural behavior of large scale concrete beams incorporating crumb rubber and steel fibers. Percentage of CR (0 -35% by volume of sand), volume of SFs (0%, 0.35% and 1%) and length of SFs (35mm and 60mm) were considered. The experimental results showed that increase in CR appeared to narrow the crack widths, reduce self weight and improve deformability at given loads. Increase in CR content lead to higher reduction in ultimate load, ductility and toughness of SCRC and VRC beams.
Deepthi Dennison et al (2014) investigated the effect of metakaolin on the structural behavior of normal and steel fiber reinforced concrete beams. Compressive strength, split tensile strength, flexural strength and modulus of elasticity of concrete with various percentage of metakaolin 0%,5%, 7.5% by weight of cement were considered. The optimum metakaolin crimped steel fiber reinforced concrete 1.5%, 2% and 2.5% by volume of cement were also considered. The experimental results showed that load deflection pattern of metakaolin crimped steel fiber reinforced concrete beams showed greater load carrying capacity and deflection than that of control specimens in flexure and shear due to the effective bridging action of CSF. RC beams strengthened with MK and CSF showed a better structural performance in terms of first crack load, load deflection response, ultimate load carrying capacity, midspan deflection, and energy absorption and ductility index.
Halit Cenan Mertol at al (2015) investigated the flexural behavior of lightly and heavily reinforced steel fiber concrete beams. The beams specimen of size 3500mmx180mmx250mm were constructed and tested. Ten different longitudinal reinforcement ratios with minimum 0.2% and maximum 2.5% covering the range from under reinforced beam to over reinforced beams were used for testing. Two specimens were cast for each longitudinal ratio, one specimen using conventional concrete (CC) and another specimen using steel fiber reinforced concrete (SFRC). Load deflection behaviors were obtained and evaluated in terms of ultimate load, ultimate deflection, service stiffness, post peak stiffness, and flexural toughness. The results indicate that the use of SFRC increased ultimate load and service stiffness of beams slightly compared to CC specimens. As reinforcement increased the ultimate deflection of SFRC specimens has significantly improved than that of CC specimens. For over reinforced sections, the post peak stiffness of SFRC specimens was observed to be significantly lower than that of CC specimens. The flexural toughness of SFRC specimens was greater than that of CC specimens with the difference being significantly larger over reinforced sections.
Daniel C.T.Cardoso et al (2019) studied the influence of steel fibers on the flexural behavior of RC beams with low reinforcing ratios. The beam specimens size of 1200mm x150mmx150mm are cast and tested. Hooked end steel fibers with aspect ratios of 45or 80 were used to produce matrices with fiber content ranging from 0 to 2 % in volume and high compressive strength. Beams with reinforcing ratios 0.28, 0.44 and 0.70% were analyzed using digital image correlation to monitor displacement field and cracking distribution throughout the constant moment region during loading. The experimental results showed that the capacity ranges from 21 to 109% of SFRC with respect to plain RC beams and significant reduction in crack openings for given rebar stress. SFRC beams exhibited sufficient plastic rotation capacity, but with reduction of plastic hinge length as a consequence of crack localization.
Masoud Ghahremannejad et al (2018) studied the experimental investigation and identification of single and multiple cracks in synthetic fibers concrete beams. Synthetic fiber volume fractions of 0.5% and 1% were used to prepare the specimen and results compared with concrete beams with no synthetic fibers. The beams specimen size of 1143mmx152mmx229mm were cast and tested. Six reinforced and unreinforced beams with flexure behavior were considered. The digital image correlation method was utilized to record the width, spacing, number and locations of the cracks for all the specimens during displacement control type loading. The results indicated that using 1% synthetic fiber increased the failure load of the reinforced concrete beams and improved serviceability by reduced the number of cracks and width of cracks. When the cracks opened significantly, the beams with 1% fiber dosage were able to carry higher loads due to bridging action of the fibers at the cracks locations.
Alberto Meda et al (2012) investigated the flexural behavior of RC beams in fiber reinforced concrete . Seven beams specimen with size of 3600mmX200mmX300mm were cast and tested at 28 days. The three fiber contents, two longitudinal reinforcement ratios, either bonded or unbounded were considered. Experimental results proved that fibers, when provided in sufficient amount, are able to move the beam failure from concrete crushing to steel rupture. On the other hand, in all cases the addition of fibers determines a stiffer and in general enhanced post- cracking behavior in service conditions.
Holschemacher.K et al (2010) investigated the effect of steel fibers on mechanical properties of high strength concrete. SFRC is tough and high residual strength after appearing first crack. The beams specimens with size of 700mmX150mmX150mm were cast and tested at 28 days. The different bar reinforcements (26mm and 212mm) and three types of fibers configurations ( two straight with end hooks with different ultimate tensile strength and one corrugated) were used. Three different fibers contents were applied. The selected fibers content a more ductile behavior and higher load levels in the post cracking range were obtained.
Hamid Pesaran Behbahani et al(2012) investigated the flexural behavior of steel fiber added RC beams with C30 and C50 classes of concrete. The discrete and short steel fibers with optimum percentage of hooked end and the dimensions of 0.75mm in diameter, 50mm length were added in RC beams with two different classes of concrete. The experimental results proved that SFARC beams with 1% by volume of SFs have higher first cracking strength, ultimate flexural strength, stiffness and ductility. Samir A.Ashour et al (2000) investigated the effect of the concrete compressive strength and tensile reinforcement ratio on the flexural behavior of fibrous concrete beams. A total twenty seven beams specimen with size of 200mmX250mmX3400mm were cast and tested after 28 days. Concrete compressive strength of 49, 79 and 102 MPa and tensile reinforcement ratios of 1.18, 1.77 and 2.37% were used. The fibers contents were 0.0, 0.5 and 1.0% by volume. The results proved that the additional moment strength provided by fibers were not affected by the amount of tensile reinforcement ratio. The flexural rigidity increases as the concrete compressive strength and steel fiber content increases.
Olivito R.S et al (2010) investigated an experimental study on the tensile strength of steel fiber reinforced concrete. Different mixtures were prepared varying both mix design and fiber length. Fibers contents in volume were 1% and 2% . Mechanical characterization were performed by means of uni axial compression test with the aim of deriving the ultimate compressive strength of fiber concrete. Four point bending test on notched specimens were carried out to derive the first crack strength and ductiliy indexes.
Lampropoulos.A.P et al (2016) investigated the strengthening of reinforced concrete beams using ultra high performance fiber reinforced concrete. Numerical model were developed by using finite element method. The reliability of numerical model has been conducted on full scale beams strengthened with ultra high performance fiber reinforced concrete layers and jackets and these results were compared to respective results of beams strengthened with conventional RC layers and with combination of ultra high performance fiber reinforced concrete and steel reinforcing bars.
Zealakshmi.D et al (2016) investigated the flexural behavior of confined hybrid fiber in the plastic hinging region of the hi gh strength concrete beams. Steel and polypropylene fiber with varying volume fractions only at the critical sections along with stirrup confinement to improve the flexural behavior and ductility of a high strength concrete beam. A total 13 beam specimens with size of 120mmX200mmX2100mm were designed as an over reinforced section by providing high percentage of steel more than balanced state. Out of 13 beams one beam kept as reference beam without fiber reinforcement, four beams were designed as steel fiber and remaining with hybrid fibers. All the beams are tested under three point loadings and deflections were measured at respective places using dial gauges. The experimental results concluded that beams improves the flexural behavior, load carrying capacity and ductile manner.
Soulioti D.V et al (2011) investigated the Effect of fiber geometry and volume fraction on the flexural behaviour of steel fiber reinforced concrete. The flexural toughness, flexural strength and residual strength factors of the beam specimens were evaluated in accordance with ASTM standard. The experimental results proved that the improvement in mechanical properties in particular the toughness, were observed with the increase of the volume fraction of steel fibers in the concrete.
Goran H.Mahmud et al (2013) investigated the Experimental and numerical studies of size effects of ultra high performance steel fiber reinforced concrete beams. The size effects on flexural strength of similar notched UHPFRC beams under three point bending tests were conducted. The experimental results found that the size effects on the beam nominal strength are little due to high ductility of UHPFRC.
Mehmet Ozcan et al (2009) investigated the experimental and finite element analysis on the steel fibre reinforced concrete beams ultimate behavior. Three SFRC beams with 250mmX300mmX2000mm dimensions are produced using a concrete class of C20 with 30kg/m3 dosage of steel fibres and steel class S420 with shear stirrups. SFRC beams are subjected to bending by a four point loading setup in certified beam loading frame, exactly after having been moist cured for 28 days. The test are with control of loads. The beam are loaded until they are broken and the loadings are stopped when the tensile bars are broken into two pieces. Applied loads and mid section deflections are carefully recorded at every 5kN loads increment from the beginning till the ultimate failure.
Siva Chidambaram.R et al (2019) investigated the Flexural behavior of reinforced concrete beams with high performance fibre reinforced cementitious composites. Beam specimens with moderate confinement were used and tested under monotonic loading. Seven diverse types of FRCC including hybrid composites using fibres in different profiles and in different volumes. The moment curvature, stiffness, behavior, ductility, crack pattern and modified flexural damage ratio were considered. The experimental outputs demonstrates the improved post yield behavior with less rate of stiffness degradation and better damage tolerance capacity than conventional technique.
Su Tae Kang (2012) investigated the flexural behavior of UHPCC considering the effect of fibre orientation distribution. A three point bending test were carried out and the fibre orientation were quantitatively estimated by the help of image analysis process. The measured fibre orientation distributions for two different flexural performance confirmed that the fibre orientation distribution have strong impact on the deflection hardening behavior in bending. Finite element analysis were performed to predict flexural behavior of UHPCC considering the difference in fibre bridging behavior depending on the fibre orientation distribution.
Lokeshwaran.N et al (2017) investigated the flexural resistance of self compacted concrete beams by partial replacement of OPC with GGBS. Self compacting concrete were considered using GGBS by replacing the cement with 10%, 20%,30%,40% and 50% by weight. The mechanical properties of SCG (GGBS incorporated SCC) were found to be increased compared to concrete. Six reinforced concrete beams of shear span to depth ratio were tested for flexural capacity and ductile behavior. The experimental cracking moment of SCGB beams were found to be more than the theoretical cracking moment enhancing its flexural resistance. SCGB beams with higher percentage of GGBS exhibits higher ductility.
Julita Krassowska et al (2019) investigated the shear behavior of two span fibre reinforced concrete beams. The beams had varied stirrup spacing and two sorts of fibre were used as dispersed reinforcement. The steel fibre content were 78.5kg/m3 and the basalt fibre content were 5kg/m3. Concrete beams without addition of fibres were also examined as reference one. The effectiveness of both sorts of fibres as shear reinforcement were assessed on the basis of strain development and crack pattern analysis. The digital image correlation technique were used to monitor the development of cracks around the central supports of beam. It were shown that fibres control the cracking process and deformation in reinforced concrete beams and they can be effectively used as additional or the only shear reinforcement.
Faith Altun et al (2013) investigated the reinforced concrete beams behavior of steel fibre added lightweight concrete. Light weight concrete having a lower module of elasticity, a faster rate of crack development in RC members. The steel fibres are employed as an additive to the concrete in order to increase the energy absorption capacity and to control the crack development. Light weight concrete and reinforced concrete specimens were produced with the addition of steel fibres in different strength and ratios. The specimens were tested on four points through loading experiment. The experimental results found that the addition of steel fibre increased the toughness capacity, ductility and bearing strength.
