
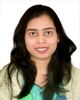
- Open Access
- Authors : Amrita Patil , Gayatri Palnitkar
- Paper ID : IJERTV9IS040527
- Volume & Issue : Volume 09, Issue 04 (April 2020)
- Published (First Online): 27-04-2020
- ISSN (Online) : 2278-0181
- Publisher Name : IJERT
- License:
This work is licensed under a Creative Commons Attribution 4.0 International License
Comparative Study and Implementation of Speed Control of BLDC Motor using Traditional PI and Fuzzy-PI Controller
Amrita Patil
Dept.of Electrical Engineering
P.E.S. Modern College of Engineering Pune, India
Asst. Prof. Gayatri Palnitkar
Dept.of Electrical Engineering
-
Modern College of Engineering Pune, India
AbstractBrushless direct current motors (BLDC) motors are widely used and commercially available for various industrial applications, which desires fast and effective control of speed. The conventional controllers like Proportional- integral (PI) controller perform better in pre-defined or user- defined speed band for which they are tuned. However, for obtaining better performance for applications involving wide ranges of speeds, they have to be re-tuned at every speed change. Hence, it is inconvenient or in many cases it is not possible to re- tune PI controller parameters at every setup to obtain optimal response from a BLDC motor drive for entire speed range. Fuzzy-logic based PI controller can effectively tune these PI parameters for every step change in command speed and improve the speed response of electric drive. This paper discusses implementation scheme for speed control of BLDC motor using PI and Fuzzy logic-based PI controller using cost- effective ATMEGA328P-PU controller. Both simulation and hardware results presented in this paper verify the effectiveness in the performance of the control scheme.
KeywordsBLDC motor, Proportional-integral (PI), fuzzy logic-based PI-controller, ATMEGA328P-PU micro-controller, MATLAB / Simulink®
-
INTRODUCTION
BLDC motors are one of the most commonly available and widely used motors across industrial, household and in some domestic segments [1]. The applications in various machining tools and robotics which may require robust and dynamic response and may have less tolerance for error in case of speed regulation against load variations, can be found out with this type of drive. PI-based controller feedback system works satisfactory for most of the cases with user-defined or predefined and constant speed drives but, it requires continuous tuning of its control parameters where wide speed range with similar fast response throughout is demanded [2, 3]. The automatic control system is one such technology that is gaining importance for specific applications. The unpredictable variation in dynamic model for non-linear system is difficult to derive [4]. The main reason for system instability is miscalculations while tuning the PI-based controller gain values [5]. For a single order system, the PI- based controller works efficiently, but is not effective when it comes to higher order and non-linear systems. So, for such kind of high performing motors, these characteristics of vulnerability is not desirable. Thus, knowledge of system to tune the controller parameters is desired to obtain the optimal performance from the system in wide operating ranges.
In case of fuzzy logic controller concepts, due to reasoning and selection of sector methodology of input and output data variables, the non-linear systems and the involvement of complex control processes is discarded [6]. As fuzzy logic- based controller mostly operates on the varying values between 0 and 1 for its membership functions, it is able to
control process [7 – 10]. Various scientists and researchers have made simulations and proved that the fuzzy-logic based controller implemented on BLDC motor give good possible outcomes in terms of speed [11 – 14]. The popular method between Mamdani and Sugeno methods is Mamdani method whose approach is tilted towards speed control of drives [15 – 18]. The experimental results in case of conventional Arduino module is published and validated by the researchers in [19 – 21]. Also, a high cost and complex algorithm in electric car wipers and wind-shield is documented in [22 – 25]. However, the cost-effective product which comprises the fuzzy logic- based control algorithm applied to BLDC motor drive for domestic, commercial and industrial applications is yet to be applied on it or else yet to be published. Also, the practical implementation of this control algorithm is vaguely documented in the literature.
So, in this paper, conventional PI and fuzzy logic-based PI control algorithm in MATLAB / Simulink® is proposed. The conventional PI and fuzzy-based PI controller strategy is simulated and validated. Later on, the experiment-based setup which consists of BLDC motor of 60W used in electric vehicle and cost effective ATMEGA328P-PU microcontroller is presented and validated using results. The responses of speed as per the applied load is validated with the comparative analysis at the end.
