
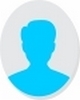
- Open Access
- Authors : Polycarp Ukachi, Ugochukwu C. Okonkwo, Ifeanyichukwu U. Onyenanu
- Paper ID : IJERTV13IS080018
- Volume & Issue : Volume 13, Issue 08 (August 2024)
- Published (First Online): 14-08-2024
- ISSN (Online) : 2278-0181
- Publisher Name : IJERT
- License:
This work is licensed under a Creative Commons Attribution 4.0 International License
Appraisal of the Insulation Potential of Rice Husk Ash Reinforced Calabash-Epoxy Composite for Vehicle Firewall Application
Polycarp Ukachi, Ugochukwu C. Okonkwo,
Department of Mechanical Engineering, Nnamdi Azikiwe University, Awka, Nigeria
Ifeanyichukwu U. Onyenanu
Department of Mechanical Engineering, Chukwuemeka Odumegwu Ojukwu University, Nigeria
ABSTRACT
This paper presents the appraisal of the insulation potential of rice husk ash-reinforced calabash-epoxy composite. Calabash and rice husks were collected from the agrarian communities in Eastern Nigeria and then processed into composite-compatible particles. The dried calabash fibres were pulverized into powder with the aid of a laboratory-scale hammer mill, while the rice husks were carbonized into ash in a furnace at about 500 0C. Samples of composites were developed with varying ratios of calabash powder (CP) and rice husk ash (RHA) for the investigation of their thermal and other material properties regarding insulation potential. Four combinations with design ratios, CPRHA, 020, 1010, 200 and 155 were considered whereas at every stage of the mixture formulation, the content of the epoxy resin was maintained as 80% of the overall mixture. The thermal properties of the developed samples had been characterized by differential scanning calorimetry and the result of this procedure revealed that the best formulation of the composite would have a mean thermal conductivity of 0.049Wm-1K-1. Furthermore, the Response Surface Methodology (RSM) provided a clear insight into how the proportion of the component of the adopted mixtures would influence the thermal and mechanical properties of the developed composites. This method determined a very close alignment of the actual and predicted values of the material properties of the composites. Also, results from the optimization process suggested that the best-fit model of the novel insulation composites would constitute 15% calabash fibre, 5% rice husk ash and 80% epoxy resin, with the resultant material density of 1.055g/cm3, thermal conductivity of 0.151Wm-1K-1, thermal resistivity of 0.183Wm-1K-1 and material hardness value of 61.046 shores D. The statistical significance of the developed model and its reliability was reinforced through a regression analysis indicating a considerable agreement between the empirical values and expected results of optimization. Comparatively, the overall results of the optimization infer adequately that the new composite would be capable of navigating the design space successfully and would also be more suitable for light-weight applications as well as have a higher potential for thermal reduction than the pressed-steel insulators whose thermal conductivity and density have been found higher. Finally, this study concludes that the developed model of RHA Reinforced Calabash Epoxy composite possesses adequate insulation potential and would be quite suitable for application in the firewall system of automotive.
-
INTRODUCTION
Thermal insulation is one aspect of engineering technology that is associated with the most global demand. It constitutes over 60% of the global demand for insulation materials which are categorically mineral wool, fiberglass and plastics [1]. In 2018, only mineral wool production reached over 16 million tons, fiberglass over 10 million tons and plastic foams including polyurethane and polyethene comprised around 35 million tons [2]. The Asia-Pacific led global consumption of insulation materials at 38% in 2018 followed by Europe at 30% and North America at 25% [1]. Insulation materials have been predominated by glass wool, lightweight and cellular concretes, kaolin, fiberglass plastic foams, Styrofoam and expanded pearlite [3]. Glass wool is the most commonly used among the materials due to its resistance to fire and its lightweight compared to other conventional insulation materials [4]. In some cases, better performance is achieved by replacing conventional materials with glass wool packed between thin metal sheets of about 0.6 mm to play a better role [5]. Carbon fibre and aluminium composites with silica blanketing for insulation and foil can also be incorporated in some cases. These insulation materials are inorganic and have been associated with some drawbacks such as shrinkage, high coefficients of heat conductance at temperatures above 300°C, and emission of fine aluminosilicate dust during the installation process of the insulation structure [6]. Besides, their continual use can be harmful to human health and the body and also cause environmental pollution through carbon emission and the release of other toxic particles [7]. The production of these materials is highly energy-intensive and their eventual disposal can also lead to environmental degradation [8]. The mitigation of these drawbacks has become an ultimate need which prioritizes studies that lead to the development of insulation composites from biological materials. Thus, there is an increasing focus on the development of environmentally friendly biomaterials, and yet
