
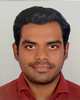
- Open Access
- Authors : Ghulekar Varun , K. Sai Priyanka , Dr. D. Govardhan
- Paper ID : IJERTV10IS050470
- Volume & Issue : Volume 10, Issue 05 (May 2021)
- Published (First Online): 05-06-2021
- ISSN (Online) : 2278-0181
- Publisher Name : IJERT
- License:
This work is licensed under a Creative Commons Attribution 4.0 International License
Computational Study of Structural and Material Analysis of Trim Tabs
Ghulekar Varun*, Ms. K. Sai Priyanka** Dr. D. Govardhan*** UG Student*, Assistant Professor**, Head of the department*** Department of Aeronautical Engineering
Institute of Aeronautical Engineering, Hyderabad, INDIA.
Abstract:- Sudden undue winds and clear air turbulence can be encountered by an aircraft at random point of time and this makes it difficult for the pilot to control the aircraft. A Trim tab is a small, secondary flight control surface that is fixed to trailing edges , primary surface, such as a rudder. Trim tabs models are developed based on the mechanism, material composites and geometric constrains or geometry, a non-linear finite element analysis of a standard trim tab is done, which helps us to determine the best shape which can hold the primary control surfaces in the desired position or angle thereby determining the turning forces acting on the primary control surface. To establish the stability
of the structure, it is necessary to simulate it at a test facility. Fusion 360 is proposed for the design, modeling, and drawing generation of the trim tab. ANSYS Workbench, the finite element software is used to carry out the analysis of the trim tab. Considering the requirement that a trim tab must counteract the aerodynamic force and stabilize the aircraft with the axis of rotation with the primary control, an analysis is performed for the designed model to find out the effect of material change, properties and eventually the best alloy is suggested.
Keywords: Secondary flight control, External pressure, Trim system.
-
INTRODUCTION
An aircrafts flight control system consists of primary and secondary control systems. The primary flight control system and are responsible to control an aircraft safely along the flight. While secondary controls are responsible for improving aircrafts performance and to relieve excessive control load caused due to aerodynamic forces acting on the aircraft. This system consists of slats, flaps, spoilers and the trim system. [1]
There exist certain forces that act on the airplane during flight. These include the aerodynamic forces- Lift, Drag, Thrust and Weight components. An equilibrium of all these four forces leads to a perfectly stabilized aircraft. An aeroplane needs to be built in a way that it is aerodynamically stable and that means if, either force by the pilot or an external force acts on the aircraft causing a change in the flight path, in a stable aircraft the aircraft itself will return to its original flight path without any inputs by the pilot. To achieve this stability in an aircraft, we have a position of the centre of the gravity and there is also a position for the centre of the lift pressure. Since the centre of gravity is always ahead of the centre of lift pressure, the aircraft gets a pitch down movement. So, if the aircraft dont have a horizontal tail, and the rear of the aircraft, then the aircraft would be un-flyable. And therefore each airliner has a horizontal stabilizer installed. Consider the tail of a Cessna 172 aircraft, and on this aircraft, the pitch trim tab is on the right (star board) side of the aircraft. [2]
Figure 1 Trim tab
When yoke is pushed forward, the elevator goes down. Now with the elevator down like that, air flowing over the whole of the horizontal stabilizer will be pushed down and when the air is pushed down, it will have an equal and opposite reaction pushing the tail up which will then make the nose of the airplane to pitch down.
Extrusion:-
As modern technologically advanced materials, aluminum and its alloys are used in emerging applications as well as revitalizing older designs. Aluminum extrusions ranging from rod, bar, or tube to complex cross-sectional designs find applications in transportation, building and construction, electrical, medical, household, aviation industry and sports products. The flexible
alternatives of the extrusion process and vast array of cross-sectional geometries in many sizes offer many design possibilities and advantages.
Manufacturing process that involves forcing base metal through a pre-shaped die to create objects with a specific shape and profile is called as extrusion. As the metal passes through the die, its shape changes according to the dies shape.
Metal extrusion is classified into following,
-
Based on working temperature as
-
Friction
-
Cols
-
Hot
-
Micro
Friction extrusion:-
Invented by The Welding Institute in the 1990s, this modern extrusion process involves the automatic rotation of the metal billets based on the position of the die. As the die rotates, it produces heat from the metal-on-metal friction around the entry of the die. This heat allows the metal to pass through the die more easily. Friction extrusion is an effective, efficient process thats becoming more gaining popular.
