
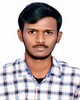
- Open Access
- Authors : Mohammed Ubed
- Paper ID : IJERTV10IS020221
- Volume & Issue : Volume 10, Issue 02 (February 2021)
- Published (First Online): 05-01-2019
- ISSN (Online) : 2278-0181
- Publisher Name : IJERT
- License:
This work is licensed under a Creative Commons Attribution 4.0 International License
CFD Analysis of Fins with Different Notches
Mohammed Ubed,
U.G. Mechanical Engineering, Vasavi College of Engineering, Hyderabad, Telangana, India.
Abstract The Engine is one of the important component in an automobile which is subjected to high temperature and thermal stresses. In order to cool the engine the fins are another component which are used to dissipate the heat from the Engine. Fins are generally used to increase the heat transfer rate from the system to the surroundings. By doing computational flow analysis on the engine cooling fins, it is helpful to know about the heat dissipation rate and the Principle implemented in this project is to increase the heat transfer rate, so in this analysis, the fins are modified by putting different types of notches and are of same material. The knowledge of efficiency and effectiveness of the fins are necessary for proper designing of fins. The main objective of our analysis is to determine the flow of heat at various notches available and the analysis is done by using ANSYS CFD Fluent software.
Keywords p-perimeter of Fin, A-surface area of Fin, Q-heat transfer rate, K-thermal conductivity, h-Heat transfer coefficient, Ta-Ambient temperature, Tb-base temperature, J-joules, m-meter, mm-millimeter, k-kelvin, L-length of Fin, W-width of Fin, W-watts, CFD-computational Fluid Dynamics, Pa-Pascal, Kg-Kilogram.
-
INTRODUCTION
Heat transfer is a thermal energy which occurs in transits due to temperature difference. Cooling system is one of the important system among all of the systems in automobile. Fins are responsible to carry out the produced heat inside the cylinder , for the heat transfer there are various modes like conduction , convection and radiation are taken place. From these modes conduction is carried out in engine cooling fins. There are two different types of cooling system that are used in the automobiles, they are:
-
Liquid cooling
-
Air Cooling
-
Liquid Cooling: Liquid cooling is also employed in maritime vehicles. For vessels, the seawater itself is mostly used for cooling. In some cases, chemical coolants are also employed (in closed systems) or they are mixed with seawater cooling. By doing the Computational Fluid analysis the heat transfer rate of the fins with various types of notches are analyses by using ANSYS.
-
Air-Cooling : Mostly automobile bikes using direct air cooling (without an intermediate liquid) were built over a long period beginning with the advent of mass produced passenger cars and ending with a small and generally unrecognized technical change. Air cooling is a method of dissipating heat. It works by expanding the surface area or increasing the flow of air over the object to be cooled, or both. An example of the former is to add cooling fins to the surface of the object, either by making them integral or by attaching them tightly to the objects surface (to ensure efficient heat transfer).
-
-
LITERATURE REVIEW
Deepak Gupta, Wankhade S.R.[Ref 1] Design and Analysis of Cooling Fins in this paper the author tells about Cooling fins are used to increase the heat transfer rate of specified surface. Engine life and effectiveness can be improved with effective cooling. The main aim of the project is to study and comparing witp00 cc Hero Honda Motorcycle fins and analyze the thermal properties by varying geometry, material and thickness. The analysis is done using ANSYS.
Vivek Kumar, Dr. V. N. Bartaria[Ref 4], CFD Analysis of an Elliptical Pin Fin Heat Sink using Ansys Fluent v12.1 in the present study carries out numerical physical insight into the flow and heat transfer characteristics. The governing equations are solved by adopting a control volume-based finite difference method with a power-law scheme on an orthogonal non-uniform staggered grid.
Sanjay Kumar Sharma and Vikas Sharma[Ref 2], Maximizing The Heat Transfer through Fins using CFD as a Tool in this author describes This study presents the results of computational numerical analysis of air flow and heat transfer in a light weight automobile engine, considering three different morphology pin fins. The results indicate that the drop shaped pin fins show improved results on the basis of heat transfer and pressure drop by comparing other fins.
G. Babu, M. Lavakumar[Ref 5], Heat Transfer Analysis and Optimization of Engine Cylinder Fins of Varying Geometry and Material in this paper the main aim of the project is to analyze the thermal properties by varying geometry, material and thickness of cylinder fins. Parametric models of cylinder with fins have been developed to predict the transient thermal behavior. The models are created by varying the geometry, rectangular, circular and curved shaped fins and also by varying thickness of the fins.
-
OBJECTIVE
To do design and CFD analysis of fins with different notches.
-
Fins with holes.
-
Fins with rectangular notches.
