
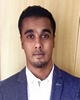
- Open Access
- Authors : Karthik M S, Manish Rao T J, Harsha A N, Vishnu R, Vachanashree H S
- Paper ID : IJERTV12IS080049
- Volume & Issue : Volume 12, Issue 08 (August 2023)
- Published (First Online): 26-08-2023
- ISSN (Online) : 2278-0181
- Publisher Name : IJERT
- License:
This work is licensed under a Creative Commons Attribution 4.0 International License
Computational Analysis on Flat and Spiral Pulsating Heat Pipes
Karthik M S 1
Assistant professor
Dept. of Mechanical Engineering SJCE, JSSS&TU
Mysore, India
Manish Rao T J2, Harsha A N3, Vishnu R4, Vachanashree H S5 Students, Bachelor of Engineering
Dept. of Mechanical Engineering
SJCE, JSSS&TU
Mysore, India
Abstract Pulsating heat pipes are new two-phase heat transfer devices that rely on the oscillatory flow of liquid and vapor plug in a long miniature tube bent into many turns. The unique thermal properties and flexible design of pulsating heat pipes offer opportunities for relatively lightweight, low cost and reliable phase change of fluid analysis. ANSYS fluent software is used to apply numerical procedure in coupled system of standard levels. Numerical method is known to perform very well over a wide range of fluids, heat inputs, materials. Numerical analysis of passive two-phase fluid flow in a 3D Closed Loop Pulsating Heat pipe is carried out; Water is used as working fluid. Filling ratio (FR) of is kept in the range of 50 to 50%. The evaporator temperature is set in the range of 353 K. The condenser temperature is set in the range of 298 K. The contours of volume fraction water, wall temperature and contours of mass flow rate is studied. Analysis of fluid flow is done with various geometrical parameter for 3D Closed Loop Pulsating Heat Pipe. Liquid and vapor slug formation are observed and evaporation and condensation process are visualized in the analysis. The aim of the numerical analysis is to find the suitable working fluid, models, simulation settings that accurately predict the phase change phenomenon and to investigate the effect of liquid vapor slug flow, changing simulation parameters on the performance of pulsating heat pipes.
Keywords Heat pipe, Computational fluid dynamics, Flat and Spiral Pulsating Heat Pipe, Volume fraction.
I. INTRODUCTION
The Heat pipe is a device, which is capable of transferring large quantities of heat with minimum temperature drop. The heat pipe is capable of transferring large quantities of heat with minimum temperature drop. When one end of the heat pipe is heated, the working fluid inside the pipe at that end vaporizes and increases the vapor pressure inside the cavity of the heat pipe. The latent heat of vaporization absorbed by the working fluid reduces the temperature at the hot end of the pipe. The vapor pressure over the hot liquid working fluid at the hot end of the pipe is higher than the equilibrium vapor pressure over the condensing working fluid at the cooler end of the pipe, and this pressure difference drives a rapid mass transfer to the condensing end where the excess vapor condenses, releases its latent heat, and warms the cool end of the pipe. With the size of electronics devices shrinking day by day there need to implement effective cooling technique which will cool the electronics devices without compromising on the performance, to achieve this goal heat pipe technology looks promising.
FIG-1: Heat Pipe
Heat Pipe For quick heat transfer Pulsating heat pipes are introduced. Pulsating heat pipe is only partially filled with liquid working fluid. The pipe is arranged in a serpentine pattern in which freely moving liquid and vapor segments alternate. Oscillation takes place in the working fluid; the pipe remains motionless. .In Pulsating heat pipe liquid and vapor slug/bubble transport is caused by the thermally induced pressure pulsations inside the device and no external mechanical power is required. The type of working fluid and the operating pressure inside the pulsating heat pipe depends on the operating temperature of the heat pipe the region between evaporator and condenser is adiabatic. The heat is transfer from evaporator to condenser by the means of pulsating action of vapor and liquid slug. Working fluid such as acetone, methanol and deionized water etc. filled partially. Pulsating heat pipes can be designed with many U-TURNS to suit different application. The design of a PHP is influenced by a variety of factors such as the working fluid, the temperature range of operation, the required heat transfer rate, filling ratio and the geometry of the device.
PULSATING HEAT PIPE
FIG-2: Pulsating Heat Pipe
The development of CFD model provide deeper understanding of the principles of thermodynamics, fluid dynamics and heat transfer within a pipe, allowing the performance of heat pipe to be enhanced for many different applications. Furthermore, modelling the complicated two – phase flow of boiling and condensation can be used for validating the experimental results. CFD model can reduce the experimental work necessary to predict the performance of system, which can then be optimized. The performance of final optimized model can be verified with the experimental results, which substantially reduces the cost. Analysis is done to test performance of closed loop pulsating heat pipe with different working fluid and geometries to cool the temperature sensitive electronic equipment like CPU of laptop, graphics card, cooling of these devices is important to improve the performance of system, these devices generate heat during the high -end task. One of the objectives is to validate the experimental results with CFD tools and to understand the behavior of fluid flow in narrow channels.