have the same and even better insulation properties than conventional materials. Most of the previous studies had investigated the insulation potential of organic fibres [9]. For example, natural fibers lead the new materials that have been widely investigated for insulation capabilities; and the use of natural fibers as viable substitutes to conventional insulating materials has favoured a lot of research in the area of renewable organic fibrous materials [8, 11, and 12]. Moreover, research reports from different regions of the world have shown that the use of agricultural and bio- materials such as coffee husk and hulls, wood, waste tea leaves, coconut husk, bagasse, cotton and oil palm for particle board production is effective and environmentally friendly [10]. Agricultural by-products used as insulating materials are believed to make significant contributions to the economic development of rural communities [10]. Also, proper management of renewable biodegradable insulators can have a net reduction in carbon dioxide emissions over the life cycle than the inorganic materials [14]. The current study responds to the quest for increased development of engineering materials from organic sources and particularly aims at investigating the insulation potential of a new composite called rice husk ash reinforced calabash epoxy composite (RHA/Calabash-Epoxy Composite).
-
MATERIALS AND METHOD
-
Raw Materials
The raw materials employed in this study were calabash powder (CP), rice husk ash (RHA) and epoxy resin with a hardener component called Liquid Vinyl Triethoxy Silane. The calabash fibre had been sourced from fresh calabash fruits which were collected from a local farm located at Ugbawka Community in Enugu State. The fruits were thoroughly cleaned, peeled and sliced into cylindrical pieces of approximate thickness of 2-3cm. About 5kg of sliced parts were evenly spread on trays and allowed to dry under ambient temperature for fourteen days. The dried fibres were pulverized with the aid of a laboratory scale hammer mill fitted with a 2 mm sieve. The rice husk which was formerly sourced from the Rice Mill Company Nigeria Limited, Abakiliki, was heated for two hours in a closed laboratory heat furnace maintained at 500°C to carbonize it to ash. The burnt rice husk was allowed to cool at room temperature after which it was ground to ash. All particle sizes were analyzed via a standard sieve analysis employing a set of sieves of apertures 150 m, 250 m, 450 m and 650 m arrangd in descending order and mounted on a mechanical shaker. The particles while placed onto the top sieve were agitated in the shaker for about 15 minutes followed by the collection and storing of the desirable particle sizes.
-
Mixture Design`
A 2-level full factorial design was adopted to determine how the thermal properties of the composite formulation would be affected by any quantitative variation in the ratio of CP to RHA. A total of four combinations with mixture ratios, CPRHA, 020, 1010, 200 and 155 were prepared to form samples 1, 2, 3, and 4 respectively. An increase in the natural fibre loading by up to 40% by weight in polymer composites would lead to an improvement in its mechanical and physical properties [11]. Hence the overall fibre content (CP + RHA) was fixed at 20% by weight while varying the individual component ratios systematically. The remaining 80% of the polymer matrix was constituted by an epoxy resin-hardener system (binder).
-
Development of Composite Samples
The composite mixture was manually blended with a spatula inside a clean, dry plastic container until a homogenous mixture was attained. A portion of the blended mixture was transferred into aluminium moulds of dimension 100 mm x 100 mm x 10 mm fabricated specifically as per ASTM C518 standard for thermal conductivity specimen preparation. All entrapped air had been expelled from the mixture using a hydraulic compression press. Upon complete mould filling, the composites were allowed to cure at room temperature for 24 hours to achieve an impartial chemical reaction between the resin and hardener and also a perfect cross- linking of the polymer chains and solidification. The solidified composites were withdrawn from the molds followed by the trimming of uneven edges. For each composition ratio, a total of eleven specimens were prepared for repeatability and statistical validity of results. The samples were classified according to their mixture design ratios as samples 1, 2, 3, and 4. A fifth sample referred to as control sample was also developed to serve as a reference for comparison. It was entirely composed of the binder in the absence of the natural fibres.
