
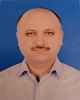
- Open Access
- Authors : Sanjay Koul
- Paper ID : IJERTV13IS090073
- Volume & Issue : Volume 13, Issue 09 (September 2024)
- Published (First Online): 04-10-2024
- ISSN (Online) : 2278-0181
- Publisher Name : IJERT
- License:
This work is licensed under a Creative Commons Attribution 4.0 International License
Comprehensive Overview of Current Transformer
Sanjay Koul,
Consultant Electrical Engineering Design
Abstract – This paper presents the fundamentals of Current transformer designed per ANSI/IEEE standards. Instrument transformers are part of Switchgear and Electrical Engineering Design Engineers depend mostly on Switchgear manufacturers to specify and select Current transformer. This paper has been prepared with Engineering Design Engineers in view to provide them sufficient information about Current transformer.
Keywords: Current Transformer, Knee point voltage, Instrument Transformer, Relay protection coordination, Power distribution system.
-
INTRODUCTION
Current transformer is designed to transform current from the high value in the electrical system to the low value for cost and safety reasons, suitable for metering instruments and standard protective relays and isolate the relays from line voltages.
CT has two windings, designated as primary and secondary, which are insulated from each other. The secondary is wound on an iron core. The primary winding is connected in series with the circuit carrying the line current to be measured; and the secondary winding is connected to protective devices, instruments, meters, or control devices. The secondary winding supplies a current in direct proportion and at a fixed relationship to the primary current.
The two main applications for which CTs are used are Metering for energy billing and Protection control for system protective relaying.
Depending on the requirements for those applications, the CT design and construction can be quite different. Generally, the metering CTs require high accuracy in the range of normal operating voltage and current. Protection CTs require linearity in a wide range of voltages and currents. During the disturbance, such as a system fault or over voltage transients, the output of the CT is used by a protective relay to initiate an appropriate action (open or close a breaker, reconfigure the system, etc.) to mitigate the disturbance and protect the rest of the power system.
The proper application of current transformers involves the consideration of several requirements, viz: design, type, construction, ratio, accuracy, burden, polarity, thermal rating, impulse level, connections & grounding.
Because of the volume of the Codes and Standards and details included in individual sections of these standards, it is difficult to cover all details. Only major parameters of Current transformers are covered in this paper for development of general understanding about Current Transformers.
-
DEFINITION
-
Continuous thermal current rating factor (RF)
The number by which the rated primary current of a current transformer is multiplied to obtain the maximum primary current that can be carried continuously without exceeding the limiting temperature rise from 30 degree C average ambient air temperature. The RF of tapped-secondary or multi-ratio transformers applies to the highest ratio, unless otherwise stated. (When current transformers are incorporated internally as parts of larger transformers or power circuit breakers, they shall meet allowable average winding and hot spot temperature limits under the specific conditions and requirements of the larger apparatus.)
-
Excitation losses for an instrument transformer
The power (usually expressed in watts) required to excite the transformer at its primary terminals. Excitation losses include core, dielectric, and winding losses due to the excitation current.
-
Phase angle correction factor (PACF)
The ratio of the true power factor to the measured power factor. It is a function of both the phase angles of the instrument transformer and the power factor of the primary circuit being measured. The phase angle correction factor is the factor that corrects for the phase displacement of the secondary current or voltage, or both, due to the instrument transformer phase angles. The measured watts or watthours in the secondary circuits of instrument transformers must be multiplied by the phase angle correction factor and the true ratio to obtain the true primary watts or watthours.
-
Phase angle of an instrument transformer (PA)
The phase displacement, in minutes, between the primary and secondary values. The phase angle of a current transformer is designated by the Greek letter beta ( ) and is positive when the current leaving the identified secondary terminal leads the current entering the identified primary terminal.
-
Ratio correction factor (RCF)
The ratio of the true ratio to the marked ratio. The primary current or voltage is equal to the secondary current or voltage multiplied by the marked ratio times the ratio correction factor.
-
Transformer correction factor (TCF)
The ratio of the true watts or watt-hours to the measured secondary watts or watt-hours, divided by the marked ratio.
The transformer correction factor for a current or voltage transformer is the ratio correction factor multiplied by the phase angle correction factor for a specified primary circuit power factor. The true primary watts or watt-hours are equal to the watts or watt-hours measured, multiplied by the transformer correction factor and the marked ratio. The true primary watts or watt-hours, when measured using both current and voltage transformers, are equal to the current transformer ratio correction factor multiplied by the voltage transformer ratio correction factor multiplied by the marked ratios of the current and voltage transformers multiplied by the observed watts or watt-hours. It is usually sufficiently accurate to calculate true watts or watt-hours as equal to the product of the two transformer correction factors multiplied by the marked ratios multiplied by the observed watts or watt-hours.
-
-
RATINGS
The terms in which ratings of a Current Transformer shall be specified are,
-
Continuous current rating
The maximum continuous-current rating should be equal to or greater than the rating of the circuit in which the CT is used. The magnitude of inrush current should also be considered, particularly with respect to its effect upon meters, relays, and other connected devices. For example, a 600:5 CT would be recommended for use on a circuit with a full-load current of 400 A.
