
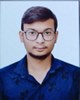
- Open Access
- Authors : Leena Patil , Chaitanya Wadbudhe , Dipti Agrawal , Prashant Negi, Pranay Kale, Amrapali Fule, Gauri Saryakar
- Paper ID : IJERTV12IS020049
- Volume & Issue : Volume 12, Issue 02 (February 2023)
- Published (First Online): 21-02-2023
- ISSN (Online) : 2278-0181
- Publisher Name : IJERT
- License:
This work is licensed under a Creative Commons Attribution 4.0 International License
Computerized Serving Robot
Leena Patil, Chaitanya Wadbudhe, Prashant Negi, Pranay Kale, Dipti Agrawal, Amrapali Fule, Gauri Saryakar
Computer Science and Engineering Department, Priyadarshini College of Engineering,
Hingna Rd, Digdoh Hills, Nagpur-440019, Maharashtra, India.
Abstract This report describes in detail the design and functionality of our project, the robotic waiter for restaurants. It is mechanical or computerized subordinate to help restaurants to serve food on the tables of customer of restaurant. The project describes the design and development of computerized serving robot by cost effective method. The human waiters are replaced by the computerized robots, robots can serve the same amount of food that a human waiter can serve. Various parts are used to design this robot so that it can move as well as serve with the same intensity as human waiter. some of the major parts are Arduino UNO, ultrasonic sensor, motor driver, servo motor, wheels, node mcu and connecting wires. Arduino UNO is micro controller used for uploading programs by connecting computer through USB port. Robot have to face obstacles coming in its way while serving food ultrasonic sensors are used so that it can find its path by avoiding obstacle coming in its path. Motor driver is use as motor controlling device in autonomous robot and embedded circuits. Different kind of algorithms are also used for Artificial Intelligence in this project.
Keywords—Serving robot, artificial intelligence, computerized robot, robotic waiter, node MCU, Arduino UNO, ultrasonic sensor, motor driver, servo motor.
-
INTRODUCTION
Nowadays, the Shortage of employees has become a huge conundrum for restaurant owners, not only in this industry but also in other businesses also. even with the deployment of good cooks and management, restaurants do not have enough manpower for serving food. Since there is less amount manpower, a quick solution may be the waiters carrying heavier load to increase efficiency. However, this solution quickly aggravates as waiters become fatigue and therefore, unable to continue working.
The Internet of Things is one the moving plan to make the a couple of systems as motorization and can diminish the number human undertakings in every space, alongside this robot making and using the robot in the dares to replace the human undertakings is one of the huge thoughts. While examining the food business, the robots fill for much need, essentially in serving the food. Robot being a great advancement in the field of technology can serve well as a waiter at restaurants and hotels. With their time efficient and dedicated task performance robot can be a perfect solution in catering work.
Robotic technology are coveted in many industries including restaurants and its because they can increase accuracy, reduce cost and increase safety for human beings. In fact, safety is one of robotics' greatest benefits, as many dangerous or unhealthy environments no longer require the human element.
-
BACKGROUND & LITERATURE REVIEW
The food serving robot for contactless experience is the thorough cutting edge uncovers that the space of mechanical technology has unbelievably accelerated the efficiency whilst contrasted with the guide introduction frameworks.The Serving Robot-Robots helps in reducing the lack of human resources to serve in restaurants. The Robot must cost effective once we built later just maintenance should be required[1].
Tells design of microcontroller based robot which works effectively in a restaurant by using Bluetooth device and the motor. presented that use of IR sensor for mapping and localization of unknown area. They uses IR sensor for pathway planning for food delivery and also to carry the baggage.The robot is line follower robot follows the predefined path .this line is sensed by the IR sensor and each to the particular destination for that he proposed Design and Implementation of Line Follower Robot. This robot makes the use of static system in which the robot moves on static lines by using Digital differential algorithm and dynamic system in which the arrangement of the following lines is changes accordingly[2].
The paper shows It's a critical part of the robot locating the table and delivering its load. It is conceived in-house integrating a commercial couster pager, an embedded processor, an IR transmitter and the table RFID with a unique table code. Each table will be installed with it. Each table has a unique RFID code that is locatable by the indoor RF location. the coaster pager that contains his paging code for the food ordered into the system at the table. When the patrons food are ready, the pager will vibrates and activates the embedded processor to instruct the IR transmitter to transmit the table RFID code protocol system found in remoter controllers for use[3].