-
Fins with v shaped notches.
-
Fins without any notches.
To know better heat transfer rate in different fins.
-
-
METHODOLOGY
We followed the methodology given in the flow chart below , first collect all the related information about the heat transfer and the cooling fins and then collecting some of the literature review.
PROBLEM IDENTFICATION
PROBLEM IDENTFICATION
SELECTION OF NOTCHES
SELECTION OF NOTCHES
3D MODEL IN CATIA V5
3D MODEL IN CATIA V5
ANALAYZE THE MODEL IN CFD
ANALAYZE THE MODEL IN CFD
COMPARING RESULTS
COMPARING RESULTS
Fig4.1 Methodology
After collecting all the related datas the cooling fins are designed using CATIA V5. After the model is created the analysis are done by using ANSYS 14.5 (CFD Fluent). Then the results of each analysis are compared and then the best notch is selected. The result from the ANSYS is compared with the theoretical calculation.
-
GEOMETRIC MODELLING
The Cooling fins are designed using CATIA in this design the 100 CC automobile Engine is selected for designing of cooling fins. The three different types of notches which are selected for analysis are,
-
Fins with Holes.
-
Fins with Rectangular Notches,
-
Fins with V Shaped Notches.
-
Fins without any Notches.
Fig5.1 Fins with Holes
Fig5.2 Fins with Rectangular Notches
Fig5.3 Fins with V Shaped Notches
Fig5.4 Fins without any Notches .
-
MATERIAL DATA FOR ALUMINIUM
For the analysis of cooling fins we choose the material as Aluminum because Aluminum is a good thermal and electrical conductor, having 59% the conductivity of copper, both thermal and electrical, while having only 30% of copper's density. The weight of the Aluminum is less and also because of a high thermal conductivity.
Material Property
Value
Density
2719 Kg/m3
Thermal conductivity
202.399 W/m-K
Specific Heat
871 J/Kg-K
Youngs modulus
3.4e+11 Pa
Poissons ratio
0.22
Bulk Modulus
2.0238e+11 Pa
Shear Modulus
1.3934e+11 Pa
Tab5.1.1 Material info
-
CFD ANALYSIS AND MESH GENERATION Computational Fluid Dynamics (CFD) is the science ofdetermining numerical solution of governing equation for the fluid flow through space or time to obtain a numerical description of the complete flow field of interest. The equation can represent steady or unsteady, Compressible or Incompressible, and in viscid or viscous flows, including non- ideal and reacting fluid behavior. The particular form chosen depends on intended application. The state of the art is characterized by the complexity of the geometry, the flow physics, and the computing time required obtaining a solution. After the model is imported in CFD domain, next step is to mesh the domain. To perform better results using CFD Tool it was mandatory to use better quality of mesh hence the meshing of the model is generated and the naming of the section is given in the model for computing purpose.
Fig5.2.1 mesh Fins with Holes
Fig5.2.2 mesh Fins with V-Shaped Notches
Fig5.2.3 mesh Fins with Rectangular Notches
Fig5.2.4 mesh Fins without any Notches
Fins type
Cells
Faces
Nodes
Normal fin
3770
13383
5940
Fin with Holes
10440
25286
7395
Fin with V-shaped Notch
5408
15638
6930
Fin with Rectangular Notch
5061
9364
6465
Tab5.2.1 Cells info
-
NAMED SECTION AND BOUNDARY CONDITIONS
In this CFD analysis the naming of section is a major thing in fluent the bottom surface of the fins is named as Inlet and the top extruded surface is named as outlet then the left side end of the fin is named as a Boundary-1 and the right side end of the fins are named as a Boundary-2. The above figure will represent the named section given in CFD, after the mesh generated the boundary conditions are defined for CFD domain and the mesh file is save as in the name of .msh format and the mesh file is imported in fluent for analysis.
-
-
RESULTS
A three-dimensional model is developed to investigate flow and heat transfer rate in the automobile fins. A series of numerical calculations have been conducted by FLUENT and the results are presented in order to show the effects of temperature distribution, overall heat transfer coefficient, heat transfer rate.
-
TEMPERATURE CONTOUR
Due to the change in shapes of the fins the temperature distribution is varied in the above figures and it can be determined by using CFD fluent. The following graph will represent the changes in the temperature of the fins under same operating condition.
After the analysis are done the results are seen in CFD post processing , by choosing the domain the results are seen by means of vectors and contour diagrams the following images shows the temperature contour of various notches and the results are given below.