-
Basic impulse insulation level (BIL)
BIL is a specific insulation level expressed in kilovolts of the crest value of a standard lightning impulse. Refer Table-1 of this Paper.
-
Nominal system voltage or maximum system voltage
CTs are typically designed to operate continuously at 10% above rated nominal system voltage. Standard nominal system voltages for most industrial applications are 480 V, 600 V, 2400 V, 4160 V, 12 470 V, 13 800 V, and 14 400 V. It is
common practice to apply window CTs rated 600 V to systems with higher voltages. This practice is done by passing fully insulated conductors through the window. The conductor insulation functions as the CT primary insulation providing a fully rated installation.
-
Rated frequency
Specified frequency per ANSI/IEEE is 60 Hz only.
-
Accuracy classes at standard burdens Refer Section VII of this paper.
-
Short-time mechanical current rating
The short-time mechanical rating is the maximum current the CT is capable of withstanding without damage with the secondary short-circuited. It is the rms value of the ac component of a completely displaced (asymmetrical) primary current wave.
When the primary circuit is protected by current-limiting fuses, the current transformers shall successfully withstand the maximum let-through current of the fuses. Unless specifically limited to a shorter time by the associated protective equipment, the duration of the momentary current shall be considered as being 10 cycles.
-
Short-time thermal current rating
The short-time thermal rating is the symmetrical root mean- square (rms) primary current that the CT can carry for 1 s with the secondary winding short-circuited, without exceeding the limiting temperature in any winding.
When the primary circuit is protected by current-limiting fuses, the current transformers shall successfully withstand the maximum let-through current of the fuses. Unless specifically limited to a shorter time by the associated protective equipment, the duration of the short circuit current shall be considered as 1s.
The limiting temperature shall be 250 degree C for copper conductor, or 200 degree C for EC aluminum conductor. A maximum temperature of 250 degree C shall be allowed for aluminum alloys that have resistance to annealing properties at 250 degree C equivalent to EC aluminum at 200 degree C, or for applications of EC aluminum where the characteristics of the fully annealed material satisfy the mechanical requirements.
Table 1- Basic impulse insulation levels and dielectric tests
Maximum System
voltage (kV)
Nominal System
voltage (kV)
BIL & full wave crest
(kV)
0.66
0.6
10
1.20
1.20
30
2.75
2.40
45
5.60
5.00
60
9.52
8.70
75
15.50
15.00
95
15.50
15.00
110
25.50
25.00
125
25.50
25.00
150
36.50
34.50
200
48.30
46.00
250
72.50
69.00
350
121.00
115.00
450
121.00
115.00
550
145.00
138.00
650
169.00
161.00
750
242.00
230.00
900
242.00
230.00
1050
362.00
345.00
1300
550.00
500.00
1675
550.00
500.00
1800
800.00
765.00
2050
-
Continuous thermal current rating factor
The continuous-thermal-current rating factor is supplied by the
CT manufacturer. It identifies the amount of current that can be carried continuously without exceeding the limiting temperature rise from 30°C ambient air temperature. The continuous current is multiplied by the rating factor to determine the maximum current. (When a CT is incorporated internally as part of a larger transformer or power circuit breaker, it shall meet allowable average winding and hot-spot temperature limits under specific conditions of the larger apparatus.) The rating factors are 1.0, 1.33, 1.5, 2.0, 3.0,
or 4.0: for example, a 100:5 CT with a rating factor equal to
1.5 may be operated up to current levels of 150:7.5 (150 A primary current: 7.5 A secondary current).
The secondary devices should be checked for continuous load capability before a CT is operated above 5 A secondary current. Damage can occur in meters and relays if operated above their limits.
-
Short- time and continuous current ratings of window-type or bushings-type current transformers
Such current transformers, in which the primary conductor is not an integral part of the current transformers, shall be rated in terms of primary current, even though the short-time mechanical and thermal limitations and the continuous thermal limitations arc those of the secondary winding only. Such ratings specified for current transformers of this construction should not be considered to be applicable to the conductor used for the primary winding of these transformers, as such conductor may be a component of other apparatus or bus work having different limitations.
-
-
TYPE
-
Wound Current transformer
A wound CT has a primary winding consisting of one or more turns mechanically encircling the core or cores. The primary and secondary windings are insulated from each other and from the core(s) and are assembled as an integral structure.
-
Bar Current transformer
A bar CT has a fixed, insulated, straight conductor in the form of a bar, rod, or tube that is a single primary turn passing through the magnetic circuit and is assembled to the secondary, core and winding.