The traditional way of serving comprises of a human waiter, who goes around the customer asking for the order. The main drawback of traditional human waiter is that it is very time consuming and employing a human can cost more as he need to be paid for his service, also when they get sick the work suffers for the owner[4].
As the above mentioned all works, focuses on the serving task in the restaurant, here in this project it has been tried to create a prototype of robotic waiter which can serve customers after having the order given by the customer sitting on the table by only pressing a button. The robot designed in this project travel from the source point to the destination table by step counting of wheels revolution
where the travelling distance has been measured and loaded in the robot. The designs and implementations of the robot waiter have been completed using existed appliances locally. These robot waiter can work in different areas such as restaurants, hospitals, office environment etc.
-
RELATED WORK
-
Incorporate Technologies
The main components used to design the robot waiter are described below:
-
Arduino Uno
It is an open-source hardware and software corporation that designs and manufactures single-board microcontrollers and microcontroller packs to be used in computerized gadgets, in addition to a project and user community. Arduino sheets may be constructed collectively by everybody and used to offer code Arduino sheets are to be had for buy immediately from the authority's internet site or via accredited resellers. Arduino boards hire a huge range of microprocessors and regulators, the sheets offer a variety of complicated and simple information/yield (io) sticks that may he connected to extraordinary improvement sheets (safeguards), breadboards (for prototyping), and circuits. Sequential interchange interfaces, together with generic serial bus (USB) on some fashions, are highlighted on the sheets, and also are used for stacking applications, in addition to a preferred API called the "Arduino language," may be used to customize the microcontrollers. The usage of conventional compiler tool chains is not the simplest option.
Microcontroller
Atmega328
Operation Voltage
5V
Input Voltage
7-12V
Input Voltage (limit)
6-20V
Fig. 1. Auduino Uno
-
Motor Driver
Actually, a motor cause pressure is some factor that reasons the motor to move in reaction to instructions or inputs (excessive and low). It takes use of the controller's low voltage to be abe to pressure a motor that requires a high enter voltage. The time period "motor force," or definitely "power, "refers to device velocity manage system. Many commercial processes, including assembly lines, must function at variable charges depending at the commodity. Whilst process conditions necessitate pump or fan go with the flow adjustment, adjusting the pressure's velocity can be greater power efficient than different float manipulate methods. Motor driver makes use of a bigger chip or discrete fets which could control better currents and voltages than a microcontroller pin's normal Sv/three.3v. They enable you to control a considerably large load with a noticeably tiny sign. It's critical to understand that even as talking approximately motor drivers and controllers, the sort of motor have to additionally be considered. The s is a brushed de motor.
Fig. 2. Motor Driver
-
Servo Motor
Digital input/output pins
14
Analog Input Pins
6
DC Current per I/O Pin
40 mA
DC Current for 3.3V Pin
50 mA
Flash Memory
32 KB of which 0.5 kb used by bootloader
SRAM
2KB (ATmega328)
EEPROM
1KB (ATmega328)
Clock Speed
16Hz
A servo motor is a type of motor that can rotate with great precision. Normally this type of motor consists of a control circuit that provides feedback on the current position of the motor shaft, this feedback allows the servo motors to rotate with great precision. If you want to rotate an object at some specific angles or distance, then you use a servo motor. It is just made up of a simple motor which runs through a servo mechanism. If motor is powered by a DC power supply then it is called DC servo motor, and if it is AC-powered motor then it is called AC servo motor. For this tutorial, we will be discussing only about the DC servo motor working. A Servo Motor is a small device that has an output shaft. This shaft can be positioned to specific angular positions by sending the servo a coded signal. As long as the coded signal exists on the input line, the servo will maintain the angular position of the shaft.
Fig. 5. Node MCU
-
Ultrasonic Sensor
Fig. 3. Servo Motor
6. Connecting Wires
Jumper wires are simply wires that have connector pins at
It is an electronic device that measures the object distance by ultrasonic sound waves and converts the reflected sound into an electrical signal. Ultrasonic waves travel faster than the speed of audible sound. It has two main components: the transmitter and the receiver. Here we have used this sensor for obstacle detection. It sends an ultrasonic pulse out at 40kHz which travels through the air if there is an object, it will bounce back to the sensor. By calculating the travel time and the speed of sound, the distance can be calculated. An ultrasonic sensor is an electronic device that measures the distance of a target object by emitting ultrasonic sound waves and converts the reflected sound into an electrical signal. Ultrasonic waves travel faster than the speed of audible sound (i.e., the sound that humans can hear). Ultrasonic sensors have two main components: the transmitter (which emits the sound using piezoelectric crystals) and the receiver (which encounters the sound after it has travelled to and from the target.
