
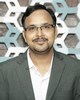
- Open Access
- Authors : Kuldeep Kumar , Dr. Virendra Kumar Paul , Abhijit Rastogi , Sumedha Dua
- Paper ID : IJERTV11IS040015
- Volume & Issue : Volume 11, Issue 04 (April 2022)
- Published (First Online): 11-04-2022
- ISSN (Online) : 2278-0181
- Publisher Name : IJERT
- License:
This work is licensed under a Creative Commons Attribution 4.0 International License
Critical Review of Common Inadequacies in Project Scheduling
Kuldeep Kumar1*
1 Ph.D. Scholar,
Department of Building Engineering and Management School of Planning and Architecture,
New Delhi, 110022, INDIA
Dr. Virendra Kumar Paul2
2 Professor and Head,
Department of Building Engineering and Management School of Planning and Architecture,
New Delhi, 110022, INDIA
Abhijit Rastogi3
3 Assistant Professor,
Department of Building Engineering and Management School of Planning and Architecture,
New Delhi, 110022, INDIA
Sumedha Dua4
4 Ph.D. Scholar,
Department of Building Engineering and Management School of Planning and Architecture,
New Delhi, 110022, INDIA
Abstract – Scheduling is one of the vital functions in construction projects to control the sequence of activities and tasks necessary to accomplish a project. A construction project has different requirements and the aim of scheduling (through adopted software) is to fulfill those requirements effectively in terms of the duration of the project and cost. In addition, the issues pertaining to scheduling must be considered planning the timeline of the project. Hence, it's is difficult for the project managers and schedulers to monitor as well as to control the issues caused by ineffectiveness and inadequacy in scheduling and lack of construction information. Moreover, as the project size increases, the construction's activities become more stringent and the conflict in the sequence of the activities occurred due to inefficient planning and inadequate scheduling. This paper aims to identify the common inadequacies during the project scheduling inadequacies and subsequently providing suitable mitigation measures and recommendations.
Keywords Project Scheduling, Scheduling Inadequacies, Scheduling Mistakes, Good Practices, Relative Importance Index
-
INTRODUCTION
Construction projects are multifaceted temporary endeavors and still, a detailed schedule with activities or tasks linked with logical relationships allows the overall project to be managed into simplified phases. Project scheduling ensures the development of effective schedule models through the application of skills, tools, techniques, and intuition acquired through knowledge, formal and informal training, and experience (PMI, 2019). It becomes critical to refine the scheduling process in a typical construction project environment due to several reasons like inadequate or insufficient planning, added decomposition of the project scope, project changes, logistic changes, or environmental changes. These reasons lead to this iterative progress which is required to forecast, identify as well as to address the growing issues that could potentially affect project performance. The purpose of the organized construction project schedule is to provide a beneficial road map that can be used by the project team and the project manager in accomplishing the project successfully and effectively. During the study of Project Schedule Recovery through the utilization of floats by (Kumar, et al., 2020), it was inferred that there are various inadequacies in project scheduling that needs to be addressed for an efficient project schedule. This has particular significance for tracking and monitoring the progress of a project.
According to (Paul & Basu, 2018), tools, techniques, and scheduling are significant in the construction sector. In their research (Paul & Basu, 2018) highlighted the important time management operates in conjunction with other interdependent processes of project management, wherein an efficient project scheduling process plays a vital role. In addition, the dynamic nature of a construction project's execution is best aided by a tool that caters to the project's internal as well as external dependencies and the possibility of analysis required to be done due to the impact of progress and risk events. Besides, in a study pertaining to the challenges for the Indian construction industry, (Sawhney, et al., 2014) revealed the sector is confronted by numerous issues, thereby reducing its efficacy and unhindered growth prospects, wherein the timely delivery of the project is one of the major issues. Hence, through an efficient project scheduling without any inadequacy can be a appropriate approach in envisaging the future delays and addressing the same though suitable and proactive steps towards the mitigation.
Below are the common scheduling mistakes seen in reviewing project schedules for numerous projects over the years (Lukas, 2007)
-
Lack of scheduling knowledge
-
Inappropriate level of detail
-
Incorrect schedule logic
-
Lack of schedule contingency
-
Presence of hangers
-
Constraints misuse
-
Confusing duration and work
-
Linking summary tasks
-
Not using start and complete milestones
-
Not using the project summary task, header, footer, and legend
Inadequate project scheduling relating to resource unavailability, material estimation, realistic duration of activities may lead to project complexities resulting in disputes further leading to considerable resource spending on heavy litigation processes, non- addressal to staffing issues limiting agencys contract oversight capabilities.