-
Window Current transformer
A window CT has a secondary winding insulated from and permanently assembled on the core, but has no primary winding as an integral part of the structure. Primary insulation is provided in the window through which one or more turns of the line conductor can be passed to provide the primary winding
-
Bushing Current transformer
A bushing CT has an annular core and a secondary winding insulated from and permanently assembled on the core, but has no primary winding or insulation for a primary winding. This type of CT is used with a fully
insulated conductor as the primary winding and used typically in equipment where the primary conductor is a component part of other apparatus, for example, on bushings of a transformer or circuit breaker. The secondary windings of bushing CTs are usually fully distributed around the core. Typically they are multi ratio with each winding tap also being fully distributed.
-
-
RATIO
CT ratios are expressed as a ratio of the rated primary current to the rated secondary current. The standard rated secondary current in all instances is 5 A as a standard.
In general, CT ratios are selected to match the maximum load current requirements, i.e., the maximum design load current should not exceed the CT rated primary current.
For example, a 600:5 CT will produce 5 amps of secondary current when 600 amps flows through the primary. As the primary current changes the secondary current will vary accordingly. With 300 amps through the 600 amp rated primary, the secondary current will be 2.5 amps (300:600 = 2.5:5). When the rated primary amps is exceeded, which is usually the case when a fault occurs on the system, the amount of secondary current will increase but, depending on the magnetic saturation in the CT, the output may not be exactly proportional.
Table 2- CT ratings with one or two ratios
Current ratings (A)
Single ratio
Double ratio with series parallel primary
windings
Double ratio with taps in secondary
winding
10:5
800:5
25 x 50:5
25/50:5
15:5
1200:5
50 x 100:5
50/100:5
25:5
1500:5
100 x 200:5
100/200:5
40:5
2000:5
200 x 400:5
200/400:5
50:5
3000:5
400 x 800:5
300/600:5
75:5
4000:5
600 x 1200:5
400/800:5
100:5
5000:5
1000 x 2000:5
600/1200:5
200:5
6000:5
2000 x 4000:5
1000/2000:5
200:5
8000:5
1500/3000:5
400:5
12000:5
2000/4000:5
600:5
IJERTV13IS090073
(This work is licensed under a Creative Commons Attribution 4.0 International License.)
Table 3 -Current transformer ratings, multi-ratio type
Current Ratings (A)
Secondary taps
Curren t Rating
s (A)
Secondary taps
600:5
50:5
X2-X3
3000:5
300:5
X3-X4
100:5
X1-X2
500:5
X4-X5
150:5
X1-X3
800:5
X3-X5
200:5
X4-X5
1000:5
X1-X2
250:5
X3-X4
1200:5
X2-X3
300:5
X2-X4
1500:5
X2-X4
400:5
X1-X4
2000:5
X2-X5
450:5
X3-X5
2200:5
X1-X3
500:5
X2-X5
2500:5
X1-X4
600:5
X1-X5
3000:5
X1-X5
1200:5
100:5
X2-X3
4000:5
500:5
X1-X2
200:5
X1-X2
1000:5
X3-X4
300:5
X1-X3
1500:5
X2-X3
400:5
X4-X5
2000:5
X1-X3
500:5
X3-X4
2500:5
X2-X4
600:5
X2-X4
3000:5
X1-X4
800:5
X1-X4
3500:5
X2-X5
900:5
X3-X5
4000:5
X1-X5
1000:5
X2-X5
500:5
X1-X2
1200:5
X1-X5
1000:5
X3-X4
2000:5
300:5
X3-X4
5000:5
500:5
X2-X3
400:5
X1-X2
1000:5
X4-X5
500:5
X4-X5
1500:5
X1-X2
800:5
X2-X3
2000:5
X3-X4
1100:5
X2-X4
2500:5
X2-X4
1200:5
X1-X3
3000:5
X3-X5
1500:5
X1-X4
3500:5
X2-X5
1600:5
X2-X5
4000:5
X1-X4
2000:5
X1-X5
5000:5
X1-X5
-
BURDEN
Table-4: Standard burdens for CTs with 5 A secondarys.
Burden designatio n
R
(ohm)
Inducta nce (mH)
Impeda nce (ohm)
VA
(at
5A)
PF
Metering burdens
B-0.1
0.09
0.116
0.1
2.5
0.9
B-0.2
0.18
0.232
0.2
5.0
0.9
B-0.5
0.45
0.580
0.5
12.5
0.9
B-0.9
0.81
1.04
0.9
22.5
0.9
B-1.8
1.62
2.08
1.8
45
0.9
Relaying burdens
B-1
0.5
2.3
1.0
25
0.5
B-2
1.0
4.6
2.0
50
0.5
B-4
2.0
9.2
4.0
100
0.5
B-8
4.0
18.4
8.0
200
0.5
Since Power = I2xR, for 5 A secondary CT with burden designation B-0.1, burden = 52 x 0.1 = 2.5 ohm (burden).
If a current transformer secondary winding is rated at other than 5 A, ohmic burdens for specification and rating shall be derived by multiplying the resistance and inductance of the table [5/(ampere rating)]2 the VA at rated current, the power factor, and the burden designation remaining the same.
These standard burden designations have no significance at frequencies other than 60 Hz.
