
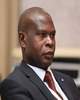
- Open Access
- Authors : Jean Ndoumbe, Emeric Tchamdjio Nkouetcha
- Paper ID : IJERTV12IS080086
- Volume & Issue : Volume 12, Issue 08 (August 2023)
- Published (First Online): 20-09-2023
- ISSN (Online) : 2278-0181
- Publisher Name : IJERT
- License:
This work is licensed under a Creative Commons Attribution 4.0 International License
Box Behnken Design Based-Optimization of 230 kV Grading Ring using Finite Element Method
Jean Ndoumbe
Laboratory of Energy, Materials, Modeling and Method University of Douala
Douala, Cameroon
Emeric Tchamdjio Nkouetcha
Laboratory of Technologies and Applied Science University Douala
Douala, Cameroon
Abstract – This paper aims to investigate the optimal design of grading rings for high-voltage polymeric composite insulators. A 230 kV composite insulator model geometry with a grading ring was modelled in COMSOL Multiphysics and was used to obtain the electric field distribution on the triple junction near of end fitting of the model by finite element method. Box Behnken Design approach was used to analyse the grading ring effect on the E-field stress. The analysis of variance is used to evaluate the interaction effects of the ring parameters. The relationship between the E-field and the ring parameters is modelled and optimized by the response surface methodology. The optimization results of grading ring lead to a significant reduction of the E-field strength at HV side and to more uniform electric field distributions. The proposed methods can help in improvement of grading ring design in reducing the electric field magnitude on the end fitting of composite insulator.
Keywords – Box Behnken Design; electric field; finite element method; grading ring; parameters optimisation.
-
INTRODUCTION
The high-voltage insulator is one of the key components of electric power transmission lines and its performance has a direct impact on the safe operation of the grid. It is designed for isolating high-voltage electric lines away from the towers while also supporting the conductors [1].
The porcelain and glass insulators have more than a century of experience in electric utilities. They have good resistance against environmental aging and they have been used in a wide range of applications. However, their pollution performance is poor due to the hydrophilic surface of the ceramic material [2].
Nowadays, polymeric composite insulators have been widely applied in power systems due to their antipollution performance, size, light weight, low maintenance requirements and operation costs, and improved mechanical performance [3, 4]. However, locally intensified electric fields remain a fundamental problem for composite insulators. This corona phenomenon occurs when the electric field (E-field) surpasses the ionization threshold of the air. It produces ozone and UV radiation and accelerates the aging of the composite insulator [5]. Prolonged occurrences of corona discharge can cause erosion on its surface, and may lead to degradation of the polymer. Therefore, it is important to study the electric field behaviour along the creepage of the insulator.
Experimental techniques can be used to determine the electric field, but they are subject to recurrent errors, which could certainly be reduced by the use of an advanced electric field detection system [6, 7]. As an alternative, several
researchers used numerical simulation techniques. Finite Element Method remains the most used numerical method for solving potential problems with multiple dielectrics and complex geometries [8].
Grading rings are usually installed to adjust the voltage distribution near the triple junction formed by the ends of insulator, the sheds and the air surfaces, thereby reducing the maximum electric field [9]. In suspension insulators grading devices, grading rings are usually required on both ends of insulators at voltages above 345 kV. In the voltage range between 230 and 345 kV, a grading device is required at the line end [10]. For voltages below 230 kV, grading rings are seldom used depending on some installation requirements. However, there is a challenge in terms of optimizing the position and the size of the ring to be used.
Previous works have evaluated the effect of the grading ring position and dimensioning on the electric field stress using FEM combined to particle swarm optimization [11-14], non- dominated sorting genetic algorithm (NSGA-II) [15], gravitational search algorithm [16] or response surface methodology [17].
The purpose of this paper is to evaluate the electric field distribution at different points of a real 230 kV polymeric composite insulator with and without a grading ring using COMSOL Multiphysics. Then, the influence of grading ring parameters on the electric field strength was be analyzed. Finally, the obtained data was analysed by Box Behnken Design.