Praveenkumar.S (2019) investigated the behavior of high performance fibre reinforced concrete composite beams in flexure. The blend mix included both free STF (Q series) and PPF (R series) and the hybridization of STF and PPF (S series) at a total volume fraction of 1% by volume of concrete with 10% bagasse ash as a substitution of cement. Structural behavior of eleven bagasse ash blended high performance concrete beams reinforced with steel, polypropylene and hybrid fibres were examined. The behavior of each beam were assessed with respect to initial crack, ultimate load, ultimate deflection, flexural strength, ductility and toughness. The inclusion of fibres increased the failure load and ensure the ductility behavior of beams. The experimental results found that adding hybrid fibres enhanced the mechanical properties as well as structural behavior of the beams.
Doo Yeol Yoo et al(2014) investigated the material and bond properties of ultra high performance fibre reinforced concrete with micro steel fibres. Four different volume ratios of micro steel fibres (Vf = 1%, 2%, 3% and 4%) were used within an identical mortar matrix. The experimental results showed that 3% steel fibre by volume yielded the best performance in terms of compressive strength, elastic modulus, shrinkage behavior, and interfacial bond strength. These parameters improved as the fibre content were increased upto 3%. Flexural behavior such as flexural strength, deflection and crack mouth opening displacement at peak load have pseudo linear relationships with the fibre content.
Silva.J.V et al (2016) investigated the influence of nano sio2 and nano Al2o3 additions on the shear strength and the bending moment capacity of RC beams. Concrete mixtures with additions of either silica nano particles( nano sio2)or aluminium nano particles (nano Al2o3) were produced. An experimental program were organized in two different sets: eight beams tested until shear failure were reached and eight beams tested until failure in bending were observed. These beams were produced with
eight distinct concrete mixtures, with and without nano particles and with and without steel fibres. The experimental results found that the addition of nano particles, mainly nano Al2o3 to the concrete mixtures can lead to a strength increase, both in shear and in bending and also concluded that the interaction between the nano particles and steel fibres have a negative effect on the beam strength.
-
MATERIALS AND METHODS
-
Artificial Neural Network(ANN)
Artificial Neural Networks are software implementations of the neural structures of human brain. ANN is a computational system influenced from the structure, processing capability and learning ability of a human brain. Let us take a look at the structure of our brain. Human brain contains billions of neurons that act as organic switches. All these neurons are interconnected to form a huge and complex structure called Neural Network. The output of a single neuron is dependent on inputs from thousands of interconnected neurons. the Learning of a human brain is simply repeated activation of certain neural connections and this repetition strengthens the connection. So, for a specified input, the neural connections make sure that output is always a desired one. A simple feedback from the outcome helps the learning process as it strengthens the neural connections. ANN are composed of multiple nodes, which imitate biological neurons of human brain. The neurons are connected by links and they interact with each other. The nodes can take input data and perform simple operations on the data. The result of these operations is passed to other neurons. The output at each node is called its activation or node value.Each link is associated with weight. ANN are capable of learning, which takes place by altering weight values. The simple ANN modeling shown in fig.1.
Figure 1. Simple Artificial Neural Network
-
Working of Artificial Neural Networks
A neural network combines several processing layers, using simple elements operating in parallel and inspired by biological nervous systems. It consists of an input layer, one or more hidden layers, and an output layer. The layers are interconnected via nodes, or neurons, with each layer using the output of the previous layer as its input. The working diagram of ANN shown in fig.2.
Figure 2. Neural Networks
-
Elements of Artificial Neuron Networks
The basic elements of any Artificial Neural Network as follows:
-
Processing Elements
-
Topology
-
Learning Algorithm
Processing Elements
ANN is a simplified computational model of a biological neural network, an ANN consists of basic processing units or elements similar to that of neurons of a brain in general, a processing unit is made up of summing unit followed by an output unit. The function of a summing unit is to taken input values, weight each input value and calculate the weighted sum of those values. The processing elements shown in fig.3
Figure 3. Processing Elements
Topology
Any Artificial Neural Network will become useful only when all the processing elements are organized in an appropriate manner so that they can accomplish the task of pattern recognition. This organization or arrangement of the processing elements, their interconnections, inputs and outputs is simply known as Topology. Generally, in an ANN, the processing units are arranged into layers and all the units in a particular layer have the same activation values and output values. Connection can be made between layers in multiple ways like processing unit of one layer connected to a unit of another layer, processing unit of a layer connected to a unit of same layer, etc. The toplogy diagram shown in fig.4
Figure 4. Topology
Learning Algorithm
The final and important elements of any ANN are Learning Algorithms or Laws. The operation any neural network is governed by Neural Dynamics consisting of both activation state dynamics and synaptic weight dynamics. Learning Algorithms or Laws are implementations of synaptic dynamics and are described in terms of first derivative of the weights. These leaning laws can be supervised, unsupervised or a hybrid of both.
-
-
Data used in ANN modeling
The geometrical properties of beam such as length (L), breadth (B) and depth (D), characteristic compressive strength of concrete (fck), yield stress (fy), diameter of reinforcement (Ast) and diameter of stirrups (Asv) were considered as the input parameters. The experimental results of all the test beams such as first crack load, deflection at first crack load, yield load, deflection at yield load, ultimate load and deflection at ultimate load were considered as the target parameters. The input and target parameters for ANN modeling are presented through Table 1 and 2.
-
Steps involved in ANN modeling
In this stage, the input data are divided into three groups which are train data, validate data and test data. The step wise procedure for ANN modeling is presented through the fig
-
Designing of ANN modeling
The basic flowchart for the designing of neural network. The flow chart are shown in fig.5.
Access and prepare the data
Create the neural network
Configure the networks inputs and outputs
Tune the network parameters
Train the network
Validate the networks results
Integrate the network
Figure 5. Flow chart for ANN mdeling
-
Building the network
This stage specifies the number of hidden layers, neurons in each layers, transfer function in each layers, training function, learning function and performance function as shown in fig.6
Figure.6 Architecture of neural network
-
Training the network
The training process are shown in fig 7 and 8
Figure 7. Training Networks Wizard
Figure 8. Neural Network Testing
-
Test performance of model
-
The fitness of the developed model is show through fig 9 to 12.
Figure 9. Neural Network Regression Plot
Figure.10 Neural Network Training Performance Plot
Figure 11. Neural Network Training State
Figure 12. Neural Network Error Histogram State
-
-
REGRESSION ANALYSIS
