
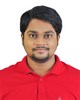
- Open Access
- Authors : D. Kashyap , A. Ajay Reddy , M. Arun , R. Sabari Vihar, D. Govardhan
- Paper ID : IJERTV10IS050446
- Volume & Issue : Volume 10, Issue 05 (May 2021)
- Published (First Online): 03-06-2021
- ISSN (Online) : 2278-0181
- Publisher Name : IJERT
- License:
This work is licensed under a Creative Commons Attribution 4.0 International License
Comparative Study on Airless Tyre of Different Spoke Structure on Aircraft
D. Kashyap1, A. Ajay Reddy2, M. Arun 3, R. Sabari Vihar4, D. Govardhan5
Research student1, Research student2, Research student3, Assistant professor4, Head of the department5, Department of Aeronautical Engineering, Institute of Aeronautical Engineering, Telangana, India.
Abstract: The air enclosed rubber is packed with pressurized air to form a pneumatic tyre. Due to its low pressure in contact, minimum vertical rigidity and low mass design, it is very dominant in the market. The NPT were introduced to overcome the disadvantages of pneumatic, which are complex manufacturing procedure, maintenance of internal air pressure. The NPT doesnt use air to support the load. The main three parts of the NPT are, a rigid hub, deformable spokes, tread, reinforced shear band which have contact with the surface. In this project, the conventional alloy wheel is replaced with flexible spoke structure in a Cessna 172 aircraft. With uni-axial load, we investigated various spokes designed for the NPT. The spokes were designed accordingly to the tyre measurements of Cessna 172 aircraft in CREO. Ansys 19.2 provides the analysis. The finite element analysis is used to study about the stresses and deformation in various speaking types. In this project we studied and tested on NPT of pipe, spline, double spline structured spokes.
Keyword: Non-Pneumatic tyre, Uni-Axial load, Spokes structures, Creo, Ansys 19.2, Cessna 172.
-
INTRODUCTION TO NON-PNEUMATIC TYRE
Introduction
Vehicles rode along with cushions of rubber-embraced air for more than 100 years. Sometimes, we become so accustomed to some product that for years or decades no real change has ever been made. This is how our project starts on the development of airless tires, which in the last few years has become increasingly prevalent. A few nonpneumatic tyre designers, including Michelin and Bridgestone, have started to experiment, but neither design has made it into mass production.
Non-Pneumatic Tyre
The development of a new non-Pneumatic tires, as one might think, will have more positive effects. There are huge safety advantages. With an airless tyre, there are no blowouts, so road accidents can be considerably reduced. It has a solid internal hub, which is attached onto the axle of the vehicle, and is enveloped in polyurethane. This forms a wedge pattern that can absorb road effects. These spokes are similar to that found on bicycles and are like a traditional pipeline to shock-absorb the air of the compressed air. Then a simple band is extended over the spokes that form the outside edge of the tyre. The air pressure used on traditional pipes is supported by the band voltage and the strength of the spokes. For example, if a car drives across an obstacle, the tread and shear strips bend when the spokes bend back into shape, before they rebound quickly.
