
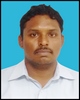
- Open Access
- Authors : M.Sai Krishna Kanth , Dr. M. V. S Murali Krishna , Dr. Narasimhulu Sanke
- Paper ID : IJERTV11IS010093
- Volume & Issue : Volume 11, Issue 01 (January 2022)
- Published (First Online): 28-01-2022
- ISSN (Online) : 2278-0181
- Publisher Name : IJERT
- License:
This work is licensed under a Creative Commons Attribution 4.0 International License
Control of Aldehydes of Diesel Engine Fuelled with CNG and Carbureted Ethanol
-
ai Krishna Kanth PhD scholar
Mechanical Engineering Department Osmania University Hyderabad, India
Dr.M.V.S Murali Krishna Professor,
Mechanical Engineering Department Chaitanya Bharathi Institute of Technology Gandipet Hyderabad India
Dr. Narasimhulu Sanke Professor
Mechanical Engineering Department, College of Engineering,
Osmania University Hyderabad, India
AbstractUsage of fossil fuels is at its maximum content that resulted in higher prices globally. The increase in fuel prices had slowed down development in countries like India. Moreover with the present stringent policies imposed by the government against the pollution levels Its been a necessity to search for an alternate fuel.
Gaseous fuels have many advantages than liquid fuels, as the pollutants emitted by gaseous fuels are low and less dangerous when compared with liquid fuels. Specifically CNG provides an affordable energy source.
Besides its cheaper prices it has better efficiency than conventional fuels, furthermore the engine health is preserved these reasons have attracted the consumers to purchase a CNG based vehicles. Emissions from a CNG based vehicle are fewer in comparison with Gasoline. The availability of CNG globally is abundant in comparison with Gasoline being a crucial advantage . CNG was injected and ethanol was carbureted in diesel engine. Ethanol owing to lower cetane number attributed to problems in combustion this demands a semi adiabatic diesel engine (SADE), which can burn low calorific value fuel, give high heat release rate and faster rate of combustion. Air gap insulation was provided with piston and liner. Investigations were carried out with CNG as primary fuel inducted by port injection and ethanol was carbureted into the engine. When engine is run with alcohols, aldehydes are to be checked. These aldehydes are carcigenic in nature. They cause health hazards, once they are inhaled in. Hence control of these emissions is an immediate effect and an urgent step. Aldehydes were measured by wet method. The maximum induction of ethanol was 40% of total mass of diesel as full load operation, while it was 60% with SADE. To control aldehyde emissions catalytic converter was employed with copper as catalyst. It was provided with air injection system. Catalytic converter along with air injection system successfully reduced aldehyde emissions.
Key words: Diesel, biodiesel, CE, LHR engine, Exhaust emissions
-
INTRODUCTION
-
The civilization of a particular country has come to be measured on the basis of the number of automotive vehicles being used by the public of the country. The tremendous rate at which population explosion is taking place imposes expansion of the cities to larger areas and common man is forced, these days to travel long distances even for their routine works. This in turn is causing an increase in vehicle population at an alarm rate thus bringing in pressure in Government to spend huge foreign currency for importing crude petroleum to meet the fuel needs of the automotive vehicles. The large amount of pollutants emitting out from the exhaust of the automotive vehicles run on fossil fuels is also increasing as this is proportional to number of vehicles. In view of heavy consumption of diesel fuel involved in not only transport sector but also in agricultural sector and also fast depletion of fossil fuels, the search for alternate fuels has become pertinent apart from effective fuel utilization which has been the concern of the engine manufacturers, users and researchers involved in combustion & alternate fuel research. Rudolph diesel, the inventor of the engine that bears his name, experimented with fuels ranging from powdered coal to peanut oil [1].Severalresearchers conducted investigations on biodiesel with conventional engine (CE) and reported that the performance marginally improved, along with reduction of particulate emissions. [2-8]. However, they further reported that NOx emissions were marginally higher with biodiesel operation in comparison with neat diesel operation on CE.
