
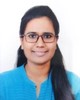
- Open Access
- Authors : Kalyani Shende, Shreyas Shingavi, Vishesh Rane
- Paper ID : IJERTV14IS030158
- Volume & Issue : Volume 14, Issue 03 (March 2025)
- Published (First Online): 03-04-2025
- ISSN (Online) : 2278-0181
- Publisher Name : IJERT
- License:
This work is licensed under a Creative Commons Attribution 4.0 International License
Correlation of Virtual and Physical Testing for Three-Wheeler Handling and Road Load Data Acquisition
Kalyani Shende (Author)
ER&D,
Tata Technologies Ltd Pune, India
Shreyas Shingavi
ER&D,
Tata Technologies Ltd Pune, India
Vishesh Rane
ER&D,
Tata Technologies Ltd Pune, India
Abstract
Three-wheeler vehicles are a cheaper mode of transportation in many parts of the world, especially in densely populated urban areas. Three-wheeler vehicles present unique challenges in handling stability and road load performance, necessitating a thorough understanding of their dynamic behavior across various driving conditions. There has been a least number of studies focusing on the correlation of Multibody Dynamics (MBD) simulations specifically for three-wheelers. The accuracy of three-wheeler MBD simulations has been a concern, particularly in replicating physical test scenarios under non-ideal conditions. However, as MBD models have evolved, they have become increasingly precise, leading to significant reductions in vehicle testing costs and time. By correlating MBD simulations with physical RLDA and handling test results, this research demonstrates the growing reliability of MBD as a tool for predicting vehicle dynamics.
This paper explores the correlation between physical and virtual handling characteristics and Road Load Data Acquisition (RLDA) parameters using Multibody Dynamics (MBD) analysis. Basic handling tests, including Double Lane Change (DLC), Constant Radius Cornering (CRC) and Straight-line Braking (SLB) were conducted to assess vehicle performance. Key performance metrics, including peak lateral acceleration, roll angle, and braking distance, were analyzed to establish the fidelity of the MBD model. For the RLDA study, Time Series Wheel Center Displacement (TSWCD) and wheel acceleration data were utilized as inputs for the MBD model to replicate real- world behavior of the suspension. Physical and virtual model correlation done by comparing spring displacement and chassis acceleration. The findings underscore how MBD can enhance vehicle design processes, improving simulation accuracy and contributing to the development of safer and higher-performing three-wheeler vehicles. This study provides a comprehensive framework for integrating MBD into modern vehicle development strategies.
Keywords Vehicle Dynamics, Three-wheeler, Multibody Dynamics, Handling Analysis, Road Load Data Acquisition
INTRODUCTION
Three-wheelers are gaining attention for their engineering benefits, such as a lighter chassis with reduced twisting loads, improved aerodynamics, and lower production costs due to fewer components. In many western countries, they are classified as motorcycles, allowing for reduced license fees and taxes, and in some cases, low speed models are exempt from stringent safety regulations [1]. These vehicles are widely used in various regions, particularly in urban and rural areas, where their compact size and maneuverability are advantageous. However, the inherent instability due to their design requires rigorous analysis and optimization of their handling characteristics and road load data (RLD) parameters to ensure safe and reliable performance under different driving conditions.
This research paper investigates the relationship between physical and virtual handling and Road Load Data Acquisition (RLDA) parameters in three-wheeled vehicles, utilizing Multibody Dynamics (MBD) analysis as the primary methodology.
The study focuses on three critical driving scenarios: Double Lane Change (DLC), Constant Radius Cornering (CRC) and Straight-Line Braking (SLB). These scenarios are particularly significant in evaluating a vehicles handling performance and stability. For DLC and CRC, the key outputs analyzed include peak lateral acceleration and peak roll angle, which are indicative of the vehicle's responsiveness and stability during abrupt maneuvers [2]. For Straight-Line Braking, the primary outputs are braking distance and time, which are crucial for assessing the vehicle's stopping capability under emergency conditions.
Using rough roads in Road Load Data Acquisition (RLDA) helps simulate real-world conditions and understand how vehicles perform under vertical loads. Rough surfaces introduce dynamic inputs that test vehicle durability, reliability,
and overall ride performance [3]. Braking at low speeds and executing turns are crucial for assessing the vehicle's longitudinal and lateral performance respectively [4]. Therefore, the following tests have been selected: driving on rough roads, braking at 10 km/h, and cornering- a left turn.