Cold extrusion:-
With cold extrusion metal is forced through the die while at or near room temperature. The metal used in cold extrusion typically comes in slugs, which are poured in to the dies feeder where pressure joins them together to create a solid object in a new shape.
Some of the most common metals used in cold extrusion are,
-
Aluminum
-
Copper
-
Niobium
-
Steel
-
Lead
-
Tin
Hot extrusion:-
Hot extrusion involves heating the metal at high temperature ad then forcing it through the die while in a molten state. Depending on the type of the metal temperatures may range from 650 *F all the way to 1300 *F. It is important for manufacturers to use the right temperature when performing hot extrusion. If the base metal isnt heated to its right temperature, it may struggle to pass through the die. However, hot extrusion is an accurate and effective way to reshape metals.
Some of the most common metals used in extrusion include,
-
Magnesium
-
Copper
-
Steel
-
Aluminum
-
Nickel
Micro extrusion:-
Micro extrusion is the latest type of extrusion process thats designed by the ability to create small, micro-sized materials. Particularly, the cross-section of the die supports base metal measuring just 1 mm. Its a modern process that was invented in the
1990s. But because of the high technicalities in creating such smaller size dies that can withstand such pressure, it has not gained much popularity . This may change as new advancements are made with micro extrusion.
-
-
-
Bases on process,
-
Direct extrusion
-
Indirect extrusion
-
Impact extrusion
-
Hydro-static extrusion
Direct extrusion:-
Direct extrusion, also called forward extrusion, is a process in which is the billet moves in the same direction as the ram and punch move. Billet slides against stationary container wall. Friction between the container and billet increases along the process. As a result, greater forces are needed. A dummy block of slightly lesser diameter than the billet is used in order to stop oxidation of the billet while hot extrusion. Hollow sections like tubes can be extruded by direct method, by using hollow billet and a mandrel attached with the dummy block.
Figure 2 Extrusion
Indirect extrusion:-
Backward extrusion (indirect extrusion) is a process in which punch moves in opposite direction to that of the billet. Here the relative motion between containerand billet is constrained. Hence, there is low friction and hence less forces are required for indirect extrusion. For extruding solid pieces, hollow punch is necessary. In hollow extrusion, the material gets forced through the annular space between the solid punch and the container. As seen, extrusion pressure for indirect extrusion is lower than that for direct extrusion. Many components are manufactured in combination of direct and indirect extrusions. Longer extrudes can not be manufactured using indirect extrusion.
Impact extrusion:-
Impact extrusion is a manufacturing-related extrusion process that forms metal slugs using a press and a punch and die package. It entails inserting a metal slug between a punch and a die, then turning on the press to push the slug through the die.
Hydrostatic extrusion: –
The jar is filled with a fluid in hydrostatic extrusion. The billet receives the extrusion pressure through the fluid. Since there is no contact between the billet and the container wall, friction is removed in this process. This method can be used to extrude brittle materials. Extrusion of highly fragile materials into a pressure chamber is possible. Greater reductions are possible by this method. Pressure involved in the process may be as high as 1700 MPa. Pressure is limited by the strength of the container, punch and die materials. Vegetable oils such as castor oil are used.
-
-
LITERATURE SURVEY:-
In his research article in 2017, Fang Liu, at center of advanced material technology, University of Sydney, Australia, wrote on matrix modification as an effective way to improve compressive performance of the composites. With extensive applications of polymers and its composited the demand for materials that possess excellent mechanical properties is increasing in the aviation
industry. In his study, Fang has demonstrated that compressive and flexural properties of carbon fibre/epoxy composites manufactured by a VARIM process are significantly enhanced by reinforcing the matrix with rigid nanoparticles. Particularly, due to the strengthening effect of the unique halloysite nanotubes, both the compressive and flexural properties of the bulk matrices and the composite laminates are remarkably increased because of the incorporation of the halloysite nanoclay. The effect of different particle contents on the compressive property of fiber/epoxy composites was more obvious than that in epoxies. Compressive and flexural properties of epoxy are more sensible to the matrix behaviour. Both their strength and modulus increase with the rigid particle loading, while they decrease with soft particle.