-
CLOSED LOOP CONTROL SCHEME OF BLDC MOTOR DRIVE
Fig. 1. Block diagram of speed control of BLDC motor drive using PI controller
The Basic PI controller based block sets of the BLDC motor drive is shown in the Fig. 1. It is the most commonly or widely used conventional type controllers used in commercial purposes. As the input is set to reference speed, the PI based controller gets its input in the form of set speed and the actual speed which brings up the differential error in the system to manipulate in the PI based controller block. This controller block sets certain gain values and directs towards the pulse width modulator of the system. he speed calculator of this control system brings up the negation of actual speed, which will eventually minimize the error. The parameters of PI controller are the output variables,
solve the uncertain and indistinct predicament in the whole in which, conditioning and calculations of minimization in
error of the signal is carried out. This conditioning defies the total PWM pulse-control as the duty cycle of the signal. The switching of TON and TOFF pattern in the inverter arms is based on the predefined sequence of rotor position, which is elucidated from the back EMF of the waveform. The PWM pulses ranges from 0% to 100% which drives the MOSFET based PWM driver circuit to control the speed of the motor. When the duty cycle is changed the controller anticipates the addition and reduction in the error, accordingly.
The block-sets of the BLDC motor drive with fuzzy logic- based PI controller is shown in Fig. 2. It has the feature of its gain varying capacity as per the operating point, which give the optimum speed variable responses.
Fig. 2. Block diagram of speed control of BLDC motor drive using fuzzy logic-based PI Controller
The scheme comprises of the fuzzy controller as an input to the system which has error (e) and change in error as (de). This is normalized to (-1, +1) by using the scaling factor method [18]. The trimf – type (shaped) membership functions are used to represent both the input and output signals of the fuzzy logic-based PI controller. These membership functions are then converted into certain logic statements of fuzzy. Specific or desired rules are generated with the combination of IfElse or IfThen combinations. Also, to linearize the system, the logical rules called as fuzzy based statements are used in order to form the logical AND or OR operation. The linear rule-based table for fuzzy control algorithm is show in Table I. The 1st rule can be expressed as, If error (e) is Negative Big (NB) AND differential error (de) is Negative Big (NB) then the output is Negative Big (NB). In this way, such desirable rules by the researcher can be made with as many rules as possible.
ede
NB
NM
NS>
ZO
PS
PM
PB
NB
NB
NB
NB
NB
NM
NS
ZO
NM
NB
NB
NB
NM
NS
ZO
PS
NS
NB
NB
NM
NS
ZO
PS
PM
ZO
NB
NM
NS
ZO
PS
PM
PB
PS
NM
NS
ZO
PS
PM
PB
PB
PM
NS
ZO
PS
PM
PB
PB
PB
PB
ZO
PS
PM
PB
PB
PB
PB
ede
NB
NM
NS
ZO
PS
PM
PB
NB
NB
NB
NB
NB
NM
NS
ZO
NM
NB
NB
NB
NM
NS
ZO
PS
NS
NB
NB
NM
NS
ZO
PS
PM
ZO
NB
NM
NS
ZO
PS
PM
PB
PS
NM
NS
ZO
PS
PM
PB
PB
PM
NS
ZO
PS
PM
PB
PB
PB
PB
ZO
PS
PM
PB
PB
PB
PB
TABLE I. A LINEAR 2-D FUZZY LOGIC CONTROL RULES BASE
culpable algorithm that stipulates the best crisp value based on a fuzzy set.
-
MATLAB SIMULATION
The real motor parameters are implemented to develop a replica of a motor in simulation model while, its PI based controller block-set is shown in Fig. 3. The working of conventional Proportional-Integral (PI) controller is based-on estimation technique of trial-and-error-method. It calculates error (e) between the measured quantity and desired quantity and convey the corrective action to continue the process. The error signal generated can be given as,
et = reference quantity (set values)
– actual quantity (determined values)
Typically, the speed control of BLDC motor drive consists of reference speed generator, speed controller, pulse width modulation, source inverter and position sensor to track the position of the rotor. The working of PI controller is stated in two categories of modes. The speed control of BLDC motor is done, by comparing speed of the motor to the reference speed value, later it is processed by PI controller and reference torque generated can be controlled by generating switching commands and setting the limits.
Fig. 3. MATLAB simulation model for speed control using PI controller
Fig. 4. PI controller subsystem blocksets in MATLAB / Simulink
The PI based simulation blockset is shown in the Fig. 4, where the gain values of Kp and Ki values are automatically kept by double clicking on the block set of PI controller. The simulation responses of speed at 500rpm, 750rpm and 1000rpm, electromagnetic torque, stator currents Iabc, and hall effect sensor output voltage, respectively, can be observed through the scope, which is as shown in Fig. (5 – 10), respectively.
