
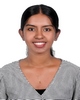
- Open Access
- Authors : Jesna Joshy, Ar.Jelitta Elizabath Sabu
- Paper ID : IJERTV13IS080089
- Volume & Issue : Volume 13, Issue 08 (August 2024)
- Published (First Online): 03-09-2024
- ISSN (Online) : 2278-0181
- Publisher Name : IJERT
- License:
This work is licensed under a Creative Commons Attribution 4.0 International License
Comparison of Residences using GFRG as a Building Material with Conventional Residences in Kerala
Jesna Joshy
Student, Department of Architecture School of Architecture and Design Bishop Jerome Institute, Kollam
Ar.Jelitta Elizabath Sabu
Assistant Professor, Department of Architecture School of Architecture & Design Bishop Jerome Institute, Kollam
Kerala, India
AbstractGFRG (Glass Fiber Reinforced Gypsum) has gained significant popularity as a building material in the state of Kerala. The establishment of the manufacturing plant by FACT (Fertilizers & Chemicals Travancore Ltd.) as a joint venture which is known as FRBL (FACT-RCF Building Products Ltd.) in Ambalamedu, Kochi, played a pivotal role in recent years, as people have increasingly sought sustainable, cost-effective, and eco-friendly solutions in building construction, and thus, GFRG residences have seen a surge in demand. Low maintenance and economic viability have been driving factors behind this trend. This study aims to comprehensively evaluate the advantages and disadvantages of GFRG as a building material when compared to conventional structures in the context of Kerala. Various factors will be considered, including area savings, cost calculations, internal temperature, acoustics, weather resistance and maintenance. The study will utilize case studies to provide practical insights into the performance and feasibility of GFRG structures in Kerala's specific conditions. These case studies will offer a deeper understanding of the suitability and potential challenges associated with GFRG in real-world construction scenarios.
KeywordsGFRG; building material; feasibility; residences; Kerala.
-
INTRODUCTION
In a world where fast paced living is the norm, the use of Prefabricated materials has risen in high demand and is the need of the hour. GFRG (Glass Fiber Reinforced Gypsum) has gained significant popularity as a building material in the state of Kerala due to the establishment of the manufacturing plant FRBL (FACT-RCF Building Products Ltd.) in Ambalamedu, Kochi, which played a pivotal role in recent years, as people have increasingly sought sustainable, cost-effective, and eco- friendly solutions in building construction. The current and only manufacturing company of GFRG panels as of 2023 is BACE India, Coimbatore. Often, the question arises as to whether conventional building materials or prefabricated building materials, despite its hype, are better at cost savings and performance. This study aims to check the feasibility of GFRG as a building material and whether it can be suggested as an alternate building material for the state of Kerala.[1][2]
-
AIM,OBJECTIVE,SCOPE
The aim of the study is to analyse the functionality and feasibility of GFRG as a building material in terms of area savings, cost, environmental factors, and maintenance in
comparison with conventional residences within Kerala context.
Objectives:
-
To compare the conventional and GFRG building construction with respect to cost and area savings and report findings.
-
To determine the feasibility of the building material through user opinion.
-
To analyse and suggest through selected parameters the most convenient building material that can be used in Kerala.
-
The study can show which building material is most effective based on cost and area savings and other qualitative parameters.
-
Cost comparison with conventional buildings and GFRG buildings.
-
The study covers the basic aspects of the need for using GFRG as a building material and whether it can be used as a better building material compared to conventional structures.
-
-
OVERVIEW
GFRG, or Glass Fiber Reinforced Gypsum, is a construction material that combines gypsum plaster with glass fibers to create a strong and lightweight composite. GFRG is known for its versatility and is commonly used in the construction industry for various applications, including wall panels, partitions, and architectural elements. GFRG Panel is the worlds largest lightweight load-bearing panels manufactured with a size 12m length, 3m heights, and 124mm thickness. Each panel has 48 modular holes of 230 mm * 94mm * 3m dimension. The weight of one panel is 1440 kg. GFRG has relatively gained popular demand in the state of Kerala as a prefabricated material mainly due to the opening of the manufacturing plant factory in the Kochi FACT-FRBL headquarters. GFRG has been chosen in this study as it has gained substantial amount of popularity in Kerala due to its claim of area and cost savings. But the question has arisen as to whether GFRG is cost and area saving material as it claims to be? A detailed comparison with other factors like maintenance and thermal comfort is necessary to understand whether the selection of GFRG as a building material is better than
conventional building materials that have predominantly existed in the local market. [1][2]
-
Conventional building materials
As per House and household amenities in Kerala, 2011 census, table 4.3, households by predominant material of wall are: Laterite stone packed with mortar (47.4%) and Burnt bricks (24.5%). A poll was conducted with a sample population of 100 persons on which building material was the individuals residences made of. The sample consisted of users from all over Kerala. According to the poll conducted, the most residences constructed were of Burnt brick 44%, followed by Cement block 33%, then Laterite at 17%, with the least building material used as Hollow brick at 6%. From this poll and the census data provided, we can deduce that the three most used conventional building materials in Kerala are: Burnt bricks, Concrete blocks and Laterite stone packed with mortar. Hence, the above mentioned three materials will be taken in this study for comparison purposes with GFRG as a building material.