-
Differential Scanning Calorimetry (DSC)
Following a procedure proposed by Harkvoor and Van Rejien in 1985, both the thermal conductivity and thermal resistance of the developed samples were determined from simple DSC measurements conforming to ASTM D318 [15]. The DSC generated thermograms of the prerequisite thermal quantities of the classified composite samples from which the thermal conductivities and resistivity of the samples were derived through
the application of the theoretical models: = ; and = , where Q is the heat flow, W, k is
coefficient of thermal conductivity, W(m-1.K-1), A is a plane area, (m2), dT is changed in temperature, K, L is unit length (m) and R is thermal resistance, W(m -1K-1),. Other material properties studied include hardness which was determined from a shore D durometer hardness tester conforming to ASTM D2240, density and morphology of the samples.
-
Design of Experiment
The experiment was conducted with the Design Expert Software 12.0 in such a way that it developed a flexible design structure to accommodate custom models, categorical factors and irregular (constrained) regions. The three primary material mixture factors that would affect the performance of the insulation composite were varied accordingly. Runs were determined by a selection criterion chosen during the build. The experiment design response is presented in Table 1. However further discussions on the responses are given in subsequent sections. Finally, the predicted developed model was validated through the use of an optimal (custom) design a specialized form of randomized design from the surface response method (RSM). This enabled the selection of the sample that has an optimal mixture model. The four product attributes of the optimal sample (density, thermal conductivity, thermal resistance, density and hardness) were measured as responses from the design of the experiment and then validated by comparison against the reference standard (control sample).
Table 1: Experimental Design Response
Component 1
Component 2
Component 3
Response 1
Response 2
Response 3
Response 4
Run
A: Calabash
B: Rice Husk Ash
C: Binder
Density
Thermal Conductivity (C)
Thermal Resistivity (R)
Hardness
%
%
%
g/cm3
W.M-1. K-1
K/W
Shore D
1
10
10
80
1.078
0.1323
0.1708
60
2
20
0
80
1.014
0.1695
0.1956
59.3
3
20
0
80
1.014
0.1695
0.1956
59.3
4
0
20
80
0.842
0.1987
0.2299
52.8
5
10
10
80
1.078
0.1323
0.1708
60
6
15
5
80
1.039
0.1789
0.205
60.5
7
5
15
80
0.996
0.2032
0.2344
56
8
10
10
80
1.078
0.1323
0.1708
60
9
0
20
80
0.842
0.1987
0.2299
52.8
10
0
20
80
0.842
0.1987
0.2299
52.8
11
20
0
80
1.014
0.1695
0.1956
59.3
-
RESULT AND DISCUSSION
-
Morphology
Figures 1(a) and 1(b) captivatingly unveil the SEM-generated imagery showcasing the intricate structure and morphology of the four composite samples. An examination of the micrographs revealed the meticulous arrangement, diverse shapes and discernible colours of the component materials within the composites. There was a striking uniformity in the distribution of the constituent materials. This is attributed to the synergistic influence of both pug milling and extrusion processes. Again, this harmonious dispersion describes the efficacy of the techniques employed and also visibly translates into the overall quality of the composite's physical and mechanical properties, reinforcing the notion of a well-crafted and skillfully engineered product.
Figure 1: SEM-generated micrograph of the composite: (a) Optical Microscopy 175x 1,
(b) Optical Microscopy 450x 1
-
Density
Density (g/cm3
The densities of the four samples were expressed as a bar chart in Figure 2. The chart explains that the samples have unequal densities, with sample 1 having the most value, then sample 3 and sample 2. This variation was due to the differencein the analytical masses of the constituents. Values of the densities measured in the order of sample classification were recorded as 0.2344g/cm3, 0.1708g/cm3 and 0.205g/cm3 in the order of sample classifications.
0.25
0.2
0.15
0.1
0.05
0
1
2
3
4
samples
Figure 2: Bar chart showing sample densities
-
Hardness
A comprehensive understanding of the trends within the hardness values dataset is illustrated in Figure 3. The chart shows that sample 3 recorded the highest value of hardness and was closely followed by sample 2 which measured 60 Shore D. That of sample 1 was 56 Shore D which was practically the least among the record. Sample 3 having the most hardness value proves that it would perform better than other samples under torsion loads commonly experienced in the engine hood of automobiles.