Where,
NB Negative Big
NM Negative Medium
NS Negative Small ZO Zero
PS Positive Small
PM Positive Medium
PB Positive Big
Fig. 5. Speed response characteristics of BLDC motor drive at 500 rpm using PI controller
To obtain the crisp output, the center of area or centroid method is used to determine the area of fuzzy sets, which is a
within the set fuzzy inference system block. The gain values of GKp and GKi values are then set to normalize the crisp fuzzified output which is also as shwon in the Fig. 12. The trimf conical format of the error and differential error with there respective membership functions is shown in Fig. 13. The Membership functions used to the output is depicted as a cris-cross format, which is also shown in the Fig. 14, respectively.
Fig. 6. Speed response characteristics of BLDC motor drive at 750 rpm using PI controller
Fig. 7. Speed response characteristics of BLDC motor drive at 1000 rpm using PI controller
At initial stage i.e. when load torque is 0.5 N-m, speed response is found to be steady and load torque oscillates between 0 to 0.6 secs. When load is increased at t = 1 sec. of 75gms., load torque disturbances are observed to be risen, accordingly. Similarly, the stator current can be observed to be disturbing in nature when load torque increases. The Te characterisctic response follows the traditional response of BLDC motor drive, as shown in Fig. (8 10). As the control logic changes, the control response changes and the duty cycle with respect to back emf also changes, respectively.
Fig. 8. Electromagnetic torque (Te) response characteristics of BLDC motor drive using PI controller
Fig. 9. Stator Currents (Iabc) response characteristics of BLDC motor drive using PI controller
The simulation of speed control of BLDC motor using fuzzy-based PI controller is shown in Fig. 11 and its corresponding Fig. 12 is the subsystem of fuzzy logic controller. It consists of certain nominal Gain values as Ge and Gde values when connected to the input side of the system. This part is input side or defuzzified input side. This is then conditioned using the fuzzy crisp rules in the fuzzy block. The fuzzified rules are stored in the .fis format
Fig. 10. Hall effect signal (habc) response characteristics of BLDC motor drive using PI controller
Fig. 11. MATLAB simulation model for speed control using Fuzzy-PI Controller
Fig. 12. Fuzzy Controller
Fig. 13. Membership function for input error and change in error
The fuzzy controller mainly works on conversion of numeric variables into linguistics variables. These fuzzy control rules are developed with the help of linguistic rules as an input and output variables are converted into linguistics variables. The control rules for fuzzy controller are shown in Table I.
The characteristic response obtained with fuzzy-based PI controller is shown in Figure (14 16). The motor parameters used in the simulation is as per Table II. At initial condition, when load torque is 0.5 N-m, the oscillations occurs between
0 to 0.2 secs. The load is applied of 75gms. at t = 1 sec., the speed slightly dips and the motor tries to minimise the error which is equal to reference speed. The response time remains steady. The torque and stator current varies steadily. The speed response using the proposed fuzzy-logic based PI controller carries the stable behaviour as compared to conventional PI controller. Hence, from Table III, for 500 rpm, the rise time and settling time is comparative to fuzzy based PI controller by 88.24% and 13.33%, respectively. For 750 rpm, the rise time and settling time is comparative to fuzzy based PI controller by 90.90% and 20.71%, respectively and For 1000 rpm, the rise time and settling time is comparative to fuzzy based PI controller by 97.77 and 20.45%, respectively.
Fig. 14. Membership function for output regulation
Fig. 15. Speed response characteristics of BLDC motor drive at 500 rpm using Fuzzy-PI controller
Fig. 16. Speed response characteristics of BLDC motor drive at 750 rpm using Fuzzy-PI controller
Fig. 17. Speed response characteristics of BLDC motor drive at 1000 rpm using Fuzzy-PI controller
TABLE II. MOTOR PARAMETERS USED IN SIMULATION
Parameters
Values
Rated Voltage (V)
24V
Stator Phase Resistance (Rs)
0.7
Stator Phase Inductance (Ls)
2.72e-3H
Back EMF Flat Area (Degrees)
120
Inertia (J)
0.8e-3 kg.m2
Viscous Damping (F)
1e-3 N.m.s
Number of Poles (P)
4
TABLE III. SIMULATION RESULTS OF TIME RESPONSE TO SYSTEM STUDY AT DIFFERENT SPEED RESPONSES
Controller Type
Speed (rpm)
Tr (Sec.)