The concept of SADE engine is to reduce heat loss to coolant by providing thermal insulation in the path of heat flow to the coolant. SADE are classified depending on degree of insulation such as low grade or SADE-1, medium grade or SADE-2 and high grade insulated engines or SADE-3. Several methods adopted for achieving low grade SADE-1 are using ceramic coatings on piston, liner and cylinder head, while medium grade SADE-2 provide air gap in the piston and other components with low-thermal conductivity materials like superni, cast iron and mild steel etc and high grade SADE-3 is the combination of low grade and medium grade engines.
Experiments were conducted on low grade sade-1 with diesel. They reported that diesel operation with sade- 1improved performance and reduced particulate levels [9-11]. However, they increased nitrogen oxide levels (NOx) levels.
Investigations were carried out with low grade SADE-1 with biodiesel. They reported that biodiesel operation with SADE-1 improved performance and reduced particulate emissions.[12-14]. However, they increased NOx levels.
Investigations were carried out with medium grade SADE-
2 with vegetable oil. They reported that vegetable oil operation with SADE-2 improved performance and reduced particulate emissions.[15-16]. However, they increased NOx levels
Investigations were carried out with medium grade SADE- 2 with biodiesel. They reported that biodiesel operation with SADE-2 engine improved performance and reduced particulate emissions.[17-18]. However, they increased NOx levels.
Investigations were carried out with biogas in conventional engine. The dual fuel mode exhibited lower peak values of heat release rate and also they reported the application of exhaust gas recirculation (EGR) to dual-fuel mode additionally decreased the in-cylinder pressure and increased the ignition delay. [19]. Dual fuel mode displayed lower emissions of NOx and smoke opacity while HC and CO concentrations were considerably higher as compared to other fuels. In dual fuel mode peak pressure and heat release rate were slightly higher compared to diesel and biodiesel mode of operation for all engine loads. [20].Investigations were carried out with biogas, diesel-methane, and neat diesel operation in conventional engine [21]. They observed higher brake thermal efficiencies compared to diesel mode at high loads. Though volumetric efficiency was almost identical in diesel and diesel-CH4 dual modes, exhaust gas temperatures were higher in diesel-biogas mode, followed by diesel-methane and diesel modes.[21]. NOx is a strong function of local temperatures. They reported that in compression ignition engine at constant speed of 1500 r/min at full load both NOx and soot missions were dropped, energy content rates in gasfuel mixture compared to only diesel fuel[22].
However, little reports were available with the use of CNG and carbureted ethanol on aldehydes. Hence authors have worked in this direction. It is attempted to determine and control the aldehydes with catalytic converter with copper as catalyst on conventional engine and SADE with CNG with carbureted ethanol and compared the data with diesel operation on CE.
2.MATERIALS AND METHODS
2.1 Fabrication of SADE combustion chamber
Figure 1 shows the assembly details of air gap insulated piston, air gap insulated liner. SADE-2 contained a two- part piston; the top crown made of low thermal conductivit material, stainless steel (A-304 Grade-A) screwed to aluminum body of the piston, providing a 3mm-air gap in between the crown and the body of the piston. The optimum thickness of air gap in the air gap piston was found to be 3-mm [23], for improved performance of the engine with stainless steel with diesel as fuel. A stainless steel (A-304 Grade-A) insert was screwed to the top portion of the liner in such a manner that an air gap of 3-mm was maintained between the insert and the liner body. At 500oC the thermal conductivity of stainless steel and air are 16.5 and 0.057 W/m-K respectively.
Insulated piston Insulated liner
-
Crown with threads 5 Insert with threads
-
Gasket 6. Air gap
-
Air gap 7. Liner
-
Body
Figure 1. Assembly details of air gap insulated piston and air gap insulated liner
-
Experimental Set-up
Description
Specification
Make
Mahindra & Mahindra
Number of cylinders
01
Number of Strokes
04
Ratio of bore to stroke
93 mm/92 mm
Power
6.6 kW (9 HP) at the rated speed of 3000rpm
Compression Ratio
18:1
Type of cooling Arrangement
Water cooling
Recommended Injection Pressure
190 bar
Recommended Injection Timing
27 degrees before top dead centre
Maximum Torque
30 Nm at 1800 rpm.
Table.1 gives the details of the engine.