-
Methodology
-
Identification of GFRG case studies- Two each of single storey and double storey. The classification is based on the number of storeys in the building. Here two residences of single storey typology and two of double storey typology are chosen. This helps to give an idea regarding carpet area calculation, cost savings, method of construction and durability.
-
Collection of quantitative data from random residences for conventional building materials to arrive at a uniform conclusion GFRG residences excluded due to limited availability.
-
Creation of similar scenarios to provide for comparison purposes.
-
Comparison of all the collected data and arrival at conclusions
-
-
CASE STUDIES AND PARAMETERS
-
Mr. Georges residence
-
Mr. Jose Antos Residence
-
Mr. Sijos Residence
-
Mr. Shibu Xaviers Residence
Quantitative Parameters considered for the purpose of this study are- 1. Area calculations 2. Cost Estimation 3. Construction time period 4. Thermal comfort 5. Acoustics
Qualitative Parameters considered for the purpose of this study are- 1. Weather resistance 2.Maintenance 3. Aesthetics and customization.
-
Area Calculations
Table 1 shows that the area calculation comparison is done by employing the floor plans of the case studies mentioned earlier and drafting the same plan with the conventional building materials selected, keeping the boundary of the buildings intact and only by making internal variation according to the
dimensions of the building material. The carpet area covered by the buildings with all the floor plans can then be compared to see which building material takes the least amount of space and provides more usable area. Comparison for case studies based on Built-up area vs. Carpet area- The savings are calculated from all case studies to find a common factor among the area used up by the building materials.
Table 1 Area calculations in sqm.
-
Cost estimation
Fig.1 shows a simple floor plan consisting of a 2bhk setup with an attached washroom is taken and the same room dimensions are maintained with different building materials. Here, we can take two approaches for the construction of GFRG Building
1. Using the GFRG panels for the construction of roof and sunshades, and 2. Using the concrete work for the construction of roof and sunshades- GFRG panels are not infilled. A significant reduction can be seen when GFRG panel leftovers are used for the construction of roofing and sunshades. Overall, not much significant changes can be observed in the cost savings. GFRG provides for more cost savings when compared to conventional building materials.
Figure 1 Sample floor plan
Building Material
Cost (INR)
GFRG
Rs.5,89,405
GFRG w/o concrete work
Rs.5,85,305
Burnt brick
Rs.6,30,388
Laterite block
Rs.6,36,436
Concrete block
Rs.6,28,268
Table 2 GFRG Panel work cost Table 3 Cost vs. Material
-
Construction time period
The Construction time period graph shows that the building construction that takes the least amount of time is GFRG buildings as opposed to conventional building materials.
Figure 2 Construction Time Period Graph in days
-
Thermal comfort
According to the international standard EN ISO 7730, thermal comfort is: that condition of mind which expresses satisfaction with the thermal environment. It is the comfortable condition where a person is not feeling too hot or too cold. Thermal comfort is an effect resulting from environmental and personal factors. Environmental factors considered in this study include:
1.Air temperature 2. Air velocity 3. Relative humidity
The Indoor vs. Outdoor temperature graph shows that GFRG has a 2-degree temperature variation in comparison to other materials.
Average wind velocity comparison graph shows that GFRG has higher wind velocities or admits higher cooling effect to the structure as compared to other building materials. There may be variation in the data as wind speeds are subject to change in time and place. GFRG buildings have lower amounts of relative humidity as compared to other structures which
leads to better indoor environments. GFRG buildings have much lower internal temperatures as opposed to conventional building materials. They have a much higher temperature variation between indoors and outdoors which proves the thermal capacity of the material. GFRG buildings have much higher wind velocities in the structure, leading to ease of ventilation. They have a significant drop in relative humidity as compared to conventional building structures.
Figure 3 Indoor vs. Outdoor Temperature graph in deg. Celesius
Figure 4 Average wind velocities in m/s Table 4 Relative Humidity chart in percentage
-
Acoustics
Sound level comparison in GFRG buildings can be attributed to the fact that there are different methods for the construction of GFRG buildings- 1. Alternate infill of concrete or other material for structural reinforcement between gaps of the panel.