Figure 3: Bar chart showing hardness values of samples
-
Thermal Conductivity
Figure 4(a) shows the DSC thermogram of sample 1 which had a mass of 7.2000 mg, 5% RHA, and 15% CP. Considering the graph, a single clear endothermic peak is visible between two temperatures namely, 337.2K and
338.38K respectively. This indicates the absorption of heat by the sample over this temperature range. Using the slope and requisite parametric values at this point in the graph, the thermal conductivity of the sample was calculated as 0.1789Wm-1K-1. Similarly, thermograms of thermal conductivities of samples 2, 3 and 4 are shown in Figures 4(b-d). The graphs also reveal that heat absorption over a certain temperature gradient was a common phenomenon among the samples. For sample 2, a single clear endothermic peak occurred between temperatures of approximately 336.06K and 337.85K, whereas for samples 3 and 4, it occurred between 335.65K and
337.55K and between 337K and 338.4K respectively. Thermal conductivities of these samples were calculated as 0.1323Wm-1K-1, 0.2032Wm-1K-1 and 0.1641Wm-1K-1 respectively.
Figure 4(a): DSC generated thermogram of sample 1
Figure 4(b): DSC generated thermogram of sample 2
Figure 4(c): DSC generated thermogram of sample 3
Figure 4(d): DSC thermogram of sample 4
-
Thermal Resistance
Figure 5 presents the DSC thermograms of the thermal resistance of the four tested samples of the composite. The corresponding values of thermal resistance of each sample had been derived from its DSC thermograms considering the region of the endothermic peak. Values of thermal resistance recorded were 0.205W/(mK), 01708W/(mK), 0.2032W/(mK) and 0.1748W/(mK) for samples 1,2,3 and 4 respectively. The coefficient of thermal resistance of a material denotes its ability to oppose heat flow and an increase in the value of thermal resistivity would result in a better insulation potential [6]. Therefore, samples 1 and 3 having the most values of thermal resistance would have a higher tendency to oppose the heat flow through them and consequently, offer a better thermal reduction. Moreover, sample 3 associated with the highest load of calabash powder has shown the best insulation potential throughout the experiment. On the other hand, samples 2 and 4 have slightly lower values of thermal resistance as a result of their low calabash fibre loading. This shows that the materials of both samples will allow marginally higher heat flow through them, hence reducing their thermal insulation potential. Above all, increasing the amount of calabash fibre loading resulted in increased thermal resistance of the composites.
Figure 5(a): Thermal Resistance of sample 1
Figure 5(b): Thermal resistance of sample 2
Figure 5(c): Thermal Resistance of sample 3
-
Optimization Response
-
-
-
Figure 5(d): Thermal Resistance of Sample 4
Improving the experimental design through the optimization process led to the generation of model equations of coefficients for the four product attributes considered as follows:
-
Density (D) = [0.009848 CP + 0.011657 RHA 0.000305(CP. RHA)]
-
Hardness (H) = [2.96272 CP + 2.63772 RHA + 0.037224(CP. RHA) + 0.000833(CP. RHA) (CP RHA)]
-
Thermal Conductivity (C) = [0.008574 CP + 0.010109 RHA 0.000381(CP. RHA)]
-
Thermal Resistance (R) = [0.009848 CP + 0.011657 RHA – 0.000305(CP. RHA)]
The predicted quantities of the requisite material properties derived from the model equations of coefficients have been compared against the actual outcomes of the experiment conducted as shown in Figures 6(a-d), which indicate close similarities between the predicted outcomes and experimental values of the material properties of the samples.
(a) Density (b) hardness
(c) Thermal conductivity (d) Thermal resistivity
Figure 6: Predicted data set vs. actual data of samples
Furthermore, from the solution of the combination of the 3 categorical factor levels, the selected or optimal material mixture values for the newly developed insulation composite material were found to be composed of 15% CP, 5% RHA and 80% Epoxy resin system. This attribute corresponds to sample 3; and the model yielded a material density of 1.055 g/cm3, thermal conductivity of 0.151 W/mK, thermal resistance of 0.183 W/mk, and material hardness value of 61.046 shore D. Comparing the material properties of the optimal against those of the control sample also revealed a close correlation between the optimal sample and the control sample as shown in figure 7.
Comparative analysis
120
100
80
60
40
20
0
0
1
2
3
4
5
6
7
8
-20
Control Sample
Optimal Sample
Figure 7: Scatter diagram of comparative analysis of control and optimal sample.