Adam Dershowitz, managing engineer at Exponent, New York, in his research work in the first quarter of 2019 gave an overview of the aircraft trim control system. Most piston powered aircraft feature a mechanical wheel by the pilots knee that can be manually rotated to adjust the trim tab position. Many large aircrafts, including mechanical and fly-by-wire control systems also include trim wheels. Trim systems generally include an electrically actuated electric or hydraulic motor that enables pilots to control the system with a simple switch. This switch is commonly mounted by the pilots thumb on the the yoke or the side stick. Pilots frequently adjust the trim to pitch the aircraft up or down during the flight. Some more automated aircraft types allow a computer to adjust the trim tab position and ease pilot workload. Others use the trim motor as an actuator for the autopilot.
-
METHODOLOGY:-
The properties of Titanium and aluminium are determined from its chemical composition as well as its method of manufacturing and process of production.
Aluminium 2024:-
Aluminum has a density of 2.7g/cm3 , and a cubic foot of Aluminum weighs about 170lb. Aluminum and its alloys have a unique combination of properties that make them one of the most flexible, cost-effective, and desirable material for a wide variety of applications It has huge demand in Engineering Applications as well and occupies second position after steel in the usage of material in Structural Metals. Aluminum has a density of 2.7g/cm3 , and a cubic foot of Aluminum weighs about 170lb. This light weight, combined with high strength of Al-Alloys, allows for the design and construction of strong, lightweight structures that are especially beneficial for vehicles such as aaircrafts, Space Vehicles as well as Under Water Vehicles. Aluminum has protective layer which can reseal itself if is scratched and also can resist corrosion by water, salt, and other external factors like chemical and physical agents.
When considering different alloys in an extrusion project, it is important to understand the properties of each alloy and how it compares to the alternatives. Aaluminum extrusions play an important role in the modern aerospace industry, thanks to their high strength-to-weight ratio and resistance to corrosion. [4]
Figure 3 Raw aluminium
2024 Aluminium is an alloy that is often used in the aerospace industry. It is a high-strength alloy suitable for projects requiring a high strength-to-weight ratio and excellent fatigue resistance. As such, it is primarily found in wing and fuselage structure that frequently come under tension. This alloy is often extruded, but it can also be found in sheets and plane forms. This alloy features a high strength, poor corrosion resistance and weldability, good workability, and fair machinability.
Titanium Grade 2:-
Pure Titanium undergoes an allotropic transformation from the hexagonal close-packed alpha phase to the body centered cubic beta phase at a temperature of 882.5 *C(1620.5*F). Commercially pure, cp Titanium is unalloyed. At service temperature it consists of 100% hcp alpha phase. As a single-phase material, its properties are controlled by chemistry (iron and interstitial impurity elements) and grain size. Titanium is classified into Grade1 depending on the yield strength and allowable levels of the elements iron, carbon, nitrogen, and oxygen. Commercially pure, Titanium Grade 2 has a minimum yield strength of 275 Mpa (40 ksi), and relatively low levels of impurity elements, which places it between Grade 1 and 3in terms of strength. [3]
Grade 2 is widely used because it combines excellent formability and moderate strength with superior corrosion resistance. This combination of properties makes CP Grade 2 titanium a candidate for a large variety of chemical and marine as well as aerospace and medical applications. CP Titanium Grade 2 may be considered in any application where formability and corrosion resistance are important, and strength requirements are moderate. Some examples of aerospace application have included airframe skins in warm areas, ductwork, brackets, and galley equipment. CP Ti Grade 2 has also been widely used in marine and chemical applications such as condensers, evaporators, reaction vessels. Other uses have included items such as jigs, baskets, cathodes and starter-sheet blanks for the electroplating industry, and a variety of medical applications.
Properties of Titanium Grade 2 Heat Treatment:-
The treatments used for the CP Ti are annealing and stress relieving. Annealing is used to fully soften the material and remove all residual stress. Annealing of wrought products at physical temperatures (below the beta transus) results in a fully recrystallized equiaxed alpha structure. Precise control of grain size (and mechanical properties) can be achieved by adjusting the anneal temperature. Stress relieving is used to remove some or most of the residual stresses from forming, or to recover compressive yield strength after stretching.
Intermediate and final annealing of CP Ti is often performed in a vacuum or inert gas atmosphere to avoid alpha case formation and the associated material loss. Vacuum annealing can also be used to remove excess hydrogen pickup, a process known as vacuum degassing. Parts to be vacuum heat treated must be thoroughly cleaned.