Regression analysis is widely used for prediction and forecasting, where its use has substantial overlap with the field of machine learning. Regression analysis is also used to understand which among the independent variables are related to the dependent variables, and to explore the forms of these relationships. In restricted circumstances, regression analysis can be used to infer causal relationship between the independent and dependent variables. Many techniques for carrying out regression analysis have been developed. Familiar methods such as linear regression and ordinary least squares regression are parametric, in that the regression function is defined in terms of a finite number of unknown parameters that are estimated from the data. Non parametric regression refers to techniques that allows the regression function to lie in a specified set of functions, which may be infinite dimensional.
The performance of regression analysis methods in practice depends on the form of the data generating process, and how it relates to the regression approach bing used. Since the truth form of the data generating process is generally not known, regression analysis often depends to some
extent on making assumptions about this process. Regression models for prediction are often useful even when the assumptions are moderately violated, although they may not perform optimally. However, in many applications, especially with small effects or questions of causality based on observational data, regression methods can give misleading results.
-
Regression equation for fibre reinforced concrete beams incorporated micro fillers and nano fibres
The coefficient of regression parameter, statistics and ANOVA for fibre reinforced concrete beams incorporating nano fillers and micro fillers calculated through ORGIN PRO are presented in Tables 3(a),3(b) and 3(c) to 8(a),8(b) and 8(c).
First Crack Load
Table 3(a) Parameters of First Crack Load
First Crack Load
Values
Standard Error
Intercept
48.51111
9.7267
b in mm
-0.09309
0.03302
d in mm
0.02161
0.02704
l in mm
0.00966
0.00188
Fck
0.05932
0.02795
Fy
-0.02651
0.01873
Ast in mm2
0.026
0.00588
Asv in mm2
-0.55841
0.10228
Table 3 (b ) Statistics for First Crack Load
First Crack Load
Number of Points
379
Degree of Freedom
371
Residual Sum of Squares
195805.04422
Adj. R-Square
0.21525
Table 3 (c) ANOVA Table for First Crack Load
First Crack Load
DF
Sum of Squares
Mean Square
F Value
Prob >F
Model
7
58416.43285
8345.20469
15.81201
0
Error
371
195805.04422
527.7764
Total
378
254221.47707
Deflection at First Crack Load
Table 4 (a) Parameters of Deflection at First Crack Load
Deflection at First Crack Load
Values
Standard Error
Intercept
88.97371
80.91538
b in mm
-0.12249
0.27468
d in mm
0.4449
0.22493
l in mm
-0.02356
0.01563
Fck
0.17406
0.23255
Fy
-0.10067
0.15577
Ast in mm2
0.03318
0.04894
Asv in mm2
-1.35944
0.85082
Table 4 (b ) Statistics for Deflection at First Crack Load
Deflection at First Crack Load
Number of Points
379
Degree of Freedom
371
Residual Sum of Squares
1.35505E7
Adj. R-Square
-0.00309
Table 4 (c) ANOVA Table for Deflection at First Crack Load
Deflection at First Crack Load
DF
Sum of Squares
Mean Square
F Value
Prob >F
Model
7
213159.58759
30451.36966
0.83373
0.55978
Error
371
1.35505E7
36524.25616
Total
378
1.37637E7
Yield Load
Table 5 (a) Parameters of Yield Load
Yield Load
Values
Standard Error
Intercept
76.40433
14.66513
b in mm
-0.37179
0.04978
d in mm
0.46918
0.04077
l in mm
-0.01128
0.00283
Fck
0.22926
0.04215
Fy
-0.10195
0.02823
Ast in mm2
0.03677
0.00887
Asv in mm2
-0.26065
0.1542
Table 5 (b ) Statistics for Yield Load
Yield Load
Number of Points
379
Degree of Freedom
371
Residual Sum of Squares
445107.76998
Adj. R-Square
0.33189
Table 5 (c) ANOVA Table for Yield Load
First Crack Load
DF
Sum of Squares
Mean Square
F Value
Prob >F
Model
7
233683.77525
33383.39646
27.82526
0
Error
371
445107.76998
1199.7514
Total
378
678791.54522
Deflection at Yield Load
Table 6 (a) Parameters of Deflection at Yield Load
Deflection at Yield Load
Values
Standard Error
Intercept
6.41907
6.26723
b in mm
-0.05275
0.02128
d in mm
0.02298
0.01742
l in mm
0.0039
0.00121
Fck
0.01455
0.01801
Fy
0.00967
0.01207
Ast in mm2
0.0171
0.00379
Asv in mm2
-0.09324
0.0659
Table 6 (b ) Statistics for Deflection at Yield Load
Deflection at Yield Load
Number of Points
379
Degree of Freedom
371
Residual Sum of Squares
81291.30095
Adj. R-Square
0.13423
Table 6 (c) ANOVA Table for Deflection at Yield Load
Deflection at Yield Load
DF
Sum of Squares
Mean Square
F Value
Prob >F
Model
7
14374.99422
2053.5706
9.37216
1.04021E-10
Error
371
81291.30095
219.11402
Total
378
95666.29518
Ultimate Load
Table 7(a) Parameters of Ultimate Load
Ultimate Load
Values
Standard Error
Intercept
65.16612
21.38557
b in mm
-0.1173
0.0726
d in mm
0.44043
0.05945
l in mm
-0.02201
0.00413
Fck
0.23504
0.06146
Fy
-0.1468
0.04117
Ast in mm2
0.01257
0.01294
Asv in mm2
0.91816
0.22487
Table 7 (b ) Statistics for Ultimate Load
Ultimate Load
Number of Points
379
Degree of Freedom
371
Residual Sum of Squares
946530.48175
Adj. R-Square
0.27466
Table 7(c) ANOVA Table for Ultimate Load
Ultimate Load
DF
Sum of Squares
Mean Square
F Value
Prob >F
Model
7
383041.68221
54720.24032
21.44802
0
Error
371
946530.48175
2551.2951
Total
378
1.32957E6
Deflection at Ultimate Load
Table 8(a) Parameters of Deflection at Ultimate Load
Deflection at Ultimate Load
Values
Standard Error
Intercept
27.16152
10.88859
b in mm
0.22081
0.03698
d in mm
-0.08007
0.03032
l in mm
0.02168
0.00212
Fck
0.09975
0.03129
Fy
-0.08273
0.02098
Ast in mm2
-0.00939
0.00661
Asv in mm2
-0.37328
0.11445
Table 8(b ) Statistics for Deflection at Ultimate Load
Deflection at Ultimate Load
Number of Points
377
Degree of Freedom
369
Residual Sum of Squares
243873.84226
Adj. R-Square
0.34536
Table 8 (c) ANOVA Table for Deflection at Ultimate Load
Deflection at Ultimate Load
DF
Sum of Squares
Mean Square
F Value
Prob >F
Model
7
135724.96018
19389.28003
29.33748
0
Error
369
243873.84226
660.90472
Total
376
379598.80244
INPUT PARAMETERS AND TARGET PARAMETRS FOR FIBER REINFORCED CONCRETE BEAMS
Table 4.1 Input Parameters for ANN based Modeling of Fiber Reinforced Concrete Beams with Incorporating Nano fillers and Micro fillers
Ref
Test Specimen
b in mm
d in mm
l in mm
fck N/mm²
Fy
Ast mm²
Asv mm²
[27] B1
100
200
2000
25
415
226.19
50.265
B2
100
200
2000
25
415
226.19
50.265
B3
100
200
2000
25
415
226.19
50.265
B4
100
200
2000
25
415
226.19
50.265
B5
100
200
2000
25
415
226.19
50.265
B6
100
200
2000
25
415
226.19
50.265
B7
100
200
2000
25
415
226.19
50.265
[6] NF
150
220
2500
200.9
510
198.6
71.3
NF
150
220
2500
200.9
510
126.7
71.3
S13
150
220
2500
211.8
495
198.6
71.3
S13
150
220
2500
211.8
495
126.7
71.3
S19.5
150
220
2500
209.7
491
198.6
71.3
S19..5
150
220
2500
209.7
491
126.7
71.3
S30
150
220
2500
209.7
491
198.6
71.3
S30
150
220
2500
209.7
491
126.7
71.3
T30
150
220
2500
232.1
491
198.6
71.3
T30
150
220
2500
232.1
491
126.7
71.3
[18] CC
230
250
2300
75.9
477
64
71
CC-SN
230
250
2300
89.3
477
64
71
CC-ST
230
250
2300
104.4
477
64
71
GG
230
250
2300
75.9
477
127
71
GG-SN
230
250
2300
89.3
477
127
71
GG-ST
230
250
2300
104.4
477
127
71
[44] S0L0
150
250
3000
26.65
500
226.194
50.265
S0L5
150
250
3000
26.65
500
226.194
50.265
S1L0
150
250
3000
26.65
500
226.194
50.265
S1L5
150
250
3000
26.65
500
226.194
50.265
[4] BY-0-2.5
140
180
1600
27.6
486
157.079
33.183
BY-1-2.5
140
180
1600
27.5
486
157.079
33.183
BY-2-2.5
140
180
1600
28.4
486
157.079
33.183
BX-1-2.5
140
180
1600
27.5
486
157.079
33.183
BX-2-2.5
140
180
1600
28.4
486
157.079
33.183
BX-1-2.5-360
140
180
1600
27.5
486
157.079
33.183
BX-2-2.5-360
140
180
1600
28.4
486
157.079
33.183
BX-1-2.5-180
140
180
1600
27.5
486
157.079
33.183
BX-1-2.5-180
140
180
1600
28.4
486
157.079
33.183
BY-0-3.5
140
180
2000
27.6
486
157.079
33.183
BY-1-3.5
140
180
2000
27.5
486
157.079
33.183
BY-2-3.5
140
180
2000
28.4
486
157.079
33.183
BX-1-3.5
140
180
2000
27.5
486
157.079
33.183
BX-2-3.5
140
180
2000
28.4
486
157.079
33.183
BX-1-2.5-360
140
180
2000
27.5
486
157.079
33.183
BX-2-2.5-360
140
180
2000
28.4
486
157.079
33.183
BX-1-3.5-180
140
180
2000
27.5
486
157.079
33.183
BX-2-3.5-180
140
180
2000
28.4
486
157.079
33.183
[46] M60
150
250
3000
67
537
339.29
50.265
M60-0.5%
150
250
3000
67
537
339.29
50.265
M60-1.0%
150
250
3000
67
537
339.29
50.265
M60-1.5%
150
250
3000
67
537
339.29
50.265
[40] RA
150
250
3000
64
456
157.079
50.265
RAC3
150
250
3000
64
456
157.079