By correlating the physical and virtual parameters through MBD analysis, this study aims to bridge the gap between experimental data and simulation results, providing a comprehensive understanding of the dynamic behavior of three-wheeler vehicles. The insights gained from this research can contribute to the development of safer and more efficient vehicle designs, particularly in optimizing handling performance and improving stability under various driving conditions.
LITERATURE REVIEW
This literature review examines the correlation between multibody dynamics (MBD) simulations and physical testing methodologies for assessing the handling and road load characteristics of three-wheeled vehicles. Defining the Three- wheelers vehicle performance requires extensive testing that includes double lane changes, steady-state cornering, and straight-line braking. Research indicates that the stability of three-wheelers during double lane changes is significantly influenced by factors such as center of gravity and weight distribution. Studies have shown that MBD simulations can effectively predict vehicle dynamics, including lateral acceleration and rollover risk [5]. Constant radius cornering is critical for understanding a vehicle's lateral stability and grip during turns, allowing for the measurement of peak lateral acceleration, a key indicator of a vehicle's ability to maintain control and prevent rollover [6]. Evaluating straight-line braking performance is also crucial for understanding a vehicle's stopping capabilities and stability during deceleration. This load case measures braking distance, time and deceleration characteristics, which are vital for assessing the effectiveness of the braking system, ensuring compliance with safety standards, and optimizing vehicle performance. [7].
The RLDA process is vital for evaluating vehicle performance under various driving conditions. In rough road tests, utilizing Time Series Wheel Center Displacement (TSWCD) allows for a detailed assessment of how a vehicle interacts with irregular road surfaces. The integration of multi-body dynamics (MBD) models enhances the accuracy of the simulation by capturing the complex dynamics involved during wheel interactions with the road. For instance, research by Zhou et al. highlights a methodology for load simulation on impact roads, utilizing wheel force transducers to validate the accuracy of MBD models against real-world data [8]. Such methodologies demonstrate the capacity of TSWCD to reflect dynamic load responses accurately, which is crucial for vehicle durability and performance assessments.
In addition to rough road tests, brake tests at low speeds, such as 10 km/h, provide insights into the vehicle's stopping behavior and load responses during deceleration. The application of TSWCD in these scenarios allows for real-time analysis of wheel acceleration and load data, enabling engineers to refine vehicle stability and safty measures. The work of Shao et al. emphasizes the significance of virtual
proving ground simulations for evaluating vehicle durability and ride comfort, underscoring the relevance of TSWCD in a comprehensive testing regime [9]. Moreover, the digital RLDA methodology proposed by Avhad and Iqbal showcases a way to capture loads, strains, and accelerations using digital models, providing a robust alternative to traditional physical testing [10]. Furthermore, cornering tests, particularly left turns, are critical for assessing lateral load transfers and overall vehicle handling. The synergy between TSWCD and physical testing informs better design and tuning of suspension systems to optimize vehicle dynamics under cornering conditions.
The integration of multibody dynamics simulations with physical testing is vital for accurately understanding the handling and road load characteristics of three-wheeled vehicles. This combined approach enhances performance evaluations, ultimately contributing to improved vehicle safety and efficiency.
METHODOLOGY
MBD Model
The model-building process commences with engineers accessing the template models available within commercial engineering application software and it is widely used to model, simulate, and analyse different vehicles and their sub- systems. These template models serve as foundational structures that encompass essential components such as chassis, suspension systems, wheels, and other vehicle elements. These templates are modified to get the desired vehicle model.
Figure 1. MBD Model of 3W Cargo Vehicle in Engineering Software
Virtual model inputs are taken from physical vehicle as shown in Table 1 to ensure a high degree of similarity and accuracy in the simulations. The tire parameters, along with the spring and damper properties, are replicated same as physical test vehicle parameters for the MBD model. The Magic Formula (MF) tire model is used for its ability to simulate complex, non-linear tire forces and moments, which are crucial for vehicle dynamics simulations [11]. The integration of these parameters ensures that the model can realistically replicate the real-world vehicle's response under various road conditions, contributing to more accurate predictions and analyses.