4. CONCLUSION
The thermal insulation effectiveness of any insulation material depends on its thermal conductivity and thermal resistance. The material density and hardness are also essential in achieving low-weight technology and product durability respectively. Therefore, to design and select an appropriate insulation material, all the thermal parameters associated with it should be studied thoroughly. This study has led to the development of a novel composite called RHA Reinforced Calabash-Epoxy composite. Thermal conductivity, thermal resistance, hardness and density of the new material have been studied and the composite has been found to have a considerable potential for thermal insulation. Finally, this study concludes that that RHA Reinforced Calabash- Epoxy composite is suitable for thermal insulator application and can also be use appropriate for use in automotive firewall design.
REFERENCES
-
Insulation Market Size, Share & Forecast Report 2032 https://www.marketresearchfuture.com/reports/insulation-market-1654
-
Owens, C. (2020). Insulation Market Overview. Global Insulation Industry Trends. https://www.owencornins/en- us/commercial/insulation/learn-and-discover/insulation-101/insulation-market-overview.html.
-
Ezema, I. C. (2019). Insulation Materials. Sustainable Construction Technologies. 237-762. Buttenworth Heinemann, 2019. https://www.sciencedirect.com/science/article/pii/B9780128117491000079
-
Salih, M. T. (2021). Thermal Conductivity of Wood Plastic Composite Insulation Panels: Theoretical and Experimental Analysis.
Epitoanyag Journal of Silicate Base And Composite Materials, vol. 73. 54-62. https://doi.10.14382/epitoanyag-jsbcm.2021.9
-
Srikanth, M. Asmantulu, R. (2013). Insulation Materials. Nanotechnology Safety n Construction and Infrastructure. 909-113
-
Ryzhenkov, A.V., Pogorelov, S. I., Longinova, N. A., Merdinikov, A. F. & Tkhabisimov, B. (2016). Radiant Heat Transfer Reduction Method in Heat Insulation of Power Equipment. https://www.witpress.com/Secure/elibrary/papers/HT16/HT16011FU1.pdf
-
Liang, H. H. & Ho, M. C. (2007). Toxicity Characteristics of Commercially Manufactured Insulation Materials for Building Applications In Taiwan. Constr. Build. Mater, 21: 1254-1261.
-
Sanjay, M. R., Arpitha, G. R., Naik, L. L., Gopalakrishnan, K. & Yogesha, B. (2016). Application of Natural Fiber and Its Composites: An Overview. Natural Resources, Vol.7(3)
-
Ogbonna, P. E, Ezemagu, C. J., Maduekwe, N. A. & Nwosis, P. U. (2013). Effect of Calabash Fiber Reinforcement and Aspect Ratio on Mechanical Properties of Calabash Polyester Composite. Research Journal of Chemical Sciences, Vol. 3.
-
Tangjuank, S. (2011). Thermal Insulation and Physical Properties of Particleboards from Pineapple Leaves. International Journal of Physical Sciences. Vol. 6(19). 4528-4532.
-
Mohd, Y., Haeryip, S., Jefferies, R., Ahmed, R., Balamurugan, A., Norazman, M., & Shohaimi, A. (2011). Optimization of Coconut Fibers Toward Heat Insulator Applications. Global Engineers and Technologists Review. https://aunilo.uum.edu.my/Find/Record/my.utem.eprints.3998/Details
-
Pickering, K. L., Efendy, M.G. & Le, T. M. (2016). A Review of Recent Development in Natural Fiber Composites and their Mechanical Performance. Composite part A: Applied Science and Manufacturing, 83, 98-112.
-
Bozsaky, D. (2019). Nature-Based Thermal Insulation Materials from Renewable Resources A State of the Art Review. https://www.semanticscholar.org. DOI: 10.2478/sjce-2019-0008.
-
Shafiqul, I. & Gajanan, B. (2019). Environmentally-Friendly Thermal and Acoustic Insulation Materials from Recycled Textiles. Journal of environmental management. 251(109536). https://doi.org/10.1016/j.jevman.2019.10536.
-
Mettler Toledo. (2010). Simple Determination of Thermal conductivity of polymers by DSC. Thermal Analysis Usercom 22. www.mt.com
IJERTV13IS080018
(This work is licensed under a Creative Commons Attribution 4.0 International License.)