
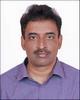
- Open Access
- Authors : Vijay Kumar Turaga
- Paper ID : IJERTV11IS070148
- Volume & Issue : Volume 11, Issue 07 (July 2022)
- Published (First Online): 26-07-2022
- ISSN (Online) : 2278-0181
- Publisher Name : IJERT
- License:
This work is licensed under a Creative Commons Attribution 4.0 International License
CFD Based Prediction of Temperature Distribution Inside Enclosure with Gas Chromatographs
Vijay Kumar Turaga
Associate General Manager, HCL Technologies Ltd., Bangalore 562106, INDIA
Abstract Gas chromatographs are used to measure concentrations of natural gas. Normally, one or more gas analyzers are placed inside a housing or enclosure, made up of an insulating material. These analyzers operate continuously in field for several months and typically operate in harsh environmental conditions. These are subject to extreme changes in temperature, humidity etc. Temperature is maintained inside enclosure by means of one or more heaters placed at suitable locations inside enclosure, which operate based on thermostats. A thermostat switches the heater off and on when the temperature exceeds or reaches below the set temperatures at specified probe point. In this study, transient CFD simulations were performed using ANSYS ICEPAK tool to predict the temperature distribution and variation with respect to time inside an enclosure, housing one gas analyzer and one heater, to assess the uniformity of temperatures during extreme temperature conditions. The CFD simulation method has been validated based on temperature measurement results from a chamber test done with varying ambient temperature. Simulations have been carried out with extreme winter and extreme summer environment conditions. Temperatures have been assessed at selected probe points within the enclosure.
Keywords CFD, Thermal analysis, Gas chromatograph, Enclosure, Natural convection
-
INTRODUCTION
Gas chromatographs play a key role in determining the components in a gas mixture and their respective proportions [1]. Natural gas analyzers operate at onsite continuously and measure gas composition and quality in real time. These analyzers often operate under harsh environment conditions. The ambient air can cause significant error in analysis of gas, primarily due to variations in temperature, pressure and humidity and also influenced by dust and pollution in the atmosphere [2]. Hence the chromatographs are placed inside an thermally insulated housing or enclosure which protects the equipment from external environmental factors. The design of enclosure is crucial in maintaining uniform temperature inside while operating in extreme hot and cold environments and in protecting the equipment from dust and humidity variations.
The enclosure wall is made of a thermally insulating material along with thin sheets of aluminum on the inner and outer sides. The enclosure is completely closed in this design and hence, protect the chromatographs from extreme ambient temperatures.
Depending on size of the enclosure, one or more chromatographs are placed inside which analyze the natural
gas. One or more electric heaters of required power are placed inside the enclosure at appropriate locations. These heaters help in maintaining a required temperature inside the enclosure under extreme cold and hot ambient temperature conditions. The heaters are equipped with thermostats which switches off the heater when temperature at a probe point goes above a set temperature and switches on when temperature reduces to below the set temperature. Requirement of the enclosure and heater arrangement is to maintain a nearly uniform temperature at all locations inside the enclosure.
A schematic representation of enclosure considered in these simulations with one single chromatograph and a heater is shown in figure 1. This enclosure is completely closed and does not have any ventilation. Hence, there is no interaction between air inside the enclosure and ambient air outside the enclosure.
Fig. 1. Schematic sketch of Enclosure
The objective of CFD simulations is predict the temperature distribution inside the enclosure for a given heater power and ambient temperature variation. Process of gas chromatography is not in the scope of these simulations. Gas chromatograph is included just as a flow obstruction inside the enclosure and have no participation in the heat transfer mechanism inside the enclosure. Hence the scope of simulation includes recirculation of air due to natural convection inside the enclosure and natural convection on the outside wall due to ambient temperature variation.
Simulations were performed with a constant ambient temperature -40oF representing winter day condition and a varying temperature with respect to time representing a summer day condition on a typical hot day. Solar radiation is included in summer day simulation.
-
LITERATURE REVIEW
A few research articles related to CFD or Thermal simulations in electronic enclosures have been published. These articles are more into temperature assessments of PCB components typically enclosed in unventilated enclosure systems. A few such articles have been discussed here.
Tang & Joshi [3] described a methodology to predict temperatures and heat transfer coefficients over PCBs. They initially developed a global enclosure model with a coarser mesh including electronic boards of different sizes to predict overall temperatures and heat transfer coefficients, which were interpolated in a detailed, fine mesh model. Kowalski & Radmehr [4] performed thermal analysis of a complex electronic cabinet used as a high-speed internet subscriber device using flow network model and CFD. Dehbi, A., et al [5] discussed primarily on impact of radiation in the natural convection problem, which is often ignored in many problems.
-
METHODOLOGY
ANSYS ICEPAK has been chosen for performing this simulation since the tool is capable of handling problems involving thermal simulations. Chromatograph and other flow obstructions have been modeled as ICEPAK objects, which are approximated as cuboid shapes and do not participate in heat transfer process. Also, ICEPAK has an option of modeling thermostat directly which is an added advantage for this specific problem, where heaters operate based on thermostat.
Casing of the enclosure was modeled with appropriate material properties of the thermally insulating material along with wall thickness values on inner and outer side with Aluminum properties.
Chromatograph, heater and a few other major objects inside the enclosure occupying significant space were included in the simulation. Other minor components such as wires, cables, strips etc. were ignored. As mentioned before, the objects occupying space were converted to ICEPAK objects.
Air was modeled as fluid inside the enclosure. Also, sufficient volume of air was added on the outside of enclosure to represent ambient air and to capture natural convection. A schematic view of CFD domain is shown in figure 2.
