
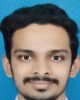
- Open Access
- Authors : S.S.Gite, G.Mahesh, D. Mahesh
- Paper ID : IJERTV13IS030227
- Volume & Issue : Volume 13, Issue 03 (March 2024)
- Published (First Online): 05-04-2024
- ISSN (Online) : 2278-0181
- Publisher Name : IJERT
- License:
This work is licensed under a Creative Commons Attribution 4.0 International License
BMS and Motor Controls for Range Extended Electric Vehicle (REEV)
S.S.Gite
Assistant Professor,
Department of Electronics and Telecommunication Engineering,
Amrutvahini College of Engineering, Maharashtra, India
G. Mahesh, D. Mahesh
U.G Students,
Department of Electronics and Telecommunication Engineering,
Amrutvahini College of Engineering, Maharashtra, India
Abstract: – Hybrid electric vehicles (HEVs) combine an internal combustion engine with an electric motor to improve fuel efficiency and reduce emissions. A Battery Management System (BMS) and Motor Controls are pivotal components in Hybrid Electric Vehicles (HEVs) that play a crucial role in optimizing performance, efficiency, and safety. It monitors individual cell voltages, temperatures, and state of charge, thermal management, and fault detection. On the other hand, Motor Controls in HEVs regulate the power distribution between the internal combustion engine and electric motor(s), maintaining a balance. These controls manage torque, speed, and regenerative braking, seamlessly transitioning between electric and gasoline power sources
Keywords- Hybrid electric vehicles, Battery Management system, Motor Controls.
INTRODUCTION
Range Extended Electric Vehicles (REEVs) have emerged as a promising solution to address the limitations of traditional electric vehicles (EVs) regarding range anxiety and infrastructure constraints. These vehicles integrate an internal combustion engine (ICE) generator, alongside an electric drivetrain and a battery pack, to extend their driving range beyond what is achievable with a pure battery-electric vehicle. Central to the operation of REEVs are Battery Management Systems (BMS) and Motor Controls, which play pivotal roles in managing the energy flow, ensuring operational efficiency, and optimizing performance.
The BMS in a REEV is responsible for monitoring the state of the battery pack, including its voltage, current, and temperature. It manages the charging and discharging processes to maintain the battery within its safe operating limits, maximizing its lifespan and ensuring its reliability. Additionally, the BMS communicates with the vehicle's motor control system to provide real-time data and optimize power delivery based on driving conditions, enhancing efficiency and performance. It also gives the information about the voltage and current flowing through it and sends back the information if there is any kind of fault in the system.
Motor controls in a REEV regulate the power flow between the battery, the electric motor, and the generator, ensuring smooth operation and maximizing energy efficiency. These systems employ sophisticated algorithms to manage torque delivery, speed control, and regenerative braking, enhancing overall vehicle dynamics and driving experience. By effectively coordinating the battery management system and
motor controls, REEVs can achieve optimal performance, extended range, and reduced environmental impact, making them a compelling choice for sustainable transportation solutions.
LITERATURE REVIEW
-
This paper deals with battery management systems (BMS) which monitor and control charging and discharging of batteries in electric vehicles to optimize performance and lifespan.
-
The paper presents the design and performance analysis of a PMDC motor for electric vehicles application through modeling, simulation and experimental validation.
-
The document discusses the development and control of hybrid electric vehicles, emphasizing the need for efficient and eco-friendly propulsion in the automotive industry, as well as the integration of various electrical systems and control strategies to achieve optimal performance.
-
The document discusses the importance of battery management systems (BMS) in electric vehicles, focusing on the need for high-power batteries and suitable BMS technologies for safe and reliable operations, as well as comparing lithium-ion (Li-ion) and Nickel-Metal Hydride (NiMH) batteries in terms of aging and the effect of temperature using state of charge (SOC) and open circuit voltage (OCV).
NEED OF PROJECT
-
Battery management systems (BMS) are important for hybrid electric vehicles (HEVs) because they monitor and control the performance of the vehicle's battery pack.
-
BMS ensures the battery's health, safety, and efficiency by managing charging and discharging processes, balancing individual cell voltages, and protecting the battery from overcharging or over-discharging.
-
Together, the battery management system (BMS) and PMDC motor control play a serious role in enhancing the efficiency, reliability, and longevity of hybrid electric vehicles (HEVs), and making them an integral part of modern HEV Technology.
