
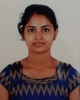
- Open Access
- Authors : B. Prayuktha , P. Partha Sai Reddy , Dr. D. Govardhan
- Paper ID : IJERTV10IS050474
- Volume & Issue : Volume 10, Issue 05 (May 2021)
- Published (First Online): 04-06-2021
- ISSN (Online) : 2278-0181
- Publisher Name : IJERT
- License:
This work is licensed under a Creative Commons Attribution 4.0 International License
Comparative Computational Analysis Of Carbon Epoxy Composite and Aluminum Alloy
B. Prayuktha1, P. Partha Sai Reddy2,Dr. D. Govardhan3
dept. Aeronautical Engineering Institute of Aeronautical Engineering, Hyderabad, India
Abstract High Performance, minimized structural weight for aerospace applications frequently exploit the us age of Carbon Epoxy composite materials and Aluminum alloy 2024 material. The main objective of this paper is to compare the computational investigation of carbon-epoxy Laminate unidirectional composite material and Aluminum alloy 2024 carrying out various mechanical tests and characterization involved parameters like Compression test, and Flexural test on the basis of high temperature at 1600c. The Specimen models are developed based on materials and geometric constrains to attain less weight, minimum deformation, minimum stress and better efficiency. FUSION 360 is proposed for the Plan, design and modeling for the test. Importing model and material selection in Static structural domain in ANSYS workbench is used to carry out the analysis for study of viability between the materials considered. The aftereffects of the tests are accounted for both the materials and analyzed between the two materials for closing the best material plausibility.
Keywords Aluminum, Carbon epoxy composite, Comparison, Computational analysis, Static Structural
-
INTRODUCTION (Heading 1)
The segments utilized for the aerospace applications are in extraordinary interest nowadays. The expanded interest is because of improved execution and decreased expense of these components. The advancement of basic parts with the best proficient materials in briefest conceivable time. This requires comprehension of new advancements and fast retention in the improvement of new items and materials required to produce parts. The carbon epoxy composite material and aluminum assumes a crucial part in the uses of aviation.The Carbon Epoxy Composite material which is a compound made up of carbon and epoxy resins that have very different physical or chemical properties, producing the material with different properties. This material which is unilayered, when applies in the field of the aerospace reduces the weight in between 20%-50%. The Mechanical properties of the composite can be custom-made by lay-up plan, with tightening thickness of sup porting fabric and material
direction, which has the high impact resistance, and high harm resilience.
The Aluminium Alloy 2024 which is light weight and strong that makes high resistance to corrosion which is easily welded and manipulated. The aluminum alloy provides maximum strength at elevated temperatures and are highly resistant to fracture and fatigue due to its strength, low density, high specific modulus and cryogenic toughness properties.
-
METHODOLOGY
-
Material Properties
Product standards define the limits for composition, quality and performance and these limits are used or presumed by structural designers.
The epoxy carbon UD prepeg which is a light weight composite made up of Epoxy Resin and Carbon fiber in the Unidirectional pattern with the rigidity of around 5000Mpa and a strain-to-disappointment of 2%. The composite has Longitudinal tensile modulus of 155-165Gpa and the Longitudinal tensile strength of 2500-3000Mpa, the elastic modulus of 230GPa.Therefore, for a given load a component or the unit made of this composite will experience a great elastic deformation with a density of 1490 kg/m3. The Elongation at break 1.2%-1.3%.
The Aluminium Alloy 2024 is another material typically having the density of 2770kg/m3. Poisson ratio of
0.33 and Tensile yield strength of 2.8E+08 pa. It is well suited for aerospace applications. Aluminium alloy has compressive yield strength of 2.8E+08 pa and Tensile Ultimate strength of 3.1E +08 pa.
-
Analytical Solution
-
Compression test: The compression test is to choose or discover the lead or response of a material while it experiences a compressive weight by assessing chief elements, for instance, strain, stress, and deformation. By testing a material in force, the compressive strength, yield strength, outrageous strength, adaptable limit, and the flexible modulus among various limits may all be settled.
F=P/A (1)
Where,
F= Compressive Strength P= Maximum Load applied A=Area
-
Flexural Test: Flexural Strength, in any case called modulus of burst or break, twist strength, or break strength, is a material property, described as the pressing factor in a material not well before it yields in a flexure test. The get over contorting test is most intermittently used, in which a model having either a round or rectangular cross-portion is bowed until break or yielding using a three-point flexural test method.