Fig.1 shows that the test engine
-
and the details of the CRDi engine are given in Table. The engine was connected to power measuring device (2). The engine had computerized test bed. There was facility of loading the engine by means of variable rheostat. (3). Outlet jacket water temperature was indicated with temperature sensor (4). The flow of the coolant was measured with flow
-
meter (5). The pressure of the gas was noted in gas pressure sensor (6). TDC encoder (7) was provided to the extended portion of dynamometer to indicate crank angle. Console (8) was provided to convert pressure signal and magnetic signal into electric signal and given to Pentium Personal Computer
(9) and Printer (10). Components (6), (7), (8),(9) and (10) were used to determine combustion characteristics of peak pressure, maximum rate of pressure rise and time of occurrence of peak pressure at full load operation of the engine. The temperature of the exhaust gas was indicated with exhaust gas temperature sensor (11). The particulate levels were determined with AVL Smoke meter (12) at different values of brake power of the engine. The pollutants of NOx. CO and UBHC were determined by Netel Chromatograph multi gas analyzer (13) at various values of brake power of the engine. The range and accuracy of the analyzers in multi gas analyzer are shown in Table.2. Filter (14) was incorporated in the circuit for the purpose of filtration. In order to measure rate of flow of exhaust gas, rotometer (15) was introduced to set exhaust gas at flow rate of 2l/m. Heater (16) was provided in the circuit to heat exhaust gas at 140oC. Round bottom flask
-
contained 2-DNPH solution was provided for bubbling exhaust gas for the measurement of aldehydes. The components (14), (15),(16) and (17) were used to determine aldehyde concentration in exhaust gas. [24]. By pass valves
-
were arranged for carbureted ethanol or air from atmosphere. Variable jet carburetor (19) was provided to carburet ethanol into the engine at different percentages of mass flow of diesel fuel at full load. Air box (20), orifice meter (21) and U-tube water manometer (22) were provided to measure rate of flow of air entering in to engine. Gas cylinder (23), pressure regulator (24), gas Using the Template
pressure sensor (25), flame arrestor (26) and rotometer
-
were employed to feed CNG into the engine by means of port injection. Ethanol was fed into the system through ethanol tank (28). Three way valve (29) and burette (30).Cam position senor was used to measure injection timing. Crank position sensor was used to determine the speed of the engine. Fuel temperature was determined with fuel temperature sensor. Gas was injected through gas injector. example, do not differentiate among departments of the same organization). This template was designed for two affiliations.
a)
Table.2
Range and accuracy of Analyzers
-
Engine, 2.Electical Dynamometer, 3.Load Box, 4. Outlet jacket water temperature indicator, 5.Outlet-jacket water flow meter Orifice meter, 6.Piezo electric pressure transducer, 7.TDC encoder, 8.Console, 9.Personal Computer, 10.Printer, 11.Exhaust gas temperature indicator, 12 AVL Smoke meter, 13.Netel Chromatograph multi-gas analyzer 14.Filter, 15. Rotometer, 16.Heater, 17.Round bottom flask containing DNPH solution, 18.Valves, 19. Variable jet carburetor, , 20.Air box, 21.Orific meter, 22.U-tube water manometer, 23. Gas cylinder, 24.Pressure regulator, 25.Gas pressure sensor, 26.Flame arrestor and 27 Rotometer, 28 Ethanol tank, 29 Three way valve and 30. Burette
-
Fig.2. Schematic diagram of experimental set up
The engine was provided with gravity lubrication system. Biogas was inducted through port injectionat the near end of compression stroke of the engine. There was facility to increase injection pressure by means of sensor.
