
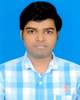
- Open Access
- Authors : Prasad Kisan Rajendra , Talwadkar Sarthak Uday , Pirjade Sahil Noormohamad , Jugal Jagtap, Mayekar Prathamesh Gajendra, Ameya Nadkarni
- Paper ID : IJERTV10IS050237
- Volume & Issue : Volume 10, Issue 05 (May 2021)
- Published (First Online): 25-05-2021
- ISSN (Online) : 2278-0181
- Publisher Name : IJERT
- License:
This work is licensed under a Creative Commons Attribution 4.0 International License
Autonomous Braking System A System That Can Be Used For All Vehicle With Little Modification
Prasad Kisan Rajendra
Mechanical Engineering
Rizvi College of Engineering
Bandra, India
Pirjade Sahil Noormohamad
Mechanical Engineering
Rizvi College of Engineering
Bandra, India
Prof. Jugal Jagtap
Mechanical Engineering
Rizvi College of Engineering
Bandra, India
Talwadkar Sarthak Uday
Mechanical Engineering
Rizvi College of Engineering
Bandra, India
Mayekar Prathamesh Gajendra
Mechanical Engineering
Rizvi College of Engineering
Bandra, India
Prof. Ameya Nadkarni Head of Department Mechanical Engineering
Rizvi College of Engineering
Bandra, India
AbstractThe major reasons for vehicle (Car, bike, truck, etc.) accidents are sudden appearance of obstacle while driving. The response time of drivers is different for everyone and varies person to person in such a panic situation and stopping distance varies some leads to accident and some prevailed the accident but of-course with serious damage. This project will help us to decrease response time by helping the driver while driving to stop in time or to minimize the stopping distance to prevent the collision.
The distance between the vehicles or moving vehicle and the obstacle can be detected by using Ultrasonic sensors. We can also install a system that can communicate between vehicles to determine the gap between vehicles i.e., approaching vehicles either from front or back. Further commands can also added to help while driving.
An Autonomous Braking system is an intelligent mechatronic system includes an Ultrasonic wave emitter provided on the front portion of a car producing and emitting Ultrasonic waves. An Ultrasonic receiver is also placed on the front portion of the car operatively receiving a reflective Ultrasonic wave signal. The reflected wave (detected pulse) gives the distance between the obstacle and the vehicle. Then a microcontroller is used to control the speed of the vehicle based on the detection pulse information to push the brake pedal and apply brake to the car stupendously for safety purpose.
The use of computer or ECU (electronic control unit) is a major step towards improving the safety and performance of vehicles as well as driver safety. In this paper we have investigated one of the aspects of braking system. The design exercise is based on calculation. This paper illustrate the problems involved and future scope for intelligent braking system.
-
INTRODUCTION
Braking system is an essential part of any automobile. It is used to stop at desire position or slow down whenever and where-ever driver wants. Sometimes while driving a suddenly a car comes in the way stop or a
person suddenly came in front of vehicle, these situations are unexpected and based on drivers expertise he/she might be able to reduce the damage to minimum.
To prevent such kind of accidents and to save drivers as well as others life Autonomous braking system will be helpful and can create major impact on safety as well as driving experience. So, we developed a System which can be developed further to improve efficiency, our System includes an ultrasonic system which gives the location of a particular thing in front of the vehicle which then can be compared with tables and act accordingly to the conditions mentioned. The system is controlled by the Microcontroller (Arduino UNO) which in turn controls the linear actuator to move the brake pedal.
Components of braking system includes: ABS Control Module
Brake Booster Disc Brakes Drum Brakes Emergency Brake Master Cylinder Brake Pedal
Wheel Speed Sensors Components of Automatic braking system:
This system includes parts from braking system plus additional components like microcontroller (Arduino module), sensors (ultrasonic sensor, lidar sensor, proximity sensor), camera module, power supply for microcontroller (batteries in case of automobile).
Arduino uno:
The Arduino Uno is used as control unit which senses the obstacle in front with the help of Ultrasonic sensor and sends a signal to Linear actuator which then applies the brake to stop or slow down the vehicle.
Ultrasonic sensor:
The HC-SR04 ultrasonic sensor is used to sense the object and gives the approximate distance of the object from the vehicle which is then compare with the help of control unit.
Linear Actuator:
A linear actuator is used because of its simplicity of use as well as space. It is connected to the brake pedal directly and it is activated as per instructions from the control unit.
-
DESIGN PROCEDURE
-
Working of Braking system
The Automatic braking system is Arduino based mechatronic system. Ultrasonic sensor and camera sensor are used as input sensors (Continuous data collector of the surrounding) for the microcontroller of the system. The working of system start as the engine starts, ultrasonic sensors and camera sensors start collecting the data as well as transmitting it to Arduino to take necessary actions. The car will be running without interruption till any obstacle comes in the way or passes near to the vehicle. When any obstacle comes the sensors will detect that and passes the information to the microcontroller and Arduino will take action to bring the vehicle to halt or slows down as per the requirement.