Ts (Sec.)
PI Controller
500
0.068
1.5
750
0.055
1.4
1000
0.045
1.32
Fuzzy Logic- Based PI Controler
500
0.008
1.3
750
0.005
1.11
1000
0.001
1.05
-
HARDWARE RESULTS
A laboratory-based test setup was designed for implementation of the fuzzy logic based control scheme to improve the speed response of the system and the Hardware was made by following the considerations of Figure (1 & 2) and the arrangements were made according to it.
The hardware comprises of a 24V, 60W BLDC motor with 1500 rpm rated speed. Hall effect sensor Ha, Hb, and Hc is inbuild in the motor itself, a 24V, 10A SMPS used as a power supply, a MOSFET IRFZ44N based Driver circuit with TLP350 based driver IC and ATMEGA328P-PU microcontroller module unit. The motor parameters are as per Table IV, tabulated and presented. The weight of 75gms is loaded by the belt pulley, vertical spring load meter and the vertical frame stand structure. The pulley is fixed on the shaft of the BLDC motor and the motor screw surface is mounted on the 90° vertical to the base plate of the frame, which is so connected that the weight of the motor and the weight of the stand can withstand with a perfectly balanced construction when in loaded or in un-loaded conditions is carried out. The PI based and Fuzzy logic-based PI programming is uploaded in the ATMEGA328P-PU microcontroller module unit and the output responses can be observed on the serial monitor of the Arduino Platform. The frequency of gate pulses is set at 2 kHz. The speed response when commanded for 500rpm, 750rpm and 1000rpm of BLDC motor using conventional PI controller is shown in Figure. (18 20), respectively. The responses are such that the amount of weight loaded on that instant is subjected to the applied speed and the distortion.
TABLE IV. MOTOR SPECIFICATIONS
Parameters
Values
Rated Voltage (V)
24V
Stator Phase Resistance (Rs)
0.87
Stator Phase Inductance (Ls)
2.72e-3H
Back EMF Flat Area (Degrees)
120
Power (P)
60W
Rate Speed (rpm)
1500
Fig. 18. Hardware based speed response of BLDC motor drive at 500 rpm using PI controller
Fig. 19. Hardware based speed response of BLDC motor drive at 750 rpm using PI controller
Fig. 20. Hardware based speed response of BLDC motor drive at 1000 rpm using PI controller
At initial conditions of hardware loading and unloading, the mechanical load torque is 0.7355 N-m, the oscillations occurs between 0.2 to 0.8 secs, which is as shown in Fig. 18. The load is applied of 75gms. at t = 1.4 sec., to observe an unconditional loading behavior while the drive is at running condition when PI control logic is applied. The load when observed on the spring type load is converted into N-m mathematically as, (11000) of a kilogram equals to 1 N-m in earths gravity, which is probably equal to the weight of (19.80665) Kgs. on earth. This can again be calculated using the Newtons second law, as f = m x a and by assuming the earths gravity of 9.80665 ms2. Thus, 0.7355 N-m (earth) = 75gms. The speed slightly dips and the motor tries to minimise the error which is equal to reference speed. The response time remains steady.
Fig. 21. Hardware based speed response of BLDC motor drive at 500 rpm using fuzzy-based PI controller
Fig. 22. Hardware based speed response of BLDC motor drive at 750 rpm using fuzzy-based PI controller
Fig. 23. Hardware based speed response of BLDC motor drive at 1000 rpm using fuzzy-based PI controller
The speed responses when commanded for fuzzy-based PI controller applied to BLDC motor at 500rpm, 750rpm and 1000rpm, is shown in Figure (21 – 23), respectively. It can be nearly seen that the fuzzy-PI based controller has better responses as compared to traditional PI controller and the response time is tabulated in Table V. The speed response using the proposed fuzzy-logic based PI controller carries the stable behaviour as compared to conventional PI controller. For 500 rpm speed response, the rise time and settling time is comparative to fuzzy based PI controller by 98.35% and 77.50%, respectively. For 750 rpm, the rise time and settling time is comparative to fuzzy based PI controller by 98.375% and 84.84%, respectively and for 1000 rpm, the rise time and settling time is comparative to fuzzy based PI controller by 96.09% and 93.33%, respectively. Hence, fuzzy logic-based PI controller has best response as compared to the PI based controller due to less settling time and good speed accuracy. Also, when the load is applied to fuzzy-logic based controller at once, there is very less distortion or sudden dip in the waveform of the drive.
