
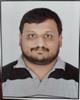
- Open Access
- [post-views]
- Authors : Kaushik V.Prasad, Dhanush K, Raravi Vinay Vardhan, Sagar Kattimani, Talari Pavan Harshavardhan
- Paper ID : IJERTV12IS050352
- Volume & Issue : Volume 12, Issue 05 (May 2023)
- Published (First Online): 13-06-2023
- ISSN (Online) : 2278-0181
- Publisher Name : IJERT
- License:
This work is licensed under a Creative Commons Attribution 4.0 International License
Characterization Of Hardness and Microstructure Of TiAlN and TiCN/Al2O3 Coatings Deposited Via LARC Deposition
Kaushik.V.Prasad
Dept. Of Mechanical Engineering School Of Engineering & Technology Jain (Deemed-to Be-University)
Kanakapura, Ramanagara, Karnataka, India.
Dhanush K, Raravi Vinay Vardhan,
Sagar Kattimani, Talari Pavan Harshavardhan Dept. Of Mechanical Engineering
School Of Engineering & Technology Jain (Deemed-to Be-University)
Kanakapura, Ramanagara, Karnataka, India.
Abstract – In the present work, we investigate the hardness and microstructure of TiAlN and TiCN/Al2O3 coatings deposited using the lateral rotating cathodes (LARC) technology. The deposited coatings are characterized for microvicker's hardness testing, x-ray diffraction analysis, and scanning electron microscopy (SEM) imaging. Our results reveal that the TiCN/Al2O3 TiAlN coatings exhibit the highest hardness of 25 GPa. The x-ray diffraction pattern of the TiCN/Al2O3 coatings exhibits a strong crystalline phases of hexahedral structure which contributes to higher hardness. The microstructure of TiAlN coatings reveal several porous sites.
Keywords Microstructure; TiAlN; TiCN/Al2O3 Coatings; Lateral Rotating Cathodes (LARC) Technology; Physical Vapor Deposition (PVD)
I. INTRODUCTION
High productivity and precision in finished products are the needs of todays metal working industries. This demand emphasizes the need of cutting tools with high wear resistance and service life. There are several classes of cutting tools available in todays market. However, the WC-Co (cemented carbide) and Coated WC-Co are extensively used in high-speed machining and in machining of hard to cut materials. The refractory ceramic oxides are known for their excellent wear and thermal resistance properties. Alumina Oxide (Al2O3) is the most commonly used refractory oxide coatings in many applications which demand wear resistance. When Al is combined with other materials such as Ti, Zr, Cr etc. its properties are further improved [1-4]. TiAlN coatings are known for their superior hardness (>25GPa) and wear resistance upto high temperatures of 1000oC. Several
studies have been carried out to understand the behaviour of TiAlN system of coatings. A comparative study made on nano AlTiN and multilayered TiAlN/TiSiN+CrN in dry machining of AISI 3430 steel showed that nano crytalline coatings exhibited higher hardness. The high hardness of nano crystalline coatings can be attributed to its high hardness (>30GPa). Similarly, Liew et al. have demonstrated that nano crystalline TiAlN coated tool produces a good surface finish with minimum lubricants. Multilayered coatings also possess superior properties and can be effectively used in high-speed machining applications. In the present work we investigate the microstructure and hardness of TiAlN and TiCN/Al2O3 coatings [5-8].
II. MATERIALS AND METHODS
In this study, the hardness and microstructure of TiAlN and TiCN/Al2O3 coatings are deposited using the lateral rotating cathodes (LARC) technology. The coating process was carried out in an industrial coating unit called PLATIT 80.
Commercially available cemented carbide substrates with TNMG 160404 specifications were chosen for coating. Prior to coating, the inserts are cleaned with deionized water and dried in an oven at 100°C. The coating chamber comprises two lateral rotating cathodes and a carousel where the inserts are mounted. The chamber is maintained at a working pressure of 1 1.5 Pa with a flow of Nitrogen and Argon gases. The substrate is biased with a voltage of
-70 to -75V, while the cathodes (targets) are biased with a voltage of -20V. The current between the cathodes ranges from 80 to 100 amperes.
A magnetic system is employed to guide the arc plasma backward, allowing large particles to deposit on the walls
and clean the impurities on the target. Without interrupting the arc, the magnetic system then redirects the plasma toward the substrate. The choice of target
-
Hardness
-
Results and Discussions
materials depends on the desired coating type. For TiAlN coating, one block of Ti and one block of Al are used. For TiCN-Al2O3 coating, one block of TiCN and another block of Al2O3 were used.The schematic of the coating chamber is as shown in figure 1.
During deposition, both the carousel and inserts continuously rotate about their vertical axis at a speed of 10 rpm. The entire process is programmed to deposit 3µm of coatings in one cycle time. The current between the cathodes is continuously controlled to maintain the desired ratio of elements in the coatings.