Flow chart of the process
Transmitter
Transmitter
Obstacle Detected
Obstacle Detected
Reflected wave
Receiver
Receiver
Braking Circuit
Braking Circuit
Car Brake
Car Brake
Figure 1: Flow-
Figure 1: Flow-
Figure 1: Flow-chart for Braking system
The break-down of the process is
-
Firstly, sensors will collect data of the surrounding and passes data to the Arduino uno.
-
Arduino will process the data and compare it with the program (Safe distance).
-
After the comparing is done, the Arduino will be taking action according to the actions decided for the different situations.
-
No action taken
-
Car will slows down done according to the distance between the vehicle and obstacle ahead.
-
Car will come to halt.
-
Fig 2: Brake Pedal Assembly
-
-
Safe Distance and Braking Distance Calculation
To calculate the safe distance, we first need to find braking distance.
Braking distance
Braking distance is a distance a vehicle will travel before coming to rest after brake is fully applied. There are many factors involve in braking like friction between the tire and the road surface, weight, wind, type of braking system, Air resistance. But the braking distance is further divided into 2 parts: (1) Total stopping distance (2) The reaction distance. Reaction distance is the distance covered before the brake is applied basically it is the reaction time taken by the driver to apply the brake.
Calculation is divided into 2 parts: Reaction distance is proportional to speed (cars running velocity). Reaction distance is product of velocity and reaction time.
.1
-
Reaction time varies according to the situation. There are 3 situations (1) expected, (2) Unexpected and (3) Surprise. Reaction time is different in different situations for expected it ranges from 0.7 to 1.0 seconds, for unexpected it ranges between 1.25 to 1.5 and for surprise it is 1.5 to 2.
Since, we are calculating for an accident or a probable cllision. Therefore, it should be surprise situation reaction time i.e., 1.5 seconds.
Reaction distance = velocity x Reaction time Reaction distance = velocity x 1.5
For 20 Km/hr = 5.56 m/s
Reaction distance = 5.56 x 1.5 = 8.34 m
Table 1: Reaction Distance
Sr.no.
Velocity (Km/hr)
Reaction distance (m)
1
20
8.34
2
40
16.67
3
60
25
4
80
33.34
5
100
41.67
Braking distance or stopping distance is a distance covered by vehicle before stopping by application of brakes. There are 2 methods to calculate stopping distance (1) Kinematics method and (2) Work-Energy method.
Kinematics method
-
The equation used to calculate the braking distance is more general equation from classical mechanics. The parent equation is given below.
….2
Figure 3: Graph for Braking distance vs Speed for dry roads
Table 3: Calculation for wet roads.
Where,Vf = Final velocity
Vi = Initial velocity a = Acceleration rate
d = Distance traversed during acceleration When calculating the braking distance, we
assume the final velocity will be zero. Based on this, the equation can be manipulated to solve for the distance traversed during braking.
3
The final formula for the braking distance is given below. Notice how the acceleration rate is calculated by multiplying the acceleration due to gravity by the sum of the coefficient of friction and grade of the road.
The value of a will be negative(deceleration)
Sr.no.
Speed (Km/hr)
Reaction distance (m)
Stopping distance (m)
Braking distance (m)
1
20
8.33
3.84
12.17
2
40
16.67
15.35
32.02
3
60
25
34.53
59.53
4
80
33.33
61.39
94.72
5
100
41.67
95.92
137.59
Sr.no.
Speed (Km/hr)
Reaction distance (m)
Stopping distance (m)
Braking distance (m)
1
20
8.33
3.84
12.17
2
40
16.67
15.35
32.02
3
60
25
34.53
59.53
4
80
33.33
61.39
94.72
5
100
41.67
95.92
137.59
Figure 4: Graph for Braking distance vs Speed for wet roads
Where, d = Braking Distance (m)
.4
Work-Energy method
The formula of braking distance calculation by work energy is
g = Acceleration due to gravity (9.81m/sec2)
G = Roadway grade as a percentage; for 6% use
0.06
Vi = Initial vehicle speed (m/sec)
= Coefficient of friction between the tires and the roadway.
-
Coefficient of friction for dry roads is 0.7 and for wet is 0.35.
Sr.no.
Speed (Km/hr)
Reaction distance (m)
Stopping distance (m)
Braking distance (m)
1
20
8.33
2.07
10.4
2
40
16.67
8.27
24.94
3
60
25
18.62
43.62
4
80
33.33
33.11
66.44
5
100
41.67
51.75
93.42
Sr.no.