In the process of CT selection we are interested in minimizing the total burden that consists of the internal resistance of the CT winding itself, the resistance of the leads from the CT to the relay including the return path, and the burden of the connected relays.
Higher ohmic burdens in the CT secondary circuit will tend to result in greater saturation of the core, and therefore, larger errors in the secondary current waveform. The reason for this is that a given secondary current requires more voltage from the CT for a higher burden, and the core flux density is proportional to the time-integral of this voltage. When the core becomes saturated, significant current is diverted through the CTs magnetizing branch, and the desired secondary current is reduced and distorted. Burden calculations are, therefore, necessary to ensure that CT accuracy limits are not exceeded. Higher ratio CTs (3000:5) contribute a resistance of 0.0025 ohms per turn to the burden and lower ratios (300:5) 0.005 ohms per turn. Consequently, applying a 600 turn (3000:5) CT
Burden, in CT terminology, is the load connected to the secondary terminals and is expressed as Volt-amperes.
The total ohmic burden on the CT is te vector sum of the CT winding resistance, the connecting lead resistance, the impedance of any auxiliary CTs, and the impedance of the connected relays and meters.
contributes an internal resistance of 1.5 ohms. In new installations we can choose the wire size to control the resistance for a circuit run. For example, the log of resistance per 1000 feet of wire is proportional to the AWG gage of the wire. A benchmark for copper wire is 0.9989 ohms/1000 feet for #10 gage AWG wire. Decreasing the gage by 3 numbers halves the resistance and increasing it by 3 doubles the resistance.
A good practice is to size the leads to limit the lead resistance to 0.5 ohms or less. Under this rule, #10 wire would be the choice if the CTs were located 250 feet from the relays for a total run of 500 feet to and from the CTs.
IJERTV13IS090073
(This work is licensed under a Creative Commons Attribution 4.0 International License.)
-
ACCURACY
Protective-relay performance depends on the accuracy of the CTs not only at load currents, but also at all fault current levels. Accuracy can be visualized as how closely the secondary wave shape resembles the primary wave shape. Wave shape and phase difference are both components of the accuracy classification.
The CT accuracy at high over-currents depends on the cross section of the iron core and the number of turns in the secondary winding. The greater the cross section of the iron core, the more flux can be developed before saturation. Saturation results in a rapid decrease in transformation accuracy. The greater the number of secondary turns, the less flux that is required to force the secondary current through the relay. This factor influences the burden the CT can carry without loss of accuracy.
Table 5- Standard accuracy class ratings Current transformers
Metering Accuracy at 60 Hz Standard burden
Ratio
B-
0.1
B-
0.2
B-
0.5
B-0.9
B-
1.8
Relaying Accuracy
50:5
1.2
2.4
–
–
–
C or T 10
75:5
1.2
2.4
–
–
–
C or T 10
100:5
1.2
2.4
–
–
–
C or T 10
150:5
0.6
1.2
2.4
–
–
C or T 20
200:5
0.6
1.2
2.4
–
–
C or T 20
300:5
0.6
1.2
2.4
2.4
–
C or T 20
400:5
0.3
0.6
1.2
1.2
2.4
C or T 50
600:5
0.3
0.3
0.3
1.2
2.4
C or T 50
800:5
0.3
0.3
0.3
0.6
1.2
C or T 50
1200:5
0.3
0.3
0.3
0.3
0.3
C 100
1500:5
0.3
0.3
0.3
0.3
0.3
C 100
2000:5
0.3
0.3
0.3
0.3
0.3
C 100
3000:5
0.3
0.3
0.3
0.3
0.3
C 100
4000:5
0.3
0.3
0.3
0.3
0.3
C 100
-
Accuracy classes for metering
A current transformer for metering shall be given an accuracy rating for each standard burden for which it is rated. For accuracy ratings assigned to a current transformer refer Table 5 of this paper. For example, 0.3 B 0.2 stands for +/- 0.3 as max. ratio error, B as burden and 0.2 as ohms (burden).
-
Accuracy classes for relaying
Relaying accuracy ratings shall be designated by a classification and a secondary terminal voltage rating as follows:
C: indicates that the leakage flux is negligible and the excitation characteristic can be used directly to determine performance. The CT ratio error can thus be calculated. It is assumed that the burden and excitation currents are in phase and that the secondary winding is distributed uniformly.
K: is the same as the C rating, but the knee-point voltage must be at least 70% of the secondary Terminal voltage rating.
T: indicates that ratio error must be determined by test. The T class CT has an appreciable core flux leakage effect and
contributes to appreciable ratio error.
The classification number indicates the secondary terminal voltage that the transformer delivers to a standard burden (as listed in Table 4 of this paper) at 20 times normal secondary current without exceeding a 10% ratio correction. The ratio correction should not exceed 10% at any current from 1 to 20 times rated current at standard burden. The standard designated secondary terminal voltages are 10 V, 20 V, 50 V, 100 V, 200 V, 400 V, and 800 V.