-
MATERIALS AND METHODS
-
Modelling
For this study, a Type A FXBW4-220/120-2350 polymeric composite insulator is used. Poly. It is a 230 kV insulator with 27 large sheds and 27 small sheds. The technical characteristics of the composite insulator are presented in Tab. I. Fig. 1 shows the simplified model of composite insulator in COMSOL Multiphysics environment. It is a software platform that provides fully coupled multiphysics and single-physics modeling capabilities. It uses finite element method simulate designs, devices, and processes in various engineering fields.
For reasons of symmetry and time saving, the geometry of the insulator was done in 2D axisymmetric. The insulator is vertically suspended with is top metallic end fitting connected to
the ground, and the bottom one connected to the 230 kV/3 HV
electrode. A grading ring is placed near the HV terminal of the
insulator side of the insulator. The insulator shed is made of
silicone rubber with a relative permittivity of 4.3. The relative dielectric constant of the glass fibre core was taken equal to 7.1.
-
Grading Ring Parameters
The electric field required for initiating streamer propagation in air has been reported to be in the range 0.45-1.1 kV/mm [18, 19]. On the end fitting seal the E-field should not exceed 0.35 kV/mm [20]. In practice, the grading rings are added to reduce the distribution of the electric field near the triple junction formed by the ends of insulator, the sheds and the air surfaces.
TABLE I. TECHNICAL INFORMATION OF COMPOSITE INSULATOR
Product model
FXBW4-220 / 120-2350
Nominal voltage (kV)
220
Dry arcing distance (mm)
2162
Creepage distance (mm)
6340
Sheds diameters (mm)
140 / 95
Number of sheds (N/n)
24/24
-
(b)
Fig. 1. 230 kV Type A composite insulator (a) Schematic (b) Simplified model for simulation
or axial points. BBD is suitable for fitting a second-order model with fewer runs than other designs, such as central composite design (CCD) or full factorial design. It is more suitable for fitting a quadratic model and exploring the effects of the factors on the response. In this study, a BBD was used to establish the relationship between the response functions and grading ring parameters to determine optimized parameters that minimise the electric field norm near the triple junction.
Grading ring dimensions differ from a manufacturer to another. Considering the size of the composite insulator, and for economic reasons, [22] the configurations have been considered with the diameter of the grading ring (D) from 150 to 450 mm by steps of 150 mm, the thickness of the grading ring (d) from 10 to 50 mm by steps of 20 mm, and the vertical distance of the grading ring from the end fitting (H) from 0 to 300 mm by steps of 150 mm Each factor to be optimised was coded at three levels, -1, 0 and 1 (Tab. II).
Fig. 2. Electric field norm near the triple junction with and without grading ring
Equation (1) shows coding of the three independent factors:
0
Fig. 2 shows the electric field magnitude near the triple junction. It can be seen that the maximum electric field
=
X
magnitude is below corona initiation field magnitude in clean
and dry conditions. The maximum electric field magnitude was scientifically decrease when using grading ring.
-
-
Experimental Design
The aim of experimental design methodology is to systematically test a hypothesis or answer a research question by manipulating one or more independent variables and measuring their effect on one or more dependent variables. Experimental design methodology can provide more rigorous and valid conclusions about the causal relationships between variables, and can be applied to a wider range of problems and domains than metaheuristic algorithms [21].
There are many different approaches to experimental design and optimization. They have some advantages and disadvantages compared to each other, depending on the context and the objectives of the experiment. Almost these approaches, Box Behnken Design (BBD) is a type of response surface methodology (RSM) that aims to fit a quadratic model to the relationship between the factors and the response. It uses three levels for each factor and avoids extreme points, such as corners
where xi and Xi are the dimensionless and the actual value of the independent factor i, X0 the actual value of the independent variable i at the central point, and Xi the step change of Xi corresponding to a unit variation of the dimensionless value. Responses (E-field) at each design point were computed and recorded. Data from the BBD were subjected to regression analysis using quadratic model to obtain the parameters of the mathematical models. The statistical significance of the regression coefficients derived from the model were checked using Students t-test. Analysis of variance (ANOVA) was applied to evaluate the statistical significance of the model. Response surface plots were obtained using the fitted model. Tab. III shows the computed results using COMSOL Multiphysics Simulation, using coded parameters.