each end, allowing them to be used to connect two points to
each other without soldering. Jumper wires are typically used with breadboards and other prototyping tools in order to make it easy to change a circuit as needed. When building electronics projects, little thought is given thought is given to the connecting wire. While it is possible to 'get away with almost anything for many projects, it is sometimes necessary to connect the various electronics components using the right wire. For example, it is often useful to use colored connecting wire to indicate such items as electronics wire used for connecting the supplies, signals, and grounds. In this way it is easier to identify the different signals and lines, and this reduces the possibility of errors. In addition to this it is sometimes necessary to have connecting wire of a particular size to ensure the connections are made in the right manner. If the wire is too thick it may not be easy to accommodate in some situations, whereas thicker wire may be needed for higher currents of physical strength or robustness in other situations.
5. Node MCU
Fig. 4. Ultrasonic Sensor
Fig. 5. Connecting Wires
The Node MCU (Node Micro Controller Unit) is an open- source software and hardware development environment that is built around a very inexpensive System-on-a-Chip (SoC) called the ESP8266. is an open-source firmware for which open-source prototyping board designs are available. The name "Node MCU" combines "node" and "MCU" (micro- controller unit). Strictly speaking, the term "Node MCU" refers to the firmware rather than the associated development kits. Both the firmware and prototyping board designs are open source.
7. IR Sensor
An infrared (IR) sensor is a type of electric sensor that detects and responds to infrared radiation in the environment. William Herschel, an area expert, discovered infrared radiation via coincidence in 1800. Whilst comparing the temperature of every color of mild, he discovered that the temperature just beyond the red mild become the maximum great (separated through a crystal). Because IR has an extended frequency than seen mild, its miles invisible to the naked eye (but it is as but on a comparable Electromagnetic range). Anything that produces warmth emits infrared radiation (that is, something that has a temperature over more or less five ranges kelvin).
Fig. 6. IR Sensor
-
-
Methodology
Regarding to the above said trouble we're going to advocate a food deliver robot for the meals industry (hotels/eating places). This robot is ready for simplest the purpose of the food serving and makes the Artwork efficient and less human interruption inside the approach. As soon as the user can region the food on the robot it'll circulate in line with the assigned table and it consists of the 12 volts battery , IR sensor and ultrasonic sensors for the higher performance and to discover the assigned table through the IR sensor[1].
Here the Arduino is used to establish the connection with the software and hardware components. It also contains Node MCU device which will be used to establish the connection between the Robot and the tables. So that the robot will exactly know to reach the respective table which is requesting for the service. Arduino and Node MCU communicates through http request and response procedure with help of Wi-Fi.
Fig.7 shows the block diagram of Autonomous Robot for delivering orders in Restaurants by using Arduino Uno. Robot having two wheels and one freewheel is mounted along with different sensors and module i.e. ultrasonic sensors and IR sensors.
Ultrasonic sensors are used to detect the obstacles in the path. It transmits the signal continuously if any obstacle come then the transmitted signal get disturb and the reflected signal known as echo which is received by the ultrasonic receiver. If the obstacle is detected in between 20cm to 5cm robot will stop else it will follows the given path & the distance is calculated by using Eq.(1) & Eq.(2) [2].
Distance=17150*Time .(1) Distance=Pulse Duration*17150 .(2)
Fig. 7. Flow Diagram for Proposed System Work
Arduino UNO is used for learning and experimental purpose. It operates on 5V power supply. In this project we use Arduino UNO as a main processor to control Robot motion. It takes the input from IRsensors and ultrasonic sensors and after processing it, it sends the data to the driver module to control the motors.
Motor driver module is used for boosting the current of Arduino UNO. The average current capacity of GPIO is 40mA but for controlling the motor we require 2A current.
We can interface two DC motors and one stepper motor to the motor driver module.
DC motors are used to convert current electrical energy into mechanical energy. It is used for controlling the wheels of Robot. It operates on 12V power supply. DC motor has higher starting torque. In Robot we uses two wheels for taking right and left moves and one free wheel for taking turn smoothly.
