
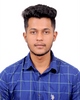
- Open Access
- Authors : Aheesh Bharadwaj K K, Likhith H L, Manjunath S Gowda
- Paper ID : IJERTV12IS110155
- Volume & Issue : Volume 12, Issue 11 (November 2023)
- Published (First Online): 01-12-2023
- ISSN (Online) : 2278-0181
- Publisher Name : IJERT
- License:
This work is licensed under a Creative Commons Attribution 4.0 International License
Automation Of Pesticide / Fertilizers Blending And Delivery System
Aheesh Bharadwaj K K
Department of Computer Science And Engineering, P.E.S College Of Engineering, Mandya
Manjunath S Gowda
Department Of Computer Science And Engineering, P.E.S College Of Engineering, Mandya
Likhith H L
Department Of Computer Science And Egnineering, P.E.S College Of Engineering, Mandya
Abstract- The tool that assists in combining the necessary chemicals in the right proportion to create the specific pesticide that crops need is the Pesticide Blending and Delivery System. It is crucial to be exact when mixing pesticides and determining how much to spray or give to the crops since various crops need different chemicals put in the right ratio. Farmers and cultivators physically carry out this operation, which poses a major risk to their health because to the toxic chemicals in the pesticides. It also poses a risk to crop yields if the quantity of pesticide applied goes over or falls short of the needed proportion. The suggested technology facilitates the entire procedure without requiring human involvement, may lessen health problems in people, and can increase agricultural yields efficiently.
Keywords Pesticide Blending and Delivery System, Farmers, Crops, Toxic chemicals, Crop yield.
-
INTRODUCTION
The main objective of the initiative is to completely automate the mixing and application of fertilizers and insecticides. Farmers and cultivators manually carry out this operation, which poses a major risk to their health because to the toxic chemicals in the pesticides. It also poses a risk to crop growth if the dose of pesticide applied goes over or falls short of the needed quantity. Our objective is to automate the insecticide spraying system in order to address this issue. This technique allows for the proper dosage of pesticides to be applied without the need for direct human interaction.
For farmers in rural India, chemical pesticide exposure during field spraying has emerged as a serious health concern. Farmers have been using a lot of pesticides in an attempt to get affluent, and as a result, they are ill with a lot of diseases. It has been claimed that a farmer recently passed away after breathing in the fumes while applying pesticides on his crops. However, the majority of farmers experience a variety of health issues as a result of pesticide spraying, including nausea, skin illnesses, digestive issues, and other conditions.
Farmers and cultivators manually carry out this operation, which poses a major risk to their health because to the
hazardous substances in the pesticides. It also poses a risk to crop yields if the quantity of pesticide applied exceeds or falls short of the needed quantity. The suggested approach facilitates the entire procedure without requiring human interaction, can lessen health problems in people, and aids in maximizing agricultural output.
-
LITERATURE REVIEW
An overview of the sources that include published works. The lookup was conducted using journals, the IEEE Explorer, and publications cited in the articles that were mentioned.
The purpose of this effort was to further minimize labour expenses and workload in order to improve the efficiency of the process of mixing organic fertilizer. The autonomous organic fertilizer mixer prototype underwent a number of design and adaptation adjustments to make room for the IoT surveillance system. The draft unit passed testing and demonstrated the needed functionality. The weight of the combination of agricultural waste in the storage drum has been accurately measured by the IoT tracking system and sent to the IoT platform. Workers may then utilize this information to be informed when to remove the processed organic fertilizer or add more agricultural waste material to the mixture. [1]
This study offers a thorough analysis of the benefits of plant control-based fertilizer combining over time-dependent fertilizer combining systems, as well as the development of a control-based mechanized fertilizer blending system employing a programmable logic controller (PLC). Control- based fertigation system can minimize water consumption up to 60% and minimizing 30% of fertilizer use. Conclusively, the control based automated system can be the best fertilizer- sufficient management practices that benefit crop production without causing environmental problems.[2]
Chemical pesticide security and configuration issues with low precision blending process design for an automation control system for a liquid chemical pesticide ingredient line. The system is made up of a host computer, a PLC, weighing devices, and a touch screen configuration. Visual Basic is used to construct and design software that can gather, store, and query data. As the master controller, Omron PLC receives data from the weighing instruments and uses it to precisely manage
the electromagnetic valves, mixers, and other equipment that regulates the intake of pesticide chemicals. Real-time data sharing between the host computer and PLC is accomplished through the use of the FINS protocol. System commissioning has been effectively implemented at a factory that produces liquid chemical pesticides. System benefits from minimal construction costs, a straightforward structure, safety, accuracy, and efficiency, as well as strong marketing value.[3] This article addresses the use of an 8051 microcontroller for automated pesticide mixing and spraying. Since farming employs 70% of the population in India, the majority of the country's income comes from it. To ensure that crops were grown properly and on a wide scale, farmers employed a variety of pesticides. Furthermore, 7580% of farmers said that they preferred using a manual approach to combine and spray such harmful chemicals that are harmful to human health. This study offers an approach to this spraying issue, which we attempted to do by designing and building an automated robot that would combine and spray pesticides. Its purpose is to combine the pesticide with water in the required amount and uniformly spray the mixture in three directions: forward, right, and left, according to the prescribed dose.[4]
-
BLOCK DIAGRAM
Figure. System Flow Diagram
Figure 2. Data Flow Diagram DATA FLOW DIAGRAM
A- CHEMICAL TANK 1 B- CHEMICAL TANK 2 C- CHEMICAL TANK 3 D- MAIN TANK
-
WORKING
Initially, we build a webpage with On and Off buttons for every crop that is necessary, as seen below.