-
-
RESULTS AND DISCUSSIONS
The results from Box Behnken Design were evaluated using Design Expert® 13.0.5 Software.
Std
Run
Factor
E-field Norm (kV/cm)
D
d
H
13
7
-1
1
-1
1.46
11
8
0
-1
1
2.82
14
9
0
0
0
1.05
10
10
0
1
-1
1.62
2
11
1
-1
0
1.56
8
12
1
0
1
1.07
15
13
1
-1
1
1.82
3
14
-1
1
0
1.48
9
15
0
-1
-1
4.45
-
Statistical Analysis
The BBD performed was designed to assess the influence of three factors, that is, the diameter of the ring, the thickness of the ring and the vertical distance from the end fitting.
Fig. 3 illustrate the results of Students t-test. The p-value less than 0.05), showing a remarkable relationship between the parameters and the E-field values at the 95.0% confidence level. Such significance implies the processing variables have significant effects on the E-field. The results of ANOVA for each parameter quadratic model are presented in Tab. IV. The Model F-value of 20.39 implies the model is significant. There is only a 0.20% chance that an F-value so large could occur due to noise. The F-values obtained show the accuracy and unwavering quality of the tests performed. Therefore, the built model can be validated. The Predicted R² of 0.7439 is in reasonable agreement with the Adjusted R² of 0.9257; i.e. the difference is less than 0.2.
The final equation in terms of coded factors is given by:
E(kV)=+1.07-0.8746A-1.09B-0.2134C+0.4860AB- 0.4860AC+0.3335BC+0.4219A²+0.5044B²+0.9694C²
Fig. 3. Student s t-test result
TABLE II. EXPERIMENTAL VALUES AND CODED LEVELS FOR FACTORIAL DESIGN
Independent factors
Code units
Coded variable level
-1
0
1
diameter of the grading ring (D)
X1
150
150
450
thickness of the grading ring (d)
X2
10
30
50
vertical distance of the grading ring from the end (H)
X3
0
150
300
Std
Run
Factor
E-field Norm (kV/cm)
D
d
H
4
1
1
1
0
0.53
1
2
-1
-1
0
4.42
5
3
-1
0
-1
2.9
7
4
-1
0
1
3.8
6
5
1
0
-1
2.08
12
6
0
1
1
1.29
TABLE III. ELECTRICAL FIELD NORM FOR INDIVIDUAL DESIGN POINTS
TABLE IV. ANOVA FOR QUADRAYIC MODEL
Source
Sum of squares
df
Mean Square
F-
Value
p- value
Model
21.01
9
2.33
20.39
0.0020
significant
A-D
7.14
1
7.14
62.36
0.0005
B-d
11.02
1
11.02
96.25
0.0002
C-H
0.4250
1
0.4250
3.71
0.1120
AB
1.11
1
1.11
9.69
0.0265
AC
1.11
1
1.11
9.69
0.0265
BC
0.5223
1
0.5223
4.56
0.0858
A²
0.4688
1
0.4688
4.09
0.0989
B²
0.6700
1
06700
5.85
0.0602
C²
2.48
1
2.48
21.62
0.0056
Residual
0.5724
5
0.1145
Cor Total
21.58
14
-
Optimisation Results
Fig. 4 illustrates the response surface plots of the grading ring parameters on the E-field distribution. They are graphical representations of the relationship between E-field values and two of grading ring parameters. It allows to explore the effects of that parameters on the E-field response at the triple junction, and to optimize (minimize) the E-field value by finding the optimal values of the grading ring parameters.
Fig. 4a shows the maximum E-field from end fitting position and ring thinness while the diameter of ring tube is kept at the middle level. It is noticed that increasing the ring thickness (d) decreases strongly the E-field to reach a minimum value before increasing again close to high value of d. On the other hand, increasing ring position (H) decreases the E-field then increases it after having reached the second half of the possible values of the position.