S.No |
Name of the Analyzer |
Principl e adopted |
Range |
Accuracy |
1 |
AVL Smoke Analyzer |
Opacity |
0-100 HSU (Hartridge Smoke Unit) |
±1 HSU |
2 |
Netel Chromatograph CO analyzer |
Infrared absorptio n spectrogr aph |
0-10% |
± 0.1% |
3 |
Netel Chromatograph UBHC analyzer |
NDIR |
0-1000 ppm |
±5 ppm |
4 |
Netel Chromatograph NOx analyzer |
Chemilu miniscen ce |
0-5000pm |
±5 ppm |
S.No |
Name of the Analyzer |
Principl e adopted |
Range |
Accuracy |
1 |
AVL Smoke Analyzer |
Opacity |
0-100 HSU (Hartridge Smoke Unit) |
±1 HSU |
2 |
Netel Chromatograph CO analyzer |
Infrared absorptio n spectrogr aph |
0-10% |
± 0.1% |
3 |
Netel Chromatograph UBHC analyzer |
NDIR |
0-1000 ppm |
±5 ppm |
4 |
Netel Chromatograph NOx analyzer |
Chemilu miniscen ce |
0-5000pm |
±5 ppm |
With alcohol-CNG mixture operation, the major pollutant emitted from the engine is aldehydes. These aldehydes are carcinogenic in nature, which are harmful to human beings. The measure of the aldehydes is not sufficiently reported in the literature. DNPH method was employed for measuring aldehydes in the experimentation. [24]. The exhaust of the engine was bubbled through 2,4dinitrophenyl hydrazine (2,4 DNPH) solution. The hydrazones formed were extracted into chloroform and were analyzed by employing high performance liquid chromatography (HPLC) to find the percentage concentration of formaldehyde and acetaldehyde in the exhaust of the engine.
The test fuels of the investigations were i) neat diesel and
-
CNG and carbureted ethanol. The configurations or the versions of the engine were normal or base engine and insulated engine.
A catalytic converter [9] (Figure .3) was fitted to exhaust pipe of engine. Provision was also made to inject a definite quantity of air into catalytic converter. Air quantity drawn from compressor and injected into converter was kept constant so that backpressure does not increase.
-
Air chamber, 2. Inlet for air chamber from the engine, 3.Inlet for air chamber from the compressor, 4.Outlet for air chamber, 5.Catalytic chamber, 6.Outer cylinder, 7.Intermediate-cylinder, 8.Inner-cylinder, 9.Inner sheet, 10.Intermediate sheet, 11.Outer sheet, 12. Outlet for exhaust gases, 13. Provision to deposit the catalyst, and, 14.Insulation.
-
Figure.3. Details of Catalytic converter
Experiments were carried out on CE and SADE with different test fuels under different operating conditions of catalytic converter like set-A, without catalytic converter and without air injection; set-B, with catalytic converter and without air injection; and set-C, with catalytic converter and with air injection. The accuracy of the instrumentation used in the experimentation is 0.1%.
3.RESULTS AND DISCUSSION
The engine performance can be improved for percentage of induction of ethanol as ethanol is highly volatile and contains and contains oxygen in its molecular composition which improves combustion. Fig .4shows variation of BTE and BP with various percentage of ethanol induction in CE. As ethanol percentage increased the performance improved as ethanol reduced dissociation losses specific heat losses. Also, it contains oxygen in its molecular composition which leads to improve combustion.
-
To determine the maximum percentage induction of ethanol in CE and SADE
However the maximum % of ethanol induction was limited to be 40 % of the total mass of diesel fuel at fuel load, Hence the optimum induction of ethanol in CE was limited to be 40
% .As it is shown in the graph BTE increased with BP for
various percentage of ethanol up to 80 % of the full load this is due to improved air fuel ratio volumetric efficiency , mechanical efficiency and fuel conversion efficiency however beyond 80 % of load BTE decreased with an increase of BP. This is due to decrease of volumetric efficiency ,mechanical efficiency and fuel conversion efficiency.