Workabilty:- Hot working:-
CP Ti Grade 2 can be processed by conventional techniques such as hot rolling, forging, and hot pressing. Temperatures for initial roughing may be as high as 30-50ºC (50-100ºF) above the beta transus, and temperatures for finish processing are typically in the alpha/beta phase field, ranging from about 815ºC (1500ºF) to about 900ºC (1650ºF). Typically, more severe forming is done in the temperature range of 480-540ºC (900-1000ºF) and milder forming from 200-315ºC (400-600ºF). Care must be taken to prevent the formation of excessive alpha case, and alpha case must be removed after processing.
Cold working:-
CP Ti Grade 2 has good ductility and can be formed at room temperature by various standard methods including bending, stretch forming, heading, stamping, and drawing. CP Ti work hardens fairly rapidly, which is a limitation in some operations, such as cold drawing. The Bauschinger effect results in a drop of up to 25% in compressive yield strength upon stretching at room temperature; this drop can be recovered by stress relieving.
Machinability:-
The machining characteristics of CP Ti Grade 2 are like those of austenitic stainless steels. In general, low cutting speeds, heavy feed rates, and copious amounts of cutting fluid are recommended. Sharp tools and rigid setups are also important. Because of the strong tendency of titanium to gall and smear, feeding should never be stopped while the tool and workpiece are in moving contact. Non-chlorinated cutting fluids are generally used to eliminate any possibility of chloride-induced stress-corrosion cracking. It should be noted that titanium chips are highly combustible and appropriate safety precautions are necessary.
Process of aluminium extrusion:-
The typical sequence of production steps for aluminum extrusion aluminum from a billet includes:
-
Preheat billets
-
Extrude
-
Quench
-
Stretch
-
Cut into mill lengths.
-
Artificially age
-
Quality control
Initially, the raw material is bought into the plant from a variety of stockists around the country. Bauxite ore is the primary source of aluminium. The ore must first be chemically processed to produce alumina.
Alumina is the smelted using an electrolysis process to produce pure aluminium metal. The raw aluminium so bought is heated until in turns into liquid state in underground furnaces. This furnace can heat the aluminium raw material up to 600 *C and at this temperature the solid aluminium turns in to pure liquid state which is then moved onto the moulding chamber where we can get the aluminium billets of required size and shape. These billets are preheated before being extruded. With increasing billet preheating temperature, the tensile strength increases.
The metal billet is forced through the die orifice in the same direction as the applied force to the billet. The extrusion is generally conducted at 350-450*C. The major advantage of this process is its high productivity due to the fact that the total length of the extrudate is generally limited by the size of the metal billet. This billet taper can be calculated for the specific process, press, shape, and alloy, allowing deformation and friction heating to equilibrate the billet temperature in the deformation zone for the entire process. This brings us to the third step of quenching. This means rapid cooling of the extruded metal from the solution treating temperature to about 400*C.
Then comes the role of the high-power rollers used for stretching the long-extruded metal beams in a straight and aligned manner. Next comes in the process of cutting the long lengths of the metal into the desired length according to the guidelines provided by the consumer. Here requires a skilled labour wherein he can keep a watch on the cutting metal as it may sometimes catch fumes due to the high frictional forces arising from the cutting drum. Then these mills or the final tabs are sent into an aging chamber where they are approximately 190-210 *C for about a period of 7 complete hours. This will induce a complete changeover in terms of the tensile strength and corrosive resistance of the metal. The main motive is to achieve a hardness level of 16.2 HRC which is the optimum condition for aircraft parts.[5]
Next step is the quality control. There exists a 4-step quality check inspection,
-
Pre-production inspection,
-
Pre-shipment inspection
-
Container loading supervision
-
Piece-by-piece inspection of the final product.
The entire process is of quality inspection is based on the non-destructive testing (NDT) of the final product. These tests are conducted to prove to the customer that the products delivered are of high standards and are of utmost fine quality. There exists a diverse variety of NDT testing conducted, these are,
-
Visual inspection 2.Ultrasonic NDT 3.Magnetic particle NDT 4.Liquid penetrant NDT 5.Leak testing
-
6.Pulse echo NDT 7.Hardness test 8.Thermo-graphic test
As a quality control and quality assurance management tool, NDT plays a major role in industries such as aerospace, pipelines, bridges, and oil platforms as well as power generation stations as it can help to predict failures that could otherwise lead to an adverse impact on safety, reliability, and the environment.
Non-Destructive Testing (NDT) is a wide group of analysis techniques used in science and industry to evaluate the properties of a material, structures or system without causing any damage to the base material.
-
Visual inspection:-
Visual testing is the most commonly used method of non-destructive testing (NDT). Visual inspection (VT) is the oldest and most widely used NDT technique.