Fig. 4b illustrates the maximum E-field from end fitting position and ring diameter while the thickness of ring tube is kept at the middle level. The increase of the ring diameter (D) decreases strongly the E-field to reach a minimum value before increasing again near to high value of the ring diameter. When
the ring position (H) increase, this decreases the E-field it decreases until reaching the average values then increases it.
Fig. 4c presents the maximum E-field from both ring diameter and thinness while the position from end is kept at the middle level. When both ring diameter and thinness increase, this decreases the E-field it decreases before increasing again close to high values.
Fig. 5 shows the BBD optimization results of the maximum E-field value using coded parameters for dry and clean conditions. The values of the diameter and the thickness of the ring are very high, without being the maximum values. The ring position values are a bit higher than the average value. It can be noted that the E-field values obtained are smaller than the computed field values.
Tab. V presents the BBD optimization results of the maximum E-field value from true parameters. The optimum dimensions are 697 mm for grading ring diameter, 240 mm for vertical distance from end fitting and 59 mm for ring thinness.
The results of the calculations, shown in Fig. 6, indicate that the reduction in the maximum E-field at the triple junction when using the optimized grading ring is quite significant.
-
Discussions
Because of there are no specific standards for the design and placement of grading rings, the design parameters such as grading ring diameter, vertical positions and diameter of the ring in practice are based upon experiences of manufacturers and specific circumstances [12]. However, for 230 kV composite insulator, the magnitude of the electric field can be enough to lead to the presence of corona activity near the end fitting, based on operational and calculation experiences [20, 23, 24].
The results of the E-field calculations on the surface of the insulator with and without grading ring, shows that without grading ring the electric field near the triple junction is about
4.64 kV/cm. With the use of a grading ring, this value reaches
-
kV/cm. This is a reduction of approximately 92.24%. The optimized ring parameters are 697 mm for diameter, 240 mm for vertical distance from end fitting and 59 mm thinness.
TABLE V. OPTIMUM PARAMETERS
D
d
H
E (kV/cm)
Coded parameters
0.785
0.633
0.199
0.356
Real parameters (mm)
696.25
58.99
239.8
Fig. 4. Optimisation results with coded parameters
.
Fig. 5. E-field distribution for the optimized grading ring
-
(b) (c)
-
Fig. 6. Response surface plot showing the effect on E-field of a) d H, b) D H and c) D d covariance
Shu, et al. [25] recommended parameters of grading ring used for 230 kV composite insulators in icing areas are: 300 mm for the ring diameter, 40 mm for the thinness ring and the height varying from 35 mm to 65 mm. The findings by Aziz, et al. [1] revealed that the absence of a grading ring significantly increased the E-field, reaching a value of 14.61 kV/cm. against
1.63 kV/cm, when using grading ring. This represents about approximatively 88.9% of reduction. Furthermore, they find the optimized dimensions for grading ring design, 280 mm for ring diameter, 40 mm for thinness, while the vertical distance position from end is 90 mm.
Others similar approach combining a finite element method and a design of experiments approach was performed to optimize the E-field near the HV end fitting electrode and avoid
the corona phenomena. Terrab and Kara [17] minimized the maximum E-field value and obtained a reduction of 71.5% compared to the E-field in the case without grading ring, using L27 Taguchi method and RSM. They found the grading ring diameter of 300 mm, projection from end fitting of 227 mm and ring tube thickness of 90 mm as optimum dimensions for 230 kV composite insulator. The results strongly depend of the maximal thinness ring used for simulation. Also, the vertical positions are closed.
Several studies have combined the finite element method and metaheuristic algorithms to minimize the electric field at the triple junction. Barros, et al. [26] performed an optimization using the Nelder-Mead method in order to determine the optimal design of a grading ring for 230 kV composite insulator. The
results showed that the electric field on the insulator was reduced about 80% when using the optimized ring. This E-field magnitude is reduced, particularly at the HV end by nearly 82% when applying the PSO Approach [11]. This Using Bat algorithm implies a significant reduction of 71.5% in the maximum E-field value compared to the case without a grading ring [27].