Fig .5 shows variation of BTE and BP with various percentage of ethanol induction in SADE.
-
To determine the optimum injection timing for improve performance for CE as well as SADE for max percentage of induction of ethanol
It is always an advantage to advance the injection timing, as this improved the performance of the engine due to atomization characteristics of fuel with air. Fig.6 shows the variation of BTE with BP at different injection timings with CE with maximum induction of ethanol. The optimum injection timing was obtained at 32obTDC for CE with maximum induction of ethanol. OIT is the Injection timing at which the maximum BTE was obtained this is due to increase in atomization characteristics, i.e. , more time was available for the fuel to react with oxygen leading to improved combustion hence the OIT was obtained at 32obTDC for CE with maximum induction of ethanol
Fig.6. Variation of BTE with BP for various injection timings in SADE with maximum induction of ethanol
3.3. Pollution Levels
This is duty of thermal engineer to check the pollution levels also apart from performance of the engine. Fig.7 presents bar chart showing the variation of formaldehyde levels at full load for versions of the engine at
RIT and OIT with maximum induction of ethanol along with CNG. Aldehydes were determined by the wet method as it is a simple and not a laborious method. The advantage of wet method is individual aldehydes (acetaldehyde and formaldehyde) can be determined. .One of the disadvantages of using ethanol is aldehyde levels were increased. However SADE decreased aldehyde levels than CE at RIT and OIT as it improved the combustion with improved heat release rates and faster rate of combustion. Aldehydes decreased with advanced injection timings with both versions of the engines with maximum induction of ethanol along with CNG. This is due to improved atomization characteristics and faster rate of combustion with the fuel with oxygen. The purpose of CNG was to decrease aldehydes in both versions of the engine, due to gaseous combustion with methane with oxygen. SADE decreased formaldehyde levels at full load by 14% at RIT and 20% at OIT in comparison with CE.
.
Fig.7. Bar chart showing the variation of formaldehyde levels at full load
Fig.8 presents bar chart showing the variation of acetaldehyde levels at full load for versions of the engine at RIT and OIT with maximum induction of ethanol along with CNG.
Fig.8. Bar chart showing the variation of acetaldehyde levels at full load
Acetaldehydes showed the similar trends with formaldehydes with both versions of engine at RIT and OIT with maximum induction of ethanol along with CNG at full load. The concentration of acetaldehyde levels was marginally higher than formaldehyde levels for two versions of the engine with maximum induction of ethanol along with CNG at full load. This is due to presence of two carbon atoms of the ethanol making acetaldehydes levels higher. Acetaldehyde levels decreased with increase of advance injection timings along
for two versions of the engine with maximum induction of ethanol along with CNG at full load. This is due to improved combustion reactions of fuel with air and also due improved in expansion stroke. SADE decreased acetaldehyde levels than CE with diesel at RIT and OIT due to improved heat release rate and faster rate of combustions.SADE decreased acetaldehyde levels at full load by 12% at RIT and 16% at OIT in comparison with CE.
Table.3.
Data of Aldehydes at full load
Formaldehyde (% Concentration) |
Acetaldehyde (% Concentration) |
||||
IT |
Set |
CE |
SADE |
CE |
SADE |
Diesel |
7 |
— |
9 |
— |
|
RIT |
— |
— |
— |
— |
|
Set-A |
14 |
12 |
16 |
14 |
|
Set-B |
9 |
7 |
11 |
9 |
|
Set-C |
6 |
4 |
8 |
6 |
|
OIT |
— |
— |
— |
— |
— |
Set-A |
10 |
8 |
12 |
10 |
|
Set-B |
8 |
6 |
10 |
8 |
|
Set-C |
5 |
3 |
7 |
5 |
Table.3 shows data of aldehydes with different versions of the engine at RIT and OIT with maximum induction of ethanol along with CNG. Set-A denotes without use of catalytic converter, while Set-B denotes with the use of catalytic converter. Set-C denotes with the use of catalytic converter along with air injection. The catalyst used in the experiment was copper. The mass of the catalyst was found be optimum at 2 kg.