Lack of sufficient stress on scheduling tools / techniques can lead to:
-
Erroneous forecasts on usage projections, demographic trends, imminent technological hassles,
-
Inadequate understanding of local environment
-
Due diligence decisions and ascertainment of risks / changes in variable factors not matching the already established decision-making process
-
Absence of new ideas being brought in causing short sighted habits and thinking.
-
-
OBJECTIVES
-
Identifying the scheduling inadequacies from the literature and industry experts.
-
Prioritizing the identified inadequacies or inefficacies through questionnaire survey and ranking method.
-
To establish the top inadequacies in scheduling along with their mitigation measures
-
-
PRIORITIZING THE SCHEDULING INADEQUACIES
Subsequent to the inadequacies identified in the previous sections through literature (PMI, 2019) (Emma, 2015) (Lukas, 2007) (Schott, 2017) and case examples, a survey was carried out with the aim to gather expert opinions regarding the inadequacies/inefficacies in the project scheduling practices.
The response was obtained through the rating with respect to the possibility of happening of inadequacies/inefficacies (at a scale of 1 to 5) in the project scheduling practices, where: 1-Low probability, 3 Medium/ average probability and 5 Very High probability. The respondents for this survey include the various industry experts including the Architects, Design Managers, Planning Engineers, Project Managers, Engineers and Academicians. The experience of the respondents is divided in to three range of below 2, 2 to 5, above 5 years
-
Questionnaire
The questionnaire consists of 20 inadequacies identified from literature, pilot project, case study and industry experts opinion. The identified inadequacies / inefficacies are:
-
Lack of scheduling knowledge (of the scheduler/planner)
-
Insufficient project details available (before the start of the schedule)
-
Documentation of schedule upgradation is not maintained (Lack of regular reviews)
-
The chedule is Out of Date (schedule is not updated frequently or as per requirement)
-
Broken critical path (missing dependency) and not closing the loop
-
Errors in technical logic (Improper logical relationship between the activities)
-
Incomplete schedule (Work started with partly approved schedule) or not getting the schedule signed-off (work started without getting prior approval)
-
Procurement of the critical materials is not included in the schedule
-
Weather restraints are not considered (extreme summers/winters, heavy rainfall, etc.)
-
Lack of Contingency (for known unknowns and unforeseen circumstances)
-
Floats and its utilization is not considered or included in the scheduling
-
Actual Resources are not considered (unlimited resources are considered mostly)
-
Durations and Productivity are unrealistic
-
Presence of hangers (an activity with no successors, leading to unrealistic float)
-
Ignoring inspections and testing of the materials/works
-
Imposing lots of Constraints on activities and milestones (leading to the reduction in flexibility and creation of negative floats)
-
Presence of concurrent activities (a lot of similar tasks scheduled to happen at the same time leading to resource overallocation)
-
Overlooking Holidays (inappropriate use of calendar and consideration of working / non-working timings)
-
Not setting the baseline as well as revising it as per the requirement.
-
Understanding and application of task types (duration, work, and units) and their relation (Duration * Units = Work) in the scheduling
-
-
Results
The response was obtained from 52 respondents of which the major ones are Project Manager, Planning Engineers, and Architects as shown in the Figure 3.1.1 and Figure 3.1.2
Figure 3.1.1 : Bifurcation of responses on the basis of their designation
Figure 3.1.2: Bifurcation of responses on the basis of the years of experience of the respondents
The responses obtained are categorized in two parts based on the year of experience of the respondents, i.e. the data obtained from the respondents with experience above 5 years and the other with experience below 5 years. It is also noticed that the inadequacy Overlooking Holidays (inappropriate use of calendar and consideration of working / non-working timings) has got least ranking among all which means that attention to the holidays / calendars is well taken into consideration during the scheduling.
-
RII (RELATIVE IMPORTANCE INDEX) For Ranking
The Relative Importance Index (RII) method is used to prioritize the inadequacies through ranking. Relative Importance Index, is the mean for a factor which gives it weightage in the opinions of respondents
Calculation of RII
RII = W / (A*N)
where,
W is the weighting given to each factor by the respondents (ranging from 1 to 5), A is the highest weight (i.e. 5 in this case), and
N is the total number of respondents.
Higher the value of RII, more possibility of occurring that inadequacy in the project scheduling. The relative importance index, RII, is computed for each inadequacy to identify the most significant inadequacies that are happening or occurring in the construction project scheduling.
The inadequacies are ranked based on RII values.