Secondary terminal voltage ratings are based on a rated secondary current of 5 A (100 A at 20 times rated) and standard burdens. The voltage ratings and their associated burdens are as follows:
Table 6- Secondary Terminal Voltage
Secondary terminal voltage
Standard burden
10
B-0.1
20
B-0.2
50
B-0.5
100
B-1
200
B-2
400
B-4
800
B-8
For example, 10C200 stands for 10% max. ratio error at 20 times rated current, C stands for low leakage unit and 200 stands for max. secondary voltage developed at 20 times rated current at a standard burden of 2.0 ohms (B-2) without exceeding the + 10% ratio error (Maximum terminal voltage = 20 x 5 A x 2 ohm = 200 V).
For example, if the rated secondary current is 1 A, the burden corresponding to B-2.0 will be 2.0 x 25, or 50 ohm (at 0.5 power factor); and the corresponding secondary terminal voltage rating will be 50 x 20 x 1 = 1000 V. In this example, the relay accuracy rating would be C1000, K1000, or T1000 as applicable.
-
-
POLARITY & TERMINAL MARKING
Polarity marks designate the relative instantaneous directions of currents. At the same instant that the primary current is entering the marked primary terminal, the corresponding secondary current is leaving the similarly marked secondary terminal, having undergone a magnitude change within the transformer.
Figure 1 – CT polarity diagram
The primary H1 and secondary X1 (also Y and Z, etc., if multiple secondary windings are provided) terminals are marked with white dots, or with a +/- symbol, or with H1 and X1.
When multiple primary windings are provided, the leads or terminals shall be designated by the letter H together with consecutive pairs of numbers (H1, H2, H3, H4, etc.). The odd- numbered leads or terminals shall be of the same polarity.
XIV. PERFORMANCE CHARACTERISTICS
-
Current transformer equivalent circuit
The specific performance characteristics of current transformers are most easily determined from the equivalent circuit.
Figure 3 shows a simplified equivalent circuit of a CT and its connected burden. The primary leakage impedance and the reactive part of the secondary leads do not substantially affect calculations and are, therefore, neglected.
Figure 2 – Equivalent Circuit of a Current transformer
VS is the secondary exciting voltage
VB is the CT terminal voltage across external burden IP is the primary current
ZE is the exciting impedance
IST is the total secondary current RS is the secondary resistance IS is the secondary load current
XL is the leakage reactance (negligible in Class C CTs) IE is the exciting current
N2:N1 is the CT turn ratio
ZB is the burden impedance (includes secondary devices and leads)
-
Phasor diagram of a current transformer with burden
To construct the phasor diagram for a CT, the procedure is as follows:
-
Start with the secondary load current IS
-
Draw the secondary volt drops: IS x RS and IS x XL
-
Add VB to the resultant voltage in order to obtain the internal secondary exciting voltage VS
-
When VS has been obtained, draw the flux phasor lagging VS by 90 degree.
The exciting current, IE, is composed of the magnetizing current, IM, which is needed to generate the flux in the CT core, and the loss current, ILOSS, which is mainly due to the hysteresis and eddy current losses.
-
Draw the magnetizing current, IM, in quadrature with the voltage and the resistive loss current, ILOSS, in phase with the secondary exciting voltage
IM + I LOSS = I E
IST = I S + I E
The primary current is then
where, N2/N1 the turns ratio
Figure 3 – Phasor diagram of a current transformer with a resistive burden (power factor of 1.0)
Figure 4 – Phasor diagram of a current transformer with a standard burden (0.5 power factor)
-
-
Fundamental transformer equation The fundamental transformer equation is
V / N = Bm Af / 22.51 x 10 2
Where,
V/N is the volts per turn, which is the same in both windings
Bm is the maximum flux density in the core (tesla)
A is the effective cross sectional area of the core, cm 2
f is the frequency (Hz)
The ideal CT operates with an ampere-turn balance such that where,
N1IP = N2 IS
Where,
N1 is the number of primary turns
N2 is the number of secondary turns
However, exciting current is needed to generate the flux, which produces the secondary voltage. This will produce a ratio error that is sometimes corrected by putting fewer turns on the core than the equation above demands. The extra secondary current compensates for the exciting current. The formula is useful for estimating the cross sectional area where the volts per turn are proportional to the area of the core. Application of the fundamental transformer equation requires the use of information on CT iron flux density characteristics and cross sectional area.
-
Secondary Excitation Characteristics and Over Current Curves
When the voltage developed across the CT burden is low, the exciting current is low. The waveform of the secondary current will contain no appreciable distortion. As the voltage across the CT secondary winding increases because either the current or the burden is increased, the flux in the CT core will also increase. Eventually the CT will operate in the region where there is a disproportionate increase in exciting current. The CT core is entering the magnetically saturated region; operation beyond this point will result in an increasing ratio error and a distorted secondary current waveform.
-
Knee-Point Voltager
The knee-point voltage of a CT with a non-gapped core is defined as the point of maximum permeability on the excitation curve, plotted on log-log axes with square decades, where the tangent to the curve makes a 45 degree angle with the abscissa. This is shown in Figure 6 of this Paper and gives a knee-point for the 1200/5 A winding of about 240 V.