2. No infilling between panel voids or 3. Infilling of all cavities. The type that provides the most acoustic privacy is the structure that is fully infilled.
In the Indoor vs. Outdoor sound level graph between materials, Laterite proves to be the material that provides the most acoustic privacy. GFRG structures provide acoustic insulation only when the panels are infilled. Here, we can deduce that the conventional building materials provide more acoustic insulation as they have more mass.
Figure 5 Sound level comparison in Decibels
Figure 6 Indoor vs Outdoor Sound level in decibels
-
Weather resistance
Rainfall and water seepage is a common problem when it comes in the case of all building materials selected. The order of resistance includes:
1.GFRG 2. Laterite 3. Concrete block 4. Burnt brick
With GFRG being the most resistant and burnt bricks being least resistant.
Table 5 Weather resistance comparison of materials
-
Maintenance
Maintenance is necessary when it comes in the case of all building materials. The order of ease of maintenance include.
1.GFRG 2. Laterite 3. Burnt brick 4. Concrete block
With GFRG needing least maintenance and concrete blocks needing the most maintenance.
Table 6 Maintenance comparison of materials
-
Aesthetics and Customization
The likeability of a building lies in its aesthetic quality. The order of aesthetic quality include.
1.GFRG 2. Laterite 3. Burnt Bricks 4. Concrete block
With concrete block being the least aesthetic and GFRG being the most. The customization of a building defines the ability of the building material to undergo modifications like cutting and trimming to achieve an aesthetic quality. The order of ease of customization include.
1.Burnt Bricks 2. Laterite 3. Cement block 4. GFRG
With GFRG being least customizable and burnt bricks being the most.
Table 7 Aesthetic comparison of materials
REFERENCES
-
BMPTC. (2014). Technology Profile- Glass Fibre Reinforced Gypsum Panel building system. New Delhi: BMPTC.
-
BMTPC. (n.d.). Brick Masonry Walls. Retrieved from BMTPC: https://bmtpc.org/Topics.aspx?mid=356&type=sub
-
Bonnet, Juan Amedee. (1939, July). The nature of laterization as revealed by chemical, physical, and mineralogical-studies of a lateritic soil profile from puerto rico. Soil Science, 25-40.
-
Concrete Blocks. (n.d.). Retrieved from https://www.engineeringcivil.com/concrete-blocks-types-uses- advantages-disadvantages.html
-
Concrete Masonry. (2023). Retrieved from ncma.org: https://ncma.org/building-solutions/concrete-masonry/
-
Engelhardt, Richard A. (2009). New Directions for Archaeological Research on the Angkor Plain: The Use of Remote Sensing Technology for Research into Ancient Khmer Environmental EngineeringEngelhardt. UNESCO.
-
gcekbpatna. (n.d.). Lecture note on Burnt Bricks. Retrieved from https://gcekbpatna.ac.in/assets/documents/lecturenotes/unit-1.pdf
-
Indian Standard. (2005). Concerete Masonry Unit- Specification. New Delhi: Bureau of Indian Standards.
-
Indian Standard. (2008). Common Burnt Clay Building Brick. New Delhi: BUREAU OF INDIAN STANDARDS.
-
J.Desai. (n.d). Concrete Block As a Building Material.
-
MANISH KUMAR SAHU, L. S. (2017). CRITICAL REVIEW ON TYPES OF BRICKS TYPE 5: COMMON BURNT CLAY BRICKS.
International Journal of Mechanical And Production Engineering, ISSN: 2320-2092, Volume- 5, Issue-11.
-
Nisha Maklur, Dr. Parag Narkhede. (2018). Study of Laterite Stone as a Building material. International Journal of Engineering Research, Volume No.7, Issue Special 3, pp : 223-226.
-
Panigrahi, D. S. (n.d.). Lecture note on Civil engineering materials and construction.
-
Paramvisions. (n.d.). Retrieved from Paramvisions: https://www.paramvisions.com/2021/08/what-are-laterite-stone-blocks- their.html
-
Structural Engineering Division, Department of Civil Engineering, IIT Madras. (2018). GFRG/Rapidwall Construction Manual. Delhi: BMPTC.
-
Tardy,Yves. (1997). Petrology of Laterites and Tropical soils. ISBN 978-90-5410-678-4.
-
Veena, Bhargava. (n.d.). Textbook of Geogrpahy- Grade 10.
-
Welch, David. (2009). Archaelological Evidence of Khmer State Political and Economic Organisation. International Archaeological Research Institute.