Figure 1. Schematic of the LARC process
To assess the hardness of the deposited coatings, Matsuzawa MMT-X7 microhardness tester is utilized. The tester employs a diamond pyramid indenter and the indentation left behind is measured and displayed on an LCD interface. The machine has a load range of 1gf 1000gf. A load of 500gf is applied to all samples with a dwell time of 15 seconds.
Scanning Electron Microscopy (SEM) was used to capture images of the coating surface. Phenom desktop scanning electron microscope was utilized for this purpose. Additionally, X-ray diffraction (XRD) studies were conducted to study the elemental phases present in the TiAlN and TiCN/Al2O3 coatings. Bruker's D8 advanced X-ray diffractometer was utilized for XRD studies.
The hardness results for the TiAlN and TiCN/Al2O3 coatings are presented in Table 1. It is observed that the hardness of the TiCN/Al2O3 coating was higher compared to the TiAlN coating. High hardness of the coating can be attributed to its bilayered structure. This also indicates the presence of a strong interface between TiCN and Al2O3 layer. Moreover, the interfacial bond between the amorphous and crystalline phases enhances the strength of the coating and restricts the movement of dislocations, leading to improved oxidation and wear resistance. The obtained hardness values in this study are comparable to hardness found in other related works. However, it should be noted that the hardness values did not reach the super hardness state.
Types of Coating
Colour
Microvickers Hardness (in GPa)
TiAlN
Grey
15
TiCN/Al2O3
Black
25
Table1. Hardness values of as deposited coatings
-
-
Scanning Electron Microscopy and X ray diffraction
The SEM images presented below depict the microstructure of the TiAlN and TiCN-Al2O3 coatings. The TiAlN coating exhibits a slightly porous morphology with some unmelted particles. These porous sites can lead to reduction in the hardness of the coatings. There were no cracks, or any other large voids present on the surface of the coating.
Similarly, the TiCN-Al2O3 coating also displays a relatively smooth surface morphology. The coating does not have any porous sites or micro cracks. Further no unmelted particles were observed.
Figure 2. SEM image of TiAlN coating.
Figure 3. SEM image of TiCN/Al2O3 coating.
-
X Ray Diffraction Studies
The XRD analysis revealed information regarding the crystal structures of the TiAlN and TiCN/Al2O3 coatings. The TiAlN coating showed the presence of Ti4AlN3 phase in low intensity. A strong peak for tungsten aluminum carbide is observed. The crystallinity of the coating is reduced when compared with TiCN/Al2O3coating. In the case of TiN/Al2O3 coating the presence of Al2O3 in rhombohedral structure has contributed to its high hardness.
Figure 5. XRD pattern of TiCN/Al2O3 coating
Figure 4. XRD pattern of TiAlN coating
-
Conclusions
All the coatings, including TiAlN and TiCN-Al2O3, underwent characterization of surface morphology and mechanical properties. It was observed that the TiAlN coating demonstrated higher hardness compared to the TiCN/Al2O3 coating. High hardness can be attributed to the presence of strong crystalline structures of TiCN and Al2O3. Further studies on wear resistance are to be investigated in future.
REFERENCES
[1] J.H. Hsieh, C. Liang, C.H. Yu, W. Wu,. Deposition and characterization of TiAlN and multi-layered TiN/TiAlN coatings using unbalanced magnetron sputtering, Journal of Surface and Coatings Technology Elsevier, 108109 (1998) 132137 [2] M.S. Karthik et al. ,Cutting parameters optimization for surface roughness during dry hard turning of EN 31 bearing steel using CBN insert, Journal of Materials Today: Proceedings, Elsevier. [3] Harsh Y. Valera and Sanket N. Bhavsar, Experimental Investigation of Surface Roughness and Power Consumption in Turning Operation of EN 31 Alloy Steel, Journal of Procedia Technology 14 ( 2014 ) 528 534 [4] J. Rajaparthiban et al, Machining of EN31 Steel Using Carbide Insert A Statistical Approach, Journal of Materials Today: Proceedings 22 (2020) 25592564 [5] A. Knutsson, M.P. Johansson, , L. Karlsson, M. Odén, Machining performance and decomposition of TiAlN/TiN multilayer coated metal cutting inserts, Journal of Surface & Coatings Technology 205 (2011) 40054010. [6] Stan Veprek, Veprek Heijman M.J.G , Industrial Applications of Superhard Nano composite Coatings, Journal of Surface and Coatings Technology, Elsevier, 2008, 5063 – 5073. [7] Dobrazanski LA, Wonsinka L, Mikula J, Golombek K, Gawarecki T, Investigation of hard gradient [TiAlSi]N coating, Journal of achievements in materials and manufacturing engineering, Volume 24, isuue 2 , october 2007, 59 62. [8] Kenneth J Brookes, PLATIT Pioneers in Physical Vapour Deposition, Paper on technical trends, Elsevier, 2013, 24 27. [9] 8. Krzysztof Lukaszkowicz, Review of Nanocomposite thin films andcoatings deposited by PVD and CVD technology, nanomaterials, Prof. Mohammed Rahman (Ed.), ISBN: 978 953 307 913 4 , 2011.