When the CT has a gapped core, the definition of the knee- point voltage is the point where the tangent to the curve makes an angle of 30 degree with the abscissa.
-
SAFETY PRECAUTIONS
An important precaution with respect to CTs is that they should never be operated with the secondary circuit open because hazardous voltages may result. Any CT that has been subjected to open secondary circuit operation should be examined for possible damage before being placed back in service. A voltage-limiting device may be installed to reduce the hazards of open secondary circuits.
Transformers conforming to ANSI/IEEE standard shall be capable of operating under emergency conditions for 1 minute with rated primary current times the rating factor with the secondary circuit open if the open-circuit voltage does not exceed 3500 V crest.
-
SATURATION
Abnormally high primary fault currents, primary fault currents having a dc offset, residual flux, high secondary burden, or a
combination of these factors results in the creation of high flux density in the CT iron core. When this density reaches or exceeds the design limits of the core, saturation results. At this point, the accuracy of the CT becomes poor, and the output waveform may be distorted by harmonics. Saturation results in the production of a secondary current lower in magnitude than would be indicated by the CT ratio.
For example, selective coordination of protective devices may not occur if CTs on a branch circuit saturate. Tripping of the branch circuit breaker may be delayed or may not even occur.
A. Minimizing the effects of current transformer saturation
A rule of thumb frequently used in relaying to minimize the CT saturation effects is to select a CT with a C voltage rating at least twice that required for the maximum steady-state symmetrical fault current.
When metering instruments are used on the same CTs as relays, the CT ratio should be sized for the relay needs and auxiliary CT used to bring the metering ratio to the desired value. The metering circuit burden is reflected through the auxiliary CT by the square of the turns ratio and added to the auxiliary CT burden. Both are minimized by selecting an auxiliary CT that will saturate at several times the maximum load current. This will minimize the metering burden on the main CTs under heavy fault current. It also reduces the likelihood of the meters being damaged during a severe fault. Damage can occur when the CTs have ratios suitable for meters and the CT C voltage rating has been chosen for relaying.
To avoid or minimize saturation effects, the secondary burden should be kept as low as possible. Where fault currents of more than 20 times the CT nameplate rating are anticipated, a different CT, different CT ratio, or a lower burden may be required.
-
EFFECTS OF REMANENCE
The remanent flux in a CT core depends on the flux in the core immediately before primary current interruption. The magnitude of the flux is determined by the value of symmetrical primary current, the dc offset, and the impedance of the secondary circuit. Maximum remanent flux is obtained when the primary current is interrupted while the transformer is in a saturated state. In addition, testing that requires dc to flow in the transformer winding will cause remanence.
Once remanent flux is established, it is dissipated very little under service conditions. A voltage of about 60% of the knee- point voltage shall be applied to reduce the remanence to less than 10% of saturation flux density. The remanent flux will, therefore, remain in the core until it is demagnetized.
-
Output of a CT with remanence
When the ramanent flux is of the opposite polarity to the flux due to the transient component of the fault current, the CT tends to produce an undistorted secondary current. If the remanent flux is of the same polarity as the flux due to the transient component of the fault current, then a distorted secondary waveform is probable.
-
Reducing remanence in CTs
The only way of reducing remanence in CT cores that are presently in service is to demagnetize them by external means. Such demagnetization can be performed using power frequency voltage. With the primary winding open circuited, a source of variable voltage is connected across the secondary winding and increased until the core starts to enter the saturated region. This point can be detected by observing the disproportionate increase in exciting current. Reduction of the voltage to zero over a period of about 3 s will demagnetize the core. A CT in service and carrying load may be demagnetized by inserting a variable resistor in the secondary circuit, increasing its resistance to achieve core saturation, and then reducing the resistance to zero.
-
-
AUXILIARY CURRENT TRANSFORMERS
Auxiliary CTs are used for the following reasons,
-
Circuit isolation to permit independent grounding,
-
Change in ratio to match current requirements,
-
To produce a phase shift in a three phase circuit,
-
To reverse polarity,
-
To limit main CT fault burden by saturating during faults,
-
To reduce the burden on the main CT by reducing the apparent impedance of a portion of the burden by the square of the auxiliary ct ratio,
-
Zero sequence shunt or trap
The auxiliary CT should be selected with an adequate continuous current rating and voltage capability for the requirements of its connected burden. The apparent impedance to the main CT of the portion of the burden in the secondary of the auxiliary CT is that portion multiplied by the square of the auxiliary CT ratio. For example, a 1.0 ohm burden in the secondary of a 2:1 auxiliary CT would appear as 0.25 ohm to the main CT, but would appear as 4.0 ohm for a 1:2 auxiliary CT. For this reason, current step-up applications should be avoided when practical.
-
-
TERMINALS
Primary terminals of wound-type and bar-type current transformers shall be suitable for use with either aluminum or copper conductors. Secondary terminals and voltage terminals, where provided, shall be suitable for use with copper conductors.