50.265
RAC5
150
250
3000
64
456
157.079
50.265
RAU3
150
250
3000
64
456
157.079
50.265
RAU5
150
250
3000
64
456
157.079
50.265
RB
150
250
3000
64
456
235.619
50.265
RBC3
150
250
3000
64
456
235.619
50.265
RBC5
150
250
3000
64
456
235.619
50.265
RBU3
150
250
3000
64
456
235.619
50.265
RBU5
150
250
3000
64
456
235.619
50.265
[28] B1
250
250
2440
65.61
417
981.747
78.539
B2
250
250
2440
58.44
417
981.747
78.539
B3
250
250
2440
48.35
417
981.747
78.539
B4
250
250
2440
38.35
417
981.747
78.539
B5
250
250
2440
59.15
417
981.747
78.539
B6
250
250
2440
49.45
417
981.747
78.539
B7
250
250
2440
40.26
417
981.747
78.539
B8
250
250
2440
29.73
417
981.747
78.539
B9
250
250
2440
31.1
417
981.747
78.539
B10
250
250
2440
32.38
417
981.747
78.539
B11
250
250
2440
30.71
417
981.747
78.539
B12
250
250
2440
31.51
417
981.747
78.539
[29] CB1
150
200
2400
35.7
382
226.194
28.274
CB2
150
200
2400
35.7
382
508.938
28.274
CB3
150
200
2400
35.7
382
628.318
28.274
HT1
150
200
2400
56.08
418
226.194
28.274
HT2
150
200
2400
56.08
418
508.938
28.274
HT3
150
200
2400
56.08
418
628.318
28.274
HC1
150
200
2400
56.08
480
226.194
28.274
HC2
150
200
2400
56.08
480
508.938
28.274
HC3
150
200
2400
56.08
480
628.318
28.274
RC1
150
200
2400
106.5
410
226.194
28.274
RC2
150
200
2400
106.5
410
508.938
28.274
RC3
150
200
2400
106.5
410
628.318
28.274
[13] CCO.20
180
250
3500
32
420
78.5
50.265
SFRCO.20
180
250
3500
34.7
420
78.5
50.265
CCO.30
180
250
3500
34.2
420
113.1
50.265
SFRCO.30
180
250
3500
40.6
420
113.1
50.265
CCO.40
180
250
3500
33.8
420
153.9
50.265
SFRCO.40
180
250
3500
31.1
420
153.9
50.265
CCO.53
180
250
3500
37.8
420
201.1
50.265
SFRCO.53
180
250
3500
41.7
420
201.1
50.265
CCO.81
180
250
3500
31.4
420
307.9
50.265
SFRCO.81
180
250
3500
29.6
420
307.9
50.265
CC1.06
180
250
3500
35
420
402.1
50.265
SFRC1.06
180
250
3500
43.9
420
402.1
50.265
CCI.60
180
250
3500
36.7
420
603.2
50.265
SFRC1.60
180
250
3500
31.9
420
603.2
50.265
CC2.02
180
250
3500
21.5
420
763.4
50.265
SFRC2.02
180
250
3500
25
420
763.4
50.265
CC2.13
180
250
3500
25.7
420
804
50.265
SFRC2.13
180
250
3500
31.8
420
804
50.265
CC2.50
180
250
3500
24.7
420
942.5
50.265
SFRC2.50
180
250
3500
22.3
420
942.5
50.265
[8] B1 0 -6
150
150
1200
76.3
575
31.172
19.634
B2 0-8
150
150
1200
76.3
574
50.265
19.634
B3 0-10
150
150
1200
76.3
553
78.539
19.634
B4-0.5/45-10
150
150
1200
95.2
553
78.539
19.634
B5-1/45-6
150
150
1200
80.2
553
78.539
19.634
B6-2/45-6
150
150
1200
81.3
575
31.172
19.634
B7-2/45-8
150
150
1200
81.3
574
50.265
19.634
B8-2/45-10
150
150
1200
81.3
553
78.539
19.634
B9-2/80-10
150
150
1200
81.3
553
78.539
19.634
[30] B1-0.0F
152
229
1144
27.6
414
235.619
71
B2-0.0F
152
229
1144
27.6
414
235.619
71
B1-0.5F
152
229
1144
27.6
414
235.619
71
B2-0.5F
152
229
1144
27.6
414
235.619
71
B1-1.0F
152
229
1144
27.6
414
235.619
71
B2-1.0F
152
229
1144
27.6
414
235.619
71
Table 4.2 Target Parameters for ANN based Modeling of Fiber Reinforced Concrete Beams with Incorporating Nano fillers and Micro fillers
Ref
Test Specimen
first crack load (kN)
Deflection (mm)
yield load (kN)
Deflection (mm)
ultimate load (kN)
Deflection (mm)
[27] B1
19
14.1
0
0
53
21.02
B2
25
19
6
22
56.8
24.07
B3
32
20
15
30
62.1
22.02
B4
31
19.5
25
32
60.2
20.07
B5
9
10
30
36
43.3
14.49
B6
27
22
35
39
59.8
20.01
B7
18
15
40
42
46.3
16.04
[6] NF
36.6
1.12
46
9.15
62.6
94.53
NF
30.6
1.09
77.9
12.06
97.9
73.03
S13
26.6
0.75
80.6
11.96
87.3
28.41
S13
23.3
0.67
109.9
12.73
124.1
20.3
S19.5
18
0.82
78
11.54
93.3
30.51
S19.5
16.7
0.63
103.3
12.29
125.2
43.35
S30
21.3
1.12
79.9
11.33
95.9
30.46
S30
18.7
0.61
105.3
13.01
124.6
45.28
T30
18
0.78
77.9
11.03
96.6
36.22
T30
14.7
0.51
111.9
13.22
133.9
43.64
[18] CC
21
0.68
20
10.5
212
43.82
CC-SN
27
0.52
35
15.2
218
36.59
CC-ST
42
0.83
40
20
225
36.81
GG
23
0.67
50
22.2
207
38.85
GG-SN
35
0.65
60
21.5
230
50.88
GG-ST
39
0.79
70
25
259
56.19
[44] S0L0
19.62
3.48
39.24
8.83
49.05
30.25
S0L5
29.43
3.7
63.77
10.42
88.29
21.22
S1L0
22
5.82
39.6
11.2
58.8
48.16
S1L5
49.05
10
93.2
21.1
112.82
34.92
[4] BY-0-2.5
0
0
41.46
6.99
48.45
31.2
BY-1-2.5
10
5
43.52
5.98
50.2
14
BY-2-2.5
20
15
47.67
5.93
50.8
18.95
BX-1-2.5
30
20
57.5
7.85
63.6
12.87
BX-2-2.5
40
20.2
59.82
6.82
67.9
21.08
BX-1-2.5-360
50
25
58.95
9.31
64.95
20.64
BX-2-2.5-360
60
30
61.57
8.87
70.2
21.55
BX-1-2.5-180
70
35
61.37
6.77
70.4
19.7
BX-1-2.5-180
80
41
64.46
8.38
74.4
24.2
BY-0-3.5
15
10
26.41
9.8
30.8
25.73
BY-1-3.5
20
12
26.2
10.05
30.2
24.75
BY-2-3.5
25
30
26.99
7.48
30.9
16.15
BX-1-3.5
30
22
37.96
10.47
41.8
16.82
BX-2-3.5
35
22
38.2
10.01
42.7
20.8
BX-1-2.5-360
40
28
39.84
10.64
44.1
18.55
BX-2-2.5-360
45
30
41.19
10.77
45.55
48.64
BX-1-3.5-180
50
32
42.22
10.9
45.95
17.1
BX-2-3.5-180
60
33.3
42.27
11.03
46.9
27.1
[46] M60
3.5
3.63
6
8.46
8.25
13.44
M60-0.5%
3.75
3.58
6.25
8.29
8.29
14.81
M60-1.0%
4.25
3.44
7
7.75
7.75
15.5
M60-1.5%
4.25
3.55
6.75
6.75
8.06
16.1
[40] RA
14.39
1.26
29.42
7.91
41.68
21.05
RAC3
16.52
1.41
36.77
9.02
51.48
33.46
RAC5
21.28
3.67
46.58
10.1
66.19
46.81
RAU3
32.94
7.98
51.48
11.42
71.09
53.26
RAU5
36.81
9.23
53.7
10.74
78.45
57.21
RB
28.32
3.68
39.22
8.11
53.93
31.28
RBC3
30.95
4.71
51.48
11.35
61.29
36.23
RBC5
32.17
4.97
53.24
12.41
63.74
56.91
RBU3
33.69
9.35
58.8
12.85
88.25
61.04
RBU5
39.41
11.14
63
12.69
100.51
65.59
[28] B1
11.18
20
11.6
15
100.68
36.9
B2
10.13
7
11.5
15.1
97.55
38
B3
8.6
5
11.5
14
90.7
37.2
B4
7.02
5.6
11.7
14.1
84.26
34.1
B5
11.39
22
11.8
15.3
101.64
41.65
B6
9.49
10
12
20.2
94.51
40.4
B7
7.44
11
11.7
16
86.8
31.4
B8
6.16
10
12.7
21
78.63
22.5
B9
6.79
9.95
12.5
22.2
82.66
28
B10
8.2
14
12.8
19
89.45
38.75
B11
6.65
11
12.7
14.5
82.11
27.2
B12
7.91
13
12.9
13
86.68
36.95
[29] CB1
12
1.15
43
12.1
48
31.5
CB2
13
1.29
90.5
13.2
94.5
25.2
CB3
20
1.38
117.5
12.2
117.5
12.2
HT1
35
1.73
124
10.8
130
17.1
HT2
45
2.23
135
9.6
176
14.7
HT3
45
1.63
178
13.2
194
17.4
HC1
11
1.01
40
9.5
53
74
HC2
15
0.88
90.5
12.6
103
40.9
HC3
15
0.74
112.5
12.7
126
40.9
RC1
10
0.74
43
11.1
59
86.7
RC2
10
0.34
90
10.1
104
39.1
RC3
15
0.75
110
10.6
131
27.3
[13] CCO.20
0
0
0
0
11.81
110.9
SFRCO.20
5
3
10
5
18.72
64.5
CCO.30
10.5
12.5
20
18
18.48
109.5
SFRCO.30
13
14
30
11
21.29
86.2
CCO.40
20
20.3
40
31
25.39
107.9
SFRCO.40
26
22
50
35
27.54
95.3
CCO.53
32
24
55
42
31.56
104..3
SFRCO.53
40.5
39.9
60
59
34.85
157
CCO.81
55
41
65
48
47.9
92.1
SFRCO.81
68
40
70.5
53
47.01
176.5
CC1.06
74
35
76
65
58.11
56.7
SFRC1.06
83
22
80
78
61.77
175.7
CCI.60
97
39
84
36
81.35
41.5
SFRC1.60
102
10.5
99
21
82.4
164.2
CC2.02
107
15
101
17
87.85
59.4
SFRC2.02
110
25
105
14
97.3
126
CC2.13
113
34
110
70
93.74
70.7
SFRC2.13
118
28
117
63
100.2
101.2
CC2.50
120
14
115
58
100.82
70
SFRC2.50
122
15.9
125
78.5
108.15
133
[8] B1 0 -6
12
14.1
4.8
5.9
4.14
57.8
B2 0-8
15
15
7.1
9.1
6.05
38
B3 0-10
18
15.9
9.6
11.1
6.48
31.8
B4-0.5/45-10
20
19
11.6
11.5
4.78
19.8
B5-1/45-6
25
20.6
13.2
12.3
7.82
26.9
B6-2/45-6
29
28
10.1
6.5
4.48
23.2
B7-2/45-8
34
31
11.2
7.9
4.21
24.9
B8-2/45-10
36
33
14.2
13.4
7.71
24.8
B9-2/80-10
40
37
14.9
14.2
7.85
16.3
[30] B1-0.0F
5
5
156
6
188.2
13.56
B2-0.0F
13
12.5
178
9.74
206.4
14.78
B1-0.5F
15
15
156
3.91
194.8
12.65
B2-0.5F
17
17.5
178
6.64
198.8
10.82
B1-1.0F
25
20.1
156
2.94
211.7
9.65
B2-1.0F
34
23.5
178
4.23
234.4
13.23
Table 4.3 Experiment and ANN results (Levenberg Marquardt Algorithm) for Fiber Reinforced Concrete Beams with Incorporating Nano fillers and Micro fillers
Ref
Test Specimens
first crack load (kN)
Deflection (mm)
yield load (kN)
Deflection (mm)
ultimate load (kN)
Deflection (mm)
Exp
ANN
Exp
ANN
Exp
ANN
Exp
ANN
Exp
ANN
Exp
ANN
[27] B1
19
26.209
14.1
18.333
0
23.351
0
30.799
53
55.720
21.02
20.446
B2
25
26.209
19
18.333
6
23.351
22
30.799
56.8
55.720
24.07
20.446
B3
32
26.209
20
18.333
15
23.351
30
30.799
62.1
55.720
22.02
20.446
B4
31
26.209
19.5
18.333
25
23.351
32
30.799
60.2
55.720
20.07
20.446
B5
9
26.209
10
18.333
30
23.351
36
30.799
43.3
55.720
14.49
20.446
B6
27
26.209
22
18.333
35
23.351
39
30.799
59.8
55.720
20.01
20.446
B7
18
26.209
15
18.333
40
23.351
42
30.799
46.3
55.720
16.04
20.446
[6] NF
36.6
23.366
1.12
5.958
46
46.453
9.15
19.011
62.6
60.685
94.53
79.910
NF
30.6
30.890
1.09
6.026
77.9
75.381
12.06
22.683
97.9
99.141
73.03
77.862
S13
26.6
19.693
0.75
0.406
80.6
82.931
11.96
8.785
87.3
95.879
28.41
36.408
S13
23.3
27.838
0.67
1.696
109.9
101.134
12.73
14.580