Khandekar and Groll (2003) conducted experiments on a PHP made of copper capillary tube of 2 mm inner diameter for three different working fluids viz. water, ethanol and R-123. The PHP was tested in vertical (bottom heat mode) as well as horizontal orientation and indicated that, a 100% filled PHP (not working in the pulsating mode but instead as a single- phase buoyancy-induced thermosyphon) is thermally better performing than a partially filled pulsating mode device under certain operating conditions. Charoensawan et al. (2003) indicated that in vertical orientation for the 2.0 mm devices, water filled devices showed higher performance as compared to R-123 and ethanol. Whereas in 1.0 mm devices, R-123 and ethanol filled devices showed comparable performance but water showing very poor results. Khandekar and Groll (2004) studied that, complete stopover is within the loop happens many times for filling magnitude relation < 50% as well as
low heat input power. Stopover development has additionally been determined for higher filling ratios. The self-sustained periodic character is then lost; such a behavior has never been according for multi-turn PHPs due to alternating periods during which bubble plugs are moving rapidly (activity phase) and stopping (static phase). Dadong and Cui (2010) indicated that the thermal resistance decreases with the rise of the heating power at an equivalent filling magnitude relation. For the pure operating fluid PHPs, the thermal resistance is decreases within the sequence of water, ethanol, methanol and acetone. Narasimha et al. (2012) studied that, at atmospheric condition; the saturation temperature is higher compared to evacuated situation. Thus, more liquid phase exists in the tube with a consequent increase in the heat transfer. Bhagat and Watt, (2015) observed that the Acetone as working fluid has higher value of bond number and lesser thermal resistance whereas Methanol has higher thermal resistance and lower value of bond number. The working fluid with higher value of bond number gives higher thermal performance than the working fluid with lower value of bond number.
II OBJECTIVES
-
To apply the principles of fluid dynamics and heat transfer to study the volume fraction of spiral and flatpulsating heat pipes. .
-
To study the complex physical phenomenon of evaporation and condensation.
-
To optimize the performance of heat pipes by various parameter such as geometry and time.
III METHODOLOGY
-
Geometry Creation:
The pulsating heat pipe used in the analysis here has inner diameter of 2mm and 1mm. various geometries with flat, and spiral. The filling ratio is taken in the range of 50 to 50%. Three phases are utilized liquid, vapor and air.
Geometry of Flat Pulsating Heat Pipe
Fig-3: 2-D Model OF Flat Pulsating Heat Pipe
Fig-4: 3-D Model Flat Pulsating Heat Pipe
Geometry of Spiral Pulsating Heat Pipe
Fig-5: 2-D Model OF Spiral Pulsating Heat Pipe
Fig-6: 3-D Model Spiral Pulsating Heat Pipe
-
Mesh Generation:
After geometry creation name the parts (Heater and Condenser), Proceed for the Mesh.
Fig-7: Meshed Model of Flat Pulsating Heat Pipe
Nodes
153664
Elements
144298
Table-1: Number of Nodes and Elements of Mesh in Flat Pulsating Heat Pipe
Fig-8: Meshed Model of Spiral Pulsating Heat Pipe
Table-2: Number of Nodes and Elements of Mesh in Spiral Pulsating Heat Pipe
Nodes
132030
Elements
116496
-
Physical Characteristics and Assumption:
The three Eulerian phases are air, water vapor and water liquid selected. The k -epsilon model is selected, with enhance wall treatment, thermal effect and curvature correction.
-
Governing Equations:
The flow inside the pulsating heat pipe is having liquid and vapor slug transformation. As the phase change takes place at the saturation temperature, the conservation of mass equation needs to be taken into consideration.
Table-3: Details of Defining the Phases
Defining the phases
Primary phase
Vapor
Secondary phase
Liquid
Secondary phase
Air
-
Cell Zone Condition:
In this section, the vacuum inside the pipe is introduced. Clicking on Cell Zone Conditions and then on Operating Conditions set the Operating Pressure as 4000, (this is the saturation pressure of the water at a saturation temperature of
29 °C. Boundary conditions are applied in the evaporator section and temperature specified as 3 53 K. The condenser temperature is kept at as 298 K. As capillary action has to takes place due to smaller diameter of tube contact angle of working fluid need to be specified at all wall geometry. The contact angle is specified as 20 degree.
-
Initializing Simulation and Patch:
After configuring the other two boundary conditions i.e., evaporator and condenser the last step before starting the simulation is initializing it and attribute initial positions for the liquid and air for the beginning of the simulation. After the initialization the zones patching is done where the geometry is patch with water as working fluid. Steam portion here is considered at 0 at initial stage.
-
Simulation Run:
The issue with simulation of multi-phase flows is that the time step needs to be sufficiently small to capture the movement of the particles, and at the same time, it needs to be big enough to reduce the computational time.
Table-4: Details of Issue with different time step
Issue with different time step |
|
Time Step |
Issue |
0.1 |
Diverge very fast |
0.01 |
Diverges |
0.001 |
Diverges after some time |
0.0005 |
Takes long time but never diverge |
IV FLOW SIMULATION
Contours of Water volume fraction of spiral pulsating heat pipes.