The website has been set up and connected with the BOLT wireless module. The Arduino is triggered by the bolt Wi-Fi module by delivering an electric pulse to its digital pins, turning it on when the button is pressed. Sub-immersible motors are then set to operate as needed based on the button that is selected on the webpage by utilizing conditional expressions. In order to do the same tasks as the Bolt Wi-Fi module, we have also included an Arduino GSM module. Rather than using buttons, text messages for instance "crop1" and "crop2" are transmitted from a mobile device to the GSM module, which then carries out the identical tasks.
The agricultural officials will supply the appropriate pesticide mix ratio based on the results of the soil analysis and the crop illnesses. Next, we will use the code to adjust the ratio and mix in the precise chemical ratio.
Two Arduino connections are used to operate the system because there are not enough ports for the bolt Wi-Fi module and the four sub-immersion motors. The I2C protocol is used to connect two Arduinos together.
Two ines are used in the I2C protocol to send and receive data: a serial data pin (SDA) that is used to transport data between both devices and a sequential clock pin (SCL) that the Arduino Master unit pulses at frequent intervals. A single bit containing information is passed from the controller to the I2C device over SDA line when the clock line goes from low to high (also referred to as the rising edge of the clock pulse). This information will comprise the address of a specific device and
a command or data in succession. As the data is transferred bit by bit, the specified device processes the request it receives and, if necessary, sends its data back to the system over the same line, synchronizing it with the clock signal that the Master on SCL is still generating.
The address of the component that the Master needs data from is contained in the first eight bits (i.e., eight clock pulses) sent from the Master to the Slaves. The memory address on the slave that the master wishes to read from or write to, as well as any data that has to be written, are included in the bits that follow.
The website has been built using the assistance of the bubble.io program, which is compatible with both the Bolt Wi-Fi component and the Bolt cloud. All crops have corresponding buttons that, when pressed by the user, cause the bolt Wi-Fi unit to transmit an impulse to the Arduino, which causes the motors to turn on. The Arduino has a master salve connection made to it. An interface between the master Arduino and the bolt Wi-Fi modulewhich communicates with both the salve and the masterwill be established.
-
CONCLUSION
The aim of this study was to create a more efficient automated organic fertilizer blender using Arduino technological advances, which would decrease labour expenses and operating workload while also improving the effectiveness of the organic fertilizer combining operation. Because employees are not required to physically visit the site to make manual inspections, the equipment remotely supervises the state of the making of organic fertilizer and gives updates and notifications to personnel on the entire process. This lowers labour needs and expenses. To accommodate the monitoring system, several modifications and design changes were carried out on the prototype of a fertilizer mixer. Tests conducted on the prototype unit showed that it performs as required in real- world usage scenarios.
The framers may securely combine or blend their fertilizers and insecticides without coming into close touch with the chemicals by following this approach. By doing this, they are
shielded against a variety of illnesses and skin conditions. Additionally, efficiency rises when blending takes place in the ideal ratio and at the right temperature, increasing crop output efficiency. There is a significant decrease in both physical labour and effort. We can fertilize a big area of crops in a short amount of time.
REFERENCES
[1] Abdul Hadi Ishak , Sami Salama Hussen Hajjaj, Kisheen Rao Gsangaya, Mohamed Thariq Hameed Sultan, Mohd Fazly Mail, Lee Seng Hua, Autonomous fertilizer mixer through the Internet of Things (IoT). [2] Dhiya Hawina Che Aziza, Nurul Hanim Razaka, Nur Izyan Zulkaflia, Shahrizal Saatb, Mohd Zaidi Mohd Tumaric, Automated Fertilizer Blending System to Reduce Nitrogen Loss and Water Runoffs: A Best Evidence Review, DOI: 10.3303/CET2189062. [3] Ping Feng, Yushun Wang, Automatic Control System of Liquid Pesticide Ingredients Production Line, 2016 9th International Congress on Image and Signal Processing, BioMedical Engineering and Informatics (CISP-BMEI 2016). [4] Jyotsna Pansare, Tanuja Nale, Surabhi Khonde, Mrs. S.M. Shaikh, Automatic Pesticides Mixing and Spraying Robot, J. P. T. N. S. K. M.S. S. (2015). Automatic Pesticides Mixing and Spraying Robot. International Journal on Recent Technologies in Mechanical and Electrical Engineering, 2(5), 0106.
[5] A.V. Barker, Fertilizers, Encyclopedia of Analytical Science, 3rd ed., 2019. [6] S. Das, S.T. Jeong, S. Das, P.J. Kim, Composted cattle manure increases microbial activity and soil fertility more than composted swine manure in a submerged rice paddy, Front. Microbiol. 8 (2017), https://doi.org/10.3389/ fmicb.2017.01702. [7] J. Zhang, S. Bei, B. Li, P. Christie, X. Li, Organic fertilizer enhances banana biomass, increases soil organic carbon and modifies soil microbiota, Appl. Soil Ecol. 136 (2019) 6779 [8] Wang Jing, Li Ji, Zhang Yan. Regional spatial and temporal evolution of Chinese agricultural support capabilities. Jiangsu Agricultural Sciences, no. 2 , pp. 419-424, 2015.in Chinese [9] Fahlenbock, Terry D, Choosing an automated batching system: Gain- inweight or losing weight power and Bulk Engineering, 2004, 9: 31-35. [10] SYSMAC CJ Series -CJ2 CPU Unit Hardware Operation Manual, 2010. [11] Malyukow, I. Yu. Automated control system of the technological process of batching. Pribory i Sistemy Upravleniya, 2004, 4: 9-12.