124.1
125.777
20.3
40.724
S19.5
18
14.067
0.82
1.326
78
81.644
11.54
6.217
93.3
95.369
30.51
31.571
S19..5
16.7
22.543
0.63
0.362
103.3
97.320
12.29
12.505
125.2
123.162
43.35
37.245
S30
21.3
14.067
1.12
1.326
79.9
81.644
11.33
6.217
95.9
95.369
30.46
31.571
S30
18.7
22.543
0.61
0.362
105.3
97.320
13.01
12.505
124.6
123.162
45.28
37.245
T30
18
19.624
0.78
1.261
77.9
79.373
11.03
7.853
96.6
96.852
36.22
26.962
T30
14.7
27.384
0.51
2.674
111.9
93.373
13.22
14.630
133.9
124.067
43.64
34.600
[18] CC
21
28.569
0.68
2.624
20
31.471
10.5
15.845
212
194.017
43.82
42.812
CC-SN
27
33.194
0.52
0.202
35
42.744
15.2
17.891
218
217.811
36.59
41.832
CC-ST
42
36.540
0.83
0.930
40
51.256
20
20.234
225
234.219
36.81
44.825
GG
23
36.203
0.67
3.283
50
52.817
22.2
20.701
207
217.510
38.85
48.531
GG-SN
35
42.982
0.65
2.159
60
66.674
21.5
24.409
230
243.192
50.88
51.181
GG-ST
39
48.822
0.79
2.422
70
78.526
25
28.643
259
262.266
56.19
58.145
[44] S0L0
19.62
35.234
3.48
8.413
39.24
50.569
8.83
14.729
49.05
75.132
30.25
34.916
S0L5
29.43
35.234
3.7
8.413
63.77
50.569
10.42
14.729
88.29
75.132
21.22
34.916
S1L0
22
35.234
5.82
8.413
39.6
50.569
11.2
14.729
58.8
75.132
48.16
34.916
S1L5
49.05
35.234
10
8.413
93.2
50.569
21.1
14.729
112.82
75.132
34.92
34.916
[4] BY-0-2.5
0
40.878
0
22.552
41.46
54.784
6.99
9.316
48.45
61.516
31.2
19.772
BY-1-2.5
10
40.916
5
22.553
43.52
54.861
5.98
9.323
50.2
61.616
14
19.739
BY-2-2.5
20
40.575
15
22.545
47.67
54.174
5.93
9.262
50.8
60.721
18.95
20.036
BX-1-2.5
30
40.916
20
22.553
57.5
54.861
7.85
9.323
63.6
61.616
12.87
19.739
BX-2-2.5
40
40.575
20.2
22.545
59.82
54.174
6.82
9.262
67.9
60.721
21.08
20.036
BX-1-2.5-360
50
40.916
25
22.553
58.95
54.861
9.31
9.323
64.95
61.616
20.64
19.739
BX-2-2.5-360
60
40.575
30
22.545
61.57
54.174
8.87
9.262
70.2
60.721
21.55
20.036
BX-1-2.5-180
70
40.916
35
22.553
61.37
54.861
6.77
9.323
70.4
61.616
19.7
19.739
BX-1-2.5-180
80
40.575
41
22.545
64.46
54.174
8.38
9.262
74.4
60.721
24.2
20.036
BY-0-3.5
15
36.268
10
21.003
26.41
33.662
9.8
11.818
30.8
40.577
25.73
22.502
BY-1-3.5
20
36.252
12
20.995
26.2
33.680
10.05
11.802
30.2
40.579
24.75
22.469
BY-2-3.5
25
36.396
30
21.072
26.99
33.521
7.48
11.947
30.9
40.561
16.15
22.763
BX-1-3.5
30
36.252
22
20.995
37.96
33.680
10.47
11.802
41.8
40.579
16.82
22.469
BX-2-3.5
35
36.396
22
21.072
38.2
33.521
10.01
11.947
42.7
40.561
20.8
22.763
BX-1-2.5-360
40
36.252
28
20.995
39.84
33.680
10.64
11.802
44.1
40.579
18.55
22.469
BX-2-2.5-360
45
36.396
30
21.072
41.19
33.521
10.77
11.947
45.55
40.561
48.64
22.763
BX-1-3.5-180
50
36.252
32
20.995
42.22
33.680
10.9
11.802
45.95
40.579
17.1
22.469
BX-2-3.5-180
60
36.396
33.3
21.072
42.27
33.521
11.03
11.947
46.9
40.561
27.1
22.763
[46] M60
3.5
8.850
3.63
5.270
6
7.979
8.46
0.046
8.25
8.949
13.44
21.913
M60-0.5%
3.75
8.850
3.58
5.270
6.25
7.979
8.29
0.046
8.29
8.949
14.81
21.913
M60-1.0%
4.25
8.850
3.44
5.270
7
7.979
7.75
0.046
7.75
8.949
15.5
21.913
M60-1.5%
4.25
8.850
3.55
5.270
6.75
7.979
6.75
0.046
8.06
8.949
16.1
21.913
[40] RA
14.39
20.048
1.26
9.784
29.42
48.463
7.91
10.961
41.68
61.774
21.05
45.565
RAC3
16.52
20.048
1.41
9.784
36.77
48.463
9.02
10.961
51.48
61.774
33.46
45.565
RAC5
21.28
20.048
3.67
9.784
46.58
48.463
10.1
10.961
66.19
61.774
46.81
45.565
RAU3
32.94
20.048
7.98
9.784
51.48
48.463
11.42
10.961
71.09
61.774
53.26
45.565
RAU5
36.81
20.048
9.23
9.784
53.7
48.463
10.74
10.961
78.45
61.774
57.21
45.565
RB
28.32
29.347
3.68
9.281
39.22
55.377
8.11
16.594
53.93
78.439
31.28
51.229
RBC3
30.95
29.347
4.71
9.281
51.48
55.377
11.35
16.594
61.29
78.439
36.23
51.229
RBC5
32.17
29.347
4.97
9.281
53.24
55.377
12.41
16.594
63.74
78.439
56.91
51.229
RBU3
33.69
29.347
9.35
9.281
58.8
55.377
12.85
16.594
88.25
78.439
61.04
51.229
RBU5
39.41
29.347
11.14
9.281
63
55.377
12.69
16.594
100.51
78.439
65.59
51.229
[28] B1
11.18
4.041
20
8.313
11.6
6.820
15
19.542
100.68
99.905
36.9
40.503
B2
10.13
4.874
7
9.661
11.5
6.360
15.1
19.036
97.55
92.903
38
40.623
B3
8.6
6.150
5
10.734
11.5
6.794
14
18.035
90.7
86.294
37.2
39.028
B4
7.02
7.431
5.6
10.976
11.7
8.115
14.1
16.721
84.26
82.745
34.1
35.675
B5
11.39
4.788
22
9.550
11.8
6.375
15.3
19.093
101.64
93.507
41.65
40.659
B6
9.49
6.008
10
10.661
12
6.694
20.2
18.160
94.51
86.849
40.4
39.296
B7
7.44
7.191
11
10.984
11.7
7.815
16
16.995
86.8
83.239
31.4
36.434
B8
6.16
8.462
10
10.676
12.7
9.618
21
15.356
78.63
81.330
22.5
31.674
B9
6.79
8.305
9.95
10.750
12.5
9.368
22.2
15.586
82.66
81.480
28
32.367
B10
8.2
8.156
14
10.810
12.8
9.138
19
15.796
89.45
81.643
38.75
32.996
B11
6.65
8.350
11
10.730
12.7
9.439
14.5
15.521
82.11
81.435
27.2
32.172
B12
7.91
8.258
13
10.770
12.9
9.294
13
15.654
86.68
81.530
36.95
32.571
[29] CB1
12
5.638
1.15
10.421
43
45.538
12.1
8.461
48
52.989
31.5
27.244
CB2
13
22.071
1.29
9.510
90.5
93.425
13.2
12.122
94.5
99.652
25.2
25.723
CB3
20
25.947
1.38
6.755
117.5
106.512
12.2
11.459
117.5
119.282
12.2
17.233
HT1
35
29.556
1.73
2.119
124
113.494
10.8
14.260
130
130.866
17.1
33.496
HT2
45
38.695
2.23
2.993
135
153.102
9.6
12.649
176
176.037
14.7
15.046
HT3
45
45.349
1.63
4.195
178
168.879
13.2
13.149
194
196.493
17.4
5.926
HC1
11
8.037
1.01
9.014
40
51.078
9.5
7.448
53
42.313
74
64.872
HC2
15
14.687
0.88
1.010
90.5
91.138
12.6
9.641
103
92.074
40.9
56.505
HC3
15
23.985
0.74
1.154
112.5
111.029
12.7
11.842
126
120.261
40.9
46.721
RC1
10
7.396
0.74
6.911
43
42.553
11.1
17.276
59
60.909
86.7
78.768
RC2
10
11.704
0.34
1.084
90
87.490
10.1
8.641
104
103.330
39.1
41.527
RC3
15
19.044
0.75
3.359
110
109.519
10.6
8.030
131
129.544
27.3
26.268
[13] CCO.20
0
0.024
0
9.951
0
8.294
0
12.465
11.81
12.705
110.9
82.289
SFRCO.20
5
0.052
3
10.031
10
9.990
5
12.752
18.72
13.068
64.5
83.542
CCO.30
10.5
11.720
12.5
14.099
20
20.784
18
21.245
18.48
20.830
109.5
99.604
SFRCO.30
13
11.780
14
14.129
30
24.667
11
21.802
21.29
22.052
86.2
101.980
CCO.40
20
25.224
20.3
18.496
40
33.163
31
30.126
25.39
29.218
107.9
114.510
SFRCO.40
26
25.161
22
18.453
50
31.861
35
29.845
27.54
28.847
95.3
113.411
CCO.53
32
39.607
24
22.583
55
47.308
42
38.591
31.56
37.746
104..3
126.536
SFRCO.53
40.5
39.433
39.9
22.334
60
48.720
59
38.620
34.85
38.373
157
126.920
CCO.81
55
65.867
41
28.694
65
66.024
48
49.689
47.9
49.284
92.1
131.080
SFRCO.81
68
65.991
40
28.833
70.5
65.852
53
49.733
47.01
49.211
176.5
131.098
CC1.06
74
81.219
35
30.071
76
78.103
65
53.658
58.11
58.034
56.7
123.238
SFRC1.06
83
80.165
22
28.402
80
78.903
78
52.726
61.77
60.779
175.7
120.433
CCI.60
97
100.775
39
28.917
84
97.850
36
56.276
81.35
80.445
41.5
102.080
SFRC1.60
102
101.099
10.5
30.014
99
96.901
21
56.749
82.4
77.311
164.2
104.091
CC2.02
107
109.789
15
30.467
101
106.353
17
58.215
87.85
86.437
59.4
96.517
SFRC2.02
110
109.698
25
29.760
105
107.171
14
57.956
97.3
88.853
126
95.179
CC2.13
113
111.186
34
29.111
110
109.924
70
57.973
93.74
93.276
70.7
92.492
SFRC2.13
118
111.117
28
27.499
117
112.102
63
57.434
100.2
99.276
101.2
89.422
CC2.50
120
115.208
14
27.444
115
117.681
58
58.123
100.82
105.678
70
85.678
SFRC2.50
122
115.166
15.9
28.112
125
116.636
78.5
58.321
108.15
102.963
133
86.974
[8] B1 0 -6
12
23.436
14.1
22.990
4.8
7.788
5.9
7.068
4.14
1.208
57.8
34.625
B2 0-8
15
20.911
15
22.709
7.1
5.907
9.1
5.684
6.05
2.961
38
34.966
B3 0-10
18
27.642
15.9
23.326
9.6
13.032
11.1
8.913
6.48
9.976
31.8
33.480
B4-0.5/45-10
20
29.615
19
23.625
11.6
13.323
11.5
10.405
4.78
12.303
19.8
34.064
B5-1/45-6
25
27.991
20.6
23.383
13.2
13.012
12.3
9.199
7.82
10.331
26.9
33.624
B6-2/45-6
29
24.044
28
23.070
10.1
8.055
6.5
7.464
4.48
2.060
23.2
34.665
B7-2/45-8
34
21.451
31
22.782
11.2
6.101
7.9
6.049
4.21
2.238
24.9
35.029
B8-2/45-10
36
28.095
33
23.400
14.2
13.015
13.4
9.281
7.71
10.443
24.8
33.662
B9-2/80-10
40
28.095
37
23.400
14.9
13.015
14.2
9.281
7.85
10.443
16.3
33.662
[30] B1-0.0F
5
18.672
5
14.678
156
168.232
6
5.054
188.2
205.910
13.56
11.714
B2-0.0F
13
18.672
12.5
14.678
178
168.232
9.74
5.054
206.4
205.910
14.78
11.714
B1-0.5F
15
18.672
15
14.678
156
168.232
3.91
5.054
194.8
205.910
12.65
11.714
B2-0.5F
17
18.672
17.5
14.678
178
168.232
6.64
5.054
198.8
205.910
10.82
11.714
B1-1.0F
25
18.672
20.1
14.678
156
168.232
2.94
5.054
211.7
205.910
9.65
11.714
B2-1.0F
34
18.672
23.5
14.678
178
168.232
4.23
5.054
234.4
205.910
13.23
11.714