-
LITERATURE REVIEW
Mohammad Fazelpour [1] was concerned with the study of meso structures in the development of the non- pneumatic tyre's shear band and concluded as below. To increase NASA manned exploration system fuel efficiency, they substituted elastomeric material with shear band shavings with materials that can withstand harsh temperatures and shear loads or replacing the material by linear elastic materials with low hysteretic loss. Shear straps of nonpneumatic tyres, which included the use of mesostructures, shear strains and contact pressure, were investigated through the implementation of new forms, including s-type mesostructures and structural analysis. In the final analysis they set out guidelines on custom mesostructural designs for challenging applications, for example the nonpneumatic tyre, and the passive morphing airfoils. In search of yielding spoke structures, A.M. Aboul-Yazid [2] examined 3 different Twell structures, resistance technologies and NPT. The quasi-static 2D analysis of pressure, vertical tyre stiffness and stress, which are influenced by spokes and shear belt, were done by creating a tyre with a composite ring and a tyre without a composite. The results showed that spokes shape and size have an effect on tyres and the shear cap reduces the impact on the contact pressure distribution of the deformed spokes shape. In its life cycle from assembly, through use and transmission Bert Bras [3] discussed the ecological effect of the Tweel tyre. Since the tweel tyre remains in the testing stage and most definitely not produced and used in large measurements, there are instabilities as regards end-of-life situations and assessments of rolling resistance which will affect the LCA
Problem Definition
Non pneumatic tyres are generally more rolling resistant and have significantly less suspension than pneumatic tyres in similar shape and size. Added, airless tyre problems contain heat dissipation that occurs when driven. Nonpneumatic tyres, as compared to air, are often packaged with compacted polymers. Taking into account the non-pneumatic tyre structure, spokes are compressed and tight while they roll in cyclical loadings. Therefore, the localized stress of spokes must be reduced, which means that spokes must be tiredness resisting. In this project we considered non-pneumatic tyre based on circular pipe, spline, double spline. The spokes of non- pneumatic tyres are crucial for the rigidity and resilience under cyclic loading of compressed stress. The challenge is to design highly rigid, highly durable materials.
-
METHODOLOGY
CAD Model
The measurements of the tyre of Cessna 172 aircraft are obtained from GOODYEAR AVIATION company tyre data book.
The aircrafts tyre is classified into types. Most of the aircrafts tires are of type 3. The type of tyre that is being used for Cessna 172, is referred as 6.00-6, where its geometric data is given below
Table 3. 1 Geometric data of NPT by Goodyear Aviation
Outside diameter(in)
Section width(in)
Shoulder(in)
6.00-
6
Max
Min
Max
Min
Max
Min
17.5
16.8
6.30
5.9
15.5
5.30
The NPT is classified into types depending on number of layers of structural spokes. There is single layer, multi layered. Here we designed 3 different spokes, pipe, spline and double spline. Here as we see the spline structured spoke is a single layered NPT, while double spline and pipe structured spokes are multilayered NPT. Spline structure is patterned with a radius of 196.7mm and thickness of 4mm, in clock-wise direction. The double spline is patterned with radius 196.7mm and thickness of 4mm in clockwise and counter clockwise as well. The pipe structured spokes are patterned with a radius of 10.51mm on the 1st layer, here we need to note that the radius of pipe shrinks as it reaches to the hub of NPT. It is done to increase the weight of tyre by increasing the number of layers in spokes. The radius of each pipe of NPT shrinks accordingly with the radius of the whole tyre. All the three spokes are of 150mm section width.
Figure 3. 2HUB
Figure 3. 3 Spokes
Figure 3. 4 Shear band
Figure 3. 1 Designing of Spokes in Creo
In the above Figure 3.1, figure a represents how to design spline structured spokes, figure b, c represents the design procedure for double spline spoke structure, figure d gives the geomeric data required to design pipe spoke structure.
Analysis
Figure 3. 5 Tread
The FEM is a numerical technique for solving differential equations that is described or can be solved for minimization of functions. In finite elements, functions approximating is determined using the nodal values of a searched continuum. The continuum or physical problem is transformed into a small finite
element problem that is discretized with unknown nodal values. FEM is a computer program used to analyze a material and find out how stresses affect the load design or material.
Material properties
The materials for NPT tyres used in this analysis include aluminium alloy, high strength steel, polyurethane, and rubber. The main reason for the selection is because they have a wide range of mechanical properties such as high rigidity and strength, high flexibility, hyper-plastic resistance, high temperature resistance and other factors. The table 3.2 gives the materials assigned to each part and its properties.
Table 3. 2 Material properties of NPT
Meshing
Boundary Conditions
Figure 3. 8 Boundary conditions applied for NPT
The internal surface of the wheel is fully restricted all the way, as the hub of the wheel is fixed and acting as a permanent support for the wheel. In y-direction on the outer surface of a wheel, the surface load of 7248 N is applied, because 7428N is the maximum braking load capacity of type 3, 6.00-6 tyre.