TABLE V. HARDWARE RESULTS OF TIME RESPONSE TO SYSTEM STUDY
Controller Type
Speed (rpm)
Tr (Sec.)
Ts (Sec.)
PI Controller
500
0.040
1.60
750
0.032
1.32
1000
0.011
1.20
Fuzzy Logic- Based PI Controler
500
0.00066
0.36
750
0.00052
0.20
1000
0.00043
0.08
The main difference between the software and hardware results by virtue of its relative comparison with distinct speed response is stated in the Table VI. As the nature of both the arrangement is conceptually similar but dis-similar practically, the time responses of both rise time and settling time is comparable. Hence, the relative analysis of each speed
can be done on the basis of results of hardware and software in the form of percentage change in both the conditions.
The difference between the speed response using PI controller in simulation and hardware for 500 rpm speed on Tr is 41.17 % and on Ts is 6.667 %; for 750 rpm speed the Tr is 41.81 % and on Ts is 5.71 %; and for 1000 rpm speed the Tr is 75.55 % and on Ts is 9.09 %. Similarly, the difference between the speed response using fuzzy-based PI cntroller in simulation and hardware for 500 rpm on Tr is 91.75 % and on Ts is 72.30 %. For 750 rpm speed the Tr is 89.60 % and on Ts is 81.98 % and for 1000 rpm speed the Tr is 57 % and on Ts is 92.38 %.
TABLE VI. RELATIVE COMPARISON OF SOFTWARE & HARDWARE TESTING RESULTS OF DISTINCT SPEED RESPONSES TO SYSTEM STUDY
Controller Type
Speed (rpm) in Simulink & Hardware
Tr (Sec.) in Simulink
Ts (Sec.) in Simulink
Tr (Sec.) in Hardware
Ts (Sec.) in Hardware
PI
Controller
500
0.068
1.5
0.040
1.60
750
0.055
1.4
0.032
1.32
1000
0.045
1.32
0.011
1.20
Fuzzy Logic- Based PI Controler
500
0.008
1.3
0.00066
0.36
750
0.005
1.11
0.00052
0.20
1000
0.001
1.05
0.00043
0.08
-
CONCLUSION
-
An implementation scheme for speed control of BLDC motor using conventional PI and fuzzy logic-based PI controller was discussed in this paper. It was seen that the fuzzy logic controller generates the required values for tuning parameters of the PI controller by using information about speed error and change in speed error. A comparison is done between conventional PI controller and fuzzy based PI controller for validation of performance. The system was simulated using MATLAB/ Simulink environment and the fuzzy logic designer toolbox was used for generating fuzzy rules and membership functions. The basic design procedure of fuzzy logic-based controller was presented along with types of fuzzy knowledge-based controller and design of fuzzy-PI controller for BLDC motor was discussed. A simple set of fuzzy logic rules were programmed in ATMEGA328P-PU microcontroller using this information. Also, the relative comparison of software-based results and hardware-based results based on Tr and Ts is presented and can be observed that, there is always a change in the practical system as compared to simulation environment. The presented results show that an artificial intelligence control method like fuzzy logic can improve speed response of the BLDC motor and can be an attractive solution for small devices with cost effective hardware using ATMEGA328P-PU microcontroller. The scheme can be extended to various electric type two-wheeler vehicles as well.
REFERENCES
-
Module 7, Lesson 35, Electrical Machine Drives, Version 2, EE. IIT Kharagpur, pp. 1-15.
-
T.J.Sokira & W.Jaffe, Brushless DC motors: Electronic Commutation and Control, Tab Books, USA, 1989.
-
Amit Kapil, Bhadja Satish Analysis of cogging torque reduction by increasing magnet edge inset in radial flux permanent magnet brushless DC motor, ICPEICES- 2016. 4-6 July 2016.
-
R. M. Pindoriya, A.K. Mishra, B.S.Rajpurohit Analysis of position and speed control of sensor less BLDC motor using zero crossing back-EMF technique, ICPEICES-2016.4-6July2016.
-
C. Sheeba Joice, P. Nivedhitha, Simulation of speed control of brushless DC motor, with Fuzzy Logic Controller, International Journal of Electrical, Electronics and Data communication, volume-2, Issue -4, April 2014.