Boussinesq approximation was used to capture density variation of air. Gravity has been activated to enable buoyancy forces.
Heater geometry was modeled along with fins, and is set to generate the needed power in Watts. Heat source was provided on the core. Fins would spread out the heat. Automatic switch on & off temperatures have been set at 49oC (120.2oF) and 51oC (123.8oF) based on temperature control probe point located above heater.
Radiation plays a significant role in case of natural convection. DO Radiation model has been activated to capture the radiation heat transfer.
A timestep size of 1 minute has been used to perform transient simulations. This timestep size is needed to capture the heater on and off phenomenon. Typical duration of
transient simulation is 18 hours for winter day simulation and 24 hours for summer day simulation. Validation case has been run for 40hours to match the test cycle.
Fig. 2. Representative CFD domain (not drawn to scale)
Thermocouple location points in the test setup were created as point probes in CFD model. These points are represented as top front center and top right back. Enclosure temperature control probe is the probe temperature by means of which thermostat operates.
-
RESULTS
-
Validation with Test Data
First simulation was performed to represent the chamber test, where the atmospheric temperature has been set to be equal to chamber temperature, which is varied to study the temperatures at designated thermocouple locations.
The chamber test has been performed by decreasing the ambient (chamber) temperature from a temperature above 125oF to a temperature below 8oF linearly over 24 hours period and increasing back to the maximum value over a period of 24 hours. This covers a 48-hour temperature variation.
The temperatures are measured at thermocouple locations, top front center and top right back. Initial temperature of air inside enclosure is assumed to be 122oF (50oC).
Probe points have been created in CFD model at thermocouple locations in the actual test. Temperature values at probes predicted by CFD model are compared with temperatures measured in chamber test. This comparison is shown in figure 3, by means of a plot showing % error at respective probe points varying with time. It can be seen that deviation is mostly within 10% at all the thermocouple locations, which is acceptable. Error values are found to be following a wavy pattern due to heater on and off during the test, with mean values lying mostly within 5%.
Fig. 3. Deviation with respect to test data
-
Winter Day Simulation
A simulation was performed to represent a typical coldest day in winter with an ambient temperature of -40oF. In this case, a fixed ambient temperature is applied as a condition outside of enclosure and transient simulation was run for a duration of 18 hours. This result is shown in figure
4. As in previous case, initial temperature of air inside enclosure is assumed to be 122oF (50oC).
Fig. 4. Winter day simulation result
Results of winter day simulation are shown in figure 4. It is seen that temperatures at probe points dropped from 122oF to close to 90oF in a period of 18 hours. The temperature stabilized at around 90oF.
-
Summer Day Simulation
Similar to winter day simulation, a simulation has been performed on a typical summer day. The ambient temperature is assumed to be varying in this case. A temperature profile based on actual temperature variation with respect to time at a typical hot location and on hottest day in season has been chosen as input condition. Temperature profile from 12 AM to 12 AM (24-hour cycle) has been provided as input. As in previous cases, initial temperature of air inside enclosure is assumed to be 122oF (50oC).
Since this simulation is representing a summer day, solar radiation plays a key role in the temperature variation. This is activated in ICEPAK with a specified North direction. Also, a specific latitude and longitude has been provided as input, corresponding to the location on the globe at which temperature variation has been chosen.
Results of summer day simulation are shown in figure 5. Ambient temperature variation as well as solar irradiation flux considered are also included in the chart. As indicated, solar radiation peaks at around 12 noon. It is seen that temperatures at probe points are maintained at around 122oF over a period of 24 hours. The heater is switched off
between 15 to 20 hours, as seen from the temperature plots during this period, as the temperature did not reduce to a value below the lower limit. This period occurs after the ambient temperature attains maximum value in the day.
Fig. 5. Summer day simulation result
-
-
CONCLUSION
An attempt has been made to capture the temperature variations inside an enclosure with gas chromatographs in response to the ambient temperature conditions, ranging from extreme winter (-40oF) to extreme summer (110oF). As a future scope, suitable design improvements can be worked upon if necessary, based on the findings from the simulations.
This exercise also helped in building a CFD based methodology using ICEPAK tool, especially in capturing the operation of heater based on thermostat.
REFERENCES
[1] Guo, Xinghua, ed. Advances in gas chromatography. BoDBooks on Demand, 2014. [2] Jahnke, J. A. Operators guide to eliminating bias in CEM systems. No. PB-98-150253/XAB. Source Technology Associates, Research Triangle Park, NC (United States); Cadmus Group, Inc., Raleigh, NC (United States); Environmental Protection Agency, Acid Rain Div., Washington, DC (United States), 1994. [3] Tang, L., and Joshi, Y. K. (June 1, 1999). "Integrated Thermal Analysis of Natural Convection Air Cooled Electronic Enclosure." ASME. J. Electron. Packag. June 1999; 121(2): 108115. [4] T. Kowalski and A. Radmehr, "Thermal analysis of an electronics enclosure: coupling flow network modeling (FNM) and computational fluid dynamics (CFD)," Sixteenth Annual IEEE Semiconductor Thermal Measurement and Management Symposium (Cat. No.00CH37068), 2000, pp. 60-67, doi: 10.1109/STHERM.2000.837062. [5] Dehbi, A., et al. "The influence of thermal radiation on the free convection inside enclosures." Nuclear engineering and design 341 (2019): 176-185. [6] Icepak, A. N. S. Y. S. "ANSYS Icepak Users Guide." ANSYS Inc (2013).