Table 4.4 Experiment and ANN results( Bayesian Regularization Algorithm) for Fiber Reinforced Concrete Beams with Incorporating Nano fillers and Micro fillers
Ref
Test Specimens
first crack load (kN)
Deflection (mm)
yield load (kN)
Deflection (mm)
ultimate load (kN)
Deflection (mm)
Exp
ANN
Exp
ANN
Exp
ANN
Exp
ANN
Exp
ANN
Exp
ANN
[27] B1
19
21.939
14.1
14.812
0
34.286
0
36.271
53
51.106
21.02
17.306
B2
25
21.939
19
14.812
6
34.286
22
36.271
56.8
51.106
24.07
17.306
B3
32
21.939
20
14.812
15
34.286
30
36.271
62.1
51.106
22.02
17.306
B4
31
21.939
19.5
14.812
25
34.286
32
36.271
60.2
51.106
20.07
17.306
B5
9
21.939
10
14.812
30
34.286
36
36.271
43.3
51.106
14.49
17.306
B6
27
21.939
22
14.812
35
34.286
39
36.271
59.8
51.106
20.01
17.306
B7
18
21.939
15
14.812
40
34.286
42
36.271
46.3
51.106
16.04
17.306
[6] NF
36.6
30.134
1.12
1.834
46
51.621
9.15
13.523
62.6
62.479
94.53
69.089
NF
30.6
28.136
1.09
2.070
77.9
76.693
12.06
15.506
97.9
93.928
73.03
74.292
S13
26.6
23.503
0.75
2.471
80.6
74.579
11.96
10.027
87.3
89.922
28.41
40.241
S13
23.3
21.899
0.67
2.836
109.9
100.319
12.73
11.700
124.1
121.691
20.3
45.485
S19.5
18
22.408
0.82
2.675
78
80.663
11.54
8.702
93.3
96.580
30.51
32.107
S19..5
16.7
21.101
0.63
3.389
103.3
106.129
12.29
11.091
125.2
127.850
43.35
38.849
S30
21.3
22.408
1.12
2.675
79.9
80.663
11.33
8.702
95.9
96.580
30.46
32.107
S30
18.7
21.101
0.61
3.389
105.3
106.129
13.01
11.091
124.6
127.850
45.28
38.849
T30
18
17.707
0.78
3.157
77.9
80.684
11.03
11.958
96.6
98.685
36.22
34.920
T30
14.7
14.640
0.51
2.597
111.9
106.344
13.22
11.258
133.9
130.164
43.64
36.162
[18] CC
21
27.111
0.68
1.044
20
26.972
10.5
12.159
212
205.850
43.82
33.834
CC-SN
27
28.526
0.52
0.116
35
37.909
15.2
15.367
218
218.253
36.59
39.629
CC-ST
42
29.979
0.83
0.934
40
50.969
20
18.811
225
232.852
36.81
45.492
GG
23
32.293
0.67
0.894
50
42.823
22.2
18.395
207
218.858
38.85
44.118
GG-SN
35
33.150
0.65
1.543
60
53.105
21.5
20.944
230
230.532
50.88
48.796
GG-ST
39
33.911
0.79
2.219
70
65.417
25
23.475
259
244.318
56.19
53.066
[44] S0L0
19.62
35.174
3.48
11.878
39.24
77.912
8.83
16.434
49.05
99.423
30.25
21.687
S0L5
29.43
35.174
3.7
11.878
63.77
77.912
10.42
16.434
88.29
99.423
21.22
21.687
S1L0
22
35.174
5.82
11.878
39.6
77.912
11.2
16.434
58.8
99.423
48.16
21.687
S1L5
49.05
35.174
10
11.878
93.2
77.912
21.1
16.434
112.82
99.423
34.92
21.687
[4] BY-0-2.5
0
40.469
0
22.152
41.46
55.440
6.99
8.188
48.45
61.693
31.2
19.944
BY-1-2.5
10
40.457
5
22.150
43.52
55.411
5.98
8.171
50.2
61.660
14
19.907
BY-2-2.5
20
40.562
15
22.176
47.67
55.667
5.93
8.321
50.8
61.962
18.95
20.238
BX-1-2.5
30
40.457
20
22.150
57.5
55.411
7.85
8.171
63.6
61.660
12.87
19.907
BX-2-2.5
40
40.562
20.2
22.176
59.82
55.667
6.82
8.321
67.9
61.962
21.08
20.238
BX-1-2.5- 360
50
40.457
25
22.150
58.95
55.411
9.31
8.171
64.95
61.660
20.64
19.907
BX-2-2.5- 360
60
40.562
30
22.176
61.57
55.667
8.87
8.321
70.2
61.962
21.55
20.238
BX-1-2.5- 180
70
40.457
35
22.150
61.37
55.411
6.77
8.171
70.4
61.660
19.7
19.907
BX-1-2.5- 180
80
40.562
41
22.176
64.46
55.667
8.38
8.321
74.4
61.962
24.2
20.238
BY-0-3.5
15
31.724
10
19.335
26.41
32.939
9.8
11.978
30.8
38.149
25.73
27.361
BY-1-3.5
20
31.698
12
19.330
26.2
32.882
10.05
11.954
30.2
38.088
24.75
27.311
BY-2-3.5
25
31.925
30
19.382
26.99
33.389
7.48
12.167
30.9
38.642
16.15
27.764
BX-1-3.5
30
31.698
22
19.330
37.96
32.882
10.47
11.954
41.8
38.088
16.82
27.311
BX-2-3.5
35
31.925
22
19.382
38.2
33.389
10.01
12.167
42.7
38.642
20.8
27.764
BX-1-2.5- 360
40
31.698
28
19.330
39.84
32.882
10.64
11.954
44.1
38.088
18.55
27.311
BX-2-2.5- 360
45
31.925
30
19.382
41.19
33.389
10.77
12.167
45.55
38.642
48.64
27.764
BX-1-3.5- 180
50
31.698
32
19.330
42.22
32.882
10.9
11.954
45.95
38.088
17.1
27.311
BX-2-3.5- 180
60
31.925
33.3
19.382
42.27
33.389
11.03
12.167
46.9
38.642
27.1
27.764
[46] M60
3.5
5.276
3.63
3.307
6
7.429
8.46
6.665
8.25
8.308
13.44
17.985
M60-0.5%
3.75
5.276
3.58
3.307
6.25
7.429
8.29
6.665
8.29
8.308
14.81
17.985
M60-1.0%
4.25
5.276
3.44
3.307
7
7.429
7.75
6.665
7.75
8.308
15.5
17.985
M60-1.5%
4.25
5.276
3.55
3.307
6.75
7.429
6.75
6.665
8.06
8.308
16.1
17.985
[40] RA
14.39
21.515
1.26
4.247
29.42
39.277
7.91
9.036
41.68
62.363
21.05
43.816
RAC3
16.52
21.515
1.41
4.247
36.77
39.277
9.02
9.036
51.48
62.363
33.46
43.816
RAC5
21.28
21.515
3.67
4.247
46.58
39.277
10.1
9.036
66.19
62.363
46.81
43.816
RAU3
32.94
21.515
7.98
4.247
51.48
39.277
11.42
9.036
71.09
62.363
53.26
43.816
RAU5
36.81
21.515
9.23
4.247
53.7
39.277
10.74
9.036
78.45
62.363
57.21
43.816
RB
28.32
33.481
3.68
5.944
39.22
54.370
8.11
14.443
53.93
73.328
31.28
50.668
RBC3
30.95
33.481
4.71
5.944
51.48
54.370
11.35
14.443
61.29
73.328
36.23
50.668
RBC5
32.17
33.481
4.97
5.944
53.24
54.370
12.41
14.443
63.74
73.328
56.91
50.668
RBU3
33.69
33.481
9.35
5.944
58.8
54.370
12.85
14.443
88.25
73.328
61.04
50.668
RBU5
39.41
33.481
11.14
5.944
63
54.370
12.69
14.443
100.51
73.328
65.59
50.668
[28] B1
11.18
8.963
20
12.792
11.6
17.624
15
20.154
100.68
96.242
36.9
41.471
B2
10.13
8.769
7
12.536
11.5
15.759
15.1
19.045
97.55
93.962
38
39.266
B3
8.6
8.654
5
12.186
11.5
13.317
14
17.504
90.7
90.970
37.2
36.174
B4
7.02
8.725
5.6
11.855
11.7
11.129
14.1
16.001
84.26
88.275
34.1
33.116
B5
11.39
8.784
22
12.561
11.8
15.939
15.3
19.154
101.64
94.182
41.65
39.484
B6
9.49
8.657
10
12.224
12
13.573
20.2
17.671
94.51
91.283
40.4
36.511
B7
7.44
8.697
11
11.917
11.7
11.528
16
16.286
86.8
88.767
31.4
33.700
B8
6.16
8.938
10
11.584
12.7
9.447
21
14.726
78.63
86.191
22.5
30.479
B9
6.79
8.894
9.95
11.626
12.5
9.701
22.2
14.927
82.66
86.507
28
30.899
B10
8.2
8.857
14
11.666
12.8
9.942
19
15.116
89.45
86.807
38.75
31.291
B11
6.65
8.906
11
11.614
12.7
9.628
14.5
14.870
82.11
86.416
27.2
30.779
B12
7.91
8.882
13
11.639
12.9
9.778
13
14.987
86.68
86.602
36.95
31.024
[29] CB1
12
0.646
1.15
7.861
43
46.986
12.1
7.560
48
48.829
31.5
35.649
CB2
13
17.169
1.29
8.912
90.5
87.933
13.2
22.955
94.5
97.957
25.2
34.172
CB3
20
21.488
1.38
3.353
117.5
115.494
12.2
12.799
117.5
124.763
12.2
5.021
HT1
35
35.950
1.73
7.296
124
109.995
10.8
2.269
130
129.339
17.1
28.888
HT2
45
40.866
2.23
1.961
135
146.867
9.6
11.018
176
172.406
14.7
20.465
HT3
45
44.369
1.63
2.165
178
166.808
13.2
7.806
194
189.523
17.4
6.069
HC1
11
14.058
1.01
10.796
40
41.088
9.5
12.527
53
49.343
74
56.226
HC2
15
18.455
0.88
2.940
90.5
92.309
12.6
9.259
103
105.080
40.9
46.998
HC3
15
35.271
0.74
2.670
112.5
113.562
12.7
18.697
126
124.321
40.9
60.487
RC1
10
16.853
0.74
6.727
43
48.208
11.1
15.946
59
58.587
86.7
72.835
RC2
10
11.189
0.34
5.157
90
89.828
10.1
9.438
104
107.551
39.1
36.074
RC3
15
17.130
0.75
6.177
110
113.002
10.6
12.720
131
127.085
27.3
33.534
[13] CCO.20
0
2.703
0
11.804
0
15.685
0
10.095
11.81
10.784
110.9
84.748
SFRCO.20
5
2.212
3
11.920
10
16.146
5
10.921
18.72
11.433
64.5
86.272
CCO.30
10.5
11.401
12.5
14.816
20
25.399
18
17.915
18.48
18.390
109.5
97.225
SFRCO.30
13
10.282
14
15.079
30
26.590
11
19.888
21.29
20.117
86.2
100.766
CCO.40
20
22.816
20.3
18.348
40
36.103
31
26.348
25.39
26.243
107.9
110.272
SFRCO.40
26
23.306
22
18.254
50
35.732
35
25.525
27.54
25.643
95.3
108.757
CCO.53
32
35.658
24
22.532
55
48.416
42
37.226
31.56
35.625
104..3
127.103
SFRCO.53
40.5
34.952
39.9
22.628
60
48.962
59
38.334
34.85
36.590
157
129.040
CCO.81
55
66.340
41
30.170
65
70.859
48
53.867
47.9
50.637
92.1
149.788
SFRCO.81
68
66.773
40
30.210
70.5
70.964
53
53.525
47.01
50.536
176.5
149.145
CC1.06
74
84.416
35
32.243
76
84.615
65
60.252
58.11
61.472
56.7
153.803
SFRC1.06
83
81.450
22
31.286
80
82.995
78
60.054
61.77
61.226
175.7
153.334
CCI.60
97
97.982
39
22.983
84
96.760
36
43.324
81.35
76.719
41.5
105.573
SFRC1.60
102
99.681
10.5
23.521
99
99.333
21
43.514
82.4
78.612
164.2
105.667
CC2.02
107
111.181
15
21.930
101
112.142
17
42.985
87.85
96.543
59.4
89.765
SFRC2.02
110
110.153
25
21.795
105
109.277
14
43.482
97.3
93.989
126
91.241
CC2.13
113
112.157
34
22.111
110
109.800
70
45.839
93.74
96.253
70.7
92.380
SFRC2.13
118
110.488
28
21.960
117
104.912
63
46.847
100.2
91.927
101.2
95.169
CC2.50
120
118.539
14
24.038
115
113.669
58
54.710
100.82
105.635
70
98.098
SFRC2.50
122
119.240
15.9
24.091
125
116.034
78.5
54.283
108.15
107.850
133
96.734
[8] B1 0 -6
12
25.172
14.1
24.398
4.8
6.870
5.9
7.113
4.14
2.833
57.8
30.349
B2 0-8
15
25.205
15
24.174
7.1
7.929
9.1
6.921
6.05
4.190
38
29.985
B3 0-10
18
27.771
15.9
24.439
9.6
12.927
11.1
8.627