Speed (Km/hr)
Reaction distance (m)
Stopping distance (m)
Braking distance (m)
1
20
8.33
2.07
10.4
2
40
16.67
8.27
24.94
3
60
25
18.62
43.62
4
80
33.33
33.11
66.44
5
100
41.67
51.75
93.42
Table 2: Calculation for dry roads.
Work done = Kinetic energy
Work done = braking force * distance = F * d Kinetic energy = ½ * m * V2
Equating both the equation we get F X d = ½ * m * V2
Taking average braking force as 2000N and weight of car as 1000Kg.
Calculation of braking distance using Work energy method is given by
…..5
Table 4: Calculation by Work Energy method
Sr.no.
Speed (Km/hr)
Reaction distance (m)
Stopping distance (m)
Braking distance (m)
1
20
8.33
7.71
16.04
2
40
16.67
30.86
47.53
3
60
25
69.44
94.44
4
80
33.33
123.45
156.78
5
100
41.67
192.9
234.57
Sr.no.
Speed (Km/hr)
Reaction distance (m)
Stopping distance (m)
Braking distance (m)
1
20
8.33
7.71
16.04
2
40
16.67
30.86
47.53
3
60
25
69.44
94.44
4
80
33.33
123.45
156.78
5
100
41.67
192.9
234.57
F – Force applied to piston
.6
P – Pressure is the master cylinder pressure which is generated after piston is pushed by brake pedal.
A – Area is the of master cylinder.
Here, in the work energy method the braking distance increases four times as speed doubles. The braking distance by this method is high as compared to kinematics method.
Safe distance
Safe distance is a distance between the vehicles or the obstacles in front of our vehicle. It is programmed in the microcontroller to avoid accident and collision. If any obstacle comes close and cross the limit of safe distance the Arduino starts alerting the driver, if driver dont take any action then the Arduino will take action and apply brake according to situation or slows down the vehicle.
Safe distance is decided as per the vehicles speed. Safe distance varies for different speeds. Safe distance for 20 Km/hris 17 – 20m as the speed is slow and other factors like friction, air resistance, weight helps to stop the vehicle within the limit. As the speed increases the vehicle gains momentum and to counter that safe distance should be more like for 60 Km/hr 80 to 90 m. Similarly, for high speed 100 Km/hr or above the safe distance should be 130 to 140 m.
This was for dry roads condition for wet roads condition like Rainy season or any fluid or liquid is spilled on the ground to counter that safe distance should be more, even for low speeds it should be more. For 20 Km/hr safe distance will be 20 25 m, for 60 km/hr safe distance is 75
-
80 m and for high speed 100 Km/hr or above should be 150m and more. Safe distance should also vary with different situation of traffic like in traffic jam where the vehicles moves but the distance between the less like just 1
-
2 m gap maybe less in some situations. We can add traffic feature in the program to avoid the false alarm situations that can damageable to both the vehicles moving close and can also affect the traffic or it can create another traffic jam.
-
-
-
Calculation of force required to Brake pedal
In automatic braking system, braking is an autonomous factor going to work independently of driver and this is done by Arduino which is taking decisions whether to brake or keep going without slowing down or slow-down to prevent collision. This can be done (1) by adding a Linear Actuator near brake pedal or wheel to brake directly (2) adding a high torque DC motor in combination with brake pedal.
We are doing it by Linear Actuator as it is more precise and easier to use in the system. Linear Actuator is controlled by Arduino to brake accurately. The force required to actuates brake must be equal to human force or greater than the human force. [5] The force required to brake is calculated as
.7
Force applied to piston = It is force generated after being pushed by pedal
Force applied on pedal = It is the force applied by human on brake pedal
where, MA is mechanical advantage of brake pedal
..8
Taking MA = 6:1 and Pressure = 127 psi. These values are average value used in various Automobiles.
Pressure = 127 psi = 875634 N/m2 Area = 5.067 X 10-4 m2
Force applied to piston = 875634 X 5.067 X 10-4 = 443.69 N
443.69 = Force applied on pedal X 6 Force applied on pedal = 73.94 N 75 N
Hence Force required to push the brake is 75 N. The Linear Actuator need to apply 75 N or more than that to successfully apply the brake.
-
Brake pedal travel distance and Linear Actuator
The brake pedal travel distance is a distance travelled by pedal when brakes applied. Sometimes it travel full distance and sometimes half according to the situation while travelling. Similarly, the linear actuator will travel different distance according to the situation.
The brake pedal travel distance is calculated as Mechanical advantage of pedal is 6:1
Height of pedal from pivot is 600mm and angle is 30° Therefore, the brake pedal travel distance at the bottom end is 692mm.
Speed of Linear Actuator is 30mm/s.