Different dimensions obtained for the grading ring design, can be considered as optimized values. The variability of the reduction rates of the E-field is extremely related to the assumptions of finite elements simulation, in particular to the calculations of the electric field at the triple point, or even the modeling of the HV electrodes, which could lead to a variability of the results.
-
-
CONCLUSION
As there are no standards for grading rings design, FEM and BBD were performed to find optimal parameters for grading ring, to avoid corona phenomena close to the end fitting of 230 kV composite insulator. The variables of the optimization method were diameter of grading ring, ring diameter and ring vertical position along the insulator, from end fitting.
It is concluded that the optimization of grading ring leads to a significant reduction of the E-field strength at HV side and to more uniform E-field distributions. The vertical distance position of the grading ring has a significant influence on the electric field. Increasing of thinness of grading ring has a good impact on E-field reduction rate and its limitations is based on economic considerations. The ring diameter has also an impact on the field. However, this impact is not significant as the ring vertical position one.
REFERENCES
[1] E. Aziz, F. Aouabed, H. Abdellah, and A. Dineva, "Case Study: Optimizing Grading Ring Design for High Voltage Polymeric Insulators in Power Transmission Systems for Enhanced Electric Field and Voltage Distribution by Using a Finite Element Method," Energies, vol. 16, no. 13, p. 5235, 2023. [2] A. Al-Gheilani, W. Rowe, Y. Li, and K. L. Wong, "Stress control methods on a high voltage insulator: A review," Energy Procedia, vol. 110, pp. 95- 100, 2017. [3] H. Shrimathi, M. Mondal, and P. Mishra, "Electric stress reduction in polymeric insulators exposed to multi-environmental conditions using a field-grading zinc-oxide Microvaristor," Electric Power Systems Research, vol. 220, p. 109342, 2023. [4] X. Zhao et al., "Grading of electric field distribution of AC polymeric outdoor insulators using field grading material," IEEE Transactions on Dielectrics and Electrical Insulation, vol. 26, no. 4, pp. 1253-1260, 2019. [5] Q. Chen, Y. Li, G. Yang, T. Jin, Z. Zhang, and S. Zhang, "Detection and analysis of ultraviolet corona discharge for earth switch grading ring," in 2019 IEEE International Conference on Computational Electromagnetics (ICCEM), 2019, pp. 1-3: IEEE. [6] R. Zeng, Y. Zhang, W. Chen, and B. Zhang, "Measurement of electric field distribution along composite insulators by integrated optical electric field sensor," IEEE Transactions on Dielectrics and Electrical Insulation, vol. 15, no. 1, pp. 302-310, 2008. [7] D. Huang, J. Ruan, W. Cai, T. Li, Y. Wei, and J. Liu, "Flashover prevention on high-altitude HVAC transmission line insulator strings," IEEE Transactions on Dielectrics and Electrical Insulation, vol. 16, no. 1, pp. 88-98, 2009. [8] S. M. Kumar and L. Kalaivani, "Electric field distribution analysis of 110 kV composite insulator using finite element modeling," in 2014International Conference on Circuits, Power and Computing Technologies [ICCPCT-2014], 2014, pp. 136-141: IEEE.
