
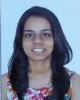
- Open Access
- Authors : Shivani Redkar , Chaya Dhargalkar , Dikshita Shirodkkar , Vrushali Kelkar , Pramila Volvoikar
- Paper ID : IJERTV9IS070211
- Volume & Issue : Volume 09, Issue 07 (July 2020)
- Published (First Online): 17-07-2020
- ISSN (Online) : 2278-0181
- Publisher Name : IJERT
- License:
This work is licensed under a Creative Commons Attribution 4.0 International License
Automated Counting System for Industrial Conveyors
Vrushali Kelkar
Electronics and Communication Engineering Department Agnel Institute of Technology and Design
Assagao, Goa-India
Pramila Volvoikar
Electronics and Communication Engineering Department Agnel Institute of Technology and Design
Assagao, Goa-India
Shivani Redkar
Electronics and Communication Engineering Department Agnel Institute of Technology and Design
Assagao, Goa-India
Chaya Dhargalkar
Electronics and Communication Engineering Department Agnel Institute of Technology and Design
Assagao, Goa-India
Dikshita Shirodkkar
Electronics and Communication Engineering Department Agnel Institute of Technology and Design
Assagao, Goa-India
AbstractProduct manufacturing could be a tedious method that involves quality management and big analysis along with its quantity measurement .The classification specifically supports production rate i.e. quantity factor. It can be achieved by manual labour in industries having either high or low production rate still it is not possible to make an accurate measurement during the production process. The amount of any product is a crucial element for estimating the economic growth and financial status of the industry. This project aims in counting the number of objects placed on a moving conveyor that helps in improving the demographics of production. The main facet of the project is to automate the process of transportation of the materials to the respective destinations using sensors and PLC.
IndexTermsPLC, Conveyor, Sensors, RS Logix 500, RS Linx.
I.INTRODUCTION
The area of focus in this project is the development of a system which helps in automatic counting of the objects passed through the conveyor belt. It saves labour force and time. The system designed is a prototype for an automatic monitoring and control system for probing objects on a conveyor belt .The counting system is mainly used for transportation operation in the industry. It also provides real time information to the operator if the predefined number of the objects is not equal to those received at the destination point. This system is implemented by using PLC which is the main component along with the sensors.
Our project aims to develop automated counting system for the conveyor belt which is used in large industries as it has advantages over manual systems. Manual systems are much cost inefficient as it includes labour wages which need to be paid time to time. More the labour , more the industry needs to spend on the wages. Also manual systems are not always accurate. There can be possibility of a mistake in counting at few events which makes them unreliable. It is also very time consuming as manpower is slow if compared to any machine designed for specific task.
The objective of the thesis is to design a automated counting system for conveyor belt which reduces the chances of error in counting.
II.METHODOLOGY
The Allen Bradley1000 PLC is the core component of the proposed system and can be programmed in ladder programming. The proximity sensor used has a range of 300 mm which is given as input to the PLC .A DC Motor is attached to the conveyor belts which will move after the motor is energized by the 12 V DC battery. When the sensor detects any object on the conveyor belt, it emits a beam of electromagnetic radiation. The transmitter andreceiver are always in the same housing so that the light transmitted is reflected in the receiver as reflection and hence the object is sensed. A relay is connected to the PLC which is used to control high current circuits using low current signals.When 12V supply is given from the battery further connected to a motor ,the motor generates back emf which may damage the PLC. Hence relay is used between motor and PLC. To count the number of objects passed through the conveyor , encoder is used which gives output in the form of pulses. It has a disk which rotates and generates a pulse for each incremental step in its rotation. When a predefined number of objects passed through the conveyor is the same which is received at the destination point, an indicator light is turned on . SMPS is used as a switching regulator. The real time movement of the objects can be viewed through WindowViewer of the WonderwareInTouch software and notify the operator time to time about any object lost in-between while on the conveyor belt.
Block diagram of prototype system III.HARDWARE COMPONENTS
- Allen Bradley 1000 PLCA programmable logic controller also referred to as programmable controller is an industrial computer employed and used in huge industries for controlling production processes.
Allen-Bradley is the name of a line of factory automation equipment which is owned by Rockwell Automation.
It also contains isolated RS-232/RS-485 combo port for network and serial communication.
It has 6 inputs and 4 outputs.
Both inputs and outputs have a DC-COM pin as well.
- Proximity sensorThe proximity sensor detects any input from the physical environment and has range of 300 mm . The principle of the diffuse proximity sensor is predicted on object reflection. The photoelectric sensor uses the light reflected by the object which is in front of the sensor. For a diffuse proximity sensor, the transmitter and receiver are always in the same housing, so that the light transmitted is reflected in the receiver as a reflection. The output produced is a signal that is converted to a form which is human-readable and is transmitted electronically over a network for further processing.
- RelayRelays are used to control high voltage circuits with the help of low voltage signals. Also they are used to control high current circuits with the help of low current signals. They are also used as protective relays and hence the faults during transmission and while receiving can be detected and isolated. A relay is an electromagnetic switch which operates when a small electric current is fed that can turn on or off a much larger electric current. It has 5 pins: Coil End 1, Coil End 2, Common, Normally Close (NC), Normally Open (NO).The 2 coil ends are used for triggering. When there is no energizing voltage applied, the COM point is linked to the normally closed (NC) point and the normally opened (NO) point remains open.But when the energizing voltage is applied, the COM point is connected to NO point and the NC point remains open.