PROPOSED METHODOLOGY
The proposed methodology for battery management and motor controls for range extended electric vehicles involves integrating advanced battery management systems (BMS) to monitor and optimize battery performance. This includes
implementing algorithms for real-time battery state estimation, thermal management, and cell balancing. Additionally, sophisticated motor control strategies are employed to maximize efficiency and range, such as field-oriented control (FOC) for the motor drive and regenerative braking systems. The overall approach aims to enhance the vehicle's performance, extend its range, and ensure the longevity of the battery pack.
a: frontal area= 1.1475m2 d: density of air= 1.2kg/m3
v: velocity=74kmph= 20.55m/s Q: inclined angle= 3
Torque=100060P/2n n: RPM
BLOCK DIAGRAM
Fig. 1: Block Diagram of The System
-
IC Engine: 4 stroke single cylinder engine of 10 CC.
-
Generator: The generator is used to convert mechanical energy to electrical energy for transmission and distribution over power lines to domestic, commercial, and industrial customers.
-
Controller: Here in this project two controllers are used, the motor controller and main controller to control low voltage designs.
-
PMDC Motor: The motor is used to rotate the shaft and further to the wheels
-
Lithium Ion Battery: Battery is used to power the motor because battery needs electrical power supply.
-
Sensors and output devices: The sensors are used to sense the data accordingly and give to the output devices like LCD Display.
-
EQUATIONS FOR MOTOR AND BATTERY
-
Motor Equations:
P total= (mgu) v+(0.5cadv2) v+ (mgsin Q) v where P total= Total Power
m: mass of vehicle= 340kg
g: acceleration due to gravity= 9.81m/s2 u: rolling resistance= 0.01
c: drag coefficient= 0.30
-
Battery Equations
Total force =(mgu) +(0.5cadv2) + (mgsin Q) Battery capacity = Force(N) range(km)/3600
Force = Total force-gradient force
Energy consumption= P total(kw)/vehicle speed(miles/hr) Electric range= Battery capacity/Energy consumption
ALGORITHM
algorithm of Hybrid Electric Vehicles Step 1: Initialize the system:
-
Start the HEV.
-
Set initial battery percentage.
-
et generator status to OFF. Step 2: Check Battery Percentage:
-
Continuously monitor the battery percentage. Step 3: Main Loop:
-
While the vehicle is running, continue to check the battery percentage and generator status.
Step 4: Battery Percentage Check:
-
If battery percentage is below 40%:
-
Turn on the generator.
-
Set generator status to ON.
-
Start recharging the battery. Step 5: Generator Power Generation:
-
When the generator is ON, it generates electricity.
-
Convert the generated electricity to the required voltage and current for battery charging.
Step 6: Battery Recharge:
-
Channel the generated electricity to the battery for recharging.
-
Monitor the battery charging status. Step 7: Battery Charging Complete:
-
When the battery percentage reaches a satisfactory level (e.g., 80%):
-
Turn off the generator.
-
Set generator status to OFF.
-
Stop recharging the battery. Step 8: Motor Power Check:
-
If the generator status is OFF, the motor requires power for propulsion.
-
Determine the power requirements of the motor. Step 9: Power Source Selection
-
If the generator status is ON, use the generator as the power source for the motor.
-
If the generator status is OFF, use the battery as the power source for the motor.
Step 10: Motor Propulsion:
-
Channel the selected power source to the electric motor for propulsion.
-
Adjust the power to control the vehicle speed.
IJERTV13IS030227 (This work is licensed under a Creative Commons Attribution 4.0 International License.)
Step 11: Continue Main Loop:
-
Repeat steps 2 through 10 as long as the vehicle is operational.
Step 12: Shutdown:
-
When the vehicle is turned off, stop all power generation and propulsion systems
-
-
FLOW CHART
ADVANTAGES
-
HEVs combine an IC engine with an electric motor, allowing them to operate more efficiently, especially in city driving conditions HEVs produce fewer emissions compared to conventional gasoline or diesel vehicles.
-
HEVs produce fewer emissions compared to conventional gasoline vehicles.
-
HEVs use regenerative braking to capture and store energy that is typically lost as heat during braking.
-
Electric motors are quieter than internal combustion engines, leading to reduced noise pollution in urban areas.
-
Many governments offer incentives such as tax credits or rebates to encourage the adoption of HEVs.
DISADVANTAGES
-
HEVs tend to be more expensive upfront compared to traditional gasoline or diesel vehicles due to the dual powertrain components
-
The dual powertrain system in HEVs can be more complex, requiring additional maintenance and potentially higher repair costs.
-
Unlike pure electric vehicles (EVs), HEVs don't benefit from a widespread charging infrastructure, limiting their electric-only capabilities.
-
Over time, the high-voltage battery in HEVs can degrade, reducing the overall efficiency and performance of the vehicle.