-
Shivanand Pandey, Bhagirath Pandey, DC motor torque control using Fuzzy Proportional Derivative controllers, International Journal of Engineering and Advance Technology, volume 3, Issue 6, Aug 2014.
-
Manoj Kushwah, Prof. Ashis Patra, Tuning PID controller for speed control of DC motor using soft computing technique A Review, Advance in Electronic and Electric Engineering, Volume 4, Issue 02, Aug 2014.
-
B.R. Lin, Analysis of Neural and Fuzzy control power Electronics Control, IEEE proceeding SCI .Meas. Tech VOl. 144,NO.1, Jan. pp2533, 1997.
-
Somanatham.R, Prasad. P.V.N, Rajkumar.A.D, Modeling and Simulation of Sensor less Control of PMBLDC Motor Using Zero Crossing Back EMF Detection, IEEE SPEEDAM 2006 International Symposium on Power Electronics, Drives, Automotive and Motion.
-
Rakesh Goswami, Dheeraj Josi, Performance Review of Fuzzy Logic Based Controllers Employed in Brushless DC Motor, vol. 132, pp. 623-631, 2018.
-
Prashant Kumar, Ranjan Kumar Behera, Devara Vijaya Bhaskar, Novel Closed Loop Speed Control of Permanent Magnet Brushless Dc Motor Drive, pp. 1-6, 2018.
-
Mega Wahyudi, BudiSetiyona Rosaliana, Sumardi, Designing of self- tuning regulator for brushless motor speed control, IEEE ICSGTEIS 2018, pp. 43-47.
-
Abasin Ulasyar, Haris Sheh Zad, Adil Zohaib, Intelligent Speed Controller Design for Brushless DC Motor, pp. 19-23, 2018.
-
Adel A. El-samahy, Mohamed A. Shamsel, Brushless DC motor tracking control using self-tuning fuzzy PID control and model reference adaptive control, Shams Engineering Journal, pp. 341-352, 2018.
-
K. Vanchinathan, K. R. Valluvan, A Metaheuristic Optimization Approach for Tuning of Fractional-Order PID Controller for Speed Control of Sensorless BLDC Motor, vol. 27, 2018.
-
Lokesh Kumar Agrawal, Bhavesh Kumar Chauhan, G. K. Banerjee, Speed Control of Brushless DC Motor Using Fuzzy Controller, vol. 119, no. 15, pp. 2689-2696, 2018.
-
Mohammad Mohiuddin Shah Khan, Shakeel M Muhammad, Analysis of speed control of Brushless D.C Motor using Hybrid Fuzzy Controller, vol. 03, no. 17, pp. 1-8, 2016.
-
Akash Varshney, Deeksha Gupta, Bharti Dwivedi, Speed response of brushless DC motor using fuzzy PID controller under varying load condition, pp. 310-321, 2017.
-
Meng Zhao, Xiangbin Liu, Hongye Su, Robust Adaptive Speed Control of Disturbed Brushless Direct Current Motor, pp. 141-146, 2017.
-
S.K. Saranya, T. Gowthamraj, P. Ranjani, THD Analysis in Three Phase-Three Level VSI with MPPT Tracker and SEPIC Converter for Solar PV Array, vol. 12, no. 16, pp. 4895-4901, 2016.
-
B. K. Bose, Power electronics and motor drives-recent technology advances, Proceedings of the IEEE International Symposium on Industrial Electronics, pp. 22-25, July 2002.
-
C Senthil Kumar, N Senthil Kumar, KS Krishna Veni, Design and Evaluation of PI Controller for Four Switch BLDC Motor Drive, Applied Mechanics and Materials, vol. 573, pp. 136-142, 2014.
-
F. Caricchi, F. Giulii Capponi, F. Crescimbini, L. Solero, Sinusoidal Brushless Drive with Low-Cost Hall Effect Position Sensors, IEEE Transaction of Industrial Application, pp. 799-804, 2001.
-
J. Shao, D. Nolan, T. Hopkins, A Novel Direct Back-EMF Detection for Sensorless Brushless DC (BLDC) Motor Drives, Applied Power Electronic Conference, pp. 33-38, 2002.
-
R. Krishnan, R. Ghosh, Starting Algorithm and Performance of a PM DC Brushless Motor Drive System with No Position Sensor, IEEE PSEC, pp. 815-82, 1989.