-
NAMEPLATES
Nameplates shall include, as a minimum, the following:
-
Manufacturer's name or trademark
-
Manufacturer's type
-
Manufacturer's serial number (SER)
-
Rated primary and secondary current
-
Nominal system voltage (NSV) or maximum system voltage (MSV) (None for bushing CTs)
-
Basic impulse insulation level (BIL kV) (None for bushing CTs)
-
Rated frequency (Hz)
-
Continuous thermal current rating factor (RF)
-
Accuracy rating
-
Metering accuracy class at a specified standard burdens: as a minimum, the burdens at which the transformer is rated 0.3 accuracy class
-
Relaying accuracy rating on transformers intended primarily for relaying applications
-
-
-
GROUNDING
-
Single Point Ground Connection in the Secondary Circuit
The reasons for making this ground connection only at a single point in each circuit are as follows:
-
To prevent differences of potential in the instrument transformer secondary circuit because of differences of potential between different points in the station ground grid. These differences are caused by the flow of fault current through the ground grid. Such differences of potential can result in the flow of current through the relay, instrument, and meter coils and cause possible incorrect performance of the relay and inaccuracies in the readings of the instruments and meters. High neutral conductor currents resulting from multiple ground connections to the neutral can cause thermal damage to the neutral conductor.
-
To facilitate the temporary removal and reestablishment of the ground connection, when desired, in order to make periodic tests for deterioration of insulation and accidental grounds in the instrument transformer secondary circuit.
-
-
Location and Making of Connection to Ground
Instrument transformer secondary circuits have been connected to ground at the instrument transformer location and at the secondary burden location (and sometimes at both locations), limiting the voltage stresses primarily to the instrument transformer secondary windings. However, secondary burden devices at the switchboard, which may be several hundred or even several thousand feet from the instrument transformer location, could be subjected to significant over-voltages during power system short circuits to ground. Also, test and operating personnel are more apt to be working at the switchboard than at the transformer location. Consequently, it is common practice to locate the instrument transformer secondary circuit ground at the first switchboard. This provides the maximum practical protection to personnel and secondary circuit connected equipment. This location also conveniently facilitates the testing requirements.
For unused instrument transformer secondary windings, the connection to the station ground bus may be made at the transformer location or at the switchboard, if the secondary circuit of the unused winding has been extended to the switchboard.
-
Minimum Size of Conductor for Ground Connection
The grounding conductor and secondary neutral bus, or both, should be conductors as large or larger than the secondary phase conductors. If made of copper, they should never be smaller than No. 12 AWG wire, for mechanical reasons. If made of other metal, they should have equal conductance, strength and current carrying capacity.
-
Unused Current Transformers
Current transformers that are unused should have the full winding shorted at the CT location and should be grounded.
-
-
TESTS
-
Routine tests
Applied voltage dielectric tests between windings and between windings and ground (with the exception there is no primary insulation test for bushing type, split-core, or any current transformer designed with incomplete insulation for the primary conductor), Induced voltage tests, Accuracy tests and Polarity test
-
Type test
Impulse (BIL) test, Wet 60 Hz 10 s withstand test, Short-time mechanical current rating test, Temperature rise test to verify the thermal burden rating, Accuracy test to verify quoted accuracy ratings and Switching impulse test.
-
Other tests
Other tests are additional tests made for application information, for provision of specific data requested by users, for verification of type capability, etc. Examples of other tests are Special accuracy tests, Open-circuit secondary voltage magnitude or withstand capability on current transformers, Radio influence voltage test (RIV) and Partial discharge test.
-
-
FIELD TESTING
-
Insulation Resistance tests
Insulation resistance between the current transformer secondary and ground is usually checked by the use of conventional insulation test instruments. The neutral ground must be removed and the current transformer preferably isolated from its burden for this test.
The resistance should be compared with those of similar devices or circuits. Readings lower than those known to be good should be carefully investigated. The generally accepted minimum insulation resistance is 1 M ohm. One of the most common reasons for low readings is the presence of moisture. Drying out the equipment and retesting should be considered before it is dismantled.
-
Ratio Tests
There are two generally accepted methods of checking the tums ratio of all types of current transformers.
-
Voltage Method: A suitable voltage, below saturation, is applied to the secondary (full winding), and the primary voltage is read with a high-impedance (20 000 ohm /V or greater) low-range voltmeter. The turns ratio is approximately equal to the voltage ratio.
At the same time the overall ratio is being determined, the tap section ratios may be checked with a voltmeter by comparing tap section voltage with the impressed voltage across the full winding. An ammeter is included in the recommended test method as a means of detecting excessive excitation current.
-
Current Method: This method of determining the turns ratio requires a source of high current, an additional current transformer of known ratio with its own ammeter, and a second ammeter for the transformer under test. Any other current transformers that may be in series with the transformer under test should be short circuited and possibly disconnected from their burdens if damage to other meters or relays, or accidental tripping, is likely. This method is not practical for current transformers in an assembled power transformer or generator.