Fig. 2: Flow Chart of the system
POWER FLOW DIAGRAM
Fig. 3: Power Flow Diagram
The Transmission system ensures that power is efficiently delivered from electric motor to wheels allowing for optimal performance and energy usage. It helps balance the power output from the electric motor and the internal combustion engine to achieve the best compromise between performance and fuel efficiency.
APPLICATIONS
-
HEVs are commonly used in passenger cars and SUVs, providing a balance between fuel efficiency and practicality for daily commuting.
-
Many cities use HEVs for buses and other forms of public transportation to reduce emissions and fuel consumption.
-
HEVs are employed in delivery and logistics vehicles to reduce fuel costs and emissions during frequent stop-and- go driving.
-
HEVs are used in taxi services due to their improved fuel efficiency and lower operating costs.
-
Government agencies and municipalities use HEVs for various purposes, including police cars, maintenance vehicles, and administrative fleets.
-
Battery
SPECIFICATIONS
FUTURE SCOPE
Battery pack configuration
6S 6p
Battery nominal voltage
51.2 V
Battery capacity
90 Ah
Battery operating voltage
44.8V to 58V
Life cycle
2000
Casing type
Metal
Battery operating temperature
0ºC – 65ºC
Continuous discharge current
200A (can be change as per bms Rating)
Pulse discharge current
300A
-
Develop advanced battery technologies such as solid-state batteries to improve energy density, reduce weight, and increase the range of hybrid vehicles.
-
Establish a widespread network of wireless charging stations to make recharging more convenient and encourage the adoption of hybrid vehicles.
-
Integrate autonomous driving features into hybrid vehicles to improve efficiency and safety, making them more attractive to consumers.
-
Implement Vehicle-To-Grid (V2G) technology in hybrid vehicles, allowing them to store excess energy and feed it back into the grid during peak demand periods.
RESULT
Table 1: Battery pack technical specifications
-
-
Motor
Parameter
Description
Max RPM
3500
Peak Power
11.5 KW
Weight
20Kg
Rated Torque
22 Nm
Ambient Temperature
32°C
Dimension (LBH)
(220120220) (in mm)
Table 2: PMDC Motor technical specifications
-
Motor Controller
-
-
Motor Control Type |
PMDC |
Input Current Rating |
152 A |
Output Current Rating |
145 A |
Voltage Rating |
48 V |
Efficiency |
85% |
Cooling |
Air Cooling |
Derating |
0.86 |
Coupling Mechanism |
Belt Drive |
Table 3: Motor Controller technical specifications
Fig 4: RPM VS Torque
The above graph shows us that, as the RPM increases Torque Decreases. It shows that Torque and RPM are inversely proportional to each other. there is more reuction in the torque in the initial stage and as the RPM increases torque gradually decreases
Fig 5: Power Vs Torque
The above graph will give us the different values of torque at different power ratings. This estimates us that what is the power required at various torque.
IJERTV13IS030227
(This work is licensed under a Creative Commons Attribution 4.0 International License.)
CONCLUSION
Hybrid Electric Vehicles has shown that these vehicles offer a promising solution for reducing fuel consumption and emissions. We successfully demonstrated the effectiveness of combining electric and internal combustion engines to improve fuel efficiency and reduce environmental impact. Our findings indicate that hybrid vehicles are a viable and eco- friendly transportation option for the future. Further research and development in this field will likely lead to even more efficient and sustainable hybrid electric vehicles. This project highlights the importance of embracing hybrid technology to address environmental concerns while maintaining practicality and convenience for consumers. Ultimately, hybrid electric vehicles are a step in the right direction towards a cleaner and more sustainable transportation future.
REFERENCE
-
Hariprasad, Battery Management System in Electric Vehicles, International Journal of Engineering Research & Technology (IJERT), Vol. 9 Issue 05, May-2020.
-
Assistant Prof. Sanjeeth P, Vishwanath Chalawadi, Design and Analysis of PMDC Motor for Electric Vehicle, International Journal of Scientific Research in Engineering and Management (IJSREM), Volume: 06 Issue: 07, July 2022.
-
G.Livint, Vasile Horga, Control of Hybrid Electric Vehicles, Research
gate,2 May 2022.
-
V Karkuzhal, Analysis of battery management system issues in electric vehicles, IOP Conference Series: Materials Science and Engineering, 2020.
-
A. Ahmed, D. D. Bhutia, Propulsion System Design and Sizing of an Electric Vehicle, International Journal of Electronics and Electrical Engineering, Volume 3, No. 1, Feb. 2015.
-
Sanjay Kumar, Hybrid Electric Vehicle, International Journal of Engineering Research & Technology (IJERT), Volume 7, Issue 11, 2019.
IJERTV13IS030227
(This work is licensed under a Creative Commons Attribution 4.0 International License.)