Fig6.1.1 Temperature Contour Rectangular Notches
Fig6.1.2 Temperature Contour without any Notches
Fig6.1.3 Temperature Contour V-shaped Notches
Fig6.1.4 Temperature Contour Fin with holes
-
HEAT FLUX CONTOUR
Heat flux is the rate of heat energy transfer through a given surface per unit time. Since the surface area of the fins are increased in different notch so the heat transfer rate is also increased, the following images shows the heat flux contour of various notches and the results are given below.
Fig6.2.1 Flux contour Rectangular Notches
Fig6.2.2 Flux contour Fins without any Notches
Fig6.2.3 Flux contour V-Shaped Notches
Fig6.2.4 Flux contour with Holes
Parameter
Temperature(oC)
Heat Flux(W/m2)
Normal Fin
287.43
8.73e+04
Fin with Holes
292.79
1.0752e+05
Fin with V- shaped Notch
295.69
7.78e+04
Fin with Rectangular Notch
296.3
7.64e+04
Tab6.2.1 Fluent-Temperature, Heat Flux Values
-
THEORETICAL CALCULATIONS
Let us consider a normal cross section fins of Length , L and Perimeter , P and heat transfer rate , Q and thermal conductivity K
Gas Temperature, Ta = 298 K (25 oC) (Ambient Temperature) Base Temperature, Tb = 573 K (300 oC)
Thermal Conductivity of the Fins, K = 202.399 W/m-k Heat transfer Co-efficient, h = 140 W/m2-k FORMULAE:
Surface area of the a Rectangle = 2 ( LxW + LxH + WxH
)
Perimeter of the Fin = 2 ( L+W ) m = ( hp / kA )0.5
Heat Transferred Q = [( hpkA )]0.5 *( Tb-Ta ) * tanh(m L) Surface area of fin = 2[13*120]+2[16*120]+3[4*120]
=8400 mm2
Perimeter of Fin = 2[2[16*120]] + 2[4+120]
= 792 mm
m = (140*0.792/202.399*0.0084)0.5
= 8.0757 m-1
Heat transfer rate
Q = (hpkA)0.5*(Tb-Ta)*tanh(mL)
=(140*0.792*202.399*0.0084)0.5*(573- 298)*tanh(8.0757*0.016)
= 485.172 Watts
The Theoretical calculation for the normal fins are calculated and the heat transfer rate is found by using formulas. By using same method the surface area and perimeter are modified and the heat transfer rate is calculated for all types of notches. The below table will clearly shows the heat transfer rate theoretically.
Shape of Fins
Heat Transfer (Watts)
Normal Fins
485.172
Fins with Holes
510.345
Fin with V-shaped Notch
495.314
Fin with Rectangular Notch
532.73
Tab6.3.1 Theoretical – Heat Transfer values
-
-
RESULTS
From the above table, we can easily understand the heat transfer rate of fins with different types of notches.
The fins with various configurations were modeled using CATIA V5 and analysis are done by using CFD Fluent in order to find out the heat transfer rate. It is clear that the results from software and theoretically says that the fins with rectangular notch have greater heat transfer rate compared to that of the fins without holes, fins with holes and V shaped fins. Since the heat dissipation rate is more in rectangular notch so we conclude that the rectangular notch fins are most efficiency and best heat transfer notch among all types of notch.
REFERENCES
-
Deepak Gupta, Wankhade S.R.[1], Design and Analysis of Cooling Fins in International Journal on Mechanical Engineering and Robotics of ISSN : 2321-5747, Volume-3, Issue-2,2015 .
-
Sanjay Kumar Sharma and Vikas Sharma[2] , Maximizing The Heat Transfer Through Fins using CFD as a Tool in International Journal of Recent advances in Mechanical Engineering of Volume-2, No.3, August 2013 .
-
S.Jamala Reddy, Y.Tejeswar , Design and Thermal Analysis of Cooling Fins by Varying its Geometry and Material in International journal of Advanced Technology and Innovative Research of ISSN 23482370 Volume-07,Issue-05, June-2015, Pages:0628-0630.
-
Sandhya Mirapalli, Kishore.P.S , Heat Transfer Analysis on a Triangular Fin in International Journal of Engineering Trends and Technology Volume-19 Number-5 Jan 2015 .
-
G. Babu, M. Lavakumar , Heat Transfer Analysis and Optimization of Engine Cylinder Fins of Varying Geometry and Material in IOSR Journal of Mechanical and Civil Engineering (IOSR-JMCE) , Volume- 7, Issue-4 (Jul. – Aug. 2013), PP 24-29 .
-
A. Rossetti, S. Minetto, S. Marinetti , A simplified thermal cfd approach to fins and tube heat exchanger: application to maldistributed airflow on an open display cabinet in International Journal of Refrigeration .
is there any powerpoint available for this topic …. if its is available can you send to me with given email below
hi sir i want a ppt regards this topic can you make