The air velocity was found to be optimum at 6 l/m. Set-B operation successfully reduced aldehydes, while Set-C operation further reduced aldehydes due to oxidation reaction. SADE decreased formaldehydes at full load with Set-B operation by 22% at RITand 25% at OIT in comparison with CE.SADE decreased formaldehydes at full load with Set-C operation by 33% at RIT and 40% at OIT in comparison with CE.SADE decreased acetaldehydes at full load with Set-B operation by 18% at RIT and 20% at OIT in comparison with CE.SADE decreased acetaldehyde at full load with Set-C operation by 25% at RIT and 28% at OIT in comparison with CE. This is due to improved heat release rate and faster rate of combustion.
3.CONCLUSIONS
The engine performance can be improved for percentage of induction of ethanol as ethanol is highly volatile and contains and contains oxygen in its molecular composition which improves combustion. Fig .4shows variation of BTE and BP with various percentage of ethanol induction in CE. As ethanol percentage increased the performance improved as ethanol reduced dissociation losses
specific heat losses. Also, it contains oxygen in its molecular composition which leads to improve combustion.
ACKNOWLEDGMENTS
Authors thank authorities of Chaitanya Bharathi Institute of Technology, Hyderabad for providing facilities for carrying out research work. Financial assistance provided by All India Council for Technical Education (AICTE), New Delhi, is greatly acknowledged.
REFERENCES
-
Cummins, C. Lyle, Jr. (1993). Diesel's Engine, Volume 1: From Conception To 1918. Wilsonville, OR, USA: Carnot Press,
-
Agarwal,A.K. Bio-fuels (alcohols and biodiesel) applications as fuels for internal combustion engines,International Journal Energy Combustion Science 226; 33:233-271.
-
Rasim, B. (2011). Performance and emission study of waste anchovy fish biodiesel in a diesel engine,Fuel Processing Technology 2011; 92: 1187-1194.
-
Jaichandar, S. and Annamalai, K. The status of biodiesel as an alternative fuel for diesel engine- An Overview, Journal of Sustainable Energy & Environment 2011; 2:71-75
-
RidvanArslan. (2011). Emission characteristics of a diesel engine using waste cooking oil as a bio-diesel fuel, African Journal of Bio- Technology 2011; 10(9):3790-3794.
-
Xue, J., Grift, T.E., Hansen, A.C. Effect of biodiesel on engine performances and emissions, Renewable and Sustainable Energy Reviews 2011; 15: 10981116.
-
McCarthy, P., Rasul, M.G., Moazzem, S. Analysis and comparison of performance and emissions of an internal combustion engine fuelled with petroleum diesel and different bio-diesels, Fuel 2011; 90: 2147 2157.
-
DurgaPrasadaRao, N., Murali Krishna, M.V.S., Anjeneya Prasad, B., and Murthy,P.V.K.Effect of injector opening pressure and injection timing on exhaust emissions and combustion characteristics of rice bran oil in crude form and biodiesel form in direct injection diesel engine. IOSRJournal of Engineering 2014; 4(2): 9-19.
-
Parlak, A., Yasar, H., ldogan O. The effect of thermal barrier coating on a turbocharged Diesel engine performance and exergy potential of the exhaust gas. Energy Conversion and Management 2005; 46(3): 489499.
-
Ekrem, B., Tahsin, E., Muhammet, C. Effects of thermal barrier coating on gas emissions and performance of a LHR engine with different injection timings and valve adjustments, Journal of Energy Conversion and Management 2006; 47:1298-1310.
-
Ciniviz, M., Hasimoglu, C., Sahin, F., Salman, M. S. Impact of thermal barrier coating application on the performance and emissions of a turbocharged diesel engine. Proceedings of The Institution of Mechanical Engineers Part D-Journal Of Automobile Eng 2008; 222 (D12):24472455.