= 3 F L / 2 ( 2 )
Where, F= Load
L= Distance between the Support
-
DESIGN AND ANALYSIS
Model is designed in the FUSION 360 and imported to ANSYS Workbench 2021 R1 Software. Selecting static structural domain in ANSYS Workbench software, materials which are epoxy carbon composite UD prepeg and aluminum alloy 2024 are opted for the model. Choosing modular analysis that prompts mechanical tests space in ANSYS and making meshing size as fine. The Material model for computational examination with fluctuating measurements for Compression trial of Length 130mm, Width 12.5mm, Thickness 3.5mm and for Flexural trial of Length 120mm, Width 15mm, Thickness 3.5mm.
-
Compression Test: The modal of dimensions Length 130mm, Width 12.5mm, Thickness 3. 5mm.Selection of Material for performing the test. Placing the model in Y axis and Fixed support is given at lower end of the Model Laminate. The load force of 40KN is applied at the free end to perform the Compression test over the considered model and selecting the environment temperature of 1600C. Solution is derived for Deformation along X, Y, Z axis, total deformation, von Moises stress (equivalent stress) and Elastic strain. The values thus obtained are stated below.
-
Flexural Test: The modal of dimensions Length 120mm, Width 15mm, Thickness 3. 5mm.Selection of Material for performing the test. Placing the model in Z axis and simply supported condition is applied to the Model Laminate. The load force of 2000N is uniformly distributed to perform the Flexural test over the considered model and selecting the environment temperature of 1600C. Solution is derived for Deformation along X, Y, Z axis, total deformation, von Moises stress (equivalent stress) and Elastic strain. The values thus obtained are stated below.
Figure 1- Model designed in FUSION 360
Figure 2-Fine Meshing of the Model
IV. RESULTS
TABLE I. EPOXY CARBON UD PREPEG(230GPA)
S.No |
Compression Test |
||
Parameter |
Minimum |
Maximum |
|
1. |
Von-Moises Stress [MPa] |
767.1 |
942.87 |
2. |
Total Deformation [mm] |
0 |
13.81 |
3. |
Equivalent Strain |
0.11922 |
0.13627 |
4. |
Deformation along X- axis [mm] |
-1.5844e-002 |
1.5844e-002 |
5. |
Deformation along Y- axis [mm] |
-13.81 |
0 |
6. |
Deformation along Z- axis [mm] |
-9.2196e-002 |
9.2196e.002 |
TABLE II. ALUMINIUM ALLOY 2024
S.No |
Compression Test |
||
Parameter |
Minimum |
Maximum |
|
1. |
Von-Moises Stress [MPa] |
601.2 |
979.29 |
2. |
Total Deformation [mm] |
0 |
1.6699 |
3. |
Equivalent Strain |
9.3027e-003 |
1.3909e-002 |
4. |
Deformation along X- axis [mm] |
-2.7091e-002 |
2.7091e-002 |
5. |
Deformation along Y- axis [mm] |
-1.6699 |
0 |
6. |
Deformation along Z- axis [mm] |
-1.0668e-002 |
1.0668e-002 |
TABLE III. EPOXY CARBON UD PREPEG(230GPA)
S.No |
Flexural Test |
||
Parameter |
Minimum |
Maximum |
|
1. |
Von-Moises Stress [MPa] |
0.55643 |
981.3 |
2. |
Total Deformation [mm] |
0 |
97.952 |
3. |
Equivalent Strain |
3.2505e-003 |
0.14036 |
4. |
Deformation along X- axis [mm] |
-0.016379 |
0.016415 |
5. |
Deformation along Y- axis [mm] |
-97.845 |
0 |
6. |
Deformation along Z- axis [mm] |
-9.1297 |
0 |
TABLE IV. ALUMINIUM ALLOY 2024
S.No |
Flexural Test |
||
Parameter |
Minimum |
Maximum |
|
1. |
Von-Moises Stress [MPa] |
0.66943 |
981.83 |
2. |
Total Deformation [mm] |
0 |
11.894 |
3. |
Equivalent Strain |
5.4327e-004 |
1.3829e-002 |
4. |
Deformation along X- axis [mm] |
-0.033837 |
0.033841 |
5. |
Deformation along Y- axis [mm] |
-11.881 |
0 |
6. |
Deformation along Z- axis [mm] |
-1.1052 |
0 |
-
Compression Test:
Epoxy Carbon UD Prepeg (230GPA): Deformation along X axis:
Figure 3- Deformation along X axis
Deformation along Y axis:
Figure 4- Deformation along Y axis