Visual Testing is based on the search for flawsvisible to the naked eye and is the most commonly used NDT method across many industries. It allows for a fragile and quick control of quality at every step of the fabrication or maintenance process.
-
Ultrasonic NDT:-
Ultrasonic testing (UT) is a family of non-destructive testing techniques which are widely used based on the propagation of the ultrasonic waves in the object. Ultrasonic waves are checked at different places in the structure to determine the weather the structure is good / bad at different locations.
In this test, ultrasonic waves passed into structure by placing the probes above and below to
structure at different locations. Based on the loss of frequency can be determine the goodness of structure.
-
Magnetic particle NDT:-
Magnetic particle inspection (often abbreviated MT or MPI) is a nondestructive inspection method that provides detection of linear flaws located at or near the surface of ferromagnetic materials. It is viewed primarily as a surface examination method. There are many different techniques. The most versatile technique is using a 110v AC hand held electromagnetic yoke magnet, a white paint as contrast background and a magnetic "ink" composed of iron powder particles in a liquid carrier base.
The area is magnetised with the yoke magnet. In the event of a surface or slightly sub surface defect being present, the lines of magnetic force will deform around the defect.The magnetic ink is applied and the iron powder particles will cover the gap caused by the defect and give a visible indication against the white background.
-
Liquid penetrant NDT:-
Liquid penetrant testing (PT) is a one of non-destructive test, which is used to detect defects such as hairline cracks, surface porosity, leaks in surface, and fatigue cracks. It can make invisible defects to be visible by using liquid dye. Capillary action is the mechanism involved in this technique.
-
Pulse echo NDT:-
A single phase current will be used in this technique in which it generates signal and passes into the composite surface and also receive the resultant signal with same probe.
-
Hardness test:-
This test is conducted to verify the strength of the material provided and is conducted by the portable dynamic hardness testing equipment.
-
Thermo-graphic test:-
Figure 4 Hardness test
Thermo-Graphic inspection refers to the Non-destructive testing of parts, structures or systems by the imaging of the thermal patterns on the objects surface.
-
-
DESIGN AND ANALYSIS:-
The initial designing is carried out in Fusion 360. Fusion 360 is a cloud based CAD/CIM tool for collaborative product development. Fusion 360 enables exploration and iteration on on different product ideas.Fusion 360 combines organic shapes modelling, mechanical design and manufacturing in one comprehensive package. Thus the airfoil strut plot is imported in to fusion 360 as shown I below figure.
Figure 5 Airfoil strut
The imported airfoil is then edited properly with all the required actions.
The structure obtained is saved and can now be imported into ANSYS workbench for further finite element analysis of the structure.
ANSYS is a computer-aided finite element modelling and analysis tool software that analyses the robustness, performance, toughness, strength, and many other qualities of the components and assemblies. In the graphical user interface of ANSYS, the user can generate 3- dimensional and finite element models, perform analysis and generate the required results of the analysis.
The ANSYS workbench module is opened, and the required geometry of structure is imported and then the mesh option is selected. After meshing is completed, pressure option is selected from the loads menu. The internal surface of the trim tab is selected and a pressure of 5 Mpa is applied. The results obtained are tabulated.
Figure 6 Mesh design
Figure 7 Pressure application on trim tab
-
RESULTS:- Table 1 Result of aluminium trim tab
1
Mass
2333.4842 [g]
2
Volume
839382.78[mm3]
3
Nodes
4600
4
Elements
2060
5
Density
0.00237[g/mm3]
Table 2 Results of aluminium trim tab
S No.
Parameters
Minimum
Maximum
1
Van mises stress
0.9551 [MPa]
24.31 [MPa]
2
Directional deformation
-0.001488 [mm]
0.001178 [mm]
3
Total deformation
0 [MJ]
1 [MJ]
Table 3 Results of titanium trim tab
1
Mass
3777.2225 [g]
2
Volume
839382.69 [mm3]
3
Nodes
4600
4
Elements
2060
5
Density
0.0045 [g/mm3]
Table 4 Results of titanium trim tab
S No.