TABLE 1. MBD MODEL INPUTS BASED ON PHYSICAL VEHICLE PARAMETERS
Parameter |
Unit |
Value |
Wheelbase |
mm |
1200 |
Weight |
kg |
1100 |
SLR Front |
mm |
232 |
SLR Rear |
mm |
229.6 |
CG Height |
mm |
633 |
Suspension type |
Front |
Leading link with damper |
Rear |
Rear swing arm coil springs |
Physical Testing Setup (Vehicle A) Handling
The test setup for evaluating vehicle dynamics includes a range of instruments (Figure 2). The IMU Gyro RT3100 captures crucial angular rate and acceleration data, essential for assessing cornering parameters and straight-line braking performance. Complementing this, the steering angle sensor provides precise measurements of steering inputs, while strain gauges measure the associated steering torque and dynamic loads. Data from these sensors are captured and analyzed through the Somat eDaq 16-channel system, offering a comprehensive view of the vehicles behavior under various conditions. Together, these tools enable a detailed evaluation of handling properties, including Double Lane Change, Constant Radius Cornering, and Straight-Line Braking, ensuring optimal vehicle performance in handling.
Figure 2. Handling Test Setup
-
Constant Radius Cornering (CRC): Test done as per ISO 4138 [12] guidelines for steady state circular driving behavior at constant radius (5m) with continuous increasing speed until the desired path could not be followed. Test was conducted in Anti-Clockwise (ACW) direction as per the standard. This comprehensive approach allows for a thorough evaluation of the vehicle's handling characteristics and performance during cornering maneuvers in left turn. By conducting the test in left direction, engineers can gather insights into the vehicle's balance, rollover stability, and responsiveness under varying driving conditions.
-
Double Lane Change (DLC): The ISO 3888-2 [13] standard outlines the procedure for conducting the Double Lane Change test, a critical evaluation method used to assess the dynamic handling characteristics of vehicles. The test is typically conducted on a specially designed facility Dynamic Pad.
This Dynamic Pad provides a controlled environment for conducting dynamic vehicle tests, ensuring precise measurements and consistent testing conditions. It consists of a large, paved surface with defined lanes and markings, allowing the accurate maneuvering and data collection during tests.
The DLC test conducted on the Dynamic Pad involves the vehicle making rapid lane changes to the left and right while maintaining stability and control within specified parameters. This test assesses the vehicle's roll properties, ability to respond to steering inputs and maintain stability during dynamic maneuvers.
Figure 3. DLC Track as per Standards
-
Straight Line Braking (SLB): The straight-line braking test is a standardized evaluation method used to assess a vehicle's braking performance under controlled conditions. In this test, the vehicle is allowed to accelerate to its maximum speed, as per standard it is typically set at 90% of top speed, on a straight and level surface. Once the desired speed is reached, the driver applies the brakes with maximum force to bring the vehicle to a complete stop as quickly as possible.
Road Load Data Acquisition (RLDA)
The goal is to capture road loads experienced by three-wheeler while moving on different surfaces. This is done by equipping appropriate transducers including accelerometers, strain gauges, displacement sensors, and IMU-RT (Inertial Measurement Unit with Real-Time capabilities) strategically positioned at specified locations (Table 2).
The following roads are recommended by reputed testing agency for accelerated durability testing of three-wheelers, simulating the equivalent of 80,000 kilometers of real-world driving:
-
Rough Road: The vehicle is subjected to driving on rough terrain to simulate real-world road conditions. Accelerometers and strain gauges are strategically placed to measure the vehicle's response to uneven surfaces, bumps, and vibrations. IMU-RT sensors provide real-time data on the vehicle's orientation and movement, helping assess its stability and handling on rough roads.
-
Brake at 10km/h: A braking test is conducted at a speed of 10km/h to evaluate the vehicle's braking performance under controlled conditions. Displacement sensors and strain gauges are installed to measure the deformation and stress on critical components during braking. Accelerometers capture the vehicle's deceleration rate, while IMU-RT sensors monitor any changes in orientation and stability during braking maneuvers.
-
Left Turn: The left turn test is designed to assess the road load data acquisition during a left-hand cornering maneuver. It involves subjecting the vehicle to a predefined left turn under controlled conditions, where various dynamic parameters, such as lateral acceleration and wheel displacement, are measured. These data help evaluate the spring displacement and chassis acceleration.
TABLE 2. SENSOR USED FOR RLDA TEST
Sr. No.