-
Contours of wall temperature at 0.01seconds
Fig-9: Contours of wall temperature at 0.01seconds
The Fig. 9 shows that the heating has started in the evaporator section small vapor bubbles can also be visualized from the flow development. The red zone indicates the presence of water.
-
Contours of wall temperature at 0.27seconds
Fig-10: Contours of wall temperature at 0.27seconds
The liquid and vapor slug flow can be observed at given flow time of 0.27 seconds. The liquid and vapor slug movement are observed from evaporator to condenser section. During the initial stage, the vapor is condensed as soon as it enters the condenser section of evaporator coil closed loop pulsating heat pipe.
-
Contours of wall temperature at 0.43seconds
Fig-11: Contours of wall temperature at 0.43seconds
The liquid and vapors slug development are rapid at the flow time of 0.43 seconds. The visualization shows the alternate liquid and vapor bubble transport phenomenon starting from evaporator section to the condenser section. The vapor slug found to get condense during the entry region where vapor gets converted into liquid.
Contours of Water volume fraction of flat pulsating heat pipes.
-
Contours of wall temperature at 0.01seconds
Fig-12: Contours of wall temperature at 0.02seconds
Fig-12 shows the contours of water volume fraction where alternative liquid and vapours slug formation are observed at given flow time. Pulsating action drive the fluid towards the condenser section of closed loop pulsating heat pipe.
-
Contours of wall temperature at 0.18seconds
Fig-13: Contours of wall temperature at 0.18seconds
Fig.13 shows the fluid flow has been developed and due to condensation, some vapor slug converted to liquid while they reached towards the condenser section. Latent heat as well as sensible heat transfer takes place.
-
Contours of wall temperature at 0.30seconds
Fig-14: Contours of wall temperature at 0.30seconds
As the pulsating action, takes place difference of pressure and density drives the flow of fluid from evaporator to condenser section. Heat transfer takes place as combination of sensible and latent heat of working fluid.
V CONCLUSION
The Numerical analysis of closed loop pulsating heat pipe is carried out by using different Flat and spiral geometries. The flow visualization using CFD tools helped in predicting the flow of fluid, the behavior is studied at various flow time. The contours of liquid volume fraction are visualized.
In spiral pulsating heat, pipes at 0.01seconds the heating has started in the evaporator section small vapor bubbles can also be visualized from the flow development. The liquid and vapor slug flow can be observed at given flow time of 0.27 seconds. The liquid and vapors slug development are rapid at the flow time of 0.43 seconds.
In flat pulsating heat, pipes at 0.02seconds liquid and vapors slug formation are observed at given flow time. Pulsating action drive the fluid towards the condenser section of closed loop pulsating heat pipe. At 0.18seconds, fluid flow has been developed and due to condensation, some vapor slug converted to liquid. As the pulsating action, takes place difference of
pressure and density drives the flow of fluid from evaporator to condenser section at given flow time of 0.30 seconds.
REFERENCES
[1] Rathor Rupali,Mrs. A .B. Jayant, A. K. G. (N.D.). Development And Performance Analysis Of Heat Pipe Air-Preheater. International Journal Of Innovation In Engineering Research & Management, December 2015, 19. [2]Transfer, M. (2022). Numerical Analysis To Predict The Behavior Of Liquid Vapor Slug Flow In Vertically Placed U-Shaped Closed. 14, 111. Https://Doi.Org/10.5098/Hmt.19.14
[3] Shah Hiren, K. B. G. (2019). Design , Fabrication & Analysis of Heat Pipe for Methanol , Ethanol & Acetone as a Working Fluid. Asian International Conference on Science, Engineering& Technology, August.
[4] Emeema, M. J. (2018). Heat Pipes A Review on Performance Parameters. International Journal of Creative Research Thoughts (IJCRT), 6(2), 746754. [5] Repository, U. I. (2013). Analysis Of Characteristic Heat Pipe As An Efficient Cooling. June. [6] Sharma, C. (2019). A Review of Heat Pipes: its Types and Applications. 8(03), 103106. [7] Charoensawan, P., & Khandekar, S. (2020). Closed loop pulsating heat pipes Part A: parametric experimental investigations. 23(2003), 20092020. https://doi.org/10.1016/S1359-4311(03)00159-5 [8] Khandekar, S., Dollinger, N., & Groll, M. (2003). Understanding operational regimes of closed loop pulsating heat pipes: an experimental study. 23, 707719. https://doi.org/10.1016/S1359-4311(02)00237-5 [9] Narasimha, K. R., Sridhara, S. N., Rajagopal, M. S., & Seetharamu, K. N. (2012). Influence of Heat Input , Working Fluid and Evacuation Level on the Performance of Pulsating Heat Pipe. 5(2), 3342.https://doi.org/10.36884/jafm.5.02.12165
[10] Bhagat, R. D., & Watt, K. M. (2015). Frontiers In Heat Pipes An Experimental Investigation Of Heat Transfer Capability And Thermal Performance Of Closed Loop Pulsating Heat Pipe With A Hydrocarbon As Working Fluid. 7.Https://Doi.Org/10.5098/Fhp.6.7