Figure 3. 9 Boundary conditions applied for NPT for rotational rad/sec
The internal surface of the wheel is fully restricted all the way. A rotational velocity of 280 rad/sec is applied in x- direction. The boundary conditions are same for every model of NPT designed.
Solver
For the above load cases, the linear static analysis and model analysis is performed on a non-pneumatic tyre. For numerical solutions, the commercial FE solver ANSYS V19.0 is used
-
RESULTS
Linear static analysis
Figure 3. 6 Mesh settings in Ansys 19.2
The mesh settings for every model of NPT are same. All the meshed models are shown in Figure 3.7.
Figure 3. 7 Meshed models of NPT
The following results were found for the above mentioned load cases
-
Total deformation
-
Von-Mises equivalent stress
-
Maximum Principal stress
-
Minimum Principal stress
Table 4.1 gives the results for respective NPTs.
Figure 4. 1Total deformation of all models
Figure 4. 2 Von-Mises Equivalent stress
Figure 4. 3 Maximum Principal Stress
Figure 4. 4 Minimum Principal Stress
Table 4. 1Results of Linear Static Analysis
Modal Analysis
Here we applied static load of 7428N and rotational velocity of 280 rad/sec in x-direction.
Frequencies and mode shapes of Pipe NPT
Figure 4. 5 Mode shape 1 and 2
Figure 4. 6 Mode Shapes 3 and 4
Figure 4. 7 Mode Shapes 5 and 6
Frequencies and mode shapes of Double spline NPT
Figure 4. 8 Mode Shape1 and 2
Figure 4. 9 Mode Shape 3 and 4
Figure 4. 10 Mode Shape 5 and 6
Frequencies and Modes Shapes of Spline NPT
Figure 4. 11 Mode Shape 1 and 2
Figure 4. 12 Mode Shape 3 and 4
Figure 4. 13 Mode Shape 5 and 6
Table 4. 2 Modal Analysis report
The above obtained operating frequencies of NPTs fall under the natural frequencies of NPT.
-
-
CONCLUSION
The linear static analysis of NPT had been carried out. The VON-MISES stress value obtained in static analysis for all three models are 53.97 MPa, 55.395 MPa, 57.564 MPa respectively for double spline, spline, Pipe NPT which are under permissible limits of material properties which concludes that the structure is safe. The modal analysis indicates that the design requires some improvements which can increase the life of the wheel.
-
RFERENCES
-
M. Fazelpour and J. D. Summers, A Comparison of Design Approaches to Meso-Structure Development, in Volume 3A: 39th Design Automation Conference, Portland, Oregon, USA, Aug. 2013, p. V03AT03A052. doi: 10.1115/DETC2013-12295.
-
Automotive and Tractor Engineering Department Helwan University, Egypt et al., EFFECT OF SPOKES STRUCTURES ON CHARACTERISTICS PERFORMANCE OF NON- PNEUMATIC TIRES, Int. J. Automot. Mech. Eng., vol. 11, pp. 22122223, Jun. 2015, doi: 10.15282/ijame.11.2015.4.0185.
-
B. Bras and A. Cobert, Life-Cycle Environmental Impact of Michelin Tweel ® Tire for Passenger Vehicles, SAE Int. J. Passeng. Cars Mech. Syst., vol. 4, no. 1, pp. 3243, Apr. 2011, doi: 10.4271/2011-01-0093.
-
K. Kim and D. M. Kim, Contact Pressure of Non-Pneumatic Tires with Hexagonal Lattice Spokes, Apr. 2011, pp. 2011-01 0099. doi: 10.4271/2011-01-0099.
-
J. Ju, B. Ananthasayanam, J. D. Summers, and P. Joseph, Design of Cellular Shear Bands of a Non-Pneumatic Tire -Investigation of Contact Pressure, SAE Int. J. Passeng. Cars Mech. Syst., vol. 3, no. 1, pp. 598606, Apr. 2010, doi: 10.4271/2010-01- 0768.
-
I. G. Masters and K. E. Evans, Models for the elastic deformation of honeycombs, Composite Structures, vol. 35, no. 4, pp. 403422, Aug. 1996, doi: 10.1016/S0263-8223(96)00054- 2.