Firstly, it checks the status of camera. If the camera is working properly then it will take instructions from the admin and will start moving towards the table. While moving towards the table if both the Ultrasonic sensors and IR sensors output are low then it indicates the robot is on correct track, then Robot moves in forward direction and reach at the destination. But if any of the sensors having high output that means if right ultrasonic sensors or IR sensors output is high then it stops left motor and moves the Robot in right direction, similarly if the left sensors output is high then it stops right motor and moves the robot in left direction. Then again it checks whether the robot is on correct track or not. According to that it will reach to the given destination and capture the table number to recognize the correct table. The Convolutional Neural Networks (CNNs) algorithm is used for recognizing the correct table number as per the instructions. After reaching to the correct table it will deliver the order to the customer. After delivering the order the robot moves to its original location or to the start location.
Fig. 8. Working of Robot.
Fig. 9. Circuit Diagram for the robot
-
-
DISCUSSION
In this design, the waiter robot can receive and execute only one request at a time. There are no memories or buffering techniques to handle more than one request asking at the same time. It can be solved in future extension of this project. The structural design has not included in prototype model of waiter robot. It is implemented only for testing the logic operation. So the height of the robot was kept short. The structural design of waiter robot can be the future extension of this project. The errors of human waiters can be overcome by the robotic waiters. The robotic waiter can be very attractive, smart and cost effective.
The targeted advantages of designed robot are mentioned below.
-
Reduce the extra manpower.
-
Working at places 24/7 without any salary.
-
It can perform tasks faster than humans and much more consistently and accurately.
This design can be extended in size and also in weightlifting capacity. There is huge scope in design of the movement from source to destination. Here fixed code has been loaded in microcontroller which may create complexion in increasing number of destinations.
-
-
CONCLUSION
In traditional serving system waiter will deliver the orders so that its time consuming & produces human errors. So we proposed this system to overcome these drawbacks. This paper is effectively experimented & implemented for the restaurants to deliver the order to the particular table and robot follows the particular path. So this robot is cost- effective, and it reduces human efforts. Also, this robot is utilized for various places like malls, cafes, hotels etc. Robot is designed to deliver the order to the particular table. It can improve the quality of service. When we press any key the Robot will follow the pre-defined path and reach to the desired path to deliver the order.
REFFERNCE
[1] J.Chandrashekhara, Divya M.S, Shivaprasad M S. "Food Serving Robot For Contactless Experince." International Journal of Innovation Research in Computer Science & Technology (IJRCST), 3(10) ( May 2022), 2347-5552. [2] Yelasange, A. M., Bhaldar, H. K., More, K. A., & Katkar, A. P. Autonomous Robot for Delivering The Orders in Restaurants By using Raspberry Pi. [3] Cheong, A., Foo, E., Lau, M. W. S., Chen, J., & Gan, H. Y. (2015).Development of a Robotics Waiter System for the food and beverage industry. In 3rd International Conference On Advances in Mechanical & Robotics Engineering. Newcastle University.
[4] Agarwal, A., Gupta, P., Iqbal, F., Kumar, A., & Madani, A. (2014). Robot as a Waiter For Restaurants. International Journal of Scientific Research and Management Studies (IJSRMS), 3(7), 271-274. [5] Kamruzzaman, M., & Tareq, M. (2017, December). Design and implementation of a robotic technique based waiter. In 2017 3rd International Conference on Electrical Information and Communication Technology (EICT) (pp. 1-5). IEEE. [6] Hasan, K.M., Al-Nahid, A., Reza, K.J., Khatun, S. and Basar, M.R., 2013, April. Sensor based autonomous color line follower robot with obstacle avoidance. In 2013 IEEE Business Engineering and Industrial Applications Colloquium (BEIAC) (pp. 598-603). IEEE. [7] Islam, M.S. and Rahman, M.A., 2013. Design and fabrication of line follower robot. Asian Journal of Applied Science and Engineering, 2(2), pp.27-32. [8] Engin, M. and Engin, D., 2012, September. Path planning of line follower robot. In 2012 5th European DSP Education and Research Conference (EDERC) (pp. 1-5). IEEE. [9] Pakdaman, M., Sanaatiyan, M.M. and Ghahroudi, M.R., 2010, February. A line follower robot from design to implementation: Technical issues and problems. In 2010 The 2nd International Conference on Computer and Automation Engineering (ICCAE) (Vol. 1, pp. 5-9). IEEE. [10] Baharuddin, M.Z., Abidin, I.Z., Mohideen, S.S.K., Siah, Y.K. and Chuan, J.T.T., 2005. Analysis of line sensor configuration for the advanced line follower robot. University Tenaga Nasional.