The test is performed by adjusting the high-current test source to a series of values over the desired range and recording the two secondary currents. The ratio of the transformer under test is equal to the tums ratio of the reference transformer multiplied by the ratio of the reference transformer secondary current to the test transformer secondary current:
-
-
Polarity Check
There are three generally accepted methods of checking current transformer polarity.
-
DC Voltage Test: In this test, a 6 to 10 V lantern-type battery is connected momentarily to the secondary of the transformer under test and the momentary deflection of a milliammeter or millivoltmeter connected to the primary noted. If the positive terminal of the battery is connected to terminal X1 and the positive terminal of the milliammeter is connected to terminal H1, as shown in Fig 6, the deflection will be upscale when the battery is connected and downscale when it is disconnected, if the polarity is in accordance with terminal markings. This test is also valid with the battery applied to the primary and the meter connected to the secondary. It is advisable to demagnetize any current transformer that is tested by impressing dc voltage across a winding.
-
AC Voltage Test Oscilloscope: An oscilloscope can be used to check current transformer polarity. The method used is to apply an ac voltage to the secondary winding and compare it with the voltage induced in the primary winding.
-
Current Method: Polarity can be conveniently checked by paralleling the reference current transformer secondary with the test transformer secondary through two ammeters. If A2 ammeter is reading higher than A1, the polarity is in accordance with terminal markings.
-
-
Winding and Lead Resistance (Internal Resistance)
The internal winding and lead resistance can be measured with a resistance bridge. Usually, it is sufficient to use the average value of resistance of the current transformers in the three phases for calculations. If it is desired to separate lead resistance and winding resistance to provide data for other calculations, the resistance of the full winding and of a tap should be measured. Assuming all tums are of equal resistance, the per-turn resistance and lead resistance can be calculated. All measurements should be made at the current- transformer short-circuiting terminal block. Because of possible remanence, the current transformer should be demagnetized after completion of this test. Proper safety precautions should be taken when connecting and disconnecting the bridge because of potentially dangerous spike voltages.
-
Excitation test
Before the excitation test is made, the current transformer should be demagnetized. To perform the test, an ac test voltage is applied to the secondary winding with the primary open circuited. The voltage applied to the secondary of the current transformer is varied, and the current drawn by the winding at each selected value of voltage is recorded. The ammeter should be an rms instrument. The voltmeter should be an average reading voltmeter across a full-wave rectifier.
Deviation from expected results may indicate a turn-to-turn short circuit, distortion of test supply voltage waveform, or the presence of a completed conducting path around the current transformer core.
This test can also be performed by energizing the current transformer primary from a high-current test source and plotting primary exciting current versus secondary open- circuit voltage. The current must be divided by the current transformer ratio in order to compare this data with Fig 10.
-
Burden Measurement
The total burden of the circuit, which is the sum of the internal current transformer burden and the external connected burden, must be determined.
The internal burden is the resistance of the secondary winding plus the lead resistance from the winding to the short- circuiting terminal block converted to volt-amperes at rated secondary current.
The external connected burden can either be calculated or measured. To determine the external connected burden in volt- amperes, measure the voltage required to drive rated current through the connected burden. If both resistive and reactive components of the burden are desired, a suitable phase-angle meter can be connected.
Burden measurements, when compared with calculated values, help to confirm circuit wiring and satisfactory contact resistances of terminal blocks and test devices.
-
-
CONCLUSION
Almost all major specifications of Current transformers have been discussed per ANSI/IEEE for the understanding and use of engineering design engineer.
-
REFERENCES
-
IEEE C57.13-2016: IEEE Standard Requirements for Instrument Transformers.
-
IEEE C57.13.1-2017: IEEE Guide for Field Testing for Relaying Current Transformers.
-
IEEE C57.13.3-2014: IEEE Guide for the Grounding of Instrument Transformer Secondary Circuits and Cases.
-
IEEE C37.110-2023: IEEE Guide for the Application of Current Transformers Used for Protective Relaying Purposes.
-
M. Davari, V. Dinavahi Current Transformer Saturation Compensation Using Kalman Filtering, IEEE Transactions on Power Systems, 2011.
-
M. Goodfellow, D. Walton Fault Performance of Medium Voltage Current Transformers, Springer, 2011.
-
F. Wei, J. Liu Accuracy and Stabilityof Current Transformers Under Varying Load Conditions, MDPI Energies, 2018.
-
L. Silva, R. Souza Performance of Current Transformers in Distributed Generation Systems, Elsevier Energy, 2015.
-
S. Koronowski, P. Musilek High-Accuracy Current Transformers for Critical Power Applications, IEEE Transactions on Power Systems, 2017.
-
J. Menendez, A. Larrain Current Transformer Saturation in Digital Relay Systems, Springer Electrical Engineering, 2010.
-
A. Stankovic, M. Sehic Comparative Analysis of Current Transformers in Industrial Power Systems, IEEE Transactions on Industry Applications, 2016.
IJERTV13IS090073
(This work is licensed under a Creative Commons Attribution 4.0 International License.)