6.48
9.110
31.8
34.852
B4-0.5/45- 10
20
27.863
19
23.974
11.6
14.908
11.5
8.535
4.78
13.031
19.8
34.706
B5-1/45-6
25
27.806
20.6
24.358
13.2
13.331
12.3
8.635
7.82
9.902
26.9
34.871
B6-2/45-6
29
25.166
28
24.302
10.1
7.254
6.5
7.108
4.48
3.711
23.2
30.298
B7-2/45-8
34
25.181
31
24.055
11.2
8.341
7.9
6.869
4.21
5.107
24.9
29.849
B8-2/45-10
36
27.814
33
24.334
14.2
13.445
13.4
8.635
7.71
10.126
24.8
34.872
B9-2/80-10
40
27.814
37
24.334
14.9
13.445
14.2
8.635
7.85
10.126
16.3
34.872
[30] B1-0.0F
5
19.915
5
15.008
156
172.684
6
7.208
188.2
207.946
13.56
12.465
B2-0.0F
13
19.915
12.5
15.008
178
172.684
9.74
7.208
206.4
207.946
14.78
12.465
B1-0.5F
15
19.915
15
15.008
156
172.684
3.91
7.208
194.8
207.946
12.65
12.465
B2-0.5F
17
19.915
17.5
15.008
178
172.684
6.64
7.208
198.8
207.946
10.82
12.465
B1-1.0F
25
19.915
20.1
15.008
156
172.684
2.94
7.208
211.7
207.946
9.65
12.465
B2-1.0F
34
19.915
23.5
15.008
178
172.684
4.23
7.208
234.4
207.946
13.23
12.465
Table 4.5 Experiment and ANN results (Scaled Conjugate Gradient Algorithm) for Fiber Reinforced Concrete Beams with Incorporating Nano fillers and Micro fillers
Ref
Test Specimens
first crack load (kN)
Deflection (mm)
yield load (kN)
Deflection (mm)
ultimate load (kN)
Deflection (mm)
Exp
ANN
Exp
ANN
Exp
ANN
Exp
ANN
Exp
ANN
Exp
ANN
[27] B1
19
25.660
14.1
15.751
0
45.794
0
2.233
53
52.413
21.02
22.090
B2
25
25.660
19
15.751
6
45.794
22
2.233
56.8
52.413
24.07
22.090
B3
32
25.660
20
15.751
15
45.794
30
2.233
62.1
52.413
22.02
22.090
B4
31
25.660
19.5
15.751
25
45.794
32
2.233
60.2
52.413
20.07
22.090
B5
9
25.660
10
15.751
30
45.794
36
2.233
43.3
52.413
14.49
22.090
B6
27
25.660
22
15.751
35
45.794
39
2.233
59.8
52.413
20.01
22.090
B7
18
25.660
15
15.751
40
45.794
42
2.233
46.3
52.413
16.04
22.090
[6] NF
36.6
14.248
1.12
7.106
46
62.002
9.15
12.301
62.6
89.956
94.53
36.561
NF
30.6
15.903
1.09
5.246
77.9
65.032
12.06
10.565
97.9
88.121
73.03
36.948
S13
26.6
19.859
0.75
5.931
80.6
83.133
11.96
16.522
87.3
99.441
28.41
49.563
S13
23.3
21.027
0.67
4.425
109.9
84.214
12.73
14.402
124.1
96.780
20.3
49.271
S19.5
18
20.685
0.82
5.311
78
85.170
11.54
16.800
93.3
102.346
30.51
51.194
S19..5
16.7
21.794
0.63
3.879
103.3
85.632
12.29
14.528
125.2
99.582
43.35
50.755
S30
21.3
20.685
1.12
5.311
79.9
85.170
11.33
16.800
95.9
102.346
30.46
51.194
S30
18.7
21.794
0.61
3.879
105.3
85.632
13.01
14.528
124.6
99.582
45.28
50.755
T30
18
22.357
0.78
6.787
77.9
95.950
11.03
18.736
96.6
97.752
36.22
56.472
T30
14.7
23.120
0.51
5.497
111.9
96.893
13.22
16.778
133.9
94.586
43.64
55.909
[18] CC
21
21.529
0.68
6.705
20
54.435
10.5
4.720
212
213.236
43.82
48.941
CC-SN
27
21.841
0.52
6.544
35
55.695
15.2
4.983
218
214.760
36.59
50.464
CC-ST
42
22.081
0.83
6.407
40
58.013
20
5.562
225
216.027
36.81
51.976
GG
23
20.936
0.67
6.407
50
54.148
22.2
4.689
207
211.617
38.85
45.367
GG-SN
35
21.201
0.65
6.145
60
54.938
21.5
4.928
230
212.991
50.88
47.206
GG-ST
39
21.403
0.79
5.906
70
56.946
25
5.554
259
214.141
56.19
49.083
[44] S0L0
19.62
17.217
3.48
16.280
39.24
12.870
8.83
12.473
49.05
27.432
30.25
29.092
S0L5
29.43
17.217
3.7
16.280
63.77
12.870
10.42
12.473
88.29
27.432
21.22
29.092
S1L0
22
17.217
5.82
16.280
39.6
12.870
11.2
12.473
58.8
27.432
48.16
29.092
S1L5
49.05
17.217
10
16.280
93.2
12.870
21.1
12.473
112.82
27.432
34.92
29.092
[4] BY-0-2.5
0
25.806
0
15.045
41.46
32.113
6.99
8.622
48.45
44.304
31.2
25.501
BY-1-2.5
10
25.808
5
15.046
43.52
32.135
5.98
8.639
50.2
44.340
14
25.507
BY-2-2.5
20
25.783
15
15.039
47.67
31.932
5.93
8.488
50.8
44.014
18.95
25.450
BX-1-2.5
30
25.808
20
15.046
57.5
32.135
7.85
8.639
63.6
44.340
12.87
25.507
BX-2-2.5
40
25.783
20.2
15.039
59.82
31.932
6.82
8.488
67.9
44.014
21.08
25.450
BX-1-2.5- 360
50
25.808
25
15.046
58.95
32.135
9.31
8.639
64.95
44.340
20.64
25.507
BX-2-2.5- 360
60
25.783
30
15.039
61.57
31.932
8.87
8.488
70.2
44.014
21.55
25.450
BX-1-2.5- 180
70
25.808
35
15.046
61.37
32.135
6.77
8.639
70.4
44.340
19.7
25.507
BX-1-2.5- 180
80
25.783
41
15.039
64.46
31.932
8.38
8.488
74.4
44.014
24.2
25.450
BY-0-3.5
15
28.044
10
13.536
26.41
36.798
9.8
7.575
30.8
54.890
25.73
27.210
BY-1-3.5
20
28.041
12
13.539
26.2
36.817
10.05
7.587
30.2
54.924
24.75
27.208
BY-2-3.5
25
28.067
30
13.513
26.99
36.654
7.48
7.483
30.9
54.620
16.15
27.225
BX-1-3.5
30
28.041
22
13.539
37.96
36.817
10.47
7.587
41.8
54.924
16.82
27.208
BX-2-3.5
35
28.067
22
13.513
38.2
36.654
10.01
7.483
42.7
54.620
20.8
27.225
BX-1-2.5- 360
40
28.041
28
13.539
39.84
36.817
10.64
7.587
44.1
54.924
18.55
27.208
BX-2-2.5- 360
45
28.067
30
13.513
41.19
36.654
10.77
7.483
45.55
54.620
48.64
27.225
BX-1-3.5- 180
50
28.041
32
13.539
42.22
36.817
10.9
7.587
45.95
54.924
17.1
27.208
BX-2-3.5- 180
60
28.067
33.3
13.513
42.27
36.654
11.03
7.483
46.9
54.620
27.1
27.225
[46] M60
3.5
13.560
3.63
6.504
6
5.284
8.46
13.611
8.25
27.399
13.44
6.507
M60-0.5%
3.75
13.560
3.58
6.504
6.25
5.284
8.29
13.611
8.29
27.399
14.81
6.507
M60-1.0%
4.25
13.560
3.44
6.504
7
5.284
7.75
13.611
7.75
27.399
15.5
6.507
M60-1.5%
4.25
13.560
3.55
6.504
6.75
5.284
6.75
13.611
8.06
27.399
16.1
6.507
[40] RA
14.39
25.987
1.26
16.793
29.42
50.414
7.91
23.195
41.68
55.944
21.05
51.147
RAC3
16.52
25.987
1.41
16.793
36.77
50.414
9.02
23.195
51.48
55.944
33.46
51.147
RAC5
21.28
25.987
3.67
16.793
46.58
50.414
10.1
23.195
66.19
55.944
46.81
51.147
RAU3
32.94
25.987
7.98
16.793
51.48
50.414
11.42
23.195
71.09
55.944
53.26
51.147
RAU5
36.81
25.987
9.23
16.793
53.7
50.414
10.74
23.195
78.45
55.944
57.21
51.147
RB
28.32
32.465
3.68
17.541
39.22
55.794
8.11
26.456
53.93
53.934
31.28
54.256
RBC3
30.95
32.465
4.71
17.541
51.48
55.794
11.35
26.456
61.29
53.934
36.23
54.256
RBC5
32.17
32.465
4.97
17.541
53.24
55.794
12.41
26.456
63.74
53.934
56.91
54.256
RBU3
33.69
32.465
9.35
17.541
58.8
55.794
12.85
26.456
88.25
53.934
61.04
54.256
RBU5
39.41
32.465
11.14
17.541
63
55.794
12.69
26.456
100.51
53.934
65.59
54.256
[28] B1
11.18
13.134
20
4.652
11.6
34.482
15
18.825
100.68
104.791
36.9
33.809
B2
10.13
12.185
7
4.322
11.5
26.666
15.1
17.065
97.55
98.845
38
34.279
B3
8.6
10.884
5
3.844
11.5
16.437
14
14.862
90.7
90.730
37.2
34.990
B4
7.02
9.640
5.6
3.362
11.7
7.144
14.1
12.965
84.26
83.013
34.1
35.727
B5
11.39
12.278
22
4.355
11.8
27.419
15.3
17.232
101.64
99.428
41.65
34.231
B6
9.49
11.024
10
3.897
12
17.510
20.2
15.088
94.51
91.600
40.4
34.910
B7
7.44
9.874
11
3.454
11.7
8.857
16
13.307
86.8
84.460
31.4
35.585
B8
6.16
8.610
10
2.943
12.7
-0.234
21
11.532
78.63
76.644
22.5
36.371
B9
6.79
8.771
9.95
3.010
12.5
0.901
22.2
11.748
82.66
77.638
28
36.269
B10
8.2
8.922
14
3.072
12.8
1.974
19
11.954
89.45
78.573
38.75
36.173
B11
6.65
8.725
11
2.991
12.7
0.577
14.5
11.686
82.11
77.355
27.2
36.298
B12
7.91
8.819
13
3.030
12.9
1.244
13
11.814
86.68
77.937
36.95
36.238
[29] CB1
12
29.190
1.15
16.677
43
62.162
12.1
20.034
48
88.746
31.5
34.427
CB2
13
37.154
1.29
21.403
90.5
107.443
13.2
22.909
94.5
127.361
25.2
27.980
CB3
20
44.592
1.38
25.343
117.5
140.232
12.2
28.671
117.5
150.377
12.2
24.976
HT1
35
28.449
1.73
14.792
124
61.036
10.8
13.421
130
82.848
17.1
30.296
HT2
45
34.265
2.23
17.699
135
96.980
9.6
18.043
176
117.410
14.7
28.174
HT3
45
40.768
1.63
20.757
178
125.658
13.2
24.782
194
140.420
17.4
27.713
HC1
11
25.110
1.01
14.595
40
64.868
9.5
8.228
53
85.807
74
21.733
HC2
15
28.634
0.88
16.873
90.5
92.389
12.6
16.156
103
117.092
40.9
22.355
HC3
15
34.212
0.74
19.013
112.5
113.013
12.7
23.623
126
139.770
40.9
25.037
RC1
10
31.526
0.74
10.370
43
65.624
11.1
15.053
59
67.618
86.7
40.068
RC2
10
39.709
0.34
10.195
90
101.327
10.1
22.385
104
103.882
39.1
47.002
RC3
15
46.905
0.75
11.733
110
126.622
10.6
29.875
131
128.406
27.3
51.524
[13] CCO.20
0
24.685
0
11.288
0
16.004
0
25.816
11.81
29.630
110.9
91.140
SFRCO.20
5
24.921
3
10.987
10
17.736
5
26.422
18.72
31.393
64.5
91.734
CCO.30
10.5
28.095
12.5
11.392
20
20.922
18
27.808
18.48
31.773
109.5
93.248
SFRCO.30
13
28.591
14
10.617
30
25.014
11
29.342
21.29
35.698
86.2
94.811
CCO.40
20
32.273
20.3
12.015
40
26.084
31
29.679
25.39
33.312
107.9
94.703
SFRCO.40
26
32.119
22
12.379
50
24.720
35
29.084
27.54
31.911
95.3
93.934
CCO.53
32
37.845
24
12.295
55
35.815
42
33.115
31.56
38.390
104..3
97.299
SFRCO.53
40.5
38.022
39.9
11.727
60
37.835
59
34.064
34.85
40.227
157
98.513
CCO.81
55
51.716
41
15.880
65
55.736
48
37.989
47.9
47.300
92.1