- EncoderAn Encoder may be a sensing device that gives feedback and converts motion to an electrical signal during a motion
system which is read by a control device, like a counter or PLC.An incremental rotary encoder provides great speed and distance feedback as compared to other type of rotary encoder which features fewer sensors, making it less expensive and having less possibilities of failure. As the disk rotates, the patterns interrupt the beam emitted onto the photo detector and generate a pulse signal output. An incremental encoder generates a pulse for every incremental step in its rotation. The two sensors of the incremental encoder allow it to determine the direction of the rotation since the two sensors are 90 degrees out of phase in terms of the generated waveforms.
- DC MotorThe basic working principle of a DC motor is: “whenever a current carrying conductor is placed in a magnetic field, it experiences a mechanical force”.DC motor uses the DC current to convert electricity into mechanical energy.
The speed of a DC motor is 250 rpm. The seed is controlled using a variable supply voltage or by changing the strength of the current within its field windings
When electric current is passed through the coil in a magnetic field, a magnetic force is generated, which produces a torque in the DC motor.
- Switched Mode Power Supply(SMPS)
SMPS stands for Switched-Mode Power Supply/Switching Mode Power Supply which is an electronic power supply that uses a switching regulator to convert electrical power efficiently. It uses a switching regulator to control and stabilize the output voltage by switching the load current on and off. These power supplies offer a greater power conversion and reduce the general power loss.
SMPS used in PLC
As PLC works on 24V DC supply we have used SMPS to convert 230V AC to 24V DC. From this we can understand that by using low power we are able to control a huge amount of power that is used to run a huge machines in industries.
- IMPLEMENTATION
- Designing an EncoderWe have designed an incremental encoder using metal. Inductive sensor is used since it detects metal plate which moves along with conveyor belt in rotary motion. A metal disc with slots is used which will help in counting pulses. Every time a slot is sensed by the sensor it indicates 1 pulse which is given to PLC
An inductive sensor is a device based on the principle of electromagnetic induction to detect objects .It develops a magnetic field when a current flows through it. Also, a current flows through a circuit containing an inductor when the magnetic field through it changes.
- PLC Connections
- Prototype System
Final Prototype System
- Designing an EncoderWe have designed an incremental encoder using metal. Inductive sensor is used since it detects metal plate which moves along with conveyor belt in rotary motion. A metal disc with slots is used which will help in counting pulses. Every time a slot is sensed by the sensor it indicates 1 pulse which is given to PLC
- SOFTWARE IMPLEMENTATIONThe hardware consisting of the PLC along with other components is programmed using RS Logix 500 which is he PLC programming software. The code is written in the form of ladder program as it is easy to understand.
RS Logix 500 is a ladder logic programming package for the SLC 500 and MicroLogix processors and can be used with any Rockwell Automation programming packages. It
has a free-form ladder editor. A point and click interface to access all of the project’s folders and files. A compare utility that allows you to view project differences.
RS Linx is the linking software of PLC .RS Linx is a window based communication software package that acts like a communication link between the Allen Bradley programming software. You can virtually communicate from anywhere using RS Linx. The product provides a user-friendly graphical interface for navigating through your network hierarchy.
WindowViewer Display
Wonderware InTouch is a Human Machine Interface (HMI).The WindowViewer display of the Wonderware InTouch software is used to display the real time movement of the objects passed through the conveyor belt.
It has an open and extensible Supervisory HMI and SCADA solution that permits rapid creation of reusable visualization applications, standardized and deployment in an enterprise.
- CONCLUSION
In this article, we presented an automated counting system for conveyor belt which reduces the error in counting. Conveyance System which will help in conveyance of object from source todestination reducing the use of manpower which was time consuming and will be cost efficient.
ACKNOWLEDGMENT
We are highly indebted to Prof. Vrushali Kelkar and Prof. Pramila Volvoikar for their expert advice, guidance, constant supervision and encouragement . We express our deepest gratitude to our family for their constant and unwavering support and for pushing us to do the best of our capabilities.
REFERENCES
- Sanjay Prakash Dabadea, Rohan Prakash Chumbleb-Automatic Sorting Machine Using Conveyor Belt – IJIERE e-ISSN: 2394 – 3343 p-ISSN: 2394 – 5494 Volume 2, Issue 5, 2015 International Journal of Advanced in Management, Technology and Engineering Sciences Volume 7, Issue 12, 2017 ISSN NO : 2249-7455 293 http://ijamtes.org/
- Wu Li, Yang Zheng, Dong Xinfa, 2010 : The design and research of belt transport system based on PLC, Advances in Energy Engineering (ICAEE), 2010. International Conference, pp. 120 124.
- Porkuian, Igor Kurganov Technological Institute, Volodymyr Dahl the East-Ukrainian National University, Lugansk , Ukraine Research of the Automatic Control System of belt conveyor on the technical basis of the Industrial Controller Schneider electric Olga COMMISSION OF MOTORIZATION AND ENERGETICS IN AGRICULTURE 2012, Vol. 12, No.4,223-228
- Industrial Production Line Automation Using PLC System, Department of Electrical and Electronic Engineering University of Khartoum, July 2009.
- Programmable Logic Controllers Programming Methods and Applications, by John Hackworth and Frederick Hackworth December-2012.
- DESIGN_AND_IMPLEMENTATION_OF_PLC_BASED_ITEM_ COUNTING_SYSTEM,IJCIRAS Research Publications