Sensor
No. of Channels
<>1 Strain Gauges
3
2
Displacement Sensor
3
3
Accelerometers
24
4
GPS Module
4
5
IMU – RT
25
Total Analogue Channels
30
Total Digital Channels
29
Instrument setup is as follows:
-
-
Chassis Accelerometer
Figure 4. Chassis Accelerometer
-
Power Unit Accelerometer
Figure 5. Power Unit Accelerometer
-
Displacement Sensor
Figure 6. Displacement Sensor
-
Strain Gauge location
Figure 7. Strain Gauges
Virtual Testing Setup (Vehicle B) Handling
-
Constant Radius Cornering: For the constant radius
cornering test, a model track template with a 5-meter radius was utilized. Turned direction set to left to ensure Anti-clockwise turning. The initial vehicle speed was set to 5 km/h, and the vehicle was then progressively accelerated to reach its top speed. During the test, the vehicle navigated around the circular path of the specified radius while maintaining a steady state. Resulting Lateral Acceleration behavior as shown in Figure 9.
Figure 8. CRC Virtual Setup
Figure 9. Lateral Acceleration vs Time during CRC Event
-
Double Lane Change: For the Double Lane Change (DLC) test, the path was set according to the specifications outlined in ISO 3888-2 [13]. This standard provides guidelines for the layout and dimensions of the test path used to assess a vehicle's dynamic handling capabilities during rapid lane change maneuvers. The highest velocity achieved during the test was 32.5 km/h, so all outputs were recorded at that speed.
Vehicles Lateral acceleration and roll angle graphs are provided (Figure 11 and Figure 12).
Figure 10. DLC Virtual Track Setup
Figure 11. Lateral Acceleration during DLC Test
Figure 12. Vehicle Roll Angle during DLC Test
-
Straight Line Braking: For the straight-line braking (SLB) test, the procedure involves allowing the vehicle to accelerate until it reaches 90% of its top speed. Once this speed is attained, the brakes are applied to initiate the braking maneuver.
During the SLB test, the vehicle's deceleration rate is controlled and applied using a predefined template within the software. This template sets the parameters for the braking event, including the rate at which the vehicle's speed decreases over time.
Vehicle CG displacement graph describes vehicle brake actuation after 2 seconds. Whereas force transfer graphs given to understand weight transfer in vehicle.
Figure 13. Straight Line Braking Virtual Setup
Figure 14. Vehicle CG Displacement vs Time during SLB test
Figure 15. Wheel Vertical Force vs Time
Road Load Data Acquisition
A key aspect of this RLDA framework is the use of Time Series Wheel Center Displacement (TSWCD) as the primary input. TSWCD is a vital parameter that captures the vertical displacements of the wheel center, which directly reflect the road-induced loads on the vehicle [14]. By incorporating TSWCD, outputs in form of displacement, forces and moments can be extracted at chassis attachment locations like suspension linkages joints with chassis, spring tops, etc. This enhancement in fidelity is crucial for obtaining reliable data that can be used to predict the vehicle's performance under various driving scenarios.
Moreover, the model integrates Center of Gravity (CG) longitudinal acceleration during braking to simulate the deceleration forces experienced by the vehicle. This component of the model is essential for replicating the forward shift of the vehicle's mass during braking, which significantly affects load transfer and braking performance. Similarly, CG lateral acceleration is introduced during cornering events to replicate the lateral forces that arise during turns [15]. These forces play a critical role in determining the vehicle's stability and handling characteristics, making them indispensable elements in the overall analysis.
Figure 16. Vehicle RLDA Setup in Software
Input correlation for virtual RLDA models:
-
Rough Road: In the physical vehicle testing, the wheel center displacement (Figure 17) and wheel center acceleration (Figure 18) graphs were used as input for the virtual model. These inputs allowed for the simulation and correlation of chassis acceleration and spring displacement, providing a comparison between physical and virtual test results.
Figure 17. Wheel Center Displacement: Front, Rear Left, Rear Right
Figure 18. Wheel Center Acceleration: Front, Rear Left, Rear Right
-
Brake at 10kmph: In the RLDA data, the longitudinal acceleration during braking was measured at 0.8 g. For the virtual model, the wheel center displacement (Figure 19) and wheel center acceleration (Figure 20) graphs obtained from physical vehicle testing were used as inputs.
-
Figure 19. Wheel Center Displacement: Front, Rear Left, Rear Right
Figure 20. Wheel Center Acceleration: Front, Rear Left, Rear Right
-
Left Turn: In the RLDA data, the lateral acceleration during the left turn was recorded as 0.3 g. During physical vehicle testing, the wheel center displacement (Figure 21) and wheel center acceleration (Figure 22) graphs were captured which used as input for the virtual model.