Deformation along Z axis:
Figure 5- Deformation along Z axis
Equivalent Elastic Strain:
Figure 6- Equivalent Elastic Strain
Total Deformation:
Figure 7-Total Deformation
Von Moises Equivalent Stress:
Figure 8-Von Moises Equivalent Stress
Aluminium Alloy 2024: Deformation along X axis:
Figure 9- Deformation along X axis
Deformation along Y axis: Von Moises Equivalent Stress
Figure 10- Deformation of Y axis
Figure 14-Von Moises Equivalent Stress
Deformation along Z axis:
Figure 11- Deformation along Z axis
Equivalent Elastic Strain
Figure 12-Equivalent Elastic strain
-
Flexural Test
Epoxy Carbon UD Prepeg (230Gpa) Deformation along X axis:
Figure 15- Deformation along X axis
Deformation along Y axis:
Figure 16-Deformation along Y axis
Total Deformation
Figure 13-Total Deformation
Deformation along Z axis:
Figure 17-Deformation along Z axis
Equivalent Elastic Strain:
Figure 18- Equivalent Elastic Strain
Deformation along Z axis:
Figure 23-Deformation along Z axis
Total Deformation:
Figure 19-Total Deformation
Equivalent Elastic Strain:
Figure 24-Equivalent Elastic Strain
Von Moises Equivalent Stress:
Figure 20-Von Moises Equivalent Stress
Aluminium Alloy 2024 Deformation along X axis:
Figure 21-Deformation along X axis
Deformation along Y axis:
Figure 22-Deformation along Y axis
Total Deformation
Figure 25-Total Deformation
Von Moises Equivalent Stress
Figure 26-Von Moises Equivalent Stress
V. CONCLUSION
From the results obtained from the analysis of the Laminate model considered of both Epoxy carbon UD prepeg (230Gpa) and Aluminium 2024 alloy, the Von Moises Equivalent Stress of Aluminium 2024 is observed to be more resistant when compared to the Epoxy carbon UD prepeg (230Gpa) in both the tests of compression and flexural. The Equivalent Strain values observed in the both the tests for different materials, results the best performance of Aluminium 2024 when compared to the Epoxy carbon UD prepeg (230Gpa) with Less deformation.
Thus, the Aluminium 2024 has more strength and shown in terms of Stress and strain observed and concluded as Aluminium 2024 is more efficient and reliable for the manufacture of components in aerospace applications.
REFERENCES
-
Gao, Feng, et al. Mode II Delamination and Damage Resistance of Carbon/Epoxy Composite Laminates Interleaved with Thermoplastic Particles. Journal of Composite Materials, vol. 41, no.1, Jan. 2007, pp. 111123, doi:10.1177/0021998306063356.
-
Alaattin Aktas, M.Husnu Dirikolu, The effect of stacking sequence of carbon epoxy composite laminates on pinned-joint strength, Composite Structures, Volume 62, Issue 1, 2003, Pages 107-111, ISSN 0263-8223, https://doi.org/10.1016/S0263-8223(03)00096-5.
-
H.A Whitworth, M Othieno, O Barton, Failure analysis of composite pin loaded joints, Composite Structures, Volume 59, Issue 2, 2003, Pages 261-266, ISSN 0263-8223, https://doi.org/10.1016/S0263-8223(02)00056-9.
-
Amos Gilat, Robert K Goldberg, Gary D Roberts, Experimental study of strain-rate-dependent behavior of carbon/epoxy composite, Composites Science and Technology, Volume 62, Issues 1011, 2002, Pages 1469-1476, ISSN 0266-3538, https://doi.org/10.1016/S0266-3538(02)00100-8.
-
Norihiko Taniguchi, iTsuyoshi Nishiwaki & Hiroyuki Kawada (2007) Tensile strength of unidi- rectional CFRP laminate under high strain rate, Advanced Composite Materials, 16:2, 167-180, DOI: 10.1163/156855107780918937.
-
Yi Wan, Jun Takahashi, Tensile and compressive properties of chopped carbon fiber tapes reinforced thermoplastics with different fiber lengths and molding pressures, Composites Part A: Applied Science and Manufacturing, Volume 87, 2016, Pages 271-281, ISSN 1359-835X, https://doi.org/10.1016/j.compositesa.2016.05.005