Table 5: Travel distance of Linear Actuator
Situations
Position of the Linear Actuator
At 180 mm
At 200 mm
At 300 mm
Distance travelled by Linear Actuator and Time
No braking
0
mm
0 sec
0 mm
0 sec
0 mm
0 sec
Partial braking
52
mm
1.73
sec
50mm
1.925
sec
86.8
mm
2.885
sec
Complete Braking
104
mm
3.46
sec
114 mm
3.5 sec
173.2
mm
5.77
sec
Fig 5: Positions for Linear actuator at 180 mm
Fig 6: Positions for Linear actuator at 180 mm
Fig 7: Positions for Linear actuator at 180 mm
-
Control system
Control system is the important part the automatic braking system. If the program does not run properly this can damage the driver as well as others. Every part of program is developed according to the conditions.
Components used are Arduino Uno
Ultrasonic sensors Linear Actuator
The working of control system:
The working of control system starts with ultrasonic wave transmitter. The transmitted waves travels and bounces back from obstacle surface (car, holding, humans, etc.) to the wave receiver. This received wave interpreted by ultrasonic receiver and information is passed to Arduino uno the processes the data and matches it with defined condition of the program under which category and take actions according to that like if obstacle is detected then it starts alarming the driver, if driver dont respond to the alarm then the Arduino will take action and applies brake to prevent it from crashing. The Arduino will work according to defined conditions.
The defined conditions are:
If no obstacle is detected the Arduino will not interfere with car.
-
If obstacle is detected it
will start alarming the driver, if the driver does not respond to the alarm, then Arduino will start to slow down the vehicle if the obstacle is closing.
-
If the obstacle crosses
the critical distance for the given speed, Arduino will kick in and stop the car.
-
-
-
RESULTS
The project Design and Fabrication of an Autonomous Braking System has been designed successfully and tested in simulation considering real life situations. The value used in the calculation of parameters are considered by taking average of various cars and model specifications. The autonomous braking system successfully worked for various conditions.
Table 7: For dry Road conditions Table 8: For wet Road conditions
Sr.no.
Speed (Km/hr)
Reaction distance (m)
Stopping distance (m)
Braking distance (m)
1
20
8.33
2.07
10.4
2
40
16.67
8.27
24.94
3
60
25
18.62
43.62
4
80
33.33
33.11
66.44
5
100
41.67
51.75
93.42
Sr.no.
Speed (Km/hr)
Reaction distance (m)
Stopping distance (m)
Braking distance (m)
1
20
8.33
3.84
12.17
2
40
16.67
15.35
32.02
3
60
25
34.53
59.53
4
80
33.33
61.39
94.72
5
100
41.67
95.92
137.59
Table 9: Brake Table
Condition
Brake Pedal (Angular Displacement)
Linear Actuator Travel (mm)
Time (sec)
No Braking
0
0
0
Partial Braking
14.04
50
1.92
Full Braking
29.68
114
3.5
-
CONCLUSIONS
Autonomous Braking system helps to avoid accident and it is effective in braking works as co-pilot. Having Arduino as (ECU) electronic control unit is very helpful. Survey says the cars with autonomous braking system have low accident rates compare to the cars those dont have. Ultrasonic sensor works perfectly and can be effective future also. Response time was good enough avoid the critical accident and minimizes the effect. This Braking system can be used in all type of vehicles. Autonomous braking is significant because it not only helps in reducing road casualties but it is also leads a path to achieve complete autonomous driving. One thing that can be improved in the current version is that we can increase the sensing range of the vehicle by fitting more sensors as well as add the speed sensor to make the vehicle stopping dynamic or by using some type of sensor/device (LIDAR or Camera) which can be used to better understand the vehicles environment. With the help of machine learning we make a system which can also predict the path or if any sudden
changes that can comes in way of the vehicle, the system can act on its own and find the best possible solution for that particular situation.
The same things can be utilized for accelerators as well as clutch pedals to control the vehicle autonomously in a most efficient way i.e. we can reduced the fuel consumption, engine wear etc by controlling the engine speed with the help of linear actuators.
Cost addition will be worth as it can save life. Provision can be given to disconnect the braking to driver to avoid confusion. Speed and acceleration measuring devices can be used with ECU for automatic braking at higher speeds. The
braking system can be turned off to ride safety in traffic jam and avoid any type of confusion in braking and for others safety.
REFERENCES
-
https://www.visualexpert.com/Resources/reactiontime.html
-
https://www.webpages.uidaho.edu/niatt_labmanual/Chapters/geomet ricdesign/theoryandconcepts/BrakingDistance.htm
-
http://hyperphysics.phy-astr.gsu.edu/hbase/Mechanics/frictire.html
-
https://www.bbc.co.uk/bitesize/guides/zs9mfcw/revision/2
-
https://www.youtube.com/watch?v=NOtogafBg0E&ab_channel=So uthwestTechMath%2FScienceCenter