For example For Ques.2: Insufficient project details available W = 196, A =5 and N =52,
Hence RII = 196/ (5 * 52) = 0.7538
Same steps are followed to calculate the Relative Importance Index (RII) of all the identified inadequacies on the basis of data obtained from the questionnaire survey
-
Analysis
The results obtained from the RII method of ranking are first ranked in the order of the decreasing order of the index to get the ranking of the inadequacies which generally occurs in the project scheduling. Below is the table with RII of each inadequacy calculated for all the responses all categories.
TABLE I. SCHEDULING INADEQUACIES WITH RESPECTIVE RII
S. No.
SCHEDULING INADEQUACIES
RII
1
Lack of scheduling knowledge
0.6500
2
Insufficient project details available
0.7538
3
Documentation of schedule upgradation is not maintained (Lack of regular reviews)
0.6885
4
The Schedule is Out of Date
0.7615
5
Broken critical path (missing dependency) and not closing the loop
0.6885
6
Errors in technical logic (Improper logical relationship between the activities)
0.7346
7
Incomplete schedule (Work started with partly approved schedule) or not getting the schedule signed-off (work started without getting prior approval)
0.6423
8
Procurement of the critical materials is not included in the schedule
0.7115
9
Weather restraints are not considered (extreme summers/winters, heavy rainfall, etc.)
0.6269
10
Lack of Contingency (for known unknowns and unforeseen circumstances)
0.6500
11
Floats and its utilization is not considered or included in the scheduling
0.6077
12
Actual Resources are not considered (unlimited resources are considered mostly) during developing the project schedule
0.7077
13
Durations and Productivity considered are unrealistic
0.6808
14
Presence of hangers (an activity with no successors, leading to unrealistic float)
0.7154
15
Ignoring inspections and testing of the materials/works in the scheduling
0.6000
16
Imposing lots of Constraints on activities and milestones (leading to the reduction in flexibility and creation of negative floats)
0.6038
17
Presence of concurrent activities (a lot of similar tasks scheduled to happen at the same time leading to resource overallocation)
0.6692
18
Overlooking Holidays (inappropriate use of calendar and consideration of working / non-working timings)
0.5385
19
Not setting the baseline as well as revising it as per the requirement.
0.5962
20
Understanding and application of task types (duration, work, and units) and their relation (Duration * Units = Work) in the scheduling
0.5923
As a process of prioritizing, the inadequacies with Relative Importance Index (RII) of more than 0.70 are selected / identified as the most occurring inadequacies in the construction project scheduling. Besides the selection of ranked results of all the respondents, the commonly occurred inadequacies (with RII more than 0.70) as ranked by the respondents (with the experience of over 5 years in the construction industry) are identified for the better ranking and analysis of the results obtained through the survey.
Figure 4.1.1 : Scheduling Inadequacies with their respective RIIs
Subsequently, the final step towards establishing the prioritizing a consolidated list of the project inadequacies by examining the results of both the group of respondents, as enumeratedabove. On this basis, the final list on the basis of top five ranked inadequacies with the highest RII (Relative Importance Index) is mentioned below.
-
Presence of hangers (an activity with no successors, leading to unrealistic float)
-
Actual Resources are not considered (unlimited resources are considered mostly) during developing the project schedule
-
The Schedule is Out of Date (schedule is not updated frequently or as per requirement)
-
Errors in technical logic (Improper logical relationship between the activities)
-
Insufficient project details available (before the start of the schedule)
-
-
-
PROPOSED MITIGATION MEASURES AND RECOMMENDATIONS
As discussed in the previous section a consolidated list of the project inadequacies by examining the results of both the group of respondents and the final list on the basis of top-ranked inadequacies with respect to the Relative Importance Index. This list in now instrumental for proposing the suitable mitigation measures which can be considered by the planners / schedulers while preparing the project schedule.
TABLE II. TOP FIVE SCHEDULING INADEQUACIES WITH RECOMMENDATIONS
S.NO.
INADEQUACIES
EXPLANATION
RECOMMENDATIONS
1
Insufficient project details available (before the start of the schedule)
Preparing a schedule with a sufficient / appropriate level of detail is quite difficult. The key is that the schedule has to work for the project team.
One additional / inadequacies mistake occurs when the schedule has too many tasks, which can make the schedule unmanageable.
As, large schedules can be unmanageable, so one technique is to use a high-level project summary schedule, with a minimum number of tasks. More detailed sub-schedules can then be prepared for each phase or major deliverables and linked to the project summary schedule.