-
RajendraPrasath, B., P. Tamilporai ,P., Mohd.Shabir, F. Analysis of combustion,performance and emission characteristics of low heat
rejection engine using biodiesel,International Journal of Thermal Sci 2010; 49:2483-2490.
-
MohamedMusthafa, M., Sivapirakasam, S.P. and UdayaKumar.M. Comparative studies on fly ash coated low heat rejection diesel engine on performance and emission characteristics fueled by rice bran and pongamia methyl ester and their blend with diesel. Energy 2011; 36(5): 2343-2351.
-
Ratna Reddy, T., Murali Krishna, M.V.S., Kesava Reddy, Ch. and Murthy, P.V.K. Performance evaluation of mohr oil based biodiesel in low grade low heat rejection diesel engine, International Journal of Innovative Research in Science, Engineering and Technology 2012; 1(1):80-94.
-
Vara Prasad, C.M, Murali Krishna, M.V.S., Prabhakar Reddy, C. and Rama Mohan, K. Performance evaluation of non-edible vegetable oils as substitute fuels in low heat rejection diesel engine. Institute of Engineers (London), Part-D, Journal of Automobile Engineering2000; 214(2):181-187.
-
Srikanth, D., Murali Krishna, M.V.S., UshasriP.and Krishna Murthy,P.V. Comparative studies on medium grade low heat rejection diesel engine and conventional diesel engine with crude cotton seed oil, International Journal of Innovative Research in Science, Engineering and Technology 013; 2(10): 5809-5228
-
Ratna Reddy, T., Murali Krishna, M.V.S., Kesava Reddy, Ch. and Murthy,P.V.K.Performance, exhaust emissions, and combustion characteristics of mohr oil in crude form and biodiesel; form in a medium grade low heat rejection diesel engine. International journal of Engineering Research and Development 2013; 2(5):58-70.
-
Murali Krishna, M.V.S., DurgaPrasadaRao, N., Anjenaya Prasad, B. and Murthy,P.V.K.Investigations on performance parameters with medium grade low heat rejection combustion chamber with rice brawn oil biodiesel. International Journal of Applied Engineering Research and Development 2014; 4(1):2946.
-
Abdelaal, M.M., Hegab,A.H. (2012). Combustion and emission characteristics of a naturalgas-fueled diesel enginewith EGR, Energy Conversion and Management 2012; 64 (1):301312.
-
M.I.Jahirul, H.H.Masjuki, R.Saidur, M. A. Kala, M. H.Jayed (2010) Comparative engine performance &emission analysis of CNG Fuelled engine,Applied Thermal Engineering 2010; 30: 2219-2226
-
MundeGopal G., Dr. DaluRajendra S. Compressed natural gas as an alternative fuel for spark ignition engine: A review, International Journal of Engineering and Innovative Technology2012 ; 2(6):25-33.
-
YasinKaragoz,TarkanSandalc, Umit O Koylu , AhmetSelimDalklcx and SomchaiWongwise (2016). Effect of the use of natural gasdiesel fuel mixture on performance, emissions, and combustion characteristics of a compression ignition engine – Advances in Mechanical Engineering 2016; 8(4): 113. DOI: 10.1177/1687814016643228,
-
Sainna, G., Murali Krishna, M.V.S., Usha Sri, P. and Ravi Chandra, M. Experimental investigations on exhaust emissions of semi-adiabatic diesel engine with exhaust gas recirculation, International Journal of Pollution Research;39(3):172-178.
-
Murali Krishna, M.V.S., SeshagiriRao, V.V.R., Kishan Kumar Reddy, T.and Murthy, P.V.K. Performance evaluation of high grade low heat rejection diesel engine with carbureted alcohol and crude jatropha oil, Renewable and Sustainable Energy Reviews 2014; 36:1 19.