96.425
SFRCO.81
68
51.701
40
16.181
70.5
55.163
53
37.583
47.01
46.785
176.5
95.720
CC1.06
74
65.502
35
17.798
76
78.647
65
44.502
58.11
60.894
56.7
97.819
SFRC1.06
83
65.493
22
16.324
80
82.002
78
46.789
61.77
63.014
175.7
101.423
CCI.60
97
94.528
39
21.101
84
111.583
36
53.762
81.35
84.692
41.5
98.321
SFRC1.60
102
94.423
10.5
21.664
99
108.373
21
52.166
82.4
83.391
164.2
96.471
CC2.02
107
112.715
15
22.184
101
102.206
17
50.498
87.85
89.509
59.4
93.336
SFRC2.02
110
112.910
25
21.918
105
105.421
14
51.879
97.3
90.702
126
94.677
CC2.13
113
116.883
34
21.384
110
104.229
70
52.246
93.74
92.221
70.7
95.130
SFRC2.13
118
117.261
28
20.982
117
109.807
63
54.602
100.2
94.374
101.2
97.403
CC2.50
120
127.867
14
19.030
115
92.161
58
51.402
100.82
94.415
70
95.192
SFRC2.50
122
127.652
15.9
19.130
125
89.799
78.5
50.432
108.15
93.446
133
94.251
[8] B1 0 -6
12
22.453
14.1
18.945
4.8
15.138
5.9
12.361
4.14
17.574
57.8
26.963
B2 0-8
15
23.022
15
18.906
7.1
15.471
9.1
12.446
6.05
19.534
38
27.806
B3 0-10
18
21.961
15.9
19.406
9.6
16.646
11.1
13.177
6.48
16.480
31.8
26.875
B4-0.5/45- 10
20
21.336
19
20.133
11.6
17.094
11.5
12.333
4.78
17.499
19.8
26.422
B5-1/45-6
25
21.791
20.6
19.564
13.2
16.677
12.3
12.943
7.82
16.584
26.9
26.701
B6-2/45-6
29
22.243
28
19.170
10.1
15.246
6.5
12.079
4.48
17.776
23.2
26.759
B7-2/45-8
34
22.832
31
19.136
11.2
15.602
7.9
12.180
4.21
19.805
24.9
27.642
B8-2/45-10
36
21.746
33
19.607
14.2
16.692
13.4
12.883
7.71
16.624
24.8
26.660
B9-2/80-10
40
21.746
37
19.607
14.9
16.692
14.2
12.883
7.85
16.624
16.3
26.660
[30] B1-0.0F
5
24.841
5
29.126
156
162.619
6
20.701
188.2
208.545
13.56
7.183
B2-0.0F
13
24.841
12.5
29.126
178
162.619
9.74
20.701
206.4
208.545
14.78
7.183
B1-0.5F
15
24.841
15
29.126
156
162.619
3.91
20.701
194.8
208.545
12.65
7.183
B2-0.5F
17
24.841
17.5
29.126
178
162.619
6.64
20.701
198.8
208.545
10.82
7.183
B1-1.0F
25
24.841
20.1
29.126
156
162.619
2.94
20.701
211.7
208.545
9.65
7.183
B2-1.0F
34
24.841
23.5
29.126
178
162.619
4.23
20.701
234.4
208.545
13.23
7.183
-
Proposed Regression Equations for Fibre Reinforced Concrete Beams Incorporated Micro Fillers and Nano Fillers are presented in table 9
Table 9. Regression Equation
PARAMETERS
REGRESSION EQUATIONS
FIRST CRACK LOAD
41.538+0.27b-0.09d+0.00l+0.06fck-0.07fy-0.03Ast-0.10Asv
DEFLECTION AT FIRST CRACK LOAD
88.97-0.122b+0.44d-0.02l+0.17fck-0.10fy+0.03Ast-1.35Asv
YIELD LOAD
76.40-0.37b+0.46d-0.01l+0.22fck-0.10fy+0.03Ast-0.26Asv
DEFLECTION AT YIELD LOAD
6.41-0.05b+0.02d+0.00l+0.01fck+0.00fy+0.01Ast-0.09Asv
ULTIMATE LOAD
65.166-0.117b+0.44d-0.02l+0.23fck-0.14fy+0.01Ast+0.91Asv
DEFLECTION AT ULTIMATE LOAD
27.161+0.22b-0.08d+0.02l+0.09fck-0.08fy-0.00Ast-0.37Asv
-
-
RESULTS AND DISCUSSION
-
For predicting the performance of fibre reinforced concrete beams incorporating nano fillers and micro fillers, regression analysis using origin pro has been used in this study. The proposed regression equations performed well for the first crack load, deflection at first crack load, yield load, deflection at yield load, ultimate load and deflections at ultimate load for fibre reinforced concrete beams incorporating nano fillers and micro fillers and the comparison of experimental and regression results for fibre reinforced concrete beams incorporating nano fillers and micro fillers are shown in table 9. To evaluate the accuracy of the models, scatter plots were drawn between the experimental and predicted results are shown in Fig13 and Fig 14. illustrate that experimental and predicted values of performance of fibre reinforced concrete beams incorporating nano fillers and micro fillers correlate well and the representative points in the scatter plots correlate to the line of equality.
Figure 13. Scatter plots of first crack load, deflection at first crack load and yield load.
Figure 14. Scatter plot of Deflection at yield load, Ultimate load and Deflection at Ultimate load.
Table 10 Statistical Indicators
OUTPUT PARAMETERS |
Fibre reinforced concrete beams incorporating nano fillers and micro fillers |
||
RMSE |
R2 |
MAPE |
|
First Crack load |
4.56 |
0.97 |
11.73 |
Deflection at First Crack load |
3.17 |
0.97 |
12.37 |
Yield load |
10.89 |
0.98 |
10.27 |
Deflection at Yield load |
3.12 |
0.98 |
12.03 |
Ultimate load |
12.57 |
0.97 |
12.70 |
Deflection at Ultimate load |
4.99 |
0.98 |
12.77 |
6.CONCLUSION
-
Fiber reinforced concrete beams incorporating nano fillers and micro fillers exhibit improved performance in terms of load and deformation capacity.
-
ANN model constituted with Bayesian Regularization Algorithm gives better results than the other two algorithm.
-
ANN modeling has proved to be a reliable tool for predicting the performance of FRC beams incorporating nano fillers and micro fillers.
REFERENCES
[1] Anwar Mohammed (2014), Influence of Nano Materials on Flexure Behavior and Compressive Strength of Concrete, Housing and Building Research Journal, Vol.11, pp 113-128. [2] Alberto Meda et al (2012),Flexural Behavior of RC Beams in Fiber Reinforced Concrete, Elsevier Composites : Part B , Vol.43, pp 2930-2937. [3] By Byung Hwan Oh , Flexural Analysis of Reinforced Concrete Beams Containing Steel Fibers, Journal of Structural Engineering , Vol.10, pp :2821-2835.
[4] Barzin Mobasher, Yiming Yao, Chote Sornakom (2015), Analytical Solutions for Flexural Design of Hybrid Steel Fiber Reinforced Concrete Beams, Engineering Structures, Vol.100,pp 167-177. [5] Bimal Babu Adhikary, Hiroshi Mutsuyoshi (2006), Prediction of Shear Strength of Steel Fiber RC Beams Using Neural Networks, Construction and Building Materials, Vol.20,pp 801-811. [6] Benmokrane.B, Chaallal.O,Masmoudi.R 1995, Glass Fibre Reinforced Plastic Rebars for Concrete Structures, Construction and Building Materials, Vol.9, pp 353-364. [7] Balaji.E, Senthil Selvan.S, Vishnu Prasad .P.R,An Experimental Study on the Effect of Nano Silica on Strength and Durability of Concrete,International Journal of Civil Engineering and Technology, Vol.8, pp 1182-1188.
[8] By Byung Hwan Oh (1992), Flexural Analysis of Reinforced Concrete Beams Containing Steel Fibers, Journal for Structural Engineering, Vol.10,pp 2821-2835. [9] Chao Xu,Ping Zhou Cao,Kai Wu,Shi Qi Lin,Ding Guo Yang (2019),Experimental Investigation of the Behavior Composite Steel Concrete Composite Beams Containing Different Amounts of Steel Fibers and Conventional Reinforcement, Construction and Building Materials, Vol.202,pp 23-26. [10] Dancygier A N and Savir Z. (2011), Effects of Steel Fibres on Shear Behaviour of High- Strength Reinforced Concrete Beams, Advances in Structural Engineering, Vol 14. [11] Doo Yeol Yoo,Young Soo Yoon (2015), Structural Performance of Ultra High Performance Concrete Beams With Different Steel Fibers,Engineering Structures, Vol.102,pp 409-423. [12] Doo Yeol Yoo, Hyun Oh Shin, Jun Mo Yang, Young Soo Yoon 2014, Material and Bond Properties of Ultra High Performance Fibre Reinforced Concrete with Micro Steel Fibres, Elsevier Composite Part B, Vol 58, pp 122-133. [13] Deepthi Dennison (2014), Effect of Metakaolin on the Structural Behavior of Normal and Steel Fiber Reinforced Concrete Beams, International Journal of Science and Engineering Research, Vol.5. [14] Daniel C.T.Cardoso,Gabriel B.S.Pereira,Flavio A.Silva,JULIO J.H.Silva Filho (2019),Influence of Steel Fibers on the Flexural Behavior of RC Beams with Low Reinforcing Ratios, Composite Structures, Vol.222,pp 110-926. [15] Delsye .C.L.Teo, Md.Abdul Mannan, John V.K uriann (2006), Flexural Behavior of Reinforced Lightweight Concrete Beams Made with Oil Palm Shell, Journal of Advanced Concrete Technology, Vol.4, pp 1-10. [16] Ehsan Nikbakht, Amin Al Fakih, Chieng Chew Hui (2019), An Experimental Investigation on the Shear and Flexural Behavior of Steel Reinforced HPSCC Beams, Structures, Vol.19,pp 286-295. [17] Frank Kusel, Elsabe Kearsley.( 2019), Effect of Steel Fibres in Combination with Different Reinforcing Ratios on the Performance of Continuous Beams, Construction and Building Materials, Vol 227, pp 116-533. [18] Farid Hasan Nattaj, Mahdi Nematzadeh (2017), The Effect of Forta Ferro and Steel Fibers on Mechanical Properties of High Strength Concrete with and without Silica Fume and Nano silicaConstruction and Building Materials, Vol.137,pp 557-572.