Parameters
Minimum
Maximum
1
Van mises stress
0.75111 [MPa]
19.706 [MPa]
2
Directional deformation
-0.002396 [mm]
0.00190 [mm]
3
Total deformation
0 [MJ]
1 [MJ]
Results generated: Aluminium 2024 Directional deformation:
Von Moises Equivalent Stress
Total Deformation
Titanium Grade 2: Directional Deformation
Figure 8 directional deformation
Figure 9 von moises stresses
Figure 10 total deformation
Figure 11 directional deformation
Von Moises Equivalent Stress
Total Deformation
Figure 12 van moises stresses
Figure 13 total deformation
-
CONCLUSION:
From the results so obtained from the analysis of the trim tabs of both Aluminium 2024 and and Titanium Grade 2 , though Titanium shows better resistance to stress in comparison with Aluminium, the greater mass of titanium makes the structure more heavy and thus resulting in lesser efficiency of the structure. Sine, an aircraft is desirable to be as light weight as possible in order in order to ensure greater fuel efficiency, Titanium would make it more difficult because of its weight. In comparison with aluminium, Titaniums mass is about 2/3 greater than aluminium and the density of Titanium Grade 2 (0.0045) is greater than Aluminium 2024 alloy( 0.002) for the same volume. Thus, from the above results, we can infer that Aluminium is much more efficient, in-terms of weight,cost and machinability when compare to that of Titanium Grade 2 alloy.
The results also show that Aluminium 2024 alloy is more reliable for the manufacture of aircraft components like the trim tabs and is much more readily available than the latter.
-
FUTURE DEVELOPMENTS
Composites:-
Clearly from the results generated,aluminium 2024 has better characteristic properties over Titanium Grade . These properties largely depend on the load acting on the surface, type of environment it is being operated in and the inputs given by the operator. For many years now, there have been enormous number of trials done to bring out the best-in -segment composite structure to build the aircraft parts in order to reduce the overall weight of the aircraft, thereby reducing the cost of operation, which directly reflects on the ticketing price and thereby leading to the development of the airline industry. By doing so, the nature will also get back its beauty as a less weighing aircraft can achieve more fuel efficiency and thereby reducing carbon footprint. Better structural efficiency can also ensure lesser sound emissions, thereby allowing airports to operate in and near any major city hub like the London city airport. [6]
A proposed composite alloy consisting of Titanium alloy 6% , Aluminium 4% and vanadium is being researched upon, which can have a tensile strength of 1000-1100 MPa and a useful creep resistance of up to 300*C of about 570 MPa for 0-1 % total
plastic strain in 100 hrs. Resistance to fatigue and crack propagation would be excellent. Like most titanium alloys and grades, TiAlV has an excellent corrosion resistance in most of the natural environments. It can be easily formed or forged as its density is lower than that of pure Titanium – 4.0-4.2 g/cm^3.
Ti-6%Al-4%V is an alpha+beta alloy containing 6% aluminium and 4 % Vanadium. The aluminium stabilizes and strengthens the alpha phase and and the vanadium provides a good amount of the ductile beta phase during hot working.
-
BIBLIOGRAPHY:-
-
Adam Dershowitz, PhD, P.E, CFEI. Thermal sciences, managing Engineer, Exponent, New York, Considerations of Aircraft trim control, Published by Thought leadership, 1Q, 2019,https://www.exponent.com/~/media/knowledge/thought leadership/2019/tl_pdf/tl_considerations-for-aircraft-trim- control.pdf.
-
Nancy Hall,National Aeronautics and Space Administration (NASA), Trimmed Aircraft, published by Glenn Reaseach Center, 2020, https://doi.org/www.grc.nasa.gov/www/k-12/airplane/trim.html.
-
Fang Liu, Shiqiang Deng, Jianing Zhang, Mechanical Properties of Titanium and its composites modified by Nanoparticles published in Hindawi journal of nanoparticles on October 2017, Volume 2017, Article ID 8146248, https://doi.org/10.1155/2017/8146248.
-
Gary Teeling, Get to know 2024 Aluminium, by Gabrian, Wrought alloys, Aluminium Extrusion, 2016, https://www.gabrian.com/024-aluminum- properties.
-
N.A. Fleck and D. Liu, Microbuckle initiation from a patch of large amplitude fibre waviness in a composite under compression and bending, European journal of mechanics -A/Solids, vol 20, no.1, pp 23-37, 2001. https://www.sciencedirect.com/science/article/abs/pii/S0997753800011244?via%3Dihub.
-
H.M. Hsiao and I. M. Daniel, Effect of fiber waviness on stiffness and strength reduction of unidirectional composites under compressive loading, Composites Science and Technology,vol-56, no.5, pp-581-593, 1996. https://www.sciencedirect.com/science/article/abs/pii/0266353896000450?via%3Dihub.