Figure 21. Wheel Center Displacement: Front, Rear Left, Rear Right
Figure 22. Wheel Center Acceleration: Front, Rear Left, Rear Right
CORRELATION
To enhance correlation, we develop a virtual model incorporating flexible bodies and non-linear stiffness data for components such as bushes and springs. This approach allows us to accurately replicate real-world scenarios, ensuring that our simulations reflect the complex behaviors of these elements under various conditions. By integrating detailed material properties and dynamic responses, we can achieve a more reliable correlation between our model predictions and actual performance, ultimately leading to improved design and analysis outcomes.
Handling
TABLE 3. HANDLING RESULTS COMPARISON (VEHICLE A- PHYSICAL TEST VEHICLE RESULTS, VEHICLE B-VIRTUAL TEST VEHICLE RESULTS)
Test Cases |
Outputs |
|||
Parameter |
Units |
Vehicle A |
Vehicle B |
|
Constant Radius Cornering |
Peak Lateral Acceleration |
g |
0.47 |
0.45 |
Double Lane Change |
Peak Lateral Acceleration |
g |
0.38 |
0.35 |
Peak Roll Angle |
deg |
6.57 |
5.98 |
|
Straight Line Braking |
Braking Distance |
m |
15.19 |
14.58 |
Braking Time |
sec |
2.37 |
2.25 |
As observed in the data presented in Table 3, a maximum deflection of 10% is consistently noted between the results obtained from physical testing and those generated through virtual simulations. This finding indicates a close alignment between the real-world performance of the vehicle and the predictions made by our virtual testing methodology. Such a minimal deviation underscores the accuracy and reliability of our simulation approach in capturing the dynamic behavior of the vehicle undr various driving conditions.
Road Load Data Acquisition
In the Road Load Data Acquisition (RLDA) tests, the movement of the vehicle's Center of Gravity (CG) plays a critical role in understanding the dynamic behavior of the vehicle. When the CG moves during cornering, braking, or while traversing rough terrain, it affects the compression and expansion of the springs, as well as the acceleration experienced by the chassis in various directions. To study these effects, graphs depicting chassis acceleration and spring displacement are obtained and then correlated. These correlations provide insights into the suspension system's behavior, chassis response, and overall vehicle dynamics. Such analysis is essential for validating both physical and virtual test results, ensuring that the vehicle maintains stability and optimal performance under varying conditions.
The red line represents the results from physical testing, while the blue line corresponds to the outcomes from virtual simulation. In simulation, max acceleration levels at chassis location are comparable with physical RLDA data. Also, the number of cycles and trend of displacement channels are captured.
-
Rough Road: Spring displacement (Figure 23) for all three wheels and Chassis accelerations (Figure 24) at different locations are captured and curves correlated as shown below:
Figure 23. Spring Displacement: Front, Rear Left, Rear Right
Figure 24. Chassis Acceleration: Front, Rear Left, Rear Right
-
Brake at 10kmph: During braking at 10 km/h, the vehicle's center of gravity shifts forward, resulting in the following spring displacement (Figure 25) and chassis acceleration (Figure 26) graphs:
Figure 25. Spring Displacement: Front, Rear Left, Rear Right
Figure 26. Chassis Acceleration: Front, Rear Left, Rear Right
-
Left Turn: During a left turn, the vehicle's center of gravity shifts laterally, leading to the below spring displacement (Figure 27) and chassis acceleration (Figure 28) graph results:
-
Figure 27. Spring Displacement: Front, Rear Left, Rear Right
Figure 28. Chassis Acceleration: Front, Rear Left, Rear Right
As observed in the graphs, the red line represents the physical test results, while the blue line represents the MBD (Multibody Dynamics) test results. Both lines closely overlap, indicating a strong correlation between the physical and virtual tests. Additionally, the overall trend of the chart shows a consistent match between the two sets of results, demonstrating the accuracy of the MBD model in replicating the real-world vehicle behavior.
CONCLUSION
This study validates that Multibody Dynamics (MBD) three- wheeler model provide accurate results, closely matching physical test outputs across various conditions, including lateral, longitudinal, and vertical dynamics. Thus, use of virtual MBD testing offers substantial cost and time savings by reducing the need for physical prototypes and its testing by enabling rapid development through virtual testing. Its flexibility in simulating various scenarios enhances three- wheeler vehicle performance understanding. The close correspondence between MBD and physical results highlights the effectiveness of MBD as a valuable tool for optimizing design and performance in three-wheelers.
