
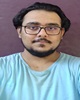
- Open Access
- Authors : Dhruv Pathak, Biswajit Sahoo, Chandraneel Pal, Piyush Nanda
- Paper ID : IJERTV9IS070675
- Volume & Issue : Volume 09, Issue 07 (July 2020)
- Published (First Online): 04-08-2020
- ISSN (Online) : 2278-0181
- Publisher Name : IJERT
- License:
This work is licensed under a Creative Commons Attribution 4.0 International License
Anti-Roll Bar Design and Material Selection for the Torsion Member for A Formula Student Vehicle
Dhruv Pathak, Biswajit Sahoo, Chandraneel Pal, Piyush Nanda
School of mechanical engineering, Kalinga Institute of Industrial Technology, Bhubaneshwar, India
Abstract – The following study will be dealing with the design procedure, constraints, and limitations that were dealt with during the design of the Anti-roll bar system of a formula student vehicle. Also, simulations with proper forces for torsion on the torsional member to select the best possible material for the torsion member was done.
Keywords- FSAE, Anti-roll bar, Roll, Formula student
INTRODUCTION
Anti-roll bar sometime also known as a stabilizer bar or sway bar is used for the purpose of controlling the roll motion of the vehicle. It provides better stability during corning. Roll motion referred as to the motion in the lateral direction on the Y-axis during which the vehicle rolls around the central axis of the vehicle.
Image Courtesy- RHD-JAPAN Anti- Rollbar increases overall roll stiffness of the vehicle, thus providing a number of advantages to the vehicle and its performance.
One of the major advantages is that it provides better traction during cornering the vehicle.
METHOD USED
The calculations were done in the following syntax –
RIDE RATES – ROLL ANALYSIS – ARB DIMENSIONS AND MATERIAL SELECTION
Ride rates were calculated by first determining the desired Natural frequencies of the front as well as rear but separately. These values were chosen using the general values which have validated after years of experimentation and observation.
Natural frequency for the front suspension = 2 Hz Natural frequency for the rear suspension = 2.5Hz
The reason behind aiming for higher natural frequency in the rear is to compensate for the response delay, since its always the front suspension which has to act first.
Then, the ride rates were calculated for the front and rear individually using the following expression-
Here, Krf= Ride Rate front wF=Natural Frequency Front
Wsf= Sprung mass front
Roll Analysis – Here the first which needs to be calculated is the COG height of the sprung mass.
which can be calculated using the following expression – Here, hs= sprung COG ht., h=COG ht., Wuf=Unsprung
wt. Front,
RLf= Tire loaded radius(Static) front, Wur=Unsprung wt. Rear
RLr=Tire loaded radius(Static) Rear
Sprung Wt. distribution = Sprung wt front/Total sprung mass.
Rolling Moment (lever Arm) =
( Sprung mass cog ht.)-[Front Roll Centre ht+(Rear Roll Centre ht.-Front Roll Centre ht.)(1-sprung mass wt. distribution)]
Rolling moment per g lateral acceleration =
Here, Hrm= Rolling moment (lever arm) ————-
—- Calculated above
Now, dividing this value with the desired roll gradient will give us the Roll Rate required(K).
Roll gradient should be taken between 1.5 – 3deg/g for an fs vehicle.
Now calculate available Front spring roll rate by using the following expression –
Here, Ksf = Front spring roll rate
Krf = Ride rate front (calculated during ride analysis) Tf = Track width front
Similarly, by using adequate value, the available rear spring roll rate(Ksr) can be determined.
Adding both the front and rear roll rates will give us the total available roll rate.
So, arb must provide = Required roll rate – available roll rate
Now, to size the front and rear bars, we need to calculate this requirement based on the weight distribution of the vehicle.
Here, TLT/Ay = Total load transfer during lateral acceleration.
Tave= Average of Front and Rear track width
Multiply this with %load transfer X 100 to get front/rear load transfer.
Front Roll Stiffness (Kf) =
Here, = Roll Gain ( 0.5 – 1 for non-aero fs vehicles)
From here, it can be calculated that the rear arb must provide
the difference between the total, rear, and that provided by the rear springs.
K(arb)rear = K – Kf – Ksr
Divide this by the Linkage ratio(rear) to get the final requirement.
For the front,
K(arb)front = (Kf – Ksf)/linkage ratio(front) RESULTS AND DISCUSSION FOR THE METHOD
The whole calculation was done by preparing a spreadsheet to facilitate the calculations. For which the results are shown as followed –
It can be seen that the required stiffness for the rear comes out to be negative, which symbolizes that the rear suspension is stiff enough and does not require an arb setup.
MATERIAL SELECTION
The following materials were considered-
Mild steel – AISI 1020 80 GPa shear modulus
Aluminum – AL-7075 T6 26.9 GPa shear modulus
Magnesium alloy – AZ31B 17 GPa shear modulus
Although magnesium alloy provides great weight reduction advantage it is expensive and also for the same thickness, withstands lower stress than aluminum.
After running simulations aluminum was considered as the optimal choice as it provided enough durability, is lightweight, and cheaper than magnesium alloy.
The size was determined by comparing the required area moment of inertial to the area moment of inertia of the arb system torsion bar with desired dimensions.
Required area moment of inertia = [(Required Roll stiffness X Length of tube)/Shear Modulus]
Area moment of inertia for cylindrical tube = [(4
4)]/32
The following simulation was done by applying 650N on both ends in torsion that sums up to 1300N in total.
With dimensions OD= 35mm
ID= 15mm
CONCLUSION –
Anti-roll bar torsion member with outer diameter of 35mm and inner diameter 15mm was designed to provide roll stiffness of 760.4731927 Nm/mm.
ACKNOWLEDGMENT
Biswajit Sahoo, School of mechanical engineering, Kalinga Institute of Industrial Technology
Chandraneel Pal, School of mechanical engineering, Kalinga Institute of Industrial Technology
Piyush Nanda, School of mechanical engineering, Kalinga Institute of Industrial Technology
Softwares Used – CAD Modelling – Solidworks 2020
Simulation – Ansys R17.2
REFERENCES
Racecar vehicle dynamics, William F. Millikan; Douglas Millikan