[9] D. C. DomÃnguez, F. P. Espino-Cortes, and P. Gomez, "Optimized design of electric field grading systems in 115 kV non-ceramic insulators," IEEE Transactions on Dielectrics and Electrical Insulation, vol. 20, no. 1, pp. 63-70, 2013. [10] "IEEE Guide for Application of Composite Insulators," in IEEE Std 987- 2001 (Revision of IEEE Std 987-1985), pp. 1-24. [11] B. M'hamdi, M. Teguar, and A. Mekhaldi, "Optimal design of corona ring on HV composite insulator using PSO approach with dynamic population size," IEEE Transactions on Dielectrics and Electrical Insulation, vol. 23, no. 2, pp. 1048-1057, 2016. [12] M. K. Hussain and B. M. Alshadeedi, "Optimal design of high voltage composite insulators with grading rings in different configurations," Electric Power Systems Research, vol. 221, p. 109493, 2023. [13] J. A. Diaz-Acevedo, A. Escobar, and L. F. Grisales-Norena, "Optimization of corona ring for 230 kV polymeric insulator based on finite element method and PSO algorithm," Electric Power Systems Research, vol. 201, p. 107521, 2021. [14] S. Zhang, "Optimization of Corona Ring Design Used in UHV Composite Insulator by PSO Algorithm," in Journal of Physics: Conference Series, 2021, vol. 2087, no. 1, p. 012032: IOP Publishing. [15] B. MHamdi, Y. Benmahamed, M. Teguar, I. B. Taha, and S. S. Ghoneim, "Multi-objective optimization of 400 kV composite insulator corona ring design," IEEE Access, vol. 10, pp. 27579-27590, 2022. [16] K. Aramugam, H. A. Illias, and Y. C. Ching, "Optimisation of corona ring design for composite insulator strings," COMPEL-The international journal for computation mathematics in electrical electronic engineering, vol. 38, no. 1, pp. 232-246, 2018. [17] H. Terrab and A. Kara, "Parameters design optimization of 230 kV corona ring based on electric field analysis and response surface methodology," Electric Power Systems Research, vol. 163, pp. 782-788, 2018. [18] T. Doshi, R. Gorur, and J. Hunt, "Electric field computation of composite line insulators up to 1200 kV AC," IEEE Transactions on Dielectrics and Electrical Insulation, vol. 18, no. 3, pp. 861-867, 2011. [19] P. Blackmore and D. Birtwhistle, "Surface discharges on polymeric insulator shed surfaces," in IEEE Transactions on Dielectrics and Electrical Insulation, vol. 4, no. 2, pp. 210-217, April 1997, doi: 10.1109/94.595248. [20] A. Phillips, A. Maxwell, C. Engelbrecht, and I. Gutman, "Electric-field limits for the design of grading rings for composite line insulators," IEEE Transactions on Power Delivery, vol. 30, no. 3, pp. 1110-1118, 2014. [21] P. Cash, T. Stankovi, and M. torga, "Design research-approaches, perspectives, applications," ed: Springer International Publishing, 2016. [22] N. Alti, A. Bayadi, and K. Belhouchet, "Grading ring parameters optimization for 220 kV metaloxide arrester using 3DFEM method and bat algorithm," IET Science, Measurement and Technology, vol. 15, no. 1, pp. 14-24, 2021. [23] E. Akbari, M. Mirzaie, A. Rahimnejad, and M. B. Asadpoor, "Finite element analysis of disc insulator type and corona ring effect on electric field distribution over 230-kV insulator strings," International Journal of Engineering and Technology, vol. 1, no. 4, pp. 407-419, 2012. [24] K. Aramugam, H. A. Illias, Y. C. Ching, M. S. Ali, and M. Z. H. Makmud, "Optimal Design of Corona Ring for 132 kV Insulator at High Voltage Transmission Lines Based on Optimisation Techniques," Energies, vol. 16, no. 2, p. 778, 2023. [25] L. Shu, S. Wang, X. Jiang, Q. Hu, Y. He, and Z. Wu, "Influences of grading ring arrangement on AC flashover performance of 220 KV ice- covered composite insulators," IEEE Transactions on Dielectrics and Electrical Insulation, vol. 21, no. 6, pp. 2652-2661, 2014. [26] R. Barros, E. Da Costa, T. Ferreira, J. Araujo, and F. Andrade, "A new approach for optimal design of corona ring," in 2016 IEEE International Power Modulator and High Voltage Conference (IPMHVC), 2016, pp. 684-687: IEEE. [27] K. Belhouchet, l. ouchen, a. bayadi, and A. Nadjim, "A Novel Application of Artificial intelligence technology for Outdoor High-Voltage Composite Insulators," J. Supercomput, 2023.