The slight deviation observed in the graph may be due to factors such as differences in modeling friction coefficients or contact dynamics in tire files and road files. Variations in environmental conditions, such as temperature or humidity, can alter material properties or sensor reading and affect test results. Numerical methods and solver settings used in simulations may introduce approximation errors, while insufficient time resolution or simulation duration can impact the accuracy of transient dynamics. Also incorporating more flexible bodies and non-linear stiffness data in virtual model will lead to accuracy. Addressing these factors can further help in getting more accurate results.
REFERENCES
-
Van Valkenburgh P. G., Klien R. H., Kanianthra J. "Three-Wheel Passenger Vehicle Stability and Handling". SAE 820140. 1982
-
Guiggiani, M., The Science of Vehicle Dynamics: Handling, Braking, and Ride of Road and Race Cars, Springer, 2014.
-
Schudt, J., R. Kodali, M. Shah, and G. Babiak. 2011. "Virtual Road Load Data Acquisition in Practice at General Motors." SAE Technical Paper 2011-01-0025. https://doi.org/10.4271/2011-01-0025.
-
Fukushima, T., Shimonishi, H., Torigaki, T., Miyachi, T. et al., "Vehicle Cornering and Braking Behavior Simulation Using a Finite Element Method," SAE Technical Paper 2005-01-0384, 2005, https://doi.org/10.4271/2005-01-0384.
-
Huston, J., Graves, B., and Johnson, D., "Three Wheeled Vehicle Dynamics," SAE Technical Paper 820139, 1982, https://doi.org/10.4271/820139.
-
Kading, R. and Crosheck, J., "Computer Simulation of Three Wheeled ATV in Constant Radius Turns," SAE Technical Paper 891107, 1989, https://doi.org/10.4271/891107.
-
Gillespie T. D. Fundamentals of Vehicle Dynamics, SAE International. R-114, ISBN of 978-1-56091-199-9.
-
Zhou, S., Yu, H., Zhu, C., and Liu, H., "Load Simulation of the Impact Road under Durability and Misuse Conditions," SAE Technical Paper 2023-01-0775, 2023, https://doi.org/10.4271/2023-01-0775.
-
Shao, Jian & Zhou, Yunping & Wang, Hua & Zhou, Shuai & Jiang, Zhongling & Wang, Wenjuan. (2021). Virtual Proving Ground Simulation in Practice for Vehicle Durability and Ride Comfort Performance. 10.1007/978-981-15-7945-5_9.
-
Avhad, A. and Iqbal, S., "Digital Road Load Data Acquisition Methodology for Automotive Durability Analysis," SAE Technical Paper 2021-26-0344, 2021, https://doi.org/10.4271/2021-26-0344.
-
Lugnér, Peter, Hans B. Pacejka and Manfred Plöchl. Recent advances in tyre models and testing procedures. Vehicle System Dynamics 43 (2005): 413 – 426.
-
ISO. 2021. ISO 4138:2021. Passenger CarsSteady-State Circular Driving BehaviourOpen-Loop Test Methods. Geneva: International Organization for Standardization.
-
ISO. 2011. ISO 3888-2:2011. Passenger CarsTest Track for a Severe Lane-Change ManoeuvrePart 2: Obstacle Avoidance. Geneva: International Organization for Standardization.
-
Pacejka, H. B., Tire and Vehicle Dynamics, 2nd ed., Butterworth- Heinemann, Oxford, UK, 2012
-
Milliken, W. F., and Milliken, D. L., Race Car Vehicle Dynamics, SAE International, Warrendale, PA, 1995.
ABBREVIATION
MBD |
Multibody Dynamics Three-Wheeler Vehicle Double Lane Change Constant Radius Cornering Road Load Data Acquisition Straight Line Braking Centre of Gravity Time Series Wheel Center Displacement Inertial Measurement Unit with Real-Time capabilities Anti-Clockwise International Organization for Standardization Static Loaded Radius |
3W |
|
DLC |
|
CRC |
|
RLDA |
|
SLB |
|
CG |
|
TSWCD |
|
IMU-RT |
|
ACW |
|
ISO |
|
SLR |