Also, it's better to get specific requirements lists from the client at the start of the project. A written document with a list of exactly what should be delivered at the project conclusion will help with every part of project management.
2
The schedule is Out of Date (documentation / schedule is not updated frequently or as per requirement)
This is the most common issue prevailing in the construction industry. A scheduler / planner creates the construction schedule based on the cash flow information but usually doesnt retain access to that information. As the project progresses, if it is found that the schedule get off track, the tracing of the reason for the same is difficult to trace.
If the appropriate documentation would have been in place, the exact reason for setting up the schedule the way it was could be easily known.
The schedule must be updated to reflect the actual state of the project.
The vast majority of the schedules I have seen are out of date. Project managers will often abandon the schedule once the project is underway and find themselves fighting fires while in execution. The likelihood of this happening increases significantly if the schedule is too detailed and requires too much work to keep it up to date.
The schedule model is regularly updated to reflect progress and changes such as scope, durations, milestones, allocated resources, productivity rates, work methodology, or scheduling logic.
The bottom line is that if the schedule is not updated, then ability to forecast future dates through the scheduling is lost.
S.NO.
INADEQUACIES
EXPLANATION
RECOMMENDATIONS
3
Errors in technical logic (Improper logical relationship between the activities)
A logical order of dependencies is there in every construction schedule. These dependencies need to be properly defined as missing dependencies can lead missed deadlines and hence the construction schedules should be thoroughly checked to confirm all dependencies are in the required logical order.
This happens when the scheduler is incompetent in making the schedule and is not able to envisage and establish proper logical relationship between the activities.
Connecting the activities and milestones with sensible logic is the bedrock of any dynamic project schedule
The method of connection is defined as a relationship. Ensuring compliance with the same will prevent the schedule from containing open ends, where activities or milestones are missing predecessors or successors
4
Presence of hangers (an activity with no successors, leading to unrealistic float)
When a task lacks a predecessor and/or successor, the task is a hanger, which is an unintended break in the project network diagramThe problem here is that the forward and backward pass calculations will be incomplete and possibly wrong because each hanger results in a roadblock for CPM calculations.The obvious exception is the project start milestone, which has no predecessor, and the project complete milestone, which has no successor
As a basic scheduling rule make sure that every task should have at least one predecessor and at least one successor.
Scrutiny for hangers can be easily done using the Gantt chart view, which can be set up with columns showing the task numbers for both predecessor and successor tasks. To check for hangers, simply scroll down the task list looking for any tasks that lack at least one predecessor or successor.
5
Actual Resources are not considered (unlimited resources are considered mostly)
Most of the schedules are prepared without considering the availability of the resources during the demand of those resources in the project. The problem occurs when it is assumed that there are unlimited resources. Also, all the resources are not available at all times of the year during the project and therefore while creating the construction project schedule, a realistic sense of available resources needs to be maintained.
The allocation and utilization of the critical resources can be properly done with this consideration into the planning, and hence delays can be avoided that results from the unavailability of resources.
It is recommended that the project managers or the schedulers shall take the time to evaluate whether realistic assignments in terms of time and work allocated within a resources capacity are made or not. Also, there should be extreme caution when using the auto resource leveling feature and is better to use the same in manual mode.
-
CONCLUSION / INFERENCES:
The purpose of scheduling in the construction industry along with the scheduling standards and good practices to followed. The proper use of the components of the scheduling will definitely be usable for planning, executing, monitoring, and closing, in addition to the delivery of the project scope to stakeholders. The practice standard provides standards and guidelines using effective schedule management for a project by providing knowledge on the creation and updating / maintenance of schedules. An organization that holds the principles and good scheduling practices outlined in this practice standard and applies them across all the projects helps in development of the support of the organization's strategic value proposition are done in a consistent manner throughout the organization.
This study concludes with the identification of scheduling inadequacies through literature and industy experts. This involves prioritizing the identified inadequacies through a questionnaire survey floated among various industry experts. Several projects scheduling inadequacies / inefficacies were identified which occurs during the scheduling process. Also, the top five inadequacies are recognized through a questionnaire survey, and recommendations and possible solutions are provided for these inadequacies. The identification of scheduling inadequacies has been carried out through literature and industry experts. This involves prioritizing the identified inadequacies through a questionnaire survey floated among various industry experts. Lastly, the description of the identified common inadequacies is furnished along with the suitable and appropriate mitigating options and the recommendations.
-
ACKNOWLEDGMENTS
I am thankful to Professor (Dr.) Virendra Kumar Paul for his valuable inputs and guiding me in framing the outline of this research paper.
-
BIBLIOGRAPHY